Isru-Based Robotic Construction Technologies for Lunar and Martian Infrastructures
Total Page:16
File Type:pdf, Size:1020Kb
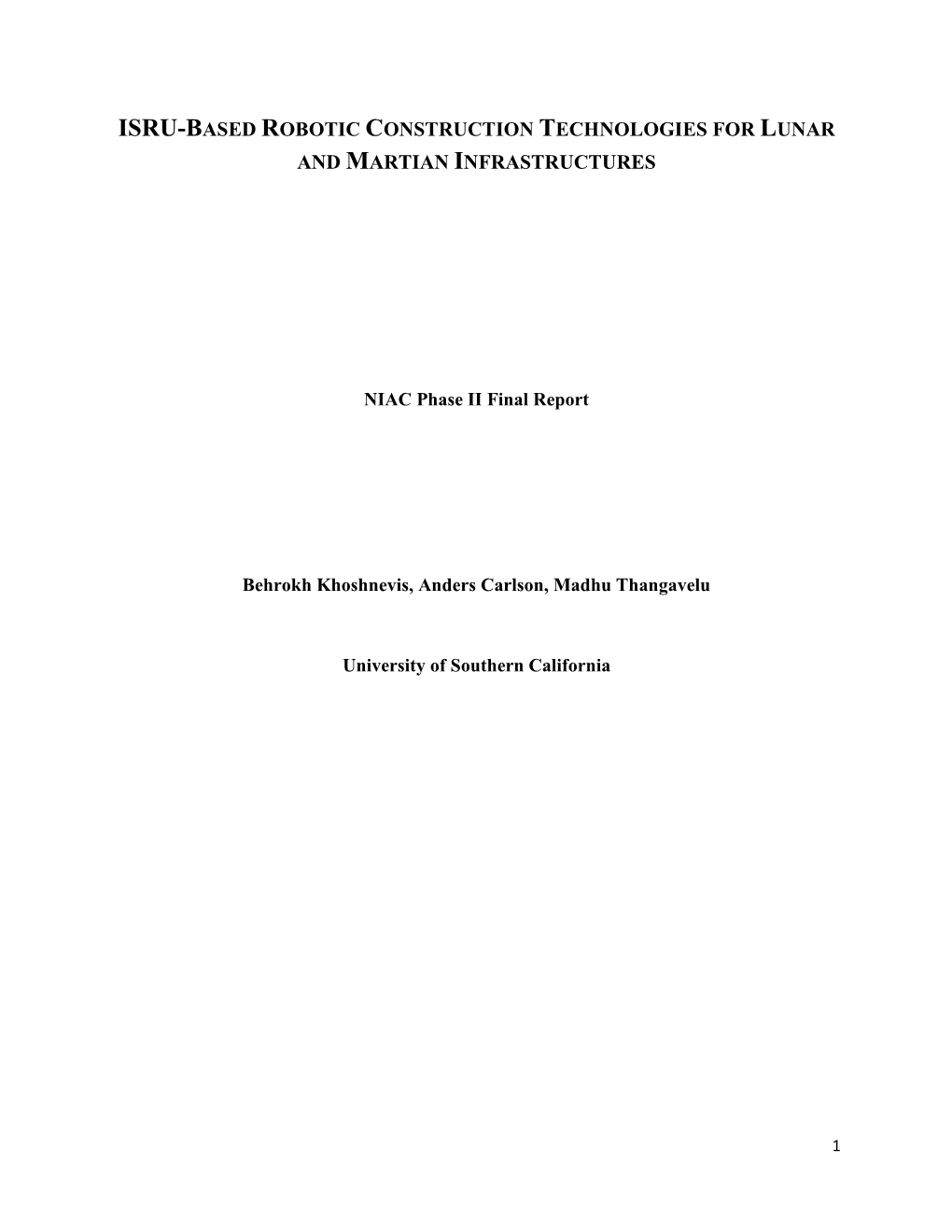
Load more
Recommended publications
-
An Investigation of High-Performance Self Compacting Concrete Under Flexural Loading
Civil Engineering and Architecture 8(6): 1414-1418, 2020 http://www.hrpub.org DOI: 10.13189/cea.2020.080624 An Investigation of High-Performance Self Compacting Concrete under Flexural Loading Theerthananda M P1,*, P C Srinivasa1, G M Naveen2 1Department of Civil Engineering, Government Engineering College, Kushalnagar, India 2Department of Civil Engineering, Government Engineering College, Chamarjanagar, India Received October 20, 2020; Revised November 25, 2020; Accepted December 30, 2020 Cite This Paper in the following Citation Styles (a): [1] Theerthananda M P, P C Srinivasa, G M Naveen, "An Investigation of High-Performance Self Compacting Concrete under Flexural Loading," Civil Engineering and Architecture, Vol. 8, No. 6, pp. 1414 - 1418, 2020. DOI: 10.13189/cea.2020.080624. (b): Theerthananda M P, P C Srinivasa, G M Naveen (2020). An Investigation of High-Performance Self Compacting Concrete under Flexural Loading. Civil Engineering and Architecture, 8(6), 1414 - 1418. DOI: 10.13189/cea.2020.080624. Copyright©2020 by authors, all rights reserved. Authors agree that this article remains permanently open access under the terms of the Creative Commons Attribution License 4.0 International License Abstract To shorten construction period, to assure compaction in the structure especially in confined zones where vibrating compaction is difficult and to eliminate noise due to vibration effective especially at concrete 1. Introduction products plants SCC is developed in practice. Also, SCC is applied to tunnel lining for preventing the cold joint High Performance Self Compacting Concrete (HPSCC) Self-compacting concrete has been used. Currently, the is the one which ability to Flow, good viscosity, main reasons for the employment of self-compacting segregation resistance and passing ability. -
Fiber in Continuously Reinforced Concrete Pavements 6
Technical Report Documentation Page 1. Report No. 2. Government 3. Recipient’s Catalog No. FHWA/TX-07/0-4392-2 Accession No. 4. Title and Subtitle 5. Report Date January 2006; Revised December 2006 Fiber in Continuously Reinforced Concrete Pavements 6. Performing Organization Code 7. Author(s) 8. Performing Organization Report No. Dr. Kevin Folliard, David Sutfin, Ryan Turner, and David P. 0-4392-2 Whitney 9. Performing Organization Name and Address 10. Work Unit No. (TRAIS) Center for Transportation Research 11. Contract or Grant No. The University of Texas at Austin 0-4392 3208 Red River, Suite 200 Austin, TX 78705-2650 12. Sponsoring Agency Name and Address 13. Type of Report and Period Covered Texas Department of Transportation Technical Report 9/1/01–8/31/03 Research and Technology Implementation Office 14. Sponsoring Agency Code P.O. Box 5080 Austin, TX 78763-5080 15. Supplementary Notes Project conducted in cooperation with the Federal Highway Administration and the Texas Department of Transportation. Project Title: Use of Fibers in Concrete Pavement 16. Abstract Continuously reinforced concrete pavement (CRCP) is a major form of highway pavement in Texas due to its increase in ride quality, minimal maintenance, and extended service life. However, CRCP may sometimes experience pavement distress that results in early failure, either due to under-design or the use of poor construction materials. Significant effort has been made to improve the performance of some of these materials (e.g. siliceous river gravel) to achieve an acceptable level of performance but has been unable to provide a practical solution. This research study investigates whether fiber reinforcement may solve some of the problems associated with siliceous river gravel, particularly spalling. -
111, Pp 7-13, December 2005
Concrete Beton, Volume 111, pp 7-13, December 2005 Variation in Cover to Reinforcement: Local and International Trends Author: P D Ronné Senior Structural and Forensic Engineer, BKS (Pty) Ltd., Cape Town ABSTRACT: Concrete cover to reinforcement is a critical parameter for durability. Despite a common perception that cover is a relatively simple subject, the terminology for cover suggests the converse. A brief review of cover meter devices, their operating principles and their appropriate use is presented. In particular, the lack of guidance in taking reliable cover surveys is identified and a suitable survey method is suggested. The variability of cover is further defined. Analyses of both international and local cover survey data are used to quantify the relationship of the relative variability measure using the coefficient of variation with the mean cover. The absolute variability measured using the standard deviation, is presented for the trend. An investigation has shown that the relative variability of cover increases significantly at low covers, and decreases at increased covers. South African construction exhibited higher absolute variability regarding the achievement of cover, as measured using the standard deviation. In building construction, the achievement of specified cover is quantitively shown to be more variable than that achieved on bridge construction projects in South Africa. Recommended tolerance margins for South African construction practice are proposed at 10mm, 15mm and 20mm for precision, normal in-situ and heavy civil works respectively. Note that full copyright of this publication belongs to the Concrete Society of Southern Africa NPC. Journal Contact Details: PO Box 75364 Lynnwood Ridge Pretoria, 0040 South Africa +27 12 348 5305 [email protected] www.concretesociety.co.za Oecember 2005 - NUM BER 111 Concrete Beton I!X __ i 4 .« u Cczz:ar 2& :z:&I&L 2 L&!li iL!!£J&i4j Technical Paper "....... -
Cathodic Protection of Concrete Bridges: a Manual of Practice
SHRP-S-372 Cathodic Protection of Concrete Bridges: A Manual of Practice J. E. Bennett John J. Bartholomew ELTECH Research Corporation Fairport Harbor, Ohio James B. Bushman Bushman & Associates Medina, Ohio Kenneth C. Clear K. C. Clear, Inc. Boston, Virginia Robert N. Kamp Consulting Engineer Albany, New York Wayne J. Swiat Corrpro Companies, Inc. Medina, Ohio Strategic Highway Research Program National Research Council Washington, DC 1993 SHRP-S-372 ISBN 0-309-05750-7 Contract C-102D Product No. 2034 Program Manager: Don M. Harriott Project Manager: It. Martin (Marty) Laylor Consultant: John P. Broomfield Production Editor: Cara J. Tate Program Area Secretary: Carina S. Hreib December 1993 key words: bridges bridge maintenance bridge rehabilitation cathodic protection chlorides corrosion corrosion prevention corrosion rate CP electrochemical methods reinforced concrete Strategic Highway Research Program National Academy of Sciences 2101 Constitution Avenue N.W. Washington, DC 20418 (202) 334-3774 The publication of this report does not necessarily indicate approval or endorsement of the findings, opinions, conclusions, or recommendations either inferred or specifically expressed herein by the National Academy of Sciences, the United States Government, or the American Association of State Highway and Transportation Officials or its member states. © 1993 National A_zademy of Sciences I.SM/NAP/1293 Acknowledgments The research described herein was supported by the Strategic Highway Research Program (SHRP). SHRP is a unit of the National Research Council that was authorized by section 128 of the Surface Transportation and Uniform Relocation Assistance Act of 1987. This report is a compilation of work by ELTECH Research Corporation, Corrpro Companies, Inc., and Kenneth C. -
Some Observations on Avoiding Pitfalls in Developing Future Flight Systems
AIAA 97-3209 Some Observations on Avoiding Pitfalls in Developing Future Flight Systems Gary L. Bennett Metaspace Enterprises Emmett, Idaho; U.S.A. 33rd AIAA/ASME/SAEIASEEJoint Propulsion Conference & Exhibit July 6 - 9, 1997 I Seattle, WA For permission to copy or republish, contact the American Institute of Aeronautics and Astronautics 1801 Alexander Bell Drive, Suite 500, Reston, VA 22091 SOME OBSERVATIONS ON AVOIDING PITFALLS IN DEVELOPING FUTURE FLIGHT SYSTEMS Gary L. Bennett* 5000 Butte Road Emmett, Idaho 83617-9500 Abstract Given the speculative proposals and the interest in A number of programs and concepts have been developing breakthrough propulsion systems it seems proposed 10 achieve breakthrough propulsion. As an prudent and appropriate to review some of the pitfalls cautionary aid 10 researchers in breakthrough that have befallen other programs in "speculative propulsion or other fields of advanced endeavor, case science" so that similar pitfalls can be avoided in the histories of potential pitfalls in scientific research are future. And, given the interest in UFO propulsion, described. From these case histories some general some guidelines to use in assessing the reality of UFOs characteristics of erroneous science are presented. will also be presented. Guidelines for assessing exotic propulsion systems are suggested. The scientific method is discussed and some This paper will summarize some of the principal tools for skeptical thinking are presented. Lessons areas of "speculative science" in which researchers learned from a recent case of erroneous science are were led astray and it will then provide an overview of listed. guidelines which, if implemented, can greatly reduce Introduction the occurrence of errors in research. -
Alkali-Silica Reactivity: an Overview of Research
SHRP-C-342 Alkali-Silica Reactivity: An Overview of Research Richard Helmuth Construction Technology Laboratories, Inc. With contributions by: David Stark Construction Technology Laboratories, Inc. Sidney Diamond Purdue University Micheline Moranville-Regourd Ecole Normale Superieure de Cachan Strategic Highway Research Program National Research Council Washington, DC 1993 Publication No. SHRP-C-342 ISBN 0-30cL05602-0 Contract C-202 Product No. 2010 Program Manager: Don M. Harriott Project Maxtager: Inam Jawed Program AIea Secretary: Carina Hreib Copyeditor: Katharyn L. Bine Brosseau May 1993 key words: additives aggregate alkali-silica reaction cracking expansion portland cement concrete standards Strategic Highway Research Program 2101 Consti!ution Avenue N.W. Washington, DC 20418 (202) 334-3774 The publicat:Lon of this report does not necessarily indicate approval or endorsement by the National Academy of Sciences, the United States Government, or the American Association of State Highway and Transportation Officials or its member states of the findings, opinions, conclusions, or recommendations either inferred or specifically expressed herein. ©1993 National Academy of Sciences 1.5M/NAP/593 Acknowledgments The research described herein was supported by the Strategic Highway Research Program (SHRP). SHRP is a unit of the National Research Council that was authorized by section 128 of the Surface Transportation and Uniform Relocation Assistance Act of 1987. This document has been written as a product of Strategic Highway Research Program (SHRP) Contract SHRP-87-C-202, "Eliminating or Minimizing Alkali-Silica Reactivity." The prime contractor for this project is Construction Technology Laboratories, with Purdue University, and Ecole Normale Superieure de Cachan, as subcontractors. Fundamental studies were initiated in Task A. -
Reinforced Concrete Failure Mechanisms
Reinforced Concrete Failure Mechanisms Best Practices in Dam and Levee Safety Risk Analyses Part E – Concrete Structures Chapter E-2 Last modified June 2017, Presented July 2019 Reinforced Concrete Failure Mechanisms OUTLINE: • Types of Structures • Spillway Piers • Navigation Lock Walls • Floodwalls • Slabs • Buttresses • Factors influencing strength and stability of reinforced concrete sections • National code requirements in the context of risk • Considerations when determining risk analysis failure probabilities based on structural analysis results • Typical event tree of the progression of failure 2 Reinforced Concrete Failure Mechanisms OBJECTIVES: • Get a broad overview of potential failure modes for different kinds of reinforced concrete structures • Understand the mechanisms that affect reinforced concrete failures • Understand how to construct an event tree to represent reinforced concrete failures • Understand how to estimate event probabilities and probability of breach Reinforced Concrete Failure Mechanisms SUMMARY OF KEY CONCEPTS: • Significant uncertainty for reinforced concrete failure mechanisms under seismic loading due to limited case histories • Concrete and reinforcement material properties can be determined with confidence for dams and floodwalls. • Type and duration of loading is important to understand – consider both static and earthquake loading • Ductile and Brittle Failure mechanisms • Seismic reinforcement details have changed dramatically over the past few decades; older concrete hydraulic structures may be -
New Fayette County Prison Volume 2 Divisions 03
SECTION 03 1000 CONCRETE FORMING AND ACCESSORIES PART 1 GENERAL 1.01 RELATED DOCUMENTS A. Drawings and general provisions of contract, including General and Supplementary Conditions and other Division 01 specification sections, apply to requirements of this Section. 1.02 SECTION INCLUDES A. Formwork for cast-in place concrete, with shoring, bracing and anchorage. B. Openings for other work. C. Form accessories. D. Form stripping. 1.03 RELATED REQUIREMENTS A. Section 03 2000 - Concrete Reinforcing. B. Section 03 3000 - Cast-in-Place Concrete. C. Section 04 2001 - Masonry Veneer: Spacing for veneer anchor reglets recessed in concrete. 1.04 REFERENCE STANDARDS A. ACI 117 - Specifications for Tolerances for Concrete Construction and Materials. B. ACI 301 - Specifications for Structural Concrete. C. ACI 318 - Building Code Requirements for Structural Concrete and Commentary. D. ACI 347R - Guide to Formwork for Concrete. E. ASTM B221 - Standard Specification for Aluminum and Aluminum-Alloy Extruded Bars, Rods, Wire, Profiles, and Tubes. F. ASTM B221M - Standard Specification for Aluminum and Aluminum-Alloy Extruded Bars, Rods, Wire, Profiles, and Tubes (Metric). G. PS 1 - Structural Plywood. 1.05 SUBMITTALS A. Shop Drawings: Indicate pertinent dimensions, materials, bracing, and arrangement of joints and ties. B. Designer's Qualification Statement. C. Design Data: As required by authorities having jurisdiction. 1.06 QUALITY ASSURANCE A. Designer Qualifications: Design formwork under direct supervision of a Professional Structural Engineer experienced in design of concrete formwork and licensed in the State in which the Project is located. 1.07 DELIVERY, STORAGE, AND HANDLING A. Deliver prefabricated forms and installation instructions in manufacturer's packaging. -
Guide to Concrete Repair Second Edition
ON r in the West August 2015 Guide to Concrete Repair Second Edition Prepared by: Kurt F. von Fay, Civil Engineer Concrete, Geotechnical, and Structural Laboratory U.S. Department of the Interior Bureau of Reclamation Technical Service Center August 2015 Mission Statements The U.S. Department of the Interior protects America’s natural resources and heritage, honors our cultures and tribal communities, and supplies the energy to power our future. The mission of the Bureau of Reclamation is to manage, develop, and protect water and related resources in an environmentally and economically sound manner in the interest of the American public. Acknowledgments Acknowledgment is due the original author of this guide, W. Glenn Smoak, for all his efforts to prepare the first edition. For this edition, many people were involved in conducting research and field work, which provided valuable information for this update, and their contributions and hard work are greatly appreciated. They include Kurt D. Mitchell, Richard Pepin, Gregg Day, Jim Bowen, Dr. Alexander Vaysburd, Dr. Benoit Bissonnette, Maxim Morency, Brandon Poos, Westin Joy, David (Warren) Starbuck, Dr. Matthew Klein, and John (Bret) Robertson. Dr. William F. Kepler obtained much of the funding to prepare this updated guide. Nancy Arthur worked extensively on reviewing and editing the guide specifications sections and was a great help making sure they said what I meant to say. Teri Manross deserves recognition for the numerous hours she put into reviewing, editing and formatting this Guide. The assistance of these and numerous others is gratefully acknowledged. Contents PART I: RECLAMATION'S METHODOLOGY FOR CONCRETE MAINTENANCE AND REPAIR Page A. -
USG Levelrock® 2500 Floor Underlayment Architectural Spec
SECTION 03540 [03 54 13] ® Cementitious Underlayment LEVELROCK ™ 2500 Specification PART 1 - GENERAL ***Notes to Architect are highlighted in red**** 1.01 SUMMARY A. Description of Work: Work of this sections includes self leveling underlayment for interior finish flooring but is not limited to, the following: ® 1. LEVELROCK 2500™ Floor Underlayment covering normal project conditions and applications. 2. Division 3 Section “Concrete Toppings” applied over various substrates. 3. Division 9 Section sound control, patching, and leveling compounds applied with finish flooring. 1.02 REFERENCES A. ASTM C472 Compressive Strength B. ASTM C33 Sand Aggregate C. ASTM D4263 Standard test method for indicating moisture in concrete D. ASTM F2419 Standard test method for installation of thick poured Gypsum concrete and preparation of surface to receive resilient flooring E. ASTM E492 Impact Insulation Class (IIC) F. ASTM E90 Sound Transmission Class (STC) 1.03 RELATED WORK SPECIFIED ELSEWHERE A. See Section 9 for acceptable flooring materials including vinyl, tile, wood, and laminates. 1.04 SUBMITTALS A. Product Data: Submit manufacturer’s specifications and installation instructions with project conditions and materials clearly identified or detailed for each required product or system. B. Acoustical Data: Submit sound tests according to IBC code criteria ASTM E492 (IIC) and ASTM E90 (STC) 1. Submit in writing that all sound tests or data provided has been tested according to UL (Underwriters Laboratory) fire resistance design number. ® ™ Cementitious 03540 - 1 LEVELROCK 2500 Underlayment Floor Underlayment Updated 9/6/06 1.05 SYSTEM REQUIREMNETS A. Performance Requirements: ® 1. LEVELROCK 2500™ Floor Underlayment a. Minimum compressive strength 2,500 psi. -
224641234.Pdf
View metadata, citation and similar papers at core.ac.uk brought to you by CORE provided by Helsingin yliopiston digitaalinen arkisto ASTROBIOLOGY Volume 19, Number 3, 2019 Mary Ann Liebert, Inc. DOI: 10.1089/ast.2018.1870 A Low-Diversity Microbiota Inhabits Extreme Terrestrial Basaltic Terrains and Their Fumaroles: Implications for the Exploration of Mars Charles S. Cockell,1 Jesse P. Harrison,2,3 Adam H. Stevens,1 Samuel J. Payler,1 Scott S. Hughes,4 Shannon E. Kobs Nawotniak,4 Allyson L. Brady,5 R.C. Elphic,6 Christopher W. Haberle,7 Alexander Sehlke,6 Kara H. Beaton,8 Andrew F.J. Abercromby,9 Petra Schwendner,1 Jennifer Wadsworth,1 Hanna Landenmark,1 Rosie Cane,1 Andrew W. Dickinson,1 Natasha Nicholson,1 Liam Perera,1 and Darlene S.S. Lim6,10 Abstract A major objective in the exploration of Mars is to test the hypothesis that the planet hosted life. Even in the absence of life, the mapping of habitable and uninhabitable environments is an essential task in developing a complete understanding of the geological and aqueous history of Mars and, as a consequence, understanding what factors caused Earth to take a different trajectory of biological potential. We carried out the aseptic collection of samples and comparison of the bacterial and archaeal communities associated with basaltic fumaroles and rocks of varying weathering states in Hawai‘i to test four hypotheses concerning the diversity of life in these environments. Using high-throughput sequencing, we found that all these materials are inhabited by a low-diversity biota. Multivariate analyses of bacterial community data showed a clear separation between sites that have active fumaroles and other sites that comprised relict fumaroles, unaltered, and syn-emplacement basalts. -
Reinforcing Steel Cover When Reinforcing Steel Is Too Close to the Surface, It Begins Rusting and Expanding, Causing the Surrounding Concrete to Break Away
BRANZ FACTS MID-RISE BUILDINGS #4 Exposed issues – reinforcing steel cover When reinforcing steel is too close to the surface, it begins rusting and expanding, causing the surrounding concrete to break away. STEEL REINFORCING BARS are used in concrete and concrete masonry to provide resistance to tensile loads and for concrete slabs and panels to help limit the risk of shrinkage cracking as the material cures. The steel relies on being sufficiently deep (called cover) within the concrete to protect it from moisture and corrosion. Where it is too close to the surface or the concrete is poor quality, it will begin rusting. As steel rusts, it expands, and this can result in concrete spalling – where pieces of concrete are broken away by the expanding steel. As the concrete breaks away or cracks, more moisture can get in and the deterioration will accelerate. The corrosion will also reduce the tensile strength of the steel as the steel deteriorates. How much cover? How much cover depends on: NZS 4229:2013 Concrete masonry buildings Tables 1 and 2 outline the requirements ● what the steel is embedded in – concrete not requiring specific engineering design: from NZS 3101.1&2:2006 Concrete structures or the grouted cells of concrete masonry ● For concrete masonry: standard. ● concrete or grout strength • 45 mm in exposure zone B For concrete masonry structures built to ● what the surface of the concrete is • 50 mm in exposure zone C NZS 4229:2013, the cover requirements from exposed to – soil or air • 60 mm in exposure zone D. the external face of uncoated masonry are: ● the corrosion or environmental zone ● For concrete: ● for exposure zone B – 45 mm with 17.5 ● the type of steel used – mild steel, • 75 mm for concrete placed directly on MPa grout galvanised, stainless steel or against the ground (can be reduced ● for exposure zone C – 50 mm with 20 ● intended life of the structure to 50 mm where there is a DPM MPa grout ● cement type.