The Corrosive Effect of Soldering Fluxes and Handling on Some
Total Page:16
File Type:pdf, Size:1020Kb
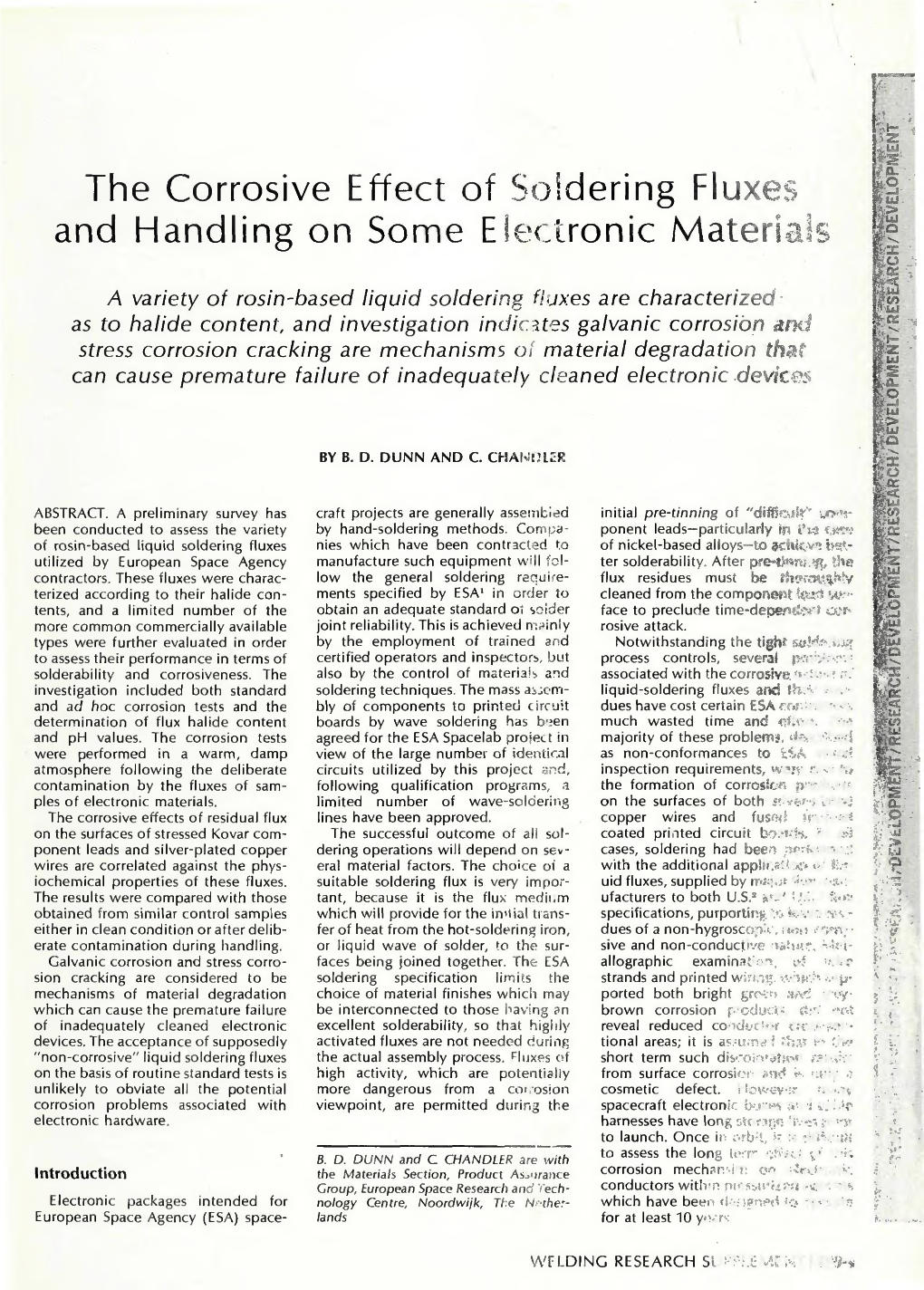
Load more
Recommended publications
-
MIL-STD-202G METHOD 208H SOLDERABILITY 1. PURPOSE. the Purpose of This Test Method Is to Determine the Solderability of All
MIL-STD-202G METHOD 208H SOLDERABILITY 1. PURPOSE. The purpose of this test method is to determine the solderability of all terminations which are normally joined by a soldering operation. This determination is made on the basis of the ability of these terminations to be wetted by solder and the predictability of a suitable fillet resulting from solder application. These procedures will verify that the pre-assembly lead finish provides a solderable surface of sufficient quality to enable satisfactory soldering. 2. PROCEDURE. The solderability test shall be performed in accordance with ANSI/J-STD-002 “Solderabiilty Tests for Component Leads, Terminations, Lugs, Terminals and Wires” and herein. The following details and exceptions shall apply: 2.1 Contractual agreements. The contractual agreements statement in ANSI/J-STD-002 shall not apply. Any exceptions to the requirements specified in ANSI/J-STD-002 and this test method shall be documented in the individual military procurement document or approved by the procuring military activity. 2.2 Coating durability. The coating durability category (from ANSI/J-STD-002) shall be as follows: a. Category 2 - for stranded wire (1 hour ±5 minutes steam aging with insulation removed). b. Category 3 - for all other components (8 hours ±15 minutes steam aging). 2.3 Test method. The test method used (from ANSI/J-STD-002) shall be as follows: a. Test A - for through-hole mount and surface mount leaded components, solid wire less than .045 inch diameter and stranded wire 18 AWG or smaller. If not otherwise specified in the procurement document, angle of immersion for surface mount leaded components shall be 90°. -
Scientific and Technical Report 2001 Volume VI Large Research Facilities
PAUL SCHERRER INSTITUT ISSN 1423-7350 March 2002 Scientific and Technical Report 2001 Volume VI Large Research Facilities ed. by: Renate Bercher, Carmen Büchli, Lotty Zumkeller CH-5232 Villigen PSI Switzerland Phone: 056/310 21 11 Telefax: 056/31021 99 http://www.psi.ch I TABLE OF CONTENTS Foreword l Accelerator Physics and Development Operation of the PSI-accelerator facility in 2001 5 Progress in the production of the new ring cyclotron cavity 7 Coupled field analysis of the new ring cyclotron cavity 9 Experimental upgrade of the injector II150 MHz RF system 11 Replacement of magnet power supplies, control and field-bus for the PSI cyclotron accelerators 13 Investigations on discharges of high voltage devices based on a transient recorder program 15 Test of a radio-frequency-driven mulitcusp proton source 16 Emittance measurements at the PSI ECR heavy ion source 17 Profile measurement of scanning proton beam for LiSoR using carbon fibre harps 18 A fast dégrader to set the energies for the application of the depth dose in proton therapy 20 MAD9P a parallel 3D particle tracker with space charge 22 Behaviour of the different poisson solvers in the light of beam dynamics simulations 24 Computational electrodynamics on the LINUX-cluster 26 Particle ray-tracing program TRACK applied to accelerators 27 Experimental Facilities Rebuilt beam line section between the targets M and E 31 Disposal preparation for meson production targets 33 A novel method to improve the safety of the planned MEGAPIE target at SINQ 34 Beamline adaptation for the MEGAPIE-target -
Outside Diameter Initiated Stress Corrosion Cracking Revised Final White Paper", Developed by AREVA and Westinghouse Under PWROG Program PA-MSC-0474
Program Management Office PWROG 102 Addison Road Connecticut 06095 q .Windsor, ko'ners-- PA-MSC-0474 Project Number 694 October 14, 2010 OG-10-354 U.S. Nuclear Regulatory Commission Document Control Desk Washington, DC 20555-0001 Subject: PWR Owners Group For Information Only - Outside Diameter Initiated Stress Corrosion Crackin2 Revised Final White Paper, PA-MSC-0474 This letter transmits two (2) non-proprietary copies of PWROG document "Outside Diameter Initiated Stress Corrosion Cracking Revised Final White Paper", developed by AREVA and Westinghouse under PWROG program PA-MSC-0474. This document is being submitted for information only. No safety evaluation (SE) is expected and therefore, no review fees should be incurred. This white paper summarizes the recent occurrences of ODSCC of stainless steel piping identified at Callaway, Wolf Creek and SONGS. Available operating experience (OE) at units that have observed similar phenomena is summarized as well to give a better understanding of the issue. Each of the key factors that contribute to ODSCC was considered along with the reported operating experience to perform a preliminary assessment of areas that may be susceptible to ODSCC. Also a qualitative evaluation was performed to determine whether ODSCC of stainless steel piping represents an immediate safety concern. This white paper is meant to address the issue of ODSCC of stainless steel systems for the near term. I&E guidelines are currently being developed through the PWROG to provide long term guidance. Correspondence related to this transmittal should be addressed to: Mr. W. Anthony Nowinowski, Manager Owners Group, Program Management Office Westinghouse Electric Company 1000 Westinghouse Drive, Suite 380 Cranberry Township, PA 16066 U.S. -
Footnotes for ATOMIC ADVENTURES
Footnotes for ATOMIC ADVENTURES Secret Islands, Forgotten N-Rays, and Isotopic Murder - A Journey into the Wild World of Nuclear Science By James Mahaffey While writing ATOMIC ADVENTURES, I tried to be careful not to venture off into subplots, however interesting they seemed to me, and keep the story flowing and progressing at the right tempo. Some subjects were too fascinating to leave alone, and there were bits of further information that I just could not abandon. The result is many footnotes at the bottom of pages, available to the reader to absorb at his or her discretion. To get the full load of information from this book, one needs to read the footnotes. Some may seem trivia, but some are clarifying and instructive. This scheme works adequately for a printed book, but not so well with an otherwise expertly read audio version. Some footnotes are short enough to be inserted into the audio stream, but some are a rambling half page of dense information. I was very pleased when Blackstone Audio agreed wholeheartedly that we needed to include all of my footnotes in this version of ATOMIC ADVENTURES, and we came up with this added feature: All 231 footnotes in this included text, plus all the photos and explanatory diagrams that were included in the text. I hope you enjoy reading some footnotes while listening to Keith Sellon-Wright tell the stories in ATOMIC ADVENTURES. James Mahaffey April 2017 2 Author’s Note Stories Told at Night around the Glow of the Reactor Always striving to beat the Atlanta Theater over on Edgewood Avenue, the Forsyth Theater was pleased to snag a one-week engagement of the world famous Harry Houdini, extraordinary magician and escape artist, starting April 19, 1915.1 It was issued an operating license, no. -
Forms of Corrosion Uniform Corrosion
Chapter 4 Forms of corrosion Uniform corrosion In such type of corrosion there is a uniform decrease in the volume of the metal due to direct contact with the surrounding environment. Examples Dissolvation of Zn, Al metal in acids and Pb metal in base. Atmospheric corrosion Atmospheric corrosion take place due to direct contact between metal and atmosphere Types of atmosphere: Gas type: contain mainly oxygen gas( 23% W / W) and water vapor. Liquid type: contain mainly water and dissolved oxygen. iron rust Atmospheric corrosion involve formation of metal oxide layer when metal in direct contact with its surrounding environment. Example: Formation of iron rust due to contact with air Fe + air, H2O Fe(OH)2 Fe2O3 Fe2O3 .3H2O is Iron rust (reddish brown ppt.) Oxide layers Protective Non Protective Non active active Non porous porous Ex: Zn, Al, Ni Ex: iron rust Rate of atmospheric corrosion depends on Nature of metal or alloy. Nature of oxide layer. Factors affecting atmospheric corrosion: Type of metal or alloy. Type of atmosphere (dust, humidity, pollutant. Water vapor, gases,…) Temperature( as T increase as rate increase) Time: The extent of corrosion increases with increased time Surface Condition: more roughness, more corrosion The presence of foreign matter influence the speed of corrosion PLAY ACTIVE FIGURE Galvanic corrosion Take place due to the contact between bimetallic couple exposed to the same environment due to the potential difference. Mechanism of galvanic corrosion: For two different metals M1 and M2 when exposed to the same corrosive environment, if M1 is more active than M2 M1 M2 Anodic reaction: M M n+ + ne- (n=1, 2, 3, …) Anodic metal will be corroded. -
STAINLESS STEEL Flux Coated
U.S. ALLOY CO. STAINLESS STEEL dba Washington Alloy 7010-G Reames Rd. Charlotte, NC 28216 Flux Coated Tig www.weldingwire.com Quality Management System in accordance with ISO 9001:2000 Cert # 05-R0925 ALLOY DESCRIPTION AND APPLICATION; These flux coated rods are primarily used for the root pass on piping where backing and purging gas may not be possible or desirable. This 39” rod should be used as a basic tig rod on DCEN, however caution is advised due to the easily removable slag covering that must be removed prior to addition welding. TYPICAL GTAW WELDING PROCEDURES; DCEN Wire Diameter Amps Volts 5/64” 90-180 12-13 3/32” 150-250 12-13 1/8” 200-375 12-14 Procedures may vary with change in position, base metals, filler metals, equipment and other changes. TYPICAL UNDILUTED METAL CHEMISTRY (%) per AWS A5.22; Chemistry Grade 1) Intended Use C Cr Ni Mo R308L 0.03 18.0-21.0 9.0-11.0 0.50 Welding of 18Cr & 8Ni such as 304, 304L R308H3) 0.04-0.08 19.5-22.0 9.0-11.0 0.50 Welding of 18Cr & 8Ni such as 304, 304H R309L 0.03 22.0-25.0 12.0-14.0 0.50 Welding of carbon steel to austenitic stainless R316L 0.03 17.0-20.0 11.0-14.0 2.0-3.0 Primarily use on 316 or 316L R347 2) 0.08 18.0-21.0 9.0-11.0 0.50 Primarily use on 347 1) All grades has the following : Mn=0.50-2.5, Si=1.2, P=0.04, S=0.03 Cu=0.50 Single values are maximum 2) R347 also has Cb+Ta =8xCmin. -
Introduction to Corrosion Your Friendly TSC Corrosion Staff
Introduction to Corrosion Your Friendly TSC Corrosion Staff: Daryl Little Ph.D. Materials Science & Engineering [email protected] 303-445-2384 Lee Sears Ph.D. Materials Science & Engineering [email protected] 303-445-2392 Jessica Torrey Ph.D. Materials Science & Engineering [email protected] 303-445-2376 Roger Turcotte, PE, CPS Materials Engineer [email protected] 303-445-2383 What is Corrosion? CORROSION IS DEFINED AS THE DETERIORATION OF A MATERIAL AND/OR ITS PROPERTIES CAUSED BY A REACTION WITH ITS ENVIRONMENT. Why is Corrosion a Major Concern? First and Most Important- Public Safety! • June 28, 1983: Mianus River Bridge, Greenwich, CT (TIME photo archive) • Northbound 3-lane section of I-95 bridge collapsed, killing 3 people • “Pin and Hanger” design was compromised when pin was displaced due to extensive corrosion of load-bearing components, amplified by salt from road maintenance. • Inadequate maintenance procedures were also cited as a contributing factor. • Subsequent to this failure, extensive inspections were conducted on this type of bridge across the country, and design modification were made to prevent catastrophic failures of this kind. First and Most Important- Public Safety! • April 28,1988, Aloha Airlines 737 Accident • 18 feet of cabin skin ripped off, resulting in the death of a flight attendant and many injuries • Attributed to corrosion fatigue Reclamation Case Study- Folsom Dam • Spillway gate No. 3 was damaged beyond repair, but no flooding occurred. • Replacement of No. 3 and repair of other gates cost ~$20 million and required 40% drainage of reservoir • Cause of failure: Increasing corrosion at the trunnion pin-hub interface raised the coefficient of friction and, therefore, the bending stress in the strut and the axial force in the brace exceeded limits. -
Stainless Steel Selection Guide
TAContentsBLE OF Discovery of Stainless Steel . .page 2 What is Stainless Steel . .page 3 Stainless Steel Classifications . .page 4 • Austenitic . .page 4 • Ferritic . .page 5 • Duplex . .page 5 • Martensitic . .page 6 • Precipitation Hardening . .page 6 Nickel Based Alloys . .page 7 Strength & Heat Treatment . .page 7 The Basics of Corrosion . .page 8 • General or Uniform Corrosion . .page 9 • Galvanic Corrosion . .page 11 • Pitting Corrosion . .page 11 • Crevice Corrosion . .page 13 • Intergranular Corrosion . .page 14 • Stress Corrosion Cracking . .page 15 • Microbiologically Influence Corrosion . .page 17 Welding Stainless Steel . .page 18 Alloy Selection . .page 22 Wrought Stainless Steel Composition . .page 24 Wrought Nickel Alloy Composition . .page 25 Stainless Steel and Nickel Alloy Filler Metal . .page 26 PR“It’sEF stainlessAC steel,E it shouldn’t rust” This is often the kind of statements heard from individuals when discussing a failure of process piping or equipment. This is also an indication of how little is actually understood about stainless steel and the applications where it is used. For years the food, beverage and pharmaceutical industries have used stainless steels in their process piping systems. Most of the time stainless steel components provide satisfactory results. Occasionally a catastrophic failure will occur. The purpose of the information contained within this document is to bring an understanding to stainless steel, it’s uses, and why it will fail under certain conditions. In the following pages we will discuss the different classes of stainless steel, heat treatment, corrosion, welding, and finally material selection. As with any failure, it is imperative the cause of the failure be identified before a proper fix can be recognized. -
Gold Embrittlement of Solder Joints 2018.Pages
Gold Embrittlement of Solder Joints Ed Hare, PhD - SEM Lab, Inc 425.335.4400 [email protected] Introduction Gold embrittlement of solder joints has been written about for at least four decades [1 – 3]. Nevertheless, gold embrittlement related solder joint failures have been analyzed in this laboratory as recently as July 2009. Gold embrittlement can be avoided by careful solder joint design and knowledge of the causes of this condition. The purpose of this paper is to provide a detailed account of material and process parameters that can lead to gold embrittlement in electronic assemblies. There are a variety of reasons that designers might want to solder to gold or gold plating. One reason is that some designs involve wire bonding and soldering operations on the same assembly. Another reason would be to include gold contact pads (e.g. for dome keypad contacts) or card edge contacts (e.g. PC cards). The wire bond pads or contact pads can be selectively gold plated, but the selective plating process can be expensive. The electronics industry currently recognizes a threshold level for gold that can be dissolved into eutectic tin-lead solder above which the solder is likely to become embrittled. This threshold is ~ 3 wt% gold. It will be shown in the paragraphs below that embrittlement of solder joints can develop at significantly lower bulk gold concentrations. Metallurgical Description of Gold Embrittlement The most important soldering alloy in the electronics industry is the eutectic tin-lead alloy, 63%Sn – 37%Pb. This may change in the near future as lead-free soldering takes its hold on the industry. -
General Purpose Liquid Soldering Flux
Weldcote Metals 842 Oak Grove Rd. Kings Mountain, NC 28086 704-739-4115 www.weldcotemetals.com WELDCOTE GENERAL PURPOSE LIQUID SOLDERING FLUX General Purpose Liquid Soldering Flux Formulated for soldering Stainless Steel and High-Chrome Alloys. Excellent across a broad range of base metals, solders, and temperatures. Exhibits excellent capillary action. DESCRIPTION Weldcote Liquid Soldering Flux is a water-based, general purpose, inorganic-acid flux formulated for soldering stainless steel and other industrial metals. The flux contains Zinc Chloride, Ammonium Chloride, and Hydrochloric Acid, that make this flux active at room temperature where it begins to clean metals and remove oxides. The flux exerts a strong scavenging action to remove oxide coatings and other impurities from the metal surface to produce strong joints. Pre-cleaning is not necessary under most conditions. APPLICATIONS Weldcote Liquid Soldering Flux is excellent for use on Stainless Steel, Monel, High-Chrome Alloys, Inconel, Nickel, Copper, Brass, Ferrous Alloys and many more metals. It is not recommended for Aluminum and Magnesium. DIRECTIONS Weldcote Liquid Soldering Flux may be applied with a brush, swab or by dipping. The flux exhibits the best activity between 93°C/200°F and 315°C/600°F. Post-solder residues are water-soluble and hot water rinses (140°F or higher) may be adequate for most applications. The following steps are recommended for optimum soldering results: • Remove any oil, grease, or other contaminants from the surface to be soldered. • Apply flux to joint by dipping, spraying, dragging, swabbing or brushing to area being soldered. • Preheat or air-dry area to be soldered after flux has been applied to activate the flux and yield optimum soldering characteristics and reduce or eliminate spattering. -
FTC Guideline - Title 16, Commercial Practices Part 23 for Gold Plating Over Sterling Silver Jewelery
Reference: FTC guideline - Title 16, commercial practices part 23 for gold plating over sterling silver Jewelery Dear Sir, My concern is on low K gold plating (10/14/18) over sterling silver. As per me, gold plating on silver Jewellery should be done only with > 23K. Following are the reasons to support my recommendation: REASONS TO AVOID LOW K GOLD PLATING • In low karat gold micron electroplating, we have to use either Au/Cu or Au/Ag chemistry. Au/Cu chemistry plating color for 14K is too pink (5N) & Au/Ag chemistry plating color is too green. We have to give top coat of 0.1 micron of high karat gold (>23K) to achieve Hamilton color (1N/2N) over low karat gold plating. • Doing low karat gold plating & cover it with nominal high karat gold for color, deficit the purpose of gold plated Jewellery. If the top flash gold will wear out then actual gold alloy color (pink/green) will expose (pink/green) which will tarnish too fast. • Achieving exact K (10/14/18) in low K electroplating is practically not possible. • We cannot identify gold purity of plating thickness on sterling silver by XRF because there are common elements present in plating thickness & base (e.g. Ag,Cu..). • Gold alloy (10/14/18) thickness testing is not possible by XRF because standards available for thickness calibration are in 24K. It is impossible to make 10/14/18 K standards as per plating compositions (Au/Cu & Au/Ag) because it cannot be fabricated. Thickness measurement of low K on XRF is manipulated method, where instrument detects pure gold ions throughout the plating layer & then by density calculation it will be converted into low K plating thickness(e.g.- 14 K density is 13 g/cc & pure gold is 19.3 g/cc. -
Soldering and Brazing of Copper and Copper Alloys Contents
Soldering and brazing of copper and copper alloys Contents 1. Introduction 4 5. Quality assurance 47 2. Material engineering fundamentals 9 6. Case studies 48 2.1. Fundamentals of copper and copper alloys 9 6.1 Hot-air solder levelling of printed circuit boards 48 2.2 Filler materials 10 6.2 Strip tinning 49 2.2.1 Soft solder 11 6.3 Fabricating heat exchangers from copper 49 2.2.2 Brazing filler metals 13 6.4 Manufacture of compact high-performance 2.3 Soldering or brazing pure copper 16 radiators from copper 49 2.4 Soldering / brazing copper alloys 18 2.4.1 Low-alloyed copper alloys 18 7. Terminology 50 2.4.2. High-alloyed copper alloys 22 8. Appendix 51 3. Design suitability for soldering/brazing 26 References 57 4. Soldering and brazing methods 29 Index of figures 58 4.1 The soldering/brazing principle 29 4.2 Surface preparation 30 Index of tables 59 4.3 Surface activation 32 4.3.1 Fluxes 33 4.3.2 Protective atmosphere / Shielding gases 35 4.4 Applying the solder or brazing filler metal 36 4.5. Soldering and brazing techniques 37 4.5.1 Soldering with soldering iron 38 4.5.2 Dip bath soldering or brazing 38 4.5.3 Flame soldering or brazing 40 4.5.4 Furnace soldering or brazing 40 4.5.5 Electric resistance soldering or brazing 43 4.5.6 Induction soldering or brazing 44 4.5.7 Electron beam brazing 45 4.5.8 Arc brazing 45 4.5.9 Laser beam soldering or brazing 46 2 | KUPFERINSTITUT.DE List of abbreviations Abbreviations Nd:YAG laser Neodymium-doped yttrium aluminium garnet laser SMD Surface-mounted device PVD Physical vapour deposition RoHS