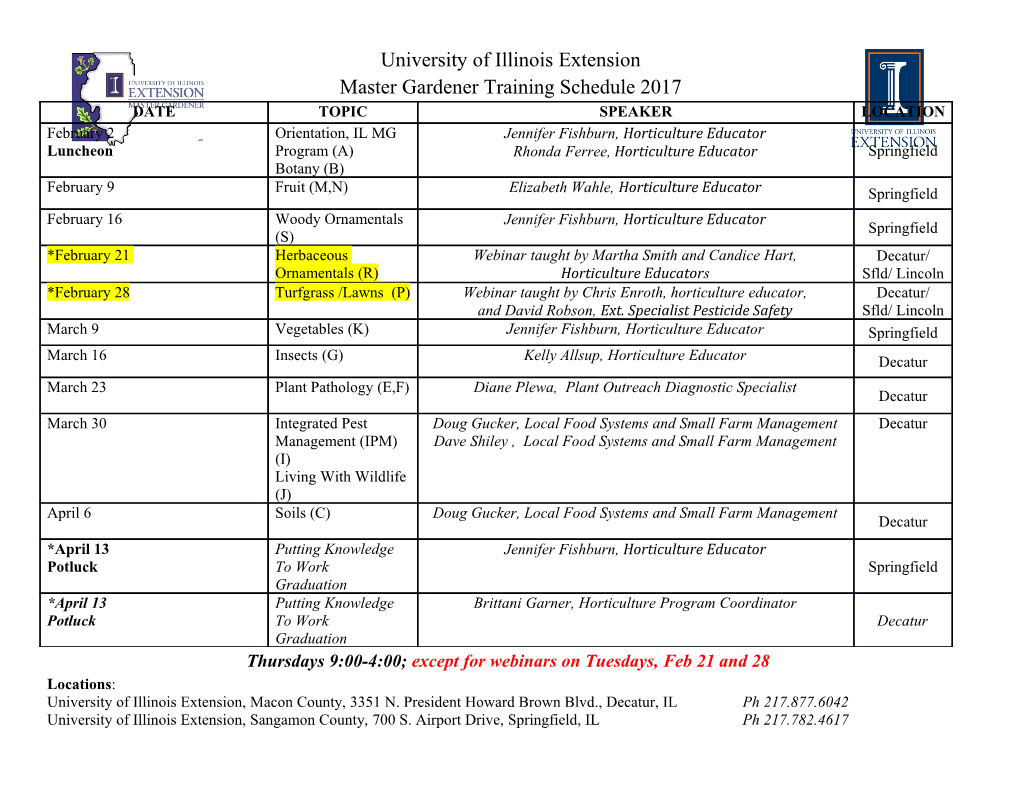
jr Z LU It'.O The Corrosive Effect of Soldering Fluxes f UJ and Handling on Some Electronic Material! 1;Q :"0 i., ^h >: s.J A variety of rosin-based liquid soldering fluxes are characterized *. tn as to halide content, and investigation indicates galvanic corrosion dmS < UJ stress corrosion cracking are mechanisms oi material degradation thy can cause premature failure of inadequately cleaned electronic devicy a. ,q pbJ > to BY B. D. DUNN AND C. CHANDLER «i o ABSTRACT. A preliminary survey has craft projects are generally assembled initial pre-tinning of "diifie-.i**- ,.-".* • been conducted to assess the variety by hand-soldering methods. Compa­ ponent leads—particularly m ris •• - of rosin-based liquid soldering fluxes nies which have been contracted to of nickel-based alloys—to adW&we h•---•• r utilized by European Space Agency manufacture such equipment will fol­ ter solderability. After pre»l?«v ..H, »he contractors. These fluxes were charac­ low the general soldering require- flux residues must be thorotggjMy I •'•'''' terized according to their halide con­ ments specified by ESA1 in order to cleaned from the component \e-rn ,*, tents, and a limited number of the obtain an adequate standard oi soider face to preclude time-depef***;-- J cor­ more common commercially available joint reliability. This is achieved mainly rosive attack. 1 •"** types were further evaluated in order by the employment of trained and Notwithstanding the tight Sofefe to assess their performance in terms of certified operators and inspectors, but process controls, several p solderability and corrosiveness. The also by the control of materials and associated with the corrosive - investigation included both standard soldering techniques. The mass assem­ liquid-soldering fluxes arid If? O and ad hoc corrosion tests and the bly of components to printed circuit dues have cost certain ESA < v determination of flux halide content boards by wave soldering has b'jen much wasted time and «•-,- and pH values. The corrosion tests agreed for the ESA Spacelab project in majority of these problem-! 4 • •' were performed in a warm, damp view of the large number of identical as non-conformances to :S atmosphere following the deliberate circuits utilized by this project and, inspection requirements, ••>"'; contamination by the fluxes of sam­ following qualification programs, a the formation of corrosic^'. ;r • '12 ples of electronic materials. limited number of wave-soldering on the surfaces of both s; . lines have been approved. a. The corrosive effects of residual flux copper wires and fus © on the surfaces of stressed Kovar com­ The successful outcome ot all sol­ coated printed circuit L- ponent leads and silver-plated copper dering operations will depend on sev­ cases, soldering had been > 1 • J wires are correlated against the phys­ eral material factors. The choice of a with the additional applicat •:- ii '. O'-. : iochemical properties of these fluxes. suitable soldering flux is very impor­ uid fluxes, supplied by rr-; - ; The results were compared with those tant, because it is the flux medii.m ufacturers to both U.S." an.' . '••••• obtained from similar control samples which will provide for the imlial trans­ specifications, purporting .••'••, v. either in clean condition or after delib­ fer of heat from the hot-soldering iron, dues of a non-hygroscopk', mm • erate contamination during handling. or liquid wave of solder, *o the sur­ sive and non-conducpv- tgtytf Met­ Galvanic corrosion and stress corro­ faces being joined together. The ESA allographic examine: gi . r sion cracking are considered to be soldering specification limits the strands and printed wi i • .•••im­ mechanisms of material degradation choice of material finishes which may ported both bright g • >-.y- which can cause the premature failure be interconnected to those having an brown corrosion p odi :i : of inadequately cleaned electronic excellent solderability, so that highly reveal reduced co devices. The acceptance of supposedly activated fluxes are not needed during tional areas; it is as • ' r "non-corrosive" liquid soldering fluxes the actual assembly process. luxes of short term such disc •.:<.•<< ,.- on the basis of routine standard tests is high activity, which are potentially from surface corrosi; > unlikely to obviate all the potential more dangerous from a corrosion cosmetic defect. v ;- corrosion problems associated with viewpoint, are permitted during the spacecraft electron:.' . • - . •,: electronic hardware. harnesses have long •:; : • to launch. Once it . to assess the long te r B. D. DUNN and C CHANDLER are with corrosion mechar sim Introduction the Materials Section, Product Assurance conductors with.- -: ; i Group, European Space Research anc Tech* which have beer (I •• ••:. •._•• • • Electronic packages intended for nology Centre, Noordwijk, Ti:e Nether­ for at least 10 year European Space Agency (ESA) space­ lands • WEEDING RESEARCH Si 'IH Problems of a more serious nature 71 previously examined in the flux system for the measurement of ionic included the failure of various gold- survey; they represent typical commer- conductivity of flux residues. This plated Kovar leads on flat-packaged ical products ranging from non-acti­ equipment, often referred to as the components. These leads had been vated to fully activated rosin-based lonograph,* has been evaluated by formed and then prepared according fluxes containing halogenated addi­ Naval Avionics and pronounced as a to the ESA requirement1 for gold tives. The copper mirror test proce­ method which provides for the semi- removal prior to soldering. De-golding dure2-4 is now re-examined against a quantitative measurement of flux resi­ 1112 and pre-tinning were performed by new flux test proposal.13 Also, certain dues on printed circuit boards. dipping the leads into solder baths special corrosion tests have been The test is limited to the detection fluxed with a mildly activated rosin. devised to reproduce those material of ionizable constituents in solder After a few months of storage, the compositions and environments fluxes which are monitored by the leads from several batches of flat pack­ thought most likely to have promoted DCM on a scale based on a known ages were observed to fracture com­ both the previously mentioned space­ quantity of sodium chloride dissolved pletely when exposed to light han­ craft corrosion problems and the few in either pure water or a 1:1 solvent dling operations. Metallographic in­ problems which have been reported in mixture of isopropanol and water. Cal­ vestigations strongly indicated that the the literature.5-10 ibration of this system was based on failure mechanism of these leads was The ionic content of each flux was the conductivity of 1 /ig NaCI per 1 ^l one of stress corrosion cracking of the assessed together with the effect of water. Kovar alloy due to the combined excessive operator handling contami­ For the purpose of this test program, effect of residual stresses in the lead nation on the ensuing corrosion of a constant amount of flux (5 /xl) was material following the forming opera­ component leads. The various flux added to the equipment's solvent tion and the presence of a thin surface types which have been subjected to which was continuously pumped in a film of supposedly "non-corrosive" this test program are listed in Ta­ closed loop and then passed through flux residue. Other failures have ble 1. two conductivity cells. Values of con­ involved the fracture of mounted tran­ ductivity were measured for each of sistor leads following equipment level the 13 fluxes in their as-received con­ vibration testing; fractography re­ Experimental and Test Procedures dition. Each flux sample was then vealed that stress corrosion had ini­ Chemical Analysis boiled for 1 minute (min) at -l-200oC tiated a crack in the lead material and (392°F) in an attempt to simulate flux this had later propagated by a fatigue Chemical analysis of solder fluxes is composition modifications which may mechanism. extremely difficult to perform and is occur during a soldering operation; often found to be inaccurate. Rosin the DCM test was then repeated by Discussion of these sporadic corro­ fluxes can include a vast range of introducing 5 /xl of the boiled flux sion-related problems during Project additives known only to the flux man­ concentrate into the solvent. Material Review Board meetings has ufacturers themselves. These may in­ led to the supposition that, although clude solvents and wetting, foaming ESA contractors purchased both cored and viscosity agents which have been Effectiveness of Flux Based on and liquid solder fluxes to recognized chosen to strengthen the fluxing prop­ Solderability Tests specifications, the complex chemical erties of the rosin. composition of activators contained in The soldering efficiencies of the Full chemical analyses have been proprietary rosin-based fluxes may various fluxes were assessed by means attempted. Fluorine, chlorine, bro­ change from one batch to another of a standard solderability test method mine, iodine, sulpher and phosphorus with resultant modification of proper­ compliant with B.S. 2011, Part 2T (Phil­ have been detected by emission spec- ties such as corrosiveness and solder­ ips Globule Method). The solderability troscopy, X-ray fluorescence spectros- ability. test was applied to both gold-plated copy and activation analysis. Gas chro- copper wire and plain copper wire by Initially, a survey of soldering fluxes matography and infrared absorption the horizontal immersion of short used by some of the major ESA con­ spectroscopy have been used to sepa­ lengths of each degreased wire in a tractors was made; the results are pre­ rate and determine the volatile organic globule of liquid eutectic solder held sented in the Appendix. This survey components. Non-volatile compo­ at 4-235°C (455°F) on a heated steel established that all the liquid soldering nents have been identified by both block. fluxes employed for component as­ ionic and non-ionic chromatography Immediately prior to wire immer­ sembly work and wire interconnec­ on ion exchange columns.
Details
-
File Typepdf
-
Upload Time-
-
Content LanguagesEnglish
-
Upload UserAnonymous/Not logged-in
-
File Pages19 Page
-
File Size-