Study of Piston Engine
Total Page:16
File Type:pdf, Size:1020Kb
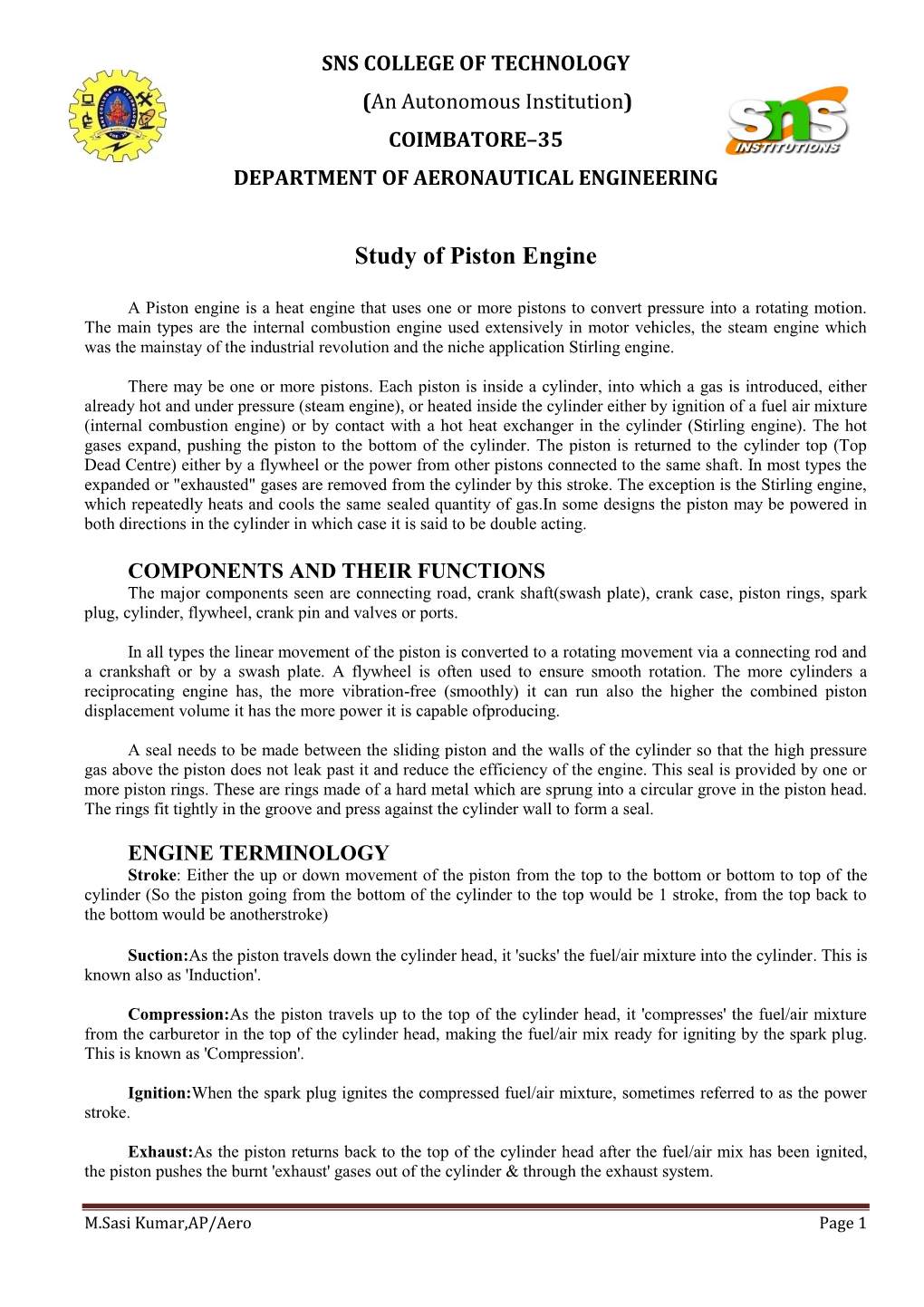
Load more
Recommended publications
-
Cylinder Deactivation: a Technology with a Future Or a Niche Application?: Schaeffler Symposium
172 173 Cylinder Deactivation A technology with a future or a niche application? N O D H I O E A S M I O U E N L O A N G A D F J G I O J E R U I N K O P J E W L S P N Z A D F T O I E O H O I O O A N G A D F J G I O J E R U I N K O P O A N G A D F J G I O J E R O I E U G I A F E D O N G I U A M U H I O G D N O I E R N G M D S A U K Z Q I N K J S L O G D W O I A D U I G I R Z H I O G D N O I E R N G M D S A U K N M H I O G D N O I E R N G E Q R I U Z T R E W Q L K J P B E Q R I U Z T R E W Q L K J K R E W S P L O C Y Q D M F E F B S A T B G P D R D D L R A E F B A F V N K F N K R E W S P D L R N E F B A F V N K F N T R E C L P Q A C E Z R W D E S T R E C L P Q A C E Z R W D K R E W S P L O C Y Q D M F E F B S A T B G P D B D D L R B E Z B A F V R K F N K R E W S P Z L R B E O B A F V N K F N J H L M O K N I J U H B Z G D P J H L M O K N I J U H B Z G B N D S A U K Z Q I N K J S L W O I E P ArndtN N BIhlemannA U A H I O G D N P I E R N G M D S A U K Z Q H I O G D N W I E R N G M D A M O E P B D B H M G R X B D V B D L D B E O I P R N G M D S A U K Z Q I N K J S L W O Q T V I E P NorbertN Z R NitzA U A H I R G D N O I Q R N G M D S A U K Z Q H I O G D N O I Y R N G M D E K J I R U A N D O C G I U A E M S Q F G D L N C A W Z Y K F E Q L O P N G S A Y B G D S W L Z U K O G I K C K P M N E S W L N C U W Z Y K F E Q L O P P M N E S W L N C T W Z Y K M O T M E U A N D U Y G E U V Z N H I O Z D R V L G R A K G E C L Z E M S A C I T P M O S G R U C Z G Z M O Q O D N V U S G R V L G R M K G E C L Z E M D N V U S G R V L G R X K G T N U G I C K O -
1 Active Stirling Engine a Thesis Submitted in Partial Fulfilment of The
Active Stirling Engine A thesis submitted in partial fulfilment of the requirements for the Degree of Doctor of Philosophy in Electrical Engineering in the University of Canterbury by Vinod Kumar Gopal University of Canterbury 2012 1 Table of Contents ACKNOWLEDGMENTS 12 ABSTRACT 14 GLOSSARY 16 1. INTRODUCTION AND HISTORY OF STIRLING ENGINE DEVELOPMENT 22 1.1 Reverend Robert Stirling and his engine 23 1.2 Philips Stirling engine development 24 1.3 Other notable Stirling engine developments 28 1.4 Stirling engine development in Japan 29 1.5 Stirling engine development in US 29 1.6 Development in Stirling engine refrigeration and cryocooling 30 2. COMBINED HEAT AND POWER OR CHP SYSTEMS 34 2.1 Introduction to CHP systems 34 2.2 WhisperGen ® microCHP systems 38 2.3 Control of existing microCHP systems 40 3. FUNDAMENTALS OF STIRLING ENGINES 44 3.1 Introduction to Stirling engine technology 44 3.2 Thermodynamic cycles 45 3.3 The Stirling cycle 48 2 3.4 Ideal and conventional Stirling engines 51 3.5 Stirling engine control 55 3.6 Temperature control of Stirling engines 55 3.7 Pressure control of Stirling engines 55 3.8 Stroke control of Stirling engines 56 3.9 Phase control in Stirling engines 57 3.10 Dead volume control 58 3.11 Speed control 58 4. THE PROBLEM TO BE SOLVED 60 4.1 Effect of phase angle on Stirling engine performance 60 4.2 Controllability of current microCHP systems 61 4.3 Making use of phase control 64 4.4 Sinusoidal vs. non linear motion of reciprocating parts 64 4.5 Achieving phase control and non linear control 66 5. -
How Many Valves Per Cylinder (Revised) – 0, 1, 2, 3, 4, 5, Or 8? with Illustrations and a P.S
DST 20 February 2015. P.1 of 13 How many valves per cylinder (revised) – 0, 1, 2, 3, 4, 5, or 8? With illustrations and a P.S. on 6 Since 1993 all Formula 1 engine designers have chosen 4 poppet valves per cylinder (2 inlet, 2 exhaust). In 2006 this layout was actually specified in the FIA regulations and the new 2014 rules continue it. Keith Duckworth, who created in 1966 a cylinder head having 4 valves per cylinder (4 v/c) opposed at a relatively narrow angle and combined them with port geometry and increased valve Lift/Diameter ratio to create in-cylinder “Barrel Turbulence” (aka “Tumble Swirl”) to raise combustion efficiency, set a benchmark to which, in time, all competitors conformed and which spread far outside the racing arena. In most of the past century this unanimity on 4 v/c did not exist. Racing 4-stroke piston engines were built with 2, 3, 4, 5, and 8 poppet valves per cylinder. This article follows the title subject generally from the series of 85 “Grand Prix Cars-of-the-Year”, 1906 – 2000, listed in this web site . Specifically this admits only 2, 3, and 4 valves per cylinder so, for general interest, substantial diversions have been included to other racing engines with a wider variety of arrangements In future references to “valve gear” it is to be understood that it refers to poppet valves opened by cams, directly or indirectly, and closed by steel springs forcing them to ride on the cam, unless otherwise mentioned (Desmodromic gear in Mercedes 1954-1955 (DVRS) and Pneumatic Valve Return Systems (PVRS) post-1990). -
Xxxciclo Del Dottorato Di Ricerca in Ingegneria E Architettura
UNIVERSITÀ DEGLI STUDI DI TRIESTE XXX CICLO DEL DOTTORATO DI RICERCA IN INGEGNERIA E ARCHITETTURA CURRICULUM INGEGNERIA MECCANICA, NAVALE, DELL’ENERGIA E DELLA PRODUZIONE WASTE HEAT RECOVERY WITH ORGANIC RANKINE CYCLE (ORC) IN MARINE AND COMMERCIAL VEHICLES DIESEL ENGINE APPLICATIONS Settore scientifico-disciplinare: ING-IND/09 DOTTORANDO SIMONE LION COORDINATORE PROF. DIEGO MICHELI SUPERVISORE DI TESI PROF. RODOLFO TACCANI CO-SUPERVISORE DI TESI DR. IOANNIS VLASKOS ANNO ACCADEMICO 2016/2017 Author’s Information Simone Lion Ph.D. Candidate at Università degli Studi di Trieste Development Engineer at Ricardo Deutschland GmbH Early Stage Researcher (ESR) in the Marie Curie FP7 ECCO-MATE Project Author’s e-mail: • Academic: [email protected] • Industrial: [email protected] • Personal: [email protected] Author’s address: • Academic: Dipartimento di Ingegneria e Architettura, Università degli Studi di Trieste, Piazzale Europa, 1, 34127, Trieste, Italy • Industrial: Ricardo Deutschland GmbH, Güglingstraße, 66, 73525, Schwäbisch Gmünd, Germany Project website: • ECCO-MATE Project: www.ecco-mate.eu Official acknowledgments: The research leading to these results has received funding from the People Programme (Marie Curie Actions) of the European Union’s Seventh Framework Programme FP7/2007-2013/ under REA grant agreement n°607214. Abstract Heavy and medium duty Diesel engines, for marine and commercial vehicles applications, reject more than 50-60% of the fuel energy in the form of heat, which does not contribute in terms of useful propulsion effect. Moreover, the increased attention towards the reduction of polluting emissions and fuel consumption is pushing engine manufacturers and fleet owners in the direction of increasing the overall powertrain efficiency, still considering acceptable investment and operational costs. -
Gordon Murray Automotive Reveals Details for Its New 'T.50'
5 June 2019 Gordon Murray Automotive reveals details for its new ‘T.50’: the purest, lightest, most driver-focused supercar ever Designed to the same exacting engineering standards as the driver-focused McLaren F1; improves upon its iconic predecessor in every way Mid-engine and rear-wheel-drive layout; famed central driving position and H-pattern gearbox all key to a matchless experience behind the wheel All-new V12 to be the highest-revving engine ever used in a production car; produces unrivalled power-to-weight ‘Fan car’ technology delivers the most advanced aerodynamics yet seen on a road car Unique carbon fibre tub and a focus on minimising the weight of every component underpin ‘lightweighting’ strategy – overall weight is just 980kg New model will set new standards for supercar packaging, providing driver and two passengers with exceptional comfort, safety, practicality and luggage space Only 100 exclusive models to be produced costing in excess of £2m (before taxes); deliveries from early 2022. Gordon Murray Automotive, sister-business of visionary vehicle design and engineering company Gordon Murray Design, has announced details of its first vehicle – the T.50 supercar. Conceived as the spiritual successor to the Murray-devised McLaren F1, the T.50 will be the purest, lightest, most driver-focused supercar ever built. The development of T.50 is at an advanced stage, with full production and customer deliveries set to commence in early 2022. Just 100 owners of the T.50 will experience Murray’s vision – a supercar inspired by his 50 years at the pinnacle of Formula One and automotive industry engineering and design. -
Service Training Course 703 Jaguar Climate Control Systems
JAGUARJAGUAR SERVICE TRAINING SERVICE TRAINING COURSE 703 JAGUAR CLIMATE CONTROL SYSTEMS ISSUE ONE DATE OF ISSUE: 07/01/2002 This publication is intended for instructional purposes only. Always refer to the appropriate Jaguar Service publication for specific details and procedures. All rights reserved. All material contained herein is based on the latest information available at the time of publication. The right is reserved to make changes at any time without notice. Publication T703/02 DATE OF ISSUE: 07/01/2002 © 2002 Jaguar Cars PRINTED IN USA JAGUAR CLIMATE CONTROL SYSTEMS Service Training INTRODUCTION Jaguar Climate Control Systems provide vehicle occupants with year-round automatic temperature and humidity control as selected on the control panel. The vehicle heating and air-conditioning systems are the foundation for providing the warm, cool or combined warm/cool air necessary to meet the desired conditions. Using advanced electronic components and a microprocessor-based control module, the Climate Control Systems produce a contin- uously comfortable environment over a wide range of ambient conditions. CLIMATE CONTROL SYSTEMS INTEGRATION CLIMATE CONTROL ENGINE CONTROL HEATER WARM AIR COOLANT VALVE MATRIX AS REQUIRED: HEATING CLIMATE CONTROL COOLING WARM / COOL BLEND A/C A/C EVAPORATOR COOL / DRY AIR SYSTEM CONTROLS MATRIX CLIMATE CONTROL T703.01 NOTES Date of Issue: 07/01/2002 Student Guide i JAGUAR CLIMATE CONTROL SYSTEMS Service Training ACRONYMS AND ABBREVIATIONS The following abbreviations and acronyms are used throughout the -
Jag Club Annual Holiday Party
april 2015 spring issue jag club annual holiday party R Dale and Barb Martin receive a Life Membership from President Dan Buchen jaguar club of minnesota newsletter PResidents’ Corner Spring has sprung. We are on the grid, ready to shift into driving season. We have had our time in the shop and pad- dock with tech sessions and social gatherings for food and drink. We are now ready for the checkered flag to signal the 1st driving events of the year. This year I have new ride. Cholmondeley (Chumley) just bought a Jaguar. After long car and soul searching, last week I acquired a 1995 XJ6. This is the last version of the inline 6 (AJ16) upgraded to 241 HP and the first version of the X300 body later used for the XJ8. I first saw her on Craig’s list: an online match-making site for guys and cars. It was love at first sight—the same red finish as my last XJ6, a youthful 85,000 miles, and a rust-free South Carolina chassis. After peeling away the onion-like layers of communication on Craig’s list: email, text, phone calls, we met. Our first date was a little rough. Her finish was not so perfect in person and she was slightly incontinent. I couldn’t seal the deal until I had a professional opinion. I made an appoint- ment with Jeff Flynn for a prenuptial inspection. The body was as sound and straight as advertised. The leaks proved to be superficial, fixable and not a sign of imminent catastro- phe. -
Initial Tech. Training (CE-28)
Click Here & Upgrade Expanded Features PDF Unlimited Pages CompleteDocuments COURSE MODULE Course No. CE 28: Initial Technician-III Duration: 13 Weeks Effective Days: 75 S. CM Sessions Periods N. No. Subjects 1 28.1 36 1-106 Electrical & Electronics 2 28.2 Hydraulics, Pneumatics & Mechanical 36 107-189 3 28.3 I.C. Engine & Workshop Technology 36 190-250 4 28.4 Track Machines & Working Principles 36 251-362 5 28.5 P.Way, Establishment, Stores & Rajbhasha 36 363-417 6 28.6 Group Inter Personal Skill Development (GIPSD) 7 418-423 7 28.7 Computer 10 424-443 8 5 Technical Film Show 9 Library 5 10 Visit to CPOH & Track Machines Working Sites 20 11 Examination (Theory/Practical/Viva-voce) & Valediction 17 244 443 T Note: 1. Eligibility: Directly Recruited Technician-III and such Promoted Technician-III, who has no exposure of track machines working. 2. Medical Awareness Programme shall be covered under Module No. 28.5. Faculty for this programme may be drawn from Medical Department. 3. Faculty for GIPSD may be drawn from CBWE, Min. of Labour & Employment or from Management Institutes. 4. Computer, Technical Film Show and Library periods shall be scheduled during the afternoon session. 5. To bridge the gap between theory and practical, fortnightly visit to CPOH for demonstration and giving hands-on training and monthly visit Track Machines Working Sites for proper understanding of machine working shall be arranged. 6. Practical demonstration in Model rooms shall be given along with theoretical sessions as and when required besides Practical sessions specifically earmarked for Model Rooms. -
Db11 Now Offered with V8 Engine
SUBLIME CHOICES: DB11 NOW OFFERED WITH V8 ENGINE • DB11 now available with choice of twin-turbocharged 4.0-litre V8 or 5.2-litre V12 engines • New V8 delivers 503bhp and 675Nm with a CO2 figure of 230g/km After its successful global introduction in 2016, Aston Martin’s definitive GT - the acclaimed DB11 - is now available with a 4.0-litre twin-turbocharged V8 engine. Perfectly complementing the DB11’s existing 5.2-litre twin turbocharged V12 engine, this new powerplant has provided the opportunity to reveal more of the DB11’s sporting character, while expanding its global appeal with a combination of exceptional performance and improved efficiency. Producing 510PS (503BHP) and 675Nm of torque, the V8 engine’s potency is beyond question, propelling the DB11 from 0-62mph in just 4.0sec and on to a top speed of 187mph. This exceptional performance is matched by impressive efficiency: CO2 emissions of 230g/km and an EU Combined fuel economy figure of 28.5mpg. This new V8 derivative brings further significant benefits in markets where car taxation policy is structured around engine capacity, such as China. Aston Martin Chief Technical Officer, Max Szwaj, commented: “As an engineer I find the DB11 a fascinating car. One with great depth of character and ability. Of course the V12-engined variant is an icon - an ultimate, if you like, but the V8 is very much its own car. One with a distinct and carefully crafted character that’s truly seductive. It has been hugely rewarding to put our stamp on this new engine - both in the way it sounds and performs - and to use its impressive attributes as the impetus to reveal a little more of the DB11’s sporting character. -
The History of the Gasoline Engine at Mercedes-‐ Benz
Contact: Josef Ernst Telephone: +49 (0) 711-17-7 64 Press Information 77 Date: June 2008 The history of the gasoline engine at Mercedes- Benz THE HISTORY OF THE GASOLINE ENGINE AT MERCEDES-BENZ ............................... 2 THE DEVELOPMENT OF THE GASOLINE ENGINE ....................................................... 4 CARL BENZ AND THE HIGH-SPEED FOUR-STROKE ENGINE ................................... 13 GOTTLIEB DAIMLER, WILHELM MAYBACH AND THE “GRANDFATHER CLOCK” .. 24 THE MERCEDES-BENZ GASOLINE ENGINE FROM 1926 ON .................................. 46 MERCEDES-BENZ GASOLINE ENGINES AFTER THE SECOND WORLD WAR ........... 53 THE CARBURETOR ERA COMES TO AN END ........................................................... 79 MERCEDES-BENZ GASOLINE ENGINES IN RESEARCH AND MOTOR SPORTS ......... 108 TIMELINE: THE HISTORY OF THE GASOLINE ENGINE AT MERCEDES-BENZ AND ITS PREDECESSOR COMPANIES .................................................................................. 120 Daimler Communications, 70546 Stuttgart/Germany The history of the gasoline engine at Mercedes- Page 2 Benz • Unparalleled development of the gasoline engine since the invention of the automobile in 1886 • Technological potential far from exhausted The four-stroke gasoline engine was the heart of the first modern automobile designed by Gottlieb Daimler and Carl Benz in 1886. Independently of one another, the two pioneers developed small, high-speed engines, based on Nikolaus Otto’s four-stroke principle, for the drive system of new automobiles. Since the use of these engines in the Benz patent motor car and Daimler’s motor carriage, the four-stroke gasoline engine has experienced unparalleled development. With their constant innovation, Daimler AG and its predecessor companies have played an important role in the success story of this internal combustion engine for more than 120 years. It was thanks to their tireless worK that the single-cylinder power unit of the automobile pioneers became an ultra-modern drive system, especially for passenger cars. -
Hydrogen-Fueled Internal Combustion Engines
Hydrogen-Fueled Internal Combustion Engines Sebastian Verhelsta,∗, Thomas Wallnerb aDepartment of Flow, Heat and Combustion Mechanics, Ghent University, Sint-Pietersnieuwstraat 41, B-9000 Gent, Belgium bEnergy Systems Division, Argonne National Laboratory, Building 362, 9700 South Cass Avenue, Argonne, IL 60439-4815, USA Abstract The threat posed by climate change and the striving for security of energy supply are issues high on the political agenda these days. Governments are putting strate- gic plans in motion to decrease primary energy use, take carbon out of fuels and facilitate modal shifts. Taking a prominent place in these strategic plans is hydrogen as a future en- ergy carrier. A number of manufacturers are now leasing demonstration vehi- cles to consumers using hydrogen-fueled internal combustion engines (H2ICEs) as well as fuel cell vehicles. Developing countries in particular are pushing for H2ICEs (powering two- and three-wheelers as well as passenger cars and buses) to decrease local pollution at an affordable cost. This article offers a comprehensive overview of H2ICEs. Topics that are dis- cussed include fundamentals of the combustion of hydrogen, details on the differ- ent mixture formation strategies and their emissions characteristics, measures to convert existing vehicles, dedicated hydrogen engine features, a state of the art on increasing power output and efficiency while controlling emissions and modeling. Key words: hydrogen, internal combustion engine, NOx emissions, direct injection, port fuel injection, abnormal combustion Contents 1 Introduction 7 ∗Corresponding author. Tel.: +32 9 264 3306; fax: +32 9 264 3590. Email addresses: [email protected] (Sebastian Verhelst), [email protected] (Thomas Wallner) Preprint submitted to Elsevier August 19, 2009 1.1 Incentives and drawbacks for hydrogen as an energy carrier . -
BMW Corporate Communications
BMW Corporate Communications Press Release October 2012 25 years of BMW 12-cylinder engines: setting new standards in the luxury class. Munich. BMW’s second-generation 7 Series, unveiled in 1986, featured two new top-of-the-range sedans whose formidable six-cylinder in-line engines generated universal enthusiasm in the motoring media. Nevertheless, it was an open secret that an even bigger star was waiting in the wings: the first German 12-cylinder luxury model in half a century. Expectations were running high, fuelled by BMW’s release of various advance details of the new model’s technical specifications. In September 1986, one news magazine informed its readers: “BMW will be opting for an aero engine- style design. That means most engine systems on the 12-cylinder 7 Series model, which is due for market release in June 1987, will be duplicated. There will even be two lambda sensors. And even if half the engine capacity failed, for some reason, speeds of over 200 km/h would be possible even on just six cylinders.” Last but not least, BMW’s development chief at the time was quoted as saying: “if the engineers wanted to go for nothing but the best of everything, we didn’t try to stop them.” The rumour mill was rife with speculation about the future top-of-the-line engine’s capabilities. One story doing the rounds claimed that: “BMW is doing everything it can to promote a sense of exclusiveness and cachet. They even want the licensing authorities to allow them to state the performance not in figures but in words – to the effect that the engine is appropriate in power and performance for the requirements of the vehicle.” In February 1987, BMW finally put an end to the speculation and released the technical specifications of the 12-cylinder engine in the new BMW 750i, ahead of its world debut at the Geneva Motor Show the following month.