Deep Water Offshore Wind Technologies
Total Page:16
File Type:pdf, Size:1020Kb
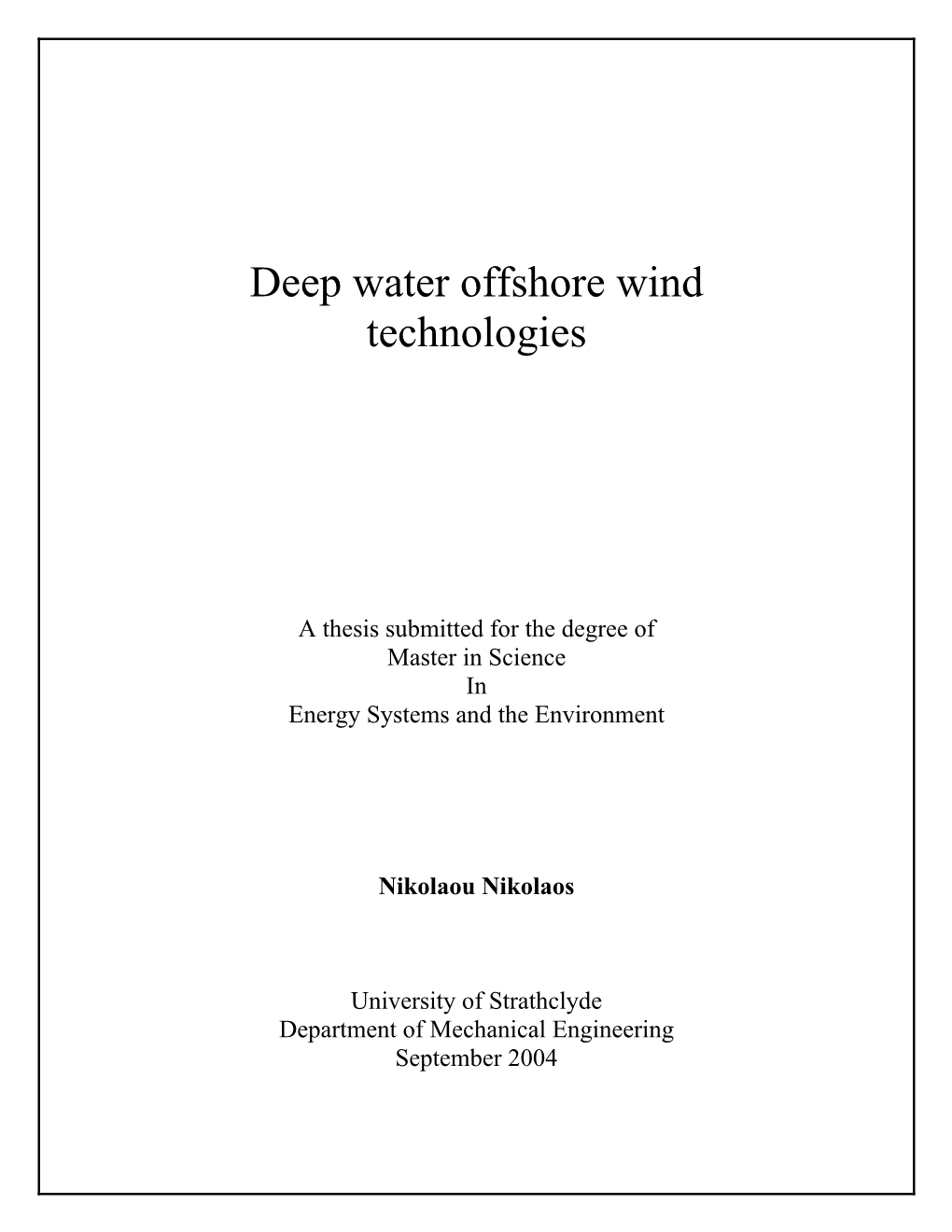
Load more
Recommended publications
-
Overview of Environmental Impacts of Offshore Wind Energy
Concerted action for offshore wind energy deployment (COD) Overview of Environmental Impacts of Offshore Wind energy Authors: E.M. Roth L.A. Verhoef M.W.L. Dingenouts EC Contract: NNE5-2001-00633 Novem contract number: 2002-03-01-03-002 New-Energy-works Project number: N0335 September 2004 Neither the Consortium of the Concerted Action for Offshore Wind Energy Deployment, nor any person acting on its behalf: a. makes any warranty or representation, express or implied with respect to the information contained in this publication; b. assumes any liability with respect to the use of, or damages resulting from this information. COD Overview of Environmental Impacts of Offshore Wind energy NNE5-2001-00633 Index 1 INTRODUCTION AND METHODOLOGY ........................................................................... 3 1.1 BACKGROUND ..................................................................................................................... 3 1.2 QUESTIONS ADDRESSED ..................................................................................................... 3 1.3 STRUCTURE OF THE DATABASE ............................................................................................ 3 1.4 METHODOLOGY OF ENVIRONMENTAL IMPACT ASSESSMENT APPLIED TO OFFSHORE PROJECTS 6 1.5 LIMITATIONS ....................................................................................................................... 7 2 WHAT KINDS OF STUDIES HAVE BEEN UNDERTAKEN AND WHICH ISSUES HAVE BEEN STUDIED? ................................................................................................................. -
For a Better World of Energy
FOR A BETTER WORLD OF ENERGY ARKLOW BANK WIND PARK PHASE 2 PUBLIC CONSULTATION ABOUT SSE RENEWABLES ABOUT THE PROJECT FOR A We’re SSE Renewables, a leading developer, owner and operator Arklow Bank Wind Park Phase 2 will be located off the coast of of renewable energy across Ireland and the UK. Arklow, Co. Wicklow. The 520MW project is the next phase of wind BETTER FUTURE energy development at Arklow Bank. Phase 1 of the Wind Park was Part of the FTSE-listed SSE plc, we employ around 1,000 people in constructed in 2003/04 consisting of seven wind turbines with a Ireland and over 10,000 in the UK, all of whom believe in building capacity of 25.2 MW. Phase 1 is owned and operated by GE Energy At SSE Renewables we’re for leading Ireland’s offshore wind a better world of energy. We’re the largest owner and operator of under a sublease to the foreshore lease and remains the first and energy ambition. We’re for building a cleaner energy future. renewable energy in Ireland and the UK, and through our sister only operational offshore wind farm in Ireland. And - through the development of Arklow Bank Wind Park company SSE Airtricity, the wind energy we produce here supplies Phase 2 off the coast of County Wicklow - we’re for creating more Irish homes and businesses than any other company. Now, SSE Renewables is proposing to invest between €1 billion and €2 billion to develop new local jobs in Arklow, Wicklow and along the East Coast Arklow Bank Wind Park to its full potential. -
Putting Wind on the Grid
SPRING 2006 ELECTRIC POWER RESEARCH INSTITUTE PUTTING WIND ON THE GRID A lso I N T H is I ssue : Energy Storage EMF and Health Effects The Electric Power Research Institute (EPRI), with major locations in Palo Alto, California, and Charlotte, North Carolina, was established in 1973 as an independent, nonprofit center for public interest energy and environmental research. EPRI brings together members, participants, the Institute’s scientists and engineers, and other leading experts to work collaboratively on solutions to the challenges of electric power. These solutions span nearly every area of electricity generation, delivery, and use, including health, safety, and environment. EPRI’s members represent over 90% of the electricity generated in the United States. International participation represents nearly 15% of EPRI’s total research, development, and demonstration program. Together…Shaping the Future of Electricity EPRI Journal Staff and Contributors David Dietrich, Editor-in-Chief Jeannine Howatt, Business Manager Debra Manegold, Layout Designer/Production Manager Ken Cox, Illustrator/Photographer Michael Rohde, Products Editor Craig Diskowski, Art Consultant Brent Barker, Executive Director, Corporate Communications Joseph Bugica, Vice President, Marketing Henry A. (Hank) Courtright, Senior Vice President, Member Services Contact Information Editor-in-Chief EPRI Journal PO Box 10412 Palo Alto, CA 94303-0813 The EPRI Journal is published quarterly. For information on subscriptions and permissions, call the EPRI Customer Assistance Center at 800.313.3774 and press 4, or e-mail [email protected]. Please include the code number from your mailing label with inquiries about your subscription. Visit EPRI’s web site at www.epri.com. © 2006 Electric Power Research Institute (EPRI), Inc. -
A Preliminary Assessment of the Long-Term Prospects for Offshore Wind Farms in Maltese Territorial Waters Dane Orion Zammit James Madison University
James Madison University JMU Scholarly Commons Masters Theses The Graduate School Fall 12-18-2010 A preliminary assessment of the long-term prospects for offshore wind farms in Maltese territorial waters Dane Orion Zammit James Madison University Follow this and additional works at: https://commons.lib.jmu.edu/master201019 Part of the Oil, Gas, and Energy Commons Recommended Citation Zammit, Dane Orion, "A preliminary assessment of the long-term prospects for offshore wind farms in Maltese territorial waters" (2010). Masters Theses. 435. https://commons.lib.jmu.edu/master201019/435 This Thesis is brought to you for free and open access by the The Graduate School at JMU Scholarly Commons. It has been accepted for inclusion in Masters Theses by an authorized administrator of JMU Scholarly Commons. For more information, please contact [email protected]. A Preliminary Assessment of the Long-Term Prospects for Offshore Wind Farms in Maltese Territorial Waters A dissertation presented in part fulfillment of the requirements for the Degree of Master of Science in Sustainable Environmental Resource Management By Dane Zammit November 2010 UNDER THE SUPERVISION OF Ing. Robert Farrugia Dr. Jonathan Miles Dr. Godwin Debono University of Malta – James Madison University ABSTRACT DANE ZAMMIT A PRELIMINARY ASSESSMENT OF THE LONG-TERM PROSPECTS FOR OFFSHORE WIND FARMS IN MALTESE TERRITORIAL WATERS Keywords: WIND; ENERGY; MALTA; OFFSHORE; VIABILITY; MARKET Almost all of Malta’s current interest in offshore wind development is focused on the development of an offshore wind farm at Sikka L-Bajda in northwest Malta by 2020, to help the country reach its mandated 2020 RES target. -
Opening Statement, Stephen Wheeler
23rd January 2018 Joint Committee on Communications, Climate Action and Environment Meeting Ireland’s targets under the 2020 Climate and Energy Package Opening Statement of Stephen Wheeler, Managing Director, SSE Ireland Chairperson, members, I’m pleased to have the chance to address the Committee on the opportunity presented by offshore wind energy towards meeting Ireland’s 2020 climate action targets. In particular, I’d like to speak on behalf of one of the companies that, as my colleagues in NOW Ireland have outlined, is ready-to-go to deliver an offshore energy project in the Irish Sea. My company, SSE, is the largest renewable energy developer and generator in Ireland. In the ten years since we entered the Irish energy market, we’ve invested almost €2.5 billion in the deployment of low carbon technology. As a result, we now have over 700MW of installed renewable capacity at our onshore wind farms including output from Ireland’s largest wind farm, the 169MW Galway Wind Park, which we co-developed with Coillte. We’re also a leading developer and operator of offshore wind energy – between projects in development, construction and operation we are involved in over 8,000MW of capacity, and have invested £1billion alongside a number of other partners. 900MW of that total is already powering energy consumers with large- scale renewable generation and is significantly contributing to Great Britain meeting its own climate change targets. Closer to home in Irish waters, we have the distinction of having co-developed Ireland’s first and only operational offshore wind farm, the 25MW Arklow Bank Phase 1. -
EOR0765 Arklow Scoping
Sure Partners Limited ARKLOW BANK WIND PARK PHASE 2 OFFSHORE INFRASTRUCTURE Environmental Impact Assessment Scoping Report EOR0765 Scoping Report Final 18 September 2020 rpsgroup.com Contractor Document Information Contractor Name RPS Contractor Doc No EOR0765 Contractor Doc Rev Final Arklow Bank Wind Park Phase 2 Offshore Infrastructure Environmental Impact Document Title Assessment Scoping Report SSE Document Number Contract Number CDL Code Sequence Sheet LF100034-CST-EV-LIC-RPT- - - - 0002 Revision Information Rev Document Issue Status Date Originator Checker Approver Final Final 18/09/2020 LB, CC (RPS) AB, LK (RPS) AB (RPS) SSE Acceptance of Contractor Document Code Description of Code SSE Designated Signatory Date 1 Accepted Kaj Christiansen 18/09/2020 2 Accepted with Comments 3 Not Accepted 4 For Information Only LF000009-PJC-MA-TEMP-0016 SURE PARTNERS LTD | ARKLOW BANK WIND PARK PHASE 2 OFFSHORE INFRASTRUCTURE - EIA SCOPING REPORT Contents Glossary ................................................................................................................................................. vii Acronyms ................................................................................................................................................. ix Units xii 1. INTRODUCTION ...................................................................................................................................... 1 1.1 Overview ....................................................................................................................................... -
Final Report
Transition to Sustainable Energy in the US Wind Energy Option Presented By: Christine Acker, Yash Agarwal , Nael Aoun, Stephen Clark Alex Hernandez, Nancy Lin, Jesse Negherbon Dimitre Ouzounov, and Reginald Preston Presented For: Francis Vanek, CEE 5910 Advisor May 5, 2009 1 TABLE OF CONTENTS EXECUTIVE SUMMARY .................................................................................................................................................... 6 PART I: INTRODUCTION.................................................................................................................................................. 8 I.1. Motivations for the project..........................................................................................................................................8 I.1.1. Planet climate change.................................................................................................................................................................................. 9 I.1.1.1. Evidences of climate change.......................................................................................................................................................... 9 I.1.1.2. Reasons for planet climate change...........................................................................................................................................10 I.1.2. Present world energy needs and future projections..................................................................................................................13 -
Wind Energy and Its Impact on Future Environmental Policy Planning: Powering Renewable Energy in Canada and Abroad
WIND ENERGY AND ITS IMPACT ON FUTURE ENVIRONMENTAL POLICY PLANNING: POWERING RENEWABLE ENERGY IN CANADA AND ABROAD by Kamaal R. Zaidi INTRODUCTION Given the tremendous pressure of using finite conventional sources of energy, many countries around the world are turning to renewable sources of energy to cushion against rising costs, while diversifying the means of delivering energy to their citizens. Wind energy is one such example of an innovative strategy to provide energy to citizens in a cleaner, abundant and reliable fashion. As society turns away from conventional sources like coal and natural gas (fossil fuels) due to the rising electricity costs and its deleterious impact on the environment, government-sponsored efforts and technological innovation are pushing wind energy to the forefront of creative environmental policy planning. More specifically, government legislation through financial incentives encourages public and private businesses to participate in pursuing renewable energy sources with more vigor. This paper examines the role of wind energy in Canada and abroad in terms of how its growing emergence is being recognized as one of the best methods of implementing sound environmental regimes that are replacing expensive conventional methods of energy extraction and utilization. Part I will examine the history and background of wind energy. Here, an overview of wind energy use in various cultures and time periods will be examined. Part II explains the role of wind energy in the context of the Kyoto Protocol. As part of this global initiative, wind energy is reviewed as to how it contributes to a “green” economy. Part III discusses the technology behind wind energy generation. -
Harnessing Our Potential Investment and Jobs in Ireland’S Offshore Wind Industry March 2020
Harnessing our potential Investment and jobs in Ireland’s offshore wind industry March 2020 1. Introduction Acknowledgements The Carbon Trust wrote this report based on an impartial analysis of primary and secondary sources, including stakeholder consultation. The Carbon Trust would like to thank everyone that has contributed their time and expertise during the preparation and completion of this report. Special thanks go to the Irish Wind Energy Association Supply Chain Working Group and Enterprise Ireland whose input and feedback were invaluable in completing this report. This report was sponsored by the GreenTech Skillnet who is being managed by the Irish Wind Energy Association. For the avoidance of doubt, this report expresses independent views of the authors. | 1 The Carbon Trust’s mission is to accelerate the move to a sustainable, low carbon economy. It is a world leading expert on carbon reduction and clean technology. As a not-for-dividend group, it advises governments and leading companies around the world, reinvesting profits into its low carbon mission. Authors: Liam Leahy [email protected] Manager Dan Kyle Spearman Manager Rory Shanahan Manager Elson Martins Associate Emily Northridge Analyst Georgia Mostyn Energy Consultant | 2 Executive Summary Ireland is on the cusp of an energy revolution. Over the next ten years Ireland will connect a new generation of offshore wind farms, providing enormous amounts of clean energy to power homes, farms and businesses. This will accelerate the ongoing decline in CO2 emissions from the electricity sector and drastically cut Ireland’s bill for foreign fossil fuel imports. Offshore wind energy is at the heart of the Climate Action Plan’s ambition to cut CO2 emissions in the electricity sector by two-thirds and increase the renewable energy share of electricity demand to 70 per cent by 2030 from its current 35 per cent. -
Wind Turbine Gearbox Technologies
8 Wind Turbine Gearbox Technologies Adam M. Ragheb1 and Magdi Ragheb2 1Department of Aerospace Engineering 2Department of Nuclear, Plasma and Radiological Engineering, University of Illinois at Urbana-Champaign, 216 Talbot Laboratory USA 1. Introduction The reliability issues associated with transmission or gearbox-equipped wind turbines and the existing solutions of using direct-drive (gearless) and torque splitting transmissions in wind turbines designs, are discussed. Accordingly, a range of applicability of the different design gearbox design options as a function of the rated power of a wind turbine is identified. As the rated power increases, it appears that the torque splitting and gearless design options become the favored options, compared with the conventional, Continuously Variable Transmission (CVT), and Magnetic Bearing transmissions which would continue being as viable options for the lower power rated wind turbines range. The history of gearbox problems and their relevant statistics are reviewed, as well as the equations relating the gearing ratios, the number of generator poles, and the high speed and low speed shafts rotational speeds. Aside from direct-drive systems, the topics of torque splitting, magnetic bearings and their gas and wind turbine applications, and Continuously Variable Transmissions (CVTs), are discussed. Operational experience reveals that the gearboxes of modern electrical utility wind turbines at the MegaWatt (MW) level of rated power are their weakest-link-in-the-chain component. Small wind turbines at the kW level of rated power do not need the use of gearboxes since their rotors rotate at a speed that is significantly larger than the utility level turbines and can be directly coupled to their electrical generators. -
Existing and Potential Ocean-Based Energy Facilities and Associated
ExistingExisting andand PotentialPotential Ocean-BasedOcean-Based EnergyEnergy FacilitiesFacilities andand AssociatedAssociated InfrastructureInfrastructure inin MassachusettsMassachusetts RFRRFR #:#: ENVENV 0606 CZMCZM 1515 June 26, 2006 Prepared for: Prepared by: Massachusetts Office TRC Environmental Corporation of Coastal Zone Management Boott Mills South 251 Causeway Street, Suite 800 116 John Street Boston, Massachusetts 02114 Lowell, Massachusetts 01852 Customer-Focused Solutions TABLE OF CONTENTS EXECUTIVE SUMMARY ........................................................................................ ES-1 1.0 INTRODUCTION.............................................................................................. 1-1 1.1 Project Background and Purpose.....................................................................1-1 1.2 Report Organization.........................................................................................1-2 2.0 METHODOLOGY ............................................................................................ 2-1 2.1 Ocean-Based Technologies Considered ..........................................................2-1 2.2 Sources of Information ....................................................................................2-1 2.3 Research Methods............................................................................................2-3 2.4 Questionnaire and Information Needs Form....................................................2-4 2.5 Telephone Call Procedures and Protocol.........................................................2-4 -
Arklow Bank Wind Park, Phase 2
Arklow Bank Wind Park, Phase 2 Marine Site Investigations Natura Impact Statement Comprising a Stage One screening appraisal for appropriate assessment, and a Stage Two appraisal for appropriate assessment SPL DOCUMENT REF: LF100034-CST-OF-LIC-LIC-0002-2 Arklow Bank Wind Park Phase 2 Marine Site Investigations Natura Impact Statement Version F06 April 2021 LF100034-CST-OF-LIC-LIC-0002–2 | Marine Site Investigations | Natura Impact Statement | April 2021 www.rpsgroup.com SPL Document Reference: LF100034-CST-OF-LIC-LIC-0002-2 Document status Review Version Purpose of document Author Reviewer Approved by date Rev F06 Revised final issue JMC MW/DN/PD JMC 13.04.2021 Approval for issue James McCrory 13 April 2021 © Copyright RPS Group Limited. All rights reserved. The report has been prepared for the exclusive use of our client and unless otherwise agreed in writing by RPS Group Limited no other party may use, make use of or rely on the contents of this report. The report has been compiled using the resources agreed with the client and in accordance with the scope of work agreed with the client. No liability is accepted by RPS Group Limited for any use of this report, other than the purpose for which it was prepared. RPS Group Limited accepts no responsibility for any documents or information supplied to RPS Group Limited by others and no legal liability arising from the use by others of opinions or data contained in this report. It is expressly stated that no independent verification of any documents or information supplied by others has been made.