Ssc-405 Fatigue Resistant Detail Design Guide for Ship Structures
Total Page:16
File Type:pdf, Size:1020Kb
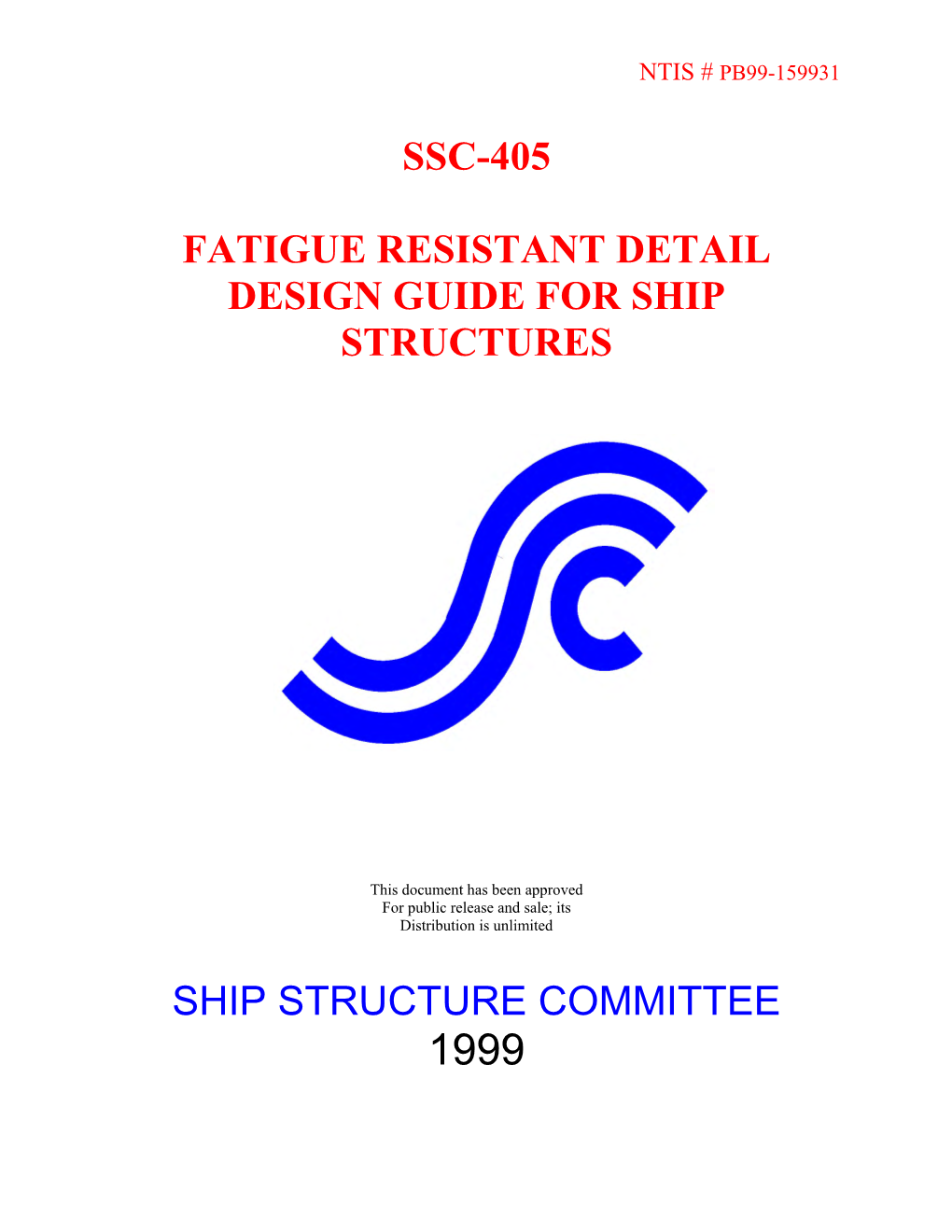
Load more
Recommended publications
-
Stability Analysis Based on Theoretical Data and Inclining Test Results for a 1200 GT Coaster Vessel
Proceeding of Marine Safety and Maritime Installation (MSMI 2018) Stability Analysis Based on Theoretical Data and Inclining Test Results for a 1200 GT Coaster Vessel Siti Rahayuningsih1,a,*, Eko B. Djatmiko1,b, Joswan J. Soedjono 1,c and Setyo Nugroho 2,d 1 Departement of Ocean Engineering, Institut Teknologi Sepuluh Nopember, Surabaya, Indonesia 2 Department of Marine Transportation Engineering, Institut Teknologi Sepuluh Nopember, Surabaya, Indonesia a. [email protected] *corresponding author Keywords: coaster vessel, final stability, preliminary stability. Abstract: 1200 GT Coaster Vessel is designed to mobilize the flow of goods and passengers in order to implement the Indonesian Sea Toll Program. This vessel is necessary to be analysed its stability to ensure the safety while in operation. The stability is analysed, firstly by theoretical approach (preliminary stability) and secondly, based on inclining test data to derive the final stability. The preliminary stability is analysed for the estimated LWT of 741.20 tons with LCG 23.797 m from AP and VCG 4.88 m above the keel. On the other hand, the inclining test results present the LWT of 831.90 tons with LCG 26.331 m from AP and VCG 4.513 m above the keel. Stability analysis on for both data is performed by considering the standard reference of IMO Instruments Resolution A. 749 (18) Amended by MSC.75 (69) Static stability, as well as guidance from Indonesian Bureau of Classification (BKI). Results of the analysis indicate that the ship meets the stability criteria from IMO and BKI. However results of preliminary stability analysis and final stability analysis exhibit a difference in the range 0.55% to 11.36%. -
13.012 Hydrodynamics for Ocean Engineers Reading #3
13.012 Hydrodynamics for Ocean Engineers Reading #3 13.012 Hydrodynamics for Ocean Engineers Prof. A.H. Techet Fall 2004 Archimedes’s Principle and Static Stability “Any object, wholly or partly immersed in a fluid, is buoyed up by a force equal to the weight of the fluid displaced by the object.” “The apparent loss in weight of a body immersed in a fluid is equal to the weight of the displaced fluid.” I. Archimedes’s Principle: The force on a body due to pressure alone (in the absence of viscous forces) K F = ∫∫ p nˆ ds (3.1) S where pressure is a function of depth below the free surface: p(z) = −ρgz . (3.2) K F = ∫∫ p nˆ ds = − ρg ∫∫ z nˆ ds (3.3) S S By Calculus the surface integral can be converted into a volume integral (Gauss’s Theorem/Divergence Theorem): K K ∫∫G ⋅ nˆ ds = ∫∫∫∇ ⋅G dV (3.4) SV Thus equation becomes: K FpndsgzndsgdVgVk==−=∫∫ˆˆρρρ ∫∫ ∫∫∫ =ˆ (3.5) SSV version 3.0 updated 9/8/2004 -1- ©2003, 2004 aht 13.012 Hydrodynamics for Ocean Engineers Reading #3 We can see now that the buoyancy force acts to counterbalance the displaced volume of fluid. For a half submerged body the area of the water plane must be accounted for in the integration. II. Moment on a body (Ideal Fluid) The moment on a submerged body follows directly from structural mechanics or dynamics methodologies. K K M = p(x × nˆ) ds ≡ (M ,M ,M ) = (M ,M ,M ) (3.6) ∫∫ 1 2 3 x y z S Figure 1: x, y, z coordinate reference frame. -
An Investigation of Head-Sea Parametric Rolling and Its Influence on Container Lashing Systems
SNAME Annual Meeting 2001 Presentation An Investigation of Head-Sea Parametric Rolling and its Influence on Container Lashing Systems William N. France,1 Marc Levadou,2 Thomas W. Treakle,3 J. Randolph Paulling,4 R. Keith Michel,5 and Colin Moore 5 Recent studies have demonstrated that parametric roll in extreme head or near head seas can occur when unfavorable tuning is combined with low roll damping (reduced speed) and large stability variations (governed by wavelength, wave height, general hull form, bow flare, and stern shapes). Parametric rolling is an unstable phenomenon, which can quickly generate large roll angles that are coupled with significant pitch motions. The rolling occurs in phase with pitch, and on containerships introduces high loads into the containers and their securing systems. It appears that post-Panamax containerships may be particularly prone to this behavior. This is an important issue considering the large number of these vessels scheduled for delivery in the next few years. In October, 1998, a post-Panamax, C11 class containership encountered extreme weather and sustained extensive loss and damage to deck stowed containers. The motions of the vessel during this storm event were investigated through a series of model tests and numerical analyses. These studies provide insight into the conditions in which post-Panamax containerships are likely to experience head sea parametric rolling, and the magnitude of motions and accelerations that can occur. The findings from this investigation are presented in this paper, together with discussion of how such extreme motions impact the design and application of container securing systems. Also outlined in the paper are recommendations for additional research needed to better understand the influence of vessel design and operational considerations on the propensity of post-Panamax containerships towards parametric rolling. -
Angle of Loll Calculation by Cubic Spline
JOURNAL OF MARITIME RESEARCH Vol. X. No. 2 (2013), pp. 21 - 26 ISSN: 1697-4040, www.jmr.unican.es Angle of Loll Calculation By Cubic Spline I. Basterretxea1,2,*, I. Sotés1,3, A. López1,4 and I. Alcedo1,5 ARTICLE INFO ABSTRACT Article history: Several years ago the Basque Government supported the programming of the software ARKITSAS in order to provide Received 28 February 2013; all existing vessels with a specific software to calculate stability, cargo and longitudinal strength data. The aim of this in revised form 12 March 2013; article is to present the part of that research concerning the definition of the static stability curve by cubic spline in its accepted 25 May 2013 initial end when the metacentric height is negative. Taking into account that the slope at initial end is known, the pre- cision of the results for low heeling angles may be improved and, in this way, the accuracy in the calculation of loll should be enhanced. This method of calculation is compared to other traditional methods used for wall-sided ships by Keywords: the application to three different ships. Static stability curve, Cubic splines, Free and fixed end, Angle of loll. © SEECMAR / All rights reserved 1. Introduction within the initial stability more precise and, taking into ac- count that the angle of loll is usually small; its calculation The static stability curve represents the values of GZ arms for would be suitable by means of non-free end cubic spline the different heeling angles. However, the stability booklet method. usually provides GZ arms for every ten or fifteen degrees of When the ship is ‘wall-sided’ the approximate formula in heeling angles. -
Stability Guide for Smaller Vessels
STABILITY GUIDE FOR SMALLER VESSELS The EU’s Ministry of Food, Fisheries Fund Agriculture and Fisheries The project is funded by the Ministry of Food, Agriculture and Fisheries and the EU 2 All photos and texts in this publication are protected by Danish copyright law. All rights belong to or are managed by the Danish Fishermen’s Occupational Health Service. It is not allowed to copy or use texts and pictures from this publication without written permission. Preface 3 Over the years, a number of vessels in the category 0 - 15 metres have capsized or sunk. Several of these losses were due to vessel instability. A number of fishermen have lost their lives because of this. Failure in stability can be the result of repeated rebuilding of a vessel, where a number of small changes suddenly has a great impact on stability. It may also be due to changes in fishing patterns as well as fishing in other waters where external influences are different. So it is important that the captain has a good knowledge of the vessel’s stability and a thorough understanding of how it can change during fishing and in connection with rig- ging to another kind of fishery. In particular when rebuilding or making other changes to the vessel, it is extremely important to be aware of the impact this has on the stability of the vessel. This reference book illustrates the basic principles of stability and how to calculate stabil- ity. It is a guide to understanding and interpreting vessel stability calculations. Stability problems are highlighted in the form of case studies with examples of both improving and deteriorating changes in stability. -
STELLAR DAISY CASUALTY INVESTIGATION REPORT Loss of Buoyancy and Foundering with Multiple Loss of Life
REPUBLIC OF THE MARSHALL ISLANDS Maritime Administrator STELLAR DAISY CASUALTY INVESTIGATION REPORT Loss of Buoyancy and Foundering with Multiple Loss of Life South Atlantic Ocean | 31 March 2017 Official Number: 3486 IMO Number: 9038725 CONDOLENCES The Republic of the Marshall Islands Maritime Administrator offers its sincere condolences to the families and friends of the 22 individuals who perished in the 31 March 2017 casualty. ACKNOWLEDGEMENTS The Republic of the Marshall Islands Maritime Administrator commends the surviving members of the crew of STELLAR DAISY for their dedication to searching for their fellow crewmembers. The Master and crew of SPITHA, and particularly ELPIDA, are also commended for their efforts in searching for and rescuing the surviving members of STELLAR DAISY crew. The Republic of the Marshall Islands Maritime Administrator thanks the marine safety investigation authorities from the Republic of Korea, the Republic of the Philippines, and the Federative Republic of Brazil, which participated as substantially interested States, and Polaris Shipping Co., Ltd., the Korean Register of Shipping, and Vale SA, which were interested parties, for their cooperation. Published by: Republic of the Marshall Islands Maritime Administrator on 19 April 2019 DISCLAIMER In accordance with national and international requirements, the Republic of the Marshall Islands Maritime Administrator (the “Administrator”) conducts marine safety investigations of marine casualties and incidents to promote the safety of life and property at sea and to promote the prevention of pollution. Marine safety investigations conducted by the Administrator do not seek to apportion blame or determine liability. While every effort has been made to ensure the accuracy of the information contained in this Report, the Administrator and its representatives, agents, employees, or affiliates accept no liability for any findings or determinations contained herein, or for any error or omission, alleged to be contained herein. -
ASTM F1321: Standard Guide for Conducting a Stability Test
By Authority Of THE UNITED STATES OF AMERICA Legally Binding Document By the Authority Vested By Part 5 of the United States Code § 552(a) and Part 1 of the Code of Regulations § 51 the attached document has been duly INCORPORATED BY REFERENCE and shall be considered legally binding upon all citizens and residents of the United States of America. HEED THIS NOTICE: Criminal penalties may apply for noncompliance. e Document Name: CFR Section(s): Standards Body: Official Incorporator: THE EXECUTIVE DIRECTOR OFFICE OF THE FEDERAL REGISTER WASHINGTON, D.C. ~~l~ Designation: F 1321 - 92 An American National Standard Standard Guide for Conducting a Stability Test (Lightweight Survey and Inclining Experiment) to Determine the Light Ship Displacement and Centers of Gravity of a VesseP This standard is issued under the fixed designation F 1321; the number immediately following the designation indicates the year of ' original adoption or, in the case of revision, the year of last revision. A number in parentheses indicates the year of last reapproval. A superscript epsilon (.) indicates an editorial change since the last revision or reapproval. INTRODUCfION This guide provides the marine industry with a basic understanding of the various aspects of a stability test. It contains procedures for conducting a stability test in order to ensure that valid results are obtained with maximum precision at a minimal cost to owners, shipyards, and the government. This guide is not intended to instruct a person in the actual calculation of the light ship displacement and centers of gravity, but rather to be a guide to the necessary procedures to be followed to gather accurate data for use in the calculation of the light ship characteristics. -
SOME IMPORTANT NAVAL ARCHITECTURAL TERMS February 2009
Page 1(6) SOME IMPORTANT NAVAL ARCHITECTURAL TERMS February 2009 ITEM EXPLANATION A-, B- and C-class divisions SOLAS has tables for structural fire protection requirement of bulkheads and decks. The requirements depend on the spaces in question, and are different for passenger ships and cargo ships. A-0, A-15, A-30, A-60: Shall be constructed of steel or equivalent material, shall be constructed to prevent passage of smoke and flame for 1 h in Standard Fire Test, shall be insulated so that the average temperature of the unexposed side does not rise more than 140ÛC (any point no more than 180ÛC) above the original temperature within 0, 15, 30 or 60 minutes. B-0, B-15: Shall be constructed to prevent passage of flame for 0.5 h in Standard Fire Test, shall be insulated so that the average temperature of the unexposed side does not rise more than 140ÛC (any point no more than 225ÛC) above the original temperature within 0 or 15 minutes. Shall be constructed of approved non-combustible materials (However, combustible veneer may be used). C: Shall be constructed of approved non-combustible materials (However, combustible veneer may be used). Alternative Design, Regulation allows for designs and arrangements which are not Alternative Arrangements according to SOLAS requirements, providing an analysis is made that shows the proposed alternative design or arrangement is, with regards to safety, at the same or better level than the SOLAS requirement. Example of an alternative design are lifeboats with a higher than 150 person capacity. Attained Subdivision Index, “A” According to probabilistic damage stability rules the vessel’s probability to survive a flooding damage (collision, grounding) is calculated with formula: = where:ܣ ݏ i represents each compartment or group of compartments under consideration. -
Stability Guide for Smaller Vessels
STABILITY GUIDE FOR SMALLER VESSELS www.balticsea-region-strategy.eu 2 Preface In 2009, the EU approved a Strategy for the Baltic Sea Region to help mobilise EU fund- ing and policies and to coordinate the actions of the European Union, EU countries, regions, pan-Baltic organisations, financing institutions and non-governmental bodies to promote a more balanced development of the region. The Strategy focuses on different Priority Areas. One of these is Maritime Safety and Security with the aim to make the Baltic Sea Region a leading region in maritime safety and security. This priority area is jointly coordinated by Denmark and Finland and they have identified a series of Flagship projects to promote maritime safety and security. The Flagship project entitled: To lay the groundwork for developing a plan to reduce the number of accidents in fisheries has been developing cooperation and exchange of infor- mation on accidents in the fisheries sector between the eight EU Member States around the Baltic Sea and Russia. Stakeholders, administration and educational establishments have worked together on this. One of the recurrent themes during the project´s several visits to the Baltic Sea States and discussions with fishermen, teachers at fishery schools and administration has been the importance of vessel stability. This is particularly important for smaller vessels, of which there are many operating in the Baltic. Teachers at the schools were asking for an easy to read illustrated guide which they can use in their work. The Danish Fishermen’s Occupational Health Services have been involved in the Flag- ship Project. -
Barge Stability Guidelines Introduction
BARGE STABILITY GUIDELINES INTRODUCTION The purpose of these Guidelines is to provide insight into the basic stability concepts relevant to loading and to loaded pontoon barges. Pontoon barges are used for a wide variety of cargoes from bulk loads such as coal, rock, and logs – with low to medium centres of gravity – through to vehicles, and unique ‘one-off’ loads such as industrial equipment and storage tanks, which can have very high centres of gravity, and windage areas. Pontoon barges are also used as work platforms for many types of equipment including cranes and pile drivers. Stability considerations are critical when conducting transportation and other marine operations safely. The guidance that follows only deals with stability. It is assumed that other aspects of best marine practice – such as having sufficient handling power (bollard pull), and manoeuvring capability, 1 watertightness arrangements (including securing of hatches etc), and ensuring adequacy of tow rigging, emergency, and safety gear – have also all been addressed. Disclaimer: All care and diligence has been used in extracting, analysing and compiling this information, however, Maritime New Zealand gives no warranty that the information provided is without error. Copyright Maritime New Zealand 2006 Parts of this publication may be reproduced provided acknowledgement is made to this publication and Maritime New Zealand as the source. ISBN 0-478-18839-0 contents 10 basic stability rules FOR SAFE PONTOON BARGE OPERATIONS 1 INTRODUCTION Understanding and managing the stability of your barge is critical to the safety of you and your crew, and to the safe delivery of your cargo. 3 10 BASIC STABILITY RULES 4 STABLE / UNSTABLE VESSEL The following basic rules offer step by step guidance aimed at ensuring safety and success. -
Boat Design Competition Illustrated Glossary
THE APPRENTICE SCHOOL STUDENT SECTION OF THE SOCIETY OF NAVAL ARCHITECTS AND MARINE ENGINEERS Boat Design Competition Illustrated Glossary 1 THE APPRENTICE SCHOOL STUDENT SECTION OF THE SOCIETY OF NAVAL ARCHITECTS AND MARINE ENGINEERS TABLE OF CONTENTS Abeam ..................................................................................................................................... 5 Aft ........................................................................................................................................... 5 Aft Perpendicular (AP) ........................................................................................................... 5 Amidships ............................................................................................................................... 5 Appendages ............................................................................................................................. 5 Athwartships ........................................................................................................................... 5 Awash ..................................................................................................................................... 5 Ballast ..................................................................................................................................... 5 Baseline (BL) .......................................................................................................................... 5 Beam or Breadth .................................................................................................................... -
Whitepaper-1401-What-Is-The-GMT
What is the GMT? ... And Why it is Important Whitepaper 1401 Topics Covered : - A Spring Stiffness / Roll Stiffness Analogy - Flat Water – Static Stability - What Happens in Real Waves? - So How Does GMT Influence Yacht Rolling? - The Problems with Very Stiff Yachts (High GMT) - Conclusions and Recommendations Whitepaper 1401: What is the GMT? What is the GMT ? … And Why it is Important Author : Paul Steinmann (Product Manager – VEEM Gyro) This article explains exactly what the mysterious GMT is, and why it is such a critical number when discussing roll stabilization. A Spring Stiffness / Roll Stiffness Analogy Before we launch into what the GMT is, allow me to present a brief analogy to help describe rolling ‘stiffness’ of yachts. Forgetting waves for now, lets consider a yacht resting in calm water. We call this a static situation as is is not changing over time. The Stability Booklet on the bridge of your yacht discusses the ‘static’ stability of the yacht. The ‘static’ stabilty ignores the effect of waves. Now, if you were magically able to heel your yacht over away from upright, and then you let it go, we know that it would roll back to it’s upright position (let’s hope so anyway). This is a bit like what happens when you stretch a spring…if you let it go, it returns to its natural relaxed length. The stiffness of a spring (K) is the ratio of the force applied to stretch the spring (F), and the amount the spring extends (X). This can be written as a mathematical equation as follows: F = K × X Force = stiffness x extension So a spring with high stiffness requires more force to stretch it by a certain amount.