Synthetic Approaches to Novel Highly Functionalized Polythiophenes Michael Mitchell Iowa State University
Total Page:16
File Type:pdf, Size:1020Kb
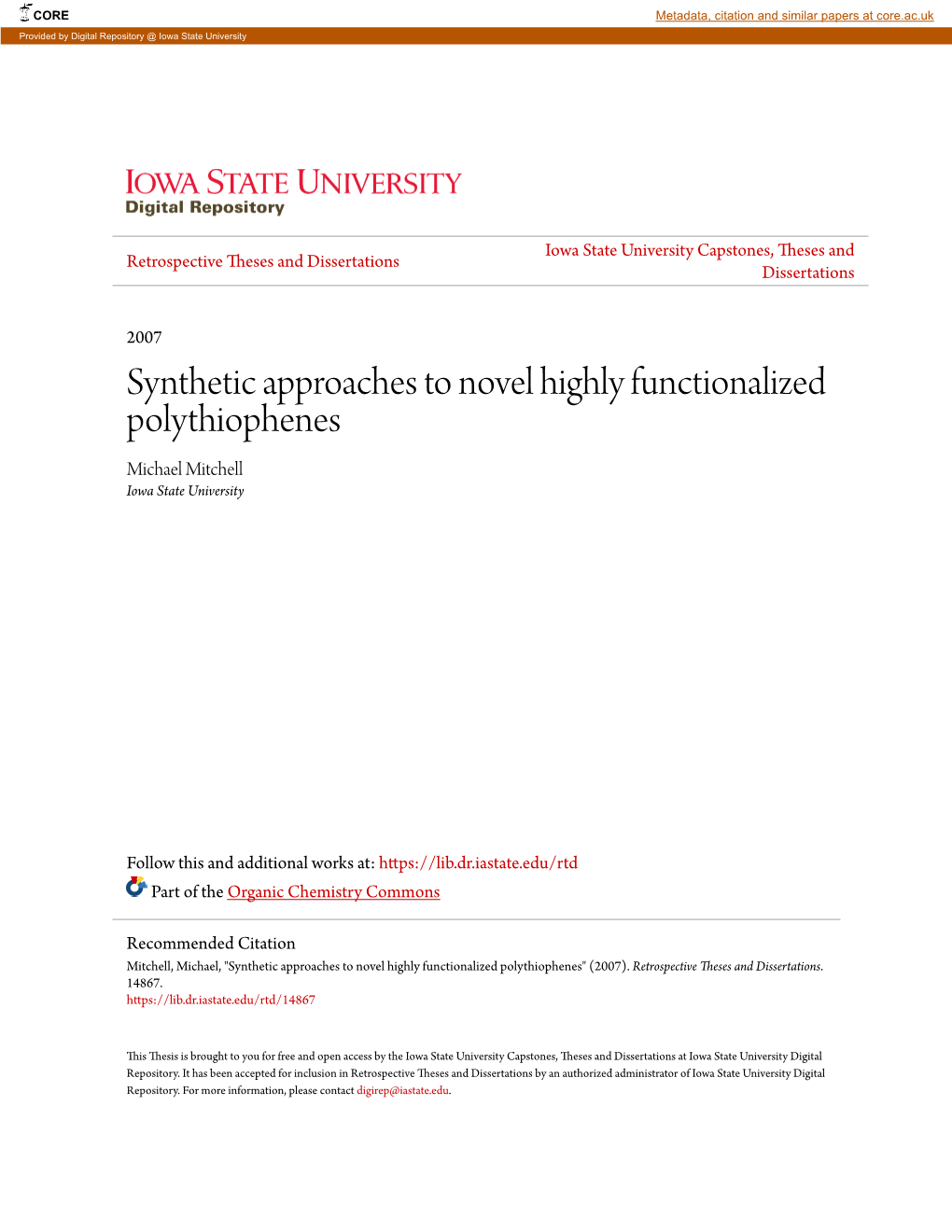
Load more
Recommended publications
-
Handbook of Less-Common Nanostructures
HANDBOOK OF LESS-COMMON NANOSTRUCTURES Boris I. Kharisov • Oxana Vasilievna Kharissova Ubaldo Ortiz-Mendez CRC Press Taylor &. Francis Croup Boca Raton London NewYork CRC Press is an imprint of the Taylor & Francis Group, an Informa business Contents Abbreviations xix Preface xxiii Acknowledgments xxv Authors xxvii PART I Introduction to Nanostructures Chapter 1 Methods for Obtaining Nanoparticles and Other Nanostructures 3 1.1 General Remarks on Nanoparticle Fabrication 3 1.2 Examples of Several Important Methods for the Synthesis of Nanoobjects 3 1.2.1 Vapor and Plasma-Based Techniques 3 1.2.2 Electrochemical Methods 10 1.2.3 Microwave, Ultrasonic, and UV-Irradiation Techniques 14 1.2.4 High-Pressure Methods 18 1.2.5 Use of Microfluidic Chips 20 1.2.6 Synthesis in Reversed Micelles 21 1.2.7 Hot-Plate Method 21 1.2.8 Other Chemical Routes 22 1.2.9 Biochemical and Self-Assembly Methods 24 1.3 "Green" Aspects of Nanoparticle Synthesis 26 References 27 Chapter 2 Brief Description of Some Classic Nanostructures 31 2.1 Carbon-Based Nanostructures 31 2.1.1 Carbon Nanotubes 31 2.1.2 Fullerenes 34 2.1.3 Nanodiamonds 35 2.1.4 Graphene and Graphane 37 2.2 Conventional Noncarbon Nanostructures 38 2.2.1 Simple and Core-Shell Nanoparticles 38 2.2.2 Nanometals 42 2.2.3 Gallery of Other Conventional Nanostructures 42 References 48 PART II Less-Common Nanostructures Chapter 3 Simple, Linear ID, 2D, and 3D Nanostructures 57 3.1 Nanolines 57 3.2 Nanopencils 61 ix X Contents 3.3 Nanodumbbells 66 3.4 Nanoshuttles 70 3.5 Nanopeapods 73 3.6 Nanopins 77 3.7 -
Synthesis, Reactivity, and Catalysis of Group 3 and Lanthanide Alkyl Complexes
Synthesis, Reactivity, and Catalysis of Group 3 and Lanthanide Alkyl Complexes By Daniel Steven Levine A dissertation submitted in partial satisfaction of the requirements for the degree of Doctor of Philosophy in Chemistry in the Graduate Division of the University of California, Berkeley Committee in charge: Professor T. Don Tilley, Co-Chair Professor Richard A. Andersen, Co-Chair Professor Alexis T. Bell Summer 2016 Abstract Synthesis, Reactivity, and Catalysis of Group 3 and Lanthanide Alkyl Complexes by Daniel Steven Levine Doctor of Philosophy in Chemistry University of California, Berkeley Professor T. Don Tilley, Co-Chair Professor Richard A. Andersen, Co-Chair Chapter 1. A series of scandium dialkyl complexes, (PNP)ScR2 (R = neopentyl, trimethylsilylmethyl), supported by the monoanionic, chelating PNP ligand (2,5- bis(dialkylphosphinomethyl)pyrrolide; alkyl = cyclohexyl, tert-butyl) was synthesized and the reactivities of these complexes toward simple hydrocarbons was investigated. The scandium– carbon bonds undergo σ-bond metathesis reactions with hydrogen and these complexes are catalysts for the hydrogenation of alkenes. Reactions with primary amines led to formation of amido complexes that undergo cyclometalation via σ-bond metathesis, without involvement of an imido complex intermediate. A variety of carbon-hydrogen bonds are also activated, including sp-, sp2-, and sp3-C–H bonds (intramolecularly in the latter case). Levine, D. S.; Tilley, T. D.; Andersen, R. A. Organometallics 2015, 34 (19), 4647. Chapter 2. Terminal group 3 methylidene complexes are generated by thermolysis of monoanionic PNP-supported scandium and yttrium dialkyl complexes. The reaction mechanism has been probed by deuterium-labeling experiments and DFT calculations. Abstraction of a γ- hydrogen from one alkyl group by the other affords a metallacyclobutane that undergoes [2+2] cycloreversion, analogous to a key step in the olefin metathesis reaction, to generate a methylidene complex and isobutene. -
Organic Materials for Electronic Devices
Organic Materials for Electronic Devices by Lichang Zeng Submitted in Partial Fulfillment of the Requirements for the Degree Doctor of Philosophy Supervised by Professor Shaw H. Chen and Professor Ching W. Tang Department of Chemical Engineering Arts, Sciences and Engineering Edmund A. Hajim School of Engineering and Applied Sciences University of Rochester Rochester, New York 2010 ii To my family iii CURRICULUM VITAE Lichang Zeng was born in 1978 in Fujian, China. In 2001, he received a Bachelors of Engineering degree in Polymer Materials from Zhejiang University, Hangzhou, China. He continued on at Zhejiang University receiving his Master of Science degree in 2004. He then moved to the University of Rochester to pursue his doctorate in Chemical Engineering under the joint supervision of Professors Shaw H. Chen and Ching W. Tang, receiving a Master of Science degree in 2009. His field of research was in organic electronic materials and devices. Selected Publications in Referee Journals 1. Zeng, L. C.; Tang, C. W.; Chen, S. H. “Effects of Active Layer Thickness and Thermal Annealing on Polythiophene:Fullerene Bulk Heterojunction Photovoltaic Cells.” Applied Physics Letters, 2010, 97, 053305. 2. Zeng, L. C.; Blanton, T. N.; Chen, S. H. “Modulation of Phase Separation between Spherical and Rod-Like Molecules Using Geometric Surfactancy.” Langmuir 2010, 26, 12877. 3. Zeng, L. C.; Lee, T. Y. S.; Merkel, P. B.; Chen, S. H. “A New Class of Non-Conjugated Bipolar Hybrid Hosts for Phosphorescent Organic Light-Emitting Diodes.” Journal of Materials Chemistry 2009, 19, 8772. 4. Zeng, L. C.; Yan, F.; Wei, S. K. H.; Culligan, S. -
Sub-10 Nm Nano-Structured Carbohydrate-Based Block Copolymer Thin Films for Organic Photovoltaic Applications Yoko Otsuka
Sub-10 nm nano-structured carbohydrate-based block copolymer thin films for organic photovoltaic applications Yoko Otsuka To cite this version: Yoko Otsuka. Sub-10 nm nano-structured carbohydrate-based block copolymer thin films for organic photovoltaic applications. Theoretical and/or physical chemistry. Université Grenoble Alpes, 2017. English. NNT : 2017GREAV024. tel-01830370 HAL Id: tel-01830370 https://tel.archives-ouvertes.fr/tel-01830370 Submitted on 5 Jul 2018 HAL is a multi-disciplinary open access L’archive ouverte pluridisciplinaire HAL, est archive for the deposit and dissemination of sci- destinée au dépôt et à la diffusion de documents entific research documents, whether they are pub- scientifiques de niveau recherche, publiés ou non, lished or not. The documents may come from émanant des établissements d’enseignement et de teaching and research institutions in France or recherche français ou étrangers, des laboratoires abroad, or from public or private research centers. publics ou privés. THÈSE Pour obtenir le grade de DOCTEUR DE LA COMMUNAUTE UNIVERSITE GRENOBLE ALPES Spécialité : Chimie Physique Moléculaire et Structurale Arrêté ministériel : 7 août 2006 Présentée par Yoko OTSUKA Thèse dirigée par Redouane BORSALI préparée au sein du Centre de Recherche sur les Macromolécules Végétales (CERMAV) et du Centre de Technique du Papier (CTP) dans l'École Doctorale Chimie et Sciences du Vivant Films minces nanostructurés de domaines sub-10 nm à partir de copolymères biosourcés pour des applications dans le photovoltaïque organique Thèse soutenue publiquement le « 4 janvier 2017 », devant le jury composé de : M. Patrice RANNOU Directeur de Recherche au CNRS, SPrAM (Président) M. Martin BRINKMANN Directeur de Recherche au CNRS, ICS (Rapporteur) M. -
Active Metals • Preparation • Characterization • Applications
Active Metals • Preparation • Characterization • Applications Edited by Alois Fürstner Weinheim • New York VCH Basel • Cambridge • Tokyo Contents Preface V List of Contributors XVII 1 Rieke Metals: Highly Reactive Metal Powders Prepared by Alkali Metal Reduction of Metal Salts R. D. Rieke, M. S. Seil, W. R. Klein, T. Chen, J. D. Brown, and M. V. Hanson 1.1 Introduction 1 1.1.1 Physical Characteristics of Highly Reactive Metal Powders 3 1.2 Rieke Magnesium, Calcium, Strontium, and Barium 3 1.2.1 Formation of Rieke Magnesium 4 1.2.2 Formation of Rieke Calcium, Strontium, and Barium 4 1.2.3 Grignard Reactions Using Rieke Metals 5 1.2.4 1,3-Diene-Magnesium Reagents 7 1.2.4.1 Preparation 7 1.2.4.2 Regioselectivity 7 1.2.4.3 Carbocyclization of (l,4-Diphenyl-2-butene-l,4-diyl)magnesium with Organic Dihalides 8 1.2.4.4 1,2-Dimefhylenecycloalkane-Magnesium Reagents 11 1.2.4.5 Synthesis of Fused Carbocycles, ß, y-Unsaturated Ketones and 3-Cyclopentenols from Conjugated Diene-Magnesium Reagents 12 1.2.4.6 Synthesis of Spiro y-Lactones and Spiro (5-Lactones from 1,3-Diene- Magnesium Reagents 16 1.2.4.7 Synthesis of y-Lactams from Conjugated Diene-Magnesium Reagents ... 20 1.3 Rieke Zinc 24 1.3.1 The Preparation of Rieke Zinc 24 1.3.2 Direct Oxidative Addition of Functionalized Alkyl and Aryl Halides .... 24 1.3.3 Reactions of Organozinc Reagents with Acid Chlorides 25 1.3.4 Reactions of Organozinc Reagents with a,/?-Unsaturated Ketones 25 1.3.5 Reactions with Allylic and Alkynyl Halides 28 1.3.6 Cross-Coupling of Vinyl and Aryl Organozinc Reagents -
Organometallic Chemistry — for Organic Synthesis Abbreviations in Chemical Structures
Organometallic Chemistry — for organic synthesis Abbreviations in Chemical Structures Me CH - methyl Bz PhC(O)- benzoyl Contents 3 Et MeCH2- ethyl Boc t-BuOCO tert-butoxycarbonyl 1. Main group organometallic chemistry Pr EtCH2- n-propyl Ts p-TolSO 2- p-toluenesulfonyl 1-1. Preparations Bu PrCH2- n-butyl Ms MeSO2- methanesulfonyl 1-2. Reactions Pent BuCH2- n-pentyl Tf CF3SO2- trifluoromethanesulfonyl Hex PentCH - n-hexyl TMS Me Si- trimethylsilyl 2. Reactions of organic molecules and transition-metal complexes 2 3 i-Pr Me2CH- isopropyl TES Et3Si- triethylsilyl 3. Reactions catalyzed by transition-metal complexes i-Bu i-PrCH- isobutyl TBS t-BuMe2Si- tert-butyldimethylsilyl 3-1. Hydrogenation s-Bu EtMeCH- sec-butyl 3-2. Cross-coupling and related reactions t-Bu Me3C- tert-butyl c-Pent c-C H - cyclopentyl 3-3. Olefin metathesis 5 9 t-Am EtMe2C- tert-amyl 3-4. Homogeneous metal catalysts in chemical industry Cy (c-Hex) c-C6H11- cyclohexyl Ph C6H5- phenyl pin -OCMe2CMe2O- pinacolate Bn PhCH2- benzyl cat 1,2-C6H4O2 catecholate Books o-Tol 2-MeC6H4- 2-methylphenyl 1. Comprehensive Organometallic Chemistry III m-Tol 3-MeC6H4- 3-methylphenyl R any C substituents eds. by D. M. P. Mingos and R. H. Crabtree, Elsevier, Oxford, 2007. p-Anis 4-MeOC6H4- 4-methoxyphenyl Ar any aromatic substituents (https://www.sciencedirect.com/science/referenceworks/9780080450476) PMB p-AnisCH2- 4-methoxybenzyl X any halogen and related leaving group Xyl 5-Me-m-Tol - 3,5-dimethylphenyl M any metal substituents 2. 第5版 実験化学講座 有機化合物の合成 VI 金属を用いる有機合成 Mes 2,4,6-Me3C6H2- mesityl 日本化学会 編, 丸善, 2004. -
Organic Solar Cell by Inkjet Printing—An Overview
technologies Review Organic Solar Cell by Inkjet Printing—An Overview Sharaf Sumaiya 1,*, Kamran Kardel 2,* and Adel El-Shahat 1,* 1 Department of Electrical Engineering, Georgia Southern University, Statesboro, GA 30458, USA 2 Department of Manufacturing Engineering, Georgia Southern University, Statesboro, GA 30458, USA * Correspondence: [email protected] (S.S.); [email protected] (K.K.); [email protected] (A.E.-S.); Tel.: +1-912-541-3821 (S.S.); +1-912-478-8566 (K.K.); +1-912-478-2286 (A.E.-S.) Received: 5 August 2017; Accepted: 16 August 2017; Published: 24 August 2017 Abstract: In recent years, organic solar cells became more attractive due to their flexible power devices and the potential for low-cost manufacturing. Inkjet printing is a very potential manufacturing technique of organic solar cells because of its low material usage, flexibility, and large area formation. In this paper, we presented an overall review on the inkjet printing technology as well as advantages of inkjet-printing, comparison of inkjet printing with other printing technologies and its potential for organic solar cells (OSCs). Here we highlighted in more details about the viability of environment-friendly and cost-effective, non-halogenated indium tin oxide (ITO) free large scale roll to roll production of the OSC by inkjet printing technology. The challenges of inkjet printing like the viscosity limitations, nozzle clogging, coffee ring effect, and limitation of printability as well as dot spacing are also discussed. Lastly, some of the improvement strategies for getting the higher efficiency of the OSCs have been suggested. Keywords: organic solar cell (OSC); inkjet printing; drop-on-demand; continuous inkjet 1. -
Ref.547.2 WAN
3632 SUBJECT INDEX 1,3-dipole, 916, 917,1217, 1504, 1505 2-nitroaniline, 142, 1868 1,3-oxazine, 1913 2-nitrobenzaldehyde, 136 1,3,2-benzothiazathiolium chloride, 1395 2-nitropropane, 1336, 1337 1,3,5-trihydroxybenzene, 1498 2-nonyne, 317 1,4-benzohydroquinone, 1477 2-oxazoline, 2529 1,4-benzoquinone, 1477, 123,2042,2044 2-picoline, 2998 1,4-dimethoxybenzene, 1128 2-pyridinealdoxime, 2734 1,4-dioxygenation, 1675 2-pyrroline, 2529 1,4-hydroquinone, 1055, 1477, 1841 2-tetrahydroxybutyl-quinoxaline, 2084, 2086 1,4-naphthoquinonedibenzene-sulfonimide, 2-thiohydantoin, 2488, 2489, 2490, 2858 2147 2-vinylbutadiene, 1014 1,4-pentadiene, 1519,2881 2-vinyloxetane, 308 1,5-cyclooctadiene,803 2-vinyloxirane, 308 1,6-naphthyridine, 2335 2-vinylphosphirane,2881 1,7-dihydroxynaphthalene, 553 2,2-diethoxypropane, 200 1 1,8-naphthalenediamine,2198 2,2,4,4-tetramethylpiperidine,3146 1,8-naphthyridine, 1138 2,2' -dibenzoyloxyacetophenone, 170 IO-ketodocosanoic acid, 422 2,3,5-triphenylimidazole, 2293 l O-phenanthroline, 1572 2,3,5,6-tetramethylacetophenone, 130 12-ketoergostane, 1857 2,4-dialkoxypyrimidine, 1408 12-ketopregnane, 1857 2,4-dimethylquinoline, 1139 17-hydroxy-20-ketosteroid,877 2,4-dinitrophenylacetone, 2017 17-keto-steroid,3158 2,4-dinitrophenylhydrazine, 1007, 1086, 1633, 17-oxo-steroid, 3158 1847, 1855 18-crown-6, 704, 737, 743, 1250, 1485, 1487, 2,4-dinitrotoluene, 1381, 1895 2008,2550,2782,2848,2976 2,4,6-trinitrotoluene, 1041 IH-l,2,3-triazole,905 2,5-dimethoxytetrahydrofuran, 667, 2415, 2416 2-acetidinethione, 1222 2,6-dinitroisovanillin, -
Kleinhenz-Dissertation-2016
LONG RANGE ORDERING IN POLY(3-HEXYLTHIOPHENE) FLUIDS AND FILMS: IMPLICATIONS FOR ORGANIC ELECTRONICS A Dissertation Presented to The Academic Faculty by Nabil Kleinhenz In Partial Fulfillment of the Requirements for the Degree Doctor of Philosophy in the School of Chemistry and Biochemistry Georgia Institute of Technology December 2016 COPYRIGHT © 2016 BY NABIL KLEINHENZ LONG RANGE ORDERING IN POLY(3-HEXYLTHIOPHENE) FLUIDS AND FILMS: IMPLICATIONS FOR ORGANIC ELECTRONICS Approved by: Dr. Elsa Reichmanis, Advisor Dr. John Reynolds School of Chemical and Biomolecular School of Chemistry and Biochemistry Engineering Georgia Institute of Technology Georgia Institute of Technology Dr. Mohan Srinivasarao Dr. David Collard School of Materials Science and School of Chemistry and Biochemistry Engineering Georgia Institute of Technology Georgia Institute of Technology Dr. Jean-Luc Brédas School of Materials Science and Engineering King Abdullah University of Science and Technology Date Approved: November 2, 2016 To our son, Badi, and any other children we may be blessed to have. ACKNOWLEDGEMENTS I would like to thank all of the family, friends and coworkers who have supported me over these past five years and throughout my life. My advisor, Elsa Reichmanis, has been incredibly kind, patient and sincerely invested in my education. I feel her approach of giving her students freedom to independently investigate the questions they have is very empowering. My coworkers and friends Ping-Hsun Chu, Nils Persson, Mike McBride, Zongzhe Xue, Jamilah Middlebrooks, Eugenia Kim, Dalsu Choi, Gang Wang, Talanna Ruffin, Zhibo Yuan, Ji-Hwan Kang, Jeff Hernandez, Bailey Risteen, Giovanni DeLuca, Yo Han Kwon, Krysten Minnici, Guoyan Zhang, Avishek Aiyar, Rui Chang, Karthik Nayani, Jinxin Fu, Mincheol Chang, Cornelia Rosu and many others have been always willing to help, have shared enlightening discussions with me and were always so kind to assist in my experimental work. -
Dissertation Peter Kazarinoff 06.07.12
© Copyright 2012 Peter D. Kazarinoff P-type and N-type Semiconducting Thiophene Copolymers for Organic Electronic Applications Peter D. Kazarinoff A dissertation submitted in partial fulfillment of the requirements for the degree of Doctor of Philosophy University of Washington 2012 Reading Committee: Professor Christine K. Luscombe, Chair Professor Fumio S. Ohuchi Professor Guozhong Cao Program Authorized to Offer Degree: Department of Materials Science and Engineering University of Washington Abstract P-type and N-type Semiconducting Thiophene Copolymers for Organic Electronic Applications Peter D. Kazarinoff Chair of the Supervisory Committee: Professor Christine K. Luscombe There has been considerable research in the pursuit of organic materials to replace inorganic materials in electronic applications because of their advantages in being light weight, flexible, and solution processable over large areas. In this examination, novel p- type and n-type thiophene based semiconducting copolymers have been analyzed. First, a series of three air stable ester-functionalized p-type polythiophenes were tested for their performance in organic thin film transistors. Increased crystallinity as measured by XRD and DSC accounts for the highest mobility polymer of this series. A HOMO level of 5.6 eV as measured by CV spectroscopy account for the air stability of the polymers over one month. Second, four highly soluble naphthalene diimide (NDI) based n-type polymers are presented - each differing only in the thiophene content comprising the material. Electron mobilities are as high as 0.076 cm 2/Vs for the novel material PNDI-3Th . Polymer crystallinity and general macromolecular order was shown to effectively improve by increasing the number of thiophene units along the polymer backbone. -
Final Lithco Complete Catalog Assembled
MILLENNIUM EDITION II Lithco Inc. Since 1963 SUPPLIES TOOLS EQUIPMENT OFFSET PRINTING DIGITAL PRINTING SCREEN PRINTING GRAPHIC DESIGN REPROGRAPHICS BINDERY & FINISHING TOOLS OF THE TRADE DIGITAL PREPRESS CHEMICALS PRESSROOM BINDERY SAFETY Sold by Graphic Arts Dealers Worldwide WELCOME Welcome to the newest, expanded LITHCO CATALOG — MILLENNIUM EDITION II. Not content with an award and Look for the following icons: industry kudos for our last catalog, we have been hard at work for over a year to bring you this even more NEW comprehensive and improved version. With this publication, we once again reinforce our commitment to you, your graphic New and improved items for this edition. arts dealer and the manufacturers we are proud to represent. We have broadened our product offering, adding forty-five new manufacturers and more than one hundred and seventy-five new products. Many of these product lines are in the electronic prepress, digital imaging and quality control areas. In addition we have significantly expanded our Tools of the Trade, Pressroom and Bindery Sections. Product Tips and Ideas. Our catalog is a valuable reference guide with information and tips to assist you in choosing the correct products for your needs. We have also expanded the use of web links so you can easily access more in-depth product information. Most importantly, use our catalog to specify products when ordering from your dealer. Total Quality Management, ISO Certified As a Master Distributor supporting your Dealer, our mission is to provide the broadest and Computer-to-Plate products. selection of the highest quality products to the printing and imaging community — worldwide! You can find LITHCO on the Internet at www.lithcoinc.com. -
Active Metals Preparation Characterization Applications
Active Metals Preparation Characterization Applications Edited by Alois Furstner Weinheim - New York VCH4b Base1 - Cambridge - Tokyo This Page Intentionally Left Blank Active Metals Edited by Alois Furstner Further Titles from VCH: C. Elschenbroich, A.Salzer Oganometallics - A Concise Introduction XlI1,495 pages, 57 tables 2nd ed. 1992. Hardcover ISBN 3-527-28165-7 2nd ed. 1991. Softcover ISBN 3-527-28164-9 E. Shustorovich Metal Surface Reaction Energetics Theory and Applications to Heterogeneous Catalysis, Chemisorption, and Surface Diffusion XII, 232 pagcs. 56 figures, 43 tables 1991. Hardcover ISBN 3-527-27938-5 J. Mulzer, et al. Organic Synthesis Highlights 1991. XII, 410 pages, 4.5 figures, 3 tables Hardcover ISBN 3-527-27355-5 H. Waldmann (ed.) Organic Synthesis Highlights I1 1995. XIII, 407 pages, 318 figures, 3 tables Hardcover ISBN 3-527-29200-4 K. C. Nicolaou, E. J. Sorensen Classics in Total Synthesis 1996. ca. 600 pages Hardcover ISBN 3-527-29284-5 Softcover ISBN 3-527-29231-4 OVCH Vcrlagsgesellschaft mbH, D-69451 Weinheirn (Federal Republic of Germany), 1996 Distribution: VCH, P.O. Box 1011 61, D-69451 Wcinheirn, Federal Kcpublic of Germany Switzerland: VCH, P. 0. Box, CH-4020 Basel, Switzerland United Kingdom and Ireland: VCH. 8 Wellington Court. Cambridgc CB1 1HZ. United Kingdom USA and Canada: VCH, 220 East 23rd Strect, New York. NY 10010-4606, USA Japan: VCH, Eikow Building, 10-9 Hongo 1-chome, Runkyo-ku, Tokyo 113, Japan ISBN 3-527-29207-1 Active Metals Preparation Characterization Applications Edited by Alois Furstner Weinheim - New York VCH4b Base1 - Cambridge - Tokyo Dr. Alois Fiirstner Max-Planck-Institut fiir Kohlenforschung Kaiser-Wilhelm-Platz 1 D-35470 hliilheini r I Thisbook was carefully produced.