Benchmark on the 3D Numerical Modeling of a Superconducting Bulk
Total Page:16
File Type:pdf, Size:1020Kb
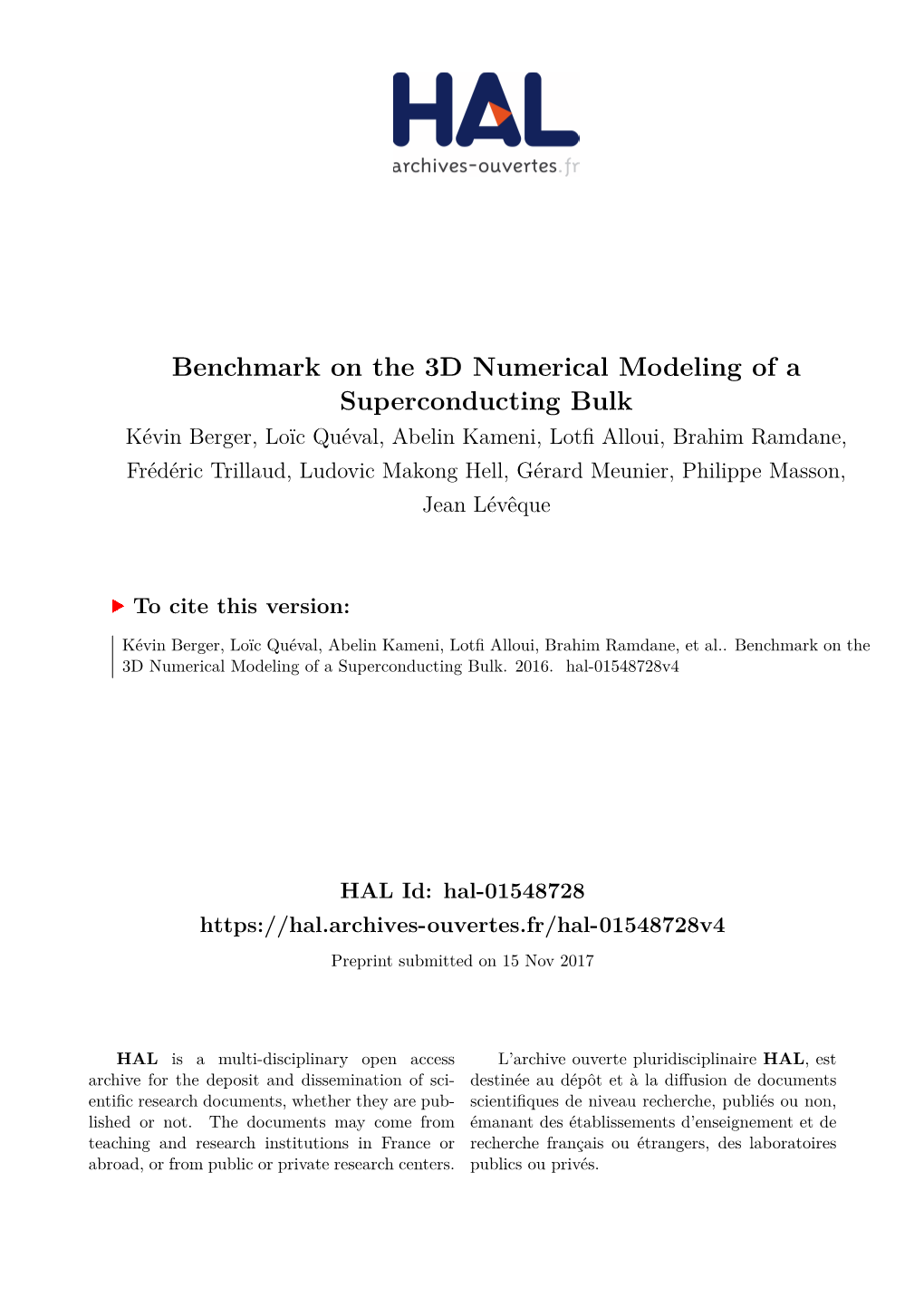
Load more
Recommended publications
-
Development of a Coupling Approach for Multi-Physics Analyses of Fusion Reactors
Development of a coupling approach for multi-physics analyses of fusion reactors Zur Erlangung des akademischen Grades eines Doktors der Ingenieurwissenschaften (Dr.-Ing.) bei der Fakultat¨ fur¨ Maschinenbau des Karlsruher Instituts fur¨ Technologie (KIT) genehmigte DISSERTATION von Yuefeng Qiu Datum der mundlichen¨ Prufung:¨ 12. 05. 2016 Referent: Prof. Dr. Stieglitz Korreferent: Prof. Dr. Moslang¨ This document is licensed under the Creative Commons Attribution – Share Alike 3.0 DE License (CC BY-SA 3.0 DE): http://creativecommons.org/licenses/by-sa/3.0/de/ Abstract Fusion reactors are complex systems which are built of many complex components and sub-systems with irregular geometries. Their design involves many interdependent multi- physics problems which require coupled neutronic, thermal hydraulic (TH) and structural mechanical (SM) analyses. In this work, an integrated system has been developed to achieve coupled multi-physics analyses of complex fusion reactor systems. An advanced Monte Carlo (MC) modeling approach has been first developed for converting complex models to MC models with hybrid constructive solid and unstructured mesh geometries. A Tessellation-Tetrahedralization approach has been proposed for generating accurate and efficient unstructured meshes for describing MC models. For coupled multi-physics analyses, a high-fidelity coupling approach has been developed for the physical conservative data mapping from MC meshes to TH and SM meshes. Interfaces have been implemented for the MC codes MCNP5/6, TRIPOLI-4 and Geant4, the CFD codes CFX and Fluent, and the FE analysis platform ANSYS Workbench. Furthermore, these approaches have been implemented and integrated into the SALOME simulation platform. Therefore, a coupling system has been developed, which covers the entire analysis cycle of CAD design, neutronic, TH and SM analyses. -
Livelink for MATLAB User's Guide
LiveLink™ for MATLAB® User’s Guide LiveLink™ for MATLAB® User’s Guide © 2009–2020 COMSOL Protected by patents listed on www.comsol.com/patents, and U.S. Patents 7,519,518; 7,596,474; 7,623,991; 8,457,932;; 9,098,106; 9,146,652; 9,323,503; 9,372,673; 9,454,625, 10,019,544, 10,650,177; and 10,776,541. Patents pending. This Documentation and the Programs described herein are furnished under the COMSOL Software License Agreement (www.comsol.com/comsol-license-agreement) and may be used or copied only under the terms of the license agreement. COMSOL, the COMSOL logo, COMSOL Multiphysics, COMSOL Desktop, COMSOL Compiler, COMSOL Server, and LiveLink are either registered trademarks or trademarks of COMSOL AB. MATLAB and Simulink are registered trademarks of The MathWorks, Inc.. All other trademarks are the property of their respective owners, and COMSOL AB and its subsidiaries and products are not affiliated with, endorsed by, sponsored by, or supported by those or the above non-COMSOL trademark owners. For a list of such trademark owners, see www.comsol.com/trademarks. Version: COMSOL 5.6 Contact Information Visit the Contact COMSOL page at www.comsol.com/contact to submit general inquiries, contact Technical Support, or search for an address and phone number. You can also visit the Worldwide Sales Offices page at www.comsol.com/contact/offices for address and contact information. If you need to contact Support, an online request form is located at the COMSOL Access page at www.comsol.com/support/case. Other useful links include: • Support Center: www.comsol.com/support • Product Download: www.comsol.com/product-download • Product Updates: www.comsol.com/support/updates • COMSOL Blog: www.comsol.com/blogs • Discussion Forum: www.comsol.com/community • Events: www.comsol.com/events • COMSOL Video Gallery: www.comsol.com/video • Support Knowledge Base: www.comsol.com/support/knowledgebase Part number: CM020008 Contents Chapter 1: Introduction About This Product 12 Help and Documentation 14 Getting Help . -
The COMSOL Multiphysics Installation and Operations User's Guide
COMSOL Multiphysics ® Installation and Operations Guide VERSION 4.3 COMSOL Multiphysics Installation and Operations Guide 1998–2012 COMSOL Protected by U.S. Patents 7,519,518; 7,596,474; and 7,623,991. Patents pending. This Documentation and the Programs described herein are furnished under the COMSOL Software License Agreement (www.comsol.com/sla) and may be used or copied only under the terms of the license agree- ment. COMSOL, COMSOL Desktop, COMSOL Multiphysics, and LiveLink are registered trademarks or trade- marks of COMSOL AB. Other product or brand names are trademarks or registered trademarks of their respective holders. Version: May 2012 COMSOL 4.3 Contact Information Visit www.comsol.com/contact for a searchable list of all COMSOL offices and local representatives. From this web page, search the contacts and find a local sales representative, go to other COMSOL websites, request information and pricing, submit technical support queries, subscribe to the monthly eNews email newsletter, and much more. If you need to contact Technical Support, an online request form is located at www.comsol.com/support/contact. Other useful links include: • Technical Support www.comsol.com/support • Software updates: www.comsol.com/support/updates • Online community: www.comsol.com/community • Events, conferences, and training: www.comsol.com/events • Tutorials: www.comsol.com/products/tutorials • Knowledge Base: www.comsol.com/support/knowledgebase Part No. CM010002 Contents Chapter 1: Introduction General Tips 8 General System Requirements for Windows, Linux, or Mac Computers . 8 Hardware Parameters that Affect Performance . 9 COMSOL Release Notes . 9 Introduction to COMSOL Multiphysics and Online Help . 9 Technical Support . -
COMSOL Multiphysics®
COMSOL Multiphysics ® M ODEL L IBRARY V ERSION 3.5a How to contact COMSOL: Germany United Kingdom COMSOL Multiphysics GmbH COMSOL Ltd. Benelux Berliner Str. 4 UH Innovation Centre COMSOL BV D-37073 Göttingen College Lane Röntgenlaan 19 Phone: +49-551-99721-0 Hatfield 2719 DX Zoetermeer Fax: +49-551-99721-29 Hertfordshire AL10 9AB The Netherlands [email protected] Phone:+44-(0)-1707 636020 Phone: +31 (0) 79 363 4230 www.comsol.de Fax: +44-(0)-1707 284746 Fax: +31 (0) 79 361 4212 [email protected] [email protected] Italy www.uk.comsol.com www.comsol.nl COMSOL S.r.l. Via Vittorio Emanuele II, 22 United States Denmark 25122 Brescia COMSOL, Inc. COMSOL A/S Phone: +39-030-3793800 1 New England Executive Park Diplomvej 376 Fax: +39-030-3793899 Suite 350 2800 Kgs. Lyngby [email protected] Burlington, MA 01803 Phone: +45 88 70 82 00 www.it.comsol.com Phone: +1-781-273-3322 Fax: +45 88 70 80 90 Fax: +1-781-273-6603 [email protected] Norway www.comsol.dk COMSOL AS COMSOL, Inc. Søndre gate 7 10850 Wilshire Boulevard Finland NO-7485 Trondheim Suite 800 COMSOL OY Phone: +47 73 84 24 00 Los Angeles, CA 90024 Arabianranta 6 Fax: +47 73 84 24 01 Phone: +1-310-441-4800 FIN-00560 Helsinki [email protected] Fax: +1-310-441-0868 Phone: +358 9 2510 400 www.comsol.no Fax: +358 9 2510 4010 COMSOL, Inc. [email protected] Sweden 744 Cowper Street www.comsol.fi COMSOL AB Palo Alto, CA 94301 Tegnérgatan 23 Phone: +1-650-324-9935 France SE-111 40 Stockholm Fax: +1-650-324-9936 COMSOL France Phone: +46 8 412 95 00 WTC, 5 pl. -
Simulations of Contact Mechanics and Wear of Linearly Reciprocating Block-On-Flat Sliding Test
Simulations of contact mechanics and wear of linearly reciprocating block-on-flat sliding test André Rudnytskyj Mechanical Engineering, master's level (120 credits) 2018 Luleå University of Technology Department of Engineering Sciences and Mathematics Simulations of contact mechanics and wear of linearly reciprocating block-on-flat sliding test Andr´eRudnytskyj Master programme in Tribology of Surfaces and Interfaces - TRIBOS 4th ed. Enrollment Semester Autumn 2016. Department of Engineering Sciences and Mathematics Lule˚aUniversity of Technology ©Lule˚aUniversity of Technology, 2018. This document is freely available at www.ltu.se Preface This master’s thesis was carried out at the Division of Machine Elements, Depart- ment of Engineering Sciences and Mathematics of Lule˚aUniversity of Technology (LTU), in Sweden. It was made possible through the Joint Erasmus Mundus Mas- ter Course (EMMC) TRIBOS (Tribology of Surface and Interfaces), of which I took part in its 4th generation between the years of 2016 to 2018. I would like to thank the Education, Audiovisual and Culture Executive Agency (EACEA) of the European Union and the TRIBOS programme coordinators, pro- fessors, tutors, lecturers, and everyone involved in the programme from the Uni- versity of Leeds (UK), the University of Ljubljana (Slovenia), the University of Coimbra (Portugal), and Lule˚aUniversity of Technology (LTU) for their support inside and outside the classroom. I also thank the people directly involved in the development of the thesis for their helpful support and discussions throughout the time of this work. Andr´eRudnytskyj Lule˚a,June 2018 I Abstract The use of computational methods in tribology can be a valuable approach to deal with engineering problems, ultimately saving time and resources. -
Finite Element Method in Computer Simulation and Engineering
Finite Element Method in Computer Simulation and Engineering Dr. Anna A. Nasedkina [email protected] Institute of Mathematics, Mechanics and Computer Science Southern Federal University Outline of the lecture Computer Aided Engineering and Finite Element Analysis Main concepts of Finite Element Method Overview of Finite Element Software packages 2 Computer Aided Engineering and Finite Element Analysis 3 CAD/CAE/CAM CAD – CAE – CAM – Computer Aided Computer Aided Computer Aided Manufacturing Design Engineering 4 Role of simulation in Engineering: CAD example Boeing 777 First jetliner that is 100% digitally designed using 3D solid technology Throughout the design process, the airplane was "preassembled" on the computer, eliminating the need for a costly, full-scale mock-up (experimental model) $4 billion in CAD infrastructure CAD system: CATIA for design CAE system: ELFINI both by Dassault Systemes (France) 5 Role of simulation in Engineering: CAE example San Francisco Oakland Bay Bridge Seismic analysis of the bridge after the 1989 Loma Prieta earthquake Finite Element model of a section of the bridge subjected to an earthquake load CAE system: ADINA (USA, located in MA) 6 Flow diagram of computer simulation process 7 From physical system to mathematical modeling Idealization: mathematical model, which is an abstraction of physical reality. It is governed by partial differential equations. Modeling can be explicit and implicit. Discretization: numerical method, for example Finite Element Method. Solution: linear system -
INTRODUCTION to COMSOL Multiphysics Introduction to COMSOL Multiphysics
INTRODUCTION TO COMSOL Multiphysics Introduction to COMSOL Multiphysics © 1998–2017 COMSOL Protected by patents listed on www.comsol.com/patents, and U.S. Patents 7,519,518; 7,596,474; 7,623,991; 8,457,932; 8,954,302; 9,098,106; 9,146,652; 9,323,503; 9,372,673; and 9,454,625. Patents pending. This Documentation and the Programs described herein are furnished under the COMSOL Software License Agreement (www.comsol.com/comsol-license-agreement) and may be used or copied only under the terms of the license agreement. COMSOL, the COMSOL logo, COMSOL Multiphysics, COMSOL Desktop, COMSOL Server, and LiveLink are either registered trademarks or trademarks of COMSOL AB. All other trademarks are the property of their respective owners, and COMSOL AB and its subsidiaries and products are not affiliated with, endorsed by, sponsored by, or supported by those trademark owners. For a list of such trademark owners, see www.comsol.com/trademarks. Version: COMSOL 5.3a Contact Information Visit the Contact COMSOL page at www.comsol.com/contact to submit general inquiries, contact Technical Support, or search for an address and phone number. You can also visit the Worldwide Sales Offices page at www.comsol.com/contact/offices for address and contact information. If you need to contact Support, an online request form is located at the COMSOL Access page at www.comsol.com/support/case. Other useful links include: • Support Center: www.comsol.com/support • Product Download: www.comsol.com/product-download • Product Updates: www.comsol.com/support/updates •COMSOL Blog: www.comsol.com/blogs • Discussion Forum: www.comsol.com/community •Events: www.comsol.com/events • COMSOL Video Gallery: www.comsol.com/video • Support Knowledge Base: www.comsol.com/support/knowledgebase Part number: CM010004 Contents Introduction . -
COMSOL Multiphysics Version 4.3 Contains Many New Functions and Additions to the COMSOL Product Suite
COMSOL Multiphysics ® Release Notes VERSION 4.3 COMSOL Multiphysics Release Notes 1998–2012 COMSOL Protected by U.S. Patents 7,519,518; 7,596,474; and 7,623,991. Patents pending. This Documentation and the Programs described herein are furnished under the COMSOL Software License Agreement (www.comsol.com/sla) and may be used or copied only under the terms of the license agree- ment. COMSOL, COMSOL Desktop, COMSOL Multiphysics, and LiveLink are registered trademarks or trade- marks of COMSOL AB. Other product or brand names are trademarks or registered trademarks of their respective holders. Version: May 2012 COMSOL 4.3 Contact Information Visit www.comsol.com/contact for a searchable list of all COMSOL offices and local representatives. From this web page, search the contacts and find a local sales representative, go to other COMSOL websites, request information and pricing, submit technical support queries, subscribe to the monthly eNews email newsletter, and much more. If you need to contact Technical Support, an online request form is located at www.comsol.com/support/contact. Other useful links include: • Technical Support www.comsol.com/support • Software updates: www.comsol.com/support/updates • Online community: www.comsol.com/community • Events, conferences, and training: www.comsol.com/events • Tutorials: www.comsol.com/products/tutorials • Knowledge Base: www.comsol.com/support/knowledgebase Part No. CM010001 1 Release Notes COMSOL Multiphysics version 4.3 contains many new functions and additions to the COMSOL product suite. These Release Notes provide information regarding new functionality in existing products and an overview of new products. We have strived to achieve backward compatibility with the previous version and to include all functionality that is available there. -
INTRODUCTION to COMSOL Multiphysics Introduction to COMSOL Multiphysics
INTRODUCTION TO COMSOL Multiphysics Introduction to COMSOL Multiphysics © 1998–2020 COMSOL Protected by patents listed on www.comsol.com/patents, and U.S. Patents 7,519,518; 7,596,474; 7,623,991; 8,457,932; 9,098,106; 9,146,652; 9,323,503; 9,372,673; 9,454,625; 10,019,544; 10,650,177; and 10,776,541. Patents pending. This Documentation and the Programs described herein are furnished under the COMSOL Software License Agreement (www.comsol.com/comsol-license-agreement) and may be used or copied only under the terms of the license agreement. COMSOL, the COMSOL logo, COMSOL Multiphysics, COMSOL Desktop, COMSOL Compiler, COMSOL Server, and LiveLink are either registered trademarks or trademarks of COMSOL AB. All other trademarks are the property of their respective owners, and COMSOL AB and its subsidiaries and products are not affiliated with, endorsed by, sponsored by, or supported by those trademark owners. For a list of such trademark owners, see www.comsol.com/ trademarks. Version: COMSOL 5.6 Contact Information Visit the Contact COMSOL page at www.comsol.com/contact to submit general inquiries, contact Technical Support, or search for an address and phone number. You can also visit the Worldwide Sales Offices page at www.comsol.com/contact/offices for address and contact information. If you need to contact Support, an online request form is located at the COMSOL Access page at www.comsol.com/support/case. Other useful links include: • Support Center: www.comsol.com/support • Product Download: www.comsol.com/product-download • Product Updates: www.comsol.com/support/updates •COMSOL Blog: www.comsol.com/blogs • Discussion Forum: www.comsol.com/community •Events: www.comsol.com/events • COMSOL Video Gallery: www.comsol.com/video • Support Knowledge Base: www.comsol.com/support/knowledgebase Part number: CM010004 Contents Introduction . -
Livelink for PTC Creo Parametric User's Guide
LiveLink™ for PTC® Creo® Parametric™ User’s Guide LiveLink™ for PTC® Creo® Parametric™ User’s Guide © 2012–2018 COMSOL Protected by patents listed on www.comsol.com/patents, and U.S. Patents 7,519,518; 7,596,474; 7,623,991; 8,457,932; 8,954,302; 9,098,106; 9,146,652; 9,208,270; 9,323,503; 9,372,673; and 9,454,625. Patents pending. This Documentation and the Programs described herein are furnished under the COMSOL Software License Agreement (www.comsol.com/comsol-license-agreement) and may be used or copied only under the terms of the license agreement. Portions of this software are owned by Siemens Product Lifecycle Management Software Inc. © 1986–2018. All Rights Reserved. Portions of this software are owned by Spatial Corp. © 1989–2018. All Rights Reserved. COMSOL, the COMSOL logo, COMSOL Multiphysics, COMSOL Desktop, COMSOL Server, and LiveLink are either registered trademarks or trademarks of COMSOL AB. ACIS and SAT are registered trademarks of Spatial Corporation. CATIA is a registered trademark of Dassault Systèmes or its subsidiaries in the US and/or other countries. Parasolid is a trademark or registered trademark of Siemens Product Lifecycle Management Software Inc. or its subsidiaries in the United States and in other countries. PTC and Creo are trademarks or registered trademarks of PTC or its subsidiaries in the U.S. and in other countries. All other trademarks are the property of their respective owners, and COMSOL AB and its subsidiaries and products are not affiliated with, endorsed by, sponsored by, or supported by those or the above non-COMSOL trademark owners. -
University of California Riverside Fem
UNIVERSITY OF CALIFORNIA RIVERSIDE FEM Based Multiphysics Analysis of Electromigration Voiding Process in Nanometer Integrated Circuits A Dissertation submitted in partial satisfaction of the requirements for the degree of Doctor of Philosophy in Electrical Engineering by Hengyang Zhao December 2018 Dissertation Committee: Dr. Sheldon Tan, Chairperson Dr. Daniel Wong Dr. Jianlin Liu Copyright by Hengyang Zhao 2018 The Dissertation of Hengyang Zhao is approved: Committee Chairperson University of California, Riverside Acknowledgments This thesis could not have been completed without the great support that I have received from so many people over the years. I wish to offer my most heartful thanks to the following people. I would like to thank my advisor, Dr. Sheldon Tan for guiding and supporting me over the years. Dr. Tan is a great example of excellence as a researcher, a mentor, an instructor and most importantly a scholar persuing rigours theorems. His kindness, insight and suggestions always guide me to the right direction. I would like to thank my committee members, Dr. Daniel Wong and Dr. Jianlin Liu for their direction, dedication and invaluable advice. I would like to thank all the members in our VSCLAB, especially Chase Cook, Haibao Chen, Han Zhou, Jinwei Zhang, Kai He, Lebo Wang, Shaoyi Peng, Sheriff Sadiq- batcha, Shuyuan Yu, Taeyoung Kim, Wentian Jin, Yan Zhu, Yue Zhao, and Zeyu Sun, for the collaborative research works, discussion and help, which lead to the presented work in this thesis. I appreciate the friendship of my fellow students in UCR. I would like to thank my friend Daniel Quach, my first good friend in the United States, who took great efforts to help me to settle down and fit in the new Ph.D. -
COMSOL Release Notes
COMSOL Multiphysics Release Notes © 1998–2020 COMSOL Protected by patents listed on www.comsol.com/patents, and U.S. Patents 7,519,518; 7,596,474; 7,623,991; 8,219,373; 8,457,932; 9,098,106; 9,146,652; 9,323,503; 9,372,673; 9,454,625; 10,019,544; 10,650,177; and 10,776,541. Patents pending. This Documentation and the Programs described herein are furnished under the COMSOL Software License Agreement (www.comsol.com/comsol-license-agreement) and may be used or copied only under the terms of the license agreement. Support for implementation of the ODB++ Format was provided by Mentor Graphics Corporation pursuant to the ODB++ Solutions Development Partnership General Terms and Conditions. ODB++ is a trademark of Mentor Graphics Corporation. COMSOL, the COMSOL logo, COMSOL Multiphysics, COMSOL Desktop, COMSOL Compiler, COMSOL Server, and LiveLink are either registered trademarks or trademarks of COMSOL AB. All other trademarks are the property of their respective owners, and COMSOL AB and its subsidiaries and products are not affiliated with, endorsed by, sponsored by, or supported by those trademark owners. For a list of such trademark owners, see www.comsol.com/trademarks. Version: COMSOL 5.6 Contact Information Visit the Contact COMSOL page at www.comsol.com/contact to submit general inquiries, contact Technical Support, or search for an address and phone number. You can also visit the Worldwide Sales Offices page at www.comsol.com/contact/offices for address and contact information. If you need to contact Support, an online request form is located at the COMSOL Access page at www.comsol.com/support/case.