Standard Compliant and Functionally Safe Engineering Design with Mechanical Auxiliary Contacts
Total Page:16
File Type:pdf, Size:1020Kb
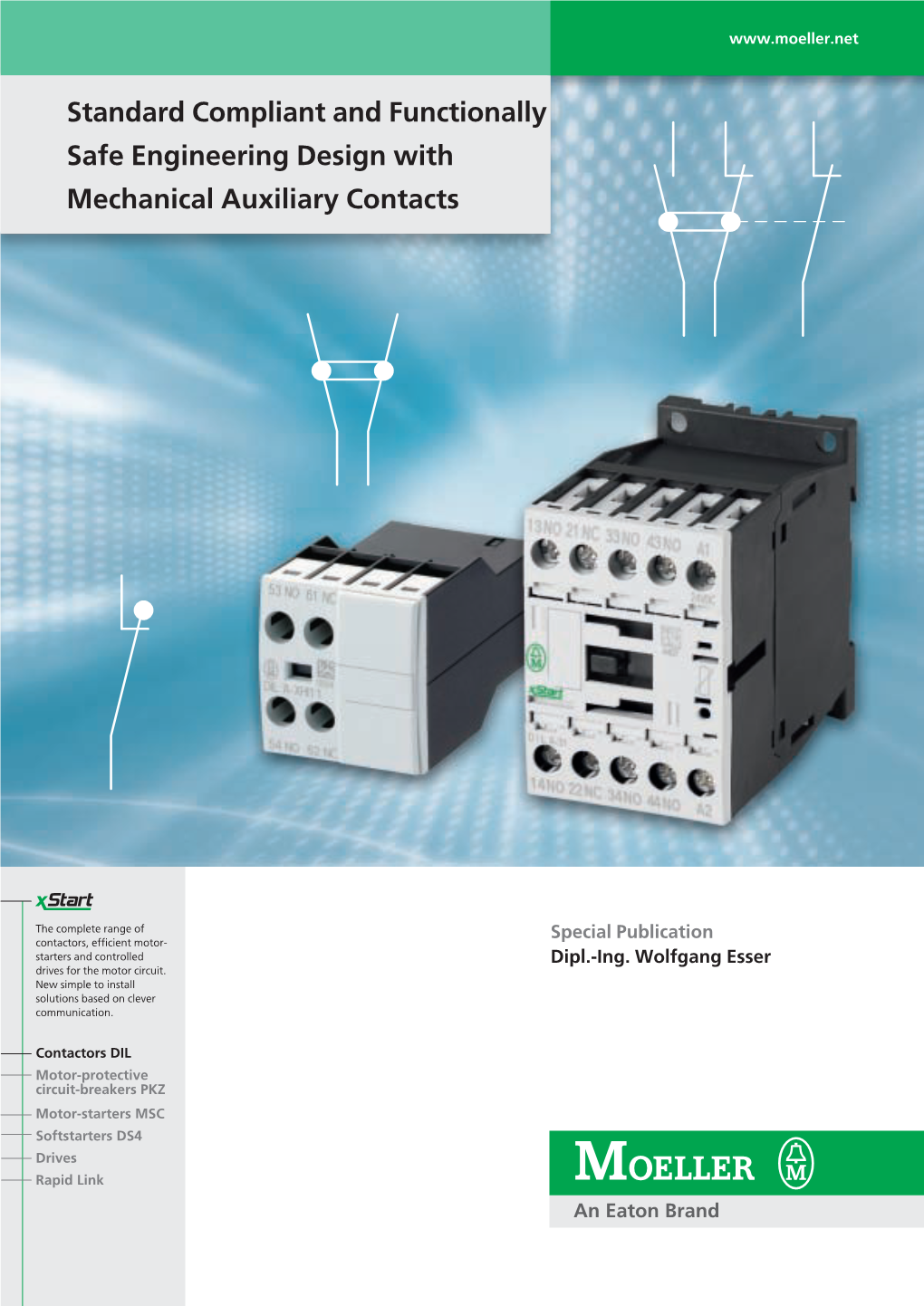
Load more
Recommended publications
-
GE Kv Vector Electricity Meter
GEH-5081B GE kV™ Vector Electricity Meter Product Description Option Board Installation Procedures, Operating Instructions, Maintenance Instructions and Site Analysis Guides Price: $ 30.00 Notice The information contained in this document is subject to change without notice. GE makes no warranty of any kind with regard to this material, including, but not limited to, the implied warranties of merchantability and fitness for a particular purpose. GE shall not be liable for errors contained herein or incidental consequential damages in connection with the furnishing, performance, or use of this material. This document contains proprietary information which is protected by copyright. All rights are reserved. No part of this document may be photocopied or otherwise reproduced without consent of GE. Copyright (c) 1997 by GE Published in a limited copyright sense, and all rights, including trade secrets, are reserved. Document Edition - First 4/96 - Version A 5/97 - Version B 11/97 kV™, Lexan™, MeterMate™, OPTOCOM™, Power Guard™, Site Genie™, Fitzall, and SMARTCOUPLER™ are trademarks of GE. FCC COMPLIANCE STATEMENT This product generates and uses radio frequency energy. It has been tested and verified that it complies with the limits for the Code of Federal Regualtions (CFR) 47, Part 15 Radio Frequency Devices, Subparts A General and B Unintentional Radiators issued by the Federal Communications Commission for Class “B” digital devices. If, however, the product causes radio or television interference, notify: Manager - Technology General -
Moeller Wiring Manual 02/05 Specifications, Formulae, Tables
Moeller Wiring Manual 02/05 Specifications, Formulae, Tables Page Marking of electrical equipment 9-2 Circuit symbols, European – North America 9-14 Circuit diagram example to North American specifications 9-27 Approval authorities worldwide 9-28 Test authorities and approval stamps 9-32 Protective measures 9-34 Overcurrent protection of cables and conductors 9-43 Electrical equipment of machines 9-51 Measures for risk reduction 9-56 Measures for risk avoidance 9-57 Degrees of protection for electrical equipment 9-58 North American classifications for control switches 9-68 9 Utilisation categories for contactors 9-70 Utilisation categories for switch-disconnectors 9-74 Rated motor currents 9-77 Conductors 9-81 Formulae 9-90 International unit system 9-94 For Immediate Delivery call KMParts.com at (866) 595-96169-1 Moeller Wiring Manual 02/05 Specifications, Formulae, Tables Marking of electrical equipment General Extracts from the DIN Standards with VDE The marking appears in a suitable position as Classification are quoted with the permission of close as possible to the circuit symbol. The the DIN (Deutsches Institut für Normung e.V.) and marking forms the link between the equipment in the VDE (Verband der Elektrotechnik Elektronik the installations and the various circuit documents Informationstechnik e.V.) It is imperative for the (wiring diagrams, parts lists, circuit diagrams, use of the standards that the issue with the latest instructions). For simpler maintenance, the date is used. These are available from complete marking or part of it, can be affixed on VDE-VERLAG GMBH, Bismarckstr. 33, 10625 or near to the equipment. -
Nortec RS Steam Humidifier Operation Manual
2582418-A EN | 06 AUG 2015 EN | 06 2582418-A OPERATION MANUAL Steam humidifier Nortec RS Humidification and Evaporative Cooling Thank you for choosing Nortec Installation date (MM/DD/YYYY): Commissioning date (MM/DD/YYYY): Site: Model: Serial number: Manufacturer Nortec Humidity Ltd. 2740 Fenton Road, Ottawa, Ontario K1T3T7 TEL: 1.866.NORTEC1, FAX: 613.822.7964 EMAIL: [email protected], WEBSITE: www.humidity.com Proprietary Notice This document and the information disclosed herein are proprietary data of Nortec Humidity Ltd. Neither this do- cument, nor the information contained herein shall be reproduced, used, or disclosed to others without the written authorization of Nortec Humidity Ltd., except to the extent required for installation or maintenance of recipient's equipment. Liability Notice Nortec Humidity Ltd. does not accept any liability due to incorrect installation or operation of the equipment or due to the use of parts/components/equipment that are not authorized by Nortec Humidity Ltd. Copyright Notice Copyright 2015, Nortec Humidity Ltd. All rights reserved. Technical modifications reserved Contents 1 Introduction 5 1.1 Before You Begin 5 1.2 Notes on the Operation Manual 5 2 For Your Safety 7 3 Product Overview 9 3.1 Construction Nortec RS steam humidifier 9 3.2 Functional Description 10 3.3 System Overview Nortec RS 11 3.4 System Overview Nortec RS for Direct Room Humidification 12 4 Operation 13 4.1 First-time Commissioning 13 4.2 Display and Operating Elements 13 4.3 Commissioning After an Interruption of Operation -
RELAY and CONTROL REQUIREMENTS for PARALLEL OPERATION of DISTRIBUTED GENERATION (12Kv and Below)
EU00536095 RELAY AND CONTROL REQUIREMENTS FOR Revision:0 PARALLEL OPERATION OF GENERATION Effective Date: 12/11/2017 Page 1 of 67 PPL ELECTRIC UTILITIES CORPORATION RELAY AND CONTROL REQUIREMENTS FOR PARALLEL OPERATION OF DISTRIBUTED GENERATION (12kV and below) REV. 0, 12/11/2017 By: Deepak Sharma Reviewer: signed Thien Hoang – Supervising Engineer Distribution Design and Standards Approver: signed Michael J. Wolf – Supervising Engineer Distribution Substation Design SHEET 1 of 67 EU00536095 RELAY AND CONTROL REQUIREMENTS FOR Revision:0 PARALLEL OPERATION OF GENERATION Effective Date: 12/11/2017 Page 2 of 67 TABLE OF CONTENTS TABLE OF CONTENTS ........................................................................................................................... 2 1 FOREWORD ........................................................................................................................................ 5 2 SCOPE ................................................................................................................................................... 6 3 OVERVIEW .......................................................................................................................................... 7 3.1 INITIATING A REQUEST TO INSTALL OR CHANGE OPERATION OF GENERATION EQUIPMENT ............................................................................................................................................................. 8 3.2 POINT OF CONTACT (POC) and INTERTIE PROTECTIVE RELAYING (IPR) ................................... -
Panasonic Switches
GENERAL CATALOG SWITCHES Panasonic Switches Development cycles in modern industry are becoming ever shorter and more complex, and they require a high degree of engineering. Components integrated into machines must therefore not only meet the current qualitative and technical standards but must also fulfill functional and application demands. Individual products can often only be integrated after they have been customized. Panasonic Electric Works has always stood for product innovation – also when it comes to mechanical switches. Our immense portfolio includes switches in all common sizes and with various IP degrees of protection, and are guaranteed to cover all standard requirements. Our switches are characterized by a large switching capacity range, long lifetime and exceptional reliability. A wide selection of supplemental actuators coupled with various terminal styles, e.g. solder, quick connect, PC board terminal and cable connections, maximize flexibility and ease application design. In addition, we concentrate on the development and implementation of customer-specific solutions: Does the cable have to be a little bit longer? Or is a pluggable solution necessary? With the engineering know-how at our European manufacturing sites, we guarantee flexible, on-time delivery and provide immediate, on-site technical support. Product lineup 36 3 1 8 ASQ ABJ ABS ABV 8 2 27. 8 AV4 AH1 AEQ AV3/AVM3/AVT3/AVL3 AV6 AM5 AM1 AV1 AGX AJ7/8 T Series Tailoring equipment 2 Contents Selector Chart........................................................... 4 AM5 (QV) switches (contact gap more than 1mm).. 80 Micro switches IP67.................................................... 4 AEQ (EQ) switches.................................................. 81 Micro switches IP40.................................................... 6 AV (FS•FS-T) switches............................................ 86 Basic switches...................................................... -
Technical Information ■ Relay Classification
Introduction Introduction Technical Information ■ Relay Classification Model Mounting Enclosure Ratings Features G4W Discrete Unsealed Designed for manual soldering. G2R Flux protection Designed inhibits flux intrusion into the casing from the ter- minals during soldering. G6A Sealed Sealed resin casings and covers, limiting damage from cor- rosive atmospheres. G6S Surface mounting Surface mounting relays permit automatic reflow soldering. ■ Construction Sealing Sealed Relays Unsealed Relays Fully sealing prevents not only flux, but also cleaning solvent from Relays of this type are intended for manual soldering. No mea- penetrating into the relay housing. Therefore, this type of relay sures are taken against penetration of flux and cleaning solvent can be immersion-cleaned. Relays are each tested before being into the relay. This type of relay cannot be immersion-cleaned. shipped. The relay is immersed in fluorocarbon solution for 1 +5°C Flux-protection Relays minute, at a temperature of 70°C /−0°C, to see if gases escape from the relay. The following figure illustrates the test conditions. Special design construction prevents flux from penetrating into the relay housing, for example, due to capillary action up the ter- minals when the relay is soldered onto a PCB. This type of relay also cannot be immersion-cleaned. 50 mm Ex.) 70 °C Relay Fluorocarbon solution Classification Unsealed Flux protection Construction Contacts located at Press-fit terminals Inserted terminals upper part of relay case Terminals separated from PCB Terminals Resin seal separated Terminals from PCB separated 0.3 mm from PCB min. base thickness Features Terminals are separated Contacts are positioned Terminals are pressed Terminals are inserted from PCB surface when away from base. -
2003 Cat.Pdf
What’s New - New Products - What’s New High Voltage Reed Switches Tilt Switch See page 37 This series of switches is designed for Non-Mercury relays which are used in high reliability areas of the elec- trotechnical and electronic industry including electronic medical equip- Changeover ment; cable tester arrays and cable test equipment; copy machines; laser optical systems and infrared equipment; test equipment S1234 They provide high voltage stand-off and switching capability. The tung- See page 78 sten plated contacts give both a low stable CR and a long and reliable life. Surface Mount Mercury free changeover tilt switch with hermetically sealed gold contacts, Switch and and a case size of just 7.6mm. It’s rugged construction makes this Sensors switch suitable for many uses in secu- The Comus Group can now supply rity products, alarm and general move- surface mount termination for a wide ment sensing. rated at 60V, 0.2A and range of products. The gold plated clips See page 70 3VA Max. give good solderability and are designed to provide stability during assembly. Magtrix Connectors are versatile miniature Magtrix Neodymium-iron-boron nickel plated 6.0 Dia x Connector 5mm long magnets connected to a 40 x 0.65mm Dia. copper-tin plated flexible lead, with an operating MC/53GNS temperature of 120°C and a maximum power rating See page of 8 Amps. Primarily designed for use as battery connectors, 68 they are also ideal for proximity sensor and reed switch triggering, connecting PCBs, test equipment connections and prototypes where connections need to be made quickly. -
• Relay Contact Protection • Noise Reduction on Controllers/Drivers • Dv
Type Q/QRL Quencharc®Capacitor RC Snubber Network Arc Suppressor • Relay contact protection • Noise reduction on controllers/drivers Snubber Network • dv/dt suppression on thyristor and triacs • EMI/RFI reduction • No lag time in suppression • Available voltages: 125 VAC - 660 VAC • Type QRL – UL/CSA version L Max. TMax. ® Quencharc¤ ITW PAKTRON QUENCHARC¤ Arc Suppressor Snubber Network ITW PAKTRON H Max. Q/QRL QUENCHARC¤ UL/CSA version .25" Max. .850" Min. ARCING, SPARKING, and TRANSIENTS often cause premature failures in relays, switches, thyristors, triacs, contactors, and related products. Paktron QUENCHARCS¤ extend operating life when properly selected and applied. D Typ. VoltagE WavefoRM CURRENT WavefoRM Electrical Schematic Non-polarized UNSUPPRESSED SUPPRESSED UNSUPPRESSED SUPPRESSED 100V/div .1ms/div 100V/div .5ms/div 100V/div .1ms/div 100V/div .1ms/div PF Value Voltage Type Ohms Watt L T H D Part Code µF VDC/VAC ±10% MAX MAX MAX Typical Number 104 .1 600 / 250 QC 22 .5 1.08 (27.4) .39(9.9) .66 (16.7) .82 (20.8) 104M06QC22 104 .1 600 / 250 QC 47 .5 1.08 (27.4) .39(9.9) .66 (16.7) .82 (20.8) 104M06QC47 104 .1 600 / 250 QC 100 .5 1.08 (27.4) .39(9.9) .66 (16.7) .82 (20.8) 104M06QC100 104 .1 600 / 250 QC 150 .5 1.08 (27.4) .39(9.9) .66 (16.7) .82 (20.8) 104M06QC150 104 .1 600 / 250 QC 220 .5 1.08 (27.4) .39(9.9) .66 (16.7) .82 (20.8) 104M06QC220 104 .1 600 / 250 QC 330 .5 1.08 (27.4) .39(9.9) .66 (16.7) .82 (20.8) 104M06QC330 104 .1 1200/480 QH 39 2.0 1.60(40.6) .64(16.3) 1.04(26.4) 1.29(32.7) 104M48QH39 104 .1 1600/660 QV 39 2.0 -
Operation Manual
NORTEC 1905 EN D 2582418- OPERATION MANUAL Steam humidifier Nortec RS series Humidification and Evaporative Cooling Thank you for choosing Condair Installation date (MM/DD/YYYY): Commissioning date (MM/DD/YYYY): Site: Model: Serial number: Contact Condair Ltd. 2740 Fenton Road, Ottawa, Ontario K1T3T7 TEL: 1.866.667.8321, FAX: 613.822.7964 EMAIL: [email protected], WEBSITE: www.condair.com Proprietary Notice This document and the information disclosed herein are proprietary data of Condair Ltd. Neither this document, nor the information contained herein shall be reproduced, used, or disclosed to others without the written authorization of Condair Ltd., except to the extent required for installation or maintenance of recipient's equipment. Liability Notice Condair Ltd. does not accept any liability due to incorrect installation or operation of the equipment or due to the use of parts/components/equipment that are not authorized by Condair Ltd. Copyright Notice © Condair Ltd. All rights reserved. Technical modifications reserved Contents 1 Introduction 5 1.1 To the very beginning 5 1.2 Notes on the operation manual 5 2 For your safety 7 3 Product Overview 9 3.1 Construction Nortec RS steam humidifier 9 3.2 Functional description 10 3.3 System overview Nortec RS 11 3.4 System overview Nortec RS for direct room humidification 12 4 Operation 13 4.1 First-time commissioning 13 4.2 Display and operating elements 13 4.3 Commissioning after an interruption of operation 14 4.4 Notes on operation 15 4.4.1 Inspections during operation 15 4.4.2 Remote -
Sensor Switch Product Catalog
/ Lighting Controls Product Catalog It’s not just smarter. It’s easier. Acuity Controls is advanced lighting controls technology, service and support from a single expert source. We offer one of the industry’s most extensive product portfolios for indoor and outdoor applications, single rooms to campuses to municipalities. Our product solutions include occupancy and photosensors, panels, switches, fixture-level and wireless controls. Printed on Recycled Paper Contents 5 ABOUT SENSOR SWITCH 38 DAYLIGHTING CONTROL SENSORS 6 Benefits 38 Ceiling Mount 7 Sensor Technology 42 Recessed Mount 8 Sensorpedia: Occupancy Sensor Reference Guide 48 Fixture Mount 54 Fixture Mount Interchangeable Lens 21 PRODUCT SELECTION GUIDE 22 Wall Switch Controls 60 POWER PACKS 32 Wireless Products 34 Ceiling Mount Sensors 75 SPECIALTY PRODUCTS 40 Recessed Mount Sensors 76 Data Logging Monitoring System 44 Fixture Mount Sensors 78 Wire Guards 50 Fixture Mount Interchangeable Lens Sensors 79 Masking Labels 56 Wide View & Hallway Sensors 79 Ballast Discriminator 58 Outdoor Sensors 60 Power Packs 81 WIRING DIAGRAMS 62 Micro Enclosure 64 Snap-Fit 94 INDEX 69 Embedded The Sensor Switch product line Performance from Acuity Controls provides an innovative, high quality and You Can Count On! cost-effective controls solution for every application. Our occupancy Our Passive Dual Technology (PIR/Microphonics™) sensors and photocell products are • looks and listens for occupants ensuring reliable detection easy to install and easy to use. • Reversible line and load wires make Sensor Switch products easy to install • Reliable-circuit protection tested for over 400,000 switching cycles • Continuous coverage patterns for a breadth of applications meeting your every need • 5-year limited product warranty • Sensor Switch products aid in ensuring buildings meet applicable energy codes (Title 24, ASHRAE and IECC) www.acuitycontrols.com / 5 BENEFITS Energy Savings The Sensor Switch offering of occupancy and daylight sensors are designed to optimize energy savings and enable sustainability. -
Relay Contact Life
Application Note Relay Contact Life Relay contacts are available in a variety of metals and alloys, sizes and Because silver and silver alloys sulfidate, contact pressures must be great styles. There is no such thing as a universal contact. The relay user enough to break through this film. (Controlled arcing will also be helpful should select contact materials, ratings, and styles to meet, as precisely in that it burns off the sulfidation, and contact overtravel wipes away the as possible, the requirements of a particular application. Failure to do so residue.) While such pressures have no appreciable effect on silver- can result in contact problems and even early contact failure. cadmium contacts, they do result in increased material wear of fine silver contacts. Also, an interface voltage of several tenths of a volt can result For example, some contact materials require an arc to keep them free of with fine silver contacts because of the sulfide film. This film has been sulfidation, oxidation, and contaminates. Such materials on contacts known to capture and imbed airborne dirt. Breaking through this film used in a dry or low-level circuit can result in the contacts failing electrically generates electrical noise. Because of this, fine silver contacts are not to close the circuit, even though they make physically. The contacts may used for low-level switching, such as audio circuits. Rather, fine silver look clean, but this is deceiving. In reality, there is a very thin film of and silver alloy contacts are for use in circuits of 12 volts, 0.4 ampere, or insulating sulfidation, oxidation or contaminates on the surface of the more. -
Reed Switch Protection
G::9HL>I8=EGDI:8I>DC Reed Switch Protection The hermetically-sealed reed switch used in GEMS level switches are 6EE:C9>MM extremely rugged and designed to operate reliably for many years – The dependable reed 2 million cycles under ideal conditions. To achieve the maximum switch is at the heart of most level switch shown service life, reed switches benefit from protected electrical supply. in this catalog. IMPORTANT: s$ONTBEMISLEDBYTHERESISTIVERATINGSOFTHESWITCHES-OSTAPPLICATIONSINVOLVE inductive loads. s$ONTBEMISLEDBYTHEWATTAGERATINGSOFLOADS,OWWATTAGELOADSAREOFTENHIGH inductive devices, making contact protection very important. Contact Protection Requirements When switching inductive loads such as relays, solenoids and transformers, reed switch contacts require protection in order to ensure long, dependable life. When current is interrupted, the inductance or electrical inertia of the load generates a large high frequency voltage, which appears across the switch contacts. If the voltage is large enough, it can break down the medium in the gap between them, making a conductive path. This phenomenon, called “arcing,” is the spark you see. Arcing can cause the contacts to burn, weld together or stick; thus, giving unreliable performance. The purpose of protection circuits is to prevent arcing, by shorting this voltage through an alternate path. Recommended Protection D.C. A 1N4004 diode (or equivalent) connected cathode-to-positive, as shown in Figure 1, is recommended. The diode does not conduct when the load is energized, but conducts and shorts out the generated voltage when the switch opens. The generated voltage Figure 1 always acts in series with the applied voltage. $##ONTACT (DRAIN THE LOAD) Protection $RAINTHE,OAD A.C. REED INDUCTIVE A resistor and capacitor, connected in parallel with the switch, as shown in Figure 2, SWITCH LOAD is recommended.