The Amateur Carpenter
Total Page:16
File Type:pdf, Size:1020Kb
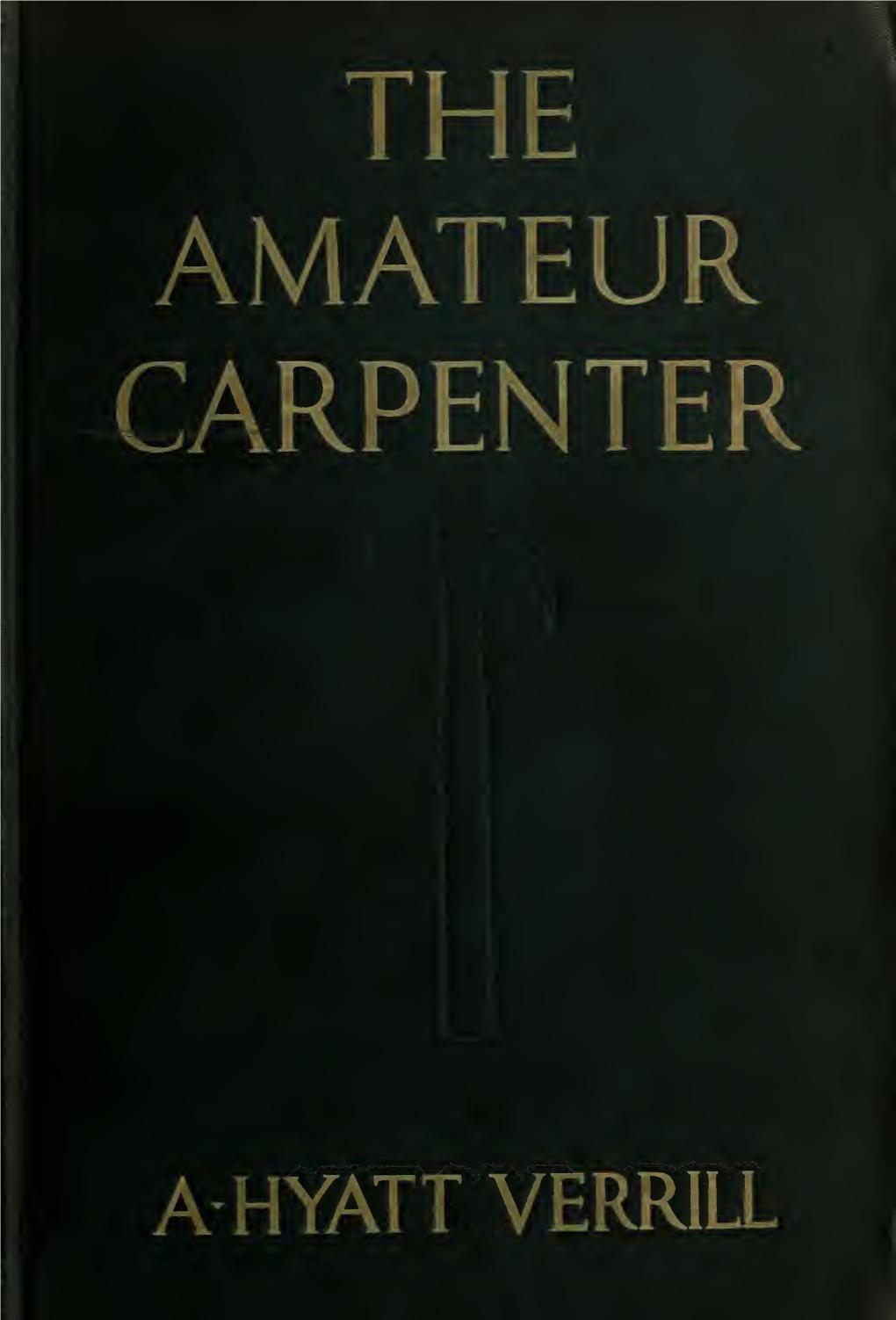
Load more
Recommended publications
-
Metalwork & Woodwork Saws
HAMMERS - ANVILS - METALWORK & WOODWORK SAWS C HAMMERS BENCH PIN & ANVIL 77 CABLE TACKER GUN 76 DAVID USE PHOTO COPING SAWS 79 SD0010 FRETSAW BLADES 79 FRETSAW FRAMES 79 O HAMMER S & MALLETS 72 - 74 HACKSAWS 76 - 77 MINITURE ANVILS 74 MINITURE PINS 75 MALLET MITRE BOXES 82 PIERCING SAW BLADES 78 PIERCING SAW FRAMES 78 N DAVID USE PHOTO PIN PUSHERS 75 SD0010 RAZOR SAWS 81 SAW BLADE LUBRICANT 78 SAW KNIFE BLADES 81 STAPLE GUNS 75 - 76 V-BLOCK & CLAMPS 77 WEB STRETCHER 82 T ANVILS WOOD SAWS 80 - 81 X-ACTO RAZOR SAWS 81 DAVID USE PHOTO ZONA RAZOR SAWS 79 SD0010 E SAWS N DAVID USE PHOTO SD0010 T V BLOCK & CLAMP DAVID USE PHOTO SD0010 S Last Revised 04/07/2011 71 SQUIRES MODEL & CRAFT TOOLS HAMMERS & MALLETS MAGNETIC TACK HAMMER 6oz a specially designed hammer having one striking face magnetised for use when fitting small nails JEWELLERS MALLET a lightweight stainless steel mallet similar and upholstery tacks. The head features a claw for removing to those used by watchmakers and jewellers, with a solid head and tacks, the striking surface is a magnetic split pattern. The head is knurled shaft. hardened and pol- Length 145mm. ished. Fitted on a Weight 2½oz. hickory handle. Weight 6oz, length overall CODE TYPE PRICE 265mm. HA0025 Jewellers Mallet.................................................... £3.99 WATCHMAKERS MALLET a lightweight jewellers and watch- CODE TYPE PRICE makers mallet with a solid brass head. The handle is 260mm long 051-006 Magnetic Tack Hammer 6oz................................. £14.99 and has an increased diameter and is knurled for extra grip. -
Headlok® and Spiderdrive® Are Registered Trademarks of OMG, Inc
® HeadLok PRODUCT DATA SPECIFICATIONS PRODUCT DESCRIPTION COATING The OMG HeadLok is a specialized, flat head OMG CR-10 corrosion resistant coating fastener engineered for a wide range of passes the corrosion requirements of FM panel applications including Structural Insu- Approval Standard 4470 and ETAG 006. lated Panels, Prefabricated Wall Panels, and APPLICATION USE Nailboard, and can also be used in wood, WITH structural concrete*, purlins*, corrugated Install the OMG HeadLok using a high torque, and structural steel substrates. low RPM screw gun. Bring underside of P the washer head flat to the surface. Do not FEATURES & BENEFITS overdrive. For steel substrates, proper point S • Three point and thread styles available style must be determined depending on the for fast installation. steel gauge thickness. W • Spade Point for use in in steel *For structural concrete, use the OMG SC HeadLok with spade points only. The fastener (18 - 22 ga.), structural concrete and DECK wood; must penetrate structural concrete decks a TYPES • Gimlet Point for use in dimensional minimum of 1-inch. Pre-drill using a 3/16-in. lumber; pilot hole at least 1/2-in. (13 mm) deeper than fastener embedment. • Drill Point for use in steel purlins PHYSICAL DATA** up to 3/16-in. thick. The 1/2-in. *For purlin attachment, use OMG HeadLok The data below is constant for each OMG HeadLok. with drill point only. drill point allows the fastener to be HEAD POINT STYLES SHANK drilled through the purlin before the *Prior to job-start, contact OMG to perform a .625" (15.87 mm) • Gimlet .190" (4.82 mm) threads engage. -
1. Hand Tools 3. Related Tools 4. Chisels 5. Hammer 6. Saw Terminology 7. Pliers Introduction
1 1. Hand Tools 2. Types 2.1 Hand tools 2.2 Hammer Drill 2.3 Rotary hammer drill 2.4 Cordless drills 2.5 Drill press 2.6 Geared head drill 2.7 Radial arm drill 2.8 Mill drill 3. Related tools 4. Chisels 4.1. Types 4.1.1 Woodworking chisels 4.1.1.1 Lathe tools 4.2 Metalworking chisels 4.2.1 Cold chisel 4.2.2 Hardy chisel 4.3 Stone chisels 4.4 Masonry chisels 4.4.1 Joint chisel 5. Hammer 5.1 Basic design and variations 5.2 The physics of hammering 5.2.1 Hammer as a force amplifier 5.2.2 Effect of the head's mass 5.2.3 Effect of the handle 5.3 War hammers 5.4 Symbolic hammers 6. Saw terminology 6.1 Types of saws 6.1.1 Hand saws 6.1.2. Back saws 6.1.3 Mechanically powered saws 6.1.4. Circular blade saws 6.1.5. Reciprocating blade saws 6.1.6..Continuous band 6.2. Types of saw blades and the cuts they make 6.3. Materials used for saws 7. Pliers Introduction 7.1. Design 7.2.Common types 7.2.1 Gripping pliers (used to improve grip) 7.2 2.Cutting pliers (used to sever or pinch off) 2 7.2.3 Crimping pliers 7.2.4 Rotational pliers 8. Common wrenches / spanners 8.1 Other general wrenches / spanners 8.2. Spe cialized wrenches / spanners 8.3. Spanners in popular culture 9. Hacksaw, surface plate, surface gauge, , vee-block, files 10. -
Powers-Tapper.Pdf
NEW CONCRETE SCREW TECHNOLOGY Tapper ®+ INSTALLATION PROCEDURES Using the proper diameter bit, drill a hole into the base material to a depth of at least 1/2” deeper than the embedment The required. A TAPPER+ drill bit Tapper+ is a must be used. Blow the hole clean of dust and other material. one-piece self-tapping concrete screw for use in a Select the TAPPER+ installation tool and drive socket to be used. variety of light to medium duty Insert the head of the TAPPER+ into the hex head socket or applications in base materials including Phillips head driver. Set the drill concrete, masonry and wood. It features motor to the “rotation only” a corrosion resistant Perma-Seal ® coating mode to install. and an optimized thread design for lower Place the point of the TAPPER+ through the fixture into the pre- installation torque. The screw also incorporates drilled hole and drive the anchor a gimlet drill point for wood base materials in one steady continuous motion until it is fully seated at the (no pre-drilling required). Tapper+ is available proper embedment. The driver in a variety of head styles and colors to match will automatically disengage from the head of the TAPPER+. the application. Note: Do not select a length that will result in an embedment into the base material which is greater than 2". Most concrete screw anchors cannot be Top Performance of properly driven to a depth of more than 2", especially the Tapper ®+ Sets a in denser base materials. New Standard for Concrete Screws Powers TAPPER ®+ ITW TAPCON ® VS. -
United States National Museum
SMITHSONIAN INSTITUTION UNITED STATES NATIONAL MUSEUM BULLETIN 2 30 WASHINGTON, D.C. 1964 MUSEUM OF HISTORY AND TECHNOLOGY The Bark Canoes and Skin Boats of North America Edwin Tappan Adney and Howard I. Chapelle Curator of Transportation SMITHSONIAN INSTITUTION, WASHINGTON, D.C. 1964 — Publications of the United States National Aiuseum The scholarly and scientific publications of the United States National Museum include two series, Proceedings of the United States National Museum and United States National Museum Bulletin. In these series the Museum publishes original articles and monographs dealing with the collections and work of its constituent museums—The Museum of Natural History and the Museum of History and Technology setting forth newly acquired facts in the fields of Anthropology, Biology, History, Geology, and Technology. Copies of each publication are distributed to libraries, to cultural and scientific organizations, and to specialists and others interested in the different subjects. The Proceedings, begun in 1878, are intended for the publication, in separate form, of shorter papers from the Museum of Natural History. These are gathered in volumes, octavo in size, with the publication date of each paper recorded in the table of contents of the volume. In the Bulletin series, the first of which was issued in 1875, appear longer, separate publications consisting of monographs (occasionally in several parts) and volumes in which are collected works on related subjects. Bulletins are either octavo or quarto in size, depending on the needs of the presentation. Since 1902 papers relating to the botanical collections of the Museum of Natural History have been published in the Bulletin series under the heading Contributions Jrom the United States National Herbarium, and since 1959, in Bulletins titled "Contributions from the Museum of History and Technology," have been gathered shorter papers relating to the collections and research of that Museum. -
Berengario's Drill: Origin and Inspiration
Neurosurg Focus 36 (4):E7, 2014 ©AANS, 2014 Berengario’s drill: origin and inspiration MICHAEL A. CHORNEY, B.S., CHIRAG D. GANDHI, M.D., AND CHARLES J. PRESTIGIACOMO, M.D. Department of Neurological Surgery, Rutgers–New Jersey Medical School, Newark, New Jersey Craniotomies are among the oldest neurosurgical procedures, as evidenced by early human skulls discovered with holes in the calvaria. Though devices change, the principles to safely transgress the skull are identical. Modern neurosurgeons regularly use electric power drills in the operating theater; however, nonelectric trephining instru- ments remain trusted by professionals in certain emergent settings in the rare instance that an electric drill is unavail- able. Until the late Middle Ages, innovation in craniotomy instrumentation remained stunted without much docu- mented redesign. Jacopo Berengario da Carpi’s (c. 1457–1530 CE) text Tractatus de Fractura Calvae sive Cranei depicts a drill previously unseen in a medical volume. Written in 1518 CE, the book was motivated by defeat over the course of Lorenzo II de’Medici’s medical care. Berengario’s interchangeable bit with a compound brace (“vertibu- lum”), known today as the Hudson brace, symbolizes a pivotal device in neurosurgery and medical tool design. This drill permitted surgeons to stock multiple bits, perform the craniotomy faster, and decrease equipment costs during a period of increased incidence of cranial fractures, and thus the need for craniotomies, which was attributable to the introduction of gunpowder. The inspiration stemmed from a school of thought growing within a population of physi- cians trained as mathematicians, engineers, and astrologers prior to entering the medical profession. -
Installation Advice
Installation Advice Tools Required Firstly, you’ll need the right tools for the job. Those are 1. A Dynamic mitre box. 2. A Dynamic polystyrene saw. 3. A Tape measure. 4. A caulking gun. 5. A chalk line. 6. A sponge. All these tools are in the Dynamic DIY Kit. Also included is an installation CD which will provide your customer with invaluable tips to assist in the installation of their Dynamic products. Mitring (Cutting) the Cornice A common mistake is to lay the cornice “flat” and cut as if it was architrave or a picture frame. Remember that the cornice is propped against the back plate of the mitre box (see images below) – The cornice is always put in the mitre box “upside down” - i.e. the edge that will be fixed to the ceiling should be on the base (horizontal section) of the box. There are two main cuts necessary when doing an installation job. The first is the simple straight cut. Place the cornice in the mitre Box and using the polystyrene saw, cut straight across using the 90º guide. The second type of cut will be necessary when cutting the cornice for corners, in other words, cutting the mitres. The first mitre we will deal with is the inside 90º mitre as this is the most common mitre. Place the cornice in the mitre box & using the 45º guide on the right hand side of the mitre box, cut the cornice. You will now have the cornice for the left hand side of your corner. For the right hand side of your corner, repeat the above but use the left hand side 45º guide to cut the cornice. -
Lighting Profiles Arstyl® | Wallstyl® | Nomastyl®
TECHNICAL BROCHURE | Products & Installation 11·2020 LIGHTING PROFILES ARSTYL® | WALLSTYL® | NOMASTYL® 5 5/1 INDEX INFO PRODUCT OVERVIEW 7 GLUE 11 GLUE CONSUMPTION 13 TOOLS 15 FINISH 19 INSPECTIONS INSTRUCTIONS 21 I · CORNICES CORNICES GENERAL PREPARATION, CUTTING, INSTALLATION 1/2 CORNICES Z40 · Z41 · Z42 ARSTYL® CUTTING, REGULAR CORNERS, IRREGULAR CORNERS 1/6 CORNICE Z7 ARSTYL® FIX THE VARIO EXTENSION, INSTALLATION 1/7 SPECIAL CASES CORNICES IN A STAIRWEL 1/10 STEPPED WALL 1/11 EXPANSION JOINTS AND ANTI-VIBRATION ISOLATION JOINTS 1/12 HOLLOW JOINT 1/12 STOPPING A MOULDING 1/13 2 · CHAIR RAILS CHAIR RAILS GENERAL PREPARATION, CUTTING, INSTALLATION 2/2 CURVES FOR CHAIR RAILS PREPARATION, CUTTING, INSTALLATION 2/5 SPECIAL CASE STOPPING A CHAIR RAIL 2/7 3 · SKIRTINGS SKIRTINGS GENERAL PREPARATION, CUTTING, INSTALLATION 3/2 SPECIAL CASES STOPPING A SKIRTING 3/5 4 · FLEXIBLE PROFILES ARSTYL® FLEX • WALLSTYL® FLEX RADIUS 4/2 5 · LIGHTING PROFILES INDIRECT LIGHTING - CORNICES PREPARATION, CUTTING, INSTALLATION 5/2 CORNICES NOMASTYL® OR WALLSTYL® FOR INDIRECT LIGHTING 5/6 WT4 WALLSTYL(r) - COMPLEMENT 5/7 INDIRECT LICHTING SKIRTINGS PREPARATION, CUTTING, INSTALLATION 5/8 LIGHTING PROFILES - FAQ 5/13 TECHNICAL BROCHURE | Index 6 · DESIGN ELEMENTS CEILING ROSES S ARSTYL® PRÉPARATION, INSTALLATION 6/2 R61 IN COMBINATION WITH Z61 PREPARATION, CUTTING, INSTALLATION 6/3 PILASTERS ARSTYL® PREPARATION, CUTTING, INSTALLATION 6/5 WALL PANELS ARSTYL® WALL PANELS PREPARATION, INSTALLATION 6/8 WALL TILES ARSTYL® WALL TILES VARIED AND CREATIVE WALL INSTALLATION OPTIONS 6/12 PREPARATION, INSTALLATION 6/12 SPECIAL CASES INSTALLATION ON A COMPLETE WALL 6/14 7 · FACADE DECORATION WINDOW SILL PROFILE PREPARATION, ANGLED SECTION 7/2 ANGLED WINDOW SILL PROFILE 7/4 FRAME PROFILES 7/5 STRING COURSE 7/9 CUT IN THE PROFILE (DOWNPIPE) 7/9 KEY STONE 7/9 AREA OF THE ROOF OVERHANG AND PASSAGE 7/11 GABLE 7/12 STONES 7/13 CEILING ROSES 7/14 REPAIR OF DAMAGED PROFILES 7/15 This technical brochure has been prepared in accordance with the current state of our knowledge. -
Build a Mitre
Build a Mitre Box 1 2 Curriculum Expectation Activity -- What You Will Do in this Unit In this unit the student will demonstrate DL-H: For students with higher abilities or, ideally, "for students who want to do more". / practise the following: B1.1 -- gather and use pertinent -research key properties of wood and how to inspect, prepare and work with salvaged wood information parts -research fabrication techniques and design strategies for using scrap or salvaged wood flooring to make a picture frame and a mitre box B1.2 -- plan and organize projects and -create, improve and follow a step-by-step fabrication procedure for making a picture related activities using a design process frame and a mitre box and appropriate methods and tools DL-H: These students should be expected to blend good ideas from a variety of possible construction strategies and procedures, thus resulting in an improved fabrication process for a more 'custom' picture frame and highly durable mitre box. B 2.3 -- produce hand-drafted and / or -use a computer aided design application to make fully dimensioned drawings of each of computer-based technical drawings of the wooden parts of the picture frame and mitre box design solutions using standard drafting -produce a complete and accurate parts list tools and conventions DL-H: Will probably want to use the assembly functionality of a 3D CAD application B3.1 -- use appropriate tools, -produce a picture frame of a marketable quality equipment and materials to create -development of hand skills will be stressed in this project -
Tools and Their Uses NAVEDTRA 14256
NONRESIDENT TRAINING COURSE June 1992 Tools and Their Uses NAVEDTRA 14256 DISTRIBUTION STATEMENT A : Approved for public release; distribution is unlimited. Although the words “he,” “him,” and “his” are used sparingly in this course to enhance communication, they are not intended to be gender driven or to affront or discriminate against anyone. DISTRIBUTION STATEMENT A : Approved for public release; distribution is unlimited. NAVAL EDUCATION AND TRAINING PROGRAM MANAGEMENT SUPPORT ACTIVITY PENSACOLA, FLORIDA 32559-5000 ERRATA NO. 1 May 1993 Specific Instructions and Errata for Nonresident Training Course TOOLS AND THEIR USES 1. TO OBTAIN CREDIT FOR DELETED QUESTIONS, SHOW THIS ERRATA TO YOUR LOCAL-COURSE ADMINISTRATOR (ESO/SCORER). THE LOCAL COURSE ADMINISTRATOR (ESO/SCORER) IS DIRECTED TO CORRECT THE ANSWER KEY FOR THIS COURSE BY INDICATING THE QUESTIONS DELETED. 2. No attempt has been made to issue corrections for errors in typing, punctuation, etc., which will not affect your ability to answer the question. 3. Assignment Booklet Delete the following questions and write "Deleted" across all four of the boxes for that question: Question Question 2-7 5-43 2-54 5-46 PREFACE By enrolling in this self-study course, you have demonstrated a desire to improve yourself and the Navy. Remember, however, this self-study course is only one part of the total Navy training program. Practical experience, schools, selected reading, and your desire to succeed are also necessary to successfully round out a fully meaningful training program. THE COURSE: This self-study course is organized into subject matter areas, each containing learning objectives to help you determine what you should learn along with text and illustrations to help you understand the information. -
Woodworking in Estonia
WOODWORKING IN ESTONIA HISTORICAL SURVEY By Ants Viires Translated from Estonian by Mart Aru Published by Lost Art Press LLC in 2016 26 Greenbriar Ave., Fort Mitchell, KY 41017, USA Web: http://lostartpress.com Title: Woodworking in Estonia: Historical Survey Author: Ants Viires (1918-2015) Translator: Mart Aru Publisher: Christopher Schwarz Editor: Peter Follansbee Copy Editor: Megan Fitzpatrick Designer: Meghan Bates Index: Suzanne Ellison Distribution: John Hoffman Text and images are copyright © 2016 by Ants Viires (and his estate) ISBN: 978-0-9906230-9-0 First printing of this translated edition. ALL RIGHTS RESERVED No part of this book may be reproduced in any form or by any electronic or mechanical means including information storage and retrieval systems without permission in writing from the publisher, except by a reviewer, who may quote brief passages in a review. This book was printed and bound in the United States. CONTENTS Introduction to the English Language Edition vii The Twisting Translation Tale ix Foreword to the Second Edition 1 INTRODUCTION 1. Literature, Materials & Methods 2 2. The Role Played by Woodwork in the Peasants’ Life 5 WOODWORK TECHNOLOGY 1. Timber 10 2. The Principal Tools 19 3. Processing Logs. Hollowing Work and Sealed Containers 81 4. Board Containers 96 5. Objects Made by Bending 127 6. Other Bending Work. Building Vehicles 148 7. The Production of Shingles and Other Small Objects 175 8. Turnery 186 9. Furniture Making and Other Carpentry Work 201 DIVISION OF LABOR IN THE VILLAGE 1. The Village Craftsman 215 2. Home Industry 234 FINAL CONCLUSIONS 283 Index 287 INTRODUCTION TO THE ENGLISH-LANGUAGE EDITION feel like Captain Pike. -
Installing GIB-Cove® Installing Range of Quality Profiles to Suit Your Own Personal Style
Introduction This leaflet covers the basics, more information is available by calling 0800 100 442. This leaflet is designed to give you some useful pointers for fixing ® GIB-Cove® at wall-ceiling junctions. Information is included for fixing Tip: GIB-Cove offers a great way to hide the speaker cables from your to new walls as well as how to change the look of a room by fixing GIB- home theatre system. Cove® over existing mouldings. The GIB-Cove® range offers you more flexibility and design choice with a Installing GIB-Cove® Installing range of quality profiles to suit your own personal style. Tip: Installing GIB-Cove® requires some practise and skill. It is possible Tools ® to hide small mistakes, but even a great repair job cannot make Some or all of the following tools will be required depending on the actual poor installation of GIB-Cove® look good. You should therefore GIB-Cove work being carried out. consider the services of an experienced tradesman. Not only will they achieve a better finish, but they will also finish the job quicker • Pencil • Tape and with less fuss. • Square • Fine Tooth Saw • Mitre Box • 150mm Broad knife Figure 1 - Profiles of GIB-Cove® • Plasterers Small Tool • Hammer • Sponge • Chalk Line 0 • Ruler • Sandpaper A good finish requires accurate cutting of mitres in GIB-Cove®. Ensure a 0 good mitre box is used, along with a fine tooth saw. Materials GIB-Cove® GIB-Cove® Classic 55mm GIB-Cove® Alto All GIB-Cove® profiles are available in 3.6m lengths. Measure the perimeter of the walls that will be using the GIB-Cove® to determine the amount required.