L%%LOSALAMOSSCIENTIFICLABORATORY Post Office Box 1663 Los Alamos
Total Page:16
File Type:pdf, Size:1020Kb
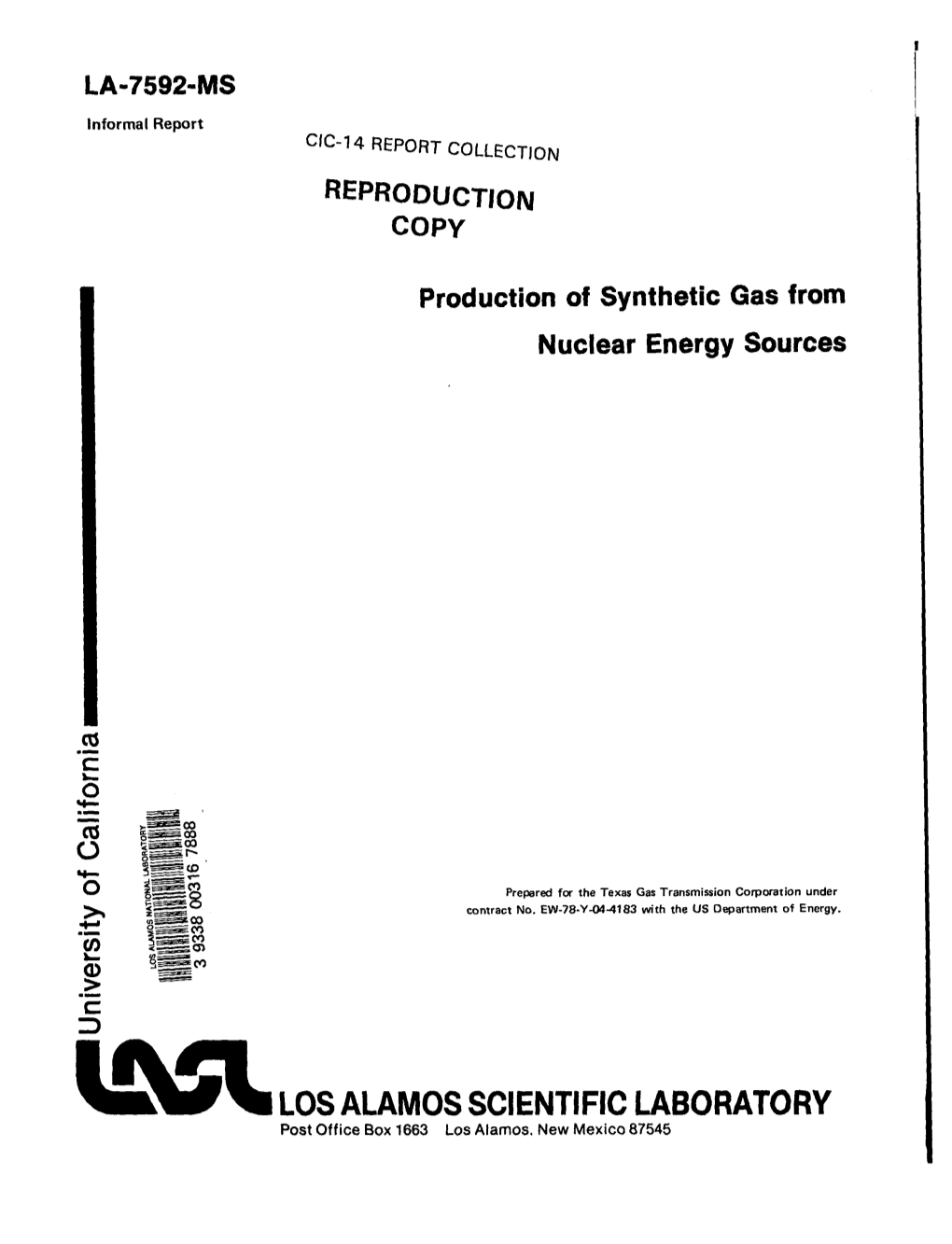
Load more
Recommended publications
-
A Novel and Cost Effective Radiant Heat Flux Gauge This Paper Presents a Patent-Pending Methodology of Measuring Radiation Emiss
A Novel and Cost Effective Radiant Heat Flux Gauge S. Safaei and A. S. Rangwala Department of Fire Protection Engineering, Worcester Polytechnic Institution, Worcester, MA, 01609, USA V. Raghavan Department of Mechanical Engineering Indian Institute of Technology Madras, Chennai, India T.M. Muruganandam, Department of Aerospace Engineering, National Center for Combustion Research and Development, Indian Institute of Technology Madras, Chennai, India This paper presents a patent-pending methodology of measuring radiation emissions from fires, for the purposes of more practical optical flame detection and analysis. Flame radiation comprises of three phenomena: chemiluminescence, photoluminescence, and thermal radiation. The first two types are caused by elementary breakdown reactions of the reactants and the molecular excitations of products such as H2O and CO2, respectively. These emissions are within narrow bands of electromagnetic radiation wavelengths, and due to their specific molecular physics, are largely fuel dependant. The third type, thermal radiation emissions come from high temperature soot, which is a blanket term for any carbonaceous intermittent species of the combustion reaction. The amount and temperature of soot is case-specific, as it is influenced by fuel type, geometries, fuel-oxidizer premixing and the resulting level of combustion efficiency. However since naturally occurring fire hazards are diffusion flames, soot is present in high quantities and the majority of the radiation can be attributed to soot alone [1 – 2]. These soot emissions are over large ranges of the electromagnetic spectrum, from ultraviolet all the way to Long wave Infrared (LWIR), following the classic Planck Law for Blackbody emitters. This distribution of radiant energy, E, is highly dependent on the temperature of the emitter, T, due to its exponential relation E=T4. -
Low Cost Solar Thermoelectric Water Floating Device to Supply Measurement Platform
78 IAPGOŚ 4/2019 p-ISSN 2083-0157, e-ISSN 2391-6761 DOI: 10.35784/IAPGOS.734 LOW COST SOLAR THERMOELECTRIC WATER FLOATING DEVICE TO SUPPLY MEASUREMENT PLATFORM Andrzej Nowrot1, Monika Mikołajczyk2, Anna Manowska1, Joachim Pielot1, Antoni Wojaczek1 1Silesian University of Technology, Department of Electrical Engineering and Automation in Industry, Gliwice, Poland, 2Famur Institute Ltd, Katowice, Poland Abstract. This work presents the prototype of the solar – thermoelectric device, which can float on water surface. It produces electrical energy as a result of the Seebeck effect in a commercial, low-cost Peltier module. The main application of the device will be an autonomous and a floating measurement platform. An important advantage of the presented solution is the possibility to work alike at day, when a solar light heats the surface of the absorber, and at night, when the different of temperatures between air and water causes the heat flux and in an effect the electricity. The device is capable of working for many cloudy days and also in winter on very short days. The presented device is based on low-cost and widely available components. Keywords: thermoelectric devices, solar power generation, energy conversion TERMOELEKTRYCZNE URZĄDZENIE SOLARNE DO ZASILANIA PLATFORMY POMIAROWEJ Streszczenie. W pracy zaprezentowano prototypowe solarne urządzenie termoelektryczne pływające po powierzchni wody. Wytwarza ono w niedrogim, komercyjnym module Peltiera energię elektryczną w wyniku zachodzącego w nim zjawiska Seebecka. Docelowo głównym obszarem aplikacyjnym urządzenia będzie zasilanie autonomicznej, pływającej platformy pomiarowa do monitorowania parametrów środowiskowych. Istotną zaletą przedstawionego rozwiązania jest możliwość pracy zarówno w dzień, gdy światło słoneczne ogrzewa powierzchnię absorbera, jak również w nocy, gdy różnica temperatur między powietrzem a wodą powoduje powstawanie strumienia ciepła w module Peltiera. -
United States Patent [191 4,2313J97 Sher
United States Patent [191 4,2313J97 Sher [54] RADIANT ENERGY TO ELECTRIC ENERGY 4,084,101 4/1978 Sher ..................................... 290/1 R CONVERTER 4,096,393 6/1978 Sher ..................................... 290A R [76] Inventor: Arden Sher, 108 Charles River OTHER PUBLICATIONS Landing Rd., Williamsburg, Va. R. Solomon et al., “Polarization in LaF,”, J. Appl. Phys., 23185 VO~.37, pp. 3427-3432, (1966). [ * 3 Notice: The portion of the term of this patent A. Sher et al., “Transport Properties of LaF3”, Phys. subsequent to Apr. 11,1995, has been Rev., vol. 144, pp. 593-604, (1966). disclaimed. J. E. Drummond, “Electrical Power Conversion”, IECEC Record ’75, pp. 569-575. [21] Appl. No.: 889,514 S. B. Skinner, “Thermodielectric Energy Conversion [22] Filed: Mar. 23,1978 by Thin Films: Experiment & Theory”, Intersociety Energy Conv. Eng. Con$, (1967), pp. 865-873. Related U.S. Application Data A. Sher et al., “LaF3 Infrared Detector”, Appl. Phys. Lett., vol. 28, pp. 676-678, (1976). [63] Continuation-in-part of Ser. No. 631,689, Nov. 13, 1975, Pat. No. 4,084,101. Primary Examiner-Aaron Weisstuch Attorney, Agent, or Firm-Lowe, King, Price and [51] Int. Cl.2 ............................................. HQlL31/Q4 Becker [52] U.S. Cl. ............................... 136/89 SP; 290/1 R 361/280; 361/282; 310/308; 310/309; 250/211 1571 ABSTRACT 250/212; 250/336 R; Radiant energy is converted into electric energy by [58] Field of Search ............ 136/89 R, 89 NB, 89 SP; irradiating a capacitor including an ionic dielectric. The 250/211 R, 212, 336; 290/1 R 361/280,282; 310/308, 309 dielectric is a sintered crystal superionic conductor, e.g., lanthanum trifluoride, lanthanum trichloride, or [561 References Cited silver bromide, so that a multiplicity of crystallites exist U.S. -
LESSON 1 What Is Energy?
LESSON 1 What is Energy? Overview In this lesson students review what they know about energy in everyday life, define it, learn the different energy forms through play, and differentiate between potential and kinetic energy. Student • I can use my own words to show I understand “energy.” Learning • I can describe the main forms of energy and give examples. Targets • I can show potential and kinetic energy with my body and I can give examples of each. • I can give examples of how I use energy every day. NGSS MS-PS3-5. Construct, use, and present arguments to support the claim that when the kinetic energy of an object changes, energy is transferred to or from the object. [Clarification Statement: Examples of empirical evidence used in arguments could include an inventory or other representation of the energy before and after the transfer in the form of temperature changes or motion of object.] [Assessment Boundary: Assessment does not include calculations of energy.] Background Energy is part of everything that happens in the world and everything we do. Energy can be in the form of heat, light, gravity, sound, motion, chemical reactions, or electricity. Energy is the ability to do work or make a change. Nine forms of energy: (see Overhead 1 “Forms of Energy”) • Chemical: Chemical energy is the energy stored in the bonds of atoms and molecules. Biomass, petroleum, natural gas, propane and coal are examples of stored chemical energy. • Nuclear: Nuclear energy is the energy stored in the nucleus of an atom. It is the energy that holds the nucleus together. -
Metal Oxides Applied to Thermochemical Water-Splitting for Hydrogen Production Using Concentrated Solar Energy
chemengineering Review Metal Oxides Applied to Thermochemical Water-Splitting for Hydrogen Production Using Concentrated Solar Energy Stéphane Abanades Processes, Materials, and Solar Energy Laboratory, PROMES-CNRS, 7 Rue du Four Solaire, 66120 Font Romeu, France; [email protected]; Tel.: +33-0468307730 Received: 17 May 2019; Accepted: 2 July 2019; Published: 4 July 2019 Abstract: Solar thermochemical processes have the potential to efficiently convert high-temperature solar heat into storable and transportable chemical fuels such as hydrogen. In such processes, the thermal energy required for the endothermic reaction is supplied by concentrated solar energy and the hydrogen production routes differ as a function of the feedstock resource. While hydrogen production should still rely on carbonaceous feedstocks in a transition period, thermochemical water-splitting using metal oxide redox reactions is considered to date as one of the most attractive methods in the long-term to produce renewable H2 for direct use in fuel cells or further conversion to synthetic liquid hydrocarbon fuels. The two-step redox cycles generally consist of the endothermic solar thermal reduction of a metal oxide releasing oxygen with concentrated solar energy used as the high-temperature heat source for providing reaction enthalpy; and the exothermic oxidation of the reduced oxide with H2O to generate H2. This approach requires the development of redox-active and thermally-stable oxide materials able to split water with both high fuel productivities and chemical conversion rates. The main relevant two-step metal oxide systems are commonly based on volatile (ZnO/Zn, SnO2/SnO) and non-volatile redox pairs (Fe3O4/FeO, ferrites, CeO2/CeO2 δ, perovskites). -
Hydrogen As an Energy Vector
Renewable and Sustainable Energy Reviews 120 (2020) 109620 Contents lists available at ScienceDirect Renewable and Sustainable Energy Reviews journal homepage: http://www.elsevier.com/locate/rser Hydrogen as an energy vector Zainul Abdin a,b, Ali Zafaranloo a, Ahmad Rafiee d, Walter M�erida b, Wojciech Lipinski� c, Kaveh R. Khalilpour a,e,f,* a Faculty of Information Technology, Monash University, Melbourne, VIC, 3145, Australia b Clean Energy Research Centre, The University of British Columbia, 6250 Applied Science Lane, Vancouver, BC, V6T 1Z4, Canada c Research School of Electrical, Energy and Materials Engineering, The Australian National University, Canberra, ACT, 2601, Australia d Department of Theoretical Foundations of Electrical Engineering, Faculty of Energy, South Ural State University, 76, Lenin Ave., Chelyabinsk, 454080, Russia e School of Information, Systems and Modelling, University of Technology Sydney, 81 Broadway, Ultimo, NSW, 2007, Australia f Perswade Centre, Faculty of Engineering and IT, University of Technology Sydney, 81 Broadway, Ultimo, NSW, 2007, Australia ARTICLE INFO ABSTRACT Keywords: Hydrogen is known as a technically viable and benign energy vector for applications ranging from the small-scale Hydrogen economy power supply in off-grid modes to large-scale chemical energy exports. However, with hydrogen being naturally Hydrogen supply chain unavailable in its pure form, traditionally reliant industries such as oil refining and fertilisers have sourced it Hydrogen carriers through emission-intensive gasificationand reforming of fossil fuels. Although the deployment of hydrogen as an Hydrogen generation alternative energy vector has long been discussed, it has not been realised because of the lack of low-cost Hydrogen storage Renewable hydrogen hydrogen generation and conversion technologies. -
Method for Evaluation of Thermochemical and Hybrid Water-Splitting Cycles
Ind. Eng. Chem. Res. 2009, 48, 8985–8998 8985 Method for Evaluation of Thermochemical and Hybrid Water-Splitting Cycles Miguel Bagajewicz,* Thang Cao, Robbie Crosier, Scott Mullin, Jacob Tarver, and DuyQuang Nguyen Department of Chemical, Biological and Materials Engineering, The UniVersity of Oklahoma, Norman, Oklahoma This paper presents a methodology for the preliminary evaluation of thermochemical and hybrid water-splitting cycles based on efficiency. Because the method does not incorporate sufficient flowsheet details, the efficiencies are upper bounds of the real efficiencies. Nonetheless, they provide sufficient information to warrant comparison with existing well-studied cycles, supporting the decision to disregard them when the bound is too low or continuing their study. In addition, we add features not present in previous works: equilibrium conversions as well as excess reactants are considered. The degrees of freedom of each cycle (temperatures, pressures, and excess reactants) were also considered, and these values were varied to optimize the cycle efficiency. Ten cycles are used to illustrate the method. I. Introduction species entering the process is water, and the only products of the process are hydrogen and oxygen. Heat and work are also Declining volumes of fossil fuel reserves and an increase in transferred across the system boundaries for the heating and their demand has caused a recent rise in the cost of energy. cooling of process streams, the separation of reactive species, Similarly, nations across the globe are aspirating to become less and to drive the chemical reactions. dependent on foreign resources for the fulfillment of energy requirements. Furthermore, a steady increase in greenhouse gas Many studies have been performed in previous years to emissions over the past decades has brought about the reality evaluate water-splitting cycles as a means to produce hydrogen. -
Late-Time Simulation of National Ignition Facility Hohlraums
UCRL-JRNL-206693 Late-time simulation of National Ignition Facility Hohlraums D.C. Eder, O.S. Jones, M.M. Marinak, M.T. Tobin, B.J. MacGowan September 21, 2004 Nuclear Fusion 2004 Disclaimer This document was prepared as an account of work sponsored by an agency of the United States Government. Neither the United States Government nor the University of California nor any of their employees, makes any warranty, express or implied, or assumes any legal liability or responsibility for the accuracy, completeness, or usefulness of any information, apparatus, product, or process disclosed, or represents that its use would not infringe privately owned rights. Reference herein to any specific commercial product, process, or service by trade name, trademark, manufacturer, or otherwise, does not necessarily constitute or imply its endorsement, recommendation, or favoring by the United States Government or the University of California. The views and opinions of authors expressed herein do not necessarily state or reflect those of the United States Government or the University of California, and shall not be used for advertising or product endorsement purposes. Late-time simulation of National Ignition Facility hohlraums D. C. Eder, A. E. Koniges, O. S. Jones, M. M. Marinak, M. T. Tobin, and B. J. MacGowan Lawrence Livermore National Laboratory, Livermore, CA 94551 Abstract The late-time (t ≥ 80 ns) behavior of hohlraums designed for the National Ignition Facility (NIF) is simulated using the multiphysics radiation hydrodynamics codes LASNEX and HYDRA. The spatial distribution of x-radiation outside the hohlraum is shown as a function of time. The energy spectrum of the x-ray emission is presented for various hohlraum viewing angles. -
Heavy Water Reactors: Status and Projected Development Designed in the Russian Federation
01-01915_TRS407.qxd 17.04.2002 14:04 Uhr Seite 1 Technical Reports Series No. This report commences with a review of the historical development of heavy water reactors (HWRs), detailing the various national efforts made in developing reactor concepts and taking them to the stage of prototype operation or commercial viability. Sections cover HWR economics, safety and fuel cycles. 4 0 7 Technical Reports Series No. 407 The future directions likely to be taken in the development of HWR technology are addressed through discussion of three national programmes: the Canadian CANDU design, the Advanced HWR currently under development in India, and an 'Ultimate Safe' reactor being Reactors: Status and Projected Development Heavy Water designed in the Russian Federation. Heavy Water Reactors: Status and Projected Development ISBN 92–0–111502–4 ISSN 0074–1914 €99.00 INTERNATIONAL ATOMIC ENERGY AGENCY, VIENNA, 2002 HEAVY WATER REACTORS: STATUS AND PROJECTED DEVELOPMENT The following States are Members of the International Atomic Energy Agency: AFGHANISTAN GREECE PARAGUAY ALBANIA GUATEMALA PERU ALGERIA HAITI PHILIPPINES ANGOLA HOLY SEE POLAND ARGENTINA HUNGARY PORTUGAL ARMENIA ICELAND QATAR AUSTRALIA INDIA REPUBLIC OF MOLDOVA AUSTRIA INDONESIA ROMANIA AZERBAIJAN IRAN, ISLAMIC REPUBLIC OF RUSSIAN FEDERATION BANGLADESH IRAQ SAUDI ARABIA BELARUS IRELAND SENEGAL BELGIUM ISRAEL SIERRA LEONE BENIN ITALY SINGAPORE BOLIVIA JAMAICA SLOVAKIA BOSNIA AND HERZEGOVINA JAPAN SLOVENIA BRAZIL JORDAN SOUTH AFRICA BULGARIA KAZAKHSTAN SPAIN BURKINA FASO KENYA SRI LANKA -
General Conference ENGLISH Original: ENGLISH, FRENCH
International Atomic Energy Agency GC(XI)/INF/97/Add.1 28 September 1967 GENERAL Distr. General Conference ENGLISH Original: ENGLISH, FRENCH ELEVENTH REGULAR SESSION PROGRESS IN PEACEFUL APPLICATIONS OF NUCLEAR ENERGY DURING THE YEAR 1966-67 Further Statements by Member States PROGRESS IN PEACEFUL APPLICATIONS OF JWUCLEAR ENERGY DURING THE YEAR 1966/67 1 CANADA The past year has been one of progress Another development in the past year was and expansion for the Canadian nuclear power the conclusion of an agreement between the programme. Probably the most significant develop Governments of India and Canada to build a ment was the decision by Canada's largest electric second 200-MW(e) CANDU unit at the Rajasthan utility company, the Hydro Electric Power Atomic Power Project in north-west India. The Commission of Ontario, to add two 540-megawatt first Rajasthan unit is under construction and is units to its Pickering nuclear power station, now expected to begin operation in 1970. In Pakistan being built near the City of Toronto. This will the Canadian General Electric Company Limited double the station's capacity to more than are building a 137-.\lW(e) heavy-water-moderated, 2000 MW(e) and make it the second largest natural-uranium-fuelled nuclear power plant. nuclear power plant under construction in North Completion is scheduled for 1970. America. Ontario Hydro's decision, involving an estimated outlay of $256 million, offers further confirmation of the confidence placed in the Thus there now are in operation or under nuclear power system developed by the Crown construction in Canada and abroad six nuclear company, Atomic Energy of Canada Limited. -
Operational Strategy of a Two-Step Thermochemical Process for Solar Hydrogen Production
international journal of hydrogen energy 34 (2009) 4537–4545 Available at www.sciencedirect.com journal homepage: www.elsevier.com/locate/he Operational strategy of a two-step thermochemical process for solar hydrogen production Martin Roeb*, Martina Neises, Jan-Peter Sa¨ck, Peter Rietbrock, Nathalie Monnerie, Ju¨rgen Dersch, Mark Schmitz, Christian Sattler German Aerospace Center – DLR, Institute of Technical Thermodynamics, Solar Research, Linder Hoehe, 51147 Cologne, Germany article info abstract Article history: A two-step thermochemical cycle process for solar hydrogen production from water has Received 28 February 2008 been developed using ferrite-based redox systems at moderate temperatures. The cycle Received in revised form offers promising properties concerning thermodynamics and efficiency and produces pure 18 August 2008 hydrogen without need for product separation. Accepted 18 August 2008 The process works by cycling stationary ferrite-coated monoliths through sequential Available online 15 October 2008 oxidation and reduction steps at 1073 and 1473 K, respectively. By using two such mono- liths in parallel, it is possible to quasi-continuously produce hydrogen. A prototype solar Keywords: reactor and peripherals suitable to proof the process concept were developed and have Thermochemical cycle been successfully tested in DLR’s solar furnace in Cologne. Repeated cycling operation is Ferrites possible with a reproducible amount of hydrogen produced. In most cases, a distinct decay Solar thermal of the amount of the evolved hydrogen is observed from cycle to cycle due to inhomoge- Water splitting neous heating of the monolithic absorber in the very first cycles and due to disappearance Iron oxide of the porosity and the associated loss of surface area in later cycles. -
X-Ray Emission from National Ignition Facility Indirect Drive Targets
UCRL-JC-123557 X-Ray Emission from National Ignition Facility Indirect Drive Targets A. T. Anderson, R. A. Managan, M. T. Tobin, and P. F. Peterson AUG 1 6 1338 This paper was prepared for submittal to the American Nuclear Society 12th Topical Meeting on the Technology of Fusion Energy Reno, NV June 16-20,1996 This isapreprintofapaperintendedforpublicationina journal orproceedings. Since changes may be made before publication, this preprint is made available with the understanding that it will not be cited or reproduced without the permission of the author. DISTRIBUTION OF THIS DOCUMENT IS UNIMTED DISCLAIMER This document was prepared as an account of work sponsored by an agency of the United States Government Neither the United States Government nor the University of California nor any of their employees, makes any warranty, express or implied, or assumes any legal liability or responsibility for the accuracy, completeness, or usefulness of any information, apparatus, product, or process disclosed, or represents that its use would not infringe privately owned rights. Reference herein to any specific commercial product, process, or service by trade name, trademark, manufacturer, or otherwise, does not necessarily constitute or imply its-endorsement, recommendation, or favoring by the United States Government or the University of California. The views and opinions of authors expressed herein do not necessarily state or reflect those of the United States Government or the University of California, and shall not be used for advertising or product endorsement purposes. DISCLAIMER Portions of this document may be illegible in electronic image products. Images are produced from the best available origmal document.