E3 M.5 FIG. 3
Total Page:16
File Type:pdf, Size:1020Kb
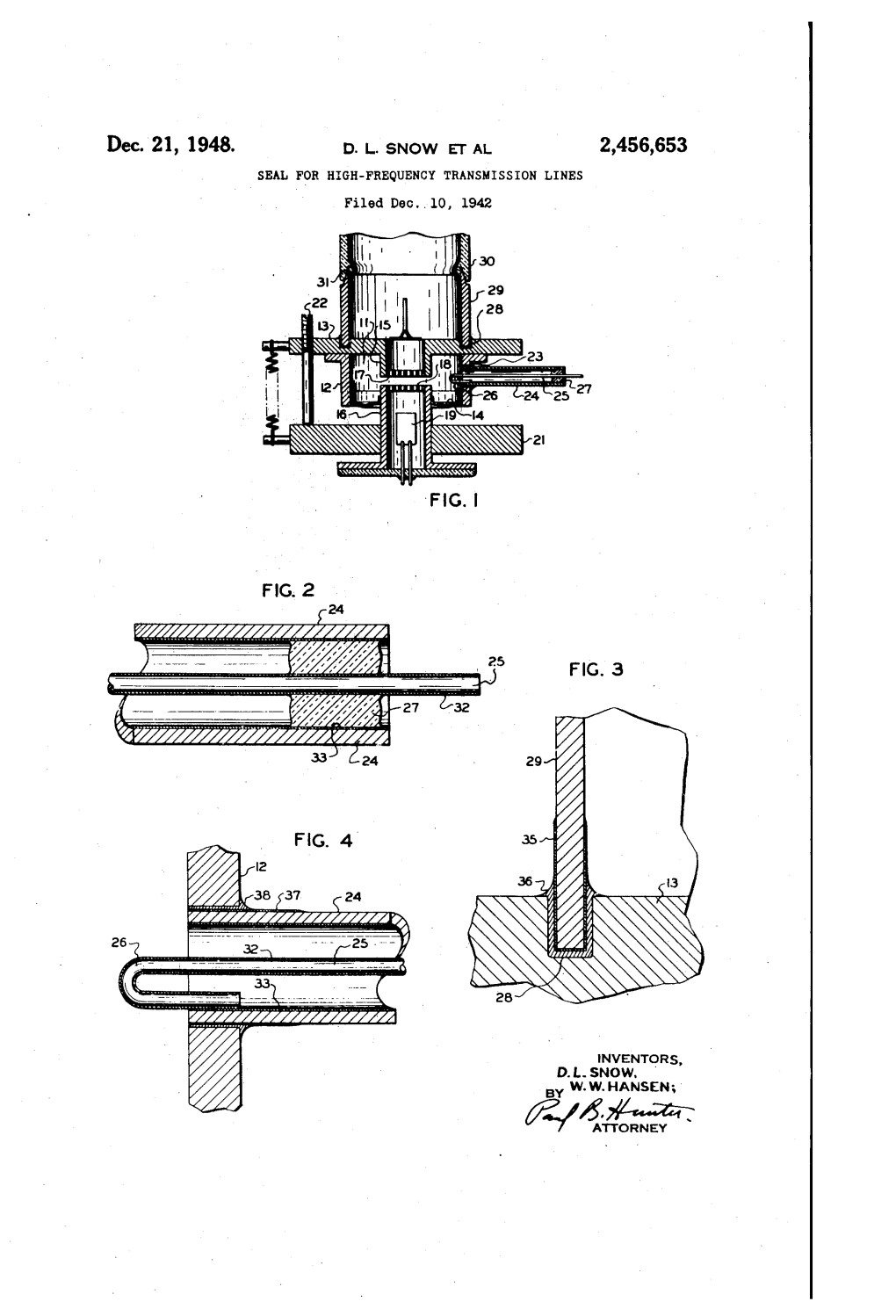
Load more
Recommended publications
-
WO 2016/193753 A2 8 December 2016 (08.12.2016) P O P C T
(12) INTERNATIONAL APPLICATION PUBLISHED UNDER THE PATENT COOPERATION TREATY (PCT) (19) World Intellectual Property Organization I International Bureau (10) International Publication Number (43) International Publication Date WO 2016/193753 A2 8 December 2016 (08.12.2016) P O P C T (51) International Patent Classification: (74) Agent: BOULT WADE TENNANT; Verulam Gardens, A61B 90/00 (2016.01) 70 Gray's Inn Road, London WC1X 8BT (GB). (21) International Application Number: (81) Designated States (unless otherwise indicated, for every PCT/GB20 16/05 1649 kind of national protection available): AE, AG, AL, AM, AO, AT, AU, AZ, BA, BB, BG, BH, BN, BR, BW, BY, (22) International Filing Date: BZ, CA, CH, CL, CN, CO, CR, CU, CZ, DE, DK, DM, 3 June 2016 (03.06.2016) DO, DZ, EC, EE, EG, ES, FI, GB, GD, GE, GH, GM, GT, (25) Filing Language: English HN, HR, HU, ID, IL, IN, IR, IS, JP, KE, KG, KN, KP, KR, KZ, LA, LC, LK, LR, LS, LU, LY, MA, MD, ME, MG, (26) Publication Language: English MK, MN, MW, MX, MY, MZ, NA, NG, NI, NO, NZ, OM, (30) Priority Data: PA, PE, PG, PH, PL, PT, QA, RO, RS, RU, RW, SA, SC, 62/170,768 4 June 2015 (04.06.2015) US SD, SE, SG, SK, SL, SM, ST, SV, SY, TH, TJ, TM, TN, TR, TT, TZ, UA, UG, US, UZ, VC, VN, ZA, ZM, ZW. (71) Applicant: ENDOMAGNETICS LTD. [GB/GB]; Jef freys Building, St John's Innovation Park, Cowley Road, (84) Designated States (unless otherwise indicated, for every Cambridge, Cambridgeshire CB4 0WS (GB). -
Sustainable Lunar In-Situ Resource Utilisation = Long-Term Planning
Sustainable Lunar In-Situ Resource Utilisation = Long-Term Planning Alex Ellery Canada Research Professor (Space Robotics) Department of Mechanical & Aerospace Engineering Carleton University Ottawa, CANADA Water + Volatile Mining . Sustainability requires consideration of future ISRU requirements . Water mining by heating regolith – higher temperatures yield highly valuable volatiles at 700oC releasing 90% of volatiles esp from smaller ilmenite particles: H2, He, CO, CO2, CH4, N2, NH3, H2S, SO2, Ar, etc . Carbon compounds = very valuable resource . Fractional distillation for well-separated fractions: He (4.2 K), H2 (20 K), N2 (77 K), CO (81 K), CH4 (109 K), CO2 (194 K) and H2O (373 K) Any Old Iron . Hydrogen reduction of ilmenite at ~1000oC to create oxygen, iron and rutile FeTiO3 + H2 → Fe + TiO2 + H2O and 2H2O → 2H2 + O2 . Wrought iron is tough & malleable for tensile structures . TuNiCo metals + W from nickel-iron meteorite impact craters (Mond process) . Tool steel (<2% C + 9-18% W) for milling tools . Silicon (electrical) steel/ferrite (<3% Si and >97% Fe) for electromagnets and motor cores . Kovar (53.5% Fe, 29% Ni, 17% Co, 0.3% Mn, 0.2% Si and <0.01% C) – type of fernico alloy with high-temp electrical conductivity . Permalloy (20% Fe + 80% Ni) for magnetic shielding Functionality Lunar Material Tensile structures Wrought iron – Aluminium Minimal Demandite Compressive structures Cast iron – Aluminium Elastic structures Steel/Al springs/flexures Silicone elastomers Thermal conductor straps Iron/Nickel/Cobalt/Aluminium Tungsten Thermal insulation Glass (silica fibre) Ceramics such as SiO2 and Al2O3 Demandite for generic High thermal tolerance Tungsten, Al2O3 Thermal sources Fresnel lenses/mirrors (optical structures) robot/spacecraft Electrical heating (iron/nickel/tungsten) Electrical conduction Fernico (e.g. -
Nickel and Its Alloys
National Bureau of Standards Library, E-01 Admin. Bldg. IHW 9 1 50CO NBS MONOGRAPH 106 Nickel and Its Alloys U.S. DEPARTMENT OF COMMERCE NATIONAL BUREAU OF STANDARDS THE NATIONAL BUREAU OF STANDARDS The National Bureau of Standards^ provides measurement and technical information services essential to the efficiency and effectiveness of the work of the Nation's scientists and engineers. The Bureau serves also as a focal point in the Federal Government for assuring maximum application of the physical and engineering sciences to the advancement of technology in industry and commerce. To accomplish this mission, the Bureau is organized into three institutes covering broad program areas of research and services: THE INSTITUTE FOR BASIC STANDARDS . provides the central basis within the United States for a complete and consistent system of physical measurements, coordinates that system with the measurement systems of other nations, and furnishes essential services leading to accurate and uniform physical measurements throughout the Nation's scientific community, industry, and commerce. This Institute comprises a series of divisions, each serving a classical subject matter area: —Applied Mathematics—Electricity—Metrology—Mechanics—Heat—Atomic Physics—Physical Chemistry—Radiation Physics—Laboratory Astrophysics^—Radio Standards Laboratory,^ which includes Radio Standards Physics and Radio Standards Engineering—Office of Standard Refer- ence Data. THE INSTITUTE FOR MATERIALS RESEARCH . conducts materials research and provides associated materials services including mainly reference materials and data on the properties of ma- terials. Beyond its direct interest to the Nation's scientists and engineers, this Institute yields services which are essential to the advancement of technology in industry and commerce. -
A Review of Solder Glasses R
Electrocomponent Science and Technology (C) Gordon and Breach Science Publishers 1975, Vol. 2, pp. 163-199 Printed in Great Britain A REVIEW OF SOLDER GLASSES R. G. FRIESER IBM System Products Division, East FishMll, Hopewell Junction, New York 12533 (Received June 16, 19 75) A compilation of data on solder glasses from the literature is presented. Sources are: Chemical Abstracts, Ceramic Abstracts, Abstracts in Physics ana Chemistry of Glasses, and pertinent books. Even though not exhaustive, domestic and foreign sources are included. INTRODUCTION between a glass and a metal. The bulk of those glasses referred to in the literature as solder glasses belong to Data on solder glasses are scattered throughout the the lead borate or lead borosilicate system. However, technological literature, but primarily throughout the other systems can and have been used, and are patent and trade literature of glass manufacturers. In discussed later in this section. most cases, even in the past reviews, the compiled With few exceptions, present literature (both information was concerned with the solution of patent and techmcal) is concerned with the solution specific engineering projectsl- 1. of specific glass-to.metal sealing problems. This is Primary sources for this review were: (a)Chemical quite understandable from an historical point of view. Abstracts, (b)Ceramic Abstracts and (c) Abstracts in With the invention and manufacture of light bulbs, Physics and Chemistry of Glasses published back to glass-to-metal seal technology became an engineering 1948. From these primary sources and from pertinent and manufacturing problem of considerable economic books,2,12,13 81 articles and 88 patents were ab- importance. -
Osram-GEC Lamp Glass Catalogue 1959
@, ffra$$ Iry0RK$ THE GENERAL ELECTR]C CO. LTD EAST LANE, WEMBLEYi MIDDLESEX Telephone: Arnold 4321 Telegrams: Osram, Fhone, Wembley IlITNODUCTItlIT Since the last edition of this publication, many changes and advances have taken place, both in the manufacturing methods and in the range of glasses available. Over a dozen new glasses are referred to in this issue and the important physical properties are summarized in a convenient table for quick reference. We offer this handy and condensed account of our products for the convenience of our many friends in the Glass Industry hoping that it will be at one and the same time an interesting and useful reference book. 054635 (March 1959) Printed in England p & M fiTA$Sil$ il{ANI][ACTI]RAil AT TIIil fr.t.c. frta$$ Iry0BK$ In the following pages, technical dataaregiven for a number of glasses manufactured by the G.E.C. Glass Works. In every case they are special-purpose glasses, carefully specified as to composition and physical properties. Control is exercised during manufacture on those physical properties which are most important for the purpose for which the individual glass is to be employed. Of the glasses listed, some are manufactured at the Company's Wembley works and others at Lemington-on-Tyne, Northumberland. In general, all pot-melted and special glasses are melted at Lemington, manufacture at Wembley being confined to the automatic production of bulbs and tubing from X.4., X.8., L.l. and M.6. Glasses described in the following pages are tabulated below. frta$st$ Page L.1 Lead Glass 6 x.8 Soda Glass (tubing) x.4 Lime Soda Glass (machine-blown) 5 x.413 Lime Soda Glass (mouth-blown) t1 M.6 Neutral Glass 8 H.R.9 Heat-Resisting Glass - Pres6ings l8 SBN.I24 Glass for sealing to Kovar and Nilo.K. -
WO 2018/183396 Al 04 October 2018 (04.10.2018) W !P O PCT
(12) INTERNATIONAL APPLICATION PUBLISHED UNDER THE PATENT COOPERATION TREATY (PCT) (19) World Intellectual Property Organization International Bureau (10) International Publication Number (43) International Publication Date WO 2018/183396 Al 04 October 2018 (04.10.2018) W !P O PCT (51) International Patent Classification: (US). CHRISTIANSEN, Daniel, Thomas; 1263 Califor B29C 64/321 (2017.01) B29C 64/209 (2017.01) nia Street, Mountain View, CA 94041 (US). ROMANO, B29C 64/393 (2017.01) B33Y 50/02 (2015.01) Richard, Joseph; 525 Felix Way, San Jose, CA 95 125 B29C 64/357 (20 17.0 1) B33Y 40/00 (20 15.0 1) (US). VITANOV, Anatolii; 4755 El Rey Avenue, Fre B29C 64/264 (2017.01) mont, CA 94536 (US). LAPPEN, Alan, Rick; 394 Avenida Abetos, San Jose, CA 95 123 (US). (21) International Application Number: PCT/US20 18/024667 (74) Agent: LYFORD, Nicholas et al; Velo3D, Inc., 511 Divi sion Street, Campbell, CA 95008 (US). (22) International Filing Date: 27 March 2018 (27.03.2018) (81) Designated States (unless otherwise indicated, for every kind of national protection available): AE, AG, AL, AM, (25) Filing Language: English AO, AT, AU, AZ, BA, BB, BG, BH, BN, BR, BW, BY, BZ, (26) Publication Language: English CA, CH, CL, CN, CO, CR, CU, CZ, DE, DJ, DK, DM, DO, DZ, EC, EE, EG, ES, FI, GB, GD, GE, GH, GM, GT, HN, (30) Priority Data: HR, HU, ID, IL, IN, IR, IS, JO, JP, KE, KG, KH, KN, KP, 62/477,848 28 March 2017 (28.03.2017) US KR, KW, KZ, LA, LC, LK, LR, LS, LU, LY, MA, MD, ME, (71) Applicant: VEL03D, INC. -
Total-Metals.Pdf
Extra slides are added to the original powerpoint Younes Ataiiyan Chapter 11- Part I History of metals You are not responsible for part I Chapter 11- Gold, Silver, Copper Earliest known metals, Why? •They can be found in metallic state in nature (not necessarily pure) •They are malleable Chapter 11- Copper History The name originates from the Latin word cyprium, after the island of Cyprus. Copper was associated with the goddess named Aphroditehttp://www.facts- about.org.uk/science/ Venus in- elementGreek-copper.htm and Roman mythology. There are reports of copper beads dating back to 9000BC found in Iraq. Methods for refining copper from its ores were discovered around 5000BC and a 1000 or so years later it was being used in pottery in North Africa. around 5000 years ago it was discovered that when copper is mixed with other metals the resulting alloys are harder than copper itself (BRONZE IS COPPER AND TIN) http://www.webelements.com/webelements/scholar/elements/copper/history.html Chapter 11- Copper Properties • Malleable + Durable • High Electrical/Thermal conductivity • High corrosion resistance • Non-Magnetic Chapter 11- Copper Properties Electrical/Thermal conductivity • Highest electrical conductivity (after Silver) • Used in electrical wiring, pipes, roofing, Culinary. Chapter 11- Copper Colors and alloying elements German Silver Chapter 11- Copper Minerals • Turquoise • Dioptase • Cuprite • Copper pyrite • Azurite Chapter 11- Copper Mines Chapter 11- Copper Mines Chapter 11- Copper Mines Chapter 11- Copper Mines Chapter 11- Copper Odd Facts • Excessive consumption of foods high in copper, such as organ meats and oysters can cause Wilson's disease . • The average home today contains about 400 pounds of copper for electrical wiring, water pipes and appliances. -
Manual S/N Prefix
I. : HP Archive .. This vintage Hewlett Packard document was preserved and distributed by www. hparchive.com ' Please visit us on the web ! .. On-line curator: Tony Gerbic 412A DC VACUUM TUBE VOLTMETER SERIALS PREFIXED: 004- OPERATING AND SERVICING MANUAL MODEL 412A DC VACUUM TUBE VOLTMETER SERIALS PREFIXED: 004- Copyright HEWLETT-PACKARD COMPANY 1959 275 PAGE MILL ROAD, PALC ALTO, CALIFORNIA, U. S. A. Page 1 of 2 Model 412A SPECIFICATIONS TOLTMETER Voltage Range: Positive and negative voltages from 1 millivolt full scale to 1000 volts ful scale in thirteen ranges. Accuracy: *l%of full scale on any range. Input Resistance: 10 megohms *l%on 1 mv, 3 mv, and 10 mv ranges. 30 megohms *l%on 30 mv range. 100 megohms +l%on 100 mv range. 200 megohms *l% on 300 mv range and above. AC Rejection: A voltage at power line or twice power line frequency 40 db greater than ful scale affects reading less than 1%. Peak voltage must not exceed 1500 volts {MMETER Current Range: Positive and negative currents from 1 microampere full scale to 1 amperc full scale in thirteen ranges. Accuracy: *2% of full scale on any range. Input Resistance: Internal Shunt Full Scale Internal Shunt Full Scale Range Resistance* Voltage Drop Range Resistance* Voltage Drop .001 ma 1000 ohms 1 mv 1 ma 1 ohm 1 mv .003 ma 316 ohms 0.9486 mv 3 ma 0.316 ohm 0.9486 mv .01 ma 100 ohms 1 mv 10 ma 0.1 ohm 1 mv .03 ma 31.6 ohms 0.9486 mv 30 ma 0.1 ohm 3 mv .1 ma 10 ohms 1 mv 100 ma 0.1 ohm 10 mv .3 ma 3.16 ohms 0.9486 mv 300 ma 0.1 ohm 30 mv 1000 ma 0.1 ohm 100 mv * For total insertion resistance add 0.07 ohms copper lead resistance at 25OC. -
United States Patent Office Patented Aug
3,396,015 United States Patent Office Patented Aug. 6, 1968 2 solution specifically addressed to nickel-cobalt-iron alloys 3,396,015 of the Kovar type. POWDER ROLLING OF NICKELRON As used herein, the term "nickel-cobalt-iron electrical COBALT ALLOYS Jerry C. La Plante, Hempstead, N.Y., assignor to Alloys alloy' is defined to include all of the following alloy com Unlimited, Inc., Melville, N.Y. 5 positions and minor variations thereof. This is thought to No Drawing. Filed Jan. 11, 1968, Ser. No. 697,037 be an adequate designation, as these alloys are believed 9 Claims. (Cl. 75-214) to be the only alloys in the nickel-cobalt-iron ternary sys tem in commercial use. ABSTRACT OF THE DISCLOSURE 10 Alloy Name Fe Ni Co C Mn The alloy 29 Ni, 17 Co, balance iron is prepared as a Kovar. --------------- 54 29 17 -------------------- Nilo-K----- - 54 29 17 -------------------- fine powder in the fully annealed condition and is rolled Fernico.-------- -- 54 28 18 -------------------- without added binders into a green strip of about 80% Fenico CG518 -- 53.8 28.0 17.9 0.06 0.23 Fernico CG604 -- 54. 27.6 17.9 0.06 0.18 density. After sintering at 2000 F. for at least two hours, Rodar----------- - 53.7 29.0 17.0 ---------- 0.30 it is reduced by rolling about 30 to 50%, after which it is Therlo-----...-------- 54 29 17 resintered. By controlling coil and roll diameters, edge (Kovar is the registered trademank of Westinghouse Co., Therlo is the breaking, curling and cracking are prevented. -
Metals Used in Valve Manufa
Metals used in Valve Manufacture http://www.r-type.org/static/glas-met.htm Sealing of Glass to Other Materials Taken from Vacuum Tubes by K Spangenberg (1948) {1001} Very few vacuum tubes have been built, as of 1948, with no glass in them. Even in the so-called ' metal tubes ' the leads are brought into the tube through a glass bead sealed into an eyelet. In experimental and developmental work, glass is used even more extensively and glass-to-metal sealing assumes even greater importance. Sealing of Small Leads into Glass The problem of bringing leads into vacuum tubes is ever present. The principal problem involved is that of finding a metal of which the expansion coefficient matches that of the glass quite closely. Since the expansion coefficient of metals is nearly constant with temperature while that of glass generally increases with temperature, the perfect combination is seldom found. However, if the diameter of the lead is small, a considerable mismatch in expansion can be tolerated. Thus with tungsten, of which the expansion coefficient is 4 ppm (parts per million) per °C, leads of diameter 0.020 inches or less can be sealed into Pyrex glass, of which the expansion coefficient is 3.3 ppm per °C, whereas leads of diameter as great as 0.125 inches can be sealed into Nonex glass, of which the expansion coefficient is 3.6 ppm per °C, without cracking. Because the coefficient of expansion of platinum, 9 ppm per °C, is very nearly the same as that of G-12 soft lime glass, 8.7 ppm per °C, lead size of this glass-metal combination is limited only by the budget. -
Space Portal Alex Ellery.Pdf
Self-Replicating Machines are the only means through which to spread through the Solar System Alex Ellery Canada Research Professor Department of Mechanical & Aerospace Engineering Carleton University Ottawa, CANADA Space Portal Commercial Space Lecture Series, 2 Jun 2021 Power of Self-Replication § Self-replication is the ONLY robust approach to space exploration § Self-replication offers exponential growth in productive capacity P= (1 + �)! where r>1 § This is a cellular approach in which each cell factory is identical § Consider launch of a single 10 tonne self-replicating factory to the Moon at a cost of $7.5 B Number of offspring Number of Population Specific per generation generations Cost ($/kg) 1 10 1024 2 7 2187 <$1000/kg 2 13 1,594,323 <$1.25/kg § Cumulative population is >1.5 x 106 within 13 generations § Initial capital cost of $7.5 B is amortised over an exponentially increasing productive capacity § For r=2 over 13 generations, specific cost to the Moon has dropped from $750,000/kg to <50 cent/kg of productive capacity § If each 10 tonne factory takes 6 months to build, we have >1.5 million factories in 6.5 years § If each of the106 factories produces 103 solar power satellites, we have109 SPS units § We could supply our global energy needs cleanly from space § SELF-REPLICATION EFFECTIVELY SIDESTEPS LAUNCH COSTS Universal Constructor ⊃ Self Replicator § John von Neumann – a sufficient (but not necessary) condition for self-replication is universal construction § Universal constructor is a kinematic machine that can manufacture -
United States Patent O" Ice Patented Oct
3,473,999 United States Patent O" ice Patented Oct. 21, 1969 l 2 sion of the vitreous seal to a thermally controlled crystal 3,473,999 lized seal. GLASS 0R METAL SURFACES SEALED It will be appreciated by those versed in the subject BY Si02-Al2O3-WlgO COMPOSHTIONS AND art that the above-mentioned complicated procedures are METHOD OF MAKING difficult to effect, time consuming and expensive and, if Gordon M. Mnchow, Sylvania, Ohio, assignor to Owens llllinois, l[nc., a corporation of Ohio composite articles can be ‘fabricated and seals compound No Drawing. Continuation-impart of application Ser. No. ed by a procedure which essentially eliminates the dis 567,350, July 25, 1966. This application Nov. 5, 1968, advantages associated with the prior art, such procedure Ser. No. 773,667 would have a de?nite commercial value to the present art. Int. Cl. B32b 17/06, 15/04 Likewise, it will be appreciated by those skilled in the in US. Cl. 161-193 17 Claims stant art that if articles of commerce and science made of both clear and opaque parts and thermally crystallized seals can be effected by a relatively simple procedure that ABSTRACT OF THE DISCLOSURE does not require a multi-step procedure of heating in A borosilicate glass or metal or metal alloy having a elaborate ovens at carefully controlled temperatures, such surface sealed or bonded to a thermally crystallized glass novel procedure would, in addition to its commercial ceramic composed essentially of from 40-70 weight per value, also represent an improved and useful contribu cent of SiO2, 15—35 weight percent A1203 and 5-15 weight tion to the art.