University of Groningen Turning Men Into Machines? Derksen, Maarten
Total Page:16
File Type:pdf, Size:1020Kb
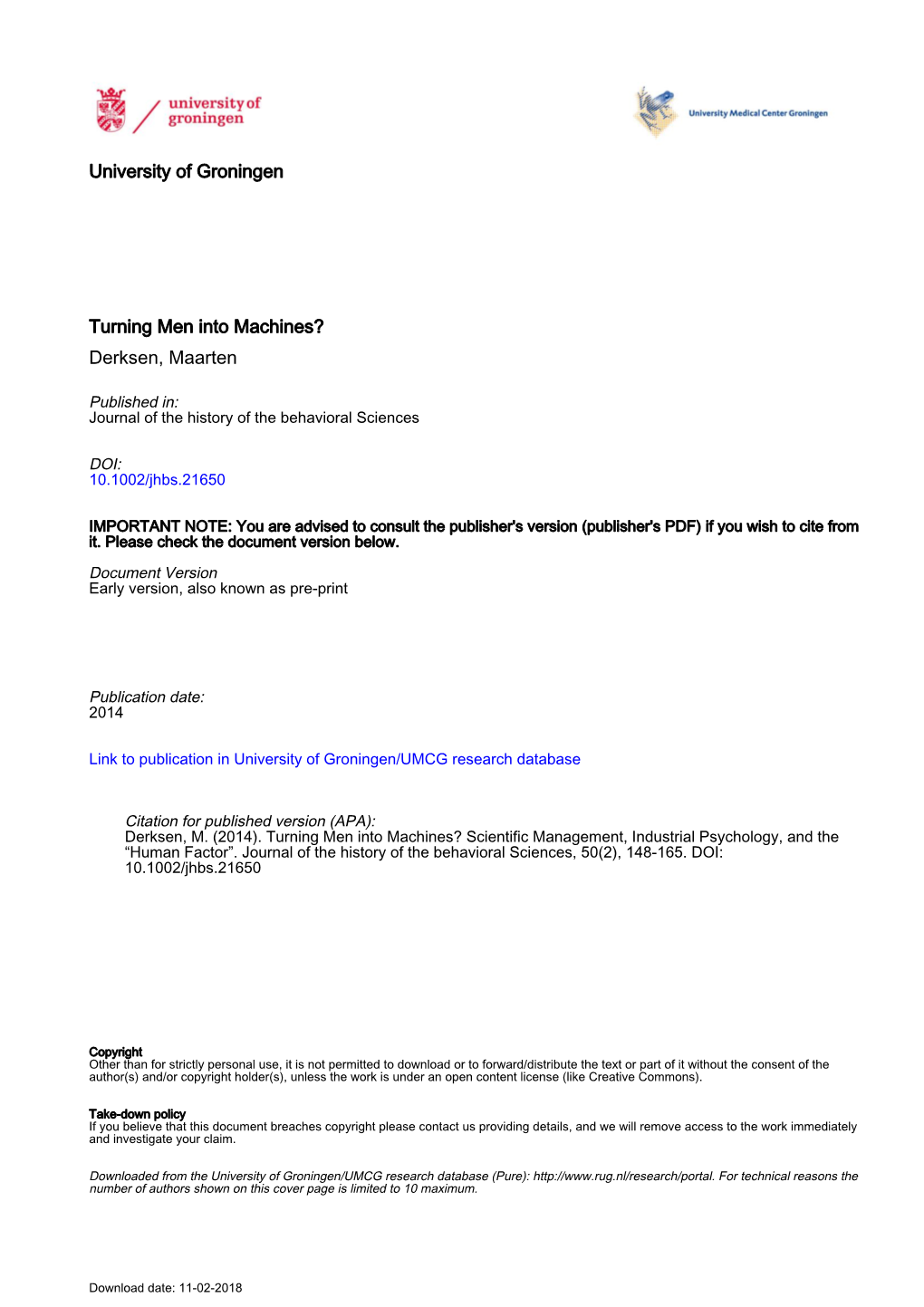
Load more
Recommended publications
-
Leading Edge Thinker: Rediscovering Mary Parker
LEADING-EDGE THINKER: REDISCOVERING MARY PARKER FOLLETT Vincent Moroz APRJ-699 Word Count: 15,525 April 14, 2017 Linda Bramble. Supervisor Mary Parker Follett. (n.d.) Retrieved February 19, 2017, from http://blog.consultorestrategia.com/ 2012/03/la- guru-de-la-administracion-mary.html “Unity, not uniformity, must be our aim. We attain unity only through variety. Differences must be integrated, not annihilated, nor absorbed.” Mary Parker Follett, The New State, 1918, Chapter 3, Para. 28 Vincent Moroz, Applied Project Leading-Edge Thinker: Rediscovering Mary Parker Follett Abstract Our constantly connected society has significantly increased the pressure on business leaders to provide real-time responses to organizational issues and customer concerns. Leaders are expected to maintain control of resources, uncover continual improvements to operations, and actively engage with employees while providing them with job enrichment opportunities. What organizational framework exists to enable business leaders to be successful at achieving all these varied demands in near real-time? This study investigates the unity framework developed by Mary Parker Follett, an early 20 th century social worker who applied practical theories for individual empowerment through community development to the problems facing modern industry. Selections from Follett's catalogue of writings have been analyzed to uncover the framework within. Comparisons are made between Follett's theories and contemporary organizational theories. Mary Follett was internationally recognized following her book The New State being published in 1918. Several identifiable themes are found within Follett's collected writings around which an identifiable framework can be constructed. There are two unique themes showing in Follett's writings which form the core of her framework: the individual and the integrative unity, and, the doctrine of integration. -
A Pragmatist Reading of Mary Parker Follett's Integrative Process
View metadata, citation and similar papers at core.ac.uk brought to you by CORE provided by Scholarworks@GVSU Grand Valley State University ScholarWorks@GVSU Faculty Peer Reviewed Articles Liberal Studies Summer 2014 A Pragmatist Reading of Mary Parker Follett’s Integrative Process Judy D. Whipps Grand Valley State University, [email protected] Follow this and additional works at: http://scholarworks.gvsu.edu/lib_articles Recommended Citation Whipps, Judy D., "A Pragmatist Reading of Mary Parker Follett’s Integrative Process" (2014). Faculty Peer Reviewed Articles. 8. http://scholarworks.gvsu.edu/lib_articles/8 This Article is brought to you for free and open access by the Liberal Studies at ScholarWorks@GVSU. It has been accepted for inclusion in Faculty Peer Reviewed Articles by an authorized administrator of ScholarWorks@GVSU. For more information, please contact [email protected]. Abstract For most of the 20th century Mary Parker Follett (1868–1933) was one of the “invis- ible women” in the history of American philosophy, although her work was taken seriously by philosophers of her time. While some have described Follett as an ideal- A Pragmatist ist, this essay develops the pragmatist and feminist elements of Follett’s philosophy. Reading of In particular, Follett’s concept of “integra- tion” can be clarified by reading it through a pragmatist lens, connecting it with Dew- Mary Parker ey’s writing on experience, and with James- ian pluralism. Follett also shares with Jane Follett’s Addams an understanding of the creative integrative power of diversity; Addams di- Integrative rectly referenced Follett in 1930 when she describes how conflicts were resolved in the Process process of mutual action. -
Democracy and Public Administration Richard C
University of Nebraska Omaha DigitalCommons@UNO Faculty Books and Monographs 2006 Democracy and Public Administration Richard C. Box Gary Marshall University of Nebraska at Omaha, [email protected] Follow this and additional works at: http://digitalcommons.unomaha.edu/facultybooks Part of the Public Administration Commons Recommended Citation Box, Richard C. and Marshall, Gary, "Democracy and Public Administration" (2006). Faculty Books and Monographs. Book 249. http://digitalcommons.unomaha.edu/facultybooks/249 This Book is brought to you for free and open access by DigitalCommons@UNO. It has been accepted for inclusion in Faculty Books and Monographs by an authorized administrator of DigitalCommons@UNO. For more information, please contact [email protected]. A Brief Tour of Public Organization Theory in the United States By: Gary S. Marshall Public administrative organizations in the United States rest on the twin pillars of management and democracy. Because the management processes of public organizations are not solely instrumental but involve the public interest, public agencies have to be more than mechanisms of rationality. Public administrative action has both an instrumental quality, i.e., its capacity for optimal technical rationality (technique), and a social quality-an underlying connection to the social bond between self and other. With this backdrop, we begin the focus of this chapter which recounts the sociology of organizations with an emphasis on key democratic moments in the history of American public administration. Before doing so, we might ask how the central terms used in our discussion will be defined. What are organizations? For the purposes of this chapter, organizations are the basic unit through which virtually all social relations are formed in post-traditional society. -
History of Management
The History of Management outline In the Beginning 4. Human Relations Management 1. The Origins of Management 4.1 Constructive Conflict and 1.1 Management Ideas and Coordination: Mary Parker Practice Throughout History Follett 1.2 Why We Need Managers 4.2 Hawthorne Studies: Elton Today Mayo 4.3 Cooperation and Accep- Evolution of Management tance of Authority: Chester 2. Scientific Management Barnard 2.1 Father of Scientific Manage- 5. Operations, Information, Systems, ment: Frederick Taylor and Contingency Management 2.2 Motion Studies: Frank and 5.1 Operations Management Lillian Gilbreth 5.2 Information Management 2.3 Charts: Henry Gantt 5.3 Systems Management 3. Bureaucratic and Administrative 5.4 Contingency Management Management 3.1 Bureaucratic Management: Key Terms Max Weber 3.2 Administrative Management: Henri Fayol study tip THE HISTORY OF MANAGEMENT We begin by reviewing the origins of management ideas and practice throughout history and the historical changes that produced the need for managers. Next, you’ll learn about various schools of management thought, beginning with scien- tific management. You’ll learn about the key contributions to scientific manage- ment made by Frederick Taylor, Frank and Lillian Gilbreth, and Henry Gantt. Next, you’ll read about Max Weber and bureaucratic management and then about Henri Fayol and administrative management. Following that, you’ll learn about human relations management and the ideas of Mary Parker Follett (con- structive conflict and coordination), Elton Mayo (Hawthorne Studies), and Chester Barnard (cooperation and acceptance of authority). Finally, you’ll learn about the history of operations management, information management, systems management, and contingency management. -
A Pragmatist Reading of Mary Parker Follett's Integrative Process
Grand Valley State University ScholarWorks@GVSU Faculty Peer Reviewed Articles Liberal Studies Summer 2014 A Pragmatist Reading of Mary Parker Follett’s Integrative Process Judy D. Whipps Grand Valley State University, [email protected] Follow this and additional works at: http://scholarworks.gvsu.edu/lib_articles Recommended Citation Whipps, Judy D., "A Pragmatist Reading of Mary Parker Follett’s Integrative Process" (2014). Faculty Peer Reviewed Articles. 8. http://scholarworks.gvsu.edu/lib_articles/8 This Article is brought to you for free and open access by the Liberal Studies at ScholarWorks@GVSU. It has been accepted for inclusion in Faculty Peer Reviewed Articles by an authorized administrator of ScholarWorks@GVSU. For more information, please contact [email protected]. Abstract For most of the 20th century Mary Parker Follett (1868–1933) was one of the “invis- ible women” in the history of American philosophy, although her work was taken seriously by philosophers of her time. While some have described Follett as an ideal- A Pragmatist ist, this essay develops the pragmatist and feminist elements of Follett’s philosophy. Reading of In particular, Follett’s concept of “integra- tion” can be clarified by reading it through a pragmatist lens, connecting it with Dew- Mary Parker ey’s writing on experience, and with James- ian pluralism. Follett also shares with Jane Follett’s Addams an understanding of the creative integrative power of diversity; Addams di- Integrative rectly referenced Follett in 1930 when she describes how conflicts were resolved in the Process process of mutual action. The latter part of Judy Whipps this essay discusses the contemporary rel- evance of Follett’s integrative “power- with” methodology in feminist thought. -
From Ontology to Administration Social Integration According to Mary Follett
Available online at www.pedagogikaspoleczna.com Social Pedagogy 1 (2015) 181-196 ISSN: 1642-672X From ontology to administration Social integration according to Mary Follett Margaret Stout Joannine M. Love Mirosław Patalon Pomeranian University, Slupsk, Poland ABSTRACT American publishing house Process Century Press signed an agrement to publish a manuscript with the working title Integrative Process: Follettian Thinking from Ontology to Administration by Margaret Stout and Jeannine Love in cooperation with Mirosław Patalon. The book will be issued in 2015. In the United States we can observe a growing interest in the work of Mary Parker Follett (1868-1933). So far she was mainly known as a very influential thinker in the field of management. Now she is more associated with public administration and social work. With the permission from Process Century Press to undertake and publish a Polish translation of the manuscript we present here first parts of the book (translated by Miroslaw Patalon). Mary Follett is described here in a wider context of American pragmatism and process philosophy of Alfred North Whitehead. Foreword to the book was written by John B. Cobb, co-funder of the Center for Process Studies in Claremont, California and a distinguished representative of the process philosophy and theology. Key words: Mary Follett, social integration, process philosophy, administration, social work. Artykuł dostępny online na www.pedagogikaspoleczna.com Pedagogika Społeczna 1 (2015) 181-196 ISSN: 1642-672X Od ontologii do administracji Integracja społeczna w ujęciu Mary Follett Margaret Stout Joannine M. Love Mirosław Patalon Akademia Pomorska, Słupsk, Poland STRESZCZENIE Amerykańskie wydawnictwo Process Century Press podpisało umowę na wydanie książki autorstwa Margaret Stout i Jeannine M. -
History of Management
Chapter 2: History of Management TRUE/FALSE 1. Management ideas and practices have actually been used from the earliest times of recorded history. ANS: T PTS: 1 DIF: Easy REF: 42 TOP: AACSB Reflective Thinking KEY: Creation of Value 2. For most of humankind’s history, people have commuted to work. ANS: F For most of history, people have worked in or near their homes and have not commuted. PTS: 1 DIF: Easy REF: 45 TOP: AACSB Reflective Thinking KEY: Creation of Value 3. After the Industrial Revolution, jobs mostly occurred in large, formal organizations where hundreds of people worked under one roof. ANS: T PTS: 1 DIF: Easy REF: 45-46 TOP: AACSB Reflective Thinking KEY: Group Dynamics | Operations Management 4. Frederick Taylor was the father of systems management. ANS: F Frederick Taylor was the father of scientific management. PTS: 1 DIF: Easy REF: 47 TOP: AACSB Reflective Thinking KEY: Operations Management | HRM | Leadership Principles 5. One of Taylor’s scientific management principles concerned how workers should be selected. ANS: T The second principle of scientific management was to scientifically select, train, teach, and develop workers to help them reach their full potential. See Exhibit 2.2. PTS: 1 DIF: Easy REF: 48 TOP: AACSB Reflective Thinking KEY: HRM 6. According to the principles of scientific management, work and the responsibility for the work should be divided equally between workers and management. ANS: T See Exhibit 2.2 PTS: 1 DIF: Moderate REF: 48 TOP: AACSB Reflective Thinking KEY: Operations Management 7. K-M-S Industries in Ohio specializes in making one-of-a-kind precision parts for performance racing, energy, transportation, and aerospace applications. -
Examining Management History Through the Lens of Critical Biography Jane Whitney Gibson, Nova Southeastern University, USA
International Journal of Management & Information Systems – Third Quarter 2014 Volume 18, Number 3 Examining Management History Through The Lens Of Critical Biography Jane Whitney Gibson, Nova Southeastern University, USA ABSTRACT This paper builds a case for using the qualitative methodology of critical biography to illuminate the life, times, and contributions of pioneers in the field of management history. First the importance of management history is discussed and the critical biography methodology is described. Then, the methodology is applied to management history through examining several articles using the methodology including articles about Mary Parker Follett and Rhona Rapaport. Pros and cons of using the methodology are discussed including approachability and high interest level as pros and necessity to make inferences and the close interplay between researcher and research as cons. Implications for future research are presented. Keywords: Qualitative Research; Biography; Critical Biography INTRODUCTION any academics would say that the value of quantitative research is considerably greater than the value of qualitative research because of its rigor, quantitative methodologies, data sets, and ability M to test complicated hypotheses. Others defend qualitative research as being better able to represent the real world where shades of grey predominate and where research consumers (the readers) may not find qualitative methodology appealing or applicable. One author posits that “The quantitative and qualitative research traditions can be thought of as distinct cultures marked by different values, beliefs, and norms (Mahoney, 2006, p. 227). Others see merit in both and suggest that qualitative and quantitative methods actually rely on each other. Says Trochim (2006), all qualitative data can be quantified when ordered into themes and all quantitative data relies on the qualitative reporting of survey data where respondents are often asked to “grade” their answer on an arguably subjective Likert scale. -
CREATIVE EXPERIENCE by M.P. Follett INTRODUCTION the Social
CREATIVE EXPERIENCE - INTRODUCTION MARY PARKER FOLLETT (1924) CREATIVE EXPERIENCE by M.P. Follett INTRODUCTION THE social sciences are not gathering all the fruits of certain recent developments of thought; they are not all of them even using the most modern method of study, which is wholly to abandon the region of abstract speculation and to study the behavior of men. Many political scientists talk about conferring power without analyzing power; many economists talk about representation in industry without analyzing representation; there are sociologists who talk about individual and social interests without sufficiently analyzing the difference, if there is one, between individual and social interests. In a book by a recent writer on politics these four words are used in a sentence of three lines: power, purpose, freedom, service. But the author has not told us what these words mean − and we do not know. We can find out only by watching in thousands of cases the working of power, purpose, freedom, only by watching the behavior of men. The greatest need of today is a keen, analytical, objective study of human relations. We preach “compromise” as the apex of the ethical life, we laud the “balance of power” as our political and international faith, we give our substance and ourselves to establish an “equilibrium” of nations. But compromise sacrifices the integrity of the individual, and balance of power merely rearranges what already exists; it produces no new values. No fairer life for men will ever be the fruit of such doctrine. By adherence to such a creed we bind ourselves to equivalents, we do not seek the plusvalents of experience. -
Mary Parker Follett and Joseph Smith on Collaborative Leadership
Voices from the Past: Mary Parker Follett and Joseph Smith on Collaborative Leadership Mark E. Mendenhall J. Burton Frierson Chair of Excellence in Business Leadership College of Business Administration University of Tennessee, Chattanooga 615 McCallie Avenue Chattanooga, TN 37403 [email protected] TEL: 423-886-4243 W. Jeffrey Marsh Associate Professor of Ancient Scripture College of Religious Education Brigham Young University 365F JSB Provo, UT 84602 [email protected] TEL: 801-422-3371 2 Voices from the Past: Mary Parker Follett and Joseph Smith on Collaborative Leadership Abstract The post-war literature has yielded important insights regarding developing collaborative leadership competencies in managers and collaborative leadership systems within organizations. However, the work of pre-World War II scholars and practitioners in this area has largely been overlooked. After introducing you to Mary P. Follett and Joseph Smith via a interview, based on our review of the work of two of these early scholars/practitioners we propose an extension of Raelin’s 2006 framework of collaborative leadership and discuss implications of their work for current management development efforts associated with developing collaborative leadership in organizations 3 Voices from the Past: Mary Parker Follett and Joseph Smith on Collaborative Leadership Raelin (2006) has observed that in the past decade there has been an increase in interest on the part of both scholars and practitioners in better understanding both the dynamics of collaborative leadership -
The American New State of Mary Parker Follett
International Journal of Sociology and Anthropology Vol. 3(3) pp.101-108, March 2011 Available online http://www.academicjournals.org/ijsa ISSN 2006- 988x ©2011 Academic Journals Review The American New State of Mary Parker Follett Wasim I. Al-Habil College of Commerce, The Islamic University, Occupied Palestinian Territories, Gaza. E-mail: [email protected]. Accepted February 2, 2011 This research tries to answer one of the major questions that has been discussed in the literature of Public Administration (PA) repeatedly. The question is: Has 21st century American government succeeded in achieving a genuinely democratic administration where efficiency and democratic values are reconciled? The main argument of this research is that it has not been possible in spite of the calls of many public administration theories which have encouraged the adoption of Follett’s equation based on the partnership between efficient government and active citizen participation. The research argues that Follett’s assertion sounds rather optimistic but it has not been implemented seriously on the ground. Key words: Public administration, efficient government, and active citizen participation. INTRODUCTION It seems that the main point Mary Parker Follett tried to encouraged the adoption of Follett’s equation based on assert is one of the basic concepts that have shaped the the partnership between efficient government and active field of public administration (PA) since Woodrow (1887) citizen participation. The research argues that Follett’s established PA as a field of study. Follett believes that assertion sounds rather optimistic but it has not been the notions of active citizenship and efficient government implemented seriously on the ground. -
Conflict Research Centre (CRC)
Conflict Research Centre (CRC) CRC Working Paper No. 1 Reconciling the carrot and the stick: An intellectual history of integrative bargaining in 20th century American organizational relations Jennifer Jones-Patulli [email protected] July 2011 This paper was originally submitted in partial fulfilment of the requirements for the degree of MA in Conflict Studies at Saint Paul University, Ottawa. Working Paper Series Conflict Research Centre Saint Paul University, Ottawa Based at Saint Paul University in Ottawa, the Conflict Research Centre (CRC) aims to contribute to the advancement of the field of conflict studies, applied peace research, and peacebuilding within Canada and internationally by conducting research and training to foster dialogue, and promote constructive responses to defusing conflict and building sustainable and just peace. The CRC Working Paper Series aims to facilitate the dissemination of new research findings and work in progress by CRC researchers and associates. The papers are intended to stimulate discussion of new research in the field of conflict studies by scholars, practitioners and policymakers. The CRC Working Papers are available to download free of charge through the CRC website. The views expressed in the CRC Working Papers are those of the author(s), and do not represent those of the CRC or Saint Paul University. Comments on the Working Papers should be directed to the author(s). For more information, please contact: Conflict Research Centre (CRC) Saint Paul University 223 Main Street Ottawa,