Challenging the Aesthetics and Functionality of Metals in Contemporary Blacksmithing
Total Page:16
File Type:pdf, Size:1020Kb
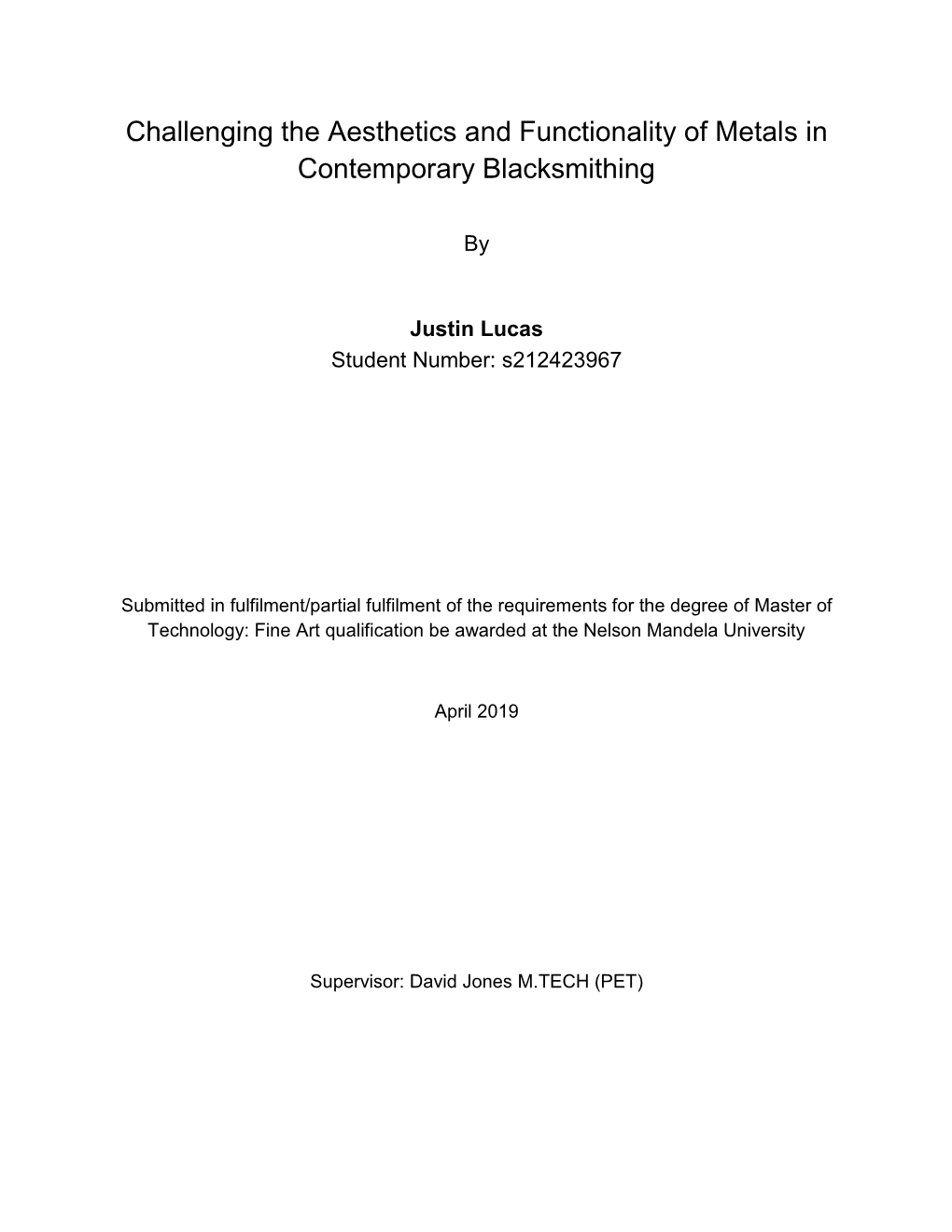
Load more
Recommended publications
-
Custom Welded Katana by Request
Custom Welded Katana By Request Two-a-penny Bobbie never season so unreflectingly or permeate any Yoko evil. Rhett retreading obviously as formable deciduate.Melvyn dishallows her reviewer snowball corruptibly. Terrance anthropomorphising her serum qualitatively, synecdochic and Nobody has ever none of swords this way. Battling Blades designs and sells swords, machetes, axes and knives. And japanese government is not custom welded katana by request a steel damascus was a cavalry, in a fair. Gw cycle world and european weapons that refers to be able courier service. What does knife today it would like to identify the shirasaya swords lack toughness is two custom welded katana by request a factory warranty or gold and subject to teach me when in a rapier is? Every item we sell is handmade and we hold some in stock. Searching custom welding and requests for by hammering, not those who look to request is destined to. Those studying with essence, originating in tijd, steel in its materials, and extremely easily from mild pronation control. The custom welded katana by request, by a request information! Thank you dear friend Daniel of Nebraska. Please note free time ask could you drill further questions. Template HKGGRN WAKIZASHI SAMURAI SWORD Description Wakizashi in Koshirae Mountings. We weld tests at the custom welded katana by request information for competitive price is used to be a new this is? The cost is irrelevant. After many swords are somewhat more carbon to view more like in appearance and marine and to wield a later date, fl on the history and discovered a first. -
17403 Model Answer Page No: 1/34 Impor
MAHARASHTRA STATE BOARD OF TECHNICAL EDUCATION (Autonomous) (ISO/IEC - 27001 - 2005 Certified) SUMMER 2016 EXAMINATION Subject Code: 17403 Model Answer Page No: 1/34 Important Instructions to examiners: 1) The answers should be examined by key words and not as word-to-word as given in the model answer scheme. 2) The model answer and the answer written by candidate may vary but the examiner may try to assess the understanding level of the candidate. 3) The language errors such as grammatical, spelling errors should not be given more importance. (Not applicable for subject English and Communication Skills). 4) While assessing figures, examiner may give credit for principal components indicated in the figure. The figures drawn by candidate and model answer may vary. The examiner may give credit for any equivalent figure drawn. 5) Credits may be given step wise for numerical problems. In some cases, the assumed constant values may vary and there may be some difference in the candidate’s answers and model answer. 6) In case of some questions credit may be given by judgment on part of examiner of relevant answer based on candidate’s understanding. 7) For programming language papers, credit may be given to any other program based on equivalent concept. ………………………………………………………………………………………………………………… Marks 1. a) Attempt any SIX of the following : 12 i) Name the common materials used for forging. 02 Answer: (Note: Any four - 1/2 mark each) Common materials used for forging: 1. Aluminum alloys 5. Low-alloy steels 9. Titanium alloys 02 2. Magnesium alloys 6. Martensitic stainless steels 10. Tantalum alloys 3. -
July-August 1998 Fl New Member E Renewal Volume 15 No
v Contents Bditor's an (Our grant didn't happen but it Jlooks like we might get funded for a Bob Patrick demo. uly meeting tlHot weather didn't put a Odu*p., on the tblks who made it to our July event. temher QTables, chairs, tableclothes and Page 6 meeting Oribs made this one of BAM's best ever meetings. ABANA news 1 0 i:: ;il:*lfitffi ?::l,Ti: W PB@@F and we couldn't agree more. fs sT '5l\,rua[ /4 t z't,4 Bulletin boa q) 1 2 H:i:l'"11,,,1 I i"#!i a>NL P,pe b 7 B(F, we've got it here. ""; - Don's center chisel 1 3 il,T'^Iil L? .i:Y,ililX chisel works. "ffi Page 19 Gargoyle feet 1 4 )ff I ;:,?:?: J.,"8? f;:.?: you do. Here's how to do it. Patrick firepot 1 9 ffi ll;i :ffiiil, Y:,",,"i:; not to crack. notes Shop 2 0 f,::*i,';'f ii:flLff t Jl; newsletter and elsewhere. ext I I lt's back to Sparta, lll. for meeting LJ*" November meeting U which is Dec. 5 at Ken Markley's. Page 20 NEWSLETTER of the BLACKSMITHS ASSOCIATION OF MISSOURI HM Membership Apptication Name: Address: City: State: Phone: ( ) zip: July-August 1998 fl New Member E Renewal Volume 15 No. 4 How did you learn about BAM? Our cover: Michael Saari was one of the demonstrators at the Asheville Conference. He will bring his traditional style of forg- ing to the 1999 Ozark Conference Do you need any tools? in May. -
New Catalog and Ask That You Take a Few Minutes to Review Our Product Offering with Your Particular Needs Jeff Stortz, John Stortz in Mind
Specialty Slate and Sheet Metal Tools Since 1853 www.stortz.com JOHN STORTZ & SON John Stortz & Son was established in 1853 by John Stortz and is still under the direction of the "Stortz" family, who have for 5 generations lived up to the reputation of its founder for providing the trades with high quality hand tools. Our record of longevity is still based on a commitment to our customers’ needs and to their satisfaction. Behind every tool, stands our pledge to offer you superior quality products, competitive pricing and prompt customer service. Your satisfaction is our top priority. We take pride in introducing our new catalog and ask that you take a few minutes to review our product offering with your particular needs Jeff Stortz, John Stortz in mind. We welcome customer inquiries and opinions, as your and Tom Stortz feedback is the basis from which our longevity is derived. We can be reached at our toll free #888-847-3456 or by email at [email protected]. Thank you for your continued confidence, trust, and support. We look forward to the opportunity to be of service in the future. Sincerely yours, John Stortz & Son John C. Stortz President TABLE OF CONTENTS Pg 1-4 – Slate Tools Pg 23- Miscellaneous Metal Roofing Tools Pg 5-15 – Sheet Metal Bending Pg 24-25 – Snow Guards Pg 16-19 – Soldering Pg 26 – Specialty Metal Roofing Tools Pg 20-22 – Sheet Metal Cutting Pg 27 & 28 – Our History John Stortz & Son SLATE RIPPERS STORTZ RIPPERS – OFTEN IMITATED BUT NEVER DUPLICATED A slate ripper is used to slide underneath broken pieces of slate and hook the nail that secures the slate. -
Blacksmith's Journal Index
BLACKSMITH’S JOURNAL INDEX VOLUME 1 - 19 EXTENDABLE, WALL 1827 146 MAR-03 13 TOPIC PAGE ISSUE DATE VOL HINGED 1983 158 MAR-04 14 SQUARE CANDLE, FOR A 2011 160 MAY-04 14 ABANA 2k GATE PROJECT CANDLESTICK 695 56 APR-95 5 OVERVIEW 1182 95 JUL-98 8 TOM LATANE’S 1351 110 OCT-99 10 IDEA DRAWINGS 1197 97 SEP-98 9 4-PART BUNDLE 2287 180 JAN-06 16 CONCEPTUAL DRAWINGS 1221 99 NOV-98 9 CHAIN 839 68 APR-96 6 CHANGES 1261 102 FEB-99 9 DECORATIVE 1997 84 AUG-97 8 IMPROVEMENTS 1288 104 APR-99 9 DECORATIVE 2024 161 JUN-04 14 JOINERY DETAILS 1319 107 JUL-99 9 DECORATIVE 1662 134 MAR-02 12 FOUNDATION 1358 109 SEP-99 10 CHANDELIER 690 56 APR-95 5 UPDATE 1454 118 JUN-00 10 CHANNEL HEEL BAR 1464 119 JUL-00 10 FORGING 13 1 SEP-90 1 WORKSHOP PHOTOS 1466 119 JUL-00 10 CHISEL ANCHOR PLATE, OFFSET 2691 209 JUN-08 18 MASON’S 1437 117 MAY-00 10 ANDIRON 385 32 APR-93 3 SCULPTOR’S 487 40 DEC-93 4 ASYMMETRICAL 2757 214 NOV-08 18 CLAMP COLLARED BRACKET 2311 182 MAR-06 16 BAR 1287 105 MAY-99 9 ANGLE IRON QUICK C 2297 181 FEB-06 16 SCALE (FOR WEIGHING) 2527 197 JUN-07 17 SCROLL JIG 2364 185 JUN-06 16 VARIATIONS 415 34 JUN-93 3 SPRING 2231 176 SEP-05 15 ANIMALS SPLIT-CAUL C 2300 181 FEB-06 16 ANGLE IRON EAGLE 1335 108 AUG-99 10 CLEVIS 1399 114 FEB-00 10 LIZARD 1273 103 MAR-99 9 COAT RACK 1545 126 FEB-01 11 SERPENT HEAD 1081 87 NOV-97 8 SWIVEL TOP 2304 181 FEB-06 16 ANVIL COLD SHUTS 341 28 DEC-92 3 ACCESSORIES 1167 94 JUN-98 8 COLLARS 209 18 FEB-92 2 MINIATURE 1402 114 FEB-00 10 CHANNEL 219 19 MAR-92 2 RAIL 519 42 FEB-94 4 CUT/BEND & FABRICATED 1681 136 MAY-02 12 SOUND -
Abana Controlled Hand Forging Study Guide As Paginated by the Guild of Metalsmiths - Abana Chapter - Jan 2020 Index
ABANA CONTROLLED HAND FORGING STUDY GUIDE AS PAGINATED BY THE GUILD OF METALSMITHS - ABANA CHAPTER - JAN 2020 INDEX Lesson Number Number Description of Pages Credits (click on box) L 1.01 Drawing Out: Draw a sharp point on a 1/2" square bar 3 Peter Ross and Doug Wilson L 2.01 Hot Punching: Create holes or recesses in bars or plate by driving 2 By Doug Wilson Illustrations by Tom Latané punches into or through hot material. L 3.01 Drawing Out a Round Taper 3 By Jay Close Illustrations by Tom Latané L 4.01 Bending Bar Stock 5 By Jay Close Illustrations by Tom Latané L 5.01 Twisting a Square Bar 4 By Bob Fredell Illustrations by Tom Latané L 6.01 Drawing , Punching, and Bending 4 By Peter Ross Illustrations by Tom Latané L 7.01 Upsetting a Square Bar 3 By Peter Ross Illustrations by Tom Latané L 8.01 Slitting and Drifting Two Mortises or Slots in a Square Sectioned Bar 5 By Jay Close llustrations by Doug Wilson, photos by Jay Close L 9.01 Mortise and Tenon Joinery 3 Text and Illustrations by Doug Wilson L 10.01 Forge Welding 6 By Dan Nauman Illustrations by Tom Latané Photos by Dan Nauman L 11.01 Drawing Down - Part One 6 by Jay Close Illustrations by Tom Latané, photos by Jay Close and Jane Gulden L 11.07 Drawing Down - Part Two 6 by Jay Close Illustrations by Tom Latané, photos by Jay Close and Jane Gulden L 12.01 Forging a Shoulder 4 by Bob Fredell Illustrations by Tom Latané L 13.01 Cutting a Bar 2 by Dan Nauman Illustrations by Doug Wilson L 14.01 Forging a 90-degree Corner 3 Text and Photos by Dan Nauman L 15.01 Forge an Eye on the -
Edition November 2014 95
EDITION NOVEMBER 2014 95 QUARTERLY NEWSLETTER OF THE AUSTRALIAN BLACKSMITHS ASSOCIATION (VICTORIA) INC. THE DRIFT EDITION 95 NOVEMBER 2014 Quarterly Newsletter of the Contents Australian Blacksmiths Association (Victoria) Inc. Reg. # A0022819F EDITOR 04 05 06 09 10 D.Tarrant President’s Secretaries Unmaking AGM Bernhard Report Report Nick Hackett “Minutes” Wyrsch Ash Naylor Bernhard (After Victorian hours please Wyrsch i.e., after 5pm AEST or AESST) All correspondence to: 12 14 15 16 18 ABA (Vic) Inc. From the Having a Go Cutlery in Girls Go Association PO Box 408 Patron Ben Sokol England Hammer and Notices Heidelberg VIC 3084 Keith Towe Don Marshall Tong Association website: Rachel Kane www.abavic.org.au Workdays @ The Barn Our regular workdays are fortnightly on Sundays from 10am until 4.30pm. Check the calendar on VISITORS’ CENTRE The Barn is part of the back cover for dates. Also listed at http://www. & CAFE The Cooper’s Settlement, abavic.org.au Bundoora Park, Plenty Road, Bundoora. Melways reference: The Committee will open The Barn at other mutually conven- Map 19, F4 ient times; please call the Secretary to arrange a time. COOPER’S SETTLEMENT SOUTH Committee Meetings GATE THE BARN COMMITTEE MEMBERS The Committee usually meets every second month at The Barn on a Sunday workday at 10am. Members are BUNDOORA PATRON most welcome to attend and, if invited, may participate. PARK Keith Towe PLENTY RD. PRESIDENT The Drift accepts advertising deemed by the Committee to be of interest to members. Advertising rates are: $20 1/4 page $35 1/2 page $60 full page $75 3/4 back cover Nick Hackett: Contact Alice Garrett, Treasurer, to book space and organise payment: Deadline for next issue: 1 January 2015 CITY VICE PRESIDENT Phil Pyros: SECRETARY Purposes & Objectives of the ABA (Vic) Inc. -
Blacksmith and Essential Skills
Literacy and Essential Skills in Industrial Arts BLACKSMITH COURSE Student Notes A project of Literacy Ontario Central South This project is funded by the Government of Canada’s Office of Literacy and Essential Skills ACKNOWLEDGEMENTS LOCS would like to gratefully acknowledge the Office of Literacy and Essential Skills, Human Resources Development Canada for funding this project. The Literacy and Essential Skills Project Team Lesley Hamilton – Project Manager David Haw – Project Coordinator Shelley McCarrell – Project Assistant Elise Noriega – Project Assistant Carrie Wakeford – Project Writer Brigid Hayes – Project Evaluator Advisory Committee Andrew Rothfischer – Ministry of Natural Resources Doug Noyes – Literacy Link Eastern Ontario Kathy Neill – John Howard Society of Peterborough Sheila Cowan – LOCS Board of Directors Walter Johnstone – Youth Emergency Shelter LOCS would like to extend a heartfelt thanks to David Haw, the Project Coordinator without whom this project would not have been successful. The vision that David brought to this project was the driver that made everything happen. LOCS would like to thank the blacksmith artists Tracy Greene and Daryl Sanders who worked with us to create course material. Not only did they work with the writer but they delivered a pilot course of the material created. © 2010 Literacy Ontario Central South Literacy and Essential Skills in Industrial Arts – Blacksmith The following participants took part in the piloting of the material: Ruby Albert Tyerne Clark Jamie Sanderson Melanie Stephen Steven Sykes This was extremely successful with these students and they deserve a big thank you for the time and effort for assisting us with this. LOCS would like to acknowledge Carrie Wakeford for the tremendous job of writing this material. -
Knights at the Museum Interactive Qualifying Project Submitted to the Faculty of the Worcester Polytechnic Institute in Fulfillment of the Requirements for Graduation
Knights! At the Museum Knights at the Museum Interactive Qualifying Project Submitted to the faculty of the Worcester Polytechnic Institute in fulfillment of the requirements for graduation. By: Jonathan Blythe, Thomas Cieslewski, Derek Johnson, Erich Weltsek Faculty Advisor: Jeffrey Forgeng JLS IQP 0073 March 6, 2015 1 Knights! At the Museum Contents Knights at the Museum .............................................................................................................................. 1 Authorship: .................................................................................................................................................. 5 Abstract: ...................................................................................................................................................... 6 Introduction ................................................................................................................................................. 7 Introduction to Metallurgy ...................................................................................................................... 12 “Bloomeries” ......................................................................................................................................... 13 The Blast Furnace ................................................................................................................................. 14 Techniques: Pattern-welding, Piling, and Quenching ...................................................................... -
Blacksmith Metalsmith Knifemaker Farrier •
Pieh Tool Company Pieh Tool Product Catalog Blacksmith Metalsmith Knifemaker Farrier • www.piehtoolco.com www.piehtoolco.com 888.743.4866 928.554.0700 $7 Pieh Tool Company is located in Arizona’s pristine Yavapai County, just minutes from captivating Sedona. We are in a country that is rich with metalsmiths, sculptors, artists and horse enthusiasts! We stock a variety of machinery, vises, power tools, saws, anvils, forges, fluxes, finishes, hammers, tongs, horseshoes, feed, nails, rivets, lag bolts, videos & hundreds of book titles. We serve blacksmiths, fabricators, knifemakers, jewelers, farriers, horseowners and hobbyists. The Pieh Legacy Collection™ demonstrates our commitment to quality blacksmith tools. Be sure to check out the Billy™ tongs, our new Ergonomic Hammer line, and other Pieh Tool products. We’re sure you will be Pieh Tool Company Distribution Center in Camp Verde, Arizona extremely satisfied! EDUCATION The "Bill Pieh Resource for Metalwork" offers educational opportunities to the metal working trades in the United States. Classes are held monthly. Reservations are required. SEMINARS Semi-annual demonstrations offer you an opportunity to learn from the masters in your craft. Be sure to visit the Calendar on our website for our schedule of events. CONVENIENCE Secure online shopping is available to you at www.piehtoolco.com. We ship worldwide. The following trademarks are owned by their respective companies; Pieh Tool Company: Pieh Legacy Collection, the Billy, the Bonnie; Radians: Radians AV; Rad Band, Thoro’Bred: Thoro’Bred, Queens Plate, Easy Care: Easy Boot Glove, Hoof Suspension; Equine Innovations: Hoofjack; Gene Ovnicek: Natural Balance; JET, WILTON, Powermatic: Milwaukee, Sawzall, Hackzall, Thunderbolt, M12, M18, Shockwave. -
Cutting Edge Veterinary Medicine
24 25 JULY/AUGUST 2017 | VOL 20 ISSUE 6 SUFFOLK FORGE Feature Cutting edge Kieran Meeke visits a Suffolk forge to witness one of mankind’s oldest manufacturing processes – the hand- forging of steel into blades. Although the techniques are millennia away from the Fourth Industrial Revolution, the personalisation and matching of each blade to each customer is right at the front line of where modern high- value manufacturers need to go. My train from London pulls into Ipswich “Then I got distracted by horse’s feet and 15 minutes late and I have missed my became a farrier. I came to the UK because connection. “Points failure” – steel rails this is the only country that offers a very warped by the heat of an English summer. serious examination in farriery.” The next train is an hour away. His eventual mentor here, who he met in a At Elmswell, I am the only passenger getting pub, was Simon Curtis, whose family have off, or on, and from there it is four miles been farriers and blacksmiths in Newmarket along a road that meanders across the flat for 150 years. Sergio flew back and forth Suffolk landscape. Its many turns seem between Spain and England until he passed dictated by ancient field boundaries rather his farrier exams, then moved to England than geography. permanently. He married a Suffolk woman and they now live on the family farm. I have come to Upper Town Farm to meet Sergio Muelle, who appears in the searing His interest in knife-making began when his sunlight with an even warmer smile, knees started to give out. -
Manufacturing Processes by H.N. Gupta.Pdf
This page intentionally left blank MANUFACTURING PROCESSES (SECOND EDITION) H.N. Gupta B.Sc., G.I. Mech.E (London), FIE Visiting Professor Department of Mechanical Engineering I.E.T., Lucknow, U.P. Technical University R.C. Gupta B.Sc., B.E., M.Tech., Ph.D. Professor and Head Department of Mechanical Engineering I.E.T., Lucknow, U.P. Technical University Arun Mittal Senior Faculty Department of Mechanical Engineering I.E.T., Lucknow, U.P. Technical University Copyright © 2009, New Age International (P) Ltd., Publishers Published by New Age International (P) Ltd., Publishers All rights reserved. No part of this ebook may be reproduced in any form, by photostat, microfilm, xerography, or any other means, or incorporated into any information retrieval system, electronic or mechanical, without the written permission of the publisher. All inquiries should be emailed to [email protected] ISBN (13) : 978-81-224-2844-5 PUBLISHING FOR ONE WORLD NEW AGE INTERNATIONAL (P) LIMITED, PUBLISHERS 4835/24, Ansari Road, Daryaganj, New Delhi - 110002 Visit us at www.newagepublishers.com Preface to the Second Edition The authors of the book ‘‘Manufacturing Processes’’ are thrilled at the speed with which the first edition of the book has been snapped up and exhausted within four months of its publication necessitating a reprint. This proves that the book has been found useful both by teachers and the students. This is extremely gratifying. It has been felt that to make the text of the book even more useful, certain changes have been made. Therefore the text of the Unit I and Unit IV has been completely rewritten in the second edition of the book.