Steam Boilers
Total Page:16
File Type:pdf, Size:1020Kb
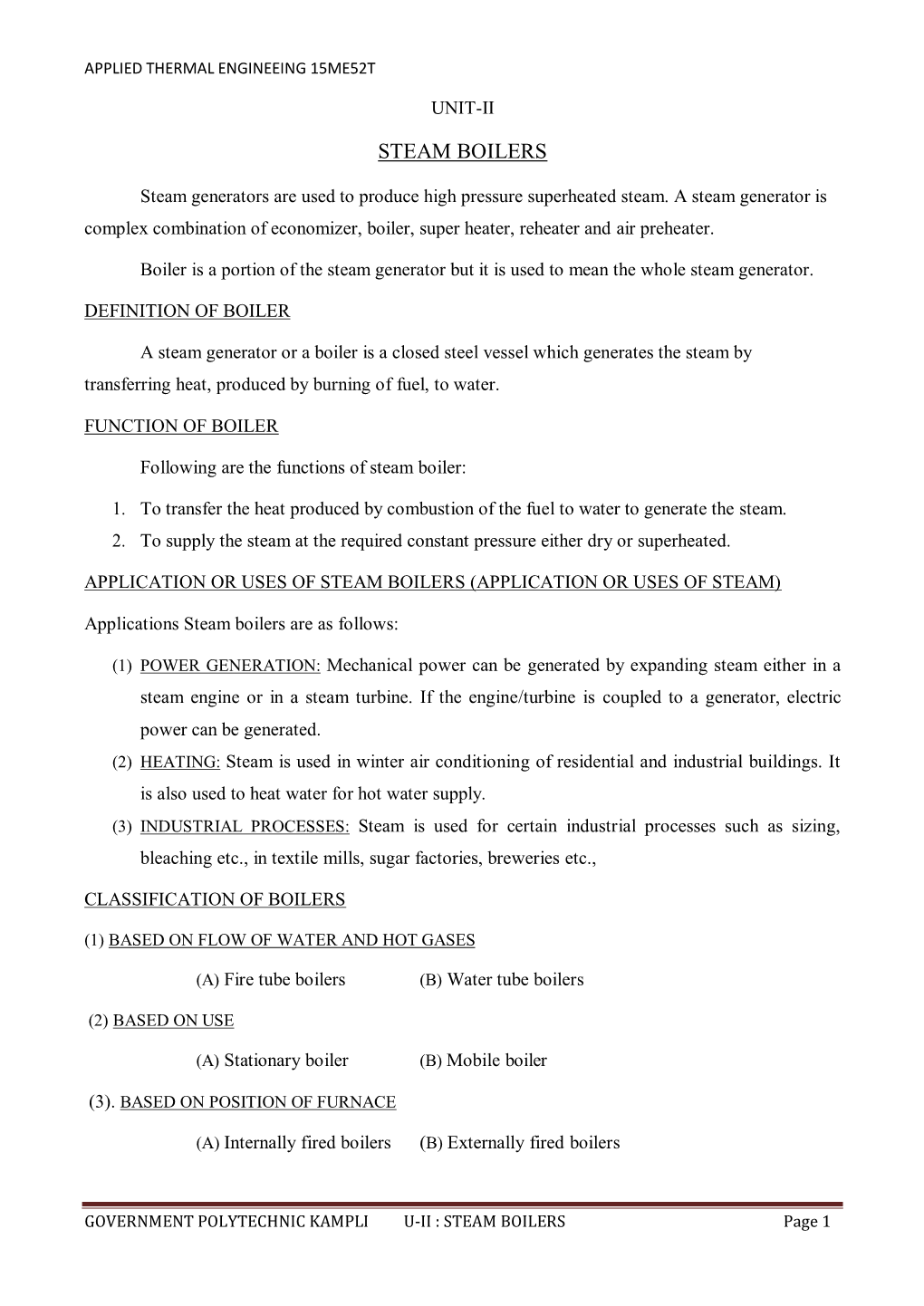
Load more
Recommended publications
-
Thermal Engg. Model Answer Subject Code: 17410
MAHARASHTRA STATE BOARD OF TECHNICAL EDUCATION (Autonomous) (ISO/IEC - 27001 - 2013 Certified) SUMMER—18 EXAMINATION Subject Name: Thermal Engg. Model Answer Subject Code: 17410 _________________________________________________________________________________________________ Important Instructions to examiners: 1) The answers should be examined by key words and not as word-to-word as given in the model answer scheme. 2) The model answer and the answer written by candidate may vary but the examiner may try to assess the understanding level of the candidate. 3) The language errors such as grammatical, spelling errors should not be given more Importance (Not applicable for subject English and Communication Skills. 4) While assessing figures, examiner may give credit for principal components indicated in the figure. The figures drawn by candidate and model answer may vary. The examiner may give credit for any equivalent figure drawn. 5) Credits may be given step wise for numerical problems. In some cases, the assumed constant values may vary and there may be some difference in the candidate‟s answers and model answer. 6) In case of some questions credit may be given by judgement on part of examiner of relevant answer based on candidate‟s understanding. 7) For programming language papers, credit may be given to any other program based on equivalent concept. Q. Answer Marking Sub Q. No Scheme No. Q. (a i) Attempt any six Extensive property:- An extensive property of a system is one whose value 2 1 ) depend upon the mass of the system. mar ks e.g. volume, energy, enthalpy, entropy, internal energy. each ii) Zero Law of thermodynamics:- if state that “If two system are both in equilibrium with a third, are equilibrium with each other”. -
Basic Mechanical Engineering and Manufacturing Practices Lab
IPS Academy, Institute of Engineering & Science 1 Department of Mechanical Engineering Basic Mechanical Engineering and Manufacturing Practices Lab Laboratory in charge Laboratory Technician Prof. Pradeep Singh Hada Mr. Prakash Take Prof. Shubham Kanungo 1st / 2nd Semester Basic Mechanical Engineering & Manufacturing Practices (ESC-202) IPS Academy, Institute of Engineering & Science 2 List of Experiments 1 To perform a tensile test on UTM. 2 To verify Bernoulli’s Theorem using Bernoulli’s apparatus. 3 Study of Two and Four Stroke SI Engine. 4 Study of Two and Four Stroke CI Engine. 5 Study of Boilers, their Mounting and Accessories. 6 Study of Lathe & Drilling Machine. 7 To prepare a job in Fitting shop. 8 To prepare a job in Carpentry shop. 9 To prepare a job in Black Smithy shop. 10 To prepare a job in Welding shop. 1st / 2nd Semester Basic Mechanical Engineering & Manufacturing Practices (ESC-202) IPS Academy, Institute of Engineering & Science 3 List of Equipment with Price S. No. List of Equipment Date Price (in Rs.) 1. Model of Babcock and Wilcox boiler 01/12/2015 7300/- 2. Model of Cochran boiler 01/12/2015 5600/- 3. Model of Simple Vertical boiler 01/12/2015 7300/- 4. Model of Four Stroke Petrol engine 01/12/2015 1925/ 5. Model of Four Stroke Diesel engine 01/12/2015 1925/- 6. Model of Two Stroke Petrol engine 01/12/2015 1925/- 7. Model of Two Stroke Diesel engine 01/12/2015 1925/- 8. Model of Steam Engine with boiler 01/12/2015 6200/- 9. Model of Nestler boiler 05/03/2019 9540/- 10. -
Boilers Leture Notes VUM
Steam Boilers Lecture Notes V Uma Maheshwar 11-11-11 Steam Boilers/Steam Generators Introduction: The function of a boiler is to evaporate water into steam at a pressure higher than the atmospheric pressure. Water free from impurities such as dissolved salts , gases and non soluble solids should be supplied to boilers. This is done by suitable water treatment . Steam is useful for running steam turbines in electrical power stations , ships and steam engines in railway locomotives. Boiler furnace fuel can use either solid , liquid or gaseous fuel: Wood, Charcoal, Coal, Coke, Oil, Municipal waste, industrial solid waste , refinery gas, rice husk, Paper sludge, Electric power Steam Boilers/Steam Generators Boilers are mainly classified as fire tube boilers and water tube boilers. Fire tube boilers :- hot gases from the furnace pass through the tubes which are surrounded by water. Water tube boilers :- water circulates inside the tubes which are surrounded by the hot gases from the furnace. Steam Boilers/Steam Generators Other Classifications : Based on Pressure : =>80 bar : High Pressure Boilers Babcock & Wilcox, Lamont, Benson, Velox <80 bar : Low Pressure Boilers Locomotive, Lancashire, Cornish, Cochran Steam Boilers/Steam Generators Other Classifications : Based on Pressure : =>80 bar : High Pressure Boilers Babcock & Wilcox, Lamont, Benson, Velox <80 bar : Low Pressure Boilers Locomotive, Lancashire, Cornish, Cochran Steam Boilers/Steam Generators Other Classifications : Based on Type of Circulation of water : Natural Circulation : Natural -
Bulletin 173 Plate 1 Smithsonian Institution United States National Museum
U. S. NATIONAL MUSEUM BULLETIN 173 PLATE 1 SMITHSONIAN INSTITUTION UNITED STATES NATIONAL MUSEUM Bulletin 173 CATALOG OF THE MECHANICAL COLLECTIONS OF THE DIVISION OF ENGINEERING UNITED STATES NATIONAL MUSEUM BY FRANK A. TAYLOR UNITED STATES GOVERNMENT PRINTING OFFICE WASHINGTON : 1939 For lale by the Superintendent of Documents, Washington, D. C. Price 50 cents ADVERTISEMENT Tlie scientific publications of the National Museum include two series, known, respectively, as Proceedings and Bulletin. The Proceedings series, begun in 1878, is intended primarily as a medium for the publication of original papers, based on the collec- tions of the National Museum, that set forth newly acquired facts in biology, anthropology, and geology, with descriptions of new forms and revisions of limited groups. Copies of each paper, in pamphlet form, are distributed as published to libraries and scientific organi- zations and to specialists and others interested in the different sub- jects. The dates at which these separate papers are published are recorded in the table of contents of each of the volumes. Tlie series of Bulletins, the first of which was issued in 1875, contains separate publications comprising monographs of large zoological groups and other general systematic treatises (occasionally in several volumes), faunal works, reports of expeditions, catalogs of type specimens and special collections, and other material of simi- lar nature. The majority of the volumes are octavo in size, but a quarto size has been adopted in a few instances in which large plates were regarded as indispensable. In the Bulletin series appear vol- umes under the heading Contrihutions from the United States Na- tional Eerharium, in octavo form, published by the National Museum since 1902, which contain papers relating to the botanical collections of the Museum. -
College of Engineering and Technology, Akola
College of Engineering & Technology Akola COLLEGE OF ENGINEERING AND TECHNOLOGY, AKOLA DEPARTMENT OF MECHANICAL ENGINEERING NAME : ................................................................... SUBJECT : ENERGY CONVERSION LAB CLASS : SECOND YEAR MECHANICAL ENGG. ROLL NO : .............. NAME OF THE FACULTY: ROSHAN D. BHAGAT DESIGNATION: ASSIST. PROFESSOR BRANCH: MECHANICAL ENGINEERING SUBJECT: EC-1LAB SEMESTER: FOURTH ACADEMIC YEAR 2016-2017 1 ENERGY CONVERSION-1 LAB College of Engineering & Technology Akola DEPARTMENT OF MECHANICAL ENGINEERING CERTIFICATE This is to certify that Mr. / Miss............................................. has satisfactorily completed the course of experiments in ENERGY CONVERSION LAB as prescribed by the Sant Gadge Baba Amravati University in the laboratory of college for the academic year 2016-2017 Date: Signature of Teacher In charge of the Batch Head of department Name of the candidate Registration no Roll no. Date of practical examination 2 ENERGY CONVERSION-1 LAB College of Engineering & Technology Akola INDEX SR.NO NAME OF EXPERIMENT DATE SIGN 1 Study of water tube boiler babcock and Wilcox 2 Study of locomotive boiler 3 Study of high pressure boiler 4 Study of boiler accessories 5 Trial on boiler and heat balance sheet 6 Study of boiler mounting 7 Study and trial on steam turbine 8 Study of condenser 9 Study of condensate and air extraction pump 10 Study of steam power plant 3 ENERGY CONVERSION-1 LAB College of Engineering & Technology Akola Practical No 1 Aim: Study of water tube Babcock and Wilcox water tube boiler Apparatus: Babcock and Wilcox water tube boiler Theory: The water tube boiler used exclusively when pressure above 10 bars and capacity in excess of 7000 kg of steam per hour is required. -
Developing of a Thermodynamic Model for the Performance Analysis
Preprints (www.preprints.org) | NOT PEER-REVIEWED | Posted: 2 August 2018 doi:10.20944/preprints201808.0045.v1 Peer-reviewed version available at Energies 2018, 11, 2655; doi:10.3390/en11102655 Developing of a thermodynamic model for the performance analysis of a Stirling engine prototype Miguel Torres García*, Elisa Carvajal Trujillo, José Antonio Vélez Godiño, David Sánchez Martínez University of Seville-Thermal Power Group - GMTS Escuela Técnica Superior de Ingenieros Industriales Camino de los descubrimientos s/n 41092 SEVILLA (SPAIN) e-mail: [email protected] KEYWORDS Stirling engine, combustion model Abstrac The scope of the study developed by the authors consists in comparing the results of simulations generated from different thermodynamic models of Stirling engines, characterizing both instantaneous and indicated operative parameters. The elaboration of this study aims to develop a tool to guide the decision-making process regarding the optimization of both performance and reliability of developing Stirling engines, such as the 3 kW GENOA 03 unit, on which this work focuses. Initially, the authors proceed to characterize the behaviour of the aforementioned engine using two different approaches: firstly, an ideal isothermal model is used, the simplest of those available; proceeding later to the analysis by means of an ideal adiabatic model, more complex than the first one. Since some of the results obtained with the referred ideal models are far from the expected actual ones, particularly in terms of thermal efficiency, the authors propose a set of modifications to the ideal adiabatic model. These modifications, mainly related to both heat transfer and fluid friction phenomena, are intended to overcome the limitations derived from the idealization of the engine working cycle and are expected to generate results closer to the actual behaviour of the Stirling engine, despite the increase in the complexity related to the modelling and simulation processes derived from those. -
Modern Steam Generators
4 MODERN STEAM GENERATORS 4.1 Introduction Boiler is a container into which water is fed, and by the application of heat, it is evaporated into steam. In early designs, the boiler was a simple shell with a feed pipe and steam outlet, mounted on a brick setting. Fuel was burnt on a grate within the setting and the heat so released was directed over the lower shell surface before most of it went out. Soon the designers realized that heating a single shell is inefficient and it was necessary to bring more of water into close contact with heat. One way, is to direct flue gases through tubes in the boiler shell. Such a '“fire-tube design’ not only increases the heating surface but also distributes area of steam formation more uniformly. Second way is water-tube design. It consists of one or more relatively small drums with number of tubes in which water-steam mixture circulates. Heat flows from flue gases outside tubes to the mixture. Thus sub-division of pressure parts make possible construction of large capacity and high pressure boilers. Fire-tube boilers and simple water-tube boilers are described in detail in chapter-8 of volume-l. Fire-tube boilers are limited to a maximum design working pressure of 25 bar and steam generating capacity of 25 tonnes per hour. Conventional water-tubes boilers work upto steam pressures of about 70 bar and 250°C superheat with a steam generating capacity of 40 tonnes per hour. Shell or fire-tube boilers are cheaper than water-tube boilers but they are suitable for low pressures and low output. -
LAB MANUAL Lab Name : Thermal Engineering Lab-1
JAIPUR ENGINEERING COLLEGE AND RESEARCH CENTRE JECRC Campus, Shri Ram Ki Nangal, Via-Vatika, Jaipur LAB MANUAL Lab Name : Thermal Engineering Lab-1 Lab Code : 6ME4-24 Branch : Mechanical Engineering Year : 3rd Year Department of Mechanical Engineering Jaipur Engineering College and Research Center, Jaipur (Rajasthan Technical University, KOTA) JAIPUR ENGINEERING COLLEGE AND RESEARCH CENTRE JECRC Campus, Shri Ram Ki Nangal, Via-Vatika, Jaipur INDEX S.NO CONTENTS CO PAGE NO. 1 VISION/MISION i 2. PEO ii 3. POS iii 4. COS iv 5. MAPPING OF CO & PO iv 6. SYLLABUS v 7. BOOKS vi 8 INSTRUCTIONAL METHODS vi 9 LEARNING MATERIALS vi 10 ASSESSMENT OF OUTCOMES vi 11 INSTRUCTION SHEET vii JAIPUR ENGINEERING COLLEGE AND RESEARCH CENTRE JECRC Campus, Shri Ram Ki Nangal, Via-Vatika, Jaipur LIST OF EXPERIMENTS (RTU SYLLABUS) Exp:- 1 Objectives :- Study of working of four stroke petrol engine and four 1 stroke diesel engine with the help of cut section models Exp:- 2 Objectives :- Study of working of two stroke petrol and two stroke 9 diesel engine with the help of cut section models Exp:-3 Objectives :- To draw valve timing diagram for a single cylinder diesel 14 engine Exp:-4 Objectives: - Study of various types of boilers 18 Exp:-5 Objectives: - Study of various types of mountings and accessories 35 Exp:-6 Objectives: - Demonstration of steering system and measurement of 43 steering geometry angles and their impact on vehicle performance Exp:-7 Objectives: - Study of braking system with specific reference to types of 47 braking system, master cylinder, -
A Handbook on the Steam Engine, with Especial Reference to Small And
ADVERTlSEMElfTS. i+t\\i JD, 3.E. YS. (YS, Tl sPOUS U ^rcacuteb to PI nd), of I tt of Toronto id). Professor E.A.Allcut AL. Is. Castings in Bronze, Brass and Gun and White Metals, Machined if required. ROLLED PHOSPHOR BRONZE, Strip and Sheet, for Air Pump Valves, Eccentric Strap Liners, etc. HIKE find TELEPHONE WIRE. AD VER TISEMENTS. THE PHOSPHOR BRONZE CO, LIMITED, 87, Sumner Street, Southwark, London, S.E. And at BIRMINGHAM. r "COG WHEEL" and Sole Makers of the j3S %jg "VULCAN" iSPI^flfiC Brands of The best and most durable Alloys for Slide Valves, Bearings, Bushes, Eccentric Straps, and other parts of Machinery exposed to friction and Piston Motor wear ; Pump Rods, Pumps, Rings, Pinions, Worm Wheels, Gearing, etc. "DURO METAL" (REGISTERED TRADE MARK). Alloy B, specially adapted for BEARINGS for HOT-NECK ROLLS. CASTINGS In BRONZE, BRASS, GUN and WHITE METALS, in the Rough, or Machined, if required. ROLLED AND DRAWN BRONZE, GERMAN SILVER, GUN METAL, TIN, WHITE METALS AND ALUMINIUM BRONZE ALLOYS PHOSPHOR TIN & PHOSPHOR COPPER, "Cog-Wheel" Brand. Please specify the Manufacture of THE PHOSPHOR BRONZE CO., Ltd., of Southwark, London. lii ADVERTISEMENTS, ROBEY & Co GLOBE WORKS, LINCOLN. Mod Compound Horizontal Fixed Engine, it.- 1 iiii I'.ii.-nt Ti-ip Kxitiimioii (ic:ir. tolnijthe limpl >nUit ml miTrt economical at uuv in tin- market, and working ;.|iei to the Newcastle-nil -Tvm .tit Station (MX large engines), also St. Helens mint lam. BrUbane Electric Tram- Open-front High-speed Vertical e, for electric lighting. All thete Engine* are specially Dengned and Adapted for Electric Lighting. -
Steam Boilers, Engines and Turbines
BOUGHT WITH THE INCOME' FROM THE SAGE ENDOWMENT FUND THE GIFT OF Henrg W. Sage .. 1891 A.^A..? 7:r..7.. s//.U.a,£... 3513-1 Cornell University Library TJ 275.W18 Steam boilers, engines and turbines, 3 1924 004 608 083 Cornell University Library The original of this book is in the Cornell University Library. There are no known copyright restrictions in the United States on the use of the text. http://www.archive.org/details/cu31924004608083 STEAM BOILERS, ENGINES, AND TURBINES c6 a* r^T OJ I O ^ r/: CI :/j STEAM BOILERS, ENGINES AND TURBINES SYDNEY F. 'gfALKER M.I.E.E^ M.Inst.M.E., M.I.M.E., Assoc.M.I.C.E., Etc. AVTHOR OF "electricity IN MINING," ETC. NEW YORK D. VAN NOSTRAND COMPANY 23 MURRAY AND 27 WARREN STREETS 1908 PREFACE In the following pages the author has endeavoured to set forth the principles and practice of steam, as they are understood by modern engineers, for the use of the student, using the term in its wide sense, viz. to include all those to whom a knowledge of steam and of steam-using apparatus will be of service. "With the universal -em- ployment of power, a knowledge of the properties of steam is becoming daily of more and more importance to engineers of all branches, and to large numbers of business men and others who are not directly engaged in the practical application of steam appliances..^ The author has endeavoured to set out, in simple language, and with the aid' of only the very simplest forms of mathematics, the properties of water, of steam, of air, and of the gases that enter into the process of combustion, and he has also endeavoured to give a resume of the latest practice in steam, and a description of the latest appliances for its economical generation and use. -
Basic Civil and Mechanical Engineering Boilers
www.vidyarthiplus.com BASIC CIVIL AND MECHANICAL ENGINEERING UNIT IV BOILERS PART A (Question and Answers) 1. How boilers are classified? (i) According to flow of water and gases (a) Fire tube boiler (b) Water tube boiler (ii) According to pressure (a) Low pressure boiler (b) High Pressure (iii) According to method of firing (a) Internally fired boiler (b) Externally fired boiler 2. List out the advantages of high pressure boiler. (i) Heat energy per kg of steam is increased at high pressure (ii) Production rate of steam is high. (iii) Superheated steam can be produced. 3. What are the various applications of steam boilers? (i) Steam produced by the boiler is used for driving steam turbines for power generation (ii) Steam is used in steam engine in railway locomotives. (iii) Steam boiler is also used in industrial applications. 4. What is the purpose of an economizer in boilers? The purpose of an economizer in a steam boiler is used to preheat the feed water from the tank, before it enters the boiler. 1 www.vidyarthiplus.com www.vidyarthiplus.com 5. What is the purpose of superheater in boiler? A superheater is used to increase the temperature the steam to convert the dry steam into super heated to steam. Superheated steam with high energy content is used to drive the turbine. 6. What is meant by forced circulation boiler? In forced circulation boiler, water is circulated with high pressure by a pump driven by the motor. Example: Lamont boiler. 7. What is the purpose of a man hole in the boiler? A man hole is a provision for a skilled personnel to enter into the boiler shell for cleaning, inspecting or for attending any repairs in the boiler. -
BASIC MECHANICAL ENGINEERING: 1FY3-07/2FY3-07) Programme: B
Swami Keshvanand Institute of Technology, Management & Gramothan, Ramnagaria, Jagatpura, Jaipur-302017, INDIA Approved by AICTE, Ministry of HRD, Government of India Recognized by UGC under Section 2(f) of the UGC Act, 1956 Tel. : +91-0141- 5160400Fax: +91-0141-2759555 E-mail: [email protected] Web: www.skit.ac.in A Course File of BASIC MECHANICAL ENGINEERING: 1FY3-07/2FY3-07) Programme: B. Tech. I YEAR Semester: I/II Session: 2020-2021 Mr. Sanjay Bairwa Assistant Professor Mechanical Engineering Department Page | 1 Swami Keshvanand Institute of Technology, Management & Gramothan, Ramnagaria, Jagatpura, Jaipur-302017, INDIA Approved by AICTE, Ministry of HRD, Government of India Recognized by UGC under Section 2(f) of the UGC Act, 1956 Tel. : +91-0141- 5160400Fax: +91-0141-2759555 E-mail: [email protected] Web: www.skit.ac.in Contents 1. Institute Vision/Mission/Quality Policy 2. Departmental Vision/Mission 3. RTU Scheme & Syllabus 4. Prerequisite of Course 5. List of Text and Reference Books 6. Time Table 7. Syllabus Deployment: Course Plan & Coverage* 8. PO/PSO-Indicator-Competency 9. COs Competency Level 10. CO-PO-PSO Mapping Using Performance Indicators(PIs) 11. CO-PO-PSO Mapping: Formulation & Justification 12. Attainment Level (Internal Assessment) 13. Learning Levels of Students Through Marks Obtained in 1st Unit Test/Quiz 14. Planning for Remedial Classes for Average/Below Average Students 15. Teaching-Learning Methodology 16. RTU Papers (Previous Years) 17. Mid Term Papers (Mapping with Bloom’s Taxonomy & COs) 18. Tutorial Sheets (with EMD Analysis)** 19. Technical Quiz Papers 20. Assignments (As Per RTU QP Format) 21. Details of Efforts Made to Fill Gap Between COs and POs (Expert Lecture/Workshop/Seminar/Extra Coverage in Lab etc.) 22.