A Novel Hybrid Vehicle Architecture: Modeling, Simulation and Experiments
Total Page:16
File Type:pdf, Size:1020Kb
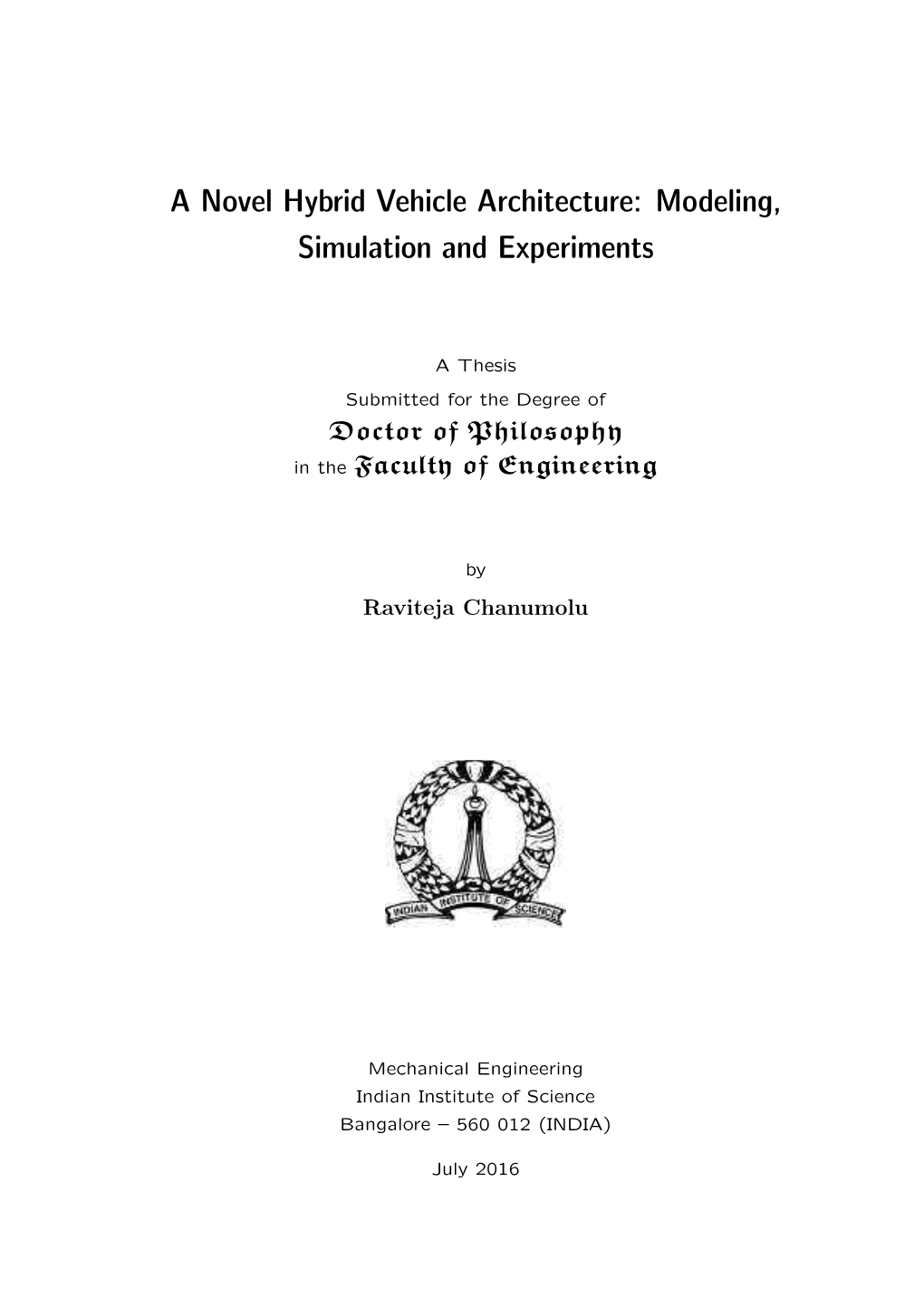
Load more
Recommended publications
-
Transport in India Transport in the Republic of India Is an Important
Transport in India Transport in the Republic of India is an important part of the nation's economy. Since theeconomic liberalisation of the 1990s, development of infrastructure within the country has progressed at a rapid pace, and today there is a wide variety of modes of transport by land, water and air. However, the relatively low GDP of India has meant that access to these modes of transport has not been uniform. Motor vehicle penetration is low with only 13 million cars on thenation's roads.[1] In addition, only around 10% of Indian households own a motorcycle.[2] At the same time, the Automobile industry in India is rapidly growing with an annual production of over 2.6 million vehicles[3] and vehicle volume is expected to rise greatly in the future.[4] In the interim however, public transport still remains the primary mode of transport for most of the population, and India's public transport systems are among the most heavily utilised in the world.[5] India's rail network is the longest and fourth most heavily used system in the world transporting over 6 billionpassengers and over 350 million tons of freight annually.[5][6] Despite ongoing improvements in the sector, several aspects of the transport sector are still riddled with problems due to outdated infrastructure, lack of investment, corruption and a burgeoning population. The demand for transport infrastructure and services has been rising by around 10% a year[5] with the current infrastructure being unable to meet these growing demands. According to recent estimates by Goldman Sachs, India will need to spend $1.7 Trillion USD on infrastructure projects over the next decade to boost economic growth of which $500 Billion USD is budgeted to be spent during the eleventh Five-year plan. -
Techno-Economic Investigation of Solar Powered Electric Auto-Rickshaw for Sustainable Transport System
Preprints (www.preprints.org) | NOT PEER-REVIEWED | Posted: 4 May 2017 doi:10.20944/preprints201705.0033.v1 Peer-reviewed version available at Energies 2017, 10, , 754; doi:10.3390/en10060754 Article Techno-Economic Investigation of Solar Powered Electric Auto-Rickshaw for Sustainable Transport System S. Aravindhan 1, K. S. Reddy 1,* and Tapas K. Mallick 2 1 Heat Transfer and Thermal Power Laboratory, Department of Mechanical Engineering, Indian Institute of Technology Madras, Chennai – 600036, India; [email protected] 2 Environment and Sustainability Institute; University of Exeter, Penryn Campus, Penryn, Cornwall TR10 9FE, UK; [email protected] * Correspondence: [email protected]; Tel: 91- 44 – 22574702; Fax: 91- 44 –22574652 Abstract: The technologies influencing alternative ways of transportation are augmenting in recent years due to increasing urbanization and motorization. In this paper, a solar powered electric auto- rickshaw (SPEA) is designed and developed for Indian conditions. The developed vehicle is comprehensively analyzed techno-economically for its viability in the Indian market. The performance analysis of SPEA results in an optimal charging rate of 2 kWh per day with an average solar irradiance of 325 W/m2 in a typical sunny day. The discharging characteristics are studied based on different loading conditions. The vehicle achieved a maximum speed of 21.69 km/h with battery discharge rate of 296W at 90kg load and also reached a maximum discharge rate of 540W at 390kg loading with a maximum speed of 12.11 km/h. The environmental analysis of SPEA indicated yearly CO2 emissions of 1,777 kg, 1,987 kg and 1,938 kg using Compressed Natural Gas, Liquefied Petroleum Gas and gasoline engines respectively can be mitigated using SPEA. -
Lok Sabha Debates
Eig~~~_Series, Vol. V No. 39 WedDesday~ May 8. 1985 Vaisakha 18. 1907 (Saka) LOK SABHA DEBATES.. (English Version) Second Session (Eighth Lok Sabha) (Vol. V contains Nos. 31 10 40) L()K SAUHA SECRETARIAT NEW DELHI Price IRs. 4.00 '.,' , , I, L L " ., ~ , I .,'.~ " r 'f ,'r,:' .... {.:"I , ~'. I , • :1 1 •• • ' , I I, I \ • ',I ~ ',~ , I', ,.' ,I r",',,' .' '~ " 1 ,,"',"1 , ','I,' t : f" , : , ," '/" L , ".' r r .,1: I_)" 1 "), , " \ . ~ : , '[Original, ~nglish, proceedings included in E'nglish Version ,and Original .H,indt, proc'~'eding. included in Hi.ndi Version', wiJl b'a treated '81 o authorilativ.' and nat the t'8n~'.,tJon thereof] CONTBNTS No. 39, W,dM,day. May 8, 1985/Yal,"""a 18, 1907 (Saka) COLUMNS Oral Answers to Questions: *Starred Questions Nos. 7S0 to 755 1-31 Wti tten Answers to QuestioDS : Starred Questions Nos. 156 to 770 ... 32-49 Unstarred Questions Nos. : SS42 to 5620. 5622 10 5778 ... 49-270 Papers laid on tbe Table ... 271·276 Calling Attention to Metter of Urgct Public Importance- 276 Reported supply of maps of sensitive and restricted areas in Kerala and Indo-Burma border by some Don-official agencies to some foreign agencies witbout obtainiDI prior clearance Shri Indraji t Gupta 276 Shri S.B. Chavan 376 Shri lai Parkash Asarwal ... 283 Shri Zainul Basber 296 Shri NarayaD Choubey ... 30J Matters under rule 377 (i) Need to constitute a Commission and take other effective steps to remove the lI'iovaaces of small regional now-papers Shri K'..N. Pradban ••• 306 (ii) Need to initiate necessary measures to stop UD authorised reproduction of books of Indian authors in Baglades Shrimati Geeta Mukherjeo .. -
Designing the User Experience of Auto-Rickshaw Commuters in Mumbai City
Designing The User Experience Of Auto-rickshaw Commuters In Mumbai City Jesal Chitalia NSCAD University Masters of Design 2018 Designing The User Experience Of Auto-Rickshaw Commuters In Mumbai City By Jesal Chitalia This thesis is submitted to The School of Graduate Studies in partial fulfillment of the requirements for The Master of Design Degree. Approved By : Dr. Rudi Meyer (Director, Master of Design Program) Professor Michael LeBlanc (Division of Design) Designing The User Experience Of Auto-Rickshaw Commuters In Mumbai City Thesis project based on the Auto Rickshaw transit system in Mumbai, India. A thesis project presented to The School of Graduate Studies - Nova Scotia College of Art & Design in partial fulfillment of the Requirements for The Master of Design Degree Program. By Jesal Chitalia NSCAD University, Halifax, Nova Scotia Canada April 2018 This thesis focuses on auto rickshaw transport in Mumbai city and the challenges faced by its users. Auto rickshaws have survived in the country since the era of the British; they are small three-wheeled vehicles which serve as a paratransit system in Mumbai city and are used by the majority of city commuters. The basis for this research initially stemmed from my passion for designing for the society and improvising the current systems. As the world moves further into the digital age, generating innovative technology and digital- born content, there is a significant demand and need in India for this transition from the manual to the technological. The project has been undertaken as a requirement for the NSCAD Masters of Design program. My research was formulated together with my respectful mentor, Dr. -
Thinking Design
THINKING DESIGN Prof. S. Balaram About the Author Singanapalli Balaram is an industrial designer; senior faculty and former Chairman of Education at the National Institute of Design in India. He is recipient of the honorary fellowship of the Society of Industrial Designers of India and an invited member of the advisory board of ‘Design Issues”, U.SA Four inventions of Balaram have been patented by NID.The Institute also won the first ICSID - Philips award (International Council of Socieiteis of Industrial Design) for its outstanding achievement in Industrial Design. One of the seven projects which won this award was Balaram’s. Life-saving medical equipment which he and a colleague jointly designed for Sri Chitra Tirunal Institute of Medical Sciences and Technology was awarded India’s prestigious National Meritorious Invention Award. Born into a farmer’s family in Gunnathota Valasa, a tiny Agraharam (a village gifted to a scholar by the king) in Andhra Pradesh, South India, Balaram did his post-graduation in product design from the National Institute of Design, Ahmedabad and a research course at the Royal College of Art, London. He holds a diploma in Mechanical Engineering. He started his professional career as a sign board painter and later became a mechanical engineer finally settling down to Design practice and .teaching, His varied pursuits include short story writing; package design and film criticism. He has held senior positions as Chairman of Extension programmes, Co-ordinator, Foundation Programme, Associate Chairman, Industrial Design etc. at the National Institute of Design. He is presently Governing Council Member of The Centre for Environmental Planning and Technology; Vice President of The Society of Industrial Designers of India and Co-ordinator, Design Foundation Studies, NID. -
Vaidakthya-2017
Vaidakthya’17 National Conference on Recent Trends in E-Business: Opportunities & Challenges P R O C E E D I N G S Naipunnya Business School, Koratty Vaidakthya-2017 Vaidakthya-2017 The Conference Proceedings “Recent Trends in E-Business: Opportunities and Challenges” Manager Fr. Saje Peter Executive Director & Principal, Naipunnya Institute of Management and Information Technology Editor Fr. (Dr) Paulachan Kaithottungal Director, Naipunnya Business School Editorial Advisory Council Dr. Joy Puthussery Dean of Studies, Naipunnya Institute of Management and Information Technology Editorial Board Dr. Jacob P M Head of the Department, Naipunnya Business School Mr. Sabu Varghese Former, Associate Professor & Training Manager, NIMIT, Pongam, Koratty East Conference Coordinators Mr. Bhuvanes Kumar Assistant Professor, Naipunnya Business School Mr. Sreenish S. R. Assistant Professor, Naipunnya Business School Dr. Ayana Johny Assistant Professor, Naipunnya Business School Editorial and Administrative Office Naipunnya Institute of Management and Information Technology, Pongam, Koratty East, Thrissur, Kerala – 680 308, Ph: 04802730340, 2730341, Web: www.mbanimit.ac.in, E-mail: [email protected] ISBN: 978-93-5268-538-7 Publisher: Naipunnya Institute of Management and Information Technology, Pongam, Koratty East, Thrissur Dist. Kerala State – 680 308, Phone: 04802730340, 2730341. Web: www.mbanimit.ac.in All Rights Reserved. No part of this publication may be reproduced, stored in a retrieval system or transmitted in any form or by any means, electronic, mechanical, photocopying, recording or otherwise, without the prior permission of the publisher. Foreword I am delighted to share the conference proceedings of Vaidakthya – 2017. It is published at a very important time, when there is an upsurge of interest in e-commerce in the country. -
Prospectus Dated August 12, 2020 Please Read Section 26 of the Companies Act, 2013 Fixed Price Issue
Prospectus Dated August 12, 2020 Please read Section 26 of the Companies Act, 2013 Fixed Price Issue TREKKINGTOES.COM LIMITED CIN: U63010RJ2012PLC040995 Our Company was incorporated as “Fylfot Comtech Private Limited” under the provisions of the Companies Act, 1956 vide Certificate of Incorporation dated December 13, 2012 bearing Registration No. 040995 issued by the Registrar of Companies, Rajasthan. Further, pursuant to change in object of our Company, the name of our Company was changed to “Trekkingtoes.com Private Limited” vide Special resolution dated October 01, 2014. A certificate confirming alteration of object clause consequent to change in object was issued to our company by the Registrar of Companies, Rajasthan on October 27, 2014 and a fresh certificate of incorporation consequent to name change was issued to our Company by the Registrar of Companies, Rajasthan on November 10, 2014. Subsequently, our Company was converted into a Public Limited Company and the name of our Company was changed to “Trekkingtoes.com Limited” vide Special Resolution dated May 06, 2020. A fresh certificate of incorporation consequent to conversion into public limited company was issued to our Company by the Registrar of Companies, Rajasthan on May 11, 2020. The Company’s Corporate Identity Number is U63010RJ2012PLC040995. For further details pertaining to the change of name of our Company, please refer the chapter “History and Certain Corporate Matters” beginning on Page No. 81 of this Prospectus. Registered Office: 236, Mahaveer Nagar 1st, Durgapura, Tonk Road, Jaipur, Rajasthan – 302 018. Corporate Office: J-2, Seema Sandesh, 3rd Floor, Jhalana Institutional Area, Jaipur, Rajasthan – 302 004. Tel No.:+91-96104-49969 / 77278-88501; Email: [email protected]; Website: www.hippocabs.com Contact Person: Mrs. -
Emerging Role of Bike (Motorcycle) Taxis in Urban Mobility © COPYRIGHT
DISCUSSION PAPER January 2020 Emerging Role of Bike (Motorcycle) Taxis in Urban Mobility © COPYRIGHT The material in this publication is copyrighted. Content from this position paper may be used for non-commercial purposes, provided it is attributed to the source. This publication do not advocate or criticise any kind of mobility service provider. Authors Palak Thakur, Research Associate, Centre for Sustainable Mobility, TERI Aakansha Jain, Research Associate, Centre for Sustainable Mobility, TERI Aravind Harikumar, Research Associate, Centre for Sustainable Mobility, TERI Reviewers Mr S Sundar, Mr Shri Prakash, Mr Sanjay Mitra, Mr IV Rao, Mr Sharif Qamar Suggested Format for Citation Thakur, P., A. Jain, and A. Harikumar. 2020. Emerging Role of Bike (Motorcycle) Taxis in Urban Mobility. New Delhi: TERI Design Sushmita Ghosh, TCA Avni, Sudeep Pawar, TERI Press PUBLISHED BY The Energy and Resources Institute (TERI) FOR MORE INFORMATION Centre for Sustainable Mobility, TERI, Darbari Seth Block, IHC Complex, Lodhi Road, New Delhi 110 003, India | Tel.: +91 11 2468 2100 or 2468 2111 | Fax: +91 11 2468 2144 or 2468 2145 Email: [email protected] | Web: www.teriin.org TABLE OF CONTENTS Acknowledgements v Introduction 1 Defining Bike Taxis 1 Conventional Bike taxis 2 New Age-App-based Bike Service Providers 2 Global Context 3 Key Takeaways 5 Mobility Options in India 6 Indian Policy Landscape 7 State-level Policy Initiatives 8 Primary Survey Results 13 Regulatory Interventions 17 Bibliography 18 End Note 19 iv DISCUSSION PAPER ACKNOWLEDGEMENTS The Energy and Resources Institute (TERI) would like to express its deep gratitude to its stakeholders and participants from diverse sectors comprising of NITI Aayog, Creative Footprints, URJA, Centre for Green Mobility, TERI University, Rapido, Jagori, Uber, Institute for Transportation and Development Policy, Mobycy, Ansal University and Rapido for giving their valuable suggestions and feedback in the roundtables organized by TERI. -
Radio Taxi Services in India: Enablers of Success Among Indian Women
UGC Approval No:40934 CASS-ISSN:2581-6403 HEB Radio Taxi Services in India: Enablers of Success CASS among Indian Women Pooja Sehgal Tabeck & Sunetra Saha Research Scholar, Amity Business School, Noida, AUUP Address for Correspondence: [email protected] ABSTRACT: - Women constitute around 48.5 percent of India’s population as per the 2011 census and are the precious human resources. Wealth is becoming more concentrated at the top of the income scale. The income of the highest earning households has shown an exponential growth while the gap in household income between top earners and middle earners has widened . There are 50.69 lakh working women in the organized sector in India, of these, the central government employees about 6 lakh, the state government employ; the state government and bodies under the state government employ about 17lakhs. Women are more independent than in past, with changing scenario they accepted different roles and job profiles in Industry. Their different roles played by women demands more travelling at different locations. The present study tried to focus on factors affecting success of Radio taxi services in India. For present study 200 women were interviewed with the help of structured questionnaire. The results of analysis shows factors affecting success of Radio taxis are brand image & Reputation, Affordability & Acceptability, Security Concerns, Easiness to book taxi and Role of Drivers. Keywords: - Women, Radio taxis, Security, Affordability, acceptability March 2019 – Vol. 3, Issue- 1, Addendum 3 (Special Issue) Page-115 UGC Approval No:40934 CASS-ISSN:2581-6403 INTRODUCTION: - Women constitute around 48.5 percent of India’s population as per the 2011 census and are the precious human resources. -
1 Revue De Presse Semaines 49 & 50 (3-16 Décembre 2018) Kannur: The
1 Revue de presse Semaines 49 & 50 (3-16 décembre 2018) Kannur: The long wait is over, and the dream has come true. Finally, Kannur International Airport (KIAL) has taken wings with the maiden flight by Air India Express to Abu Dhabi. Chief minister Pinarayi Vijayan and union minister for civil aviation Suresh Prabhu flagged off the first aircraft at 10.06 am on Sunday, carrying 185 passengers, thus crossing yet another milestone in the aviation history of the nation, by commissioning the fourth international airport in the state. Later, addressing a public meeting, Pinarayi Vijayan, who formally inaugurated the facility, said when the idea of the airport evolved way back in 1990s, there was apprehension whether it would be practical to have an airport here. But now the airport has been materialized and it has the potential to become one of the most important 4-5 airports in the country. He also said the Kerala government is ready to take over Thiruvananthapuram airport, since the central government has decided to privatise it. In the case of Kozhikode airport also the government has the same stand, as it has experience in managing airports, said the chief minister. Union minister Suresh Prabhu, who was the chief guest on the occasion, said this airport is a very good model of development with the central and state governments having stake in it. Observing that connectivity is a pre-requisite for development, the minister also said Kerala has the highest potential for growth. Though Air India Express and Go Air have started operation in the beginning, more companies would start operations in the coming days, said the officials. -
Analysis of Autorickshaw As an Intermediate Paratransit System
International Journal of Pure and Applied Mathematics Volume 118 No. 24 2018 ISSN: 1314-3395 (on-line version) url: http://www.acadpubl.eu/hub/ Special Issue http://www.acadpubl.eu/hub/ Analysis of Autorickshaw as an Intermediate Paratransit system Tushar R Bagul1, Kiran Patil2, Alka Kote3, B.S.Balpgold4, Ravindra Kumare5, Rakesh Kumar6, 1Associate Professor,34Professor 134DYPCOE College of Engineering Akurdi,Pune 2Assistant professor AISSMS College of Engineering Pune 5 Principal Scientist CSIR-Central Road Research Institute, New Delhi 110020, India. 6Associate Professor, S.V. National Institute of Technology, Surat 39500, India May 23, 2018 Abstract The paratransit system becomes indispensable transport mode due to its easy maneuvering on congested urban roads in India. The utility of three wheelers as a paratransit system study was undertaken in typical three regions of cities namely; central business district, developed, and developing. This study shows details the overall role of three-wheeler Autorickshaw service as it provides complete flexibility to reach the destination defined by the passenger. The operators and passengers survey was conducted by considering major nodes on arterial, sub-arterial, collector and local roads of the 1 International Journal of Pure and Applied Mathematics Special Issue particular regions to developed multinomial logit model based on disaggregated data. The explanatory variables included in the model are the demographic and socioeconomic characteristics of individuals, trip/travel characteristics, and Autorickshaw operational attributes. The findings from the present study revealed that as low and medium class population income (80.5%) prefer to use shared Autorickshaw as Intermediate Paratransit Mode as compared to other Paratransit modes such as a bicycle, demand responsive modes. -
INDIA the Economic Scenario
` ` 5/2018 INDIA Contact: Rajesh Nath, Managing Director Please Note: Jamly John, General Manager Telephone: +91 33 40602364 1 crore = 10 000 000 Fax: +91 33 2321 7073 1 lakh = 100 000 E-mail: [email protected] 1 Euro = Rs.78 The Economic Scenario Economic Growth The much-anticipated New Industrial Policy, which will replace the 27-year-old existing policy and pave the way for promotion of new technology and reduced regulations, has been placed before the Union Cabinet for approval. The New Industrial Policy is now just a Cabinet nod away. Its implementation will lead to job creation and modernisation of units, and will encourage entrepreneurs to experiment with new technology to improve efficiency. All ministries and departments concerned were kept in the loop throughout the drafting process. Hence, there were no major changes proposed during the inter-ministerial consultations. This will be the third industrial policy drafted in independent India. The first was announced in 1956, and the second, in 1991. The draft industrial policy floated in August 2017 by the Department of Industrial Policy & Promotion aims to create jobs over the next two decades, promote foreign technology transfer and attract $100 billion FDI annually. While the policy does not suggest direct changes in laws such as those governing labour, it is likely to propose the establishment of a body with representation from the Centre and the States to work on changes whenever required. It also suggests strengthening of municipal bodies. To promote the use of new technology such as robotics and artificial intelligence, the policy is expected to emphasise promoting R&D and set up an institutional mechanism to encourage commercial utilisation of research done using government funds.