Research on Lubrication Model of Rock Bit Bearings with Non-Newtonian Medium*
Total Page:16
File Type:pdf, Size:1020Kb
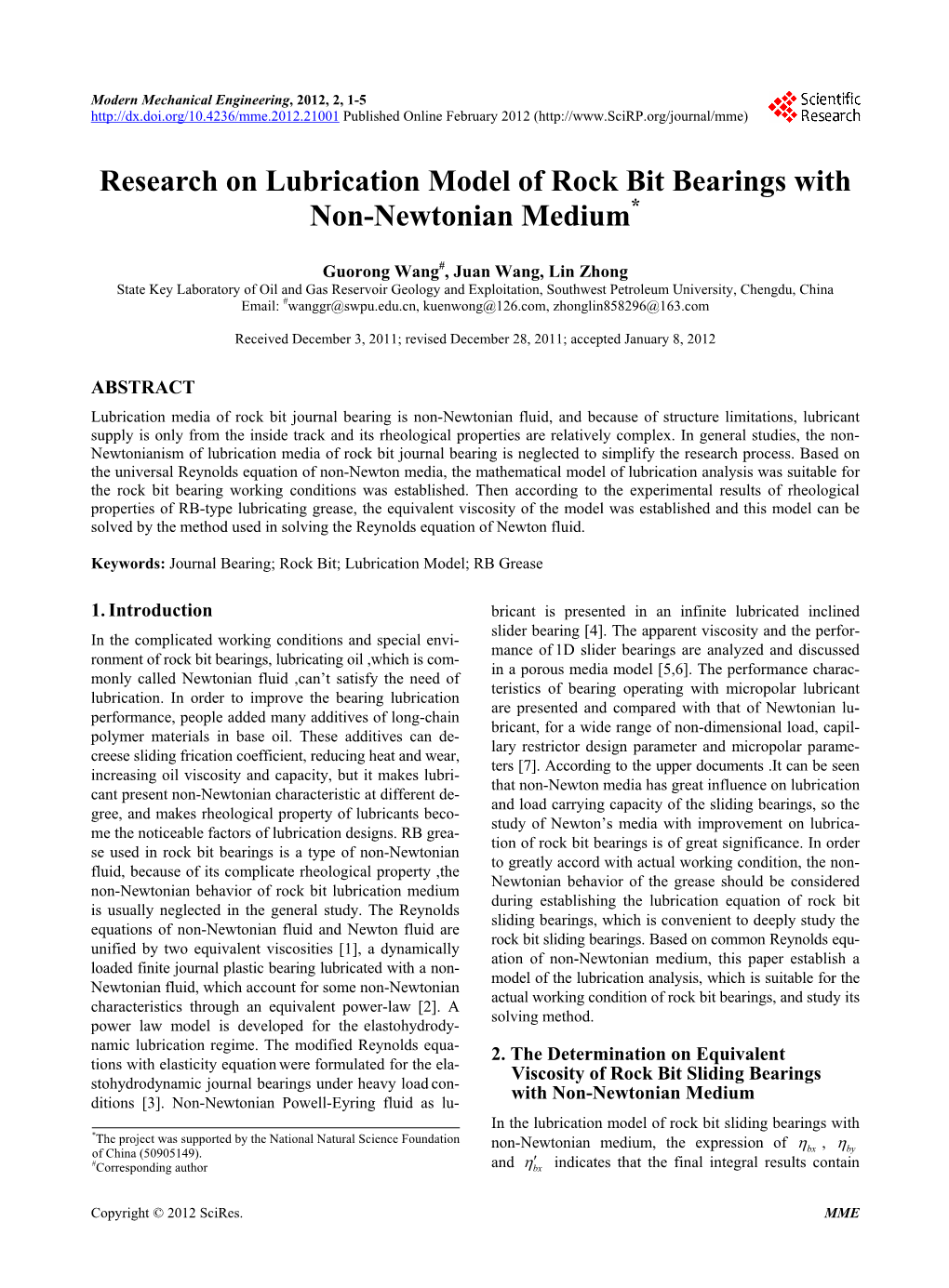
Load more
Recommended publications
-
Theoretical Studies of Non-Newtonian and Newtonian Fluid Flow Through Porous Media
Lawrence Berkeley National Laboratory Lawrence Berkeley National Laboratory Title Theoretical Studies of Non-Newtonian and Newtonian Fluid Flow through Porous Media Permalink https://escholarship.org/uc/item/6zv599hc Author Wu, Y.S. Publication Date 1990-02-01 eScholarship.org Powered by the California Digital Library University of California Lawrence Berkeley Laboratory e UNIVERSITY OF CALIFORNIA EARTH SCIENCES DlVlSlON Theoretical Studies of Non-Newtonian and Newtonian Fluid Flow through Porous Media Y.-S. Wu (Ph.D. Thesis) February 1990 TWO-WEEK LOAN COPY This is a Library Circulating Copy which may be borrowed for two weeks. r- +. .zn Prepared for the U.S. Department of Energy under Contract Number DE-AC03-76SF00098. :0 DISCLAIMER I I This document was prepared as an account of work sponsored ' : by the United States Government. Neither the United States : ,Government nor any agency thereof, nor The Regents of the , I Univers~tyof California, nor any of their employees, makes any I warranty, express or implied, or assumes any legal liability or ~ : responsibility for the accuracy, completeness, or usefulness of t any ~nformation, apparatus, product, or process disclosed, or I represents that its use would not infringe privately owned rights. : Reference herein to any specific commercial products process, or I service by its trade name, trademark, manufacturer, or other- I wise, does not necessarily constitute or imply its endorsement, ' recommendation, or favoring by the United States Government , or any agency thereof, or The Regents of the University of Cali- , forma. The views and opinions of authors expressed herein do ' not necessarily state or reflect those of the United States : Government or any agency thereof or The Regents of the , Univers~tyof California and shall not be used for advertismg or I product endorsement purposes. -
Fluid Inertia and End Effects in Rheometer Flows
FLUID INERTIA AND END EFFECTS IN RHEOMETER FLOWS by JASON PETER HUGHES B.Sc. (Hons) A thesis submitted to the University of Plymouth in partial fulfilment for the degree of DOCTOR OF PHILOSOPHY School of Mathematics and Statistics Faculty of Technology University of Plymouth April 1998 REFERENCE ONLY ItorriNe. 9oo365d39i Data 2 h SEP 1998 Class No.- Corrtl.No. 90 0365439 1 ACKNOWLEDGEMENTS I would like to thank my supervisors Dr. J.M. Davies, Prof. T.E.R. Jones and Dr. K. Golden for their continued support and guidance throughout the course of my studies. I also gratefully acknowledge the receipt of a H.E.F.C.E research studentship during the period of my research. AUTHORS DECLARATION At no time during the registration for the degree of Doctor of Philosophy has the author been registered for any other University award. This study was financed with the aid of a H.E.F.C.E studentship and carried out in collaboration with T.A. Instruments Ltd. Publications: 1. J.P. Hughes, T.E.R Jones, J.M. Davies, *End effects in concentric cylinder rheometry', Proc. 12"^ Int. Congress on Rheology, (1996) 391. 2. J.P. Hughes, J.M. Davies, T.E.R. Jones, ^Concentric cylinder end effects and fluid inertia effects in controlled stress rheometry, Part I: Numerical simulation', accepted for publication in J.N.N.F.M. Signed ...^.^Ms>3.\^^. Date Ik.lp.^.m FLUH) INERTIA AND END EFFECTS IN RHEOMETER FLOWS Jason Peter Hughes Abstract This thesis is concerned with the characterisation of the flow behaviour of inelastic and viscoelastic fluids in steady shear and oscillatory shear flows on commercially available rheometers. -
Lecture 1: Introduction
Lecture 1: Introduction E. J. Hinch Non-Newtonian fluids occur commonly in our world. These fluids, such as toothpaste, saliva, oils, mud and lava, exhibit a number of behaviors that are different from Newtonian fluids and have a number of additional material properties. In general, these differences arise because the fluid has a microstructure that influences the flow. In section 2, we will present a collection of some of the interesting phenomena arising from flow nonlinearities, the inhibition of stretching, elastic effects and normal stresses. In section 3 we will discuss a variety of devices for measuring material properties, a process known as rheometry. 1 Fluid Mechanical Preliminaries The equations of motion for an incompressible fluid of unit density are (for details and derivation see any text on fluid mechanics, e.g. [1]) @u + (u · r) u = r · S + F (1) @t r · u = 0 (2) where u is the velocity, S is the total stress tensor and F are the body forces. It is customary to divide the total stress into an isotropic part and a deviatoric part as in S = −pI + σ (3) where tr σ = 0. These equations are closed only if we can relate the deviatoric stress to the velocity field (the pressure field satisfies the incompressibility condition). It is common to look for local models where the stress depends only on the local gradients of the flow: σ = σ (E) where E is the rate of strain tensor 1 E = ru + ruT ; (4) 2 the symmetric part of the the velocity gradient tensor. The trace-free requirement on σ and the physical requirement of symmetry σ = σT means that there are only 5 independent components of the deviatoric stress: 3 shear stresses (the off-diagonal elements) and 2 normal stress differences (the diagonal elements constrained to sum to 0). -
A Fluid Is Defined As a Substance That Deforms Continuously Under Application of a Shearing Stress, Regardless of How Small the Stress Is
FLUID MECHANICS & BIOTRIBOLOGY CHAPTER ONE FLUID STATICS & PROPERTIES Dr. ALI NASER Fluids Definition of fluid: A fluid is defined as a substance that deforms continuously under application of a shearing stress, regardless of how small the stress is. To study the behavior of materials that act as fluids, it is useful to define a number of important fluid properties, which include density, specific weight, specific gravity, and viscosity. Density is defined as the mass per unit volume of a substance and is denoted by the Greek character ρ (rho). The SI units for ρ are kg/m3. Specific weight is defined as the weight per unit volume of a substance. The SI units for specific weight are N/m3. Specific gravity S is the ratio of the weight of a liquid at a standard reference temperature to the o weight of water. For example, the specific gravity of mercury SHg = 13.6 at 20 C. Specific gravity is a unit-less parameter. Density and specific weight are measures of the “heaviness” of a fluid. Example: What is the specific gravity of human blood, if the density of blood is 1060 kg/m3? Solution: ⁄ ⁄ Viscosity, shearing stress and shearing strain Viscosity is a measure of a fluid's resistance to flow. It describes the internal friction of a moving fluid. A fluid with large viscosity resists motion because its molecular makeup gives it a lot of internal friction. A fluid with low viscosity flows easily because its molecular makeup results in very little friction when it is in motion. Gases also have viscosity, although it is a little harder to notice it in ordinary circumstances. -
Rheology of Petroleum Fluids
ANNUAL TRANSACTIONS OF THE NORDIC RHEOLOGY SOCIETY, VOL. 20, 2012 Rheology of Petroleum Fluids Hans Petter Rønningsen, Statoil, Norway ABSTRACT NEWTONIAN FLUIDS Among the areas where rheology plays In gas reservoirs, the flow properties of an important role in the oil and gas industry, the simplest petroleum fluids, i.e. the focus of this paper is on crude oil hydrocarbons with less than five carbon rheology related to production. The paper atoms, play an essential role in production. gives an overview of the broad variety of It directly impacts the productivity. The rheological behaviour, and corresponding viscosity of single compounds are well techniques for investigation, encountered defined and mixture viscosity can relatively among petroleum fluids. easily be calculated. Most often reservoir gas viscosity is though measured at reservoir INTRODUCTION conditions as part of reservoir fluid studies. Rheology plays a very important role in The behaviour is always Newtonian. The the petroleum industry, in drilling as well as main challenge in terms of measurement and production. The focus of this paper is on modelling, is related to very high pressures crude oil rheology related to production. (>1000 bar) and/or high temperatures (170- Drilling and completion fluids are not 200°C) which is encountered both in the covered. North Sea and Gulf of Mexico. Petroleum fluids are immensely complex Hydrocarbon gases also exist dissolved mixtures of hydrocarbon compounds, in liquid reservoir oils and thereby impact ranging from the simplest gases, like the fluid viscosity and productivity of these methane, to large asphaltenic molecules reservoirs. Reservoir oils are also normally with molecular weights of thousands. -
Lecture 2: (Complex) Fluid Mechanics for Physicists
Application of granular jamming: robots! Cornell (Amend and Lipson groups) in collaboration with Univ of1 Chicago (Jaeger group) Lecture 2: (complex) fluid mechanics for physicists S-RSI Physics Lectures: Soft Condensed Matter Physics Jacinta C. Conrad University of Houston 2012 Note: I have added links addressing questions and topics from lectures at: http://conradlab.chee.uh.edu/srsi_links.html Email me questions/comments/suggestions! 2 Soft condensed matter physics • Lecture 1: statistical mechanics and phase transitions via colloids • Lecture 2: (complex) fluid mechanics for physicists • Lecture 3: physics of bacteria motility • Lecture 4: viscoelasticity and cell mechanics • Lecture 5: Dr. Conrad!s work 3 Big question for today!s lecture How does the fluid mechanics of complex fluids differ from that of simple fluids? Petroleum Food products Examples of complex fluids: Personal care products Ceramic precursors Paints and coatings 4 Topic 1: shear thickening 5 Forces and pressures A force causes an object to change velocity (either in magnitude or direction) or to deform (i.e. bend, stretch). � dp� Newton!s second law: � F = m�a = dt p� = m�v net force change in linear mass momentum over time d�v �a = acceleration dt A pressure is a force/unit area applied perpendicular to an object. Example: wind blowing on your hand. direction of pressure force �n : unit vector normal to the surface 6 Stress A stress is a force per unit area that is measured on an infinitely small area. Because forces have three directions and surfaces have three orientations, there are nine components of stress. z z Example of a normal stress: δA δAx x δFx τxx = lim τxy δFy δAx→0 δAx τxx δFx y y Example of a shear stress: δFy τxy = lim δAx→0 δAx x x Convention: first subscript indicates plane on which stress acts; second subscript indicates direction in which the stress acts. -
Chapter 3 Newtonian Fluids
CM4650 Chapter 3 Newtonian Fluid 2/5/2018 Mechanics Chapter 3: Newtonian Fluids CM4650 Polymer Rheology Michigan Tech Navier-Stokes Equation v vv p 2 v g t 1 © Faith A. Morrison, Michigan Tech U. Chapter 3: Newtonian Fluid Mechanics TWO GOALS •Derive governing equations (mass and momentum balances •Solve governing equations for velocity and stress fields QUICK START V W x First, before we get deep into 2 v (x ) H derivation, let’s do a Navier-Stokes 1 2 x1 problem to get you started in the x3 mechanics of this type of problem solving. 2 © Faith A. Morrison, Michigan Tech U. 1 CM4650 Chapter 3 Newtonian Fluid 2/5/2018 Mechanics EXAMPLE: Drag flow between infinite parallel plates •Newtonian •steady state •incompressible fluid •very wide, long V •uniform pressure W x2 v1(x2) H x1 x3 3 EXAMPLE: Poiseuille flow between infinite parallel plates •Newtonian •steady state •Incompressible fluid •infinitely wide, long W x2 2H x1 x3 v (x ) x1=0 1 2 x1=L p=Po p=PL 4 2 CM4650 Chapter 3 Newtonian Fluid 2/5/2018 Mechanics Engineering Quantities of In more complex flows, we can use Interest general expressions that work in all cases. (any flow) volumetric ⋅ flow rate ∬ ⋅ | average 〈 〉 velocity ∬ Using the general formulas will Here, is the outwardly pointing unit normal help prevent errors. of ; it points in the direction “through” 5 © Faith A. Morrison, Michigan Tech U. The stress tensor was Total stress tensor, Π: invented to make the calculation of fluid stress easier. Π ≡ b (any flow, small surface) dS nˆ Force on the S ⋅ Π surface V (using the stress convention of Understanding Rheology) Here, is the outwardly pointing unit normal of ; it points in the direction “through” 6 © Faith A. -
7. Fluid Mechanics
7. Fluid mechanics Introduction In this chapter we will study the mechanics of fluids. A non-viscous fluid, i.e. fluid with no inner friction is called an ideal fluid. The stress tensor for an ideal fluid is given by T1= −p , which is the most simplest form of the stress tensor used in fluid mechanics. A viscous material is a material for which the stress tensor depends on the rate of deformation D. If this relation is linear then we have linear viscous fluid or Newtonian fluid. The stress tensor for a linear viscous fluid is given by T = - p 1 + λ tr D 1 + 2μ D , where λ and μ are material constants. If we assume the fluid to be incompressible, i.e. tr D 1 = 0 and the stress tensor can be simplified to contain only one material coefficient μ . Most of the fluids can not be modelled by these two simple types of stress state assumption and they are called non-Newtonian fluids. There are different types of non-Newtonian fluids. We have constitutive models for fluids of differential, rate and integral types. Examples non-Newtonian fluids are Reiner-Rivlin fluids, Rivlin-Ericksen fluids and Maxwell fluids. In this chapter we will concentrate on ideal and Newtonian fluids and we will study some classical examples of hydrodynamics. 7.1 The general equations of motion for an ideal fluid For an arbitrary fluid (liquid or gas) the stress state can be describe by the following constitutive relation, T1= −p (7.1) where p= p (r ,t) is the fluid pressure and T is the stress. -
Equation of Motion for Viscous Fluids
1 2.25 Equation of Motion for Viscous Fluids Ain A. Sonin Department of Mechanical Engineering Massachusetts Institute of Technology Cambridge, Massachusetts 02139 2001 (8th edition) Contents 1. Surface Stress …………………………………………………………. 2 2. The Stress Tensor ……………………………………………………… 3 3. Symmetry of the Stress Tensor …………………………………………8 4. Equation of Motion in terms of the Stress Tensor ………………………11 5. Stress Tensor for Newtonian Fluids …………………………………… 13 The shear stresses and ordinary viscosity …………………………. 14 The normal stresses ……………………………………………….. 15 General form of the stress tensor; the second viscosity …………… 20 6. The Navier-Stokes Equation …………………………………………… 25 7. Boundary Conditions ………………………………………………….. 26 Appendix A: Viscous Flow Equations in Cylindrical Coordinates ………… 28 ã Ain A. Sonin 2001 2 1 Surface Stress So far we have been dealing with quantities like density and velocity, which at a given instant have specific values at every point in the fluid or other continuously distributed material. The density (rv ,t) is a scalar field in the sense that it has a scalar value at every point, while the velocity v (rv ,t) is a vector field, since it has a direction as well as a magnitude at every point. Fig. 1: A surface element at a point in a continuum. The surface stress is a more complicated type of quantity. The reason for this is that one cannot talk of the stress at a point without first defining the particular surface through v that point on which the stress acts. A small fluid surface element centered at the point r is defined by its area A (the prefix indicates an infinitesimal quantity) and by its outward v v unit normal vector n . -
Lecture 3: Simple Flows
Lecture 3: Simple Flows E. J. Hinch In this lecture, we will study some simple flow phenomena for the non-Newtonian fluid. From analyzing these simple phenomena, we will find that non-Newtonian fluid has many unique properties and can be quite different from the Newtonian fluid in some aspects. 1 Pipe flow of a power-law fluid The pipe flow of Newtonian fluid has been widely studied and well understood. Here, we will analyze the pipe flow of non-Newtonian fluid and compare the phenomenon with that of the Newtonian fluid. We consider a cylindrical pipe, where the radius of the pipe is R and the length is L. The pressure drop across the pipe is ∆p and the flux of the fluid though the pipe is Q (shown in Figure 1). Also, we assume that the flow in the pipe is steady, uni-directional and uniform in z. Thus, the axial momentum of the fluid satisfies: dp 1 @(rσ ) 0 = − + zr : (1) dz r @r dp ∆p Integrate this equation with respect to r and scale dz with L , we have: r σzr = σ ; (2) R wall ∆pR where σwall represents the stress on the wall and is given by σwall = 2L . For the power-law fluid, the constitutive equation is: n σzr = kγ_ ; (3) L R Q P Figure 1: Pipe flow 28 n = 1 n<1 Figure 2: Flow profile where k is a constant and γ_ is the scalar strain rate. For the pipe flow, the strain rate can be expressed as: dw γ_ = − ; (4) dr where w is the axial velocity. -
Rotating Stars in Relativity
Living Rev Relativ (2017) 20:7 https://doi.org/10.1007/s41114-017-0008-x REVIEW ARTICLE Rotating stars in relativity Vasileios Paschalidis1,2 · Nikolaos Stergioulas3 Received: 8 December 2016 / Accepted: 3 October 2017 / Published online: 29 November 2017 © The Author(s) 2017. This article is an open access publication Abstract Rotating relativistic stars have been studied extensively in recent years, both theoretically and observationally, because of the information they might yield about the equation of state of matter at extremely high densities and because they are considered to be promising sources of gravitational waves. The latest theoretical understanding of rotating stars in relativity is reviewed in this updated article. The sec- tions on equilibrium properties and on nonaxisymmetric oscillations and instabilities in f -modes and r-modes have been updated. Several new sections have been added on equilibria in modified theories of gravity, approximate universal relationships, the one-arm spiral instability, on analytic solutions for the exterior spacetime, rotating stars in LMXBs, rotating strange stars, and on rotating stars in numerical relativity including both hydrodynamic and magnetohydrodynamic studies of these objects. Keywords Relativistic stars · Rotation · Stability · Oscillations · Magnetic fields · Numerical relativity This article is a revised version of https://doi.org/10.12942/lrr-2003-3. Change summary: Major revision, updated and expanded. Change details: The article has been substantially revised and updated. Expanded all sections, and moved former Subsect. 2.10 to Sect. 3. The number of references (now 863) has more than doubled. B Nikolaos Stergioulas [email protected] Vasileios Paschalidis [email protected] 1 Theoretical Astrophysics Program, Departments of Astronomy and Physics, University of Arizona, Tucson, AZ 85721, USA 2 Department of Physics, Princeton University, Princeton, NJ 08544, USA 3 Department of Physics, Aristotle University of Thessaloniki, 54124 Thessaloniki, Greece 123 7 Page 2 of 169 V. -
Complex Fluids in Energy Dissipating Systems
applied sciences Review Complex Fluids in Energy Dissipating Systems Francisco J. Galindo-Rosales Centro de Estudos de Fenómenos de Transporte, Faculdade de Engenharia da Universidade do Porto, CP 4200-465 Porto, Portugal; [email protected] or [email protected]; Tel.: +351-925-107-116 Academic Editor: Fan-Gang Tseng Received: 19 May 2016; Accepted: 15 July 2016; Published: 25 July 2016 Abstract: The development of engineered systems for energy dissipation (or absorption) during impacts or vibrations is an increasing need in our society, mainly for human protection applications, but also for ensuring the right performance of different sort of devices, facilities or installations. In the last decade, new energy dissipating composites based on the use of certain complex fluids have flourished, due to their non-linear relationship between stress and strain rate depending on the flow/field configuration. This manuscript intends to review the different approaches reported in the literature, analyses the fundamental physics behind them and assess their pros and cons from the perspective of their practical applications. Keywords: complex fluids; electrorheological fluids; ferrofluids; magnetorheological fluids; electro-magneto-rheological fluids; shear thickening fluids; viscoelastic fluids; energy dissipating systems PACS: 82.70.-y; 83.10.-y; 83.60.-a; 83.80.-k 1. Introduction Preventing damage or discomfort resulting from any sort of external kinetic energy (impact or vibration) is an omnipresent problem in our society. On one hand, impacts and vibrations are responsible for several health problems. According to the European Injury Data Base (IDB), injuries due to accidents are killing one EU citizen every two minutes and disabling many more [1].