Plasma Temperature of Spark Discharge in a Spark-Ignition Engine Using a Time Series of Spectra Measurements
Total Page:16
File Type:pdf, Size:1020Kb
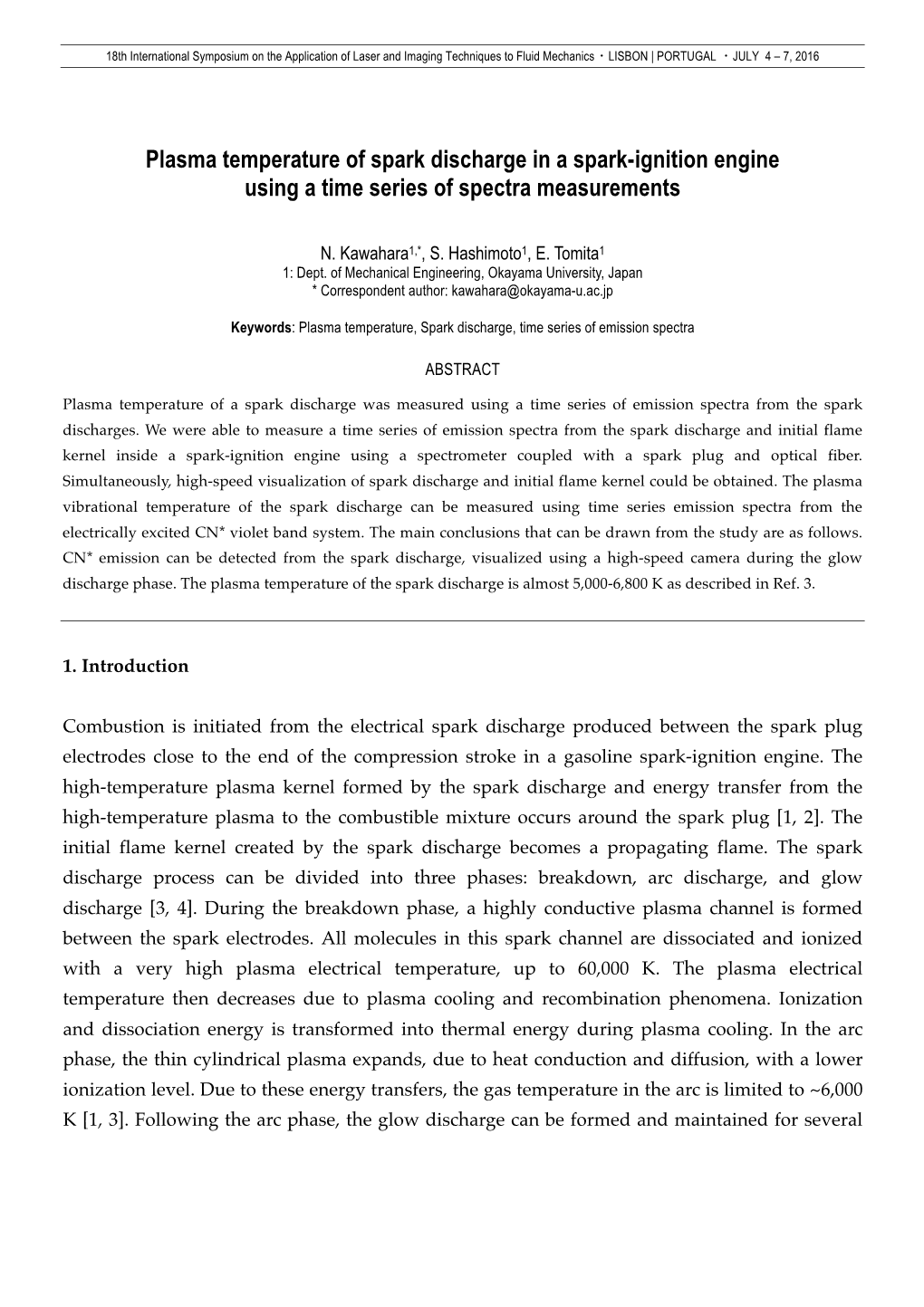
Load more
Recommended publications
-
Detailed Investigation of the Electric Discharge Plasma Between Copper Electrodes Immersed Into Water
atoms Article Detailed Investigation of the Electric Discharge Plasma between Copper Electrodes Immersed into Water Roman Venger 1, Tetiana Tmenova 1,2,*, Flavien Valensi 2, Anatoly Veklich 1, Yann Cressault 2 and Viacheslav Boretskij 1 1 Electronics and Computer Systems, Faculty of Radio Physics, Taras Shevchenko National University of Kyiv, 64, Volodymyrska St., 01601 Kyiv, Ukraine; [email protected] (R.V.); [email protected] (A.V.); [email protected] (V.B.) 2 Université de Toulouse, UPS, INPT; LAPLACE (Laboratoire Plasma et Conversion d’Energie), 118 route de Narbonne, F-31062 Toulouse CEDEX 9, France; [email protected] (F.V.); [email protected] (Y.C.) * Correspondence: [email protected]; Tel.: +38-063-598-5219 Academic Editors: Milan S. Dimitrijevi´cand Luka C.ˇ Popovi´c Received: 11 September 2017; Accepted: 16 October 2017; Published: 23 October 2017 Abstract: A phenomenological picture of pulsed electrical discharge in water is produced by combining electrical, spectroscopic, and imaging methods. The discharge is generated by applying ~350 µs long 100 to 220 V pulses (values of current from 400 to 1000 A, respectively) between the point-to-point copper electrodes submerged into the non-purified tap water. Plasma channel and gas bubble occur between the tips of the electrodes, which are initially in contact with each other. The study includes detailed experimental investigation of plasma parameters of such discharge using the correlation between time-resolved high-speed imaging, electrical characteristics, and optical emission spectroscopic data. Radial distributions of the electron density of plasma is estimated from the analysis of profiles and widths of registered Hα and Hβ hydrogen lines, and Cu I 515.3 nm line, exposed to the Stark mechanism of spectral lines’ broadening. -
Research Paper Commerce Physics Atomic Emission Spectroscopy
Volume-4, Issue-10, Oct-2015 • ISSN No 2277 - 8160 Commerce Research Paper Physics Atomic Emission Spectroscopy Ramanjeet Kaur Assistant Professor Physics Department, R S D College, Ferozepur City ABSTRACT The atomic emission spectroscopy is method based on the study of light emitted by atoms to determine the proportional quantity of a particular element in a given sample. Three techniques of atomic emission spectroscopy flame emission arc & spark emission and plasma atomic emission spectroscopy, their working, Principle and applications has been discussed in detail. KEYWORDS : -spectroscopy, flame, spark & arc, plasma, qualitative & quantitative analysis INTRODUCTION Atomic spectroscopy is the determination of elemental composition termining the accuracy of the analysis. The most popular sampling by its electromagnetic spectrum. Electrons exist in energy levels with- method is nebulization of a liquid sample to provide a steady flow of in an atom. These levels have well defined energies and electrons aerosol into a flame. An introduction system for liquid samples con- moving between them must absorb or emit energy equal to the dif- sists of three components: (a) a nebulizer that breaks up the liquid ference between them. The wavelength of the emitted radiant ener- into small’ droplets, (b) an aerosol modifier that removes large drop- gy is directly related to the electronic transition which has occurred. lets from the stream, allowing only droplets smaller than a certain Since every element has a unique electronic structure, the wave- size to pass, and (c) the flame or atomizer that converts the anaIyte length of light emitted is a unique property of each individual ele- into free atoms. -
Identification of the Electric Spark Electromagnetic Waveform Based on SVM
Advances in Engineering Research, volume 127 3rd International Conference on Electrical, Automation and Mechanical Engineering (EAME 2018) Identification of the Electric Spark Electromagnetic Waveform Based on SVM Tongtong Li1,*, Ziyuan Tong2, Shoufeng Tang1, Xia Qin1, Mingming Tong1 and Zhaoliang Xu3 1China University of Mining and Technology, China 2School of Electrical Engineering and Telecommunications, The University of New South Wales, Australia 3Xuzhou Hanlin Technology Co., Ltd., China *Corresponding author Abstract—Electromagnetic wave of electrical spark is a current. potential cause to eletrical equipment failure. This research focused on identificating and comparative analyzing the different A. Electromagnetic Characteristics Extraction of the Electric types of electromagnetic waveform generated by eletrical Spark equipment failure based on SVM. After analyzing and extracting the features the electromagnetic waveform, a model was built to First, confirm that you have the correct template for your identificate the type of the elctromagnetic waveform. The paper size. This template has been tailored for output on the collected standard electromagnetic waveforms were used as the US-letter paper size. If you are using A4-sized paper, please imput of the train model and the model accuracy was improved close this file and download the file for “MSW_A4_format”. by adjusting training parameters afer analyzing the results, When the distance between the contact closure electrodes When inputting an unknown type of electromagnetic waveform, gradually decreases or a strong electric field occurs[6], the SVM may predict the output of the network according to the current density gradually increases and produces high recognition rule. Then the types of electromagnetic waveforms temperature ionization, then contact and electrode gas will be were identificated by using adjusted models. -
Plasma Discharge in Water and Its Application for Industrial Cooling Water Treatment
Plasma Discharge in Water and Its Application for Industrial Cooling Water Treatment A Thesis Submitted to the Faculty of Drexel University by Yong Yang In partial fulfillment of the Requirements for the degree of Doctor of Philosophy June 2011 ii © Copyright 2008 Yong Yang. All Rights Reserved. iii Acknowledgements I would like to express my greatest gratitude to both my advisers Prof. Young I. Cho and Prof. Alexander Fridman. Their help, support and guidance were appreciated throughout my graduate studies. Their experience and expertise made my five year at Drexel successful and enjoyable. I would like to convey my deep appreciation to the most dedicated Dr. Alexander Gutsol and Dr. Andrey Starikovskiy, with whom I had pleasure to work with on all these projects. I feel thankful for allowing me to walk into their office any time, even during their busiest hours, and I’m always amazed at the width and depth of their knowledge in plasma physics. Also I would like to thank Profs. Ying Sun, Gary Friedman, and Alexander Rabinovich for their valuable advice on this thesis as committee members. I am thankful for the financial support that I received during my graduate study, especially from the DOE grants DE-FC26-06NT42724 and DE-NT0005308, the Drexel Dean’s Fellowship, George Hill Fellowship, and the support from the Department of Mechanical Engineering and Mechanics. I would like to thank the friendship and help from the friends and colleagues at Drexel Plasma Institute over the years. Special thanks to Hyoungsup Kim and Jin Mu Jung. Without their help I would not be able to finish the fouling experiments alone. -
Electrical Breakdown and Ignition of an Electrostatic Particulate Suspension Tae-U Yu Iowa State University
Iowa State University Capstones, Theses and Retrospective Theses and Dissertations Dissertations 1983 Electrical breakdown and ignition of an electrostatic particulate suspension Tae-U Yu Iowa State University Follow this and additional works at: https://lib.dr.iastate.edu/rtd Part of the Mechanical Engineering Commons Recommended Citation Yu, Tae-U, "Electrical breakdown and ignition of an electrostatic particulate suspension " (1983). Retrospective Theses and Dissertations. 7661. https://lib.dr.iastate.edu/rtd/7661 This Dissertation is brought to you for free and open access by the Iowa State University Capstones, Theses and Dissertations at Iowa State University Digital Repository. It has been accepted for inclusion in Retrospective Theses and Dissertations by an authorized administrator of Iowa State University Digital Repository. For more information, please contact [email protected]. INFORMATION TO USERS This reproduction was made from a copy of a document sent to us for microfilming. While the most advanced technology has been used to photograph and reproduce this document, the quality of the reproduction is heavily dependent upon the quality of the material submitted. The following explanation of techniques is provided to help clarify markings or notations which may appear on this reproduction. 1. The sign or "target" for pages apparently lacking from the document photographed is "Missing Page(s)". If it was possible to obtain the missing page(s) or section, they are spliced into the film along with adjacent pages. This may have necessitated cutting through an image and duplicating adjacent pages to assure complete continuity. 2. When an image on the film is obliterated with a round black mark, it is an indication of either blurred copy because of movement during exposure, duplicate copy, or copyrighted materials that should not have been filmed. -
When Lightning Strikes
2016 CASE STUDY 1 2 3 4 When Lightning Strikes Lightning is an electrical discharge in the atmosphere. Slow motion video allows scientists to study the build up, release, and dissipation of that discharge. When Lightning Strikes: Florida Institute of Technology Uses High Speed Imagery to Observe Lightning When you were a child, it’s likely your mother urged you to come inside during a storm, especially when there was lightning present. Every year the Earth experiences an average of 25 million lightning strikes during some 100,000 thunderstorms. This equates to more than 100 lightning bolts per second! A typical lightning strike travels at speeds of up to 60 miles per second, and the average length of a single lightning bolt measures between 2-3 miles and can commonly extend as far as 60 miles. A lightning bolt can reach a temperature of roughly 30,000 kelvins – or 53,540 degrees Fahrenheit – hotter than the surface of the sun. This makes lightning one of the most interesting, and dangerous, natural occurrences on our planet. No wonder your mother didn’t want you outside during a thunderstorm. By way of simple definition, lightning is a ‘brilliant electric spark discharge in the atmosphere, occurring within a thundercloud, between clouds, or between a cloud and the ground.’ Scientists around the globe have been studying the phenomena of lightning for decades to understand weather When it’s too fast to see and too important not to.® patterns. Recently, this feat has been made easier with the use of high speed imagery from Vision Research, as demonstrated by Dr. -
On the Plasma and Electrode Erosion Processes in Spark Discharge Nanoparticle Generators
On the plasma and electrode erosion processes in spark discharge nanoparticle generators Ph.D. Dissertation Attila Kohut Supervisor: Dr. Zsolt Geretovszky associate professor Doctoral School of Physics Department of Optics and Quantum Electronics Faculty of Science and Informatics University of Szeged Szeged 2017 Table of contents List of abbreviations ............................................................................................................................................. 4 1. Introduction ................................................................................................................................................... 5 1.1 Motivation and aims .......................................................................................................................... 5 1.2 Generation of nanoparticles .......................................................................................................... 7 1.3 The electric spark discharge ....................................................................................................... 11 1.3.1 Classification of gas discharges ........................................................................................ 11 1.3.2 Microsecond-long, atmospheric pressure oscillatory spark discharges ........ 13 1.4 Spark discharge nanoparticle generation ............................................................................. 16 1.4.1 General concept ..................................................................................................................... -
Plasma of Underwater Electric Discharges with Metal Vapors V.F
PLASMA OF UNDERWATER ELECTRIC DISCHARGES WITH METAL VAPORS V.F. Boretskij1, A.N. Veklich1, T.A. Tmenova1, Y. Cressault2, F. Valensi2, K.G. Lopatko3, Y.G. Aftandilyants3 1Taras Shevchenko National University of Kyiv, Kyiv, Ukraine; 2Universite Paul Sabatier, Toulouse, France; 3National University of Life and Environmental Sciences of Ukraine, Kyiv, Ukraine E-mail: [email protected]; [email protected]; [email protected] This paper deals with spectroscopy of underwater electric discharge plasma with. In particular, the focus is on configuration where the electrodes are immersed in liquid and its application in nanoscience and biotechnology. General overview of the experimental approach adopted by authors aiming to study the water-submerged electrical discharge plasma and effects of various parameters on its properties is described. The electron density was estimated on the base of spectral line broadening and shifting. PACS: 52.25.−b, 52.80.−s, 52.80.Wq INTRODUCTION components are typically studied in distinct fields of PLASMAS IN LIQUID research. Plasmas in liquid are becoming an increasingly PLASMA-LIQUID INTERACTIONS FOR important topic in the field of plasma science and NANOMATERIAL SYNTHESIS technology. In the last two decades, attention of research on the The focus of this paper, in particular, is directed interactions of plasmas with liquids has spread on a towards a relatively new branch of plasma research, variety of applications that include electrical switching nanomaterial synthesis through plasma–liquid [1], analytical chemistry [2], environmental remediation interactions, which has been developing rapidly, mainly [3, 4], sterilization and medical applications [5], etc. due to the various recently developed plasma sources These opportunities have challenged plasma community operating at low and atmospheric pressures. -
Prospects in Analytical Atomic Spectrometry
Russian Chemical Reviews 75 $4) 289 ± 302 $2006) Prospects in analytical atomic spectrometry AABol'shakov, AAGaneev, V M Nemets Contents I. Introduction 289 II. Atomic absorption spectrometry 290 III. Atomic emission spectrometry 292 IV. Atomic mass spectrometry 293 V. Atomic fluorescence spectrometry 295 VI. Atomic ionisation spectrometry 296 VII. Sample preparation and introduction, atomisation and data processing 298 VIII. Conclusion 298 Abstract. The trends in the development of five main branches of processing $averaging) of noise and enhances the analysis accu- atomic spectrometry, viz., absorption, emission, mass, fluores- racy due to the use of correlation models and neural network cence and ionisation spectrometry, are analysed. The advantages algorithms. and drawbacks of various techniques in atomic spectrometry are The development of analytical spectrometry and detection considered. Emphasised are the applications of analytical plasma- techniques is stimulated by the diverse and increasing demands in and laser-based methods. The problems and prospects in the industry, medicine, science, environmental control, forensic ana- development in respective fields of analytical instrumentation lysis, etc. The development of portable analysers for the determi- are discussed. The bibliography includes 279 references.references. nation of elements in different media at the immediate point of sampling, which eliminates the stages of collecting, transportation I. Introduction and storage of samples, is one of the most important directions. It should be noted that the development of atomic spectro- Analytical atomic spectrometry embraces a multitude of techni- metry slowed down in recent years; particularly, a trend towards a ques of elemental analysis that are based on the decomposition of decreasing number of scientific publications occurred. -
UNIT 10 ATOMIC EMISSION Spectrometry SPECTROMETRY
Atomic Emission UNIT 10 ATOMIC EMISSION Spectrometry SPECTROMETRY Structure 10.1 Introduction Objectives 10.2 Principle of Atomic Emission Spectrometry Atomic Emission Spectrometry using Plasma Sources 10.3 Plasma and its Characteristics Inductively Coupled Plasma Direct Current Plasma Microwave Induced Plasma Choice of Argon as Plasma Gas 10.4 Instrumentation for ICP-AES Sample Introduction Monochromators Detectors Processing and Readout Device 10.5 Types of instruments for ICP-AES Sequential Spectrometers Simultaneous Spectrometers 10.6 Analytical Methodology in ICP-AES Qualitative Analysis using ICP-AES Quantitative Analysis using ICP-AES 10.7 Interferences in ICP-AES Spectral Interferences Physical Interferences Chemical Interferences 10.8 Applications of ICP-AES 10.9 Summary 10.10 Terminal Questions 10.11 Answers 10.1 INTRODUCTION In Unit 9, you have learnt in detail about the underlying principles, instrumentation and applications of atomic absorption spectrophotometry (AAS). You would recall that in AAS the atomic vapours in the ground state absorb the characteristic radiation of the element and the absorbed radiation and its intensity form the basis for the qualitative and quantitative applications. In contrast to this, in the current unit we take up atomic emission spectrometry (AES) that concerns the emission of radiation by the suitably excited atomic vapours of the analyte. Here, the emitted radiation and its intensity form the basis for the qualitative and quantitative applications of the technique. AES is one of the oldest spectroscopic methods of analysis. It is a multi- element analytical technique that can be used for the analysis of materials in gaseous, liquid, powder or solid form. Its high detection power and wide variety of excitation sources makes it the most extensively used method for analysis. -
Analy&Cal(Methods( For(Environmental(Geochemistry(
LECTURE!2! Analy&cal(Methods( for(Environmental(Geochemistry( Determina&on(of(Elemental(Concentra&ons(( and(Natural(Isotopes(Abundances! LECTURE(2:(Arba(Minch,(Ethiopia,(Oct(15,(2014(( Overview(R(Analy&cal(Methods(( ! Basic(Terms((Defini&ons,(etc.)( ( ! Atomic(Spectroscopy( ( o Op&cal(Spectroscopy( !)!Atomic!absorp5on!spectroscopy!(AAS)! !)!Atomic!emission!spectroscopy!(AES)! !)!Induc5vely!coupled!plasma!atomic!emission!spectroscopy!(ICP!AES)! ! o Mass(Spectroscopy( ()!Mass!spectrometry!with!induc5vely!coupled!plasma! ()!Single!collector!mass!spectrometry! !)!Mul5collector!mass!spectrometry! ! o Data(Processing(R(Construc&on(of(Calibra&on(Curves( ! ! Isotope(Analysis( ()!TIMS!(Thermal!ionisa5on!mass!spectrometry)! !!!!!!!!!!!!!!!!!!!)!MC!ICP!MS!(Mul5collector!Induct.!Coupled!plasma!mass!spectrometry)! ( 2! Basic(Terms(( Instrumental(analysis!is#a#field#of#analy-cal#chemistry#that#inves-gates#analytes#using# scien-fic#(analy-cal)#instruments.# ! Instrument(is#an#equipment#capable#to#convert#a#specific#sample#property#to#analogue# (con-nuous)#or#digital#(discrete<-me)#response#or#signal,#which#is#then## compared#the#signal#or#response#of#a#specific#standard.# Sample(is#our#study#material#with#specific#characteris-cs#and#measureable#proper-es,# and#it#can#be#divided#into#analyte#and#sample#matrix.# ( Analyte(is#a#substance#or#chemical#cons-tuent#that#is#of#our#interest#in#an#analy-cal# procedure.## ( Matrix(the#rest#of#sample#composi-on#which#is#not#measured#but#must#be#monitored# due#to#effect#of#interference,#etc.# ( Interference!is#false#response#of#sample#matrix#being#read#as#an#analyte#signal.+ -
Plasma Physics and Technology 4(1):28–31, 2017 © Department of Physics, FEE CTU in Prague, 2017
doi:10.14311/ppt.2017.1.28 Plasma Physics and Technology 4(1):28–31, 2017 © Department of Physics, FEE CTU in Prague, 2017 PLASMA ASSISTED GENERATION OF MICRO- AND NANOPARTICLES A. Veklicha,∗, A. Lebida, T. Tmenovaa, V. Boretskija, Y. Cressaultb, F. Valensib, K. Lopatkoc, Y. Aftandilyantsc a Taras Shevchenko National University of Kyiv, 64/13, Volodymyrska str., Kyiv, Ukraine b Université de Toulouse; UPS, INPT; LAPLACE (Laboratoire Plasma et Conversion d’Energie); 118 route de Narbonne, F-31062 Toulouse Cedex 9, France c National University of Life and Environmental Sciences of Ukraine, Kiev, Ukraine ∗ [email protected] Abstract. In this research, the peculiarities of micro- and nanoparticles generation are considered. Two techniques of micro- and nanoparticles’ formation using electric arc and underwater discharge plasma sources are proposed. Molybdenum oxide crystals were deposited on side surface of the bottom electrode (anode) of the free-burning discharge between metallic molybdenum electrodes. Friable layer of MoO3, which consists of variously oriented transparent prisms and platelets (up to few hundreds of µm in size), was formed by vapor deposition around the electrode. In the second technique, plasma of the underwater electric spark discharges between metal granules was used to obtain stable colloidal solutions with nanoparticles of 20–100 nm sizes. Keywords: molybdenum trioxide, plasma evaporation, underwater spark discharge, colloidal liquids. 1. Introduction 2. Techniques of micro- and nanoparticles generation Plasma treatment of materials attracts strong interest due to extreme conditions of processes, which can’t be 2.1. Micro-structured molybdenum trioxide achieved in other way. Particularly, plasma technology crystal fabrication in electric arc plasma can be used for fabrication of materials structured on source micro- and nanoscale [1, 2].