Installation Guidelines for Power Drive Systems
Total Page:16
File Type:pdf, Size:1020Kb
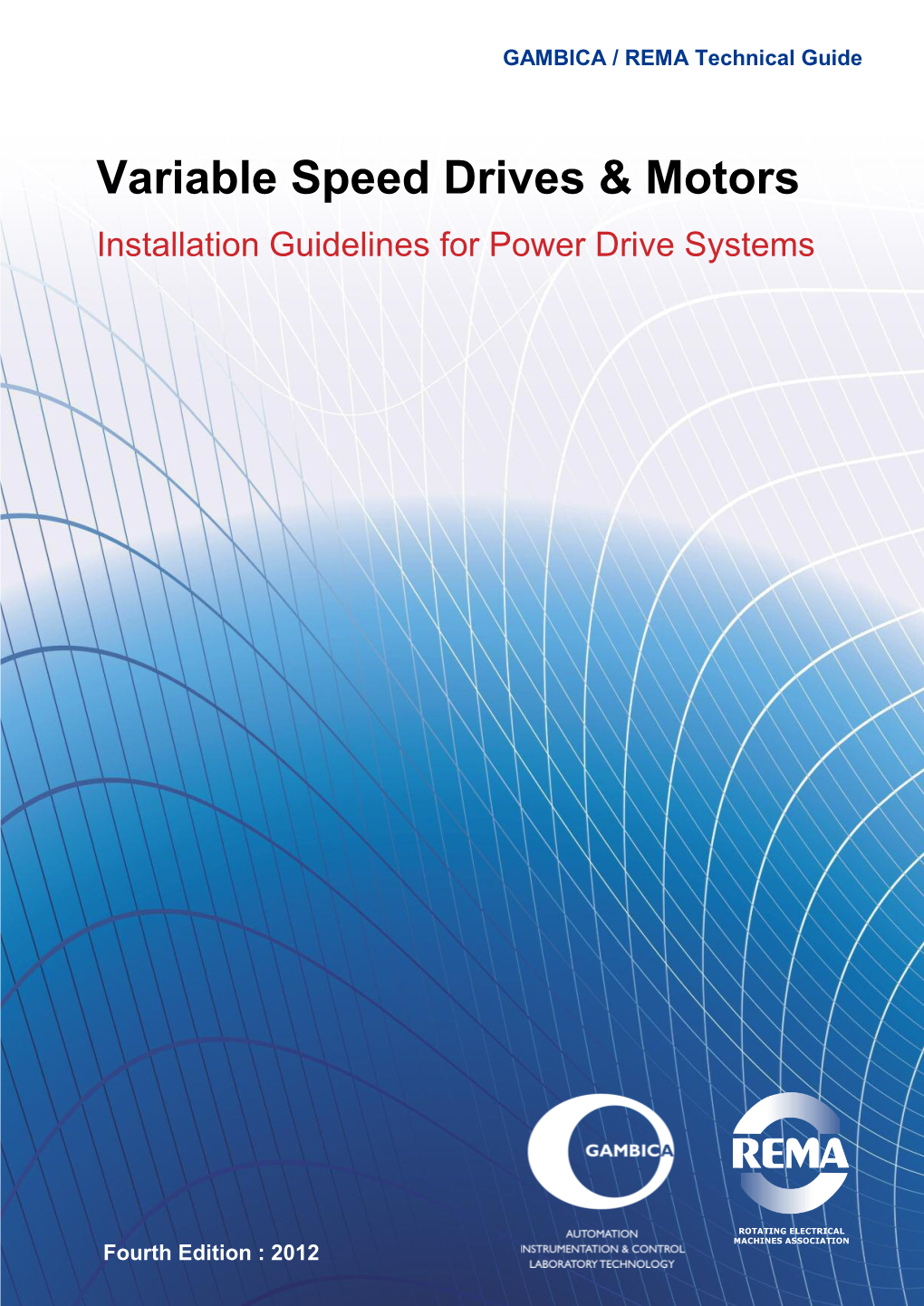
Load more
Recommended publications
-
Best Practice Guide to Cable Ladder and Cable Tray Systems
Best Practice Guide to Cable Ladder and Cable Tray Systems Channel Support Systems and other Associated Supports November 2012 BEAMA Best Practice Guide to Cable Ladder and Cable Tray Systems Including Channel Support Systems and other Associated Supports Companies involved in the preparation of this Guide Contents INTRODUCTION 5 DEFINITIONS AND ABBREVIATIONS 6 1. Packing Handling and Storage 8 1.1 General Packing and Handling 8 1.2 Loading and offloading recommendations 9 1.3 Storage 11 2A. Installation of the system 12 2.1 Common tools for Installation 12 2.2 Structural characteristics 12 2.3 Support Systems 18 2.4 Straight cable ladder and cable tray lengths 29 2.5 Coupler types (refer to manufacturer’s literature) 32 2.6 Fixings 36 2.7 Fittings 36 2.8 Accessories 39 2.9 Site modification 39 2.10 Earth protection and EMC 40 2B. Installation of Cable 41 2.11 Preparation 41 2.12 Wiring Regulations 41 2.13 Power Cables 41 2.14 Data Cables 46 2.15 Expansion 46 2.16 Electro Mechanical Effects 46 3. Environment 48 3.1 Selecting the right material and finish 48 3.2 Finishes 56 3.3 Non-Metallic systems 61 3.4 Loadings 63 3.5 Temperature 65 4. Health & Safety 67 5. Maintenance 68 5.1 Inspection 68 5.2 Removal of cables 68 5.3 On site repairs 68 6. Sustainability 69 6.1 Sustainable development 69 6.2 REACH regulations 69 6.3 The management of WEEE and RoHS 69 6.4 Environmental footprint 70 7. Applicable Standards 71 Companies involved in the preparation of this Guide 72 FIGURES Figure 1: Methods of removal 9 Figure 2: Loaded beams 13 Figure -
Answer the Purpose: 4
Page 26 1. CONDUCTORS Conductors are defined as materials that easily allow the flow of _________. Metals are _______ conductors while insulators are ______ . The 2 common metals used for conductors in the electrical trade are: ___________ and ______________. Aluminium has become more prevalent for larger C.S.A. conductors as it is cheaper and lighter but more brittle than copper. Current/ Copper/ Aluminium Thermoplastic-sheathed cable (TPS) consists of an outer toughened sheath of polyvinyl chloride (PVC) (the thermoplastic element) covering one or more individual cables which are PVC insulated annealed copper conductors. It is a commonly used type of wiring for residential and light commercial construction in many countries. The flat version of the cable with two insulated conductors and an uninsulated earth conductor all within the outer sheath is referred to as twin and earth. In mainland Europe, a round equivalent is more common. Flat cables (or festoon cables) are made in PVC and Neoprene and are used as trailing cables for cranes, open filed conveyors and shelve service devices. Flat cables offer the advantages of extremely small bending radius’s, high flexibility and minimum wastage of space. Thermoplastic-sheathed cable (TPS) consists of an outer toughened sheath of polyvinyl chloride (PVC) (the thermoplastic element) covering one or more individual cables which are PVC insulated annealed copper conductors. It is a commonly used type of wiring for residential and light commercial construction in many countries. The flat version of the cable with two insulated conductors and an uninsulated earth conductor all within the outer sheath is referred to as twin and earth. -
BICC Industrial Cables Catalog
TECHNICAL INFORMATION Click here for Table of Contents 9. Technical Information Click the BICC logo above to return to the Section Index TECHNICAL INFORMATION 9.i BICC Cables has made every effort to ensure the accuracy of the information provided in this catalog, however, we cannot be responsible for errors, omissions, or changes due to obsolescence. All data herein is subject to change without notice. Data and suggestions made in this catalog are not to be construed as recommendations to use any product in violation of any government law or regulations relating to any material or its use. EFFECTIVE 1998-09-30 TABLE OF CONTENTS 9. Technical Information Glossary..........................................................................................9.01-9.07 Reference Standards........................................................................9.08-9.16 Cable Handling and Storage ...........................................................9.17-9.20 Cable Pre-Installation..............................................................................9.21 Cable Installation............................................................................9.22-9.28 Cable Testing ..................................................................................9.29-9.32 Common Color Sequence........................................................................9.33 Metric Conversion ..................................................................................9.34 Copper Short Circuit Currents................................................................9.35 -
Electric Cooktop Installation Instructions
ELECTRIC COOKTOP INSTALLATION INSTRUCTIONS INSTALLATION AND SERVICE MUST BE PERFORMED BY A QUALIFIED INSTALLER. IMPORTANT: SAVE FOR LOCAL ELECTRICAL INSPECTOR'S USE. READ AND SAVE THESE INSTRUCTIONS FOR FUTURE REFERENCE. WARNING FOR YOUR SAFETY: Do not store or use gasoline or other flammable vapors and liquids in the vicinity of this or any other appliance. IMPORTANT INSTALLATION INFORMATION • All electric cooktops run off a single phase, three-wire or four-wire cable, 240/208 volt, 60 hertz, AC only electrical supply with ground. • Minimum distance between cooktop and overhead cabinetry is 30" (76.2 cm). For Standard Installation: * 30" (76.2 cm) min. for unprotected cabinet 24" (61 cm) min. for protected surface 30" Min. * (76.2 cm) B Cooktop Dimensions A C 4"X 8" (10.2 cm x 20.3 cm) opening to route armoured cable. Cooktop Cutout Dimensions 7¼" (18.4 cm) H*** E F D G 1" (2.5 cm) 35 1/8" (89.2 cm) **Note: D & E are critical to the proper installation of the cooktop. Please make sure to respect those Do not slide unit into cabinet cutout. dimensions. D reflects a finished dimension it is Protruding screws on the bottom of recommended to undercut this dimension and unit may damage the bottom front adjust upon installation of the appliance due to the finish. Figure 1 variation in countertop materials. CUTOUT DIMENSIONS H. DEPTH BELOW MODEL A. LENGTH B. WIDTH C. DEPTH LENGTH WIDTH COOKTOP*** D** E** FG 7 15 3 1 1 36 (91.4 ) 35 /8 (91.1) 25¾ (65.4) 7¾ (19.7) 35 /16 (91.3) 35 /16 (89.4) 22 (55.9) 1 /8 (2.9) Max. -
Technical Data 20 Amp 20 AX Switches
Technical Data 20 Amp 20 AX Switches Brief product description: Features: A range of IP rated accessories designed to protect • Clearly marked terminals with backed out the potentially dangerous electricity supply in the most captive screws for easy installation arduous of conditions • 20 Amp, 20AX inductive rated • Covers to seal the fixing screws • Earth terminal in mounting box • All cable entries in the 4 sides have removable blanking caps. • Housing will accept alternative switch modules from the Grid range • Neon indicator that can be wired to illuminate when off or on depending on wiring blanking caps. Product Images WP12 / WP30 WP14 WP42 WP42 Rear View WP12/30/42 Side View Technical Specifications Standard(s) BS EN 60669-1 Rating 20 Amp 250V~ (20AX - no derating for inductive or fluorescent loads) Switch Type Single pole (WP12, WP14, WP42 products) Double pole (WP30 products) Contact Gap 3.0mm minimum Terminal Capacity 4 x 1.0mm² 4 x 1.5mm² 2 x 2.5mm² 1 x 4.0mm² IP Rating IP66 RoHS Directive No WEEE Directive No Number of 20mm cable entries 5 x 20mm. 1 in each of 3 sides and 2 in the remaining side 1 drill out entry 20/25mm in rear face Size 91mm x 91mm x 67mm 20 Amp 20 AX Switches Line Diagrams 1 4 9 4 91 67 44 WP12 / WP30 1 4 9 4 91 67 44 WP14 4 1 4 9 91 67 44 WP42 Packaging Information Cat No. Description Packaging Type Pack Quantity Barcode Product Inner Box Outer Box Each Inner Outer Individual Inner Box Outer Box Box Box WP12 20A 1G, 2 Way Printed Box / Printed Outer Box 1 / 10 5050765022132 / 5050765022231 WP42 20A 2G, 2 Way Printed Box / Printed Outer Box 1 / 10 5050765022149 / 5050765022248 WP14 20A 1G, 1W, "PRESS" Printed Box / Printed Outer Box 1 / 10 5050765022156 / 5050765022255 WP30 20A 1G, Double Pole Printed Box / Printed Outer Box 1 / 10 5050765022163 / 5050765022262 Weights & Dimensions Cat No. -
Electrical for Garages
Electrical for Detached Garages: Updated Dec. 10, 2016 for 2015 CE Code * Garage construction requires permits (building and electrical) * Building and electrical permits must be applied for at the same time * Click before you dig – Alberta One Call – www.albertaonecall.com 1-800-242-3447 Underground branch circuit feeding a detached garage: There are several acceptable methods for feeding garages with underground wiring. Ensure the chosen method includes proper depth of burial, wire approved for wet locations and proper protection for the cable chosen. NMD90 (known as Loomex or Romex) shown above is not rated for underground use! Underground wiring methods. These are not the only approved methods but this shows the 3 most common methods: 1. NMWU cable in conduit - one continuous cable running from the panelboard in the house to a junction box, first device box or panel installed in the garage. The cable is protected by PVC conduit on all exterior surfaces and for the entire underground section. Buried minimum 18” below finished grade. 2. NMWU cable direct buried - one continuous cable running from the house panel to a junction box, first device box or panel installed in the garage. Cable protected by PVC conduit on all exterior surfaces to the bottom of the trench. Cable is then laid in the trench (direct buried) and protected by a layer of screened sand with a maximum particle size of 4.75 mm or screened earth at least 75 mm (3”) deep both above and below the cable. Buried minimum 24” below finished grade. 1 3. TECK Cable - one continuous cable running from the house panel to a junction box, first device box or panel installed in the garage. -
L Power Outage in Nigeria: History, Causes and Possible Solutions
Journal of Energy Technologies and Policy www.iiste.org ISSN 2224-3232 (Paper) ISSN 2225-0573 (Online) Vol.2, No.6, 2012 Electrical Power outage in Nigeria: History, causes and possible solutions 1Arobieke Oluwole, 2Osafehinti Samuel, 3Oluwajobi Festus, 4Oni Olatunji Electrical Engineering Department, Rufus Giwa Polytechnic, Owo. *Email Corresponding Author [email protected] Abstract Power outages have assumed a very high embarrassing dimension in Nigeria. There are several areas of national life that power outage should never rear its ugly head but alas in Nigeria power outage for several days is commo n and could happen just anywhere – In 2009, the presidential palace was not spared and power outage became so frequent that ever since, the state house is powered 24 hours with generators. The last Junior World cup played in Nigeria really brought out some embarrassing moments when the whole pitch was thrown in darkness. The Muritala Mohammed Airport is not spared despite being the main gateway in the south into and out of this country. In the midst of this however, Nigeria's demand for energy and electrici ty is increasing rapidly and Nigeria has a 20 - 2020 vision (i.e. to become one of the twenty industrialized countries by year 2020). This paper covers 120 substations in Ondo State of Nigeria that can be described as fairly industrialised and well populat ed. The information available from these stations helps to describe a general situation facing the country as a whole. This article presents some solutions to these embarrassing moments. It is a paper designed to highlight some steps that can help achieve stable power supply in Nigeria. -
Guide to the Installation of PV Systems 2Nd Edition
73376 COVERS 17/10/06 3:10 pm Page 2 Photovoltaics in Buildings Guide to the installation of PV systems 2nd Edition the department for Enterprise DTI/Pub URN 06/1972 73376 COVERS 17/10/06 3:10 pm Page 3 Preface to 2nd edition 2006 Since the first edition (2002) the guide has been updated to reflect the significant experience gained with- in the UK PV industry under the DTI solar PV grants programmes. Other major changes covered include: l Engineering Recommendation G83/1(2003) issued to replace ER G77/1 l additional guidance for off-grid battery systems l guidance for larger systems connected under ER G59/1 l Part P Building Control notification Requirements ETSU Report No: ETSU S/P2/00355/REP/1 Authors BRE EA Technology Halcrow Group SunDog Energy (2nd Edition: Sundog Energy, Halcrow Group, Energy Saving Trust) Acknowledgments Thanks to the following for commenting on the drafts IEE, HSE, ESD, Intersolar, NAPS Systems, NHBC, Dulas, CREST, DTI Engineering Inspectorate, EST, Solarcentury. Special thanks to Martin Cotterell First Published 2002 2nd Edition 2006 The work described in this report was carried out under contract as part of the DTI Sustainable Energy Programmes. The views and judgements expressed in this report are those of the contractor and do not nec- essarily reflect those of the DTI. This guide was originally prepared by BRE and others on behalf of the DTI. Every effort has been made to ensure that the information given herein is accurate but no legal responsibili- ty can be accepted by the DTI, BRE and their collaborators, for any errors, omissions or misleading statements. -
Wire and Cables
ALCAN CaBLE INSTALLER’S HANDBOOK FOR ALCAN WIRE AND CABLES ABOUT THIS GUIDE This guide is intended to provide introductory technical Wire and cable products supplied by Alcan comply with data to aid the correct selection of wire and cable for the codes, standards and product specifications as permanent installation in commercial, institutional and indicated in this guide. industrial premises. Such installations are governed by the Weights and measurements are subject to manufacturing requirement of the Canadian Electrical Code Part I, and tolerances and product design changes. Consequently, enforced by the appointed authority having jurisdiction in Alcan does not accept responsibility for costs incurred by this area under provincial law (federal law in the case of a purchaser as a result of weights and measurements not federal territories), with or without Code amendments as conforming exactly to those indicated. the case may be. Wires and cables in installations falling under the jurisdiction of the provincial and territorial inspection authorities are almost invariably required to be certified to the requirements of CSA standards under the approval of the CSA Technical Committee on Wiring Products. This guide provides information on standard products stocked by Alcan’s Distributors. Alcan manufactures a wide range of additional products in various sizes which can be supplied by special order. For more information, contact your distributor or visit www.cable.alcan.com for the most current list of product offerings. ABOUT ALCAN Alcan is a name people know and trust. For over a We’re committed to the success of our products, and to century, our products have helped supply communities the satisfaction of our customers. -
CEC-12 [Rev-6] Page 1 of 6
ELECTRICAL SAFETY Information Bulletin March 2014 CEC-12 [rev-6] Page 1 of 6 CANADIAN ELECTRICAL CODE SUBJECT: Section 12 – Wiring Methods Conductors General Insulation Thickness on Conductors Used in Ungrounded or Impedance Grounded Systems With the change in the conductor standards, RW90 conductor is now available with a voltage rating of 600V. The suitability of this conductor on 600V ungrounded and impedance grounded systems, where past practice has been to use 1000 V conductors, has been questioned. Electro-Federation C.A.N.A.D.A has issued a paper explaining that the insulation thickness on low voltage conductors is intended for mechanical strength as well as insulation value. Therefore, it is thicker than would be required for insulation value alone. Based on this, the wire and cable manufacturers have agreed that 600V RW90 rated cable is suitable for use on 600V ungrounded or impedance grounded systems. Rule 12-012 Underground Installations Mechanical Protection for Direct Buried Conductors The Appendix B Note on Rule 12-012 indicates that polyethylene water pipe in conformance with CSA Standard B137.1, Polyethylene Pipe for Cold Water Services is considered acceptable for mechanical protection of conductors or cables used for direct earth burial. Although acceptable for mechanical protection of conductors or cables installed underground, this material is not approved as a wiring material and should not be installed as a raceway inside buildings. Protection of Conductors and Cables A review of Rule 12-012(5) indicates that it is intended to apply to cables other than armoured cable, mineral-insulated cable and aluminum-sheathed cable. -
Regulations for Electrical Installations - 1997 Edition
REGULATIONS FOR ELECTRICAL INSTALLATIONS 2017 EDITION INTRODUCTION: This edition supersedes the REGULATIONS FOR ELECTRICAL INSTALLATIONS - 1997 EDITION. The Revised Edition incorporates the amendments and guidelines issued and posted on DEWA website from time to time. The objective of the regulation is to provide consumers, consultants, contractors, electrical engineers & technicians with general guide for design, installation, inspection and compliance with DEWA’s requirements for electric installations, in order to safeguard person and property from hazards arising from the use of electricity. The regulation however is not intended to substitute detailed specifications nor to serve as an instruction manual for untrained persons. It is essential that all consultants, contractors, electrical engineers & technicians study and abide by these regulations. This of course does not absolve the concerned parties from obtaining other necessary approvals from DEWA. References are generally made to the seventeenth edition of the IET (The Institution of Engineering and Technology) wiring regulation and International Electromechanical Commission (IEC) documents. Consideration has been given to the prevention of fire and shock hazards as well as proper operation and maintenance of wiring installation and equipment. REGULATIONS FOR ELECTRICAL INSTALLATIONS CONTENTS INTRODUCTION SECTION1: GENERAL REQUIREMENTS 1.1 Scope 1.2 Electricity supply 1.3 Ambient conditions 1.4 DEWA enrolment for consultants and electrical contractors 1.5 Workmanship 1.6 Standards -
Iberville®/Nutek®/Steel City®/Carlon® - Boxes and Covers — A
— A Iberville®/Nutek®/Steel City®/Carlon® - Boxes and covers — A Iberville/Nutek/Steel City/Carlon - Boxes and covers — Table of contents Section A Boxes and Covers Iberville/NuTek/Carlon A4 Device boxes A17 4 in. octagonal boxes A35 4 in. square boxes A39 4 11/16 in. square boxes A45 Utility boxes and covers A47 Concrete rings and accessories A49 Concrete rings / mud boxes A50 Masonry boxes and accessories A51 347 V Boxes A52 Power / communication A57 Pre-ganged boxes A59 Extension rings A60 Rework boxes A61 Steel stud boxes A63 Bar hangers and brackets A67 Brackets, clamps, partitions A70 Accessories A71 Low voltage brackets A72 Vapour barriers A74 5 SquareTM boxes A75 NuTek nonmetallic boxes A79 NuTek Extension rings / vapour barriers A82 Carlon curved lid A83 A4 IBERVILLE/STEEL CITY/NUTEK/CARLON BOXES AND COVERS — Major types of electical boxes Technical specifications There are 10 major types of electrical boxes used in Canada. All these types of boxes serve specific purposes and are offered with various features / characteristics. Type Purpose Features / Characteristics Device boxes Flush installation of a device (switch, receptacle, thermostat, ...) From 11 ⁄2 in. deep up to 3 in. deep Available options: cable clamps, brackets, gangable For new or old work Octagonal boxes Wire connections (junction box) 3 depths available: 1 ⁄2 in., 11 ⁄2 in., 21 ⁄8 in. Light fixture installation Available options: cable clamps, brackets, extensions Temporary device installation 4 in. Square boxes Wire connections (junction box) 2 depths available: 11 ⁄2 in., 21 ⁄8 in. Flush or surface device installation (special cover required) Available options: brackets and extensions 411 ⁄16 in.