Investigation of Potential Pathways and Multi-Cycle Bioregeneration of Ion-Exchange Resin Laden with Perchlorate
Total Page:16
File Type:pdf, Size:1020Kb
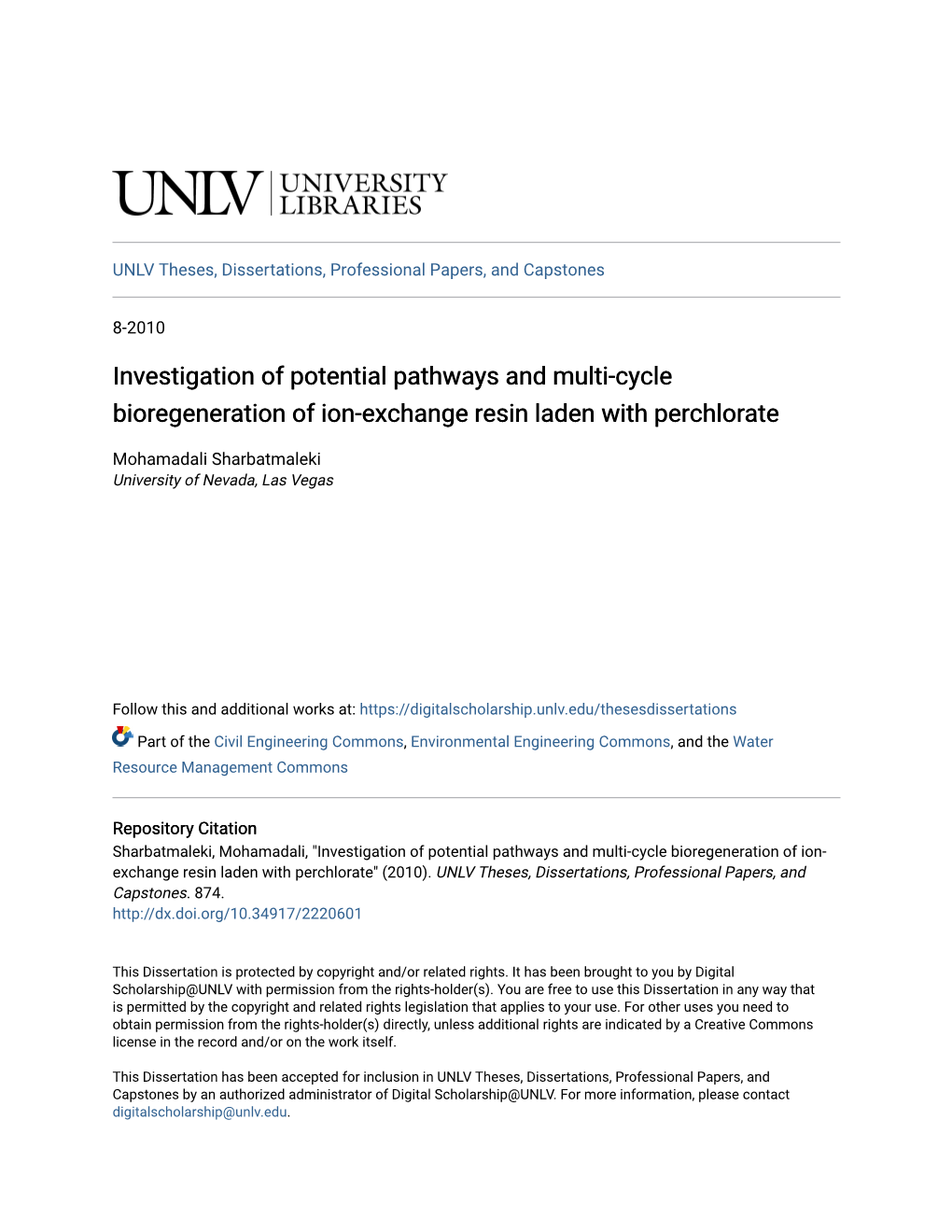
Load more
Recommended publications
-
Microbial (Per)Chlorate Reduction in Hot Subsurface Environments
Microbial (Per)chlorate Reduction in Hot Subsurface Environments Martin G. Liebensteiner Thesis committee Promotor Prof. Dr Alfons J.M. Stams Personal chair at the Laboratory of Microbiology Wageningen University Co-promotor Dr Bart P. Lomans Principal Scientist Shell Global Solutions International B.V., Rijswijk Other members Prof. Dr Willem J.H. van Berkel, Wageningen University Prof. Dr Mike S.M. Jetten, Radboud University Nijmegen Prof. Dr Ian Head, Newcastle University, UK Dr Timo J. Heimovaara, Delft University of Technology This research was conducted under the auspices of the Graduate School for Socio-Economic and Natural Sciences of the Environment (SENSE) Microbial (Per)chlorate Reduction in Hot Subsurface Environments Martin G. Liebensteiner Thesis submitted in fulfi lment of the requirements for the degree of doctor at Wageningen University by the authority of the Rector Magnifi cus Prof. Dr M.J. Kropff, in the presence of the Thesis Committee appointed by the Academic Board to be defended in public on Friday 17 October 2014 at 4 p.m. in the Aula. Martin G. Liebensteiner Microbial (Per)chlorate Reduction in Hot Subsurface Environments 172 pages. PhD thesis, Wageningen University, Wageningen, NL (2014) With references, with summaries in Dutch and English ISBN 978-94-6257-125-9 TABLE OF CONTENTS Chapter 1 General introduction and thesis outline 7 Chapter 2 Microbial redox processes in deep subsurface environments 23 and the potential application of (per)chlorate in oil reservoirs Chapter 3 (Per)chlorate reduction by the hyperthermophilic -
Enzymes and Electron Transport in Microbial Chlorate Respiration
Faculty of Technology and Science Chemistry Jan Bohlin Enzymes and electron transport in microbial chlorate respiration DISSERTATION Karlstad University Studies 2008:36 Jan Bohlin Enzymes and electron transport in microbial chlorate respiration Karlstad University Studies 2008:36 Jan Bohlin. Enzymes and electron transport in microbial chlorate respiration DISSERTATION Karlstad University Studies 2008:36 ISSN 1403-8099 ISBN 978-91-7063-196-2 © The Author Distribution: Faculty of Technology and Science Chemistry 651 88 Karlstad 054-700 10 00 www.kau.se Printed at: Universitetstryckeriet, Karlstad 2008 Abstract Microbial chlorate respiration plays an important role in the turnover of oxochlorates in nature and in industrial waste management. This thesis deals with the characterization of the molecular components of chlorate respiration in Ideonella dechloratans. Chlorate respiration utilizes two soluble periplasmic enzymes, chlorate reductase and chlorite dismutase, to convert chlorate to chloride and oxygen. The genes encoding the enzymes participating in the chlorate degradation have been sequenced, and are found in close proximity, forming a gene cluster for chlorate metabolism. This work also includes the successful recombinant expression of three genes from Ideonella dechloratans. Two of the gene products, chlorite dismutase and the C subunit of chlorate reductase, participate in the chlorate respiration. The third gene, which is found close to the gene cluster for chlorate metabolism, encodes a soluble c-type cytochrome. The localization of the gene suggests the corresponding protein as a candidate for a role as electron donor to chlorate reductase. Also, the role of soluble periplasmic c cytochromes of Ideonella dechloratans in chlorate respiration was studied. At least one of the soluble c cytochromes was found capable of serving as electron donor for chlorate reduction. -
Pseudomonas Stutzeri Biology Of
Biology of Pseudomonas stutzeri Jorge Lalucat, Antoni Bennasar, Rafael Bosch, Elena García-Valdés and Norberto J. Palleroni Microbiol. Mol. Biol. Rev. 2006, 70(2):510. DOI: 10.1128/MMBR.00047-05. Downloaded from Updated information and services can be found at: http://mmbr.asm.org/content/70/2/510 These include: http://mmbr.asm.org/ REFERENCES This article cites 395 articles, 145 of which can be accessed free at: http://mmbr.asm.org/content/70/2/510#ref-list-1 CONTENT ALERTS Receive: RSS Feeds, eTOCs, free email alerts (when new articles cite this article), more» on January 28, 2014 by Red de Bibliotecas del CSIC Information about commercial reprint orders: http://journals.asm.org/site/misc/reprints.xhtml To subscribe to to another ASM Journal go to: http://journals.asm.org/site/subscriptions/ MICROBIOLOGY AND MOLECULAR BIOLOGY REVIEWS, June 2006, p. 510–547 Vol. 70, No. 2 1092-2172/06/$08.00ϩ0 doi:10.1128/MMBR.00047-05 Copyright © 2006, American Society for Microbiology. All Rights Reserved. Biology of Pseudomonas stutzeri Jorge Lalucat,1,2* Antoni Bennasar,1 Rafael Bosch,1 Elena Garcı´a-Valde´s,1,2 and Norberto J. Palleroni3 Departament de Biologia, Microbiologia, Universitat de les Illes Balears, Campus UIB, 07122 Palma de Mallorca, Spain1; Institut Mediterrani d’Estudis Avanc¸ats (CSIC-UIB), Campus UIB, 07122 Palma de Mallorca, Spain2; and Department of Biochemistry and Microbiology, Rutgers University, Cook Campus, 3 New Brunswick, New Jersey 08901-8520 Downloaded from INTRODUCTION .......................................................................................................................................................511 -
Arsenic Transformations
Structural and mechanistic analysis of the arsenate respiratory reductase provides insight into environmental arsenic transformations Nathaniel R. Glassera, Paul H. Oyalab, Thomas H. Osbornec, Joanne M. Santinic, and Dianne K. Newmana,d,1 aDivision of Biology and Biological Engineering, California Institute of Technology, Pasadena, CA 91125; bDivision of Chemistry and Chemical Engineering, California Institute of Technology, Pasadena, CA 91125; cInstitute of Structural and Molecular Biology, Division of Biosciences, University College London, London WC1E 6BT, United Kingdom; and dDivision of Geological and Planetary Sciences, California Institute of Technology, Pasadena, CA 91125 Edited by Joan Selverstone Valentine, University of California, Los Angeles, CA, and approved July 13, 2018 (received for review May 9, 2018) Arsenate respiration by bacteria was discovered over two decades A microbe’s capacity for arsenate respiration corresponds ago and is catalyzed by diverse organisms using the well-conserved with the genes encoding the arsenate respiratory reductase (Arr) Arr enzyme complex. Until now, the mechanisms underpinning this complex, present in phylogenetically diverse organisms, includ- metabolism have been relatively opaque. Here, we report the struc- ing Gram-negative and Gram-positive bacteria (13). The ture of an Arr complex (solved by X-ray crystallography to 1.6-Å Arr complex is a member of the DMSO reductase family of resolution), which was enabled by an improved Arr expression molybdoenzymes and comprises two proteins, a large subunit method in the genetically tractable arsenate respirer Shewanella ArrA and a smaller subunit ArrB (13, 14). The ArrA subunit is sp. ANA-3. We also obtained structures bound with the substrate predicted to contain a Mo atom coordinated by a pyranopterin arsenate (1.8 Å), the product arsenite (1.8 Å), and the natural in- guanine dinucleotide cofactor (Mo-bisPGD), as well as a single hibitor phosphate (1.7 Å). -
Peak Antibody Name Immunogen
Positive in Supp. Peak Antibody name Immunogen/ Antigen type Source/Strain Phylum Group/Cluster this study References 1 A139 Sonicated cells Leptospirillum ferroxidans Nitrospirae Fe-S oxidizers cultures [1] 2 IVE3C_182 Intact cells Acidithiobacillus ferroxidans Gammaproteobacteria Fe-S oxidizers cultures + [1] 3 A183 Sonicated cells A. ferroxidans Gammaproteobacteria Fe-S oxidizers cultures + [1] 4 A184 Intact cells A. ferroxidans Gammaproteobacteria Fe-S oxidizers cultures + [1] 5 A186 Intact cells L. ferroxidans Nitrospirae Fe-S oxidizers cultures + [1] 6 IVE1BF Biofilm L. pherrifilum (LPH2) fermentor Nitrospirae Fe-S oxidizers cultures + [2] 7 IVE1S100 Soluble cellular fraction (SB-S100) L. pherrifilum (LPH2) fermentor Nitrospirae Fe-S oxidizers cultures + [2] 8 IVE1C2 Pellet insoluble cellular fraction L. pherrifilum (LPH2) fermentor Nitrospirae Fe-S oxidizers cultures + [2] 9 IVE2S1 Supernatant NtD (Leptospirillum ferrifilum) Nitrospirae Fe-S oxidizers cultures + [2] 10 IVE3C1 Celulas Intactas Acidithiobacillus caldus Gammaproteobacteria Fe-S oxidizers cultures + [2] 11 IVE3S100 Soluble cellular fraction (SB-100) A. ferroxidans Gammaproteobacteria Fe-S oxidizers cultures + [2] 12 IVE4C1 Intact cells Acidithiobacillus thioxidans Gammaproteobacteria Fe-S oxidizers cultures + [2] 13 IVE4C2 Pellet S100 A. thioxidans Gammaproteobacteria Fe-S oxidizers cultures + [2] 14 IVE4S100 Soluble cellular fraction (SB-100) A. thioxidans Gammaproteobacteria Fe-S oxidizers cultures + [2] 15 IVE5C1 Intact cells Acidithiobacillus albertensis Gammaproteobacteria Fe-S oxidizers cultures + [2] 16 IVE6C1 Intact cells A. caldus Gammaproteobacteria Fe-S oxidizers cultures + [2] 17 IVE6C2 Pellet S100 A. caldus Gammaproteobacteria Fe-S oxidizers cultures + [2] 18 IVE6S100 Soluble cellular fraction (SB-100) A. caldus Gammaproteobacteria Fe-S oxidizers cultures [2] 19 IVE7C1 Intact cells Halothiobacillus neapolitanus Gammaproteobacteria Fe-S oxidizers cultures + [3] 20 IVE8C1 Intact cells Acidimicrobium ferrooxidans Actinobacteria Fe-S oxidizers cultures + [3] 21 IVE9C1 Intact cells L. -
Genome-Resolved Metagenomics Identiies Genetic Mobility, Metabolic
The ISME Journal (2018) 12:1568–1581 https://doi.org/10.1038/s41396-018-0081-5 ARTICLE Genome-resolved metagenomics identifies genetic mobility, metabolic interactions, and unexpected diversity in perchlorate- reducing communities 1 1 1,2 1 1 Tyler P. Barnum ● Israel A. Figueroa ● Charlotte I. Carlström ● Lauren N. Lucas ● Anna L. Engelbrektson ● John D. Coates1 Received: 19 October 2017 / Revised: 9 January 2018 / Accepted: 18 January 2018 / Published online: 23 February 2018 © International Society for Microbial Ecology 2018 Abstract Dissimilatory perchlorate reduction is an anaerobic respiratory pathway that in communities might be influenced by metabolic interactions. Because the genes for perchlorate reduction are horizontally transferred, previous studies have been unable to identify uncultivated perchlorate-reducing populations. Here we recovered metagenome-assembled genomes from perchlorate-reducing sediment enrichments and employed a manual scaffolding approach to reconstruct gene clusters for perchlorate reduction found within mobile genetic elements. De novo assembly and binning of four enriched communities 1234567890();,: yielded 48 total draft genomes. In addition to canonical perchlorate reduction gene clusters and taxa, a new type of gene cluster with an alternative perchlorate reductase was identified. Phylogenetic analysis indicated past exchange between these gene clusters, and the presence of plasmids with either gene cluster shows that the potential for gene transfer via plasmid persisted throughout enrichment. However, a majority of genomes in each community lacked perchlorate reduction genes. Putative chlorate-reducing or sulfur-reducing populations were dominant in most communities, supporting the hypothesis that metabolic interactions might result from perchlorate reduction intermediates and byproducts. Other populations included a novel phylum-level lineage (Ca. -
Physiology and Biochemistry of Aromatic Hydrocarbon-Degrading Bacteria That Use Chlorate And/Or Nitrate As Electron Acceptor
Invitation for the public defense of my thesis Physiology and biochemistry of aromatic hydrocarbon-degrading of aromatic and biochemistry Physiology bacteria that use chlorate and/or nitrate as electron acceptor as electron nitrate and/or use chlorate that bacteria Physiology and biochemistry Physiology and biochemistry of aromatic hydrocarbon-degrading of aromatic hydrocarbon- degrading bacteria that bacteria that use chlorate and/or nitrate as electron acceptor use chlorate and/or nitrate as electron acceptor The public defense of my thesis will take place in the Aula of Wageningen University (Generall Faulkesweg 1, Wageningen) on December 18 2013 at 4:00 pm. This defense is followed by a reception in Café Carré (Vijzelstraat 2, Wageningen). Margreet J. Oosterkamp J. Margreet Paranimphs Ton van Gelder ([email protected]) Aura Widjaja Margreet J. Oosterkamp ([email protected]) Marjet Oosterkamp (911 W Springfield Ave Apt 19, Urbana, IL 61801, USA; [email protected]) Omslag met flap_MJOosterkamp.indd 1 25-11-2013 5:58:31 Physiology and biochemistry of aromatic hydrocarbon-degrading bacteria that use chlorate and/or nitrate as electron acceptor Margreet J. Oosterkamp Thesis-MJOosterkamp.indd 1 25-11-2013 6:42:09 Thesis committee Thesis supervisor Prof. dr. ir. A. J. M. Stams Personal Chair at the Laboratory of Microbiology Wageningen University Thesis co-supervisors Dr. C. M. Plugge Assistant Professor at the Laboratory of Microbiology Wageningen University Dr. P. J. Schaap Assistant Professor at the Laboratory of Systems and Synthetic Biology Wageningen University Other members Prof. dr. L. Dijkhuizen, University of Groningen Prof. dr. H. J. Laanbroek, University of Utrecht Prof. -
Structure and Evolution of Chlorate Reduction Composite Transposons
RESEARCH ARTICLE Structure and Evolution of Chlorate Reduction Composite Transposons Iain C. Clark,a Ryan A. Melnyk,b Anna Engelbrektson,b John D. Coatesb Department of Civil and Environmental Engineeringa and Department of Plant and Microbial Biology,b University of California, Berkeley, California, USA ABSTRACT The genes for chlorate reduction in six bacterial strains were analyzed in order to gain insight into the metabolism. A newly isolated chlorate-reducing bacterium (Shewanella algae ACDC) and three previously isolated strains (Ideonella dechlora- tans, Pseudomonas sp. strain PK, and Dechloromarinus chlorophilus NSS) were genome sequenced and compared to published sequences (Alicycliphilus denitrificans BC plasmid pALIDE01 and Pseudomonas chloritidismutans AW-1). De novo assembly of genomes failed to join regions adjacent to genes involved in chlorate reduction, suggesting the presence of repeat regions. Using a bioinformatics approach and finishing PCRs to connect fragmented contigs, we discovered that chlorate reduction genes are flanked by insertion sequences, forming composite transposons in all four newly sequenced strains. These insertion sequences delineate regions with the potential to move horizontally and define a set of genes that may be important for chlorate reduction. In addition to core metabolic components, we have highlighted several such genes through comparative analysis and visualiza- tion. Phylogenetic analysis places chlorate reductase within a functionally diverse clade of type II dimethyl sulfoxide (DMSO) reductases, part of a larger family of enzymes with reactivity toward chlorate. Nucleotide-level forensics of regions surrounding chlorite dismutase (cld), as well as its phylogenetic clustering in a betaproteobacterial Cld clade, indicate that cld has been mobi- lized at least once from a perchlorate reducer to build chlorate respiration. -
Dissertation Wenjie Sun 2008 FV
Microbial Oxidation of Arsenite in Anoxic Environments: Impacts on Arsenic Mobility Item Type text; Electronic Dissertation Authors Sun, Wenjie Publisher The University of Arizona. Rights Copyright © is held by the author. Digital access to this material is made possible by the University Libraries, University of Arizona. Further transmission, reproduction or presentation (such as public display or performance) of protected items is prohibited except with permission of the author. Download date 26/09/2021 19:57:24 Link to Item http://hdl.handle.net/10150/194899 MICROBIAL OXIDATION OF ARSENITE IN ANOXIC ENVIRONMENTS: IMPACTS ON ARSENIC MOBILITY by Wenjie Sun _____________________ Copyright © Wenjie Sun 2008 A Dissertation Submitted to the Faculty of the DEPARTMENT OF CHEMICAL AND ENVIRONMENTAL ENGINEERING In Partial Fulfillment of the Requirements For the Degree of DOCTOR OF PHILOSOPHY WITH A MAJOR IN ENVIRONMENTAL ENGINEERING In the Graduate College THE UNIVERSITY OF ARIZONA 2008 2 THE UNIVERSITY OF ARIZONA GRADUATE COLLEGE As members of the Dissertation Committee, we certify that we have read the dissertation prepared by Wenjie Sun entitled “Microbial Oxidation of Arsenite in Anoxic Environments: Impacts on Arsenic Mobility”, and recommend that it be accepted as fulfilling the dissertation requirement for the Degree of Doctor of Philosophy. _______________________________________________________________________ Date: 11/10/08 Maria R. Sierra Alvarez _______________________________________________________________________ Date: 11/10/08 -
Discovery of Industrially Relevant Oxidoreductases
DISCOVERY OF INDUSTRIALLY RELEVANT OXIDOREDUCTASES Thesis Submitted for the Degree of Master of Science by Kezia Rajan, B.Sc. Supervised by Dr. Ciaran Fagan School of Biotechnology Dublin City University Ireland Dr. Andrew Dowd MBio Monaghan Ireland January 2020 Declaration I hereby certify that this material, which I now submit for assessment on the programme of study leading to the award of Master of Science, is entirely my own work, and that I have exercised reasonable care to ensure that the work is original, and does not to the best of my knowledge breach any law of copyright, and has not been taken from the work of others save and to the extent that such work has been cited and acknowledged within the text of my work. Signed: ID No.: 17212904 Kezia Rajan Date: 03rd January 2020 Acknowledgements I would like to thank the following: God, for sending me angels in the form of wonderful human beings over the last two years to help me with any- and everything related to my project. Dr. Ciaran Fagan and Dr. Andrew Dowd, for guiding me and always going out of their way to help me. Thank you for your patience, your advice, and thank you for constantly believing in me. I feel extremely privileged to have gotten an opportunity to work alongside both of you. Everything I’ve learnt and the passion for research that this project has sparked in me, I owe it all to you both. Although I know that words will never be enough to express my gratitude, I still want to say a huge thank you from the bottom of my heart. -
Perchlorate and Chlorate Degradation by Two Organisms Isolated from Wastewater CHEMISTRY
Perchlorate and chlorate degradation by two organisms isolated from wastewater Microbial identification and kinetics Filipa Costa Pinto Prata Thesis submitted in fulfilment of the requirements for the degree of Master Science in CHEMISTRY President: Profª Doutora Matilde Marques, IST-UTL Promotors: Profª Doutora Cristina Costa, FCT-UNL Profª Doutora Cristina Viegas, IST-UTL Doutor Paulo Costa Lemos, FCT-UNL November 2007 ACKNOWLEDGMENTS I wish to express my sincere gratitude to Prof ª Doutora Maria Cristina Costa, for the opportunity to perform my dissertation, support and guidance. To Profª Doutora Cristina Viegas I would like to thank to accept to be my promotor. I would also especially like to thank Doutor Paulo Lemos and Profª Doutora Maria Ascensão Miranda Reis for their laboratorial guidance, suggestions and scientific advises which improved this work. I would like to thank the BioEng staff for their friendship during my laboratorial work and also my gratitude to Marta for her hold. Many thanks to my friends for their constant hold, encouragement and patience throughout the duration of this project. They always have a word of support and a smile to give me. Thank you Cristiana, Mariana and Bruna. Never enough thanks to one who doesn’t want to be named but he knows who he is and so do I. To my family I just want to thank for their care, support and ethical values that always motivated me to improve my knowledge and personality. ABSTRACT - - The biological removal of perchlorate (ClO 4 ) and chlorate (ClO 3 ) can be viewed as a very promising water treatment technology. -
Environmental Microbiology, Second Edition Edited by Ralph Mitchell and Ji-Dong Gu Copyright © 2010 Wiley-Blackwell
ENVIRONMENTAL MICROBIOLOGY SECOND EDITION Edited by Ralph Mitchell and Ji-Dong Gu A JOHN WILEY & SONS, INC., PUBLICATION ENVIRONMENTAL MICROBIOLOGY ENVIRONMENTAL MICROBIOLOGY SECOND EDITION Edited by Ralph Mitchell and Ji-Dong Gu A JOHN WILEY & SONS, INC., PUBLICATION Copyright © 2010 by Wiley-Blackwell. All rights reserved. Published by John Wiley & Sons, Inc., Hoboken, New Jersey Published simultaneously in Canada. Wiley-Blackwell is an imprint of John Wiley & Sons, formed by the merger of Wiley’s global Scientific, Technical, and Medical business with Blackwell Publishing. No part of this publication may be reproduced, stored in a retrieval system, or transmitted in any form or by any means, electronic, mechanical, photocopying, recording, scanning, or otherwise, except as permitted under Section 107 or 108 of the 1976 United States Copyright Act, without either the prior written permission of the Publisher, or authorization through payment of the appropriate per-copy fee to the Copyright Clearance Center, Inc., 222 Rosewood Drive, Danvers, MA 01923, 978-750-8400, fax 978-750-4470, or on the web at www.copyright.com. Requests to the Publisher for permission should be addressed to the Permissions Department, John Wiley & Sons, Inc., 111 River Street, Hoboken, NJ 07030, 201-748-6011, fax 201-748-6008, or online at http://www.wiley.com/go/permission. Limit of Liability/Disclaimer of Warranty: While the publisher and author have used their best efforts in preparing this book, they make no representations or warranties with respect to the accuracy or completeness of the contents of this book and specifically disclaim any implied warranties of merchantability or fitness for a particular purpose.