State of the Art in Hydrogen Liquefaction
Total Page:16
File Type:pdf, Size:1020Kb
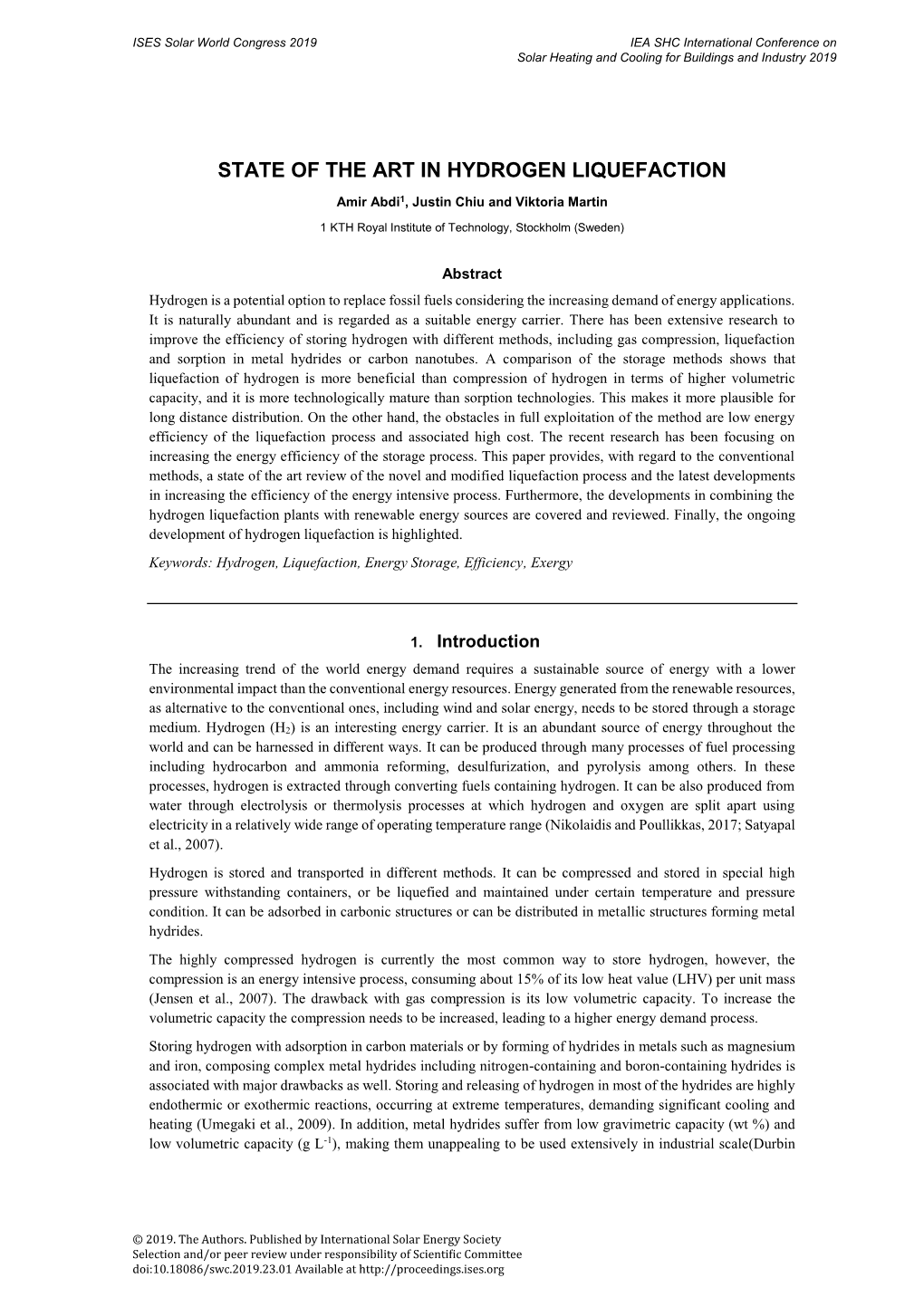
Load more
Recommended publications
-
High Efficiency and Large-Scale Subsurface Energy Storage with CO2
PROCEEDINGS, 43rd Workshop on Geothermal Reservoir Engineering Stanford University, Stanford, California, February 12-14, 2018 SGP-TR-213 High Efficiency and Large-scale Subsurface Energy Storage with CO2 Mark R. Fleming1, Benjamin M. Adams2, Jimmy B. Randolph1,3, Jonathan D. Ogland-Hand4, Thomas H. Kuehn1, Thomas A. Buscheck3, Jeffrey M. Bielicki4, Martin O. Saar*1,2 1University of Minnesota, Minneapolis, MN, USA; 2ETH-Zurich, Zurich, Switzerland; 3TerraCOH Inc., Minneapolis, MN, USA; 4The Ohio State University, Columbus, OH, USA; 5Lawrence Livermore National Laboratory, Livermore, CA, USA. *Corresponding Author: [email protected] Keywords: geothermal energy, multi-level geothermal systems, sedimentary basin, carbon dioxide, electricity generation, energy storage, power plot, CPG ABSTRACT Storing large amounts of intermittently produced solar or wind power for later, when there is a lack of sunlight or wind, is one of society’s biggest challenges when attempting to decarbonize energy systems. Traditional energy storage technologies tend to suffer from relatively low efficiencies, severe environmental concerns, and limited scale both in capacity and time. Subsurface energy storage can solve the drawbacks of many other energy storage approaches, as it can be large scale in capacity and time, environmentally benign, and highly efficient. When CO2 is used as the (pressure) energy storage medium in reservoirs underneath caprocks at depths of at least ~1 km (to ensure the CO2 is in its supercritical state), the energy generated after the energy storage operation can be greater than the energy stored. This is possible if reservoir temperatures and CO2 storage durations combine to result in more geothermal energy input into the CO2 at depth than what the CO2 pumps at the surface (and other machinery) consume. -
Thermodynamics for Cryogenics
Thermodynamics for Cryogenics Ram C. Dhuley USPAS – Cryogenic Engineering June 21 – July 2, 2021 Goals of this lecture • Revise important definitions in thermodynamics – system and surrounding, state properties, derived properties, processes • Revise laws of thermodynamics and learn how to apply them to cryogenic systems • Learn about ‘ideal’ thermodynamic processes and their application to cryogenic systems • Prepare background for analyzing real-world helium liquefaction and refrigeration cycles. 2 Ram C. Dhuley | USPAS Cryogenic Engineering (Jun 21 - Jul 2, 2021) Introduction • Thermodynamics deals with the relations between heat and other forms of energy such as mechanical, electrical, or chemical energy. • Thermodynamics has its basis in attempts to understand combustion and steam power but is still “state of the art” in terms of practical engineering issues for cryogenics, especially in process efficiency. James Dewar (invented vacuum flask in 1892) https://physicstoday.scitation.org/doi/10.1063/1.881490 3 Ram C. Dhuley | USPAS Cryogenic Engineering (Jun 21 - Jul 2, 2021) Definitions • Thermodynamic system is the specified region in which heat, work, and mass transfer are being studied. • Surrounding is everything else other than the system. • Thermodynamic boundary is a surface separating the system from the surrounding. Boundary System Surrounding 4 Ram C. Dhuley | USPAS Cryogenic Engineering (Jun 21 - Jul 2, 2021) Definitions (continued) Types of thermodynamic systems • Isolated system has no exchange of mass or energy with its surrounding • Closed system exchanges heat but not mass • Open system exchanges both heat and mass with its surrounding Thermodynamic State • Thermodynamic state is the condition of the system at a given time, defined by ‘state’ properties • More details on next slides • Two state properties define a state of a “homogenous” system • Usually, three state properties are needed to define a state of a non-homogenous system (example: two phase, mixture) 5 Ram C. -