Mosfet/Igbt Drivers Theory and Applications
Total Page:16
File Type:pdf, Size:1020Kb
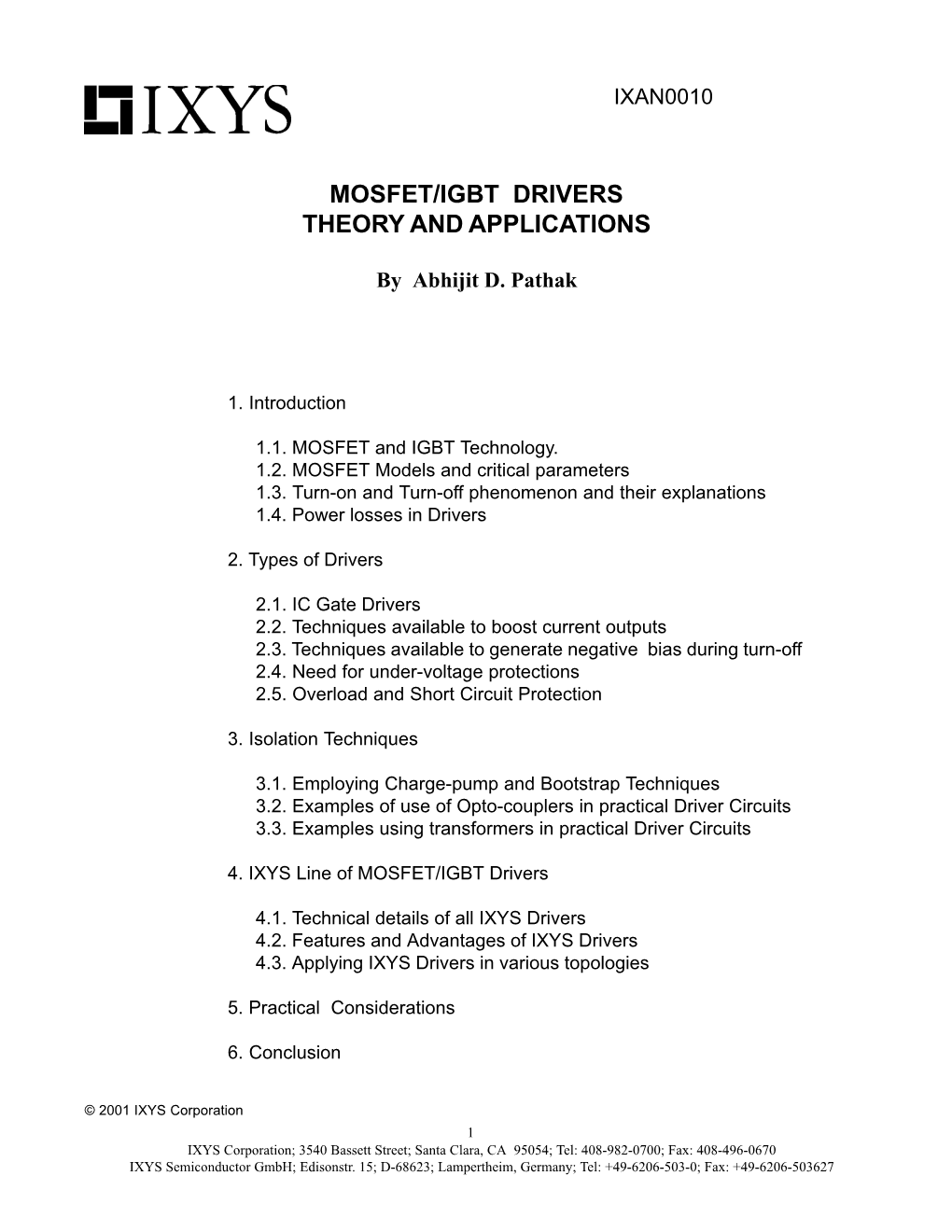
Load more
Recommended publications
-
UCC27531 35-V Gate Driver for Sic MOSFET Applications (Rev. A)
(1) Application Report SLUA770A–March 2016–Revised May 2018 UCC27531 35-V Gate Driver for SiC MOSFET Applications Richard Herring........................................................................................... High Power Driver Solutions ABSTRACT SiC MOSFETs are gaining popularity in many high-power applications due to their significant switching performance advantages. SiC MOSFETs are also available with attractive voltage ratings and current capabilities. However, the characteristics of SiC MOSFETs require consideration of the gate-driver circuit to optimize the switching performance of the SiC device. Although SiC MOSFETs are not difficult to drive properly, many typical MOSFET drivers may result in compromised switching speed performance. The UCC27531 gate driver includes features and has operating parameters that allow for driving SiC power MOSFETs within the recommended optimum drive configuration. This application note reviews the characteristics of SiC MOSFETs and how to drive them to achieve the performance improvement that SiC can bring at the system level. The features of UCC27531 to achieve optimal performance of SiC are explained and results from a demonstration circuit are provided. 1 Introduction In the past, the majority of applications such as uninterruptible power supplies (UPS), photovoltaic (PV) inverters, and motor drive have utilized IGBTs for the power devices due to the combination of high- voltage ratings exceeding 1 kV and high current capability. Usable switching frequency of IGBTs has typically been limited to 20–30 kHz, due to the high turnoff losses caused by the long turnoff current tail. Design comparisons have shown that SiC MOSFET designs can operate at considerably higher switching frequency and achieve the same or better efficiency. Although the device cost of the SiC MOSFETs are higher than the equivalent IGBTs, the significant savings in transformer, capacitor, and enclosure size results in a lower system cost. -
Egan® Ics for Low Voltage DC-DC Applications Egan® Ics for Low Voltage DC-DC Applications EFFICIENT POWER CONVERSION
APPLICATION NOTE: AN025 eGaN® ICs for Low Voltage DC-DC Applications eGaN® ICs for Low Voltage DC-DC Applications EFFICIENT POWER CONVERSION Michael de Rooij, Ph.D., Vice President of Applications Engineering , Yuanzhe Zhang, Ph.D., Director of Applications Engineering eGaN® FETs from EPC have repeatedly demonstrated higher performance over Monolithic integration of the gate driver to the MOSFET counterparts in many applications [1]. The lateral structure and material FET offers the lowest possible common source properties of eGaN FETs make it possible to monolithically integrate a number of FETs inductance (CSI) as it is moved to within the as demonstrated by products such as the EPC2107 [2]. The next phase in the eGaN IC structure. Furthermore the gate driver has been optimized for the FET being driven to offer FET and IC evolution includes gate driver integration. Integrating the gate driver with maximum performance under any operating the FET offers a number of additional advantages over discrete gate driver and FET condition. These benefits are on top of the well- solutions such as extremely low common source inductance, matched gate driver established low capacitance and inductance, and to FET, and ease of design. All the traditional eGaN FET benefits such as significantly zero reverse recovery charge (QRR) that enable lower capacitance and inductance with zero reverse recovery charge (QRR) in a smaller efficient operation at high switching frequencies even under hard switching conditions. The key footprint for a given on-resistance (RDS(on)) than comparable MOSFETs are retained. However, the combined effect of the new characteristics and benefits ensures an ever characteristics of the EPC2112 are given in table 1. -
Moogerfooger® MF-107 Freqbox™
Understanding and Using your moogerfooger® MF-107 FreqBox™ TABLE OF CONTENTS Introduction.................................................2 Getting Started Right Away!.......................4 Basic Applications......................................6 FreqBox Theory........................................10 FreqBox Functions....................................16 Advanced Applications.............................21 Technical Information...............................24 Limited Warranty......................................25 MF-107 Specifications..............................26 1 Welcome to the world of moogerfooger® Analog Effects Modules. Your Model MF-107 FreqBox™ is a rugged, professional-quality instrument, designed to be equally at home on stage or in the studio. Its great sound comes from the state-of-the- art analog circuitry, designed and built by the folks at Moog Music in Asheville, NC. Your MF-107 FreqBox is a direct descendent of the original modular Moog® synthesizers. It contains several complete modular synth functions: a voltage-controlled oscillator (VCO) with variable waveshape, capable of being hard synced and frequency modulated by the audio input, and an envelope follower which allows the dynamics of the input signal to modulate the frequency of the VCO. In addition the amplitude of the VCO is controlled by the dynamics of the input signal, and the VCO can be mixed with the audio input. All performance parameters are voltage-controllable, which means that you can use expression pedals, MIDI-to-CV converter, or any other source of control voltages to 'play' your MF-107. Control voltage outputs mean that the MF-107 can be used with other moogerfoogers or voltage controlled devices like the Minimoog Voyager® or Little Phatty® synthesizers. While you can use it on the floor as a conventional effects box, your MF-107 FreqBox is much more versatile and its sound quality is higher than the single fixed function "stomp boxes" that you may be accustomed to. -
Maintenance in Instrumentation Maintenance with Concept and Technology Focusing on Results
Maintenance in instrumentation Maintenance with concept and technology focusing on results www.andritz.com Specific knowledge for reliable instruments. Analytical instrumentation Due to its close relation with operation and process control, Instrumentation is a fundamental discipline to In Analytical Instrumentation, Maintenance continued process industries. Maintenance Solutions Division of ANDRITZ offers to Clients maintenance Solutions Division of ANDRITZ offers ser- contracts, as assuming the responsibility of managing and implementing conventional Instrumentation, as vices ranging from factory’s analyzers to managing specialized modules, such as analytics, metrology, automation and valves. a complete maintenance structure. MS Division can also assume full responsibili- Conventional instrumentation ty of the function, from the management of analyzers’ performance to the purchase Differentials and importation of spares. The purpose is to provide even more reliability to analytical ▪ Active in the management of contracts since 1993 process and environmental variables. ▪ Experience in major projects: “greenfield” and “brownfield“ Scope of the function ▪ Large specific instrumentation training bank ▪ Control loops in general ▪ Technologies integration capacity, ranging from pneumatic ▪ Field instrumentation and accessories nstrumentation through Fieldbus ▪ Primary measuring elements: sensors, Differentials ▪ Technological exchange between the diverse hired contracts Scope of the function detectors and meters ▪ Pioneer in Brazil in analytical -
Resonant Gate-Drive Circuits for High-Frequency Power Converters
Resonant Gate-Drive Circuits for High-Frequency Power Converters A dissertation submitted in partial fulfillment of the requirements for the degree of Doctor of Philosophy By Hur Jedi B. S., University of Baghdad, Baghdad, Iraq, 2003 M. S., University Putra Malaysia, Selangor, Malaysia, 2010 2018 Wright State University WRIGHT STATE UNIVERSITY GRADUATE SCHOOL November 16, 2018 I HEREBY RECOMMEND THAT THE DISSERTATION PREPARED UNDER MY SUPERVISION BY Hur Jedi ENTITLED Resonant Gate-Drive Circuits for High-Frequency Power Converters BE ACCEPTED IN PARTIAL FULFILLMENT OF THE REQUIREMENTS FOR THE DEGREE OF Doctor of Philosophy. Marian K. Kazimierczuk, Ph.D. Dissertation Director Arnab Shaw, Ph.D. Director, Electrical Engineering Ph.D. Program Barry Milligan, Ph.D. Interim Dean of the Graduate School Committee on Final Examination Marian K. Kazimierczuk, Ph.D. Ray Siferd, Ph.D. Henry Chen, Ph.D. Saiyu Ren, Ph.D. Yan Zhuang, Ph.D. Abstract Jedi, Hur. Ph.D., Electrical Engineering Ph.D. Program, Department of Electrical Engineering, Wright State University, 2018. Resonant Gate-Drive Circuits for High- Frequency Power Converters. The development trend of power converters motivates the pursuit with high den- sity, high efficiency, and low cost. Increasing the frequency can improve the power density and lead to small passive elements and a fast dynamic response. Each one of these power converters must be driven by a gate-drive circuit to operate efficiently. Conventional gate-drivers are used up to frequencies of about 5 MHz and suffer from switching losses. Therefore, the development of switch-mode power supplies (SMPS) operating at high frequencies requires high-speed gate drivers. -
Igbts (Insulated Gate Bipolar Transistor) Application Note
IGBTs (Insulated Gate Bipolar Transistor) Application Note IGBTs (Insulated Gate Bipolar Transistor) Description This document describes the basic structures, ratings, and electrical characteristics of IGBTs. It also provides usage considerations for IGBTs. © 2018 1 2018-09-01 Toshiba Electronic Devices & Storage Corporation IGBTs (Insulated Gate Bipolar Transistor) Application Note Table of Contents Description ............................................................................................................................................ 1 Table of Contents ................................................................................................................................. 2 1. Device structure and characteristics of IGBTs ............................................................................. 6 1.1. Basic structure of the IGBT ................................................................................................................ 6 1.2. Comparison of different types of transistors (bipolar transistors, MOSFETs, and IGBTs) ....... 8 2. Different types of IGBTs and their structures ............................................................................ 11 2.1. Gating structures ................................................................................................................................11 2.2. IGBT classification based on the vertical structure ...................................................................... 12 2.2.1. Punch-through (PT) IGBTs ................................................................................................................12 -
Chapter 6 BUILDING a HOMEBREW
1. Chapter 6, Harris CRYSTAL SETS TO SIDEBAND © Frank W. Harris 2002 Chapter 6 BUILDING A HOMEBREW QRP Among the guys I work, QRPs seem to be the most common homebrew project, second only to building antennas. Therefore this chapter describes a simple QRP design I have settled on. I use my QRPs as stand-alone transmitters or I use them to drive a final amplifier to produce higher power, 25 to 100 watts. It’s true that before you build a transmitter you’ll need a receiver. Unfortunately, a good selective, all-band ham receiver is complicated to build and most guys don’t have the time and enthusiasm to do it. (See chapter 13.) The next chapter describes building a simple, 5 transistor 40 meter receiver which I have used with the QRP below to talk to other hams. This simple receiver will work best during off hours when 40 meters isn’t crowded. It can also be used to receive Morse code for code practice. A 40 meter QRP module. The QRP transmitter above is designed exclusively for 40 meters, (7.000 to 7.300 MHz.) The twelve-volt power supply comes in through the pig-tail wire up on the right. The telegraph key plugs into the blue-marked phono plug socket on the right of the aluminum heat sink. The antenna output is the red-colored socket on the left end of the heat sink. The transmitting frequency of the QRP module is controlled by a quartz crystal. That’s the silver rectangular can plugged into the box on the right front. -
What Is a Neutral Earthing Resistor?
Fact Sheet What is a Neutral Earthing Resistor? The earthing system plays a very important role in an electrical network. For network operators and end users, avoiding damage to equipment, providing a safe operating environment for personnel and continuity of supply are major drivers behind implementing reliable fault mitigation schemes. What is a Neutral Earthing Resistor? A widely utilised approach to managing fault currents is the installation of neutral earthing resistors (NERs). NERs, sometimes called Neutral Grounding Resistors, are used in an AC distribution networks to limit transient overvoltages that flow through the neutral point of a transformer or generator to a safe value during a fault event. Generally connected between ground and neutral of transformers, NERs reduce the fault currents to a maximum pre-determined value that avoids a network shutdown and damage to equipment, yet allows sufficient flow of fault current to activate protection devices to locate and clear the fault. NERs must absorb and dissipate a huge amount of energy for the duration of the fault event without exceeding temperature limitations as defined in IEEE32 standards. Therefore the design and selection of an NER is highly important to ensure equipment and personnel safety as well as continuity of supply. Power Transformer Motor Supply NER Fault Current Neutral Earthin Resistor Nov 2015 Page 1 Fact Sheet The importance of neutral grounding Fault current and transient over-voltage events can be costly in terms of network availability, equipment costs and compromised safety. Interruption of electricity supply, considerable damage to equipment at the fault point, premature ageing of equipment at other points on the system and a heightened safety risk to personnel are all possible consequences of fault situations. -
INSTRUMENTATION and CONTROL Module 3 Level Detectors
Department of Energy Fundamentals Handbook INSTRUMENTATION AND CONTROL Module 3 Level Detectors Level Detectors TABLE OF CONTENTS TABLE OF CONTENTS LIST OF FIGURES .................................................. ii LIST OF TABLES ................................................... iii REFERENCES ..................................................... iv OBJECTIVES ...................................................... v LEVEL DETECTORS ................................................ 1 Gauge Glass .................................................. 1 Ball Float .................................................... 4 Chain Float ................................................... 5 Magnetic Bond Method .......................................... 6 Conductivity Probe Method ....................................... 6 Differential Pressure Level Detectors ................................. 7 Summary ................................................... 10 DENSITY COMPENSATION .......................................... 11 Specific Volume .............................................. 11 Reference Leg Temperature Considerations ............................ 12 Pressurizer Level Instruments ..................................... 13 Steam Generator Level Instrument .................................. 13 Summary ................................................... 14 LEVEL DETECTION CIRCUITRY ...................................... 15 Remote Indication ............................................. 15 Environmental Concerns ........................................ -
Programmable Logic Controller
Revised 10/07/19 SPECIFICATIONS - DETAILED PROVISIONS Section 17010 - Programmable Logic Controller C O N T E N T S PART 1 - GENERAL ....................................................................................................................... 1 1.01 DESCRIPTION .............................................................................................................. 1 1.02 RELATED SECTIONS ...................................................................................................... 1 1.03 REFERENCE STANDARDS AND CODES ............................................................................ 2 1.04 DEFINITIONS ............................................................................................................... 2 1.05 SUBMITTALS ............................................................................................................... 3 1.06 DESIGN REQUIREMENTS .............................................................................................. 8 1.07 INSTALLED-SPARE REQUIREMENTS ............................................................................. 13 1.08 SPARE PARTS............................................................................................................. 13 1.09 MANUFACTURER SERVICES AND COORDINATION ........................................................ 14 1.10 QUALITY ASSURANCE................................................................................................. 15 PART 2 - PRODUCTS AND MATERIALS......................................................................................... -
Pulse Width Modulation
International Journal of Research in Engineering, Science and Management 38 Volume-2, Issue-12, December-2019 www.ijresm.com | ISSN (Online): 2581-5792 Pulse Width Modulation M. Naganetra1, R. Ramya2, D. Rohini3 1,2,3Student, Dept. of Electronics & Communication Engineering, K. S. Institute of Technology, Bengaluru India Abstract: This paper presents pulse width modulation which can 2. Principle be controlled by duty cycle. Pulse width modulation(PWM) is a Pulse width modulation uses a rectangular pulse wave powerful technique for controlling analog circuits with a digital signal. PWM is widely used in different applications, ranging from whose pulse width is modulated resulting in the variation of the measurement and communications to power control and average value of the waveform. If we consider a pulse signal conversions, which transforms the amplitude bounded input f(t), with period T, low value Y-min, high value Y-max and a signals into the pulse width output signal without suffering noise duty cycle D. Average value of the output signal is given by, quantization. The frequency of output signal is usually constant. By controlling analog circuits digitally, system cost and power 1 푇 푦̅= ∫ 푓(푡)푑푡 consumption can be reduced. The PWM signal is still digital 푇 0 because, at any instant of time, the full DC supply will be either fully_ ON or fully _OFF. Given a sufficient bandwidth, any analog 3. PWM generator signals (sine, square, triangle and so on) can be encoded with PWM. Keywords: decrease-duty, duty cycle, increase-duty, PWM (pulse width modulation), RTL view 1. Introduction Pulse width modulation (or pulse duration modulation) is a method of reducing the average power delivered by an electrical Fig. -
How Can You Replicate Real World Signals? Precisely
How can you replicate real world signals? Precisely tç)[UP.)[ 7QQ PSDIBOOFMT FG400 Series t*OUVJUJWFPQFSBUJPOXJUIBw Arbitrary/Function Generator LCD screen t4ZODISPOJ[FVQUPVOJUTUP QSPWJEFVQUPPVUQVU DIBOOFMT t"WBSJFUZPGTXFFQTBOE modulations Bulletin FG400-01EN Features and benefits FG400 Series Features and CFOFýUT &BTJMZHFOFSBUFCBTJD BQQMJDBUJPOTQFDJýDBOEBSCJUSBSZXBWFGPSNT 2 The FG400 Arbitrary/Function Generator provides a wide variety of waveforms as standard and generates signals simply and easily. There are one channel (FG410) and two channel (FG420) models. As the output channels are isolated, an FG400 can also be used in the development of floating circuits. (up to 42 V) Basic waveforms Advanced functions 4JOF DC 4XFFQ.PEVMBUJPO Burst 0.01 μHz to 30 MHz ±10 V/open Frequency sweep "VUP Setting items Oscillation and stop are 4RVBSF start/stop frequency, time, mode automatically repeated with the (continuous, single, gated single), respectively specified wave number. function (one-way/shuttle, linear/ log) 0.01 μHz to 15 MHz, variable duty Pulse 18. Trigger Setting items Oscillation with the specified wave carrier duty, peak duty deviation number is done each time a trigger Output duty is received. the range of carrier duty ±peak duty deviation 0.01 μHz to 15 MHz, variable leading/trailing edge time Ramp ". Gate Setting items Oscillation is done in integer cycles carrier amplitude, modulation depth or half cycles while the gate is on. Output amp. the range of amp./2 × (1 ±mod. 0.01 μHz to 5 MHz, variable symmetry Depth/100) 3 For trouble shooting Arbitrary waveforms (16 bits amplitude resolution) of up to 512 K words per waveform can be generated. 128 waveforms with a total size of 4 M words can be saved to the internal non-volatile memory.