Introduction Roles
Total Page:16
File Type:pdf, Size:1020Kb
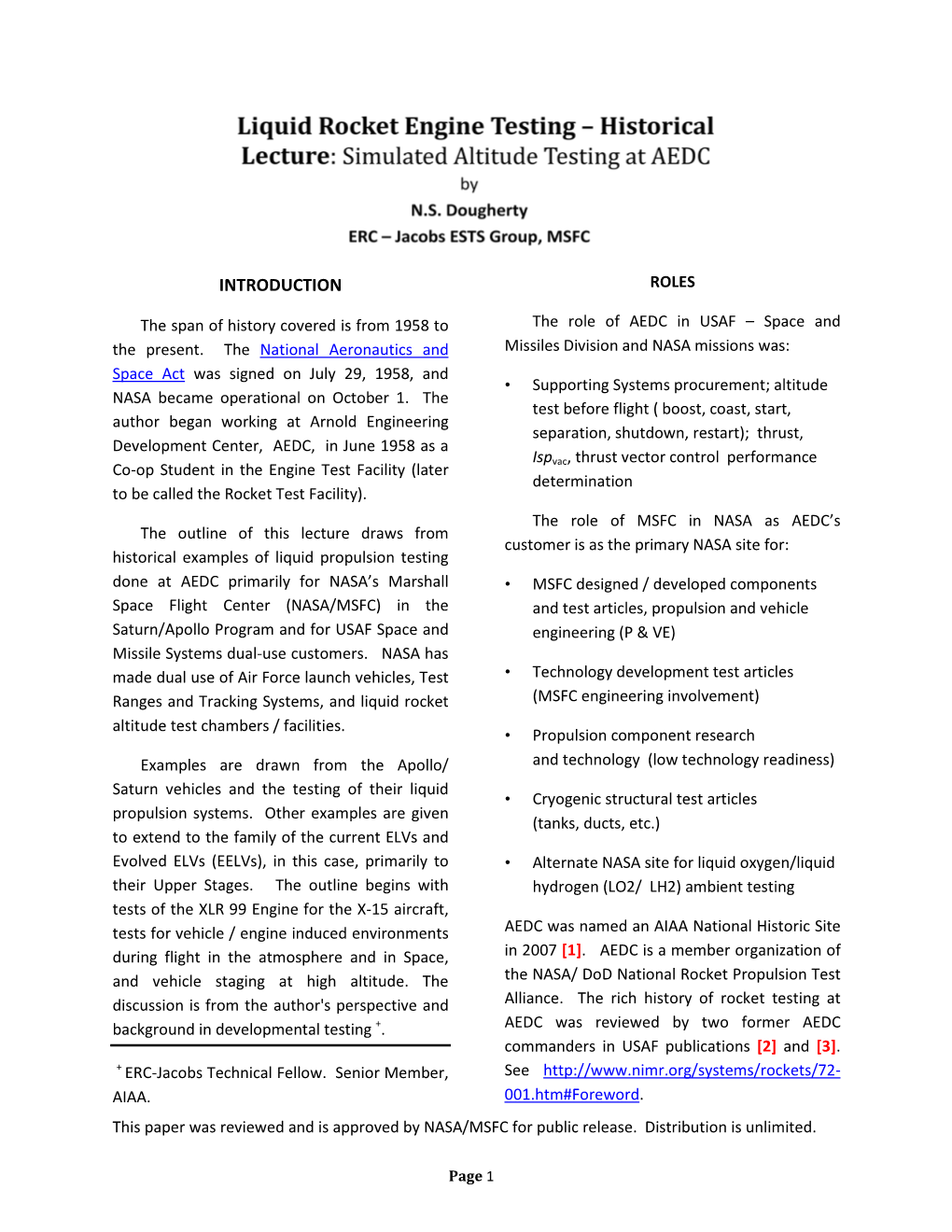
Load more
Recommended publications
-
Space Administration
https://ntrs.nasa.gov/search.jsp?R=19700024651 2020-03-23T18:20:34+00:00Z TO THE CONGRESSOF THE UNITEDSTATES : Transmitted herewith is the Twenty-first Semiannual Repol* of the National Aeronautics and Space Administration. Twen~-first SEMIANNUAL REPORT TO CONGRESS JANUARY 1 - JUNE 30, 1969 NATIONAL AERONAUTICS AND SPACE ADMINISTRATION WASHINGTON, D. C. 20546 Editors: G. B. DeGennaro, H. H. Milton, W. E. Boardman, Office of Public Affairs; Art work: A. Jordan, T. L. Lindsey, Office of Organiza- tion and Management. For sale by the Superintendent of Documents, U.S. Government Printing Office Washington, D.C. 20402-Price $1.25 THE PRESIDENT May 27,1970 The White House I submit this Twenty-First Semiannual Report of the National Aeronautics and Space Aldministration to you for transmitttal to Congress in accordance with section 206(a) of the National Aero- nautics and Space Act of 1958. It reports on aotivities which took place betiween January 1 and June 30, 1969. During this time, the Nation's space program moved forward on schedule. ApolIo 9 and 10 demonstrated the ability of ;the man- ned Lunar Module to operate in earth and lunar orbit and its 'eadi- ness to attempt the lunar landing. Unmanned observatory and ex- plorer class satellites carried on scientific studies of the regions surrounding the Earth, the Moon, and the Sun; a Biosatellite oarwing complex biological science experiment was orbited; and sophisticated weather satellites and advanced commercial com- munications spacecraft became operational. Advanced research projects expanded knowledge of space flighk and spacecraft engi- neering as well as of aeronautics. -
Back to the the Future? 07> Probing the Kuiper Belt
SpaceFlight A British Interplanetary Society publication Volume 62 No.7 July 2020 £5.25 SPACE PLANES: back to the the future? 07> Probing the Kuiper Belt 634089 The man behind the ISS 770038 Remembering Dr Fred Singer 9 CONTENTS Features 16 Multiple stations pledge We look at a critical assessment of the way science is conducted at the International Space Station and finds it wanting. 18 The man behind the ISS 16 The Editor reflects on the life of recently Letter from the Editor deceased Jim Beggs, the NASA Administrator for whom the building of the ISS was his We are particularly pleased this supreme achievement. month to have two features which cover the spectrum of 22 Why don’t we just wing it? astronautical activities. Nick Spall Nick Spall FBIS examines the balance between gives us his critical assessment of winged lifting vehicles and semi-ballistic both winged and blunt-body re-entry vehicles for human space capsules, arguing that the former have been flight and Alan Stern reports on his grossly overlooked. research at the very edge of the 26 Parallels with Apollo 18 connected solar system – the Kuiper Belt. David Baker looks beyond the initial return to the We think of the internet and Moon by astronauts and examines the plan for a how it helps us communicate and sustained presence on the lunar surface. stay in touch, especially in these times of difficulty. But the fact that 28 Probing further in the Kuiper Belt in less than a lifetime we have Alan Stern provides another update on the gone from a tiny bleeping ball in pioneering work of New Horizons. -
Progress Report on Apollo Program
PROGRESS REPORT ON APOLLO PROGRAM Michael Collins, LCol. USAF (M) Astronaut NASA-MANNED SPACECRAFT CENTER It is a great pleasure to be here today and to greet you hardy suMvors of the pool party. I will do my best to avoid loud noises and bright colors during my status report. Since the last SETP Symposium, the Apollo Program has been quite busy in a number of different areas. (Figure 1) My problem is to sift through this information and to talk only about those things of most interest to you. First, to review briefly our hardware, we are talking about two different spacecraft and two different boosters. (Figure 2) The Command Module is that part of the stack COLLINS which makes the complete round trip to the moon. Attached to it is the Service Module, containing expendables and a 20,000 pound thrust engine for maneuverability. The Lunar Module will be carried on later flights and is the landing vehicle and active rendezvous partner. The uprated Saturn I can put the Command and Service Modules into earth orbit; the Saturn V is required when the Lunar Module is added. Since the last symposium, we have flown the Command and Service Modules twice and the Lunar Module once, all unmanned. Apollo 4, the first Saturn V flight, was launched in November 1967. (Figure 3) The Saturn V did a beautiful, i.e. nominal, job of putting the spacecraft into earth parking orbit. After a coast period, the third stage (S-IVB by McDonnell Douglas) was ignited a second time, achieving a highly elliptical orbit. -
Delta II Icesat-2 Mission Booklet
A United Launch Alliance (ULA) Delta II 7420-10 photon-counting laser altimeter that advances MISSION rocket will deliver the Ice, Cloud and land Eleva- technology from the first ICESat mission tion Satellite-2 (ICESat-2) spacecraft to a 250 nmi launched on a Delta II in 2003 and operated until (463 km), near-circular polar orbit. Liftoff will 2009. Our planet’s frozen and icy areas, called occur from Space Launch Complex-2 at Vanden- the cryosphere, are a key focus of NASA’s Earth berg Air Force Base, California. science research. ICESat-2 will help scientists MISSION investigate why, and how much, our cryosphere ICESat-2, with its single instrument, the is changing in a warming climate, while also Advanced Topographic Laser Altimeter System measuring heights across Earth’s temperate OVERVIEW (ATLAS), will provide scientists with height and tropical regions and take stock of the vege- measurements to create a global portrait of tation in forests worldwide. The ICESat-2 mission Earth’s third dimension, gathering data that can is implemented by NASA’s Goddard Space Flight precisely track changes of terrain including Center (GSFC). Northrop Grumman built the glaciers, sea ice, forests and more. ATLAS is a spacecraft. NASA’s Launch Services Program at Kennedy Space Center is responsible for launch management. In addition to ICESat-2, this mission includes four CubeSats which will launch from dispens- ers mounted to the Delta II second stage. The CubeSats were designed and built by UCLA, University of Central Florida, and Cal Poly. The miniaturized satellites will conduct research DELTA II For nearly 30 years, the reliable in space weather, changing electric potential Delta II rocket has been an industry and resulting discharge events on spacecraft workhorse, launching critical and damping behavior of tungsten powder in a capabilities for NASA, the Air Force Image Credit NASA’s Goddard Space Flight Center zero-gravity environment. -
Information Summaries
TIROS 8 12/21/63 Delta-22 TIROS-H (A-53) 17B S National Aeronautics and TIROS 9 1/22/65 Delta-28 TIROS-I (A-54) 17A S Space Administration TIROS Operational 2TIROS 10 7/1/65 Delta-32 OT-1 17B S John F. Kennedy Space Center 2ESSA 1 2/3/66 Delta-36 OT-3 (TOS) 17A S Information Summaries 2 2 ESSA 2 2/28/66 Delta-37 OT-2 (TOS) 17B S 2ESSA 3 10/2/66 2Delta-41 TOS-A 1SLC-2E S PMS 031 (KSC) OSO (Orbiting Solar Observatories) Lunar and Planetary 2ESSA 4 1/26/67 2Delta-45 TOS-B 1SLC-2E S June 1999 OSO 1 3/7/62 Delta-8 OSO-A (S-16) 17A S 2ESSA 5 4/20/67 2Delta-48 TOS-C 1SLC-2E S OSO 2 2/3/65 Delta-29 OSO-B2 (S-17) 17B S Mission Launch Launch Payload Launch 2ESSA 6 11/10/67 2Delta-54 TOS-D 1SLC-2E S OSO 8/25/65 Delta-33 OSO-C 17B U Name Date Vehicle Code Pad Results 2ESSA 7 8/16/68 2Delta-58 TOS-E 1SLC-2E S OSO 3 3/8/67 Delta-46 OSO-E1 17A S 2ESSA 8 12/15/68 2Delta-62 TOS-F 1SLC-2E S OSO 4 10/18/67 Delta-53 OSO-D 17B S PIONEER (Lunar) 2ESSA 9 2/26/69 2Delta-67 TOS-G 17B S OSO 5 1/22/69 Delta-64 OSO-F 17B S Pioneer 1 10/11/58 Thor-Able-1 –– 17A U Major NASA 2 1 OSO 6/PAC 8/9/69 Delta-72 OSO-G/PAC 17A S Pioneer 2 11/8/58 Thor-Able-2 –– 17A U IMPROVED TIROS OPERATIONAL 2 1 OSO 7/TETR 3 9/29/71 Delta-85 OSO-H/TETR-D 17A S Pioneer 3 12/6/58 Juno II AM-11 –– 5 U 3ITOS 1/OSCAR 5 1/23/70 2Delta-76 1TIROS-M/OSCAR 1SLC-2W S 2 OSO 8 6/21/75 Delta-112 OSO-1 17B S Pioneer 4 3/3/59 Juno II AM-14 –– 5 S 3NOAA 1 12/11/70 2Delta-81 ITOS-A 1SLC-2W S Launches Pioneer 11/26/59 Atlas-Able-1 –– 14 U 3ITOS 10/21/71 2Delta-86 ITOS-B 1SLC-2E U OGO (Orbiting Geophysical -
Development of Turbopump for LE-9 Engine
Development of Turbopump for LE-9 Engine MIZUNO Tsutomu : P. E. Jp, Manager, Research & Engineering Development, Aero Engine, Space & Defense Business Area OGUCHI Hideo : Manager, Space Development Department, Aero Engine, Space & Defense Business Area NIIYAMA Kazuki : Ph. D., Manager, Space Development Department, Aero Engine, Space & Defense Business Area SHIMIYA Noriyuki : Space Development Department, Aero Engine, Space & Defense Business Area LE-9 is a new cryogenic booster engine with high performance, high reliability, and low cost, which is designed for H3 Rocket. It will be the first booster engine in the world with an expander bleed cycle. In the designing process, the performance requirements of the turbopump and other components can be concurrently evaluated by the mathematical model of the total engine system including evaluation with the simulated performance characteristic model of turbopump. This paper reports the design requirements of the LE-9 turbopump and their latest development status. Liquid oxygen 1. Introduction turbopump Liquid hydrogen The H3 rocket, intended to reduce cost and improve turbopump reliability with respect to the H-II A/B rockets currently in operation, is under development toward the launch of the first H3 test rocket in FY 2020. In rocket development, engine is an important factor determining reliability, cost, and performance, and as a new engine for the H3 rocket first stage, an LE-9 engine(1) is under development. A rocket engine uses a turbopump to raise the pressure of low-pressure propellant supplied from a tank, injects the pressurized propellant through an injector into a combustion chamber to combust it under high-temperature and high- pressure conditions. -
Rocket Propulsion Fundamentals 2
https://ntrs.nasa.gov/search.jsp?R=20140002716 2019-08-29T14:36:45+00:00Z Liquid Propulsion Systems – Evolution & Advancements Launch Vehicle Propulsion & Systems LPTC Liquid Propulsion Technical Committee Rick Ballard Liquid Engine Systems Lead SLS Liquid Engines Office NASA / MSFC All rights reserved. No part of this publication may be reproduced, distributed, or transmitted, unless for course participation and to a paid course student, in any form or by any means, or stored in a database or retrieval system, without the prior written permission of AIAA and/or course instructor. Contact the American Institute of Aeronautics and Astronautics, Professional Development Program, Suite 500, 1801 Alexander Bell Drive, Reston, VA 20191-4344 Modules 1. Rocket Propulsion Fundamentals 2. LRE Applications 3. Liquid Propellants 4. Engine Power Cycles 5. Engine Components Module 1: Rocket Propulsion TOPICS Fundamentals • Thrust • Specific Impulse • Mixture Ratio • Isp vs. MR • Density vs. Isp • Propellant Mass vs. Volume Warning: Contents deal with math, • Area Ratio physics and thermodynamics. Be afraid…be very afraid… Terms A Area a Acceleration F Force (thrust) g Gravity constant (32.2 ft/sec2) I Impulse m Mass P Pressure Subscripts t Time a Ambient T Temperature c Chamber e Exit V Velocity o Initial state r Reaction ∆ Delta / Difference s Stagnation sp Specific ε Area Ratio t Throat or Total γ Ratio of specific heats Thrust (1/3) Rocket thrust can be explained using Newton’s 2nd and 3rd laws of motion. 2nd Law: a force applied to a body is equal to the mass of the body and its acceleration in the direction of the force. -
Privacy Statement Link at the Bottom of Aerojet Rocketdyne Websites
Privacy Notice Aerojet Rocketdyne – For external use Contents Introduction ...................................................................................................................... 3 Why we collect personal information? ............................................................................. 3 How we collect personal information? ............................................................................. 3 How we use information we collect? ............................................................................... 4 How we share your information? .................................................................................... 4 How we protect your personal information? ..................................................................... 4 How we collect consent? .............................................................................................. 4 How we provide you access? ........................................................................................ 4 How to contact Aerojet Rocketdyne privacy?.................................................................... 5 Collection of personal information .................................................................................. 5 Disclosure of personal information.................................................................................. 5 Sale of personal information .......................................................................................... 6 Children’s online privacy .............................................................................................. -
PCEC V2.3 (For Real This Time)
PCEC v2.3 (For Real This Time) 2021 NASA Cost & Schedule Symposium 14 Apr 2021 Brian Alford Mark Jacobs Booz Allen Hamilton TGS Consultants Shawn Hayes Richard Webb TGS Consultants KAR Enterprises NASA MSFC Victory MIPSSSolutions Team SB Diversity Outline • PCEC Overview • Robotic SC Updates • CASTS Updates • PCEC v2.3 Interface Updates • Closing Victory Solutions MIPSS Team 2 What is PCEC? • The Project Cost Estimating Capability (PCEC) is the primary NASA in-house developed parametric tool for estimating the cost of robotic missions, launch vehicles, crewed vehicles, etc. – Overarching tool for creating an estimate that spans the full NASA WBS – CERs included out-of-the-box for estimating the costs of a flight system (e.g., thermal) and support functions (e.g., project management) – Connects to other NASA-sponsored specialized tools to cover the complete NASA WBS (e.g., NICM, MOCET) – Excel-based (presented as add-in in the Ribbon) with completely visible calculations and code – Consists of the PCEC Interface (the Ribbon and supporting code) and the PCEC Library (the artifacts used to estimate cost) – Available to the General Public Victory Solutions MIPSS Team 3 What is PCEC? Cont’d • PCEC comprises two primary ‘models’, offered seamlessly to the user under a single, integrated tool – Robotic Spacecraft (Robotic SC) – Crewed and Space Transportation Systems (CASTS) • These models have separate data normalizations, collections of CERs, core WBSs, modeling approaches, estimating template worksheets, and scope – Estimating artifacts constitute -
Materials for Liquid Propulsion Systems
https://ntrs.nasa.gov/search.jsp?R=20160008869 2019-08-29T17:47:59+00:00Z CHAPTER 12 Materials for Liquid Propulsion Systems John A. Halchak Consultant, Los Angeles, California James L. Cannon NASA Marshall Space Flight Center, Huntsville, Alabama Corey Brown Aerojet-Rocketdyne, West Palm Beach, Florida 12.1 Introduction Earth to orbit launch vehicles are propelled by rocket engines and motors, both liquid and solid. This chapter will discuss liquid engines. The heart of a launch vehicle is its engine. The remainder of the vehicle (with the notable exceptions of the payload and guidance system) is an aero structure to support the propellant tanks which provide the fuel and oxidizer to feed the engine or engines. The basic principle behind a rocket engine is straightforward. The engine is a means to convert potential thermochemical energy of one or more propellants into exhaust jet kinetic energy. Fuel and oxidizer are burned in a combustion chamber where they create hot gases under high pressure. These hot gases are allowed to expand through a nozzle. The molecules of hot gas are first constricted by the throat of the nozzle (de-Laval nozzle) which forces them to accelerate; then as the nozzle flares outwards, they expand and further accelerate. It is the mass of the combustion gases times their velocity, reacting against the walls of the combustion chamber and nozzle, which produce thrust according to Newton’s third law: for every action there is an equal and opposite reaction. [1] Solid rocket motors are cheaper to manufacture and offer good values for their cost. -
École De Paris Tableaux Modernes Photographies Aviation Conquête Spatiale
EXPERTISES – VENTES AUX ENCHÈRES École de Paris Tableaux modernes Photographies Aviation Conquête spatiale Paris - Hôtel Drouot - 8 et 9 octobre 2019 EXPERTISES – VENTES AUX ENCHÈRES VENTE AUX ENCHÈRES PUBLIQUES Hôtel Drouot Richelieu salle 6 9, rue Drouot à Paris IXe Mardi 8 octobre 2019 à 14 h École de Paris Tableaux Modernes Mercredi 9 octobre 2019 à 14 h Photographies Aviation Conquête spatiale Reproduction des œuvres sur : www.ogerblanchet.fr - www.jj-mathias.fr Expositions publiques : Le lundi 7 octobre de 11 h à 18 heures Le mardi 8 octobre de 11 h à 12 heures Le mercredi 9 octobre de 11 h à 12 heures EXPERTISES – VENTES AUX ENCHÈRES 22 rue Drouot - 75009 Paris 01 42 46 96 95 - [email protected] ASSISTÉS DES EXPERTS Pour les lots 5 à 10 Pour l’École de Paris Éric SCHOELLER Christophe ZAGRODKI Tél. +33 (0)6 11 86 39 64 Tél. +33 (0)1 43 21 44 52 [email protected] [email protected] Pour les lots 38, 82 à 136, 252, 253, 281 à 287, Pour les autographes et manuscrits 289 à 314 M. Jean-Emmanuel RAUX Cabinet PERAZZONE-BRUN Arts et Autographes 4, rue Favart - 75002 9 rue de l’Odéon - 75006 Paris Tél. +33 (0)1 42 60 45 45 01 43 25 60 48 - [email protected] Pour les photographies M. Serge PLANTUREUX 80 Rue Taitbout - 75009 Paris Tél. +33 (0)6 50 85 60 74 - [email protected] AVERTISSEMENT Concernant l’état des œuvres décrites dans le présent catalogue, des rapports d’état sont disponibles sur simple demande Pour les estampes, sauf mention contraire, les dimensions sont celles de la cuvette pour les gravures et du sujet pour les lithographies J.J. -
Design for Demise Analysis for Launch Vehicles
A first design for demise analysis for launch vehicles Henrik Simon, Stijn Lemmens Space debris: Inactive, manmade objects in space Source: ESA Overview Introduction Fundamentals Modelling approach Results and discussion Summary and outlook What is the motivation and task? INTRODUCTION Motivation . Mitigation: Prevention of creation and limitation of long-term presence . Guidelines: LEO removal within 25 years . LEO removal within 25 years after mission end . Casualty risk limit for re-entry: 1 in 10,000 Rising altitude Decay & re-entry above 2000 km Source: NASA Source: NASA Solution: Design for demise Source: ESA Scope of the thesis . Typical design of upper stages . General Risk assessment . Design for demise solutions to reduce the risk ? ? ? Risk A Risk B Risk C Source: CNES How do we assess the risk and simulate the re-entry? FUNDAMENTALS Fundamentals: Ground risk assessment Ah = + 2 Ai � ℎ = =1 � Source: NASA Source: NASA 3.5 m 5.0 m 2 2 ≈ ≈ Fundamentals: Re-entry simulation tools SCARAB: Spacecraft-oriented approach . CAD-like modelling . 6 DoF flight dynamics . Break-up / fragmentation computed How does a rocket upper stage look like? MODELLING Modelling approach . Research on typical design: . Elongated . Platform . Solid Rocket Motor . Lack of information: . Create common intersection . Deliberately stay top-level and only compare effects Modelling approach Modelling approach 12 Length [m] 9 7 5 3 2 150 300 500 700 800 1500 2200 Mass [kg] How much is the risk and how can we reduce it? SIMULATIONS Example of SCARAB re-entry simulation 6x Casualty risk of all reference cases Typical survivors Smaller Smaller fragments fragments Pressure tanks Pressure tanks Main tank Engine Main structure + tanks Design for Demise .