Use of Magnesium Alloys in Tension Band Wiring of Olecranon Fractures
Total Page:16
File Type:pdf, Size:1020Kb
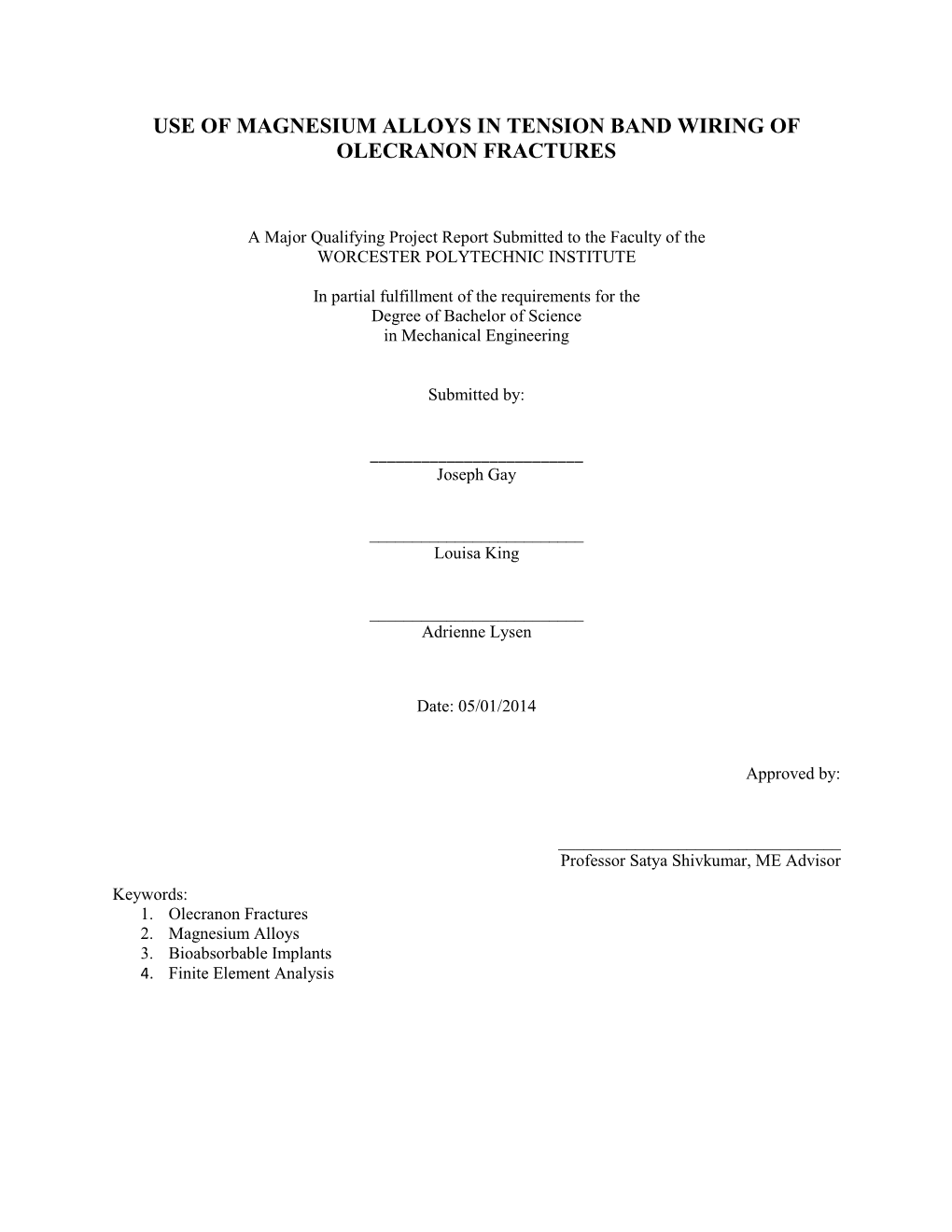
Load more
Recommended publications
-
Tension Band Wiring Is As Effective As a Compression Screw in a Neglected, Medial Maleolus Non-Union
Case Report Journal of Orthopaedic Case Reports 2017 Jul-Aug: 7(4):Page 72-75 Tension Band Wiring Is As Effective As A Compression Screw In A Neglected, Medial Maleolus Non-Union: A Case-Based Discussion & Literature Review Rakesh John¹, Mandeep Singh Dhillon¹, Ankit Khurana², Sameer Aggarwal¹, Prasoon Kumar¹ Learning Points for this Article: Compression screw fixation has been the workhorse implant for medial malleolar nonunions; however, tension band wiring may be a better technique for such nonunions, as seen in this rare case of isolated, medial malleolus gap nonunion. Abstract Introduction: Isolated, neglected medial malleolus nonunion cases are a rare entity in orthopedic literature. All studies (except one) have described the use of compression screws (with or without plates) for medial malleolar nonunion management. In acute fractures, tension band wiring (TBW) has shown excellent results both in biomechanical and in clinical studies. On the contrary, it has seldom been used in nonunion or in neglected cases. Case Report: We describe a 6-month-old neglected medial malleolus gap nonunion case who presented with progressive pain and limp. TBW with a monoblock, inlay, tricortical, and iliac crest bone graft for the defect was performed. The fracture united within 12 weeks and patient went back to his normal work routine; on the latest follow-up at 3 years, the patient was asymptomatic with no clinicoradiologic signs of secondary osteoarthritis of the ankle joint. Conclusion: TBW may be better than screw fixation in the management of medial malleolus nonunion as it is technically straightforward and cost-effective, can provide equal or more compression than a screw; it does not damage the sandwiched inlay bone graft, and the amount of compression is surgeon-controlled. -
Case Report Arthroscopic Removal of a Wire Fragment from the Posterior Septum of the Knee Following Tension Band Wiring of a Patellar Fracture
Hindawi Publishing Corporation Case Reports in Orthopedics Volume 2015, Article ID 827140, 5 pages http://dx.doi.org/10.1155/2015/827140 Case Report Arthroscopic Removal of a Wire Fragment from the Posterior Septum of the Knee following Tension Band Wiring of a Patellar Fracture Yasuaki Tamaki, Takashi Nakayama, Kenichiro Kita, Katsutosi Miyatake, Yoshiteru Kawasaki, Koji Fujii, and Yoshitsugu Takeda Department of Orthopedic Surgery, Tokushima Red Cross Hospital, 103 Irinokuchi, Komatsushima-cho, Komatsushima, Tokushima 773-8502, Japan Correspondence should be addressed to Yoshitsugu Takeda; [email protected] Received 25 November 2014; Accepted 22 January 2015 Academic Editor: Dimitrios S. Karataglis Copyright © 2015 Yasuaki Tamaki et al. This is an open access article distributed under the Creative Commons Attribution License, which permits unrestricted use, distribution, and reproduction in any medium, provided the original work is properly cited. Tension band wiring with cerclage wiring is most widely used for treating displaced patellar fractures. Although wire breakage is not uncommon, migration of a fragment of the broken wire is rare, especially migration into the knee joint. We describe here a rare case of migration of a wire fragment into the posterior septum of the knee joint after fixation of a displaced patellar fracture with tension band wiring and cerclage wiring. Although it was difficult to determine whether the wire fragment was located within or outside the knee joint from the preoperative plain radiographs or three-dimensional computed tomography (3D CT), we found it arthroscopically through the posterior transseptal portal with assistance of intraoperative fluoroscopy. Surgeons who treat such cases should bear in mind the possibility that wire could be embedded in the posterior septum of the knee joint. -
Variability in Olecranon Ao Fracture Fixation: a Radiological Study V.M
Original Article East African Orthopaedic Journal VARIABILITY IN OLECRANON AO FRACTURE FIXATION: A RADIOLOGICAL STUDY V.M. Mutiso*, MBChB, MMed(Surg), FCS(ECSA), Department of Orthopaedic Surgery, College of Health Sciences, University of Nairobi, P. O. Box 19676 – 00202, Nairobi, Kenya and J. Chigumbura, MBBS (University of Warwick), GPST1, UHNS *At the time of writing the author was a Clinical Fellow ( Arthroscopy & Arthroplasty) in the Directorate of Orthopaedics and Trauma at the University of North Staffordshire in United Kingdom Correspondence to: Dr. V.M. Mutiso, Department of Orthopaedic Surgery, College of Health Sciences, University of Nairobi, P. O. Box 19676 – 00202, Nairobi, Kenya. Email: [email protected] ABSTRACT Background: Tension Band Wire(TBW) fixation of olecranon fracture is a commonly used technique by orthopaedic surgeons. However surgeons do not strictly adhere to the AO standard. Objectives: To determine the use and variability of this technique by surgeons at the hospital. Design: A hospital based retrospective study using anonymous radiological records. Setting: North Staffordshire University Hospital in United Kingdom. Materials and Methods: Computer software was used to retrieve, review and measure pre and postoperative radiographs of olecranon fracture cases. All identifying information was electronically masked. Results: The mean age was 50.1 years with a median of 56 years. 16.9% were open fractures. Fifty percent of the TBW met the AO standard. INTRODUCTION The triceps muscle attaches to the ulna proximally and it articulates with the distal humerus. It is Olecranon fractures are a relatively common acute subcutaneous along most of its length and is thus injury worldwide and are commonly treated operatively. -
Comparison of Two Types of Fixation for Proximal Tibial Epiphysiodesis: an Experimental Study in a Rabbit Model
Jt Dis Relat Surg Joint Diseases and 2021;32(2):468-477 Related Surgery ORIGINAL ARTICLE Comparison of two types of fixation for proximal tibial epiphysiodesis: An experimental study in a rabbit model Alkan Bayrak, MD1, Altuğ Duramaz, MD1, Cemal Kızılkaya, MD2, Malik Çelik, MD3, Cemal Kural, MD1, Serdar Altınay, MD4, Alev Kural, MD5, Serdar Hakan Başaran, MD1 1Department of Orthopedics and Traumatology, University of Health Sciences, Bakırköy Dr. Sadi Konuk Training and Research Hospital, Istanbul, Turkey 2Department of Orthopedics and Traumatology, Bahçelievler State Hospital, Istanbul, Turkey 3Department of Orthopedics and Traumatology, Batman State Hospital, Batman, Turkey 4Department of Pathology, University of Health Sciences, Bakırköy Dr. Sadi Konuk Training and Research Hospital, Istanbul, Turkey 5Department of Biochemistry, University of Health Sciences, Bakırköy Dr. Sadi Konuk Education and Research Hospital, Istanbul, Turkey Growth plate or the physis is a cartilage structure ABSTRACT that occurs at the distal part of the long bones and provides bone elongation. Physeal injuries are Objectives: In this study, we describe a novel hemiepiphysiodesis technique to prevent implant-related perichondrial ring injury in a difficult to treat and cause complications such as rabbit model. growth arrest, progressive angular deformities, and Materials and methods: Proximal tibial epiphyseal plates of a limb length discrepancy after childhood physeal total of 16 white New Zealand rabbits were used for this animal damage.[1] After traumatic epiphyseal injuries, a physeal model. The subjects were divided into three equal groups as bar may occur that may lead to progressive angular follows: Group 1 (Kirschner wire [K-wire]/cerclage), Group 2 deformities or limb shortness during the fracture (8-plate) right-hind legs, Group 3 (Control) left hind legs. -
Os Acromiale, a Cause of Shoulder Pain, Not to Be Overlooked
Orthopaedics & Traumatology: Surgery & Research (2013) 99, 465—472 View metadata, citation and similar papers at core.ac.uk brought to you by CORE provided by Elsevier - Publisher Connector Available online at www.sciencedirect.com ORIGINAL ARTICLE Os acromiale, a cause of shoulder pain, not to be overlooked ∗ O. Barbier , D. Block, C. Dezaly, F. Sirveaux, D. Mole Emile Gallé Surgical Center, 49, rue Hermitte, 54000 Nancy, France Accepted: 5 October 2012 KEYWORDS Summary Acromion; Introduction: Os acromiale is a failure of fusion of the acromial process. It is usually asymp- tomatic and discovered by chance. When it is painful a differential diagnosis must be made in Iliac graft; relation to the subacromial impingement syndrome. Internal fixation Hypothesis: Unstable os acromiale is the cause of atypical scapulalgias. Stabilization by tension band wiring and an embedded slot shaped graft achieves union and relieves pain. Patients et methods: This series includes 10 patients mean age 43 years old presenting with shoulder pain resistant to a mean 15 months of conservative treatment. Pain followed trauma in three cases. Three patients had a history of acromioplasty, which had not relieved pain. All had pain during palpation of the superior aspect of the acromion. The diagnosis was confirmed in eight patients by positive results to local injection of the os acromiale. The mean preop- erative Constant score was 53.4. The procedure included open reduction and fixation of the acromion by tension band wiring and pinning associated with an embedded iliac crest graft without acromioplasty. Results: The mean follow-up was 48 months. Pain was relieved in seven cases and all patients had improved and were satisfied. -
Bimalleolar Fracture of Ankle Joint Managed by Tension Band Wiring Technique: a Prospective Study Dr
Scholars Journal of Applied Medical Sciences (SJAMS) ISSN 2320-6691 (Online) Sch. J. App. Med. Sci., 2014; 2(1D):428-432 ISSN 2347-954X (Print) ©Scholars Academic and Scientific Publisher (An International Publisher for Academic and Scientific Resources) www.saspublisher.com Research Article Bimalleolar Fracture of Ankle Joint Managed By Tension Band Wiring Technique: A Prospective Study Dr. Maruthi CV*1, Dr.Venugopal N2, Dr. Nanjundappa HC2, Dr. Siddalinga swamy MK2 1Assistant Professor, Department of Orthopaedics, MVJ MC and RH, Hoskote, Bangalore, India 2Professor, Dept of Orthopaedics, MVJ MC and RH, Hoskote, Bangalore, India 3MVJ Medical College & Research Hospital, Hoskote, Bangalore -562 114, India *Corresponding author Dr. Maruthi CV Email: Abstract: Ankle fractures are the most commonly encountered by most of the orthopaedic surgeons. According to the lauge Hansen’s classification five different types can be seen. The surgical treatment of adduction, abduction and supination external rotation type of injuries leading to bimalleolar fractures can be fixed with either tension band technique or cancellous screws. Here we are done a study to evaluate the benefits of tension band wiring technique in the management of bimalleolar fractures of the ankle. In our study, 40 cases of bimalleolar fracture of ankle joint of above mentioned types were admitted in Department of Orthopaedics, between February 2009 and November 2013 was included. We included patients above 20 and below 58 years. We excluded patients with pronation external rotation, vertical compression and trimalleolar fractures, pathological fractures, compound fractures and who are medically unfit and at extremely high anaesthesia risk. All the patients, operated by open reduction and internal fixation using tension band wiring technique. -
Scientific Programme
10TH EFORT CONGRESS VIENNA, AUSTRIA 3 – 6 JUNE 2009 OFFICIAL PROGRAMME Level –1: Rooms D, G, H, K, P Level 0: Rooms E1, E2, F1, F2 Level 1: Rooms L, N, J EFORT – JOINT EFFORTS CONTENTS WELCOME ADDRESS INDUSTRY & EXHIBITION Message from the President of EFORT 3 Industry partners of the 10th EFORT Congress 155 Message from the Chairman of the Local Organising Exhibition Floor Plans 156 – 157 Committee 4 Exhibitors List 159 – 160 Welcome Address from the Chairman of the Scientifi c Committee 5 Company descriptions and contact details 161 – 202 OVERVIEW & HIGHLIGHTS SOCIETIES Colour guide per topic 7 National Member Societies 205 – 206 Collaborating Speciality Societies and SESSION OVERVIEW & ABSTRACT INFORMATION Affi liated Organisations with own Sessions 207 Symposia 9 – 10 Instructional course lecture 10 – 11 GENERAL CONGRESS INFORMATION Controversial case discussion 12 Social programme 209 ExMEx 12 – 13 About the host city 210 Guest societies and other sessions 13 – 14 General congress information 211 – 213 Satellite symposia 15 – 16 City map 214 Free paper sessions 16 – 20 Public transportation map 215 Number of abstracts by category 21 Floor plans 216 – 217 Number of abstracts by country 22 Abstract reviewers 23 – 24 ABOUT EFORT EFORT Committees 219 – 220 WEDNESDAY 3 JUNE 09 About EFORT 221 – 222 Programme of the day 27 – 61 EFORT Advanced Training Programme 223 EFORT Fora 224 THURSDAY 4 JUNE 09 Programme of the day 63 – 95 E-POSTERS & INDEX List of e-posters 225 – 331 FRIDAY 5 JUNE 09 Index of authors 332 – 361 Programme of the day 97 – 131 SATURDAY 6 JUNE 09 Programme of the day 133 – 152 Published by textbildtechnik.ch 1 MESSAGE FROM THE PRESIDENT OF EFORT Karl-Göran Thorngren EFORT President Dear Colleagues, This year we will all meet for the EFORT Congress in Vienna. -
Screw Fixation Versus Tension Band Wiring in Treatment of Closed
International Journal of Surgery Science 2020; 4(4): 137-141 E-ISSN: 2616-3470 P-ISSN: 2616-3462 © Surgery Science Screw fixation versus tension band wiring in Treatment www.surgeryscience.com 2020; 4(4): 137-141 of closed displaced horizontal oblique medial malleolar Received: 07-08-2020 Accepted: 09-09-2020 fracture Dr. Abbas Silman Altaei Kerbala Health Directorate, Iraq Dr. Abbas Silman Altaei, Dr. Abdulameer Raheem Hussein and Dr. Aamer Naji Shaalan Dr. Abdulameer Raheem Hussein Kerbala Health Directorate, Iraq DOI: https://doi.org/10.33545/surgery.2020.v4.i4c.549 Dr. Aamer Naji Shaalan Kerbala Health Directorate, Iraq Abstract Background: Fractures of the medial malleolus are part of the ankle injures which require an orthopedic care. Most of these injuries are low energy, rotational injuries. Many modalities of treatment are present, including non-operative or operative treatment to restore normal anatomical alignment and to resume normal fictional ability of the ankle. Aim of study: To determine the outcome of surgical treatment of the medial malleolar fractures by tension band wiring versus screws fixation techniques. Patients and Methods: Randomized controlled trial conducted to study two groups of patients at Department of Orthopedic surgery in Al- Hussain medical city teaching hospital from July 2017 to July 2020, to evaluate the outcome of 36 patients with closed displaced horizontal oblique medial malleolar fractures. All the patients admitted to the emergency department of the hospital and operated within 24 hours. The study is based on 36 patients including males and females having closed displaced medial malleolar fractures of skeletally mature patients, divided in to two groups; group (A) managed by tension band wiring and group (B) with screws fixation, and followed for a maximum period of 20 weeks looking for union rate, infection, loss of reduction and the reoperation rate. -
Review Laminectomy for Cervical Myelopathy
Spinal Cord (2003) 41, 317–327 & 2003 International Spinal Cord Society All rights reserved 1362-4393/03 $25.00 www.nature.com/sc Review Laminectomy for cervical myelopathy NE Epstein*,1,2,3,4 1The Albert Einstein College of Medicine, Bronx, NY, USA; 2The North Shore-Long Island Jewish Health System, Manhasset, NY, USA; 3New Hyde Park, NY, USA; 4Winthrop University Hospital, Mineola, NY, USA Study design: Cervical laminectomy with or without fusion, or laminoplasty, successfully address congenital or acquired stenosis, multilevel spondylosis, ossification of the posterior longitudinal ligament (OPLL), and ossification of the yellow ligament (OYL). To optimize surgical results, however, these procedures should be applied to carefully selected patients. Objectives: To determine the clinical, neurodiagnostic, appropriate posterior cervical approaches to be employed in patients presenting with MR- and CT-documented multilevel cervical disease. To limit perioperative morbidity, dorsal decompressions with or without fusions should be performed utilizing awake intubation and positioning and continuous intraoperative somatosensory- evoked potential monitoring. Setting: United States of America. Methods: The clinical, neurodiagnostic, and varied dorsal decompressive techniques employed to address pathology are reviewed. Techniques, including laminectomy, laminoforaminotomy, and laminoplasty are described. Where preoperative dynamic X-rays document instability, simultaneous fusions employing wiring or lateral mass plate/screw or rod/screw techniques may be employed. Nevertheless, careful patient selection remains one of the most critical factors to operative success as older individuals with prohibitive comorbidities or fixed long-term neurological deficits should not undergo these procedures. Results: Short- and long-term outcomes following dorsal decompressions with or without fusions vary. Those with myelopathy over 65 years of age often do well in the short-term, but demonstrate greater long-term deterioration. -
Korean Knee Society Terminology Book For
Korean Knee Society’s Terminology Book This edition first published 2015 © 2015 by Korean Knee Society. Published edition © 2015 Wiley Publishing Japan K.K. All rights reserved. No part of this publication may be reproduced, stored in a retrieval system, or transmitted, in any form or by any means, electronic, mechanical, photocopying, recording or otherwise, without the prior permission of the copyright owner. ISBN: 978-4-939028-29-8 Published by Wiley Publishing Japan K.K. Tokyo Office: Frontier Koishikawa Bldg. 4F, 1-28-1 Koishikawa, Bunkyo-ku, Tokyo 112-0002, Japan Telephone: 81-3-3830-1221 Fax: 81-3-5689-7276 Internet site: http://www.wiley.com/wiley-blackwell e-mail: [email protected] Printed and bound in Korea by JEIL PRINTECH 발 간 사 대부분의 의학 용어는 영어에서 유래되어 그 해석과 의미가 오 랜 시간 동안 계승 발전되어 왔습니다. 그러나 오랜 역사를 거 치면서 용어의 해석이 다양해져 교육 현장은 물론 임상에서도 여러 용어로 혼용되고 있어 ‘용어 통일’의 필요성이 지속적으로 대두되어 왔습니다. 이에 대한슬관절학회에서는 슬관절 분야 에서 많이 쓰이고 있는 용어들을 수집하여 용어를 재정비 하고 통일하는 사업을 추진하였습니다. 대한슬관절학회 교과서편찬위원회에서는 2013년 12월에 업무를 개시하여 1년 5 개월 동안 슬관절 분야의 대표적 영어 교과서의 색인, 대한정형외과학회 교과서 색 인 및 용어집, 대한슬관절학회 교과서 편찬시 논의 된 용어통일 리스트에서 용어를 수집하여 약 5,000 여개의 주요 용어를 정리하였습니다. 이번 용어 편찬 작업에서 주목할 만한 부분은 관련 전문가들은 물론 일반인들도 용 어 해석을 쉽게 찾아볼 수 있도록 어플리케이션을 제작하여 앱 스토어나 플레이 스 토어에서 무료로 다운로드 하여 볼 수 있도록 접근성을 높였다는 것입니다. 이번 용 어집 편찬 작업이 선생님들의 진료와 연구에 도움이 되고, 일반인들도 보다 쉽고 정 확하게 의료진들과 소통할 수 있길 바라며 앞으로 꾸준히 발전해 나갈 수 있도록 많 은 관심 바랍니다. -
Case Report Surgical Fixation of Bilateral Simultaneous Avulsion
Hindawi Case Reports in Orthopedics Volume 2017, Article ID 5925421, 6 pages https://doi.org/10.1155/2017/5925421 Case Report Surgical Fixation of Bilateral Simultaneous Avulsion Fractures of the Proximal Tibia in a 12-Year-Old with History of Conservatively Managed Unilateral Tibial Avulsion Fracture Christopher Newman, Dharsh Musiienko, and Samuel Law Western Health Department of Orthopaedics, Footscray Hospital, Gordon Street, Footscray, VIC 3011, Australia Correspondence should be addressed to Christopher Newman; [email protected] Received 12 February 2017; Accepted 22 March 2017; Published 3 April 2017 Academic Editor: Johannes Mayr Copyright © 2017 Christopher Newman et al. This is an open access article distributed under the Creative Commons Attribution License, which permits unrestricted use, distribution, and reproduction in any medium, provided the original work is properly cited. Fractures of the proximal tibial epiphysis are rare, representing less than 3% of all epiphyseal and 1% of all physeal injuries in adolescents. Bilateral injuries are extremely rare. The specific anatomical and histological features of the proximal tibial epiphysis make it vulnerable to a specific fracture pattern that occurs when the tensile force of the quadriceps is greater than the fibrocartilaginous tissue underlying the tibial tuberosity. We report the first case to our knowledge of a 12-year-old boy who sustained simultaneous bilateral tibial avulsion fractures on the background of a previous conservatively managed unilateral tibial tuberosity avulsion fracture. We report this case for its uniqueness and as an educational review of the anatomy, the mechanism of injury, and the development of classifying these fractures and discussion of the stages of the growing physis that determine the treatment approach. -
Trauma to the Upper Extremities
7 Trauma to the Upper Extremities Contents 7.1 Sternoclavicular Joint 192 7.1.1 Sternoclavicular Joint Dislocation 192 7.1.2 Clinical Signs to Suggest Dangerous Posterior Dislocation 192 7.1.3 Reduction Manoeuvre 192 7.1.4 Main Pitfall 193 7.1.5 Complications (Posterior Injuries) 193 7.2 Acromioclavicular Joint Dislocation 193 7.2.1 Rockwood Classification 193 7.2.2 Management 193 7.3 Shoulder Dislocation and Instability 195 7.3.1 General Concepts 195 7.3.2 Facts and Myths of Shoulder Dislocation 195 7.3.3 Investigations 196 7.3.4 Anterior Dislocation: Treatment Principles 196 7.3.5 Key Points: Anterior Dislocations 198 7.3.6 Pearl 198 7.3.7 Posterior Dislocations 198 7.3.8 Pearl 199 7.3.9 Is It Multi-Directional or Voluntary Instability? 199 7.3.10 Dx of Multi-Directional Instability 199 7.3.11 Appendix on Multi-Directional Instability 200 7.3.12 A Word About Arthroscopy 200 7.4 Fractured Clavicle 200 7.4.1 Pathomechanics 201 7.4.2 Fractured Clavicle Classification 201 7.4.3 Classification of Lateral Third Fractures 201 7.4.4 Conservative Treatment: Majority of Patients 201 7.4.5 Operative Indications 202 7.4.6 Reason for the Trend Towards Fixing Displaced Clavicular Fractures 202 7.4.7 Choice of Fixation 203 7.4.8 Choice of Fixation of Lateral Third Fractures 203 7.4.9 Weaver-Dunn Procedure 204 7.4.10 Complications 204 7.4.11 Treatment of Non-Unions 204 7.5 Fractured Scapula and Glenoid 204 186 7 Trauma to the Upper Extremities 7.5.1 Ideberg Classification of Glenoid Fractures 205 7.5.2 Rn of Scapula Body Fractures 205 7.5.3 Rn of Extra-Articular