Battery Digest Article
Total Page:16
File Type:pdf, Size:1020Kb
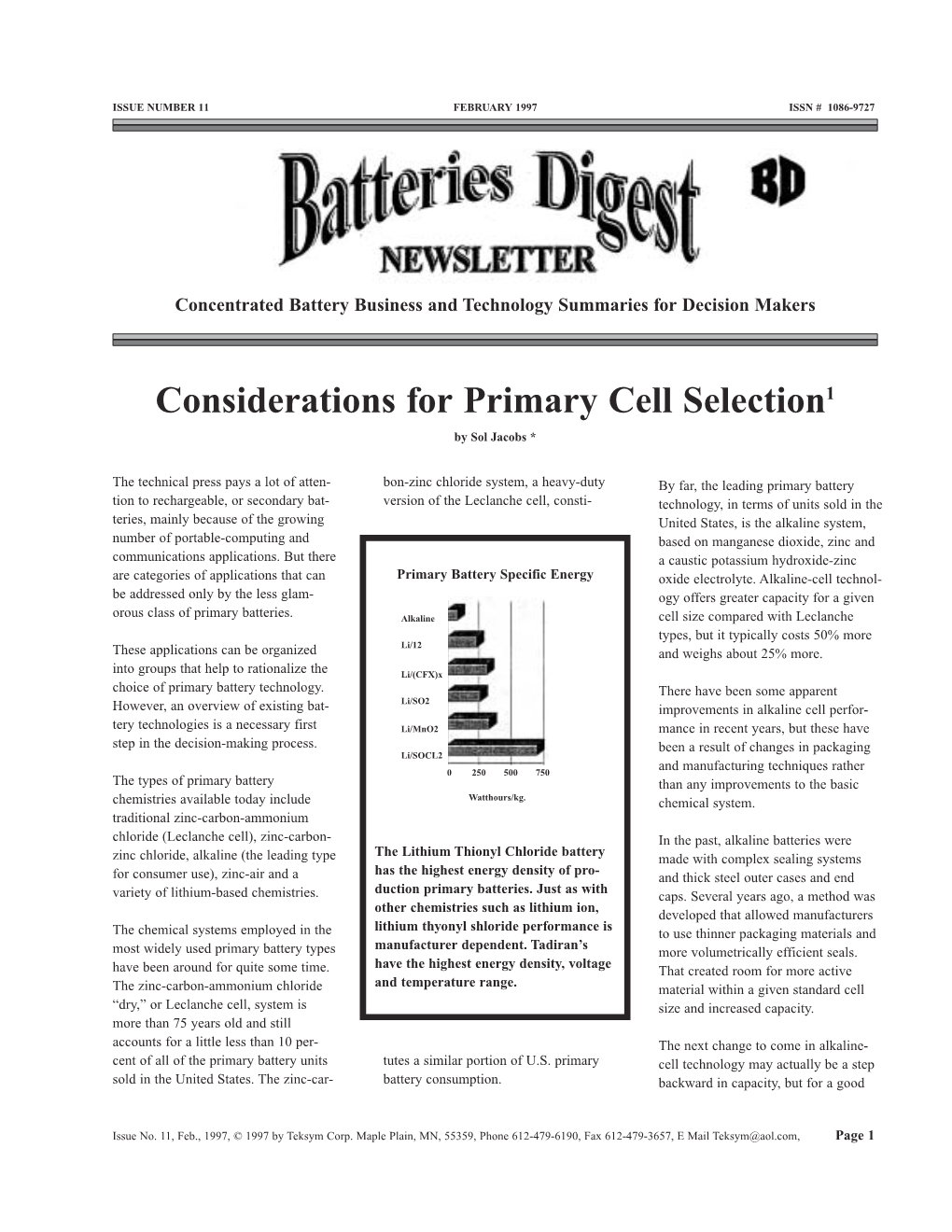
Load more
Recommended publications
-
Hydrogel Leclanché Cell: Construction and Characterization
energies Article Hydrogel Leclanché Cell: Construction and Characterization Greg Jenson 1,2,* , Gurjap Singh 2,3 , Jay K. Bhama 2,4,5 and Albert Ratner 2,3 1 Department of Surgery, University of Iowa Hospitals and Clinics, Iowa City, IA 52242, USA 2 Bhama-Ratner Artificial Heart & MCS Advancement Lab, University of Iowa Department of Mechanical Engineering, 3131 Seamans Ctr, Iowa City, IA 52242, USA; [email protected] (G.S.); [email protected] (J.K.B.); [email protected] (A.R.) 3 Department of Mechanical Engineering, University of Iowa, Iowa City, IA 52242, USA 4 Baptist Health Medical Center, Little Rock, AR 72205, USA 5 Division of Cardiovascular Surgery, University of Arkansas for Medical Sciences, University of Arkansas for Medical Sciences, 4301 W Markham, Little Rock, AR 72205, USA * Correspondence: [email protected] Received: 10 December 2019; Accepted: 21 January 2020; Published: 28 January 2020 Abstract: A liquid-to-gel based Leclanché cell has been designed, constructed and characterized for use in implantable medical devices and other applications where battery access is limited. This well-established chemistry will provide reliable electrochemical potential over a wide range of applications and the novel construction provides a solution for the re-charging of electrodes in hard to access areas such as an internal pacemaker. The traditional Leclanché cell, comprised of zinc (anode) and manganese dioxide (cathode), conductive carbon powder (acetylene black or graphite), and aqueous electrolyte (NH4Cl and ZnCl2), has been suspended in an agar hydrogel to simplify construction while maintaining electrochemical performance. Agar hydrogel, saturated with electrolyte, serves as the cell support and separator allowing for the discharged battery suspension to be easily replaced once exhausted. -
247. the Leclanche Cell Copy
Notes from the Oesper Collections The Leclanché Cell William B. Jensen Department of Chemistry, University of Cincinnati Cincinnati, OH 45221-0172 The previous three issues of Museum Notes have described the Edison nickel-iron alkaline storage cell (1), the Daniel gravity cell (2), and the Grove and Bun- sen cells (3) respectively. This issue will deal with yet a fifth cell of historical importance found among the collection of voltaic cells donated to the Oesper Col- lections some years ago by the Chemistry Department of Oberlin College – the primary Leclanché cell. First described by the French scientist, Georges Leclanché, (figure 1) in 1868 (4, 5), this cell is based on the net cell reaction: Zn(s) + 2MnO2(s) + 2(NH4)Cl(aq) + 2H2O(l) → ZnCl2(aq) + 2Mn(OH)3 + 2NH3(aq) + ΔEel in which Zn(0) is oxidized to Zn(II) at the anode, Mn(IV) is reduced to Mn(III) at the cathode, and the resulting net cell potential is roughly 1.4 V. Figure 1. A portrait medallion commemorating Georges Like the Edison cell described earlier, the Leclan- Leclanché (1838-1882). ché cell was a single-fluid system that employed a saturated aqueous solution of ammonium chloride [(NH4)Cl] as the electrolyte. As originally conceived, the MnO2(s) and an inert rectangular carbon cathode came sealed in a large porous ceramic spacer (figures 2-3) and the Zn anode as a separate rod. Both of these were placed in a large rectangular glass battery jar and the jar half-filled with the (NH4)Cl(aq) electrolyte. To increase the conductivity of the MnO2(s), it was in- termixed with an equal quantity of powdered carbon. -
On Manganese (IV) Oxide (Mno2) in a Leclanche Dry Cell
Available online a t www.pelagiaresearchlibrary.com Pelagia Research Library Der Chemica Sinica, 2012, 3(1):182-191 ISSN: 0976-8505 CODEN (USA) CSHIA5 2+ Adsorption of zinc ion (Zn ) on manganese (IV) oxide (MnO 2) in a leclanche dry cell Adejoh Adu Zakariah* and Aloko Duncan Folorunsho Department of Chemical Engineering, University of Abuja, Nigeria _____________________________________________________________________________________________ ABSTRACT This work was carried out to study the adsorption of zinc nitrate (Zn(NO 3)2) on manganese (IV) oxide (MnO 2) in a leclanche dry cell. The aim of the study is to optimize the process for the adsorption of zinc ion on MnO 2 in a leclanche dry cell using a second order factorial method. Potentiometric titration method was the adsorption method used. Considering the temperature effect on electric surface charge, pH respond during titration, concentration effect on adsorption and surface charge and the nature of cation, results obtain show that adsorption is inversely proportional to temperature, in other words, as temperature of cation increases, the adsorption capacity on MnO 2 decreases at a given concentration. Also at a given temperature adsorption capacity increases as the concentration of the adsorbent increases. The highest adsorption capacity was observed at 0.1M for Zn 2+ at 28 oC . Key words : Adsorption, zinc nitrate (Zn(NO 3)2), manganese (IV) oxide, potentiometric, concentration, adsorbent. _____________________________________________________________________________________________ INTRODUCTION An electrochemical cell is a device designed to produce electrical energy as the primary output product with the cell itself undergoing a chemical transformation (reaction). Conversely, in cell some chemical reaction can be made to occur through ionic mechanism by passing electric energy into the cell (as a form of secondary input). -
Introduction to Batteries
Introduction to Batteries Course No: E03-002 Credit: 3 PDH A. Bhatia Continuing Education and Development, Inc. 22 Stonewall Court Woodcliff Lake, NJ 07677 P: (877) 322-5800 [email protected] CHAPTER 2 BATTERIES LEARNING OBJECTIVES Upon completing this chapter, you will be able to: 1. State the purpose of a cell. 2. State the purpose of the three parts of a cell. 3. State the difference between the two types of cells. 4. Explain the chemical process that takes place in the primary and secondary cells. 5. Recognize and define the terms electrochemical action, anode, cathode, and electrolyte. 6. State the causes of polarization and local action and describe methods of preventing these effects. 7. Identify the parts of a dry cell. 8. Identify the various dry cells in use today and some of their capabilities and limitations. 9. Identify the four basic secondary cells, their construction, capabilities, and limitations. 10. Define a battery, and identify the three ways of combining cells to form a battery. 11. Describe general maintenance procedures for batteries including the use of the hydrometer, battery capacity, and rating and battery charging. 12. Identify the five types of battery charges. 13. Observe the safety precautions for working with and around batteries. INTRODUCTION The purpose of this chapter is to introduce and explain the basic theory and characteristics of batteries. The batteries which are discussed and illustrated have been selected as representative of many models and types which are used in the Navy today. No attempt has been made to cover every type of battery in use, however, after completing this chapter you will have a good working knowledge of the batteries which are in general use. -
Evaluation of Rapid Electric Battery Charging Techniques
UNLV Theses, Dissertations, Professional Papers, and Capstones 2009 Evaluation of rapid electric battery charging techniques Ronald Baroody University of Nevada Las Vegas Follow this and additional works at: https://digitalscholarship.unlv.edu/thesesdissertations Part of the Power and Energy Commons Repository Citation Baroody, Ronald, "Evaluation of rapid electric battery charging techniques" (2009). UNLV Theses, Dissertations, Professional Papers, and Capstones. 156. http://dx.doi.org/10.34917/1392506 This Thesis is protected by copyright and/or related rights. It has been brought to you by Digital Scholarship@UNLV with permission from the rights-holder(s). You are free to use this Thesis in any way that is permitted by the copyright and related rights legislation that applies to your use. For other uses you need to obtain permission from the rights-holder(s) directly, unless additional rights are indicated by a Creative Commons license in the record and/ or on the work itself. This Thesis has been accepted for inclusion in UNLV Theses, Dissertations, Professional Papers, and Capstones by an authorized administrator of Digital Scholarship@UNLV. For more information, please contact [email protected]. EVALUATION OF RAPID ELECTRIC BATTERY CHARGING TECHNIQUES By Ronald Baroody Bachelor of Science University of Nevada, Las Vegas 2005 A thesis submitted in partial fulfillment of the requirements for the Master of Science in Engineering Department of Electrical and Computer Engineering Howard R. Hughes College of Engineering Graduate -
A Mathematical Model of a Lithium/Thionyl Chloride Primary Cell T
University of South Carolina Scholar Commons Faculty Publications Chemical Engineering, Department of 1989 A Mathematical Model of a Lithium/Thionyl Chloride Primary Cell T. I. Evans Texas A & M University - College Station T. V. Nguyen Texas A & M University - College Station Ralph E. White University of South Carolina - Columbia, [email protected] Follow this and additional works at: https://scholarcommons.sc.edu/eche_facpub Part of the Chemical Engineering Commons Publication Info Journal of the Electrochemical Society, 1989, pages 328-339. © The Electrochemical Society, Inc. 1989. All rights reserved. Except as provided under U.S. copyright law, this work may not be reproduced, resold, distributed, or modified without the express permission of The Electrochemical Society (ECS). The ra chival version of this work was published in the Journal of the Electrochemical Society. http://www.electrochem.org/ DOI: 10.1149/1.2096630 http://dx.doi.org/10.1149/1.2096630 This Article is brought to you by the Chemical Engineering, Department of at Scholar Commons. It has been accepted for inclusion in Faculty Publications by an authorized administrator of Scholar Commons. For more information, please contact [email protected]. 328 J. Electrochem. Soc., Vol. 136, No. 2, February 1989 The Electrochemical Society, Inc. Table A-I. Concentration, density, and mole fraction of LiAICI4-SOCI2 (p +_ 0.0001) = (0.594484 • 0.000934). XLjAlCI4 solutions at 25~ based on the experiment of Venkatasetty and Saathoff (5) + (1.64388 --+ 0.00004) (R 2 = 0.99997) These lines are valid in the range 0 < XLIA~C14< 0.11, 0 < C Concentration Density < 1.50 mol/liter and 1.64 < p < 1.71 g/cm ~ and at 25~ At (mol/liter) (g/cm~) XLiAIC14a higher concentrations linear extrapolation cannot be done with confidence. -
Development of Cathode Materials for Magnesium Primary Cell K
View metadata, citation and similar papers at core.ac.uk brought to you by CORE provided by KnowledgeCuddle Publication (E-Journals) International Journal of Research in Advance Engineering, (IJRAE) Vol. 2, Issue 5, Sep-Oct-2016, Available at: www.knowledgecuddle.com/index.php/IJRAE Development of cathode materials for magnesium primary cell K. Narthana1, M. Selvam1, K. Saminathan, V. Rajendran and Karan V.I.S. Kaler2 aCentre for nano science and technology, K S Rangasamy College of technology, Tiruchengode -637 215, Tamil Nadu, India bSchulich School of Engineering , Department of Electrical and Computer Engineering, University of Calgary, Calgary, Alberta, Canada. Abstract: The Zinc Sulfide nanoparticles were synthesized by simple chemical reaction of ZnCl2 and Sulphur powder in aqueous solution. The main advantage of this method is the use of non-toxic precursors and water as solvent. The BZ1 and NZ2 samples reveal an average particle size respectively 510 and 43.7 nm. The structural, morphological, chemical composition and optical properties of the nanoparticles were investigated by X-ray diffraction, Scanning electron Microscopy, and Energy-dispersive X-ray Spectroscopy, Ultra Violet Spectroscopy and Electrochemical studies. The NZ2 sample showed a high discharge capacity of 362 mAh g -1, whereas the BZ1 sample showed a discharge capacity of 120 mAh g -1. The discharge capacity of NZ2 sample based cathode was 33.1 % higher than BZ1 sample based cathode. Thus, the above studies confirm that zinc sulfide nano powders show promise application as a cathode material for Mg/ZnS primary cell. Key words: BZ1 sample, NZ2 sample, Discharge capacity, Electro chemical studies, Band gap *Corresponding author: [email protected] I. -
Battery Recycling: Defining the Market and Identifying the Technology Required to Keep High Value Materials in the Economy and out of the Waste Dump
Battery Recycling: defining the market and identifying the technology required to keep high value materials in the economy and out of the waste dump By Timothy W. Ellis Abbas H. Mirza Page 1 of 33 Introduction: The accumulation of post consumer non-Lead/Acid batteries and electrochemical (n-PbA) cells has been identified as a risk in the waste stream of modern society. The n-PbA’s contain material that is environmentally unsound for disposal; however, do represent significant values of materials, e.g. metals, metal oxides, and carbon based material, polymers, organic electrolytes, etc. The desire is to develop systems whereby the nPbA’s are reprocessed in a hygienic and environmentally astute manner which returns the materials within the n-PbA’s to society in an economically and environmentally safe and efficient manner. According to information published in the Fact File on the “Recycling of Batteries” by the Institution of Engineering and Technology (www.theiet.org) the following, Table 1, describes the recycling market. Table 1: Recoverable Metals from Various Battery Types Battery Type Recycling Alkaline & Zinc Carbon Recycled in the metals industry to recover steel, zinc, ferromanganese Nickel – (Cadmium, Metal Hydride) Recycled to recover Cadmium and Nickel with a positive market value Li-Ion Recycled to recover Cobalt with a positive market value Lead-Acid Recycled in Lead industry with a positive market value Button Cells Silver is recovered and has a positive market value; Mercury is recovered by vacuum thermal processes A literature search on “Recycling and Battery” on the STN Easy data base produced over 2500 hits. -
Electric Current Is a Flow of Charge
Page 1 of 7 KEY CONCEPT Electric current is a flow of charge. BEFORE, you learned NOW, you will learn • Charges move from higher to • About electric current lower potential • How current is related to • Materials can act as conductors voltage and resistance or insulators • About different types of • Materials have different levels electric power cells of resistance VOCABULARY EXPLORE Current electric current p. 28 How does resistance affect the flow of charge? ampere p. 29 Ohm’s law p. 29 PROCEDURE MATERIALS electric cell p. 31 • pencil lead 1 Tape the pencil lead flat on the posterboard. • posterboard 2 Connect the wires, cell, bulb, and bulb • electrical tape holder as shown in the photograph. • 3 lengths of wire 3 Hold the wire ends against the pencil lead • D cell battery about a centimeter apart from each other. • flashlight bulb Observe the bulb. • bulb holder 4 Keeping the wire ends in contact with the lead, slowly move them apart. As you move the wire ends apart, observe the bulb. WHAT DO YOU THINK? • What happened to the bulb as you moved the wire ends apart? • How might you explain your observation? Electric charge can flow continuously. Static charges cannot make your television play. For that you need a different type of electricity. You have learned that a static charge contains a specific, limited amount of charge. You have also learned that a static charge can move and always moves from higher to lower VOCABULARY potential. However, suppose that, instead of one charge, an electrical Don’t forget to make a four square diagram for the pathway received a continuous supply of charge and the difference in term electric current. -