The Nation Multiplittle
Total Page:16
File Type:pdf, Size:1020Kb
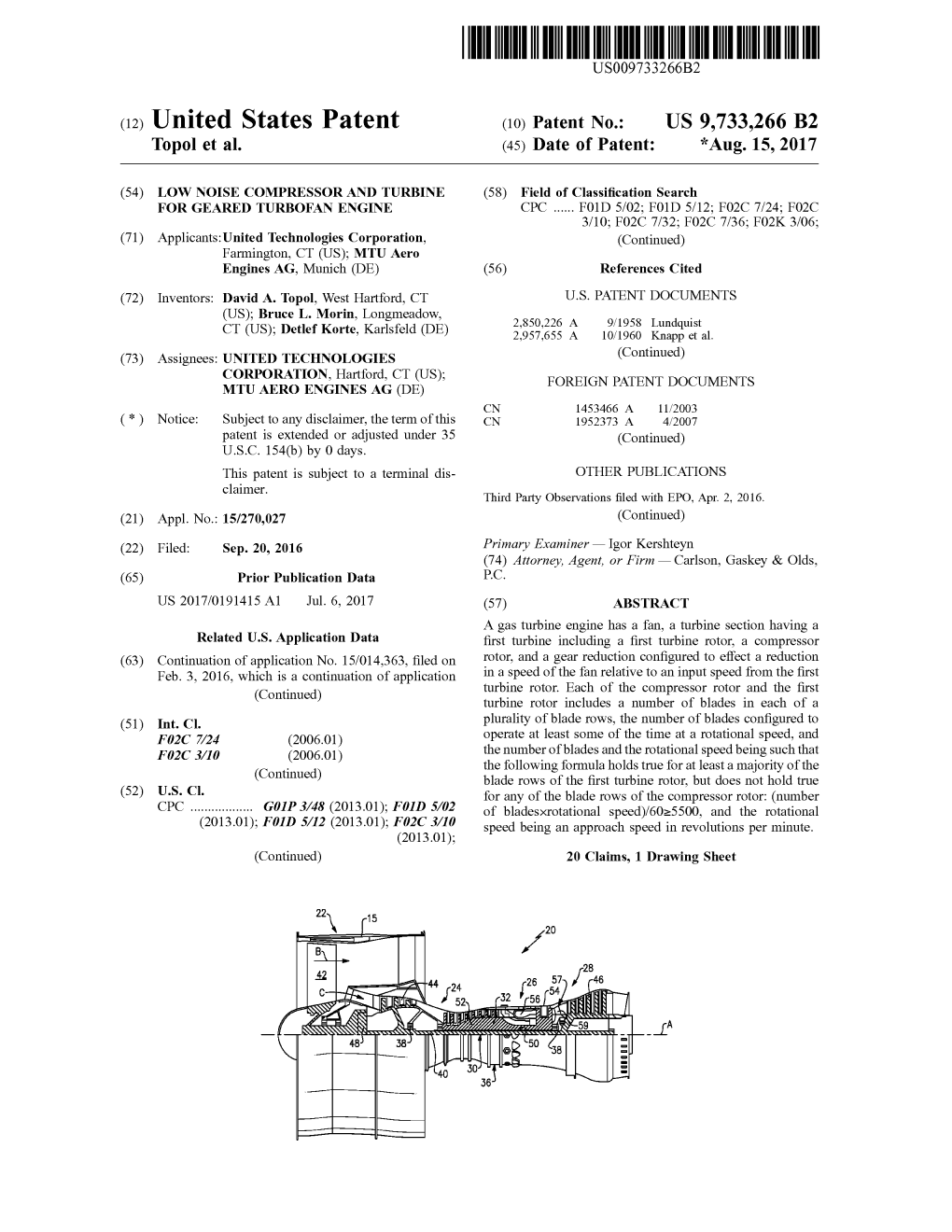
Load more
Recommended publications
-
Signature Redacted Department of Civil and Envirnmental Engineering, MIT Sloan School of Management May 11,2018
Next Generation Commercial Aircraft Engine Maintenance, Repair, and Overhaul Capacity Planning and Gap Analysis by Amanda J. Knight B. S. Mechanical Engineering, The University of Texas at Austin, 2006 M.S. Aerospace Engineering, The University of Southern California, 2011 Submitted to the MIT Sloan School of Management and the Department of Civil and Environmental Engineering in Partial Fulfillment of the Requirements for the Degrees of Master of Business Administration and Master of Science in Civil and Environmental Engineering In conjunction with the Leaders for Global Operations Program at the Massachusetts Institute of Technology June 2018 2018 Amanda J. Knight. All rights reserved. The author hereby grants MIT permission to reproduce and to distribute publicly paper and electronic copies of this thesis document in whole or in part in any medium now known or hereafter created. Signature of Author: Signature redacted Department of Civil and Envirnmental Engineering, MIT Sloan School of Management May 11,2018 Certified by: Signature redacted __ DI Roy Welsch, Thesis Supervisor Professor of Statistics and Engineering Systems Certified by: Signature redacted Dr. Daniel Wh The i Supervisor Senior Research ScientisU/Eyneritust Lecturer, IVVT Leaders for obal Operations Certified by: _____Signature redacted _ _ _ _ _ _ Dr. David Simchi-Levi, Thesis Supervisor Prof"or,9 C ppdEnvironmental Engineering Accepted by: Signature redacted____ Jesse H. Kroll Profesor of Civil and Environmental Engineering Chair, Graduate Program Committee Accepted by: Signature redacted MHro MASSACHUSETTS INSTITUTE ' M PM ManuraHerson OF TECHNOLOGY co Director, MBA Program, MIT Sloan School of Management JUN 0 7 2018 LIBRARIES This page has been intentionally left blank Page | 2 Next Generation Commercial Aircraft Engine Maintenance, Repair, and Overhaul Capacity Planning and Gap Analysis by Amanda J. -
It's No American Dream: Pratt & Whitney GTF Engine Now a Reality
A D D E N D U M It’s No American Dream: Pratt & Whitney GTF Engine Now a Reality... and chosen in Time's November issue one of "The 50 Best Inventions of the Year" In the August try-tasked capabilities. 2008 issue of Gear For those who can’t Technology, we ran recall how the GTF a story (“Gearbox works, here’s a piece Speed Reducer Helps lifted from the 2008 Fan Technology for Gear Technology arti- ‘Greener” Jet Fuel cle explaining—with Efficiency’) on the help from Robert Saia, then ongoing, extreme- Pratt & Whitney vice ly challenging and pro- president, next-gener- tracted development ation products—what of Pratt & Whitney’s makes it leading edge: geared turbofan (GTF) (What’s unique) jet engine. If success- is the addition of a ful, the engine would reduction gear box— provide a 20 percent or transmission sys- reduction in carbon tem—comprised of a emissions and fuel star gear system with burn and up to 50 per- five stationary gears. cent in general noise As Saia explains, the reduction. The targeted The long-awaited Pratt & Whitney GTF (PurePower PW1000G) jet gear box decouples the market and application engine is now a reality, with customer orders now in production (cour- fan from the turbine so for the engine was the tesy Pratt & Whitney). that each component narrow-body commer- can turn at its optimum cial airline industry—until now a dormant market for P&W— speed while also allowing for a lighter, more efficient turbine to which had long demanded a total plane package that would turn at a higher speed in driving a much larger, slower-turning achieve reduced maintenance, lower emissions, better fuel burn, fan. -
The Pratt & Whitney Purepower® Geared Turbofan™ Engine Overview
9/27/2015 The Pratt & Whitney PurePower® Geared Turbofan™ Engine Alan Epstein VP, Technology and Environment Pratt & Whitney Academie de l’Air et de l’Espace Paris, September 2015 © 2015 United Technologies Corporation This document has been publicly released 1 Overview The Development of the Geared TurbofanTM Engine • Some historical perspective • A recurrent theme - conventional wisdom vs. reality • The roles of architecture, design, and technology • Speculation on the future © 2015 United Technologies Corporation This document has been publicly released 2 1 9/27/2015 PurePower® Geared Turbofan™ Engine © 2015 United Technologies Corporation This document has been publicly released 3 Why History? “There is nothing new in the world except the history you do not know.” Harry S. Truman © 2015 United Technologies Corporation This document has been publicly released 4 2 9/27/2015 Pratt & Whitney – Dependable Engines Wasp Pic Wasp Engine Turbofan Engine 1925 2015 © 2015 United Technologies Corporation This document has been publicly released 5 Eras of Engine Architecture Single Spool Dual Spool Turbojet High Bypass Turbofan Ultra-High Bypass (1937) (1951) (1969) Geared Turbofan (2015) >10% STEPS IN EFFICIENCY OVERALL EFFICIENCY EFFICIENCY OVERALL 1940 1960 1980 2000 2020 © 2015 United Technologies Corporation This document has been publicly released 6 3 9/27/2015 Geared Turbofan Technology Demonstrators Over 50 years of interest Hamilton Standard General Electric Lycoming ALF502 4 5 Pratt & Whitney PW304, 1957 Q-Fan, 19722 QCSEE, 1977 1980 -
Fourteenth European Rotorcraft Forum A
. ' . FOURTEENTH EUROPEAN ROTORCRAFT FORUM Paper No. 96 A HYDRODYNAMIC TURBO-FAN/SHAFT CONVERTIBLE ENGINE R. R. OSSI TEXTRON LYCOMING STRATFORD, CONNECTICUT USA 20-23 September, 1988 MILAN, ITALY ASSOCIAZIONE INDUSTRIE AEROSPAZIALI ASSOCIAZIONE ITALIANA DI AERONAUTICA ED ASTRONAUTICA ABSTRACT A HYDRODYNAMIC TURBO-FAN/SHAFT CONVERTIBLE ENGINE R. R. Ossi Textron Lycoming Stratford, Connecticut USA Advanced powered lift aircraft will require greater translational flight speed to render themselves economically competitive with other .~uture modes of transportation. Initial and operational costs of such aircraft may be reduced significantly by effective consolidation of the various propulsion schemes into a m~n~mum number of prime movers. Such is the motivation behind the concept of the "convertible" engine. The most common current perception of the convertible engine is a standard configuration turbofan which incorporates aerodynamic devices to redirect the engine's low-pressure-spool shaft-power to an appropriate power takeoff on the engine structure. The available mechanical shaft-power is directed to the VTOL aircraft lift system during the lift-off or landing operations. The use of a hydrodynamic drive on the low-pressure-spool may present certain engine design, installation, and operational advantages for future vertical lift aircraft. By this system, a compact transformation of a standard configuration turbofan engine can be designed wherein the fan component is operated by a variable geometry hydrodynamic drive unit. This device is directly driven by the two-spool turbofan engine low pressure gas turbine. Actuation of the variable geometry can provide a wide variety of ·operating modes by controlling the fan speed. As the fan speed is reduced, the gas turbine power is made available on an appropriate mechanical power takeoff for vertical powered lift operation. -
On the Design of Energy Efficient Aero Engines Some Recent Innovations
THESIS FOR THE DEGREE OF DOCTOR OF PHILOSOPHY in Thermo and Fluid Dynamics On the Design of Energy Efficient Aero Engines Some Recent Innovations By Richard Avellán Department of Applied Mechanics CHALMERS UNIVERSITY OF TECHNOLOGY Göteborg, Sweden, 2011 On the Design of Energy Efficient Aero Engines: Some Recent Innovations Richard Avellán © RICHARD AVELLÁN, 2011. ISBN 978-91-7385-564-8 Doktorsavhandlingar vid Chalmers tekniska högskola Ny serie nr 3245 ISSN 0346-718X Department of Applied Mechanics Chalmers University of Technology SE-412 96 Gothenburg Sweden Telephone + 46 (0)31-772 1000 Cover: [Artist’s impression of a future energy efficient aircraft driven by counter-rotating propeller engines. Source: Volvo Aero Corporation] Printed at Chalmers Reproservice Göteborg, Sweden On the Design of Energy Efficient Aero Engines Some Recent Innovations By Richard Avellán Division of Fluid Dynamics Department of Applied Mechanics Chalmers University of Technology SE-412 96 Göteborg Abstract n the light of the energy crisis of the 1970s, the old aerospace paradigm of flying higher and I faster shifted towards the development of more energy efficient air transport solutions. Today, the aeronautical research and development community is more prone to search for innovative solutions, in particular since the improvement rate of change is decelerating somewhat in terms of energy efficiency, which still is far from any physical limits of aero engine and aircraft design. The Advisory Council for Aeronautics Research in Europe has defined a vision for the year of 2020 for aeronautical research in Europe which states a 50% reduction in CO2, 80% reduction in NOx and a 50% reduction in noise. -
MTU Aero Engines (MTX.DE) Investment Memo Date: 6/11/2020; Closing Stock Price: €154.4 (EUR)
MTU Aero Engines (MTX.DE) Investment Memo Date: 6/11/2020; Closing stock price: €154.4 (EUR) Disclaimer This report is for informational purposes only and does not constitute an offer to sell, solicitation to buy, or a recommendation for any security, or as an offer to provide advisory or other services in any jurisdiction in which such offer, solicitation, purchase or sale would be unlawful under the securities laws of such jurisdiction. Any offer to sell is done exclusively through the fund's Private Placement Memorandum. Past performance may not be indicative of any future results. No current or prospective client should assume that the past performance of any investment or investment strategy referenced directly or indirectly herein will perform in the same manner in the future. Different types of investments and investment strategies involve varying degrees of risk—all investing involves risk—and may experience positive or negative growth. Nothing herein should be construed as guaranteeing any investment performance. Investment funds advised by LRT Capital Management, LLC may maintain positions in the securities discussed within. The views presented here are subject to risk and uncertainties. The views presented herein may change without notice. For more information contact [email protected]. Overview MTU Aero Engines (“MTU”) operates in the aerospace engine market as an engine sub-system supplier and an independent provider of maintenance, repair, and overhaul services (MRO). MTU’s business is broken down into three divisions – commercial OEM business, military OEM business, and commercial MRO business. MTU’s revenues are split 40/60 between new engine manufacturing and MRO services, respectively. -
Inhaltsverzeichnis
Inhaltsverzeichnis 1 Einleitung 8 1.1 Marktsituation 8 1.2 Zukunftspotential 9 2 Konzept des Geared Turbofan 13 2.1 Erläuterung des Konzepts 13 2.2 Auswirkungen des Konzepts auf die einzelnen Triebwerksteile 14 2.2.1 Fanbereich 14 2.2.2 Niederdruckteil 14 2.2.3 Hochdruckteil 15 2.2.4 Brennkammer 15 2.2.5 Gehäuse 15 2.2.6 Getriebe 16 2.3 Zusammenfassung der Auswirkungen 18 3 Zur Historie des Geared Turbofan-Konzepts 20 3.1 Aubisque & Astafan 20 3.2 ALF502 & LF 507 20 3.3 Garrett TFE731 21 3.4 Rolls-Royce/SNECMA MS45SD-02 21 3.5 IAE V2500 SuperFan 22 3.6 Vorgänger des Pratt & Whitney PW1000G 23 3.6.1 Pratt & Whitney/Allison 578-DX 23 3.6.2 Advanced Ducted Propulsor (ADP) 23 3.6.3 Pratt & Whitney PW8000 23 3.6.4 Advanced Technology Fan Integrator (ATFI) 24 3.7 Pratt k Whitney PW1000G 24 4 Leistungssyntheserechnung 26 4.1 Programm 26 4.2 Eingabeparameter 26 4.2.1 Vorüberlegungen 26 4.2.2 Schub im Reiseflug 26 4.2.3 Nebenstromverhältnis und Massenströme 27 4.2.4 Wellendrehzahlen 29 4.2.5 Polytrope Wirkungsgrade 30 4.2.6 Brennkammerparameter 35 4.2.7 Druckverluste 35 4.2.8 Schubdüse 36 4.2.9 Luftsystem 37 4.2.10 Leistungsentnahme 37 4.2.11 Mechanische Wirkungsgrade 38 4.2.12 Druckverhältnisse 39 4.3 Ergebnisse der Leistungsrechnung im Auslegungspunkt 40 ii http://d-nb.info/1035562723 4.4 Berücksichtigung der Startforderung 42 5 Missionsanalyse 45 5.1 Definition der Flugprofile 45 5.1.1 Mittelstreckenmission 45 5.1.2 Kurzstreckenmission 46 5.2 Bestimmung des Schubs je Zustandspunkt 48 5.3 Ergebnisse der Missionsanalyse 51 5.4 Mögliche Optimierungen 55 6 Massenabschätzung des Getriebes 56 6.1 Vorstellung der empirischen Ansätze 56 6.1.1 Motivation 56 6.1.2 Ansatz nach Worobel und Mayo 56 6.1.3 Ansatz nach Plencner, Senty und Wickenheiser 57 6.1.4 Ansätze nach Grieb 57 6.1.5 Ansatz nach Tong. -
Influence of Regeneration in the Performance of a Propfan Engine
UNIVERSIDADE DA BEIRA INTERIOR Engenharia Influence of Regeneration in the Performance of a Propfan Engine Carolina da Silva Ferreira Thesis submitted in partial fulfillment of the requirements for the degree of Master of Science in Aeronautical Engineering (Ciclo de Estudos Integrado) Orientador: Prof. Doutor Francisco Miguel Ribeiro Proença Brójo Covilhã, October 2013 1 To my parents Elisabete e Joaquim and my brother Miguel 2 Resumo A indústria da aviação é um elemento essencial na sociedade de hoje em dia, e como tal, não pode ignorar as preocupações públicas sobre o aquecimento global e as questões ambientais, e sobre a economia global e o preço dos combustíveis. O actual pensamento “verde” e as novas políticas de protecção ambiental promoveram a criação de alguns projectos aeronáuticos amigos do ambiente. Estes projectos são destinados à criação de novas e melhores soluções procurando reduzir a pegada ambiental da indústria da aviação. Estas considerações envolvem o desenvolvimento de novos conceitos de aeronaves com menores emissões poluentes e consumo de combustível. Assim sendo, este estudo visa analisar a viabilidade de um motor propfan incorporado com um regenerador de calor. De acordo com vários autores, os motores propfan são mais eficientes que os actuais turbofans e a introdução de regeneradores de calor em turbinas de gás reduz o seu consumo específico de combustível. Assim sendo, a combinação de ambos pode ser uma solução viável para uma redução ainda maior do consumo específico nos actuais motores. O principal propósito desta tese é analisar se este novo conceito de motor poderá ser um substituto mais amigo do ambiente dos actuais turbofans. -
Ultra-High Bypass Ratio Turbofan for Next-Generation Large Aircraft
Ultra-High Bypass Ratio Turbofan for Next-Generation Large Aircraft Nicholas Turo-Shields, Sebastian Perkinson, Shashank Kashyap, Chris Vodney, Maunik Patel, Gerardo Martinez, Aditya Anilkumar AAE/ME 538 14 December 2018 Table of Contents Nomenclature 3 1 Abstract 4 2 Design Requirements 4 3 Baseline Engine 4 4 Team Structure 8 5 Design Methodology 8 5.1 Choice of Architecture . .8 5.2 BPR and Core Sizing . .9 5.2.1 Initial Core Scaling (constant fan mass flow) .......................9 5.2.2 Bypass Scaling (constant core scale) ............................9 5.2.3 Evaluation of Design for Takeoff . 10 5.2.4 Sizing for Cruise . 11 5.2.5 Further Improvements . 12 5.3 Gearbox . 12 5.4 Compressors . 13 5.4.1 LP Compressor (Fan) . 13 5.4.2 IP Compressor (Booster) . 15 5.5 LP Turbine . 16 5.5.1 Optimization of Specific Fuel Consumption . 17 5.5.2 Optimization of Core Flow . 17 5.5.3 Final Results for LP Turbine . 18 5.6 Materials . 19 5.7 Engine Cycle Improvements . 21 5.8 Risks and Concerns . 22 6 Our Engine Solution 23 7 Off-Design Analysis 24 7.1 Off-Design Operating Point . 24 7.2 Mission Profile . 25 7.3 Flight Envelope . 26 7.4 Mission Points . 28 7.5 Results . 28 8 Trade-off Study 30 8.1 Parametric Study . 31 8.2 Baseline Engine . 31 8.3 Geared Solution . 32 9 Limits of Analysis 33 10 Appendix A - Velocity Triangles 34 11 Appendix B - GasTurb Engine Configuration (Final GTF) 35 12 Appendix C - Material Properties 40 2 Symbols and Abbreviations A Area (m2) L Low-pressure spool alt Altitude (m) LP- Low-pressure amb Ambient LPC LP compressor (fan) -
Energies-13-04157-V2.Pdf
energies Article Aircraft Propellers—Is There a Future? † Pedro Alves * , Miguel Silvestre and Pedro Gamboa C-MAST—Center for Mechanical and Aerospace Science and Technologies, University of Beira Interior, Rua Marquês d’Ávila e Bolama, 6201-001 Covilhã, Portugal; [email protected] (M.S.); [email protected] (P.G.) * Correspondence: [email protected] † This paper is an extended version of our paper published in ICEUBI2019—International Congress on Engineering—Engineering for Evolution, Covilhã, Portugal, 27–29 November 2019. Received: 18 June 2020; Accepted: 7 August 2020; Published: 11 August 2020 Abstract: The race for speed ruled the early Jet Age on aviation. Aircraft manufacturers chased faster and faster planes in a fight for pride and capability. In the early 1970s, dreams were that the future would be supersonic, but fuel economy and unacceptable noise levels made that era never happen. After the 1973 oil crisis, the paradigm changed. The average cruise speed on newly developed aircraft started to decrease in exchange for improvements in many other performance parameters. At the same pace, the airliner’s power-plants are evolving to look more like a ducted turboprop, and less like a pure jet engine as the pursuit for the higher bypass ratios continues. However, since the birth of jet aircraft, the propeller-driven plane has lost its dominant place, associated with the idea that going back to propeller-driven airplanes, and what it represents in terms of modernity and security, has started a propeller avoidance phenomenon with travelers and thus with airlines. Today, even with the modest research effort since the 1980s, advanced propellers are getting efficiencies closer to jet-powered engines at their contemporary typical cruise speeds. -
Propfan, an Alternative for Turbofan Engines
Propfan, an alternative for turbofan engines Tackling the technical design characteristics of a propfan Propfan, an alternative for turbofan engines Introduction The Aviation industry grows with an annual average of 2.5% until 2022, at the same time the fuel prices are expected to increase (FAA, 2017). On a global scale, aviation is responsible for 2.5% of the CO2 emissions from worldwide fossil fuel consumption (Brueckner & Abreu, 2017). For this reason, an innovative propulsive concept is required which offers great improvements in terms of emissions and fuel usage. A designed concept to fulfill this need is the propfan concept, which goes under different names. These names include “open rotor”, “unducted fan”, “ultra-high bypass ratio engine” and “propfan”, which is the term used throughout this fact sheet. Propfans are characterized by two very large diameter fans that are not covered by a nacelle. The ultra-high bypass ratio of the propfan increases propulsive efficiency. This in turn creates the potential of significant reductions in fuel consumption and emissions relative to turbofan engines (Rolls Royce, )(Safran, 2017). The propfan concept was introduced in the 1970s in NASA’s Aircraft Energy Efficiency program (Guynn et al., 2011; Van Zante, 2015) as a response to the oil crisis. However, the development of the propfan was put on hold after the oil prices went down. This reduced the demand for a more fuel efficient engine (Sweetman, 2005). Today, propfans are being developed by several major organizations, including General Electric, Rolls Royce, NASA, Boeing and the FAA. In Europe the concept is being supported by the Clean Sky Program (Lecompte-Boinet, 2017; Rolls Royce, ; Van Zante, 2015). -
1111111111111111111Inuuu11
1111111111111111111inuuu1111111111u~ (12) United States Patent (io) Patent No.: US 9,926,885 B2 Gallagher et al. (45) Date of Patent: Mar. 27, 2018 (54) EFFICIENT, LOW PRESSURE RATIO (56) References Cited PROPULSOR FOR GAS TURBINE ENGINES U.S. PATENT DOCUMENTS (71) Applicant: United Technologies Corporation, 2,258,792 A 4/1941 New Farmington, CT (US) 2,936,655 A 5/1960 Peterson et al. (Continued) (72) Inventors: Edward J. Gallagher, West Hartford, CT (US); Byron R. Monzon, FOREIGN PATENT DOCUMENTS Cromwell, CT (US) EP 0791383 8/1997 (73) Assignee: UNITED TECHNOLOGIES EP 1142850 10/2001 CORPORATION, Farmington, CT (Continued) (US) OTHER PUBLICATIONS (*) Notice: Subject to any disclaimer, the term of this patent is extended or adjusted under 35 McMillian, A.(2008) Material development for fan blade contain- U.S.C. 154(b) by 0 days. ment casing. Abstract. p. 1. Conference on Engineering and Physics: Synergy for Success 2006. Journal of Physics: Conference Series (21) Appl. No.: 15/709,540 vol. 105. London, UK. Oct. 5, 2006. (22) Filed: Sep. 20, 2017 (Continued) (65) Prior Publication Data Primary Examiner Zelalem Eshete US 2018/0023511 Al Jan. 25, 2018 (74) Attorney, Agent, or Firm Carlson, Gaskey & Olds, Related U.S. Application Data P.C. (63) Continuation of application No. 15/252,689, filed on Aug. 31, 2016, which is a continuation of application (57) ABSTRACT (Continued) A gas turbine engine includes a bypass flow passage that has (51) Int. Cl. an inlet and defines a bypass ratio in a range of approxi- F02K 3/075 (2006.01) mately 8.5 to 13.5.