Analysis of Drilling Tool Life—A Review
Total Page:16
File Type:pdf, Size:1020Kb
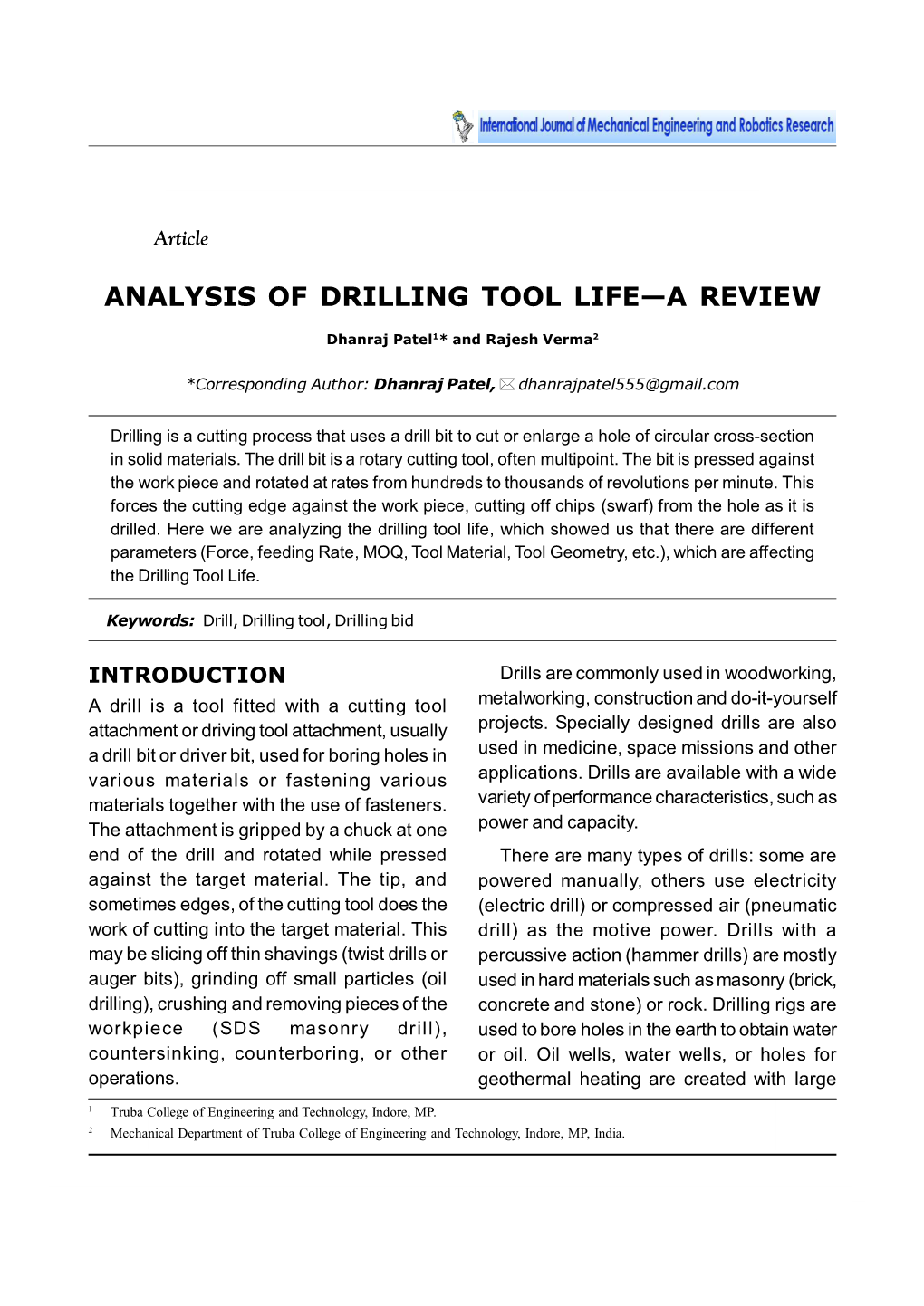
Load more
Recommended publications
-
TOOLS and EQUIPMENT Orthotic 561
TOOLS AND EQUIPMENT Orthotic 561 Tools Shoe Stretchers............................562 Brannock Measuring Device..................562 Mixing Bowls ..............................562 Aluminum Cast Mandrels ....................562 Laminating Fixtures.........................563 Vises and Yates Clamps.................563-564 Measuring Devices .....................564-567 Hex Sets and Balldrivers.................567-569 Screw and Drill Gages ......................569 Cutting Nippers ............................570 Plastering Tools............................571 Shears and Scissors ....................571-572 Blades, Knives and Surforms .............572-575 Rivets, Punch Sets and Eyelets ...........576-579 Reamers .................................579 Needle Kit ................................579 Deburring Tool.............................579 Rout-A-Burr ...............................579 Precision Oiler.............................580 Countersinks ..............................580 Adjustable Bits.............................580 Tools Ball Set Tool . 580 Micro Torches and Heat Guns ............580-582 Cast Spreaders and Cutters ..............583-584 Alignment Fixtures .........................584 Benders and Contouring Iron .............584-585 Equipment Carvers, Cutters and Routers.............585-588 Sanding Accessories............ 589-591, 601-603 Sewing and Patching Machines ...............592 Drill Press ................................593 Band Saws . .594-595 Dust Collectors ........................596-597 -
Grinding Your Own Lathe Tools
WEAR YOUR SAFETY GLASSES FORESIGHT IS BETTER THAN NO SIGHT READ INSTRUCTIONS BEFORE OPERATING Grinding Your Own Left Hand Right Hand Boring Tool Cutting Tool Cutting Tool Lathe Tools As with any machining operation, grinding requires the Dressing your grinding wheel is a part of maintaining the utmost attention to “Eye Protection.” Be sure to use it when bench grinder. Grinding wheels should be considered cutting attempting the following instructions. tools and have to be sharpened. A wheel dresser sharpens Joe Martin relates a story about learning to grind tools. “My by “breaking off” the outer layer of abrasive grit from the first experience in metal cutting was in high school. The wheel with star shaped rotating cutters which also have to teacher gave us a 1/4" square tool blank and then showed be replaced from time to time. This leaves the cutting edges us how to make a right hand cutting tool bit out of it in of the grit sharp and clean. a couple of minutes. I watched closely, made mine in ten A sharp wheel will cut quickly with a “hissing” sound and minutes or so, and went on to learn enough in one year to with very little heat by comparison to a dull wheel. A dull always make what I needed. I wasn’t the best in the class, wheel produces a “rapping” sound created by a “loaded just a little above average, but it seemed the below average up” area on the cutting surface. In a way, you can compare students were still grinding on a tool bit three months into the what happens to grinding wheels to a piece of sandpaper course. -
Ld-16B - Ld-16Ba - Ld-16Be - Ld-16Bt
RAIL DRILL LD-16B - LD-16BA - LD-16BE - LD-16BT ENGLISH OPERATION AND MAINTENANCE MANUAL 1 16 M 187 E INDEX page 1. General characteristics ............................................................................................................................................... 6 2. Accessories supplied with the drill ........................................................................................................................ 7 3. Accessories to be ordered separately ................................................................................................................... 9 4. Spindle advance lever ................................................................................................................................................ 13 5. Motor ON/OFF switch (EMERGENCY) ................................................................................................................... 14 6. LED worklights ON/OFF switch ............................................................................................................................... 14 7. LED indicator .................................................................................................................................................................. 15 8. "Drilling assistance" function ................................................................................................................................... 15 9. Rechargeable battery ................................................................................................................................................ -
Optimization of Broaching Tool Design
Intelligent Computation in Manufacturing Engineering - 4 OPTIMIZATION OF BROACHING TOOL DESIGN U. Kokturk, E. Budak Faculty of Engineering and Natural Sciences, Sabanci University, Orhanli, Tuzla, 34956, Istanbul, Turkey Abstract Broaching is a very common manufacturing process for the machining of internal or external complex shapes into parts. Due to the process geometry, broaching tool is the most critical parameter of the broaching process. Therefore, optimal design of the tools is needed in order to improve the productivity of the process. In this paper, a methodology is presented for optimal design of the broaching tools by respecting the geometric and physical constraints. The method has also been implemented on a computer code. Keywords: Broaching, optimization, tooling 1 INTRODUCTION Broaching is commonly used for machining of internal or methods that use databases [6], have also been used. external complex profiles that are difficult to generate by Combinations of different approaches have also been other machining processes such as milling and turning. utilized with a mixture of fuzzy basics [7]. Erol and Ferrel Originally, broaching was developed for noncircular [8] also used fuzzy methods among many others. In most internal profiles and keyways. The process is very simple, of these studies, the mechanics of the process such as and decreases the need for talented machine operator forces, deflections, vibrations etc., other than tool wear, while providing high production rate and quality. Because were not included in the analysis. of the straight noncircular motion, very high quality surface Although there have been many studies on various finish can be obtained. In addition, roughing and finishing machining processes, there has been only a few on operations can be completed in one pass reducing total broaching. -
Types of Tap
Types of Tap HAND TAPS ISO 529 These are straight flute general purpose tools which can be used for both machine or hand tapping. They are generally the most economical tool for use on production runs, but are best on materials that produce chips, or where the swarf breaks readily. Where deep holes are to be tapped, in materials which produce stringy swarf, serial taps may be needed, especially for coarse threads. ISO 529 hand taps can be supplied in sets of three; bottom, second and taper leads, or individually. BOTTOM TAPS have a chamfer (lead) of 1–2 threads, the angle of the lead being around 18 degrees per side. They are used to produce threads close to the bottom of blind holes. SECOND TAPS have a lead of 3-5 threads at 8 degrees per side. They are the most popular and can be used for through holes, or blind holes where the thread does not need to go right to the bottom. TAPER TAPS have a lead of 7-10 threads at 5 degrees per side. The taper lead distributes the cutting force over a large area, and the taper shape helps the thread to start. They can therefore be used to start a thread prior to use of second or bottom leads, or for through holes. IMPORTANT NOTE ON TERMINOLOGY! In the U.K. bottom taps are often referred to as ‘plugs’. In North America second taps are often referred to as ‘plugs’! This can easily lead to confusion. To avoid problems when ordering it is best to use the terms bottom, second and taper. -
Introduction to Turning Tools and Their Application Identification and Application of Cutting Tools for Turning
Introduction to Turning Tools and their Application Identification and application of cutting tools for turning The variety of cutting tools available for modern CNC turning centers makes it imperative for machine operators to be familiar with different tool geometries and how they are applied to common turning processes. This course curriculum contains 16-hours of material for instructors to get their students ready to identify different types of turning tools and their uses. ©2016 MachiningCloud, Inc. All rights reserved. Table of Contents Introduction .................................................................................................................................... 2 Audience ..................................................................................................................................... 2 Purpose ....................................................................................................................................... 2 Lesson Objectives ........................................................................................................................ 2 Anatomy of a turning tool............................................................................................................... 3 Standard Inserts .............................................................................................................................. 3 ANSI Insert Designations ............................................................................................................. 3 Insert Materials -
High Pressure Waterjet
Application Note High Pressure Waterjet A water jet is a cutting tool capable of slicing metal or other materials by using a narrow stream of water at high velocity and pressure, or a mixture of water and an abrasive substance. The process erodes the materials in the same way as water erosion found in nature but accelerated and concentrated through high pressure. It is often used in the fabrication or manufacture of parts for machinery and other industries. It is used in applications in the mining to aerospace industries where it performs operations such as cutting, shaping, carving, and reaming. The water jet is usually connected to a high-pressure water pump (Viatran supplies units at 60K PSI) where the water is then ejected from the nozzle, cutting through the material by spraying it with the jet of high-speed water. Adding suspended grit or other abrasives, such as garnet and aluminum oxide, can accelerate this process. Because the characteristics of the cutting stream can be easily modified, water jets can be used to cut materials from processed food to exotic metals. There are few materials that cannot be effectively cut with a water jet cutter. Two of these are tempered glass and certain ceramics are resistant to water jet cutting. Water jet cuts are not typically limited by the thickness of the material, and are capable of cutting materials over a foot (30 cm) thick. An important benefit of the water jet cutter is the ability to cut material without compromising the material's inherent structure. The effects of heat are minimized by the water jet. -
Broaching Principles
Broaching Principles Broaching is a machining process that pushes or pulls a cutting tool (called a broach) over or through the surface being machined. Its high-production, metal-removal process is sometimes required to make one-of-a-kind parts. The concept of broaching as a legitimate machining process can be traced back to the early 1850s. Early broaching applications were cutting keyways in pulleys and gears. After World War 1, broaching contributed to the rifling of gun barrels. Advances in broaching machines and form grinding during the 1920s and 30s enabled tolerances to be tightened and broaching costs to become competitive with other machining processes. Today, almost every conceivable type of form and material can be broached. It represents a machining operation that, while known for many years, is still in its infancy. New uses for broaching are being devised every day. Figure 1. Cutting action of a broaching tool. Broaching is similar to planing, turning, milling, and other metal cutting operations in that each tooth removes a small amount of material (Figure 1 ). Figure 2. Typical push keyway broaching tools and a shim. The broaching tool has a series of teeth so arranged that they cut metal when the broach is given a linear movement as indicated in figure 1. The broach cuts away the material since its teeth are progressively increasing in height. Properly used, broaching can greatly increase productivity, hold tight tolerance, and produce precision finishes. Tooling is the heart of broaching. The broach tool's construction is unique for it combines rough, semi-finish, and finish teeth in one tool (Figure 3). -
Waterjet Cutting
Waterjet Cutting Waterjet cutting is one of today’s fastest-growing technologies and is quickly becoming a leading fabrication process. Waterjet cutting uses a high-pressure stream of water with an abrasive such as garnet to make the cut. No heat is generated during Waterjet cutting, eliminating the risk of material distortion. Edge finish of Waterjet machined parts is smooth and satiny, with no jagged edges, slag or burrs, eliminating the need for other finishing processes such as grinding. Water jet cutting technology utilizes high pressure water with an abrasive substance to create a cutting tool that travels at three times the speed of sound. With this tool, virtually any material can be cut with or without an abrasive in some Hi-Tech Welding is a one-stop service center for welding and cases. The Mitsubishi control, combined with a CAD-CAM fabrication in Lee’s Summit, MO. generated CNC code, allows for simple or complex shapes to be cut. Speed and accuracy (compensation is within In 1985 Hi-Tech Welding originally began as a tool and die welding ±0.005” per 36” length) are easy to achieve with the Waterjet facility. Over the years it has grown into a full welding and fabrication Intelligent Taper ControlTM System. shop. Waterjet Cuts Virtually Any Material Services offered • Laser Welding Waterjet cutting is suitable for nearly any material, and can • Tool and Die Welding cut any material up to 6” thick. • Waterjet Cutting • Welding Repair We have software that allows us to make high quality ducts, • Repair and Refurbishment fittings, flanges and brackets. -
Drilling 22 | Drilling | Overview Bosch Accessories for Power Tools 09/10 Your Guide to the Right Drill Bit
Drilling 22 | Drilling | Overview Bosch Accessories for Power Tools 09/10 Your guide to the right drill bit. These information pages are designed to help users. They cover the correct use of the appropriate power tool and the various drill bits for commonly-used materials. The charts given below are only intended as recommendations and cannot be regarded as a complete guide. For more detailed queries, please contact Bosch directly. The fact that power tools and drill bits are mutually dependent is often ignored. It is only once this relationship has been identifi ed and taken into account that the service life of both the tool and its drill bit can be optimised. Drill/Impact drill Drill/Impact drill Drill/Impact drill Drill/Impact drill up to 600 watts up to 700 watts up to 1010 watts up to 1150 watts Cordless drill/driver Cordless drill Cordless impact drill Metal drill bits Sheet metal cone bit up to 20 mm over 30 mm Steel drill bit up to 10 mm up to 13 mm up to 20 mm Wood drill bit Wood drill bit up to 15 mm up to 25 mm up to 32 mm Auger bit up to 18 mm up to 32 mm Installation and form- work drill bits 18 mm 30 mm Flat drill bits up to 40 mm Forstner bit up to 50 mm TC-tipped hinge-boring bit up to 50 mm Concrete drill bit Concrete drill bit up to 15 mm up to 20 mm up to 25 mm Masonry drill bit up to 12 mm up to 18 mm up to 24 mm up to 30 mm Core cutters up to 68 mm up to 82 mm Diamond core edge sinkers up to 82 mm Multi-purpose and rotary drill bits Multi-purpose drill bit 14 mm Glass drill bit 12 mm Holesaws up to 40 mm up to 60 mm up to 80 mm up to 152 mm Bosch Accessories for Power Tools 09/10 Drilling | Overview | 23 Working on metal and plastic. -
Common Saw Types
Common Saw Types “Basic” Handsaw This is the most recognizable and the simplest to operate of all of saws. It works on wood of all types but is best for “soft” woods. Can be used for all types of cuts. Hack Saw This type of handsaw features a fine-toothed replaceable blade on a C-frame. Commonly used for cutting metals and plastics. Japanese Saws A saw type with a thinner blade with crosscut teeth on one side and rip teeth on the other. These saws are more often found in a fine woodworking or furniture making situation. Coping Saw Popular with artists, this simple but useful cutting tool consists of a thin replaceable blade in a C-shaped frame that uses interchangeable blades for both metal and wood. It can cut tight radiuses but perhaps its most useful feature is the ability to remove the blade and thread it through a drilled hole to cut inside profiles. Jigsaw/Reciprocating Saw If you’ve ever needed to cut a custom shape out of a sheet of plywood or even plastic, this is a great saw. If a perfectly straight line is what you need, then leave this tool on the shelf. Even in the hands of a skilled operator the blade will drift easily. Circular Saw This saw is the standard for making cross and rip cuts. If you van only have one powered saw, this is the one. When it is paired with a saw guide it can make surprisingly accurate cuts. Table Saw Ripping and beveling are the things the table saw does best. -
Utilization of Waste by Preparing the Product from Swarf Forging of Alloy
et International Journal on Emerging Technologies 6(2): 181-183(2015) ISSN No. (Print) : 0975-8364 ISSN No. (Online) : 2249-3255 Utilization of Waste by Preparing the Product from Swarf Forging of Alloy Steel (16MNCR5) Abid Nazir and Harvinder Lal Department of Mechanical Engineering, RIET, Phagwara, (PB), India (Corresponding author: Abid Nazir) (Received 01 October, 2015 Accepted 06 November 2015) (Published by Research Trend, Website: www.researchtrend.net) ABSTRACT: The aim of thesis is to prepare the product from swarf forging of alloy steel (16MnCr5). This thesis is an example of how the waste fraction can be transferred from waste to a resource that can be used in other industrial processes. It offers both environmental and economic benefits. Swarf forging gives better control, environmental credits, cost savings an increased margins. Swarf collected from lathe, milling, drill or any other cutting machine is cleaned by degreasing, pickling and acid pickling. Preliminary heat treatment is done to eliminate the work hardening, moisture content and impurity content. Swarf can be continuous, discontinuous or powder form. After collection of swarf, put in mild steel tube for compression. Compression of swarf is done by hydraulic press. The force is applied on piston which is inserted in tube. After compression, swarf which is in form of cylinder is taken out. After this heat the samples are heated and forged with the help of manual hammers or with help of hydraulic hammer. After forging hardness, density and microstructure are checked. The values indicate that product made by swarf forging can be used for low load application like door handles, hangers etc.