Anl-79-94 High-Performance Batteries for Stationary
Total Page:16
File Type:pdf, Size:1020Kb
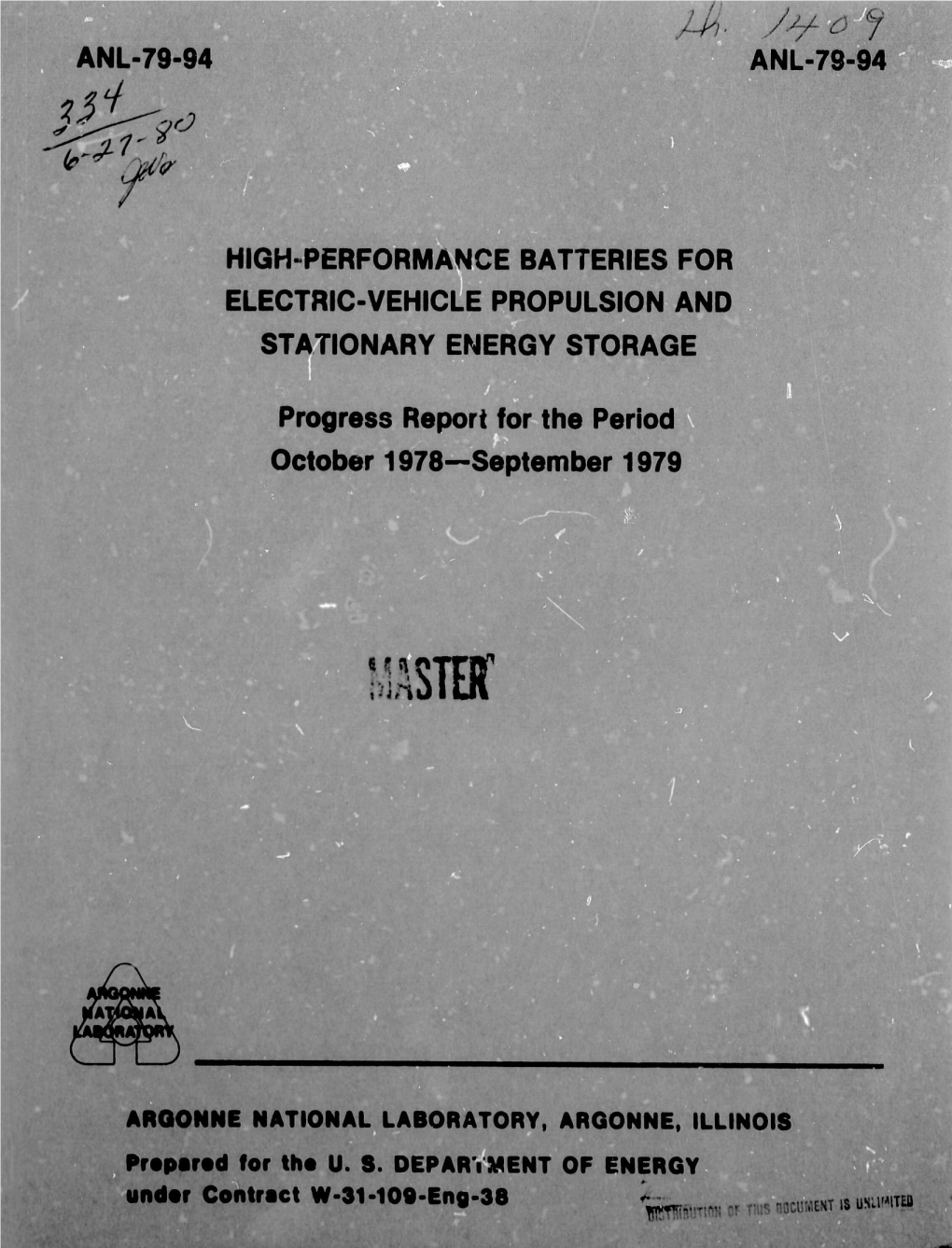
Load more
Recommended publications
-
Some Observations on Avoiding Pitfalls in Developing Future Flight Systems
AIAA 97-3209 Some Observations on Avoiding Pitfalls in Developing Future Flight Systems Gary L. Bennett Metaspace Enterprises Emmett, Idaho; U.S.A. 33rd AIAA/ASME/SAEIASEEJoint Propulsion Conference & Exhibit July 6 - 9, 1997 I Seattle, WA For permission to copy or republish, contact the American Institute of Aeronautics and Astronautics 1801 Alexander Bell Drive, Suite 500, Reston, VA 22091 SOME OBSERVATIONS ON AVOIDING PITFALLS IN DEVELOPING FUTURE FLIGHT SYSTEMS Gary L. Bennett* 5000 Butte Road Emmett, Idaho 83617-9500 Abstract Given the speculative proposals and the interest in A number of programs and concepts have been developing breakthrough propulsion systems it seems proposed 10 achieve breakthrough propulsion. As an prudent and appropriate to review some of the pitfalls cautionary aid 10 researchers in breakthrough that have befallen other programs in "speculative propulsion or other fields of advanced endeavor, case science" so that similar pitfalls can be avoided in the histories of potential pitfalls in scientific research are future. And, given the interest in UFO propulsion, described. From these case histories some general some guidelines to use in assessing the reality of UFOs characteristics of erroneous science are presented. will also be presented. Guidelines for assessing exotic propulsion systems are suggested. The scientific method is discussed and some This paper will summarize some of the principal tools for skeptical thinking are presented. Lessons areas of "speculative science" in which researchers learned from a recent case of erroneous science are were led astray and it will then provide an overview of listed. guidelines which, if implemented, can greatly reduce Introduction the occurrence of errors in research. -
Enhancing the Corrosion Resistance of Api 5L X70 Pipeline Steel Through Thermomechanically Controlled Processing
ENHANCING THE CORROSION RESISTANCE OF API 5L X70 PIPELINE STEEL THROUGH THERMOMECHANICALLY CONTROLLED PROCESSING A Thesis Submitted to the College of Graduate and Postdoctoral Studies In Partial Fulfillment of the Requirements For the Degree of Doctor of Philosophy In the Department of Mechanical Engineering University of Saskatchewan Saskatoon By Enyinnaya George Ohaeri © Copyright Enyinnaya George Ohaeri, April 2020. All rights reserved. PERMISSION TO USE In presenting this thesis, in partial fulfillment of the requirements for a degree of Doctor of Philosophy from the University of Saskatchewan, I agree that the Libraries of this University may make it freely available for inspection. I further agree that permission for copying this thesis in any manner, in whole or in part, for scholarly purposes may be granted by Professor Jerzy Szpunar, who supervised my thesis work or, in his absence, by the Head of the Department or the Dean of the College in which my thesis work was done. It is understood that any copying or publication or use of this thesis, or parts thereof, for financial gain shall not be allowed without my written permission. It is also understood that due recognition shall be given to me and to the University of Saskatchewan in any scholarly use which may be made of any material in my thesis. Requests for permission to copy or to make other use of material in this thesis in whole or in part should be addressed to: Head of the Department of Mechanical Engineering University of Saskatchewan 57 Campus Drive Saskatoon, Saskatchewan S7N 5A9 Canada OR Dean College of Graduate and Postdoctoral Studies University of Saskatchewan 116 Thorvaldson Building, 110 Science Place Saskatoon, Saskatchewan S7N 5C9 Canada i ABSTRACT Pipelines are widely used for transportation of oil and gas because they can carry large volume of these products at lower cost compared to rail cars and trucks. -
Difficult Experiments on Weird Rocks Written by G
PSR Discoveries:Hot Idea: Enstatite Meteorites http://www.psrd.hawaii.edu/Dec99/indarch.html posted December 17, 1999 Difficult Experiments on Weird Rocks Written by G. Jeffrey Taylor Hawai'i Institute of Geophysics and Planetology Enstatite meteorites are a diverse group of strange rocks. They contain little or no oxidized iron, a rare occurrence in the Solar System. Nevertheless, melting experiments on these oxygen-depleted meteorites give clues about magma compositions and core formation in asteroids. Tim McCoy (Smithsonian Institution), Tamara Dickinson (Catholic University), and Gary Lofgren (Johnson Space Center) heated an enstatite chondrite (called Indarch) to a range of temperatures above the temperature of initial melting. They found that the sulfide minerals in the rock melted at 1000o C. This disproved a hypothesis that the calcium sulfide in the rock formed at a very high temperature in the gas-dust cloud from which the planets formed and survived melting in igneous enstatite meteorites. The experiments also indicate that the metallic iron and sulfide minerals begin to form connected networks when only about 20% of the rocky material is melted. This suggests that core formation in the asteroid could have taken place at such low amounts of melting, rather than requiring much higher amounts of melting as some scientists have argued. The experiments also show that igneous enstatite meteorites could have formed from unmelted enstatite chondrites. Reference: McCoy, Timothy J., Tamara L.Dickinson, and Gary E. Lofgren, 1999, Partial melting of the Indarch (EH4) meteorite: A textural, chemical, and phase relations view of melting and melt migration, Meteoritics and Planetary Science, vol. -
Team Studies Rare Meteorite Possibly from the Outer Asteroid Belt 20 December 2012
Team studies rare meteorite possibly from the outer asteroid belt 20 December 2012 The asteroid approached on an orbit that still points to the source region of CM chondrites. From photographs and video of the fireball, Jenniskens calculated that the asteroid approached on an unusual low-inclined almost comet-like orbit that reached the orbit of Mercury, passing closer to the sun than known from other recorded meteorite falls. "It circled the sun three times during a single orbit of Jupiter, in resonance with that planet," Jenniskens said. Based on the unusually short time that the asteroid was exposed to cosmic rays, there was not much time to go slower or faster around the sun. That puts the original source asteroid very (Phys.org)—Scientists found treasure when they close to this resonance, in a low inclined orbit. studied a meteorite that was recovered April 22, 2012 at Sutter's Mill, the gold discovery site that "A good candidate source region for CM chondrites led to the 1849 California Gold Rush. Detection of now is the Eulalia asteroid family, recently the falling meteorites by Doppler weather radar proposed as a source of primitive C-class asteroids allowed for rapid recovery so that scientists could in orbits that pass Earth," adds Jenniskens. study for the first time a primitive meteorite with little exposure to the elements, providing the most pristine look yet at the surface of primitive asteroids. An international team of 70 researchers reported in today's issue of Science that this meteorite was classified as a Carbonaceous-Mighei or CM-type carbonaceous chondrite and that they were able to identify for the first time the source region of these meteorites. -
The Isotopic Abundance and Content of Sulfur I N
I THE ISOTOPIC ABUNDANCE AND CONTENT Hard copy (HC) OF SULFUR IN METEORITES * (,' .,. Microfiche (MF) LYY- I 1 Q by T. R. Kaplanl and J. R. Hulston" (Hexahedrites and Octahedrites) and stony (Enstatite achondrite, Carbonaceous, Enstatite and Olivine chondrites) families. The iron meteorites contain troilite as the chief sulfur component and the 6S34 ranges from 0 to 3 0.6'/00 with respect to Canyon Diablo troilite. Stony ner;eorites demonstrate a wide varieky of sulfur compounds fur, water, and acid soluble sulfates and unidentified components soluble only in aqua regia. The 6S34 content 3f the isolated compounds varies from 3-2.5 to -5.5'/00 ,vich respect to Canyon Diablo. The weighted average for t all components of each meteorite, however, falls within 4 5lo/oo of Canyon Diablo. The S33 distribution closely follows S34. The data suggest that differentiations have occurred in the meteorites starting from a single source K Division of Geological Sciences, California Institute of Technology, Pasadena, California. 209 WLlOl ALll13Vl CL,.Jartment of Physics, McMaster University, Hamilton, OnLario, Canada. * Contribution No. 1333 of the Division of Geological Sciences, I" California Institute of Technology, Pasadena, California. L C 2 of sulfur. There is no evidence for biological activity having occurred in the meteorite, either from the distribution of sulfur compounds- or from the isotope abundance data. This study has been supported by National Aeronautics and Space Administration Grant NsG 347/05-002-006. .' 3 INTRODUCTION Sulfur is a common and often important constituent of many meteorites, and since it is found in a number of minerals and sometimes occurs in various valence states ic one meteorite specimen, its distribution may closely reflect the history of the meteorite. -
Accretion of the Earth—Missing Components?
View metadata, citation and similar papers at core.ac.uk brought to you by CORE provided by Bern Open Repository and Information System (BORIS) Space Sci Rev (2020) 216:27 https://doi.org/10.1007/s11214-020-00649-y Accretion of the Earth—Missing Components? K. Mezger1 · M. Schönbächler2 · A. Bouvier3 Received: 5 February 2019 / Accepted: 19 February 2020 / Published online: 4 March 2020 © The Author(s) 2020 Abstract Primitive meteorites preserve the chemical and isotopic composition of the first aggregates that formed from dust and gas in the solar nebula during the earliest stages of solar system evolution. Gradual increase in the size of solid bodies from dust to aggregates and then to planetesimals finally led to the formation of planets within a few to tens of mil- lion years after the start of condensation. Thus the rocky planets of the inner solar system are likely the result of the accumulation of numerous smaller primitive as well as differ- entiated bodies. The chemically most primitive known meteorites are chondrites and they consist mostly of metal and silicates. Chondritic meteorites are derived from distinct prim- itive planetary bodies that experienced only limited element fractionation during formation and subsequent differentiation. Different chondrite classes show distinct chemical and iso- | downloaded: 27.12.2020 topic characteristics, which may reflect heterogeneities in the solar nebula and the slightly different pathways of their formation. To a first approximation the chemical composition of the bulk Earth bears great similarities to primitive meteorites. However, for some elements there are striking and significant differences. The Earth shows a much stronger depletion of the moderate to highly volatile elements compared to chondrites. -
Development of Novel Controllable Hydrogen Sulfide Donors
DEVELOPMENT OF NOVEL CONTROLLABLE HYDROGEN SULFIDE DONORS By YU ZHAO A dissertation submitted in partial fulfillment of The requirement for the degree of DOCTOR OF PHILOSOPHY WASHINGTON STATE UNIVERSITY Department of Chemistry May 2014 © Copyright by YU ZHAO, 2014 All Rights Reserved © Copyright by YU ZHAO, 2014 All Rights Reserved To the Faculty of Washington State University: The members of the Committee appointed to examine the dissertation of YU ZHAO find it satisfactory and recommend that it be accepted. Ming Xian, Ph.D., Chair Clifford E. Berkman, Ph.D. Jeffery P. Jones, Ph.D. Robert C. Ronald, Ph.D. ii ACKNOWLEDGMENT I would like to extend my sincere gratitude to my advisor, Dr. Ming Xian, for his supervision during my Ph.D. study at Washington State University (WSU). It was him who guided me towards the top research of hydrogen sulfide. He helped me to build my research interests in the field of organic chemistry and chemical biology. I have gained valuable experiences from Dr. Xian in experimental techniques and logical thinking, without which I could never build a solid background for my future career. I would always be thankful to my committee members, Dr. Cliff Berkman, Dr. Rob Ronald, and Dr. Jeff Jones, for their valuable suggestions in my research, seminars, and research proposals. I would thank Dr. Phil Garner for his comments in our group meetings. I would also thank our collaborators, Dr. David J. Lefer (Department of Pharmacology and Experimental Therapeutics and Cardiovascular Center of Excellence, Louisiana State University Health Sciences Center, New Orleans, LA) and Dr. -
1 the Lifecycle of Hollows on Mercury
The Lifecycle of Hollows on Mercury: An Evaluation of Candidate Volatile Phases and a Novel Model of Formation. 1 1 2 3 M. S. Phillips , J. E. Moersch , C. E. Viviano , J. P. Emery 1Department of Earth and Planetary Sciences, University of Tennessee, Knoxville 2Planetary Exploration Group, Johns Hopkins University Applied Physics Laboratory 3Department of Astronomy and Planetary Sciences, Northern Arizona University Corresponding author: Michael Phillips ([email protected]) Keywords: Mercury, hollows, thermal model, fumarole. Abstract On Mercury, high-reflectance, flat-floored depressions called hollows are observed nearly globally within low-reflectance material, one of Mercury’s major color units. Hollows are thought to be young, or even currently active, features that form via sublimation, or a “sublimation-like” process. The apparent abundance of sulfides within LRM combined with spectral detections of sulfides associated with hollows suggests that sulfides may be the phase responsible for hollow formation. Despite the association of sulfides with hollows, it is still not clear whether sulfides are the hollow-forming phase. To better understand which phase(s) might be responsible for hollow formation, we calculated sublimation rates for 57 candidate hollow-forming volatile phases from the surface of Mercury and as a function of depth beneath regolith lag deposits of various thicknesses. We found that stearic acid (C18H36O2), fullerenes (C60, C70), and elemental sulfur (S) have the appropriate thermophysical properties to explain hollow formation. Stearic acid and fullerenes are implausible hollow-forming phases because they are unlikely to have been delivered to or generated on Mercury in high enough volume to account for hollows. -
Mineralogical Variations Among High Albedo E-Type Asteroids: Implications for Asteroid Igneous Processes
Lunar and Planetary Science XXXV (2004) 1812.pdf MINERALOGICAL VARIATIONS AMONG HIGH ALBEDO E-TYPE ASTEROIDS: IMPLICATIONS FOR ASTEROID IGNEOUS PROCESSES. Michael J. Gaffey1 and Michael S. Kelley2, 1Space Studies Department, University of North Dakota, Box 9008, Grand Forks, ND 58202, email: [email protected]; 2Department of Geology and Geography, Georgia Southern University, Statesboro, GA 30460; email: [email protected] The link between the E-type asteroids and the pyroxene-plus-feldspar assemblage. Aubrites are enstatite achondrites (aubrites) was first proposed for mantle rocks from a highly reduced (E-chondrite-like) the original E-asteroid, 44 Nysa [1]. The association parent body(ies) which has undergone melting and was based on the high albedos and the featureless differentiation. The corresponding feldspar-rich spectra shared by the E-asteroids and the aubrites. basaltic rocks have not been identified in the meteorite Among the plausible geologic and meteoritic materials, collections and may have been erupted as gas-driven only enstatite (the magnesium end-member of the pyroclastic materials at velocities sufficient to escape pyroxene solid solution series) is sufficiently abundant their parent bodies and thus never formed discrete to comprise asteroid-sized bodies [2]. However, the lithologic units [7]. The E[I]-subtype probably presence of a weak 0.89 µm absorption feature in the represent mantle (and possibly crustal) material from a spectrum of 44 Nysa indicates that its pyroxene differentiated, highly reduced parent body of contains a small amount of Fe2+ but still substantially approximately enstatite chondrite composition. Based more than any aubrite present in the meteorite on melting experiments on enstatite chondrites, the collection [3]. -
Use of Air-Cooled Blast Furnace Slag As Coarse Aggregate in Concrete Pavements— a Guide to Best Practice
Use of Air-Cooled Blast Furnace Slag as Coarse Aggregate in Concrete Pavements— A Guide to Best Practice Prepared for Federal Highway Administration 1200 New Jersey Avenue, SE Washington, DC 20590 Report No. FHWA-HIF-12-009 February 2012 Notice—This report is disseminated under the sponsorship of the U.S. Department of Transportation in the interest of information exchange. The U.S. Government assumes no liability for the use of the information contained in this document. The U.S. Government does not endorse products or manufacturers. Trademarks or manufacturers’ names appear in this report only because they are considered essential to the objective of the document. Quality Assurance Statement—FHWA provides high-quality information to serve Government, industry, and the public in a manner that promotes public understanding. Standards and policies are used to ensure and maximize the quality, objectivity, utility, and integrity of its information. FHWA periodically reviews quality issues and adjusts its programs and processes to ensure continuous quality improvement. TECHNICAL REPORT DOCUMENTATION PAGE 1. Report No. 2. Government Accession No. 3. Recipient’s Catalog No. FHWA-HIF-12-009 4. Title and Subtitle 5. Report Date Use of Air-Cooled Blast Furnace Slag as Coarse February 2012 Aggregate in Concrete Pavements—A Guide to Best 6. Performing Organization Code: Practice 7. Author(s) 8. Performing Organization Report No. Kurt D. Smith, Dennis A. Morian, Thomas J. Van Dam 9. Performing Organization Name and Address 10. Work Unit No. Quality Engineering Solutions, Inc. 405 Water Street, PO Box 3004 11. Contract or Grant No. Conneaut Lake, PA 16316 DTFH61-08-D-00020-T-09001 12. -
A Mineralogical Context for the Organic Matter in the Paris Meteorite Determined by a Multi-Technique Analysis
life Article A Mineralogical Context for the Organic Matter in the Paris Meteorite Determined by A Multi-Technique Analysis Manale Noun 1,2,* , Donia Baklouti 3,* , Rosario Brunetto 3, Ferenc Borondics 4 , Thomas Calligaro 5,6 ,Zélia Dionnet 3,7, Louis Le Sergeant d’Hendecourt 3,8, Bilal Nsouli 2, Isabelle Ribaud 1, Mohamad Roumie 2 and Serge Della-Negra 1 1 Institut de Physique Nucléaire d’Orsay, UMR 8608, CNRS/IN2P3, Université Paris-Sud, Université Paris-Saclay, F-91406 Orsay, France; [email protected] (I.R.); [email protected] (S.D.-N.) 2 Lebanese Atomic Energy Commission, NCSR, Beirut 11-8281, Lebanon; [email protected] (B.N.); [email protected] (M.R.) 3 Institut d’Astrophysique Spatiale, UMR 8617, CNRS/Université Paris-Sud, Université Paris-Saclay, bâtiment 121, Université Paris-Sud, 91405 Orsay CEDEX, France; [email protected] (R.B.); [email protected] (Z.D.); [email protected] (L.L.S.d.) 4 Synchrotron Soleil, L’Orme des Merisiers, BP48, Saint Aubin, 91192 Gif sur Yvette CEDEX, France; [email protected] 5 Centre de Recherche et de Restauration des musées de France, UMR 171, Palais du Louvre, 75001 Paris, France; [email protected] 6 PSL Research University, Institut de Recherche Chimie Paris, Chimie ParisTech, CNRS UMR 8247, 75005 Paris, France 7 Università degli Studi di Napoli Parthenope, Dip. di Scienze e Tecnologie, CDN IC4, I-80143 Naples, Italy 8 Université Aix-Marseille, Laboratoire de Physique des Interactions Ioniques et Moléculaires (PIIM), UMR CNRS 7345, F-13397 Marseille, France * Correspondence: [email protected] (M.N.); [email protected] (D.B.); Tel.: +961-1-45-08-11 (M.N.); +33-1-69-85-87-88 (D.B.) Received: 30 March 2019; Accepted: 25 May 2019; Published: 30 May 2019 Abstract: This study is a multi-technique investigation of the Paris carbonaceous chondrite directly applied on two selected 500 500 µm2 areas of a millimetric fragment, without any chemical × extraction. -
Enstatite Chondrites EL3 As Building Blocks for the Earth: the Debate 1 Over the 146 Sm-142 Nd Systematics Maud Boyet, A
Enstatite chondrites EL3 as building blocks for the Earth: the debate 1 over the 146 Sm-142 Nd systematics Maud Boyet, A. Bouvier, P. Frossard, Tahar Hammouda, M. Garçon, Abdelmouhcine Gannoun To cite this version: Maud Boyet, A. Bouvier, P. Frossard, Tahar Hammouda, M. Garçon, et al.. Enstatite chondrites EL3 as building blocks for the Earth: the debate 1 over the 146 Sm-142 Nd systematics. Earth and Planetary Science Letters, Elsevier, 2018, 488, pp.68-78. 10.1016/j.epsl.2018.02.004. hal-01723716 HAL Id: hal-01723716 https://hal.uca.fr/hal-01723716 Submitted on 5 Mar 2018 HAL is a multi-disciplinary open access L’archive ouverte pluridisciplinaire HAL, est archive for the deposit and dissemination of sci- destinée au dépôt et à la diffusion de documents entific research documents, whether they are pub- scientifiques de niveau recherche, publiés ou non, lished or not. The documents may come from émanant des établissements d’enseignement et de teaching and research institutions in France or recherche français ou étrangers, des laboratoires abroad, or from public or private research centers. publics ou privés. 1 Enstatite chondrites EL3 as building blocks for the Earth: the debate 2 over the 146Sm-142Nd systematics 3 4 M. Boyet1, A. Bouvier2, P. Frossard1, T. Hammouda1, M. Garçon3, A. Gannoun1 5 1 Laboratoire Magmas et Volcans, Université Clermont Auvergne, France 6 2 Department of Earth Sciences, Centre for Planetary Science and Exploration, 7 University of Western Ontario, London, Canada 8 3 Department of Earth Sciences, ETH Zurich, Switzerland 9 10 Earth and Planetary Science Letters 488 (2018) 68–78 11 12 13 Keywords: 146Sm-142Nd systematics, enstatite chondrites, Earth’s evolution, Earth’s 14 building blocks 15 16 Abstract 17 The 146Sm-142Nd extinct decay scheme (146Sm half-life of 103 My) is a powerful tool 18 to trace early Earth silicate differentiation.