Analysis of Smoak Tannins
Total Page:16
File Type:pdf, Size:1020Kb
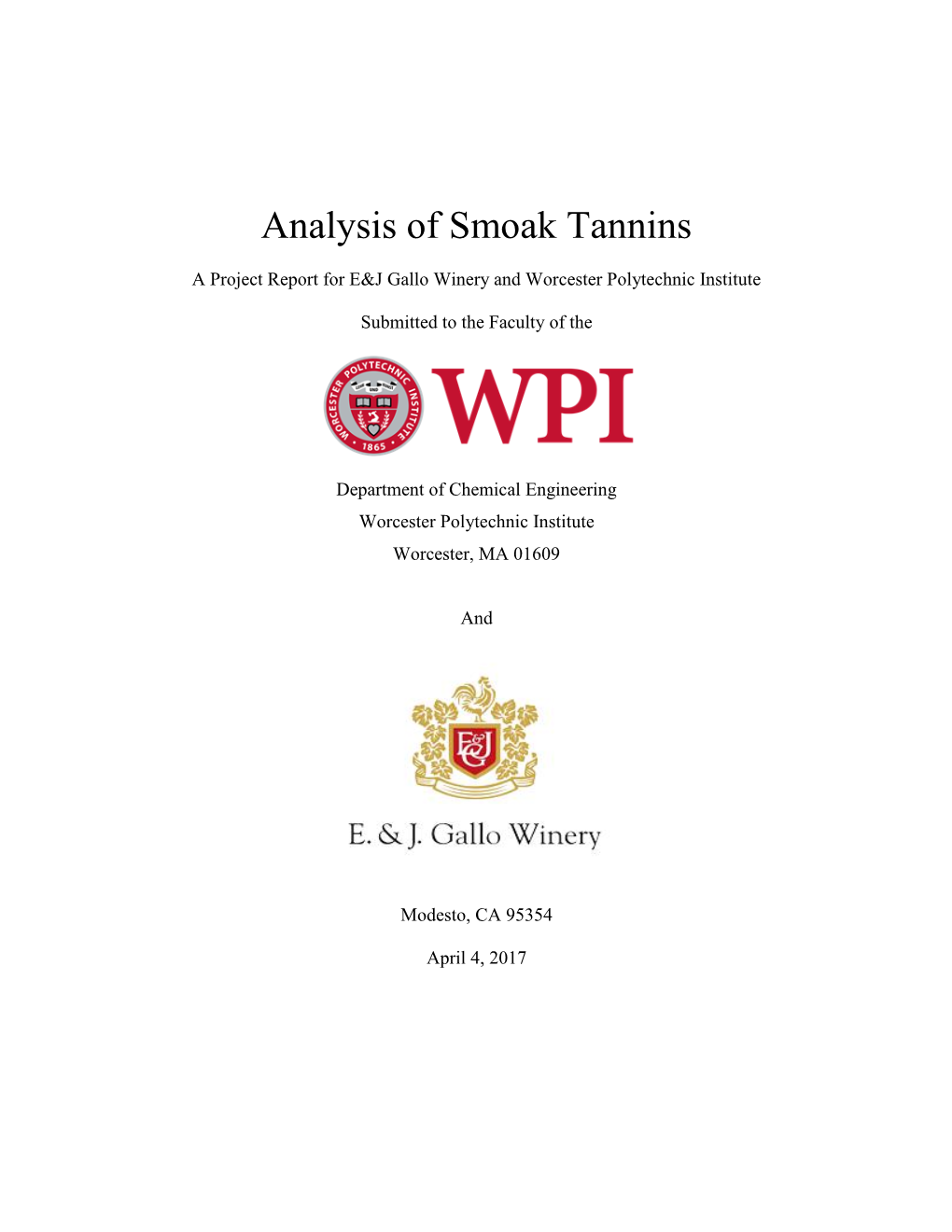
Load more
Recommended publications
-
A History of Wine in America from the Beginnings to Prohibition 2Nd Edition Download Free
A HISTORY OF WINE IN AMERICA FROM THE BEGINNINGS TO PROHIBITION 2ND EDITION DOWNLOAD FREE Thomas Pinney | 9780520254299 | | | | | A History of Wine in America: From the Beginnings to Prohibition It is a story that touches on nearly every section of the United States and includes the whole range of American society from the founders to the latest immigrants. Australia New Zealand. Today the American wine industry faces the growing challenges of expanding international exports and dealing with domestic regulations on interstate sales and shipment of wine. Forms of Life in a Dry World 2. If you don't follow our item condition policy for returnsyou may not receive a full refund. Faculty published reports on which varieties of grapes grew best in which regions of the state, held seminars on winemaking techniques, consulted with grape growers and winemakers, offered academic degrees in viticulture, and promoted the production of quality wines. LeFranc produced good wine as did his son-in-law, Paul Masson. There are 2 items available. Read preview. Add links. Seller information greatbookpriceau Early on, the Napa Valley demonstrated leadership in producing quality wine. Many talented winemakers had died, vineyards had been neglected or replanted in poor quality grapes, and Prohibition had changed Americans' taste in wines. Overview A History of Wine in America is the definitive account of winemaking in the United States, first as it was carried out under Prohibition, and then as it developed and spread to all fifty states after the repeal of Prohibition. Report item - opens in a new window or tab. Consumer Tips Item specifics Condition: Brand new: A new, unread, A History of Wine in America From the Beginnings to Prohibition 2nd edition book in perfect condition with no missing or damaged pages. -
Spring 2014 Spring 2014 Publication Schedule
NYU PRESS spring 2014 SPRING 2014 PUBLICATION SCHEDULE NYU MARCH MONTHLY REVIEW PRESS MONTHLY REVIEW PRESS The Theory of Monopoly Capitalism Race to Revolution a NEW IN PAPERBACK PRESS John Bellamy Foster — page 47 Gerald Horne — page 49 Getting Ahead Silvia Domínguez — page 15 NEW IN PAPERBACK Strange Neighbors Up Against a Wall Edited by Carissa B. Hessick NEW YORK UNIVERSITY PRESS Global Mixed Race Rose Corrigan — page 34 and Gabriel J. Chin — page 34 838 Broadway, 3rd Floor Edited by Rebecca C. King-O’Riain, Stephen Small, Minelle Mahtani, The Tolerance Trap New York, New York 10003-4812 Miri Song and Paul Spickard Suzanna Danuta Walters — page 1 Telephone: 1.800.996.NYUP (6987) — page 17 MAY Toxic Communities Fax: 212.995.3833 God and Blackness Choosing the Future Dorceta E. Taylor — page 13 Web: www.nyupress.org Andrea C. Abrams — page 41 for American Juvenile Justice Visions of Zion Edited by Franklin E. Zimring Erin C. Macleod — page 43 Find original articles, podcasts, Heart-Sick and David S. Tanenhaus — page 20 and reviews on our blog: Janet K. Shim — page 17 Walking Where Jesus Walked MONTHLY REVIEW PRESS NEW IN PAPERBACK Hillary Kaell — page 42 WWW.FROMTHESQUARE.ORG E.P. Thompson and Lotions, Potions, Pills, and Magic When Boys Become Boys the Making of the New Left Also sign up to receive monthly Elaine G. Breslaw — page 10 Judy Y. Chu — page 37 e-announcements at: Edited by Cal Winslow — page 48 Mississippi River Tragedies The Expeditions WWW.NYUPRESS.ORG Christine A. Klein JULY Ma’Mar Ibn Rashid and Sandra B. -
Here Are Certain Restrictions Regarding the Shipment of Spirits
zachys® The Holiday Auction December 6 & 7, 2019 at 10:00 AM EST Day One, The Holiday Auction: Lots 1–848 Day Two, The Holiday Auction: Lots 849–1254 and The Black Tie Collection: Lots 1255–1631 Smith & Wollensky 797 Third Ave PLEASE NOTE: The Black Tie Collection will New York, NY 10022 immediately follow the multi-vendor auction on December 7, 2019. Sale 1912N324 Upcoming Zachys Wine Auctions February 12, 2020 – New York March 5 & 6, 2020 – La Paulee, New York March 27 & 28, 2020 – Hong Kong May 14 & 15, 2020 – New York In addition to the sales listed above, Zachys holds eAuctions monthly. Please see our website zachys.com/auctions for details. Zachys Consolidated Sea Shipment Zachys offers FREE consolidated sea shipping between Hong Kong and New York several times a year. Local delivery charges will apply. Please email [email protected] for more information. Zachys Consolidated Air Shipment Zachys offers special consolidated air shipping between Hong Kong and New York at a discounted rate of US$84 per 9L. These containers generally depart three weeks post auction. Local delivery charges will apply. Please email [email protected] for more information. New York – Washington, DC Consolidated Shipments Zachys offers FREE temperature-controlled consolidated shipments of wine purchased at Zachys auctions between Zachys New York in White Plains, NY and Zachys DC in Washington, DC. Please contact 914.448.3026 or [email protected] for further information. Shipment of Spirits Buyers should be advised there are certain restrictions regarding the shipment of spirits. Clients wishing to ship outside of the U.S. -
Honda to Award Record $4.55 to Charity Cuisine the Honda Classic Has Hit a “We Continue to Raise the Bar Said
INSIDE WEEK OF JUNE 14-20, 2018 www.FloridaWeekly.com Vol. VIII, No. 33 • FREE Pixie play The group joins Weezer for a show at Coral Sky. B1 X In 1962, our state was the staging Collector’s Corner Antique postcards offer a peek at area for the Cuban missile crisis — another world. B2 X it nearly started World War III BYY KARINKARRINN LILLISLIILLIL S FloridaFlorida WeeklyWeekly CorrespondentCorrespondent AIR FORCEORCE CAPTAPT. JERRYERRY MCILMOYLELMOYLE HADHAD A strangestrange feeling.ffeeling. SomethingSommething nigglingniggglingn awayawaay in thethe US backbab ckk of hihiss mindmindd waswass saying,saying, “You needneed to getget outouut ofo hhere.”ere e.” ThatThat ppremonitionrer monition wwasas rright.igghth . Capt.Capt. McIlmoyleMcIlmom yle waswas amongamong thethe pilotspilol tst whowho flewflel w U-2U-2 jetsjets — high-higgh- Business flyingflyiy nng spyspypy planesplanees — overovo er CubaCubba in thethe middlemiddd le ofof ththee CubanCubab n missilemim ssile Gov. Scott asks feds for crisis,crissis, a 13-day13-day ColdColld WarWaW r standoffstanndoff gun-control help. A13 X betweenbetween thethe UnitedUnnitedd StatesStat tetes andannd theththe SovietSoviet UnionUnion thatthat putput bothbooth nationsnatioons SEESEE SPIES,SPIES, A1AA100 X Clockwise from top left: U.S. Air Force Capt. Jerry McIlmoyle with his U-2 spy plane during missions out of Florida; a U-2 plane; a portrait of Capt. McIlmoyle; and President John F. Kennedy speaking to the nation during the crisis. PHOTOS COURTESY OF U.S. AIR FORCE; CAPT. JERRY MCILMOYLE, PUBLIC DOMAIN AND PUBLIC AFFAIRS MCILMOYLE, PUBLIC DOMAIN AND AFFAIRS JERRY OF U.S. AIR FORCE; CAPT. PHOTOS COURTESY Honda to award record $4.55 to charity Cuisine The Honda Classic has hit a “We continue to raise the bar said. -
From Dutzow to Hermann, Missouri
University of Missouri, St. Louis IRL @ UMSL Theses UMSL Graduate Works 4-22-2011 A History of Weinbau in the Lower Missouri Valley: From Dutzow to Hermann, Missouri Todd J. Brown University of Missouri-St. Louis Follow this and additional works at: https://irl.umsl.edu/thesis Recommended Citation Brown, Todd J., "A History of Weinbau in the Lower Missouri Valley: From Dutzow to Hermann, Missouri" (2011). Theses. 163. https://irl.umsl.edu/thesis/163 This Thesis is brought to you for free and open access by the UMSL Graduate Works at IRL @ UMSL. It has been accepted for inclusion in Theses by an authorized administrator of IRL @ UMSL. For more information, please contact [email protected]. A History of Weinbau in the Lower Missouri Valley: From Dutzow to Hermann. Todd J. Brown M.A., History Department, University of Missouri-St.Louis, 2011 A Thesis Submitted to The Graduate School of the University of Missouri-Saint Louis in partial fulfillment of the requirement for the degree Master of Arts in History. April 2011 Advisory Committee Dr. Kevin Fernlund Chairperson Dr. Andrew Hurley Dr. Steven Rowan Dr. William Klein Copyright, Todd J. Brown, 2011 Thesis Abstract: April 22, 2011 Brown, Todd J. A History of Weinbau in the Lower Missouri Valley: From Dutzow to Hermann. M.A Thesis, University of Missouri-St. Louis, 2011. The thesis presented is a history focusing on the rise of German immigration, wine growing and production or Weinbau, in the lower Missouri valley from Dutzow, Missouri to Hermann, Missouri, and the connection between the nineteenth century Missouri Germans and the rise of the Missouri wine industry. -
“Replacing” Tobacco on Kentucky Farms: Discourses of Tradition, Heritage, and Agricultural Diversification
“Replacing” Tobacco on Kentucky Farms: Discourses of Tradition, Heritage, and Agricultural Diversification Dissertation Presented in Partial Fulfillment of the Requirements for the Degree Doctor of Philosophy in the Graduate School of The Ohio State University By Ann Katherine Ferrell, MA Graduate Program in English The Ohio State University 2009 Dissertation Committee: Amy Shuman, Advisor Dorothy Noyes Patrick B. Mullen Nan Johnson Copyright by Ann Katherine Ferrell 2009 ABSTRACT Tobacco farms, once an icon of American history, are disappearing from the landscape. For the Kentucky tobacco growers who are the focus of this study, tobacco farming is a livelihood that involves a mastery of traditional skills passed through generations and adapted to changing circumstances—technological, economic, social, and political. In this project, I examine the consequences of the changing status of tobacco and the category “tobacco farmer,” both of which have become stigmatized because of the health effects of tobacco use. This dissertation examines the current period of transition for Kentucky burley production and the implications for tobacco farmers of the changing contexts of this traditional occupation, often described as “a way of life.” The project is based on ethnographic fieldwork in Central Kentucky, supplemented by the collection of public discourses from multiple sites about tobacco production past and present. It brings folklore research and theory together with historical and archival research, economic data, and rhetorical analysis. In addition to a metahistory of tobacco production in the U.S. and Kentucky, and a fieldwork- based description of the 2007 crop-year, this dissertation examines the movement of the social and occupational category “tobacco farmer” from respect to stigma, and considers the repercussions of this movement on central folkloristic concepts, heritage and tradition. -
Open Thesis Final Draft.Pdf
The Pennsylvania State University The Graduate School College of the Liberal Arts GERMAN IN EVERY PARTICULAR? FROM HISTORIC SETTLEMENT TO THEME TOWNS: EXAMPLES OF “LITTLE GERMANIES” IN AMERICA A Thesis in German by Dirk Lehmann © 2007 Dirk Lehmann Submitted in Partial Fulfillment of the Requirements for the Degree of Doctor of Philosophy May 2007 The thesis of Dirk Lehmann was reviewed and approved* by the following: Francis G. Gentry Emeritus Professor of German Thesis Adviser Chair of Committee A. Gregg Roeber Professor of Early Modern History and Religious Studies B. Richard Page Associate Professor of German and Linguistics William Pencak Professor of American History Daniel L. Purdy Associate Professor of German Adrian J. Wanner Professor of Slavic Languages and Literatures and Comparative Literature Head of the Department of Germanic and Slavic Languages and Literatures *Signatures are on file in the Graduate School. iii ABSTRACT Among America’s most successful cultural and heritage tourism destinations are towns with a distinct and identifiable German character or theme. These “Little Germanies” are popular tourist destinations because of their historic and architectural ambiance and the natural beauty of their location. They are “German in every particular,” just as their visitors demand it. A multitude of special events and celebrations add to their popularity and success. Although they have in common their cultural theme and character, they are all very different in regards to their location, history and purpose of their founding, efforts in historic preservation, community profiles, tourism programs, and in many other respects. These “Little Germanies” can be divided into three different categories: “Historic Settlement,” “Theme Town” and “Historic Settlement turned Theme Town.” In their efforts to market themselves as a viable destination to tourists seeking a German cultural experience, America’s “Little Germanies” employ differing approaches and unique characteristics in order to sell a similar product. -
Fine & Rare Wines
zachys® Fine & Rare Wines June 26, 2020 at 10:00 AM EST Lots 1–773 This auction will be held “live online,” with a live feed of the auctioneer. Zachys is also accepting online, absentee, and phone bids, like all auctions. For assistance bidding from home, contact [email protected]. Sale 2006N353 Upcoming Zachys Wine Auctions Please visit Zachys.com/auctions for our monthly online auctions! Zachys Consolidated Shipment Zachys offers consolidated shipping from New York to Hong Kong several times a year. Local delivery charges apply. Please email [email protected] for more information. Zachys Consolidated Air Shipment Zachys offers special consolidated air shipping between Hong Kong and New York at a discounted rate of US$84 per 9L. Local delivery charges will apply. Please email [email protected] for more information. New York – Washington, DC Consolidated Shipments Zachys offers FREE temperature-controlled consolidated shipments of wine purchased at Zachys auctions between Zachys New York in White Plains, NY and Zachys DC in Washington, DC. Please contact 914.448.3026 or [email protected] for further information. Shipment of Spirits Buyers should be advised there are certain restrictions regarding the shipment of spirits. Clients wishing to ship outside of the U.S. must arrange delivery through their carrier for international shipping. In addition, Zachys is unable to arrange common carrier delivery of hard liquor or spirits outside the state of NY. H LIVE ONLINE BIDDING! In addition to browsing the catalog and placing absentee bids online, now you can get in on the action live from the comfort of your home or office! Visit www.zachys.com/auctions for details. -
Fine & Rare Wines
zachys® Fine & Rare Wines October 3 at 9:00 AM EST Day One, The White Tie Collection Part II: Lots 1–524 Day Two, Fine & Rare Wines: Lots 525-1352 Zuma 261 Madison Ave, New York, NY 10016 Official Champagne Sponsor Sale 1910N327 Upcoming Zachys Wine Auctions October 26-New York November 22 & 23-Hong Kong December 6 & 7-New York In addition to the sales listed above, Zachys holds eAuctions monthly. Please see our website zachys.com/auctions for details. Zachys Consolidated Sea Shipment Zachys offers FREE consolidated sea shipping between Hong Kong and New York several times a year. Local delivery charges will apply. Please email [email protected] for more information. Zachys Consolidated Air Shipment Zachys offers special consolidated air shipping between Hong Kong and New York at a discounted rate of US$84 per 9L. These containers generally depart three weeks post auction. Local delivery charges will apply. Please email asia@zachys. com for more information. New York-Washington, DC Consolidated Shipments Zachys offers FREE temperature-controlled consolidated shipments of wine purchased at Zachys auctions between Zachys New York in White Plains, NY and Zachys DC in Washington, DC. Please contact 914.448.3026 or [email protected] for further information. Shipment of Spirits Buyers should be advised there are certain restrictions regarding the shipment of spirits. Clients wishing to ship outside of the U.S. must arrange delivery through their carrier for international shipping. In addition, Zachys is unable to arrange common car- rier delivery of hard liquor or spirits outside the state of NY. -
Planting the Vines an Introduction Fritz Allhoff
9781405154314_4_000.qxd 8/3/07 11:48 AM Page 1 Planting the Vines An Introduction Fritz Allhoff Socrates took his seat . and had his meal . When dinner was over, they poured a libation to the god, sang a hymn, and – in short – followed the whole ritual. Then they turned their atten- tion to drinking. At that point, Pausanias addressed the group: “Well gentlemen, how can we arrange to drink less tonight? To be honest, I still have a terrible hangover from yesterday, and I could really use a break. I daresay most of you could, too, since you were also part of the celebration. So let’s try not to overdo it.” Plato (427–347 bce), Symposium 176a2–176a1 Wine and philosophy have long had a symbiotic relationship, extending back toward the origins of both. Some of the earliest archeo- logical evidence that we have for the existence of wine comes from the Neolithic period in modern Armenia and northern Iran; a pot- tery jar coated with wine residue has been dated to 5400 bce. By 2500 bce, wine was being cultivated on Crete, and probably on main- land Greece as well.1 But the period of time that I want to call to attention is the fifth and fourth centuries bce when Greek philo- sophers, such as Plato and Aristotle, laid the foundations of what would become Western culture. Wine undoubtedly played an import- ant social role during this time and, by extension, has had a significant impact on our own culture and history. 1 Tom Standage, A History of the World in Six Glasses (New York: Walker and Co., 2005), pp. -
2103LP-Catalog-Day1.Pdf
Day 1: Fine Wines of the World (except Burgundy) featuring Pioneers II March 11 at 10:00 AM EST Lots 1–592 Day 2: The Burgundy Auction In Celebration of featuring Pioneers II March 12 at 10:00 AM EST Lots 593-1591 This auction will be held “live online,” with a live feed of the auctioneer. Zachys is also accepting online, absentee, and phone bids, like all auctions. For assistance bidding from home, contact [email protected]. Sale 2103LP Upcoming Zachys Wine Auctions April 16 & 17 – Hong Kong – Fine & Rare Wines In addition to the sales listed above, Zachys holds eAuctions monthly. Please see our website zachys.com/auctions for details. Zachys International Shipping Zachys offers FREE consolidated sea shipments between White Plains, Hong Kong and Rotterdam several times a year. Subsidized air shipping is available at a rate of US$12/bottle, HK$100/bottle, or £9/bottle, with currency determined by the origin of the shipment. New York – Washington, DC Consolidated Shipments Zachys offers temperature-controlled consolidated shipments of wine purchased at Zachys auctions between Zachys New York in White Plains, NY and Zachys DC in Washington, DC. Please contact 914.448.3026 or [email protected] for further information. Shipment of Spirits Buyers should be advised there are certain restrictions regarding the shipment of spirits. Clients wishing to ship outside of the U.S. must arrange delivery through their carrier for international shipping. In addition, Zachys is unable to arrange common carrier delivery of hard liquor or spirits outside the state of NY. H LIVE ONLINE BIDDING! In addition to browsing the catalog and placing absentee bids online, now you can get in on the action live from the comfort of your home or office! Visit www.zachys.com/auctions for details. -
Wine Club “ May 2012 Extraordinary Team of Stonemasons to Fill in All Gaps in the Stone Work
wine club “ may 2012 extraordinary team of stonemasons to fill in all gaps in the stone work. RESTORING A Each side of the building will be checked, a process that will be time consuming but will help maintain the LEGEND structural integrity of our cellars. Inside the historic cellar walls major repairs are also being done. The strengthening of our stone winery’s walls consists of an innovative technique called Center Core Drilling. The reason we have applied this to the retrofit process is that it strengthens the exterior masonry walls with no visible evidence. Additional work inside includes, the three vaults (wine caves) reinforced as well as repairs and restoration to all three levels of this historic building. Our skilled restoration team has reached the half way point and every day progress is being made so that by fall, the champagne cellars will be reopened for all to see and experience again. Follow our progress online at BuenaVistaWinery.com Many have been forever charmed by Buena Vista and its cellars and vaults, the oldest stones of the California wine world. As one of our valued club members, you are part of our extended family and it is our goal to keep you informed during this SPARKLING WINE RETURNS TO exciting renovation. While we would love to have you visit every week, we realize BUENA VISTA for many of you that is not an option, so throughout this exciting progress we will While Agoston Haraszthy was most recognized as being the be updating our website www.buenavistawinery.com. We strongly encourage you Father of California viticulture, he was also the father of six to track our progress - you are just as much a part of it as we are.