2. the Growth and Decline of Cottonopolis
Total Page:16
File Type:pdf, Size:1020Kb
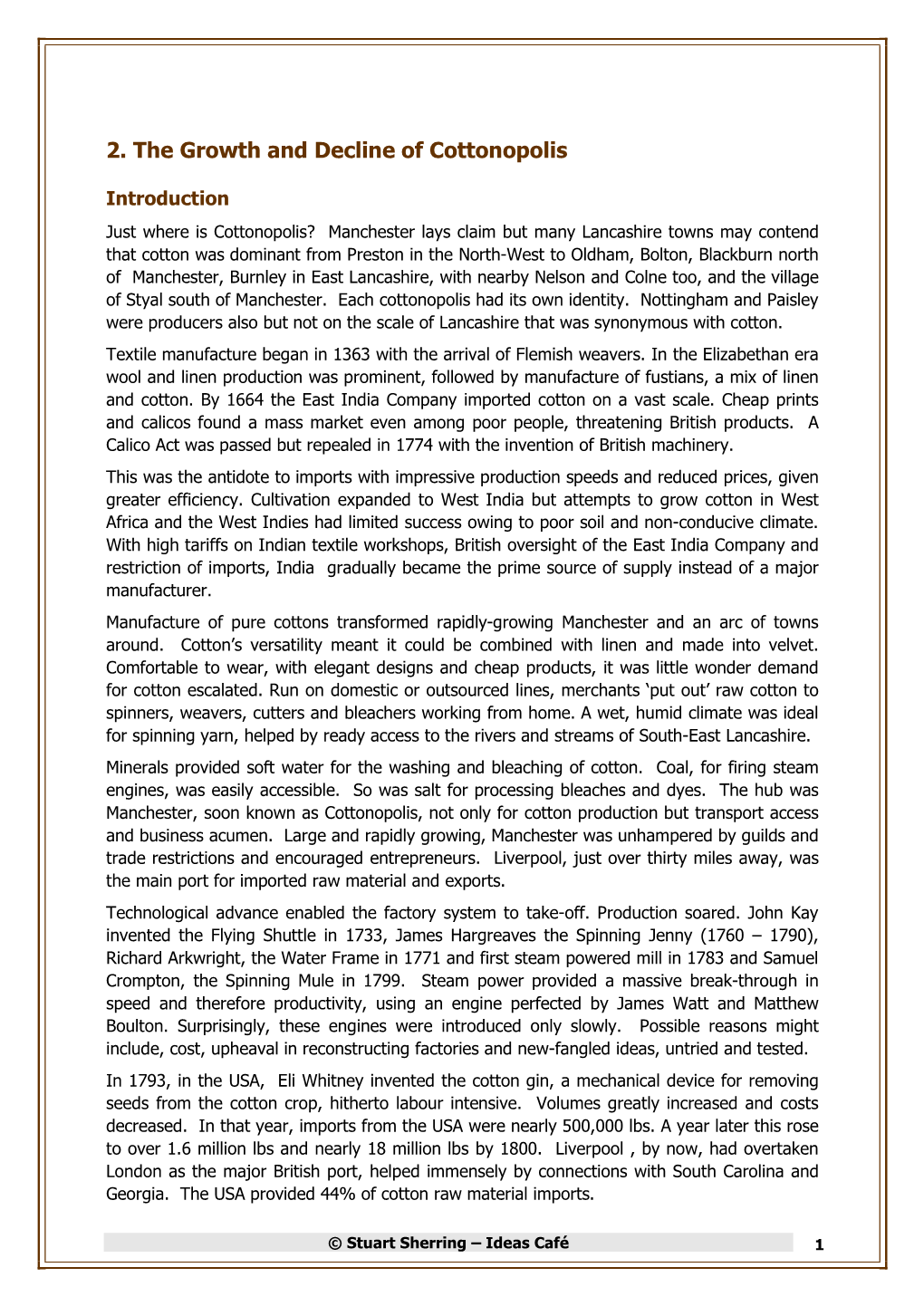
Load more
Recommended publications
-
Manchester Visitor Information What to See and Do in Manchester
Manchester Visitor Information What to see and do in Manchester Manchester is a city waiting to be discovered There is more to Manchester than meets the eye; it’s a city just waiting to be discovered. From superb shopping areas and exciting nightlife to a vibrant history and contrasting vistas, Manchester really has everything. It is a modern city that is Throw into the mix an dynamic, welcoming and impressive range of galleries energetic with stunning and museums (the majority architecture, fascinating of which offer free entry) and museums, award winning visitors are guaranteed to be attractions and a burgeoning stimulated and invigorated. restaurant and bar scene. Manchester has a compact Manchester is a hot-bed of and accessible city centre. cultural activity. From the All areas are within walking thriving and dominant music distance, but if you want scene which gave birth to to save energy, hop onto sons as diverse as Oasis and the Metrolink tram or jump the Halle Orchestra; to one of aboard the free Mettroshuttle the many world class festivals bus. and the rich sporting heritage. We hope you have a wonderful visit. Manchester History Manchester has a unique history and heritage from its early beginnings as the Roman Fort of ‘Mamucium’ [meaning breast-shape hill], to today’s reinvented vibrant and cosmopolitan city. Known as ‘King Cotton’ or ‘Cottonopolis’ during the 19th century, Manchester played a unique part in changing the world for future generations. The cotton and textile industry turned Manchester into the powerhouse of the Industrial Revolution. Leaders of commerce, science and technology, like John Dalton and Richard Arkwright, helped create a vibrant and thriving economy. -
From Manufacturing Industries to a Services Economy: the Emergence of a 'New Manchester' in the Nineteen Sixties
Introductory essay, Making Post-war Manchester: Visions of an Unmade City, May 2016 From Manufacturing Industries to a Services Economy: The Emergence of a ‘New Manchester’ in the Nineteen Sixties Martin Dodge, Department of Geography, University of Manchester Richard Brook, Manchester School of Architecture ‘Manchester is primarily an industrial city; it relies for its prosperity - more perhaps than any other town in the country - on full employment in local industries manufacturing for national and international markets.’ (Rowland Nicholas, 1945, City of Manchester Plan, p.97) ‘Between 1966 and 1972, one in three manual jobs in manufacturing were lost and one quarter of all factories and workshops closed. … Losses in manufacturing employment, however, were accompanied (although not replaced in the same numbers) by a growth in service occupations.’ (Alan Kidd, 2006, Manchester: A History, p.192) Economic Decline, Social Change, Demographic Shifts During the post-war decades Manchester went through the socially painful process of economic restructuring, switching from a labour market based primarily on manufacturing and engineering to one in which services sector employment dominated. While parts of Manchester’s economy were thriving from the late 1950s, having recovered from the deep austerity period after the War, with shipping trade into the docks at Salford buoyant and Trafford Park still a hive of activity, the ineluctable contraction of the cotton industry was a serious threat to the Manchester and regional textile economy. Despite efforts to stem the tide, the textile mills in 1 Manchester and especially in the surrounding satellite towns were closing with knock on effects on associated warehousing and distribution functions. -
Belper Mills Site
Belper North Mill Trust Outline masterplan for the renewal of the Belper Mills site February 2017 Belper North Mill Trust Outline masterplan for the renewal of the Belper Mills site Contents Page numbers 1 Introduction 1 2 Heritage significance 1 - 4 3 End uses 4 - 5 4 Development strategy 5 - 9 4.1 Phase 1 6 - 7 4.2 Phase 2 7 4.3 Phase 3 8 4.4 The end result 9 5 Costs of realisation 10 - 11 6 Potential financing – capital and revenue 11 - 15 6.1 Capital/realisation 11 - 12 6.2 Revenue sustainability 12 - 15 7 Delivery 15 - 16 Appendices 1 Purcell's Statement of Significance 2 Purcell's Feasibility Study Belper North Mill Trust Outline masterplan for the renewal of the Belper Mills site 1 Introduction As part of this phase of work for the Belper North Mill Trust we have, with Purcell Architects, carried out an outline masterplanning exercise for the whole Belper Mills site. At the outset, it is important to say that at the moment the site is privately owned and that while Amber Valley Borough Council initiated a Compulsory Purchase Order process in 2015, that process is still at a preliminary stage. This is a preliminary overview, based on the best available, but limited, information. In particular, access to the buildings on site has been limited; while a considerable amount of the North Mill is accessible because it is occupied, access to the East Mill, now empty, was not made available to us. Also, while we have undertaken some stakeholder consultation, we have not at this stage carried out wider consultation or public engagement, nor have we undertaken detailed market research, all of which would be essential to any next stage planning for the future of the site. -
Newsletter 39
77 ` DIARY DATES – (WHAT’S ON) LFHHS IRISH ANCESTRY GROUP The Gazette All meetings held at The LFHHS Resource Centre, 2 Straits, Oswaldtwistle. § www.lfhhs-pendleandburnley.org.uk Advice & Research Workshop Pendle & Burnley Saturday 14th August 2010, 1 pm to 4.30 pm Branch Issue 39 - July 2010 § Irish War Memorials Mike Coyle Saturday 9th October 2010, 1pm to 4.30pm Inside this Issue Archive Closures & News 14 LancashireBMD 3 Programme 3 § Advice & Research Workshop Diary Dates 2 Lancashire R.O. 15 Query Corner 18 Saturday 4th December 2010, 1 pm to 4.30 pm Federation News 15 Library 3 Society Resource Centre 2 Enquiries – Shaun O'Hara, 8 Liddington Close, Newfield Park, Blackburn, Heirs House, Colne 14 News from TNA 13 Society Special offer 3 BB2 3WP. e-mail: [email protected] Heritage Open Days List 18 Probate Records in 15 Sutcliffes of Pendleton 4 LFHHS CHORLEY BRANCH "Celebration of Family History" Nelson and areas around Astley Hall, Chorley PR7 1NP Saturday 7th August 2010 11am to 5 pm Admission Free HERITAGE OPEN DAYS 9th to 12th September 2010 THE NATIONAL FAMILY HISTORY FAIR Explore the heritage buildings in our area or even further afield – Barnoldswick, Newcastle Central Premier Inn, Newbridge St., Newcastle Upon Tyne, NE1 8BS Blackburn, Blackpool, Chorley, Fleetwood, Lancaster, Nelson, Ormskirk, Preston. Saturday 11th September 2010, 10am to 4pm See the website http://www.heritageopendays.org.uk/directory/county/Lancashire Admission £3, Children under 15 free for a list of many of the places that will be open. Examples in our area DONCASTER LOCAL HISTORY FAIR Queen Street Mill Textile Museum, Queen Street, Harle Syke, Burnley BB10 2HX Doncaster Museum and Art Gallery, Chequer Road, Doncaster, DN1 2AE open Sun 12th September, 12noon to 5pm Saturday, 18th September 2010, Gawthorpe Hall, Padiham open Sun 12th September, 1pm to 4.30pm 10am to 4pm St Mary's Church, Manchester Road, Nelson and Higherford Mill, Barrowford NORTH MEOLS (SOUTHPORT) FHS ANNUAL OPEN DAY open Thurs 9th September to Sunday 12th September 11am to 4 pm on all days. -
Dukinfield) OLD CHAPEL and the UN1 TA R I a N STORY
OLD CHAPEL AND THE UNITARIAN- - STORY (Dukinfield) OLD CHAPEL AND THE UN1 TA R I A N STORY DAVID C. DOEL UNITARIAN PUBLICATION Lindsey Press 1 Essex Street Strand London WC2R 3HY ISBN 0 853 19 049 6 Printed by Jervis Printers 78 Stockport Road Ashton-Under-Lyne Tameside CONTENTS PREFACE CHAPTER ONE: AN OLD CHAPEL HERITAGE TRAIL CHAPTER TWO: BIDDLE AND THE SOCINIANS CHAPTER THREE: THE CIVIL WAR CHAPTER FOUR: MILTON AND LOCKE CHAPTER FIVE: SAMUEL ANGIER AND HIS CONTEMPORARIES CHAPTER SIX: JOSEPH PRIESTLEY CHAPTER SEVEN: WILLIAM ELLERY CHANNING CHAPTER EIGHT: FIRST HALF OF THE NINETEENTH CENTURY CHAPTER NINE: HOPPS, MARTINEAU AND WICKSTEED CHAPTER TEN: FIRST HALF OF THE TWENTIETH CENTURY CHAPTER ELEVEN: SECOND HALF OF THE TWENTIETH CENTURY APPENDIX Ai WHERE THE STORY BEGINS APPENDIX B: THE TRINITY APPENDIX C: THE ALLEGORICAL METHOD APPENDIX D: BIBLIOGRAPHY APPENDIX E: GLOSSARY SIX ILLUSTRATIONS: a) Old Chapel exterior b) Old Chapel interior c) The original Chapel d) The Old School e) The New School f) The Original Schoc! OLD CHAPEL, DUKlNFlELD PREFACE Old Testament prophets, or was he a unique expression, once and once only, of God on earth in human form? OLD CHAPEL AND THE UNITARIAN STORY is an account of the life and history of Old Chapel, Dukinfield, set within the As I point out in the Appendix on The Trinity, there emerged larger context of the story of the growth and devlopment of from all this conflict not one doctrine of the Trinity, but many. Unitarianism, which we, the present congregation, inherit from the trials and tribulations, the courage, vision and the joy The Trinity is a theological model for expressing the Nature of of our ancestors. -
Industrialism, Androids, and the Virtuoso Instrumentalist
UNIVERSITY OF CALIFORNIA Los Angeles Performing the Mechanical: Industrialism, Androids, and the Virtuoso Instrumentalist A dissertation submitted in partial satisfaction of the requirements for the degree Doctor of Musical Arts by Leila Mintaha Nassar-Fredell 2013 © Copyright by Leila Mintaha Nassar-Fredell 2013 ABSTRACT OF THE DISSERTATION Performing the Mechanical: Industrialism, Androids, and the Virtuoso Instrumentalist by Leila Nassar-Fredell Doctor of Musical Arts University of California, Los Angeles, 2013 Professor Robert S. Winter, Chair Transactions between musical androids and actual virtuosos occupied a prominent place in the music of the eighteenth and nineteenth centuries. Instrumentalists and composers of instrumental music appropriated the craze for clockwork soloists, placing music in a position of increased social power in a society undergoing rapid technological transformation. The history of musical automata stretches back to antiquity. Androids and automata, vested by audiences with spiritual and magical qualities, populated the churches of the broader populations and the Renaissance grottos of the aristocracy. As ii the Industrial Revolution began, automata increasingly resembled the machines changing the structure of labor; consequently, androids lost their enchanted status. Contemporary writers problematized these humanoid machines while at the same time popularizing their role as representatives of the uncanny at the boundaries of human identity. Both instrumental performers and androids explored the liminal area between human and machine. As androids lost their magic, musical virtuosos assumed the qualities of spectacle and spirituality long embodied by their machine counterparts. In this process virtuosi explored the liminal space of human machines: a human playing a musical instrument (a machine) weds the body to a machine, creating a half-human, half-fabricated voice. -
A Special and Unusual Loom Frame from the First Half of the Nine
FINDING THE THREAD RESTORATION OF A PROFESSIONAL WEAVER'S LOOM Rabbit Goody A special and unusual loom frame from the first half of the nine teenth century now in the collection of the Ontario Agricultural Mu seum, Milton, Ontario,1 has provided an opportunity to examine some of the specialized equipment used by weavers in the nineteenth century to weave cloth with speed, intricate geometric patterns, and/or accommodate longer lengths of cloth. Surviving examples of cloth have made it apparent that trained weavers, weaving fancy cloth during the nineteenth century were using more complex equipment than that commonly associated with home textile produc tion. However, until now surviving examples of the equipment have been scarce. The museum's loom is one of a small number that can be linked to the production of the more complex cloths of this pe riod. At least, it has specialized equipment which professional weavers might choose to place on their looms. It is the most com plete example currently known. In their book, "Keep Me Warm One Night", Dorothy and Harold Burnham have identified this loom as being a professional weaver's loom because of its specialized features.2 It is being restored for the purpose of reproducing some of the more intricate cloth woven by professional weavers in the Niagara Peninsula. The survival of this loom frame, with its special features, has made it possible to set certain criteria for identifying other looms used by professionals and to corroborate the descrip tions of equipment and methods found in publications and manuscripts from the last half of the eighteenth century and early nineteenth century used to weave fancy cloth rapidly by profes sionals. -
7. Industrial and Modern Resource
Chapter 7: Industrial Period Resource Assessment Chapter 7 The Industrial and Modern Period Resource Assessment by Robina McNeil and Richard Newman With contributions by Mark Brennand, Eleanor Casella, Bernard Champness, CBA North West Industrial Archaeology Panel, David Cranstone, Peter Davey, Chris Dunn, Andrew Fielding, David George, Elizabeth Huckerby, Christine Longworth, Ian Miller, Mike Morris, Michael Nevell, Caron Newman, North West Medieval Pottery Research Group, Sue Stallibrass, Ruth Hurst Vose, Kevin Wilde, Ian Whyte and Sarah Woodcock. Introduction Implicit in any archaeological study of this period is the need to balance the archaeological investigation The cultural developments of the 16th and 17th centu- of material culture with many other disciplines that ries laid the foundations for the radical changes to bear on our understanding of the recent past. The society and the environment that commenced in the wealth of archive and documentary sources available 18th century. The world’s first Industrial Revolution for constructing historical narratives in the Post- produced unprecedented social and environmental Medieval period offer rich opportunities for cross- change and North West England was at the epicentre disciplinary working. At the same time historical ar- of the resultant transformation. Foremost amongst chaeology is increasingly in the foreground of new these changes was a radical development of the com- theoretical approaches (Nevell 2006) that bring to- munications infrastructure, including wholly new gether economic and sociological analysis, anthropol- forms of transportation (Fig 7.1), the growth of exist- ogy and geography. ing manufacturing and trading towns and the crea- tion of new ones. The period saw the emergence of Environment Liverpool as an international port and trading me- tropolis, while Manchester grew as a powerhouse for The 18th to 20th centuries witnessed widespread innovation in production, manufacture and transpor- changes within the landscape of the North West, and tation. -
Prices and Profits in Cotton Textiles During the Industrial Revolution C
PRICES AND PROFITS IN COTTON TEXTILES DURING THE INDUSTRIAL REVOLUTION C. Knick Harley PRICES AND PROFITS IN COTTON TEXTILES DURING THE 1 INDUSTRIAL REVOLUTION C. Knick Harley Department of Economics and St. Antony’s College University of Oxford Oxford OX2 6JF UK <[email protected]> Abstract Cotton textile firms led the development of machinery-based industrialization in the Industrial Revolution. This paper presents price and profits data extracted from the accounting records of three cotton firms between the 1770s and the 1820s. The course of prices and profits in cotton textiles illumine the nature of the economic processes at work. Some historians have seen the Industrial Revolution as a Schumpeterian process in which discontinuous technological change created large profits for innovators and succeeding decades were characterized by slow diffusion. Technological secrecy and imperfect capital markets limited expansion of use of the new technology and output expanded as profits were reinvested until eventually the new technology dominated. The evidence here supports a more equilibrium view which the industry expanded rapidly and prices fell in response to technological change. Price and profit evidence indicates that expansion of the industry had led to dramatic price declines by the 1780s and there is no evidence of super profits thereafter. Keywords: Industrial Revolution, cotton textiles, prices, profits. JEL Classification Codes: N63, N83 1 I would like to thank Christine Bies provided able research assistance, participants in the session on cotton textiles for the XII Congress of the International Economic Conference in Madrid, seminars at Cambridge and Oxford and Dr Tim Leung for useful comments. -
895 Bus Time Schedule & Line Route
895 bus time schedule & line map 895 Dill Hall View In Website Mode The 895 bus line (Dill Hall) has 2 routes. For regular weekdays, their operation hours are: (1) Dill Hall: 7:25 AM (2) Lane Bottom: 3:25 PM Use the Moovit App to ƒnd the closest 895 bus station near you and ƒnd out when is the next 895 bus arriving. Direction: Dill Hall 895 bus Time Schedule 63 stops Dill Hall Route Timetable: VIEW LINE SCHEDULE Sunday Not Operational Monday 7:25 AM Stirling Court, Lane Bottom Tuesday 7:25 AM Sun Inn, Haggate Wednesday 7:25 AM Turning Circle, Harle Syke Thursday 7:25 AM Queen Street, Harle Syke Friday 7:25 AM Burnley Road, Burnley Saturday Not Operational Granville Street, Harle Syke Parker Street, Burnley Moorview Close, Harle Syke Briercliffe Road, Burnley 895 bus Info Direction: Dill Hall Craven Heifer, Harle Syke Stops: 63 Trip Duration: 75 min Red Spar Road, Kibble Bank Line Summary: Stirling Court, Lane Bottom, Sun Inn, Haggate, Turning Circle, Harle Syke, Queen Street, Clock House Court, Kibble Bank Harle Syke, Granville Street, Harle Syke, Moorview Hillingdon Road, Burnley Close, Harle Syke, Craven Heifer, Harle Syke, Red Spar Road, Kibble Bank, Clock House Court, Kibble Bank, Beckenham Court, Reedley Beckenham Court, Reedley, Longridge Heath, Kibble Beckenham Court, Burnley Bank, Hillingdon Roadd Jct, Kibble Bank, Kibble Crescent, Lane Head, Underley Street, Lane Head, Longridge Heath, Kibble Bank Lytham Road, Lane Head, Casterton Avenue, Lane Chislehurst Grove, Burnley Head, Burnley General Hospital, Browhead, Haydock Street, -
The London Gazette, Hth April 1989
4492 THE LONDON GAZETTE, HTH APRIL 1989 Clifton Street, north side, from a point 50 metres west of Sandygate, Burnley Talbot Square to a point 20 metres west of Abingdon Street. Saunder Bank, Burnley Town Hall Perimeter, Padiham A copy of the Order, which will come into operation on 24th April Widow Hill Road, Burnley 1989, and a map showing the roads affected may be inspected during normal office hours at the address below. SCHEDULE 2 Any person who desires to question the validity of the Order or of any provision contained in it on the grounds that it is not within the Proposed Waiting Restrictions powers conferred by the Road Traffic Regulation Act 1984 or on the Back Burnley Road, Padiham grounds that any requirement of the Act or any regulation made Brennand Street, Burnley under it has not been complied with in relation to the Order, may Briercliffe Road, Burnley within 6 weeks from the date of this notice apply to the High Court Brougham Street, Burnley for this purpose. Brownside Road, Burnley D. Wardman, Chief Executive Burleigh Street, Burnley P.O. Box 77, Town Hall. Burnley Road, Harle Syke, Burnley Clifton Road, Burnley 14th April 1989. (533) Colne Road, Burnley Croft Street, Burnley Eastern Avenue, Burnley BURNLEY BOROUGH COUNCIL Elizabeth Street, Burnley Finsley Gate, Burnley The Lancashire County Council (Borough of Burnley) ( Various Free Trade Street, Burnley Roads) (Prohibition and Restriction of Waiting, etc.) Order 1989 Griffin Close, Burnley Notice is hereby given that the Burnley Borough Council, as agent Hammerton -
Cottonopolis
1 Greater Manchester U3A Network Toolbox 2 Introduction This pack had its origin in the U3A’s greater focus on research by member U3As as a learning activity, as well as a joint project between the GMU3A network and Manchester University ‘Cottonopolis’ was chosen as a uniting theme for this initiative as it summarises the huge impact that the sudden industrial growth of Manchester had on all aspects of society. What you will find in this resource pack is a set of notes organised by theme under the over-arching topic of 'Cottonopolis'. They are intended to help participating U3As of the Greater Manchester U3A Network assess what they might be able to contribute, either as individuals or as groups within their respective U3As, to co-ordinated research as a learning activity which may eventually benefit from a negotiated partnership with the University of Manchester. The themes and associated notes provided here are intended to be suggestive rather than prescriptive. They should be seen as starting points for the dissemination of ideas or as catalysts for further investigation. Hopefully they will allow interested third-agers to claim a stake in an exciting project which seeks to take advantage of our unique geographical location in the world's first industrial city. The notes in this pack do not yet address all aspects of the topic outlined in the diagram of 'the Cottonopolis Effect' on page 4. Please feel free to compile equivalent notes for any topic which still needs developing within your own fields of interest. Tony Pearson, October