HONG KONG AIRPORT CORE PROJECTS SPECIAL ISSUE 1/1999 Vol
Total Page:16
File Type:pdf, Size:1020Kb
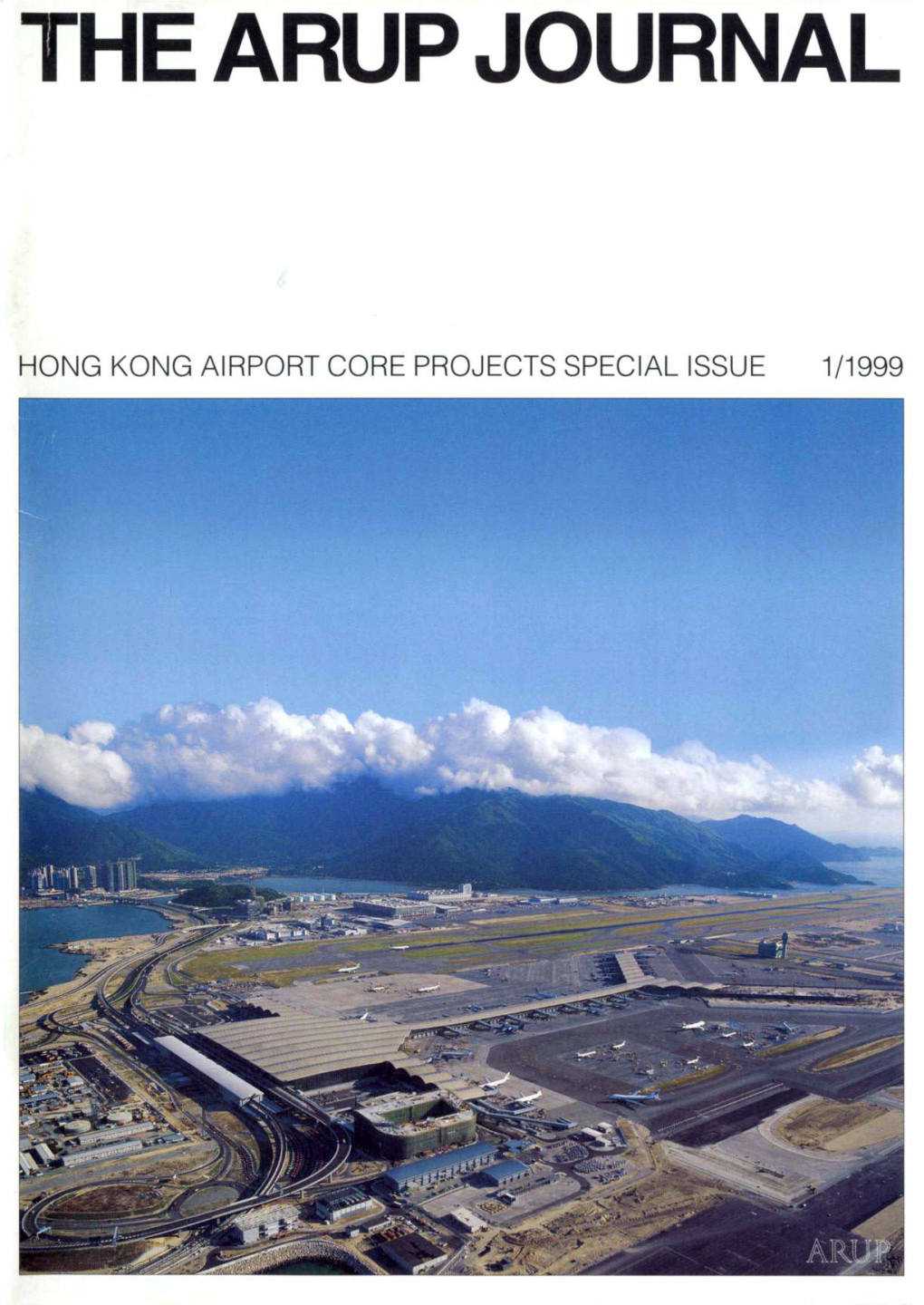
Load more
Recommended publications
-
T and Analysis of Walkability in Hong Kong
Measurement and Analysis of Walkability in Hong Kong By: Michael Audi, Kathryn Byorkman, Alison Couture, Suzanne Najem ZRH006 Measurement and Analysis of Walkability in Hong Kong An Interactive Qualifying Project Report Submitted to the faculty of the Worcester Polytechnic Institute In partial fulfillment of the requirements for Degree of Bachelor of Science In cooperation with Designing Kong Hong, Ltd. and The Harbour Business Forum On March 4, 2010 Submitted by: Submitted to: Michael Audi Paul Zimmerman Kathryn Byorkman Margaret Brooke Alison Couture Dr. Sujata Govada Suzanne Najem Roger Nissim Professor Robert Kinicki Professor Zhikun Hou ii | P a g e Abstract Though Hong Kong’s Victoria Harbour is world-renowned, the harbor front districts are far from walkable. The WPI team surveyed 16 waterfront districts, four in-depth, assessing their walkability using a tool created by the research team and conducted preference surveys to understand the perceptions of Hong Kong pedestrians. Because pedestrians value the shortest, safest, least-crowded, and easiest to navigate routes, this study found that confusing routes, unsafe or indirect connections, and a lack of amenities detract from the walkability in Hong Kong. This report provides new data concerning the walkability in harbor front districts and a tool to measure it, along with recommendations for potential improvements. iii | P a g e Acknowledgements Our team would like to thank the many people that helped us over the course of this project. First, we would like to thank our sponsors Paul Zimmerman, Dr. Sujata Govada, Margaret Brooke, and Roger Nissim for their help and dedication throughout our project and for providing all of the resources and contacts that we required. -
Initial Transport Assessment of Development Options
This subject paper is intended to be a research paper delving into different views and analyses from various sources. The views and analyses as contained in this paper are intended to stimulate public discussion and input to the planning process of the "HK2030 Study" and do not necessarily represent the views of the HKSARG. WORKING PAPER NO. 35 INITIAL TRANSPORT ASSESSMENT OF DEVELOPMENT OPTIONS Purpose 1. The purpose of this paper is to provide information on the reference transport demand forecasts, assessment of Reference Scenario and framework for option evaluations. Background 2. Under Stage 3 of the HK2030 Study, Development Scenario and Development Options are formulated. The Development Options are then subject to transport, economic, financial as well as environmental assessments. Under the integrated approach adopted for the Study, the transport requirements identified for the Development Options are also assessed in terms of the environmental, economic and financial implications in order that a meaningful comparison of the Development Options could be made. 3. Under the Reference Scenario, various development choices have been considered to satisfy the land requirements. They can broadly be categorised into two different options of development patterns, namely Decentralisation and Consolidation. The details are presented in the paper on Development Options under the Reference Scenario. Assessments have been carried out to identify the transport requirements of the two Development Options in 2010, 2020 and 2030. The findings are summarised in the following sections. Development Options 4. Under the Reference Scenario, the population in 2030 could be in the region of 9.2 million which is only marginally more than the population of 8.9 million for 2016 adopted in the previous strategic planning. -
Destinations : Tin King Estate - Admiralty/Central
Residents’ Service Route No. : NR723 Destinations : Tin King Estate - Admiralty/Central Routeing (Tin King Estate - Admiralty) : via Tin King Road, Tsing Tin Road, Tuen Mun Road, Tsing Long Highway, Cheung Tsing Highway, Cheung Tsing Tunnel, Tsing Kwai Highway, West Kowloon Highway, Western Harbour Crossing, Sai Ying Pun Interchange, Connaught Road West, Connaught Road Central, Man Kat Street, Man Cheung Street, Man Yiu Street, Harbour View Street, Connaught Road Central, Harcourt Road, Cotton Tree Drive slip road, Queensway, Rodney Street and Drake Street. Stopping Places : Pick Up : Tin King Road outside Tin Chui Set Down : 1. Connaught Road West House Waterfront Police Station 2. Man Cheung Street Hong Kong Station 3. Drake Street Admiralty Garden Departure time : Mondays to Saturdays (except Public Holidays) 1. 7.00 a.m. 5. 7.55 a.m. 2. 7.15 a.m. 6. 8.05 a.m. 3. 7.30 a.m. 7. 8.15 a.m. 4. 7.45 a.m. 8. 8.30 a.m. Routeing (Central - Tin King Estate) : via Connaught Road Central, Connaught Road West, Wing Lok Street, Hillier Street, Connaught Road Central, Connaught Road West, Sai Ying Pun Interchange, Western Harbour Crossing, West Kowloon Highway, Tsing Kwai Highway, Cheung Tsing Tunnel, Cheung Tsing Highway, Tsing Long Highway, Tuen Mun Road, Tuen Hi Road, Tuen Mun Road, Tsing Tin Road, Ming Kum Road and Tin King Road. Stopping Places : Pick Up : 1. No. 137 Connaught Road Central Set Down : 1. Tuen Hi Road outside Tuen Mun Town Hall 2. Tin King Road outside Tin Chui House Departure time : Mondays to Fridays (except Public Holidays) 1. -
PR074/19 11 December 2019 Free Rides for Children and Half-Price
PR074/19 11 December 2019 Free Rides for Children and Half-price Octopus Fares for Seniors on Airport Express during Christmas and New Year Holiday Period Come and enjoy some Christmas cheer during the festive season with the MTR! For those planning getaways during the upcoming holiday period, special treats on the Airport Express, such as free rides for kids and half-price fares for the elderly, are up for grabs. Starting from next Monday (16 December 2019) until 2 February 2020, children aged 3 to 11 who hold valid Child Octopus* and passengers aged 65 or above with valid Elder Octopus will enjoy free rides and half-price Octopus fares respectively when they travel on the Airport Express from Hong Kong, Kowloon or Tsing Yi stations to Airport Station, or vice versa. All they need to do to enjoy the discount is simply tap on with their Child or Elder Octopus when passing through the Airport Express ticket gates. Furthermore, to offer more convenience to passengers travelling to and from the airport, the Airport Express will enhance its service during the Christmas and New Year holidays. During the peak travel days between 22 and 24 December 2019, the first train will depart from Hong Kong Station at 5:00am (50 minutes earlier than usual) for the convenience of passengers catching early flights at the airport. And on 26 December 2019 and 1 January 2020, the last train from AsiaWorld-Expo Station, which will stop at Airport Station, will depart at 1:25am (40 minutes later than usual). Details of the train service enhancements can be found in the Annex. -
Proposed Road Improvement Works in West Kowloon Reclamation Development Phase I
Proposed Road Improvement Works in West Kowloon Reclamation Development Phase I Project Profile (Report No. 276799/11.01/B) August 2011 Highways Department, HKSAR Government Proposed Road Improvement Works in West Kowloon276799 ReclamationTNI Development BRI 096/03 B P:\Hong Kong\ENL\PROJECTS\276799(BRI) West Kowloon Road Phase I Impr\reports\PP\Project Profile RevA doc 01 December 2009 Schemes H, I, J, Q (Interim Option) and Improvement Works at the Junction of Canton Road/ Ferry Street/ Jordan Road Project Profile August 2011 Highways Department 6/F., Homantin Government Offices, 88 Chung Hau Street, Homantin, Kowloon Mott MacDonald, 20/F, Two Landmark East, 100 How Ming Street, Kwun Tong, Kowloon, Hong Kong T +852 2828 5757 F +852 2827 1823 W www.mottmac.com.hk Phase I Project Profile Issue and revision record Revision Date Originator Checker Approver Description A June 2011 Various Eric Ching H. T. Cheng First Issue B August 2011 Various Eric Ching H. T. Cheng Second Issue This document is issued for the party which commissioned it We accept no responsibility for the consequences of this and for specific purposes connected with the above-captioned document being relied upon by any other party, or being used project only. It should not be relied upon by any other party or for any other purpose, or containing any error or omission used for any other purpose. which is due to an error or omission in data supplied to us by other parties This document contains confidential information and proprietary intellectual property. It should not be shown to other parties without consent from us and from the party which commissioned it. -
Yum Sing Coupon[Relaxation]
10% off Ocean Park Daytime Admission Ticket Ocean Park Aberdeen, Hong Kong Tel: (852) 3923 2323 Opening Time: 10:00 – 18:00 (daily) (extended opening hours during festive events) Terms and Conditions: 1. Ocean Park Admission Tickets must be purchased on-site at the Ticketing Offices located at 6. Please present a valid boarding pass (within 7 days of arrival day) and the offer coupon Ocean Park Main Entrance and Tai Shu Wan Entrance. upon patronage. 2. Only one Ocean Park Day Admission Ticket can be purchased with this offer coupon. 7. The special offers cannot be used in conjunction with other promotional offers. 3. This offer coupon cannot be exchanged for cash. 8. Participating venues reserve the right of final decision on matters concerning the offers. 4. This coupon cannot be sold. Any person caught selling this coupon will be subject to 9. Offer is valid until 15 April 2011. prosecution. 5. Ocean Park reserves the right to terminate this offer without prior notice. HK$20 off regular-priced adult admission ticket Madame Tussauds Hong Kong Shop P101, The Peak Tower, 128 Peak Road The Peak, Hong Kong Tel: 2849 6966 Opening Time: l0:00 – 22:00 (daily) Terms and Conditions: 1. Each coupon can be used once only. 6. Please present a valid boarding pass (within 7 days of arrival day) and the offer coupon upon 2. This coupon cannot be redeemed for cash and cannot be used in conjunction with other patronage. promotional offers. 7. Participating venues reserve the right of final decision on matters concerning the offers. -
CCB (Asia) Hong Kong Wine & Dine Festival Free Wine Packs for Visitors
CCB (Asia) Hong Kong Wine & Dine Festival Free Wine Packs for Visitors Channel 2: Visitors who patronise the attractions below or purchase travel products from the following tour operators during the period of 22–28 October 2018 can present valid travel documents at the relevant attraction or tour operator to pick up a Wine Pack voucher. Merchant Location Big Bus Tours Big Bus Tours Information Centre (TST) Unit KP-38, 1/F, Kowloon Star Ferry Pier, Tsim Sha Tsui, Kowloon Big Bus Tours Information Centre (Central) Shop i2, 1/F, Central Ferry Pier 7, Central, Hong Kong Island Crystal Bus Suite 2215, Langham Place, 8 Argyle Street, Mong Kok, Kowloon Gray Line Tours of Hong Kong Limited 5/F Cheong Hing Building, 72 Nathan Road, Kowloon Tourist Services Counter, MTR Customer Service Centre, Level 5, Arrival Platform, MTR Airport Station, Lantau Island, Outlying Islands Tourist Services Counter, MTR Customer Service Centres, Arrival Halls A & B, Level 5, Terminal 1, Hong Kong International Airport, Lantau Island, Outlying Islands Tourist Services Counter (Next to Customer Service Centre), CAC 2, 2/F Arrival Hall, MTR Lo Wu Station, New Territories Tourist Services Counter, Level 3 – L3-048 MTR Lok Ma Chau Station, New Territories Tourist Services Counter (Opposite to MTR Customer Service Centre), HUH E6, MTR Hung Hom Station, Kowloon Harbour Cruise Bauhinia Units 2201-2, 22/F, Java 108 Commercial Centre, North Point, Hong Kong Island Jumbo Kingdom Shum Wan Pier Drive, Wong Chuk Hang, Aberdeen, Hong Kong Madame Tussauds Hong Kong Shop P101, -
5. Air Quality Impact
Expansion of Hong Kong International Airport into a Three-Runway System Environmental Impact Assessment Report 5. Air Quality Impact 5.1 Introduction 5.1.1 Overview 5.1.1.1 This section presents the assessment of potential air quality impacts associated with the construction and operation phases of the project, which has been conducted in accordance with the criteria and guidelines as stated in section 1 of Annex 4 and Annex 12 of the Technical Memorandum on Environmental Impact Assessment Process (EIAO-TM) as well as the requirements given in Clause 3.4.3 and Section I of Appendix A of the EIA Study Brief (ESB- 250/2012). 5.1.2 Air Quality Legislations, Standards and Guidelines 5.1.2.1 The assessment is carried out following the relevant criteria and standards as specified in the following legislation and guidelines for evaluating air quality impacts: ° Environmental Impact Assessment Ordinance (EIAO) (Cap. 499.S16), EIAO-TM, Annexes 4 and 12; ° Air Pollution Control Ordinance (APCO) (Cap. 311): ° Air Pollution Control (Construction Dust) Regulation; ° Guidance Note on the Best Practicable Means for Cement Works (Concrete Batching Plant) BPM 3/2 (93); ° Guidance Note on the Best Practicable Means for Tar and Bitumen Works (Asphaltic Concrete Plant) BPM 15 (94); and ° Guidance Note on the Best Practicable Means for Mineral Works (Stone Crushing Plants) BPM 11/1 (95). Technical Memorandum on Environmental Impact Assessment Process 5.1.2.2 The criteria and guidelines for evaluating air quality impacts are set out in Section 1 of Annex 4 and Annex 12 respectively of the EIAO-TM. -
Paper on Fare Adjustment of Airport Express Line Prepared By
立法會 Legislative Council LC Paper No. CB(4)839/16-17(07) Ref. : CB4/PL/TP Panel on Transport Meeting on 21 April 2017 Background brief on fare adjustment of Airport Express Line Purpose This paper provides background information on the fare adjustment of of the Airport Express Line ("AEL"). It also summarizes the major views and concerns expressed by Legislative Council ("LegCo") Members on the subject. Background 2. AEL provides a dedicated express railway service linking the city centre with the Hong Kong International Airport ("HKIA") and the AsiaWorld-Expo ("AWE"). It commenced operation in July 1998 to tie in with the opening of the new airport, and has been extended to AWE since December 2005 to serve passengers patronizing the exhibition centre. AEL is operated by the MTR Corporation Limited ("MTRCL"). At present, there are five stations along AEL, namely, AWE Station, Airport Station, Tsing Yi Station, Kowloon Station and Hong Kong Station. Patronage 3. As the clienteles of AEL are mainly passengers travelling to and from HKIA, MTRCL advises that its patronage fluctuates and is affected by various factors such as travel season and overall economic conditions. From 2006 to 2016, the average daily patronage of AEL increased from around 26 200 to around 44 100. Having regard to the growing loading in recent years, MTRCL has enhanced train frequency of AEL from 12 minutes to 10 minutes since January 2012, with a view to providing a better travelling environment for passengers. The patronage figures for the past decade are at Appendix I. - 2 - Fares 4. According to the Operating Agreement signed between the Government and MTRCL ("OA") upon the rail merger in 2007, AEL is not a public transport mode for daily commuting, but mainly for business and travelling. -
Hong Kong Bird Report 2011
Hong Kong Bird Report 2011 Hong Kong Bird Report 香港鳥類報告 2011 香港鳥類報告 Birdview report 2009-2010_MINOX.indd 1 5/7/12 1:46 PM Birdview report 2009-2010_MINOX.indd 1 5/7/12 1:46 PM 防雨水設計 8x42 EXWP I / 10x42 EXWP I • 8倍放大率 / 10倍放大率 • 防水設計, 尤合戶外及水上活動使用 • 密封式內充氮氣, 有效令鏡片防霞防霧 • 高折射指數稜鏡及多層鍍膜鏡片, 確保影像清晰明亮 • 能阻隔紫外線, 保護視力 港澳區代理:大通拓展有限公司 荃灣沙咀道381-389號榮亞工業大廈一樓C座 電話:(852) 2730 5663 傳真:(852) 2735 7593 電郵:[email protected] 野 外 觀 鳥 活 動 必 備 手 冊 www.wanlibk.com 萬里機構wanlibk.com www.hkbws.org.hk 觀鳥.indd 1 13年3月12日 下午2:10 Published in Mar 2013 2013年3月出版 The Hong Kong Bird Watching Society 香港觀鳥會 7C, V Ga Building, 532 Castle Peak Road , Lai Chi Kok, Kowloon , Hong Kong, China 中國香港九龍荔枝角青山道532號偉基大廈7樓C室 (Approved Charitable Institution of Public Character) (認可公共性質慈善機構) Editors: John Allcock, Geoff Carey, Gary Chow and Geoff Welch 編輯:柯祖毅, 賈知行, 周家禮, Geoff Welch 版權所有,不准翻印 All rights reserved. Copyright © HKBWS Printed on 100% recycled paper with soy ink. 全書採用100%再造紙及大豆油墨印刷 Front Cover 封面: Chestnut-cheeked Starling Agropsar philippensis 栗頰椋鳥 Po Toi Island, 5th October 2011 蒲台島 2011年10月5日 Allen Chan 陳志雄 Hong Kong Bird Report 2011: Committees The Hong Kong Bird Watching Society 香港觀鳥會 Committees and Officers 2013 榮譽會長 Honorary President 林超英先生 Mr. Lam Chiu Ying 執行委員會 Executive Committee 主席 Chairman 劉偉民先生 Mr. Lau Wai Man, Apache 副主席 Vice-chairman 吳祖南博士 Dr. Ng Cho Nam 副主席 Vice-chairman 吳 敏先生 Mr. Michael Kilburn 義務秘書 Hon. Secretary 陳慶麟先生 Mr. Chan Hing Lun, Alan 義務司庫 Hon. Treasurer 周智良小姐 Ms. Chow Chee Leung, Ada 委員 Committee members 李慧珠小姐 Ms. Lee Wai Chu, Ronley 柯祖毅先生 Mr. -
2 March 2016
THE HONGKONG AND SHANGHAI HOTELS, LIMITED 2 March 2016 THE HONGKONG AND SHANGHAI HOTELS, LIMITED CELEBRATES ITS 150th ANNIVERSARY IN 2016 The Hong Kong-based parent company of The Peninsula Hotels, The Peak Tram, Peak Tower and Repulse Bay Complex, celebrates 150 years of tradition well served. HONG KONG 2 March, 2016: The distinguished heritage of The Hongkong and Shanghai Hotels, Limited (HSH) reaches a new milestone today as HSH celebrates its 150th anniversary. Originally incorporated on 2 March 1866 as The Hongkong Hotel Company, Limited, HSH was one of the first companies to be listed on the Hong Kong Stock Exchange and is currently the oldest registered company on the Hong Kong Companies Registry. For a century and a half, the compelling story of HSH has been closely tied to its city of origin, Hong Kong. Whilst evolving to meet the changing times at home and abroad, HSH has never lost respect for its past and its heritage, and it continually strives to emulate the standards of service and style that earned it the accolade of “The Far East’s leading hotel company”. The concept of “Tradition well served” remains fundamental to HSH’s approach. “Tradition is taking account of a wonderful history, but remembering that everybody today looks to the future. It is important not to forget that the future is built on the past, and we have a great legacy,” said The Hon. Sir Michael Kadoorie, Chairman of HSH. “We believe that our rich history gives us a fuller understanding of our shared identity, culture and values, enabling us to manage change responsibly, to safeguard the best of the past and to keep innovating to meet the demands of the next generation.” Today, the HSH legacy encompasses a diverse portfolio of assets worth HK$44.2 billion1 including ten Peninsula Hotels around the world, The Peak Tram, The Peak Tower and The Repulse Bay Complex in Hong Kong. -
Why Some Airport-Rail Links Get Built and Others Do Not: the Role of Institutions, Equity and Financing
Why some airport-rail links get built and others do not: the role of institutions, equity and financing by Julia Nickel S.M. in Engineering Systems- Massachusetts Institute of Technology, 2010 Vordiplom in Wirtschaftsingenieurwesen- Universität Karlsruhe, 2007 Submitted to the Department of Political Science in partial fulfillment of the requirements for the degree of Master of Science in Political Science at the MASSACHUSETTS INSTITUTE OF TECHNOLOGY February 2011 © Massachusetts Institute of Technology 2011. All rights reserved. Author . Department of Political Science October 12, 2010 Certified by . Kenneth Oye Associate Professor of Political Science Thesis Supervisor Accepted by . Roger Peterson Arthur and Ruth Sloan Professor of Political Science Chair, Graduate Program Committee 1 Why some airport-rail links get built and others do not: the role of institutions, equity and financing by Julia Nickel Submitted to the Department of Political Science On October 12, 2010, in partial fulfillment of the Requirements for the Degree of Master of Science in Political Science Abstract The thesis seeks to provide an understanding of reasons for different outcomes of airport ground access projects. Five in-depth case studies (Hongkong, Tokyo-Narita, London- Heathrow, Chicago- O’Hare and Paris-Charles de Gaulle) and eight smaller case studies (Kuala Lumpur, Seoul, Shanghai-Pudong, Bangkok, Beijing, Rome- Fiumicino, Istanbul-Atatürk and Munich- Franz Josef Strauss) are conducted. The thesis builds on existing literature that compares airport-rail links by explicitly considering the influence of the institutional environment of an airport on its ground access situation and by paying special attention to recently opened dedicated airport expresses in Asia.