R'type Bentley (With Automatic Gearbox)
Total Page:16
File Type:pdf, Size:1020Kb
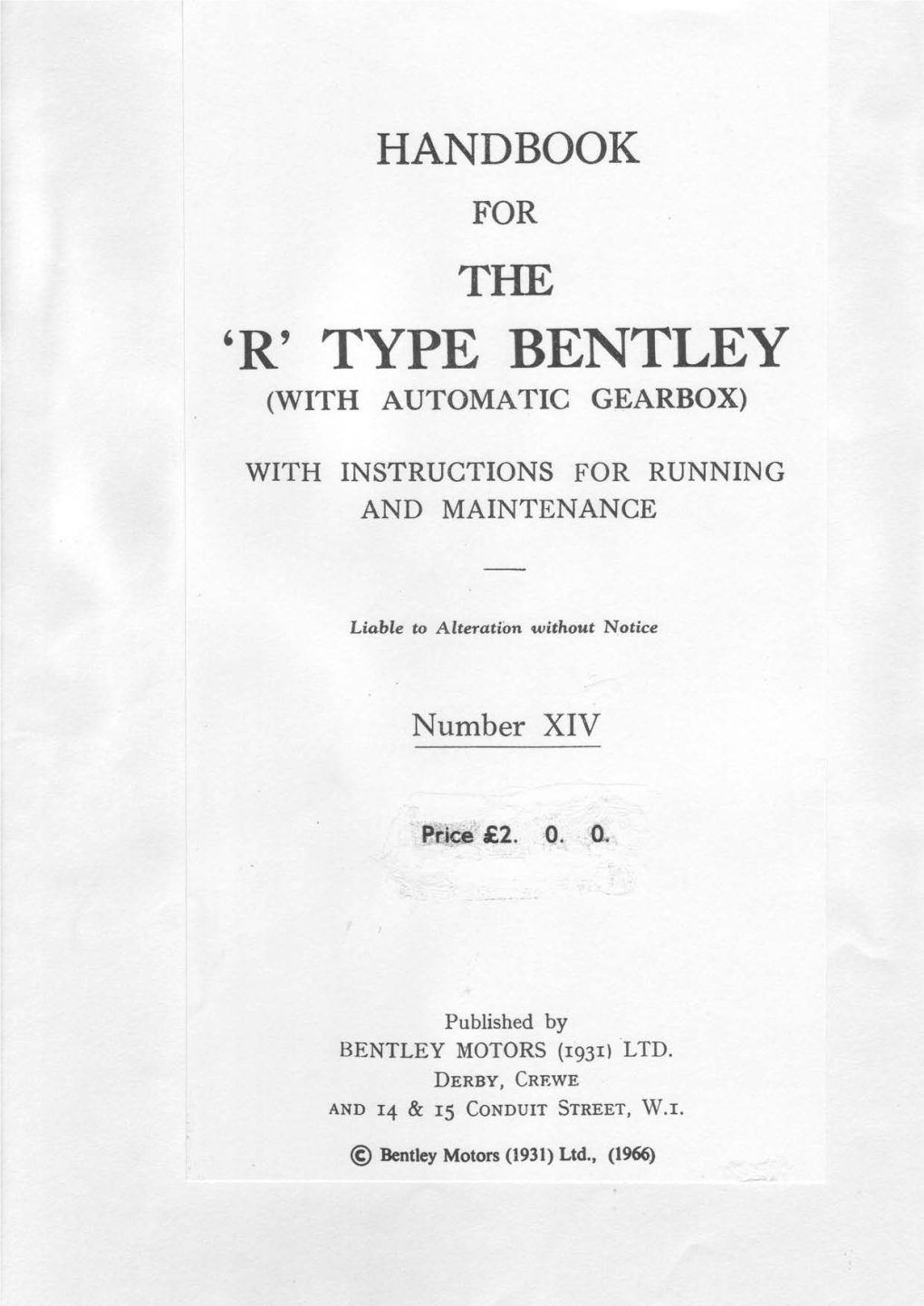
Load more
Recommended publications
-
Identifying Austin Sevens
AUSTIN POSTER BY LETTER A3 size 13/5/14 7:39 pm Page 1 Identifying Austin Sevens The Austin Motor Co. produced Austin Seven cars from 1923 -1939 which are identified by their style initials F rom 1923-1939 at least 50 body styles of Austin Seven and many specials were made. This re f e rence guide has been produced by the Austin Seven Clubs’ Association to help Austin Seven owners with the pro g ressive diff e rences between the models and the initials they became known as. XL 1,2,3 Prototypes (Note: cars illustrated are not necessarily from first year of pro d u c t i o n ) TOURERS AND TWO-SEATERS A/B C D/AD AE AF AG A/B Tourer The first 100 factory made C Tourer June 1924 - Feb 1926; flatter D / A D To u re r Feb 1926 - Sept 1929; 2” greater AE Tourer 1929 - mid 1930; coil ignition A F To u re r mid 1930 - early 1931; steel body; AG Tourer Early1931 - mid 1932; short cars from Oct 1922 - March 1923 (696cc) sides to scuttle; wider, sloping doors for width, length and knee room; curved lower from Jan 1929; diecast 22FZB Zenith carb; 5 gallon tank; louvred bonnet as fitted to chassis; last of the small doored tourers; 1 were designated the initial ‘A’ then easier access; hinged seat frame (passen- edge to windscreen; external doorhandles; 2” longer and 2 /2” wider body; speedo- the Type RL saloon; dial oil guage (May pressed steel body; bonnet and radiator became ‘B’ (now 747cc) from March 1923 ger seat only); electric starter (Jan1924); initally 6” brakes then closed centre wheels for meter closer to centre of dashboard and 1930); 2 level -
165 Road Safety and Vehicular Light
ISSN 2239-978X Journal of Educational and Social Research Vol. 4 No.5 ISSN 2240-0524 MCSER Publishing, Rome-Italy July 2014 Road Safety and Vehicular Light Standardization in Nigeria Amidst Ameriacan and UN Regulation Standard (WP.29) Dukiya, J. J. Owoeye A. A. Department of Transport Management Technology, Federal University of Technology, PMB 65, Minna, Ngeria Doi:10.5901/jesr.2014.v4n5p165 Abstract Since the first Ford’s Model Ts vehicle in 1908 which has metamorphosis into the present day hybrid vehicles, yearly auto-crash leads to the death of 1.2 million people, injury and disability of another 50 million is challenging. This study assesses road users’ perception and responses to red signal-lights of new/second hand vehicles imported into Nigeria and theoretical review of human vision. Questionnaires were administered to urban road users at public garages, oral interviews with the Federal Road Safety Corps (FRSC, Nigeria) and traffic cops and personal observation at intersections to assess drivers’ perception of red turning signal- lights. The result reveals that 76% of the road users have low perception of red turning-signal and that poor utilization of turning- signal are responsible for 45% intra-urban road crashes. In conclusion, it is recommended that the federal government through the relevant agencies should redefine her stand on the US and World Forum for Harmonization of Vehicle Regulations, WP.29 in the furtherance of road safety crusade in the country. Keywords: Turning Signal-Light, Visual Perceptions, Vehicle Blinkers, Traffic Safety, and WP 29. 1. Introduction Science and technological advancement is not so pronounced in any sector globally as in the transportation sector. -
The All New Lexus IS250C Intelligent Sports Convertible
Press Release 5 June 2009 For Immediate Release The All New Lexus IS250C Intelligent Sports Convertible “Capturing Attention” “Lexus IS250C x JESSICAR Launch Party” co – organized by Crown Motors Ltd. and South China Media was held at Lexus Showroom on 5 June 2009 with a great success celebrating the launch of the All New Lexus IS250C and the brand new car magazine JESSICAR ¡ . Our Honorable guests, Mr. Keiichi Yoneda (Chief Engineer of Lexus IS250C) and Mr. Patrick S Lee (Managing Director of Crown Motors Ltd.) officiated the launch ceremony together with Ms. Jessica Ng (Publisher of JESSICAR) and Mr. Chacky Ip (Chief Editor of JESSICAR). Amongst the officiating guests list were celebrities including Ms. Annie Lau, Ms. Nikki Chow, Ms. Tiffany Lee, Ms. Zoie Tam, and Hong Kong top model Ms. Ana R as well as Ms. Cara G. This new Lexus exudes luxurious, sophisticated refinement from every angle, once ¢ again proving the success of the L-finesse design philosophy “Simplicity ¢Elegance Anticipation”. Add to this the sophisticated engineering and advanced technology that lies beneath the exterior and you have a car of stunning beauty and unbeatable performance. Top down or top up, this sports convertible retains the classic lines we have come to expect from Lexus thanks to the innovative and ingenious lightweight, 3-piece, aluminium alloy roof. When the roof is deployed the car looks like a classic sports coupe with harmoniously balanced cabin and body. When the roof is retracted the vehicle transforms into a thrilling open-top sports car. Numerous advanced features, such as the button-operated fold & return front seats, show that this vehicle has the characteristic thoughtful design for which Lexus is renowned. -
[email protected] Web Page: Wire Wrapdescription B B Braided Wire and Braid Outer Wrap
©2007 MORRIS CATALOG #15 BRITISH WIRING INC. P.O. BOX 185 617 WALNUT STREET BALLY, PA 19503 Toll Free: 866-461-9050 Fax: 610-845-3518 e-mail: [email protected] web page: www.britishwiring.com Wire WrapDescription B B Braided wire and Braid outer wrap. P B PVC wire and Braid outer wrap. P P PVC wire and PVC tape outer wrap. Choose - Headlamp Pigtails for the Models in this Listing - need 2 per car Part # Wire Wrap Pcs Wrap Blue/White (UW) wire Blue/Red (UR) wire Black (B) ground wire 141 P P 1 PVC PVC PVC PVC 141 XP PB P 1 PVC Braid Braid PVC 141 BB B B 1 Braid Braid Braid Braid Alternator Conversion ALT - - All Any model, factory conversion of harness from generator to alternator. Morris Part # Wire Wrap Pcs Year Model, Series , Chassis # and Identifying Features BW63 P B 1 Pre 1960 Morris Minor, Dip switch lead BW64 P B 1 Post1960 Morris Minor, Dip switch lead 437 B B 2 48-61 Morris Minor, Original Style Add on harness for 8 Way Relay 417 P B Flashers. ALT MM P B 1 All Add-on alternator adaptor sub-harness with plug for all Morris Minor 421 B B 1 48/49 Morris Minor SV, SMM 501 – on, 401 P B No High Beam Warning Light, Offside Dash, Trafficators 422 B B 1 49/52 Morris Minor SV, 63822 – on, 402 P B No High Beam Warning Light, Trafficators 471 B B 3 52/53 Morris Minor OHV, 138415 – on, 451 P B Four door with main beam warning light, Trafficators 423 B B 3 52/53 Morris Minor OHV, 140823 – on, 403 P B Two door with Main Beam Warning Light, Trafficators 424 B B 3 53/54 Morris Minor OHV, 221763 – on, Series 2 starts, 404 P B Offside -
The Mk 1 Consul, Zephyr and Zodiac Owners Club Technical Manual
The Mk 1 Consul, Zephyr and Zodiac Owners Club Technical Manual Originally created in 1991 by Neil Tee, with contributions from John Blythe, Phil Downer, Dave Hardwick, Mick Johnson, Rowland Oliver, Alan Sim, Neil Tee, Andy Tutt, John Wiles. Retyped and Reformatted by Gaz Leaver, 2017. 1 Contents Bodywork ................................................................................................................................................ 6 Initial examination - bolt on parts and sills ......................................................................................... 6 Door Sill Replacement ......................................................................................................................... 8 Structurally important areas ............................................................................................................... 9 Non-Structural Rot ............................................................................................................................ 11 Doors ................................................................................................................................................. 11 Bonnets ............................................................................................................................................. 12 Rear Panel ......................................................................................................................................... 12 Boot Guttering ................................................................................................................................. -
Always Forgive Your Enemies - Nothing Annoys Them So Much
Volume 57, Issue 8 Volume 57, Issue 8 August, 2017 Editor Tissy Smith-Hatcher Always forgive your enemies - nothing annoys them so much. Oscar Wilde Inside this issue: President’s Message/ 2 New Members, Changes & Correc- tions/Sunshine & Sorrow Tours & Activities/ 3 Calendar/Swap Meets The 13 Most Danger- 4 ous Car Interiors in History Board Member 5 Contact Info General Meeting Minutes Turn, Turn, Turn: A 6 History of the Turn Signal Items for Sale 10 This Lady Drives a 11 Model A (Part 2) Orange County Model A Ford Club Page 2 August, 2017 The Distributor President’s Message I would like to start with a big Thank You to Ed and Patty Cote, for hosting the Ice Cream Social. As always, it was well attended. Plenty of ice cream, with toppings, and of course Ed’s famous auction. A good time was had by all. Speak- ing of a good time, I think everyone had fun and plenty to eat at the potluck, at Hart Park. I think we had sixty five members and 15 Model-A’s. Nice turn out! I know the weather has been a little hot and I’m not going to complain. May- be next month when I get my electric bill! The warm (should I say Hot) weather hasn’t kept Dianne and me from driving our Model-A’s. We made a few trips to Shoreline Village in Long Beach, Redondo Beach, and Huntington Beach. See the pattern here? We always seem to end up at the beach. It’s a great way to spend a summer evening and you meet a lot of nice people every time you stop. -
BW-145-Dec-1983 Low.Pdf
A practical way to fabricate RACING MANIFOLDS, EXHAUST PIPES, TRAILERS, CANOPY FRAMES, GATES, and many other items. ~ ~-= N.z. o CAR STANDS *ALL STEEL TUBULAR CONSTRUCTION *MAXIMUM LOAD 1000 Kg PER STAND *HEIGHT FROM 330mm to 440mm *7HEIGHT POSITIONS ~ VINTAGE CAR CLUB OF N.Z.(INC.) NATIONAL EXECUTIVE President: N. A. Dewhurst (AucklandI Club Captain: A. D.Storer [Banks Peninsula] Club Vice-Captain: M. K. Holland (Manawa tu) VOL. XXIX No . 145 Hon. Secretary: Clyn t Inns (Bank s Penins ula) Administrative Secretary: Robert Duns, Phone 517-335, Chr istchurch . December 1983-Jan 1984 Club Registrar: Don Bennetts, 714 Hills Road, Christchurch. Executive: Messrs B. J. Barne s (Southland), W. M. Birch 29th YEAR OF PUBLICATION [Wellington]. J. W. A. Newell (Banks Peninsula], N.C. Skevington (Canterbury). IN THIS ISSUE CORRESPONDENCE President's Message 2 Club correspo ndence, including members' CHANGES OF De Dion, 23 Years later 3 ADDRESS, must be sent to Canterbury Opening run 5 The Vintage Car Club ofN.Z. fIne.) r.o. Box 2546, The Suicide Saucers 6 Christchurch. Obituary 10 Members should state 6 figure number from Membership Card. Vintage Racing Fords 11 Intend ing members should write to this add ress . Fall and Rise of 1147 15 All Beaded Wheels corresponde nce and subscribers change of address to P.O. Box 13140. Dunvegan 1983 22 Branch Notes 24 Letter to Editor 31 BEADED WHEELS EDITORIAL COMMITIEE Chairman : Spencer Barnard. Classified Ads 33 Committee: Geoff Hockley, Bruce Pidgeon, Bob Scott, Paul Giesler, Bob Entwistle. Material for publication is the responsibility of this committee and should be forw arded to P.O. -
The M.G. 1 ¼-Litre Saloon
May 14, 1947. May 14, 1947. 1947 CARS The M.G. 1 ¼-litre Saloon A New, Independently Sprung Model From a Famous Sports car Factory EW cars made in this country have ever endeared themselves to so many enthusiastic drivers as has the F M.G. Midget, which has been popular in different forms ever since 1928. Owners have always lamented the fact that, when growing families made an open two-seater unsuitable for them, they were obliged to buy a more touring make of car. Now the M.G. Car Co., Ltd., can offer them a four-seater saloon, powered by an engine of the same dimensions as the TC series Midget, combining comfort with a lively performance. The price of £671 11s. 8d., including purchase tax, exceeds that of the 2-seater model by only some 25 per cent. The most striking innovation in the new 1¼-litre model is undoubtedly the adoption of independent springing for the front wheels. Eleven years ago the R type of racing M.G. Midget featured independent springing of all wheels, but only now have the manufacturers been sufficiently satisfied with their test results to incorporate independent suspension on a production model. The potential gains from the elimination of a rigid front axle are very substantial. There can be some reduction in FAMILY LIKENESS.—The new model combines accepted M.G. lines with new standards of small-car comfort and refinement. unsprung weight, to the advantage of’ both comfort and road Engine Dimensions: Transmission – holding. Flexible springs can be used Cylinders 4 (Contd.) without any wheel tramp or steering Bore 66.5 mm Prop. -
AIS Codes of Practice
Section 3 INDEX OF ATTACHMENTS 1(a) Modification Codes for Commercial Vehicle Modifications 2 1(b) Modification Codes for Light Vehicle Modifications 4 2 Australian Design Rule (ADR) Seat Belt Requirements 5 3 Mudguard and Mudflap Requirements 16 4 Headlamp Testing Screens 18 5 Missing Compliance Plates 19 6 LPG and CNG Certification 21 7 Braided Brake Hoses 23 8 Motor Vehicle Lighting 25 9 Rear Marking Plates 27 10 Replacing or Repairing Windscreens 36 11 Rust and Corrosion 40 12(a) Safety Chains for trailers less than 3.5 tonnes ATM 46 12(b) Safety Chains for trailers 3.5 tonnes ATM and above and for rigid draw bar pig trailers above 2.5 tonnes GTM and fitted with automatic pin type couplings 47 13 Ground Clearance Requirements 52 14 ADR Applicability Tables, Vehicle Categories and Definitions 53 15 Retreaded Tyres 67 16 Brake drums and discs 71 17 Replacement Steering Wheels 75 18 Fitting of body lift kits and suspension height modifications to motor vehicles 78 19 Commercial Vehicle Modifications carried out prior to 1990 80 20 Suspension Modifications 82 21 Lighting Standards 85 Page 1 AIS INFORMATION SHEET No. 1(a) CODE OF PRACTICE COMMERCIAL MOTOR VEHICLE MODIFICATION CODES FOR APPROVED PERSONS CODE MODIFICATION A1 Engine Substitution A2 Air Cleaner Substitution or Additional Fitting A3 Turbocharger Installation A4 Exhaust System Alterations A5 Road Speed Limiter Installation B1 Transmission Substitution or Additional Fitting C1 Tailshaft Alterations D1 Rear Axle/s Installation D2 Differential Substitution E1 Front Axle Installation -
1996 Summer.Pdf
MOSSMOTORING Is published A DECADE OF HAVE YOU REGISTERED YET? by Moss Motors, Ltd. MEMORIES ^1 Own «a Editor: Ken Smith HURRY, ONLY 60 DAYS TO GO! Contributing Writers:Mike Chaput, Ron • "^b. Bob Consoll, Robert Goldman, Bob move last year to (new premisescaused Classic •iday,Robert Koval,Harry Newton,Scott Nielsen. ChrisNowlan, RonPhillips, Bob Oct disturb the Rothstein, JohnSprinzel. SusanScott inevitable dust in quite a Thompson, and EricWilhelm. • few comers. In one of these Production: JillLee-Jones,IdealImages fur Hung alcoves of memo '"Only ries we came across a num Althoughwe makeeveryeffortto ensure the ber of very early copies of correctness of technical articles, Moss Motors, AfossMotoring. I'm sure you Ltd. assumes no liability forthe accuracy, safe know bow it is when you ty,or legality oftnese contributions. All techni $ 1595 come to throw out all those I rUC II UP FARMS, JULY 18-21, 1996 calmaterial shouldbe weighed againstcom monly accepted practice. Anyopinions old car magazines that you expressed in this magazineare those ol the never read. Something 4TH ANNUAL authors and do not necessarily reflectthe opin catches your eye and before ions or policiesol Moss Motors. you know where you are, hall the day has been spent reminiscing over MOSS MOTORS Mass Moloringis© 1996 Moss Motors, Ltd. times, cars, and events long past. Al rights reserved. Well, this happened to me with those back Issuesof Moss Motoring. BRITISH CAR FESTIVAL All I really wanted to do was to put them away somewhere where they CONTRIBUTIONS INVITED would not be ravaged by the natural phenomena that prevails in the JULY 18-21, 1996 Contributions are greatlyappreciated and Golden Stale such as earthquakes. -
Identifying Austin Sevens Factory Initials
A5 BOOKLET for WEBSITE 26/8/13 4:16 pm Page 1 IDENTIFYING AUSTIN SEVENS FROM THEIR FACTORY INITIALS by Graham Baldock © A7CA and Graham Baldock A5 BOOKLET for WEBSITE 26/8/13 4:16 pm Page 2 AUSTIN SEVEN BODY TYPES TOURERS Identifying Austin Sevens XL 1,2,3 Prototypes May 1922 A Cars A1-100 based on prototype; 696cc engine; no running boards 1st Nov 1922 to mid Nov 1922 B ‘Chummy’; aluminum body; 747cc engine; scooped scuttle Mid Nov 1922 to June 1924 from their FACTORY INITIALS C ‘Chummy’; sloping doors and vertical screen June 1924 to early 1926 D also AD Scuttle headlights; 4-seater, wing headlights Early 1926 to September 1929 by Graham Baldock AE Four seater, two inches wider than AD September 1929 to mid 1930 AF Steel bodied, four seater, coupled brakes; 6” scuttle, 271/2” bonnet Sept 1930 to early 1931 AG SWB; Open four seater; 8” scuttle, 251/2” bonnet Jan 1931 to mid 1932 Since 2015 when this booklet was first published in printed form, more information AH Pressed steel body, LWB four seater, rear tank from Sept 1932 Mid 1932 to mid 1934 has come to light mainly concerning production dates. Where it is not certain, dates AAK Open Road Tourer; cowled radiator; high frame, open spare wheel Aug 1934 to Aug 1936 are followed by a ‘?’ mark: as new information comes to light we will update the AC Pearl Cabriolet, exposed hood irons; low frame August 1934 AAL Open Road Tourer, covered spare wheel (chrome rad until July ’35 then cowled) July 1935? to Jan 1939 website accordingly. -
The Square Rigger
The Square Rigger Quarterly Newsletter of the Chesapeake Chapter of the New England MG-T Register HTTP://WWW.CHESAPEAKECHAPTERMGTCLUB.COM The Square Rigger SUMMER 2020 Edition Published – June 2020 BE KIND, HAVE GRACE, GIVE THANKS, SPEAK LOVE, & STAY SWAGGY 1 WORDS FROM OUR CHAIRMAN Greetings! These last few months were pretty much at a standstill for most of us as activities either were postponed or cancelled. Like most people I had plenty to do either completing things around the house, especially in the garage, or improving on the curb appeal of the house. However, looking through the current Sacred Octagon issue, you can see John Tokar working in his garage on his MGTD – finally catching up his restoration project. As you know all Chapter events for 2020, except for the Fall Ramble in October, have been cancelled. As it stands now it is still taking place as scheduled. There was a book review of Why We Drive by Matthew Crawford which I read today. It explores how the joy of driving is being replaced by the boredom of navigation screens, self-braking devices and other gizmos which result in a less attentive driver. Cannot say that about driving our MGT-Series cars. Since our last TSR issue appeared, a couple of CCNEMGTR members volunteered to fill the two club officer vacancies. John Debelius will serve as the Treasurer/Secretary and Jim Bradley has stepped forward to be Regalia Chairman. We appreciate both John and Jim for helping us by filling these slots. Wishing you well and encourage you and your family to keep taking the needed steps to remain healthy and safe.