Preparation and Processing of Doped Aln Nanopowders
Total Page:16
File Type:pdf, Size:1020Kb
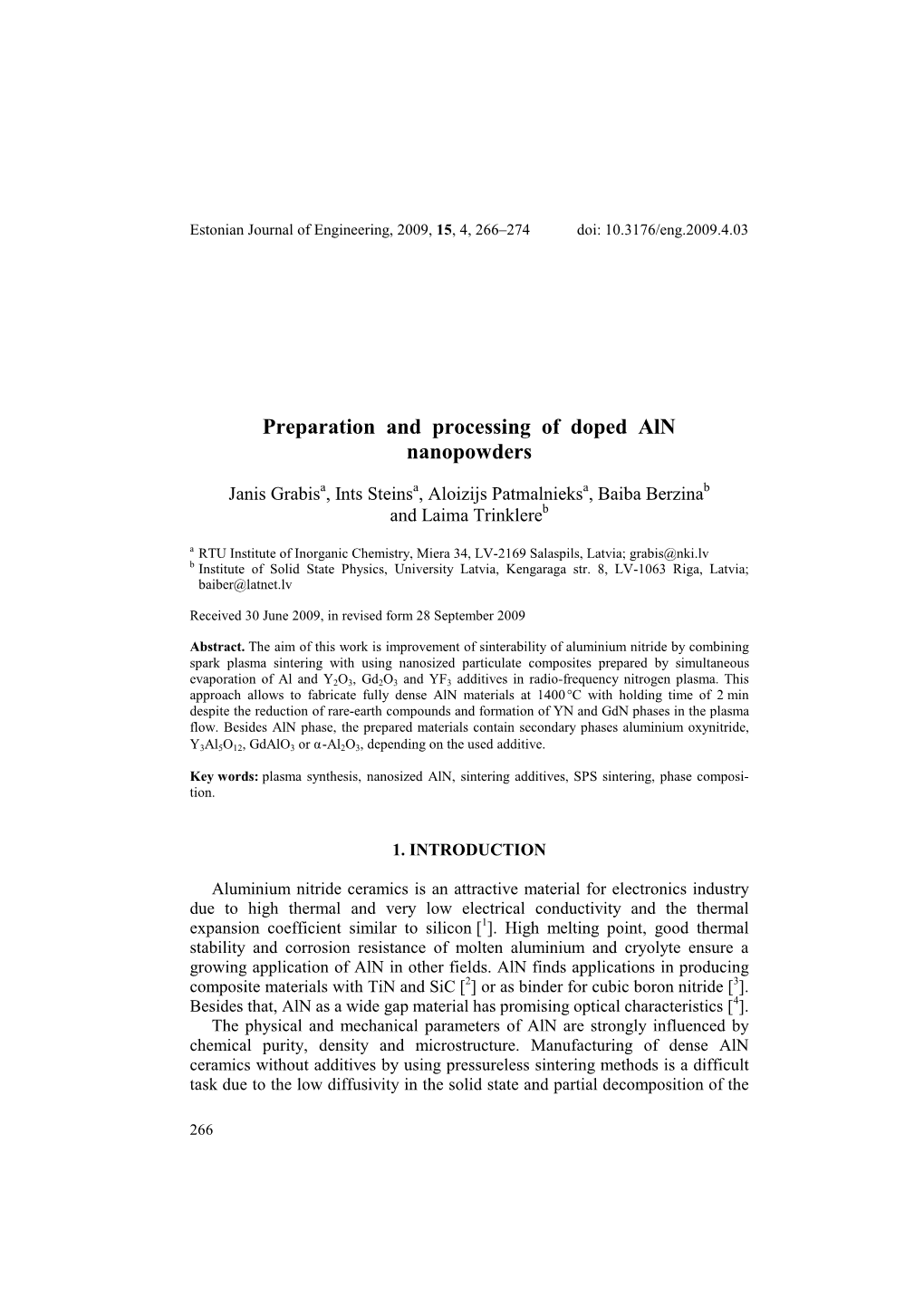
Load more
Recommended publications
-
1 Penetration of a Glass-Faced Transparent
Int. J. Impact Engng., 36 (1) pp. 147-153 (2009) PENETRATION OF A GLASS-FACED TRANSPARENT ELASTOMERIC RESIN BY A LEAD-ANTIMONY-CORED BULLET P J Hazell1*, M R Edwards1, H Longstaff1 and J Erskine2 1Cranfield University, Defence College of Management and Technology, Shrivenham, Oxfordshire, SN6 8LA, United Kingdom. 2Hamilton Erskine Ltd, 17 Moss Road, Ballygowan, Co. Down, BT23 6JQ, Northern Ireland. * Corresponding author SUMMARY The penetration of the lead antimony-cored 7.62 mm × 51 mm bullet into a glass-faced polyurethane elastomeric polymer resin has been studied. The resulting craters in the resin contained elongated bullet core material that had a significant amount of porosity. A simple linear viscoelastic model was applied to AUTODYN- 2D to describe the behaviour of the resin and numerical results of the penetration mechanism and depth-of-penetration appeared to match experimental observations well. Analysis of the high-speed photography and a numerical model of this bullet penetrating a viscoelastic polymer showed that during the initial stages of penetration, the projectile is essentially turned inside-out. Furthermore, the shape of the cavity was defined by the elastic relaxation of the polymer that led to compression of the core material. A weight analysis of the penetrated materials showed that using a thicker tile of glass resulted in better ballistic performance. Keywords: lead-antimony-cored bullet, penetration mechanisms, elastomeric resin, transparent armour, numerical modelling. 1 Int. J. Impact Engng., 36 (1) pp. 147-153 (2009) INTRODUCTION Armour systems usually consist of a hard disrupting face and some kind of absorbing element behind. The purpose of the disruptor is to induce fragmentation in the projectile or induce erosion thereby redirecting and dispersing the kinetic energy. -
09 S Bandyopadhyay.Pmd
ARTICLE TRANSPARENT CERAMICS S. BANDYOPADHYAY* AND R. HALDER* Transmission Through Material ight is electromagnetic radiation (EMR) that consists of a broad spectrum of wavelengths ranging from Lultraviolet (UV) to infrared (IR). So far as the sense of sight in human eyes is concerned, light is categorized into two groups- the visible part of EMR with wavelength from 400-700 nm that enables human-being to see. EM spectrum shorter (UV) or longer (IR) than the wave lengths of the visible range is invisible. When light interact any material medium, it may undergo several changes along its path, resulting in several optical phenomena to take Fig. 1. Interaction of light with matter place. The electronic structure, surface property and Transparent Materials in Common Practice microstructure of the medium guide these optical phenomena. The incident energy may partly or fully be The most common experience on transparent medium lost in certain cases. Light may bounce off any object for us is the natural atmosphere (gaseous) or clean water surface (reflection). Photons of appropriate energy may (liquid). Besides the natural resources, artificially made spontaneously be emitted out when electrons return to the silicate-based super cooled liquid with short ranged ground state after being promoted to the excited state by structure, called glass is the most widely used transparent absorbing photons of different incoming frequency materials those pass large quantities of light through them (luminescence). The incident energy may also scatter with little absorption and reflection. Because of its superior because of variation of refractive index within the medium, transmission property in the visible range glass is therefore usually resulted from the presence of impurities, defects, universally used as structural components like door and pores and inhomogeneities in the medium. -
Combustion Synthesis of Aluminum Oxynitride in Loose Powder Beds
materials Article Combustion Synthesis of Aluminum Oxynitride in Loose Powder Beds Alan Wilma ´nski*, Magdalena Zarzecka-Napierała and Zbigniew P˛edzich* Faculty of Materials Science and Ceramics, AGH University of Science and Technology, 30 Mickiewicz Av., 30-059 Kraków, Poland; [email protected] * Correspondence: [email protected] (A.W.); [email protected] (Z.P.) Abstract: This paper describes combusting loose powder beds of mixtures of aluminum metal powders and aluminum oxide powders with various grain sizes under various nitrogen pressure. The synthesis conditions required at least 20/80 weight ratio of aluminum metal powder to alumina powder in the mix to reach approximately 80 wt% of γ-AlON in the products. Finely ground fused white alumina with a mean grain size of 5 µm was sufficient to achieve results similar to very fine alumina with 0.3 µm grains. A lower nitrogen pressure of 1 MPa provided good results, allowing a less robust apparatus to be used. The salt-assisted combustion synthesis upon addition of 10 wt% of ammonium nitrite resulted in a slight increase in product yield and allowed lower aluminum metal powder content in mixes to be ignited. Increasing the charge mass five times resulted in a very similar γ-AlON yield, providing a promising technology for scaling up. Synthesis in loose powder beds could be utilized for effective production of relatively cheap and uniform AlON powder, which could be easily prepared for forming and sintering without intensive grounding and milling, which usually introduce serious contamination. Keywords: aluminum oxynitride; combustion synthesis; salt-assisted; SHS; AlON Citation: Wilma´nski,A.; Zarzecka-Napierała, M.; P˛edzich,Z. -
Valpos As Efficient Catalysts for Glycerol Conversion to Methanol
catalysts Article VAlPOs as Efficient Catalysts for Glycerol Conversion to Methanol 1, , 2, 2 2 Gheorghit, a Mitran * y, Florentina Neat, u y,S, tefan Neat, u , Mihaela M. Trandafir and Mihaela Florea 1,2,* 1 Department of Organic Chemistry, University of Bucharest, Biochemistry & Catalysis, Faculty of Chemistry, 4-12, Blv. Regina Elisabeta, 030018 Bucharest, Romania 2 National Institute of Material Physics, 405A Atomi¸stilor, P.O. Box MG 7, 077125 Măgurele, Romania; florentina.neatu@infim.ro (F.N.); stefan.neatu@infim.ro (S, .N.); mihaela.trandafir@infim.ro (M.M.T.) * Correspondence: [email protected] (G.M.); mihaela.florea@infim.ro (M.F.) Authors with equal contribution. y Received: 24 April 2020; Accepted: 28 June 2020; Published: 1 July 2020 Abstract: The catalytic activity of a series of vanadium aluminophosphates catalysts prepared by sol-gel method followed by combustion of the obtained gel was evaluated in glycerol conversion towards methanol. The materials were characterized by several techniques such as X-ray diffraction (XRD), UV-vis, Fourier-transform infrared (FTIR), Raman and X-ray photoelectron (XPS) spectroscopies. The amount of vanadium incorporated in aluminophosphates framework played an important role in the catalytic activity, while in the products distribution the key role is played by the vanadium oxidation state on the surface. The sample that contains a large amount of V4+ has the highest selectivity towards methanol. On the sample with the lowest vanadium loading the oxidation path to dihydroxyacetone is predominant. The catalyst with higher content of tetrahedral isolated vanadium species, such V5APO, is less active in breaking the C–C bonds in the glycerol molecule than the one containing polymeric species. -
Transparent Ballistic Armour Ceramics. Recent Advances and Issues to Be Overcome
Transparent ballistic armour ceramics. Recent advances and issues to be overcome Felipe Orgaz Instituto de Ceramica y Vidrio, CSIC, Spain Transparent armour is a system designed to be -Transparent ceramics offer significant ballistic optically transparent to support dynamic protection in relation to conventional glass/plastic fragmentation when subjected to the high strain systems. A few companies produce this kind of rates produced by ballistic impacts. They are mainly products: Surmet (ALON® technology), Armorline used to protect vehicle occupants from terrorist (Spinel), Saint Gobain Group (Sapphire), Technology actions and other hostile conflicts, as visors for non- Assessment and Transfer (TA&T) (Spinel). For combat use like riot control or explosive actions, etc. technology transfer: Fraunhofer Institut (IKTS). Light weight, small thickness, low optical distortion, compatibility with night vision equipment and multi Some issues must be overcome: commercial hit capability are needed to defeat armour piercing availability, very high cost raw materials, high ammunitions (AP) threats. These systems consist of investments, complex processing techniques (hot a sandwich structure with a hard front layer of pressing, hot isostatic pressing, Spark Plasma transparent ceramic joined to several plies of glass Sintering), machining and polishing costs, large with polymer inter layers and polycarbonate formats and curved shapes, new structural designs backing. Advances in material science and for multi hit capability, etc technology over the last 40 years has made available sub-μm grain size polycrystalline α- Al2O3 -Several programs are investigating for cost aluminium oxynitride (AlON) , magnesium aluminate reduction, new processing ways and scale up of spinel (MgAl2O4)3 and these materials: As strategies are proposed: single crystal sapphire (Al2O3) as alternative ceramic Conventional pressureless sintering, gel casting, materials able to satisfy the requirements of nanotechnology, nanocomposite optical ceramics transparency and hardness for armours application. -
Two-Step Preparation of Alon Transparent Ceramics with Powder Synthesized by Aluminothermic Reduction and Nitridation Method
Two-step preparation of AlON transparent ceramics with powder synthesized by aluminothermic reduction and nitridation method Ying Wang College of Physical Science and Technology, Sichuan University, Chengdu 610064, Sichuan, People’s Republic of China; and Key Laboratory of High Energy Density Physics of Ministry of Education, Sichuan University, Chengdu 610064, Sichuan, People’s Republic of China Xiumin Xie College of Physical Science and Technology, Sichuan University, Chengdu 610064, Sichuan, People’s Republic of China; and Key Laboratory of Radiation Physics and Technology of Ministry of Education, Sichuan University, Chengdu 610064, Sichuan, People’s Republic of China Jianqi Qia) College of Physical Science and Technology, Sichuan University, Chengdu 610064, Sichuan, People’s Republic of China; and Key Laboratory of High Energy Density Physics of Ministry of Education, Sichuan University, Chengdu 610064, Sichuan, People’s Republic of China Jun Wang School of Science, Sichuan University of Science and Engineering, Zigong 643000, Sichuan, People’s Republic of China Di Wu and Xiaofeng Guo Peter A. Rock Thermochemistry Laboratory and NEAT ORU, University of California, Davis, California 95616, USA Nian Wei College of Physical Science and Technology, Sichuan University, Chengdu 610064, Sichuan, People’s Republic of China; and Key Laboratory of High Energy Density Physics of Ministry of Education, Sichuan University, Chengdu 610064, Sichuan, People’s Republic of China Tiecheng Lub) College of Physical Science and Technology, Sichuan University, Chengdu 610064, Sichuan, People’s Republic of China; and International Center for Material Physics, Chinese Academy of Sciences, Shenyang 110015, Liaoning, People’s Republic of China (Received 15 April 2014; accepted 11 August 2014) The aluminothermic reduction and nitridation method using microsized Al powder and nanosized alumina powder was employed to fabricate AlON powder under N2 atmosphere. -
A Study of Alkali-Resistant Materials for Use in Atomic Physics Based Systems
Wright State University CORE Scholar Browse all Theses and Dissertations Theses and Dissertations 2017 A Study of Alkali-Resistant Materials for Use in Atomic Physics Based Systems Aaron Thomas Fletcher Wright State University Follow this and additional works at: https://corescholar.libraries.wright.edu/etd_all Part of the Physics Commons Repository Citation Fletcher, Aaron Thomas, "A Study of Alkali-Resistant Materials for Use in Atomic Physics Based Systems" (2017). Browse all Theses and Dissertations. 1851. https://corescholar.libraries.wright.edu/etd_all/1851 This Thesis is brought to you for free and open access by the Theses and Dissertations at CORE Scholar. It has been accepted for inclusion in Browse all Theses and Dissertations by an authorized administrator of CORE Scholar. For more information, please contact [email protected]. A STUDY OF ALKALI-RESISTANT MATERIALS FOR USE IN ATOMIC PHYSICS BASED SYSTEMS A thesis submitted in partial fulfillment of the requirements for the degree of Master of Science By AARON THOMAS FLETCHER B.S., Wright State University, 2015 2017 Wright State University WRIGHT STATE UNIVERSITY GRADUATE SCHOOL July 24, 2017 I HEREBY RECOMMEND THAT THE THESIS PREPARED UNDER MY SUPERVISION BY Aaron Thomas Fletcher ENTITLED A Study of Alkali-Resistant Materials for Use in Atomic Physics Based Systems BE ACCEPTED IN PARTIAL FULFILLMENT OF THE REQUIREMENTS FOR THE DEGREE OF Master of Science. ___________________________ Gregory Kozlowski, Ph.D. Thesis Director _____________________________ Jason Deibel, Ph.D. Chair, Physics Department College of Science and Mathematics Committee on Final Examination ___________________________ Gregory Kozlowski, Ph.D. ___________________________ Steven Fairchild, Ph.D. ___________________________ David Turner, Ph.D. -
Salt-Assisted SHS Synthesis of Aluminium Nitride Powders for Refractory Applications
Journal of Materials Science and Chemical Engineering, 2014, 2, 26-31 Published Online October 2014 in SciRes. http://www.scirp.org/journal/msce http://dx.doi.org/10.4236/msce.2014.210004 Salt-Assisted SHS Synthesis of Aluminium Nitride Powders for Refractory Applications Alan Wilmański, Mirosław M. Bućko, Zbigniew Pędzich, Jacek Szczerba AGH University of Science and Technology, Faculty of Materials Science and Ceramics, Krakow, Poland Email: [email protected] Received July 2014 Abstract Powders of aluminum nitride can be prepared by self-sustain high-temperature synthesis (SHS) between aluminum and nitrogen but its high exothermic effect causes melting and evaporation of aluminum and low efficiency of such reaction. A presence of inorganic salt in the starting powder mixture can decrease a heat evolved in the SHS reaction, hinders melting and coalescence of alu- minum, and facilitates penetration of nitrogen into interior of a powder bed. Mixtures of alumina powders with different grain sizes and different amounts of aluminum carbonate were subjected to the SHS reaction under 0.05, 0.1 or 1 MPa nitrogen. The powders were composed of aluminum nitride, unreacted aluminum, aluminum oxynitride and in some cases corundum and aluminum oxycarbonate. The finale effects are strongly dependent on the amount of the salt, a grain size of aluminum and a nitrogen pressure. Keywords Aluminum Nitride, Self-Sustain High-Temperature Synthesis, Salt Assisted Synthesis, Refractory Materials 1. Introduction Aluminum nitride, AlN, is a promising ceramic material for functional and structural applications due to its very high thermal conductivity, low electrical conductivity, high flexural strength of about 400 MPa and a hardness of about 15 GPa [1]-[3]. -
A Study of the Mechanical Properties of Silicon-Based Thin Films
MECHANICAL PROPERTIES OF SILICON-BASED FILMS FABRICATED BY PECVD A STUDY OF THE MECHANICAL PROPERTIES OF SILICON-BASED THIN FILMS DEPOSITED BY ECR-PECVD AND ICP-CVD By OWEN TAGGART, B.ENG. A Thesis Submitted to the School of Graduate Studies in Partial Fulfillment of the Requirements for the Degree Master of Applied Science McMaster University © Copyright by Owen Taggart, April 2013 McMaster University MASTER OF APPLIED SCIENCE (2013) Hamilton, Ontario (Engineering Physics) Title: A Study of the Mechanical Properties of Silicon-Based Thin Films Deposited by ECR-PECVD and ICP-CVD AUTHOR: Owen Taggart SUPERVISOR: Professor Peter Mascher Number of pages: xv, 151 ii Abstract Silicon-based dielectric thin films including amorphous hydrogenated aluminium-doped silicon oxides (a-SiAlxOy:H), amorphous hydrogenated silicon nitrides (a-SiNx:H), and amorphous hydrogenated silicon carbides (a-SiCx:H) were deposited by remote plasma chemical vapour deposition (RPECVD) techniques including electron cyclotron resonance plasma enhanced chemical vapour deposition (ECR-PECVD) and inductively-coupled-plasma chemical vapour deposition (ICP-CVD) on silicon (Si) wafers, soda-lime glass microscope slides, and glassy carbon (C) plates. Aluminium (Al) in the SiAlO films was incorporated by way of a metalorganic Al(TMHD)3 precursor. Thickness, refractive index, and growth rate of the films were measured using variable angle spectroscopic ellipsometry (VASE). Film composition was measured using energy dispersive X-ray spectroscopy (EDX) for the SiAlO films and Rutherford backscattering spectrometry (RBS) for the SiCx films. Elastic modulus and hardness of the SiAlO and SiCx films were measured using nanoindentation and their adhesion was characterized via progressive load scratch testing. -
Aluminum Magnesium Oxynitride: a New Transparent Spine1 Ceramic
Journal of the European Ceramic Society 15 (1995) 249-254 0 1995 Elsevier Science Limited Printed in Great Britain. All rights reserved 0955-2219l95lS9.50 Aluminum Magnesium Oxynitride: A New Transparent Spine1 Ceramic Arielle Granon, Patrice Goeuriot & FranCois Thevenot Ecole Nationale Superieure des Mines de Saint-Etienne, 158 Cours Fauriel, 42 023 Saint-Etienne, France (Received 13 May 1994; revised version received 27 July 1994; accepted 1 August 1994) Abstract results were: (i) the control of the parasite reaction between AlN-MgO and AIN-MgAl,O,; (ii) the A pure and dense spine1 solid solution can be role of cationic vacancies of the intermediate obtained by reaction-sintering between alumina- aluminate of magnesium phase; and (iii) the morph- magnesia or aluminate ofmagnesium and aluminum ology role of the starting materials. nitride or oxynitride. The influence of post isostatic pressing on density, microstructure and transmit- 2 Experiments tance (visible-IR) is studied for dtflerent starting materials. Transmittances of 65 and 80% are Six compositions (A to F) with different starting obtained for a 6 mm thick sample in visible and materials (Table 1) were studied: alumina (a + y infra-red spectra, respectively. and y crystallographic forms), magnesium oxide or aluminate of magnesium, aluminum nitride 1 Introduction (commercial powder or obtained by nitridation of boehmite15), aluminum oxynitride (also obtained New technologies need optical materials with the by nitridation of boehmitei6) and MgAlON pow- best mechanical properties. Initially monocrys- der prepared in the laboratory. talline ceramics as quartz or sapphire were devel- Starting powders (samples A to E) were milled oped, and more recently polycrystalline ceramics with highly pure alumina balls in anhydrous ethyl like MgA12041m3and yA10Nh8 have been studied. -
1 Penetration of a Glass-Faced
CORE Metadata, citation and similar papers at core.ac.uk Provided by Cranfield CERES Int. J. Impact Engng., 36 (1) pp. 147-153 (2009) PENETRATION OF A GLASS-FACED TRANSPARENT ELASTOMERIC RESIN BY A LEAD-ANTIMONY-CORED BULLET P J Hazell1*, M R Edwards1, H Longstaff1 and J Erskine2 1Cranfield University, Defence College of Management and Technology, Shrivenham, Oxfordshire, SN6 8LA, United Kingdom. 2Hamilton Erskine Ltd, 17 Moss Road, Ballygowan, Co. Down, BT23 6JQ, Northern Ireland. * Corresponding author SUMMARY The penetration of the lead antimony-cored 7.62 mm × 51 mm bullet into a glass-faced polyurethane elastomeric polymer resin has been studied. The resulting craters in the resin contained elongated bullet core material that had a significant amount of porosity. A simple linear viscoelastic model was applied to AUTODYN- 2D to describe the behaviour of the resin and numerical results of the penetration mechanism and depth-of-penetration appeared to match experimental observations well. Analysis of the high-speed photography and a numerical model of this bullet penetrating a viscoelastic polymer showed that during the initial stages of penetration, the projectile is essentially turned inside-out. Furthermore, the shape of the cavity was defined by the elastic relaxation of the polymer that led to compression of the core material. A weight analysis of the penetrated materials showed that using a thicker tile of glass resulted in better ballistic performance. Keywords: lead-antimony-cored bullet, penetration mechanisms, elastomeric resin, transparent armour, numerical modelling. 1 Int. J. Impact Engng., 36 (1) pp. 147-153 (2009) INTRODUCTION Armour systems usually consist of a hard disrupting face and some kind of absorbing element behind. -
CHEMICAL VAPOUR DEPOSITION of the Al-O-N SYSTEM B
CHEMICAL VAPOUR DEPOSITION OF THE Al-O-N SYSTEM B. Aspar, B. Armas, C. Combescure, D. Thenegal To cite this version: B. Aspar, B. Armas, C. Combescure, D. Thenegal. CHEMICAL VAPOUR DEPOSITION OF THE Al-O-N SYSTEM. Journal de Physique IV Proceedings, EDP Sciences, 1991, 02 (C2), pp.C2-665-C2- 672. 10.1051/jp4:1991280. jpa-00249870 HAL Id: jpa-00249870 https://hal.archives-ouvertes.fr/jpa-00249870 Submitted on 1 Jan 1991 HAL is a multi-disciplinary open access L’archive ouverte pluridisciplinaire HAL, est archive for the deposit and dissemination of sci- destinée au dépôt et à la diffusion de documents entific research documents, whether they are pub- scientifiques de niveau recherche, publiés ou non, lished or not. The documents may come from émanant des établissements d’enseignement et de teaching and research institutions in France or recherche français ou étrangers, des laboratoires abroad, or from public or private research centers. publics ou privés. JOURNAL DE PHYSIQUE IV C2-665 Colloque C2, suppl. au Journal de Physique 11, Vol. 1, septembre 1991 CHEMICAL VAPOUR DEPOSITION OF THE A1-0-N SYSTEM B. ASPAR, B. ARMAS, C. COMBESCURE and D. THENEGAL Institut de Science et de Genie des Materiaux et ProcBdBs, C.N..R.S, BP 5, F-66120 Font Romeu, Odeillo, France ABSTRACT - Using chemical vapour deposition, aluminium - oxygen- nitrogen coatings have been synthesized with aluminium trichloride, hydrogen, ammonia and nitrous oxide. The composition of the equilibrium phases is first determined by a thermodynamic calculation. The only AlON phase we investigate is (y) spinel aluminium oxynitride and it is considered as a stoichiometric phase with a composition of Al,O,N.