S9086-Cj-Stm-010/Ch-075R2 Revision 2
Total Page:16
File Type:pdf, Size:1020Kb
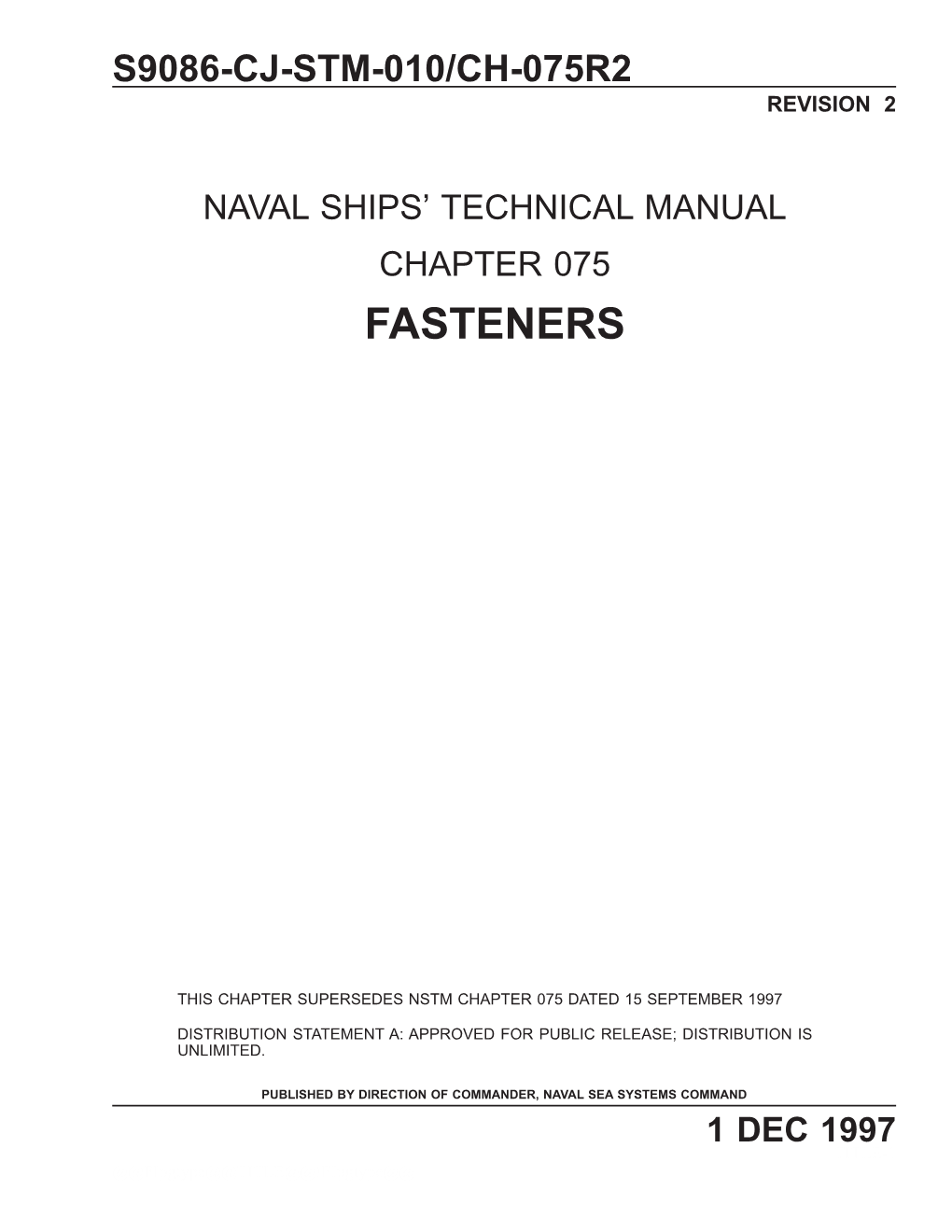
Load more
Recommended publications
-
[email protected]
BOLTING Basics, Tips & Best Practices g... urin Feat SmartBolts® Direct Tension Indicating Fasteners™ Address: 202 Perry Parkway, Suite 7 Gaithersburg, MD 20877 United States Phone: +1 (240) 631-7246 Fax: +1 (240) 750-6025 Email: [email protected] URL: www.smartbolts.com www.stressindicators.com Stress Indicators Incorporated is a solutions-driven engineering and manufacturing firm based in Maryland, USA. Formed in 1992, we provide innovative Visual Indication Systems™ solutions for customers worldwide. Stress Indicators Incorporated invented and developed SmartBolts® technology and commercialized the products to enable broad industry acceptance. All SmartBolts® are manufactured from quality fasteners at our USA facility. Disclaimer While we try to make sure that all data/information posted in this report is accurate at all times, we are not responsible for typographical and other errors that may appear. Data/Information is subject to change without notice. Stress Indicators assumes no responsibility or liability for any damages incurred directly or indirectly as a result of any data errors, omissions, or discrepancies. BOLTING Basics, Tips & Best Practices Table of Contents Introduction ................................................................................................................................................. 4 Part One: Basics of Specifying a Bolt Step One: Specifying the Basics of a Fastener .......................................................................................... 6 Selecting a Head Type ............................................................................................................................. -
Michigan Underground Storage Tank Rules
DEPARTMENT OF LICENSING AND REGULATORY AFFAIRS BUREAU OF FIRE SERVICES STORAGE TANK DIVISION UNDERGROUND STORAGE TANK REGULATIONS Filed with the Secretary of State on November 14, 2018 These rules become effective immediately upon filing with the Secretary of State unless adopted under section 33, 44, 45a(6), or 48 of 1969 PA 306. Rules adopted under these sections become effective 7 days after filing with the Secretary of State. (By authority conferred on the director of the department of licensing and regulatory affairs by section 21106 of 1994 PA 451, MCL 324.21106, and Executive Reorganization Order Numbers 1995-16, 1998-2, 2009-31, 2011-1, and 2012-7, MCL 324.99903, 29.461, 324.99919, 324. 99921, and 29.462.) R 29.2101, R 29.2103, R 29.2105, R 29.2107, R 29.2109, R 29.2111, R 29.2113, R 29.2115, R 29.2117, R 29.2119, R 29.2121, R 29.2122, R 29.2123, R 29.2125, R 29.2126, R 29.2127, R 29.2129, R 29.2131, R 29.2133, R 29.2135, R 29.2137, R 29.2139, R 29.2151, R 29.2153, R 29.2155, R 29.2157, R 29.2159, R 29.2161, R 29.2163, R 29.2163a, R 29.2163b, R 29.2163c, R 29.2163d, R 29.2163e, R 29.2164, R 29.2166, R 29.2166a, R 29.2167, R 29.2168, R 29.2168a, R 29.2168b, R 29.2168c, R 29.2168d, R 29.2169, R 29.2170, R 29.2171, R 29.2172, and R 29.2174 are amended, R 29.2108, R 29.2141, R 29.2143, R 29.2145, R 29.2147, R 29.2149, R 29.2165, and R 29.2173 are rescinded, and R 29.2114, R 29.2116, R 29.2120, R 29.2120a, R 29.2130, R 29.2162, R 29.2163f, R 29.2163g, R 29.2165a, R 29.2165b, R 29.2175, R 29.2176, R 29.2177, R 29.2178, R 29.2178a, R 29.2179, R 29.2180, R 29.2190, R 29.2191, and R 29.2192 are added to the Code, to read as follows: R 29.2101 Adoption of standards by reference. -
PDF Product List
STRUCTURAL BOLTS MACHINE BOLTS NUTS A325 Screw Only, A193 B7 Heavy Hex Head Bolt Acorn (Cap) Nut Domestic & Import A307A Breakaway Bolt Allen Nut A325 Bolt with Nut A307B Heavy Head Bolt Cap (Acorn) Nut A325 Type 3 Bolt, Domestic F1554 Hex Machine Bolt Castle Nut A325 Interference Body Bolt (Grades 36, 55, & 105) Coupling Nut Canadian A325 Bolt w/DH Nut, Square Head Machine Bolt Coupling Nut, Reducer Hot Dip Galvanized Coupling Nut, Heavy Duty A490 Screw Only, BOLTS & SCREWS Hex Nut Domestic & Import Carriage Bolt Hex Nut, Left Hand TC A325 Assembly, Countersunk Bolt Hex Nut, Heavy Grade 4 Domestic& Import Counterbore Screw, 12 Point Hex Nut, Heavy, Grade 7 TC A490 Assembly, Elevator Bolt Hvy Double Recess Guardrail Nut Domestic & Import Flange Bolt Jack Nut Flat Head Bolt, Slotted Jam Nut STRUCTURAL NUTS Guardrail Bolt Jam Nut, Left Hand A194 2H Nut, Domestic Hanger Bolt Flange Nut A194 2H Nut, Import Lag Screw High Nut A563 Grade DH Heavy Nut, Lag Screw, 1-Way Truss Head Knurled Nut Domestic Lag Screw, Indented HWH Machine Screw Nut, Hex A563 DH Type 3 Nut Full Thread Machine Screw Nut, Small Pattern ANCO Heavy Hex Locknut Lag Screw, Square Head Machine Screw Nut, Square ANCO Finished Locknut Penta Head Bolt Palnut ANCO 2H Heavy Locknut Place Bolt Panel Nut ANCO A325 Locknut Plow Bolt, Grade 2 Slotted Nut Plow Bolt, Grade 5 Slotted Nut, Heavy STRUCTURAL WASHERS Plow Bolt, Grade 8 Square Nut F436 Hardened Washer Shaker Screen Bolt, Grade 5 Square Nut, Heavy Domestic & Import Shackle Bolt Tee Nut F436 Type 3 Washer Security Bolt Wing -
Fastener Identification Guide • 4.13 KM • Printed in the USA
HEAD STYLES Hex Cap Screw Bugle Hex cap screws feature a washer face on the Button Washer bearing surface, a chamfered point, and tighter body tolerances than hex bolts. Pan Binding Undercut Hex Bolt Similar to hex cap screw, hex bolts do not require a washer face or a pointed end and have a greater tolerance range in the body. Round Head Fillister Socket Head Cap Screw Socket heads feature an internal hexagonal drive DRIVES socket and close tolerances for precision assembly. Flat 82° Cross Recess Button Head Socket Cap Screw Type I FASTENER (Phillips) Button heads feature a dome shaped head, though Flat 100° this feature reduces the tensile capacity. Cross Recess Flat Head Socket Cap Screw Type IA Flat heads feature an 82° countersunk head for Flat Undercut (Pozidriv®) IDENTIFICATION flush connections. Like the button heads, this feature reduces the tensile capacity. Cross Recess Type II (Frearson) Low Head Socket Cap Screw Indented Hex Low heads are similar to standard socket heads, but with a shorter head for applications where clearance Cross Recess Square GUIDE is an issue. This head configuration also reduces the Combo strength capacity. Indented Hex Washer (Quadrex®) NUTS Carriage Bolt A round head bolt with a square neck under the Slotted head. These must be tightened with a nut. Serrated Hex Finished Hex Nuts: Hex Coupling Nuts: Washer Hexagonal shaped nuts with internal screw Designed to join two externally threaded Plow Bolt threads. Finished hex nuts are one of the most objects, usually threaded rod, together. Combination Similar to a carriage bolt, these have a flat head common nuts used. -
Threaded Fasteners
Threaded Fasteners Introduction If you are designing and building a Formula SAE vehicle, threaded fasteners will likely be used to join the various components and systems together and allow the vehicle to function as a unified machine. The reliability of your vehicle is key to realize your potential at the competition. Even though threaded fasteners have been in use for hundreds of years and are in products that we use every day, their performance is dependent on a wide range of factors. This chapter covers some of the main factors that can influence reliability and is intended as an aid in joint design, fastener selection, and installation. The first portion of this chapter covers several design and installation factors that can work together to improve the reliability of your vehicle’s bolted joints. These topics include, the importance of generating and maintaining clamp load, and how clamp load, along with joint stiffness, can work together to prevent self-loosening and improve fatigue performance. The second portion of this chapter reviews how installation method and torque are related to clamp load, and also includes a comparison between common fastener types to aid in selection. The chapter concludes with a short tutorial showing how to obtain Mil Spec information on fasteners and similar hardware. Disclaimer – Multiple factors on each component in a bolted joint affect its performance. Additionally, service requirements for every joint differ. Each joint must be evaluated and tested for its ability to perform the desired function. The information in this chapter provides general background and does not represent how a specific design or piece of hardware will perform. -
Cord Buckles Center-Release Spaenaur Home Spaenaur 2 All Rights Rights All Reserved
1-800-265-8772 [email protected] Spaenaur Home Full Spaenaur Catalog Contact Us Français Metric Center-Release Buckles / Cord Locks & Cord Ends Métrique Boucles à dégagement central / Autobloqueurs et embouts de cordon EXTRA STRONG CLIP BUCKLE (Clip and Hold) Suitable for webbings of Terylene, Nylon, etc. Special protection against accidental opening. Used on Life-Saving Jackets, heavy Rucksacks, etc. 86 mm 122-A01-1M. Suitable for 40 mm strap of 1.4 - 1.5 mm thickness. The surface of the strap should not be too smooth. Mounting without sewing or rivets. Insert the strap in the clip and holder to the desired length. The Clip Buckle remains in position whether the strap is in use or not, but is nevertheless adjustable. Adjust the position by pushing the outer part of the strap inwards in order to release the strap. The loose end is hidden by the outer 122-A01-1M part of the strap. SPAENAUR Strap Strap PKG No. Colour Width Thickness QTY. 122-A01-1M Black 40 mm 1.4 to 1.5 mm 10 M All CORD BUCKLE Buckles Holder and locking wheel have supplied separately. White Locking Used for bags and clothing. E.g. ruck- Wheel sacks, duffel bags, laundry bags, CATALOG 14 C CATALOG AT sleeping bag covers, anoraks, ALOG 1 swimming trunks, sou’westers. 4 SPAENAUR No. For Cord Size WHITE BLACK PKG QTY. 25 2 mm 122-652 122-655 3-4 mm 122-660 122-663 MOUNTING: After threading the cord through the holder, push in the locking wheel. Knot the ends of the cord. -
Engineered Domestic Lock Nuts
LOCK NUTS Engineered Domestic Lock Nuts Principal Products: Markets Collarlok® Nuts Aerospace ESlok® Nuts Automotive Brake, Exhaust, Fuel, Interior Trunk, Fuel, Strux® Nuts Power Steering, Power Train, Suspension Whiz Lock® Nuts Agriculture Wheel nuts Sickle Bar Guards, Wheel Fastening Nut & bracket assemblies Truck and Trailer Nut & washer assemblies Bearing Retention, Wheel Fastening Nylon nuts Industrial Fasteners used for assemblies All metal lock nuts Lawn and Garden Lawn Tractor Components, Shift Linkages Collarlok® The Collarlok prevailing torque hex or flange nut design offers the reuse characteristics of the proven ESNA insert type. A red nylon collar bonded into the head of the nut provides a prevailing torque type nut with the advantage of high speed assembly using automatic assembly tools. The non-galling collar offers superior vibration performance in standard or metric threads. ESlok® The ESlok red nylon locking patch type fastener has a controlled amount of red nylon permanently bonded to the threads of the standard hex nut and to the center threads of the nut permitting either end entry of the bolt for automatic machine assembly. Parts are easily removed with a wrench and may be reused up to five times. No metal is removed or distorted insuring the tensile strength and non-galling characteristics of an ESlok self-locking fastener. 2369 Schuetz Road Saint Louis, Missouri 63146 Phone 314/ 567-8585 Fax 314/567-7334 LOCK NUTS Strux® Nuts The Strux nuts system provides a completely automated, accurate and reliable method for installing fasteners, as well as eliminating expensive manual secondary operations and increasing productivity. The result is a precisely located threaded hole that becomes an integral part of the steel plate. -
Maclean ESNA's Catalog
611 COUNTRY CLUB ROAD POCAHONTAS, ARKANSAS 72445 SALES: 1-(800)-331-6469 FAX: 1-(870)-892-8938 WWW.MACLEANFOGGCS.COM 1 The ESNA® story began in 1927, when a young engineer named Carl Arthur Swanstrom came to this country from Sweden. He brought with him a license to manufacture and sell a unique new self-locking fastener. The Inventor called the new fastener an “Elastic Stop® nut” because the nut remained “stopped” anywhere along the bolt threads. A non-damaging insert, fitted into the top of the nut, gripped the bolt threads firmly, holding the nut in position without seating against the work or using secondary locking devices. The only problem with the new nut was the inability to mass-produce them. The next few years were spent perfecting an automatic assembly machine to insert the locking device into the top of the nut. Swanstrom perfected the machine in the early 1930s and only four years later the Elastic Stop® Nut Corporation of America was founded. A threaded fastener, able to positively resist the loosening effect of vibration, had long been sought by manufacturers of every type of equipment. The Elastic Stop® nut proved to be the answer — totally reliable, able to reduce maintenance costs and prevent equipment failure. The outstanding performance of the Elastic Stop® nut was further substantiated in 1943 when the Air Force tested and issued the first approval letter to use ESNA® fasteners on military aircraft, both fuselage and engines. During WWII billions of Elastic Stop® nuts were produced for every branch of the armed services. -
Neutron Diffraction Study of Engineering Materials Subjected to Complex Loadings
University of Tennessee, Knoxville TRACE: Tennessee Research and Creative Exchange Doctoral Dissertations Graduate School 8-2014 Neutron Diffraction Study of Engineering Materials Subjected to Complex Loadings Jeffrey R. Bunn University of Tennessee - Knoxville, [email protected] Follow this and additional works at: https://trace.tennessee.edu/utk_graddiss Part of the Civil Engineering Commons, and the Structural Materials Commons Recommended Citation Bunn, Jeffrey R., "Neutron Diffraction Study of Engineering Materials Subjected to Complex Loadings. " PhD diss., University of Tennessee, 2014. https://trace.tennessee.edu/utk_graddiss/2805 This Dissertation is brought to you for free and open access by the Graduate School at TRACE: Tennessee Research and Creative Exchange. It has been accepted for inclusion in Doctoral Dissertations by an authorized administrator of TRACE: Tennessee Research and Creative Exchange. For more information, please contact [email protected]. To the Graduate Council: I am submitting herewith a dissertation written by Jeffrey R. Bunn entitled "Neutron Diffraction Study of Engineering Materials Subjected to Complex Loadings." I have examined the final electronic copy of this dissertation for form and content and recommend that it be accepted in partial fulfillment of the equirr ements for the degree of Doctor of Philosophy, with a major in Civil Engineering. Dayakar Penumadu, Major Professor We have read this dissertation and recommend its acceptance: Easo P. George, Richard M Bennett, H. Choo, Thomas R. Watkins Accepted for the Council: Carolyn R. Hodges Vice Provost and Dean of the Graduate School (Original signatures are on file with official studentecor r ds.) Neutron Diffraction Study of Engineering Materials Subjected to Complex Loadings A Dissertation Presented for the Doctor of Philosophy Degree The University of Tennessee, Knoxville Jeffrey R. -
Stainless Steel Fasteners – a Systematic Approach to Their Selection
STAINLESS STEEL FASTENERS – A SYSTEMATIC APPROACH TO THEIR SELECTION A DESIGNERS’ HANDBOOK SERIES NO 9003 Produced by Distributed by AMERICAN IRON NICKEL AND STEEL INSTITUTE INSTITUTE STAINLESS STEEL FASTENERS – A SYSTEMATIC APPROACH TO THEIR SELECTION A DESIGNERS’ HANDBOOK SERIES NO 9003 Originally, this handbook was published in 1976 by the Committee of Stainless Steel Producers, American Iron and Steel Institute. The Nickel Institute republished the handbook in 2020. Despite the age of this publication the information herein is considered to be generally valid. Material presented in the handbook has been prepared for the general information of the reader and should not be used or relied on for specific applications without first securing competent advice. The Nickel Institute, the American Iron and Steel Institute, their members, staff and consultants do not represent or warrant its suitability for any general or specific use and assume no liability or responsibility of any kind in connection with the information herein. Nickel Institute [email protected] www.nickelinstitute.org CONTENTS Introduction ................................................3 Fastener Materials ..........................................3 Stainless Steels Identification ................................5 Choosing the Right Type .....................................8 Stainless Steel Fastener Properties ...........................13 Tensile & Yield Strength Shear Strength High- and Low-Temperature Service ..........................16 Magnetic and -
Machinery Repairman
NAVEDTRA 12204-A Naval Education and September 1993 Training Manual Training Command 0502-LP-477-5600 (TRAMAN) Machinery Repairman DISTRIBUTION STATEMENT A: Approved for public release; distribution is unlimited. Nonfederal government personnel wanting a copy of this document must use the purchasing instructions on the inside cover. Although the words “he,” “him,” and “his” are used sparingly in this manual to enhance communication, they are not intended to be gender driven nor to affront or discriminate against anyone reading this text. DISTRIBUTION STATEMENT A: Approved for public release; distribution is unlimited. Nonfederal government personnel wanting a copy of this document must write to Superintendent of Documents, Government Printing Office, Washington, DC 20402 OR Commanding Officer, Naval Publications and Forms Directorate, Navy Aviation Supply Office, 5801 Tabor Avenue, Philadelphia, PA 19120-5099, Attention: Cash Sales, for price and availability. MACHINERY REPAIRMAN NAVEDTRA 12204-A 1993 Edition Prepared by MRCS Wayne T. Drew COMMANDING OFFICER NETPDTC 6490 SAUFLEY FIELD RD PENSACOLA, FL 32509-5237 ERRATA #1 18 April 2000 Specific Instructions and Errata for the TRAMAN MACHINERY REPAIRMAN, NAVEDTRA 12204-A 1. No attempt has been made to issue corrections for errors in typing, punctuation, etc. 2. Make the following changes to the Machinery Repairman text: Page Column Paragraph Chancre 2-2 1 3rd complete Change paragraph to read as follows: "If a paragraph dimension is given as 3.000 inches, the. is ±0.005 inch: or if the dimension. is ±0.010 inch." vice "If a dimension is given as 3.000 inches., the. is ±0.0005 inch: or if the dimension.. -
Self-Clinching Nuts Install Permanently in Aluminum, Steel Or Stainless Steel Sheets
PEM® brand self-clinching nuts install permanently in aluminum, steel or stainless steel sheets. CL™ SELF-CLINCHING NUTS SELF-CLINCHING NUTS Self-clinching nuts are installed by placing them in properly sized holes in sheets and applying a parallel squeezing force to the head of the nut. The sheet metal surrounding the head cold flows into an undercut thereby making the fastener an integral part of the sheet. A serrated clinching ring prevents the fastener from rotating after installation. S™/SS™/CLA™/CLS™/CLSS™ nuts H™ (non-locking) and HNL™ (locking) provide load-bearing threads in thin nuts have threads that provide high sheets with high pushout and torque-out pushout and torque-out resistance - resistance - PAGES 4 and 5 PAGE 8 SP™, PEM 300® nuts provide strong SH™ hard panel nuts install into thin, load-bearing threads in stainless steel harder, high strength steel materials - sheets as thin as .030”/0.8 mm - PAGE 8 PAGES 4 and 5 SMPS™/SMPP™ nuts are for thinner PEM RT® free-running locknuts are sheet/close-to-edge applications - free-running until clamp load is induced. A PAGE 9 modified thread angle on the loaded flank provides the vibration resistant locking Material and finish specifications - PAGE 9 feature- PAGE 6 SL™ self-locking nuts are designed with Installation - PAGES 10 and 11 a unique and economical TRI-DENT® locking feature, meeting 3 cycle locking Performance data - PAGES 12 - 15 performance requirements - PAGE 7 Many PEM self-clinching nuts in this bulletin are dimensionally equivalent to nuts manufactured to NASM45938/1 specifications. Consult our Marketing department for a complete Military Specifications and National Aerospace Standards guide (Bulletin NASM) on our website.