Improving Calibration Results for Optical Spectrometers
Total Page:16
File Type:pdf, Size:1020Kb
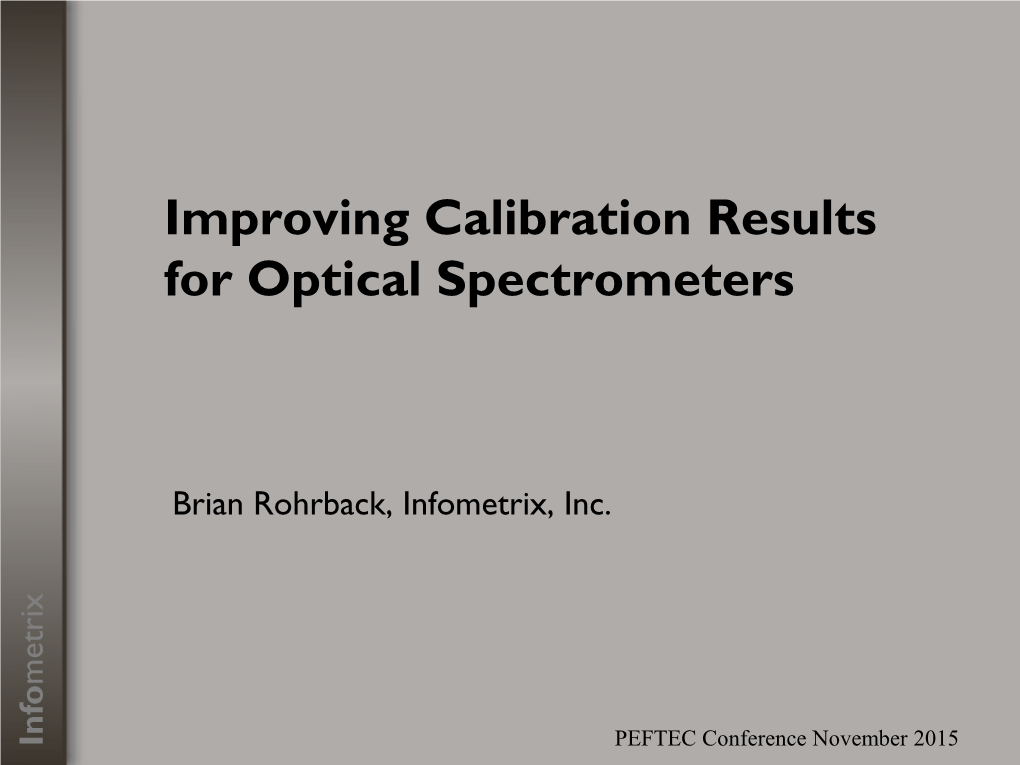
Load more
Recommended publications
-
Ultrasensitive Detection of Waste Products in Water Using Fluorescence Emission Cavity-Enhanced Spectroscopy
Ultrasensitive detection of waste products in water using fluorescence emission cavity-enhanced spectroscopy Joel N. Bixlera, Michael T. Conea, Brett H. Hokra, John D. Masona, Eleonora Figueroaa, Edward S. Frya, Vladislav V. Yakovleva, and Marlan O. Scullya,b,c,1 aTexas A&M University, College Station, TX 77843; bPrinceton University, Princeton, NJ 08540; and cBaylor University, Waco, TX 76706 Contributed by Marlan O. Scully, March 5, 2014 (sent for review December 1, 2013; reviewed by Peter M. Rentzepis and Vadim Backman) Clean water is paramount to human health. In this article, we ecosystem can result in environmental crises, such as devastation present a technique for detection of trace amounts of human to the aquatic population, red-tide blooms, as well as beach or animal waste products in water using fluorescence emission closings. Molecular methods based on polymerase chain reac- cavity-enhanced spectroscopy. The detection of femtomolar con- tions are commonly used to monitor viral, bacterial, and pro- centrations of urobilin, a metabolic byproduct of heme metabo- tozoan pathogens in wastewater (9). Microbiological indicators lism that is excreted in both human and animal waste in water, such as fecal coliforms, Escherichia coli and Etherococci, are the was achieved through the use of an integrating cavity. This indicators most commonly used to analyze and evaluate the level technique could allow for real-time assessment of water quality of fecal contamination. However, the suitability of these indi- without the need for expensive laboratory equipment. cators has been questioned (10), and it takes a substantial time from the extraction of water sample for analysis to the moment water contamination | fluorescence spectroscopy | femtomolar detection when the results are ready. -
Fourier Transformation of an Interferogram
CHEM 411L Instrumental Analysis Laboratory Revision 1.0 Fourier Transformation of an IR Interferogram In this laboratory exercise we will use a Fourier Transform Infrared (FTIR) spectrometer to generate a time domain Interferogram for a simple organic liquid. We will then Fourier Transform this data to obtain a frequency domain Infrared Spectrum for the sample. Time domain spectrometers were initially developed during the 1950's for the acquisition of Infrared Spectra (IR) and are now in almost universal use as IR, NMR and mass spectrometers. This is because with modern electronic computers rapid Fourier Transformation (FT) of time domain signals into frequency domain spectra is now possible. The time domain signal from an FT spectrometer is sampled using an analog-to-digital converter, loaded in a digital computer's memory and then computationally transformed to the frequency domain. The advantages of FT spectroscopy are multiple: A greater throughput of radiant power to the instrument's detector resulting in a greater signa-to-noise ratio. A greater resolving power for the instrument. A rapid spectral acquisition time. These advantages are considerable and mean spectra with considerable detail and better detection limits are possible. In a typical frequency domain optical spectrometer, radiation from a source enters a monochrometer where a particular wavelength or frequency is selected, then allowed to pass through a sample of the analyte and the resulting signal is then detected. P a g e | 2 The radiant power at the detector P is then compared to the power of the radiation of the source Po to determine the sample's transmittance T at the given frequency : T = (Eq. -
Center for Nanoscale Materials Tools and Capabilities
CENTER FOR NANOSCALE MATERIALS TOOLS AND CAPABILITIES Nanofabrication ¨ Lambda Microwave Plasma CVD System: ¨ Other specialized analysis and Devices Nanocrystalline Diamond Deposition software or modeling expertise ¨ Oxford Plasmalab 100 Inductively Lithography Coupled Plasma Enhanced Chemical Nanophotonics and ¨ Electron Beam Lithography: JEOL 8100FS Vapor Deposition Biofunctional Structures ¨ Electron Beam Lithography: Raith 150 ¨ Thermal/PECVD System for CNT and Graphene Synthesis Bench-Top Spectroscopy ¨ Focused Ion Beam: FEI Nova 600 NanoLab ¨ AJA Dielectric Sputtering System ¨ UV-Visible Absorption ¨ ¨ Heidelberg MLA 150 Maskless Lithography ¨ AJA Metal Sputtering System Emission (uv-vis, NIR, MIR) ¨ ¨ Interferometric Lithography System ¨ Atomic Layer Deposition FTIR Absorption (Arradiance Gemstar) ¨ ¨ Laser Pattern Generator (Microtech Circular Dichroism LW405, Direct Write Optical Lithography) ¨ Integrated UV-Ozone Cleaner and ¨ Cryostat/Temperature Control ¨ SUSS MA6/BA6: Contact aligner for front Molecular Vapor Coater (NanoneX Magneto-optical Microscope (MOM) side and front-to-back side alignment Ultra-100) Magneto-Electro-Optical Spectrometer ¨ Wafer Priming Oven: YES-TA Series Piezo-Optomechanical Spectrometer (MEOS) ¨ Stepper: ASML PAS 5000 Wafer Stepper (POMS) Raman Spectroscopy Post-Processing Ultralow Temperature/Strong Magnetic ¨ Temperature-Controlled Stage ¨ AS-One 150 Rapid Thermal Processor Field Measurements ¨ Cleaving Machine: LatticeGear AX 420 Electron Paramagnetic Resonance ¨ BlueFors LD400 Dilution Refrigerator -
THE GLOW DISCHARGE - a MULTIFACETED OPTICAL EMISSION SOURCE: from SOLIDS ANALYSIS to METALLOPROTEINS Timothy Brewer Clemson University, [email protected]
Clemson University TigerPrints All Dissertations Dissertations 5-2007 THE GLOW DISCHARGE - A MULTIFACETED OPTICAL EMISSION SOURCE: FROM SOLIDS ANALYSIS TO METALLOPROTEINS Timothy Brewer Clemson University, [email protected] Follow this and additional works at: https://tigerprints.clemson.edu/all_dissertations Part of the Analytical Chemistry Commons Recommended Citation Brewer, Timothy, "THE GLOW DISCHARGE - A MULTIFACETED OPTICAL EMISSION SOURCE: FROM SOLIDS ANALYSIS TO METALLOPROTEINS" (2007). All Dissertations. 62. https://tigerprints.clemson.edu/all_dissertations/62 This Dissertation is brought to you for free and open access by the Dissertations at TigerPrints. It has been accepted for inclusion in All Dissertations by an authorized administrator of TigerPrints. For more information, please contact [email protected]. THE GLOW DISCHARGE - A MULTIFACETED OPTICAL EMISSION SOURCE: FROM SOLIDS ANALYSIS TO METALLOPROTEINS _____________________________________________ A Dissertation Presented to the Graduate School of Clemson University _____________________________________________ In Partial Fulfillment of the Requirements for the Degree Doctor of Philosophy Chemistry _____________________________________________ by Tim M. Brewer May 2007 _____________________________________________ Accepted by: Dr. R. Kenneth Marcus, Committee Chair Dr. Kenneth Christensen Dr. Stephen Creager Dr. Julia Brumaghim ABSTRACT Glow discharges (GD) are well known for their application to direct solids elemental analysis of metals and alloys by optical emission -
AAS, GFAAS, ICP Or ICP-MS? Which Technique Should I Use? an Elementary Overview of Elemental Analysis
1069 primer reprint 11/29/01 2:41 PM Page 3 AAS, GFAAS, ICP or ICP-MS? Which technique should I use? An elementary overview of elemental analysis. 1069 primer reprint 11/29/01 2:41 PM Page 4 Start here. If your laboratory is performing elemental analysis on solutions, there are a number of mature, effective spectrometric techniques you could use, including flame and furnace AA (Atomic Absorption), ICP (Inductively Coupled Plasma), and ICP-MS (ICP Mass Spectrometry). Selecting the most appropriate tool for the job can sometimes appear to be a daunting task, especially since there is considerable overlap of capabilities. In fact, all of the techniques may be able to perform your particular analysis at acceptable levels of accuracy and precision. However, by evaluating the relative strengths and weaknesses of each of the techniques, particularly as they may apply to the practical and performance requirements of your analysis, it is possible to establish a rational basis for decision making. In other words, it needn’t be all that difficult. Even if you’re new to elemental analysis, this booklet will get you well on your way to selecting the best technique (or techniques) to meet your lab’s needs. Understanding how each technique works. While it isn’t necessary to grasp all of the complex technological details of each of the various elemental analysis instruments, for comparison purposes it is helpful to have a general understanding of basic principles. Let’s start at the beginning, with atomic absorption. 2 1069 primer reprint 11/29/01 2:42 PM Page 5 Percent Relative Standard Deviation (% RSD) Short-term stability The standard deviation expressed as a percentage of the total. -
Design of a Simple Optical Spectrometer
DESIGN AND FABRICATION OF A PORTABLE SPECTROMETER TO INVESTIGATE OPTICAL PROPERTIES OF THIN FILMS BENARD RIRO MORUMBWA [B.Ed. (Sc)] I56/10991/2006 ` A thesis submitted in partial fulfillment of the requirements for the award of the degree of Master of Science (Electronics and Instrumentation) in the School of Pure and Applied Sciences of Kenyatta University June, 2013 ii DECLARATION This thesis is my original work and has not been presented for the award of a degree or any other award in any other University Benard Riro Morumbwa …………………………. ……………………….. Department of Physics Signature Date Kenyatta University P.O. BOX 43844 - 00100 NAIROBI- KENYA We confirm that the work reported in this thesis was carried out by the candidate under our supervision. Dr. Patrick M. Karimi ………………………….. …………………………. Department of Physics Signature Date Kenyatta University P.O. BOX 43844 - 00100 NAIROBI- KENYA Dr. Daniel M. Wamwangi ……… ……10.06.2013…… School of Physics Signature Date University of Witswatersrand PRIVATE BAG 3, 2050 JOHANNESBERG - SOUTH AFRICA iii DEDICATION This thesis is dedicated to my wife Stellah Kemunto and my daughters, Brenda and Mitchell. iv ACKNOWLEDGEMENTS I thank in a special way Dr. P.M. Karimi and Dr. D. Wamwangi for their invaluable support, guidance and advice which enabled successful completion of this research. I do appreciate the attention and timely response they gave whenever I was in need of help. Their wide and in-depth knowledge in material science, electronics and instrumentation gave me the courage and ability I needed most in doing this work. I once more thank them for the great efforts and sacrifice they made to ensure that this work was a success. -
Proceedings of the 2019 Joint Workshop of Fraunhofer IOSB And
A Theoretical Model for Measuring and Sensor Characterization in Optical Spectroscopy Julius Krause Vision and Fusion Laboratory Institute for Anthropomatics Karlsruhe Institute of Technology (KIT), Germany [email protected] Technical Report IES-2019-11 Abstract The optical and digital resolution, as well as the signal-to-noise ratio are important characteristics of optical spectrometers and available in data sheets. But how can an optical spectrometer system be selected for a specific application? The article shall serve as an aid to characterize optical spectrometers and hyperspectral cameras by introducing a benchmark calculation which indicates the measurement uncertainty of absorption bands. 1 Introduction In optical spectroscopy, the wavelength depended intensity of light is measured. Due to the interaction between light and matter, the direction of the light propagation can change by elastic scattering processes. Furthermore, light can be absorbed by interaction with molecules, which changes the intensity of the light. The wavelength dependent probability of light scattering and absorption depends on the material properties of the sample. Therefore, it is possible 69 Julius Krause to determine material properties of the sample by recording its reflected or transmitted optical spectrum. Applications can be found in various fields like smart agriculture, food industry as well as in petro chemistry [9]. Due to the continuously advancing development of microsystems technology (MEMS), miniaturized spectrometers and hyperspectral camera systems can be manufactured cost-effectively and in large quantities. In order to achieve a comparability of sensors of different types, a benchmark parameter is presented below, which links the sensor noise with the optical and digital resolution. -
Market Brief: Vacuum & Optical Technologies for ICP-OES
SOLUTIONS IN ANALYTICAL INSTRUMENTATION Vacuum & Optical Technologies for ICP-OES Broad product portfolio of reliable, innovative solutions for your most challenging Inductively Coupled Plasma Optical Emission Spectroscopy (ICP-OES) applications Introduction ICP-OES, also known as ICP-AES (Atomic Emission Spectroscopy), is a widely used analytical technique for trace element analysis in predominantly water-dissolved samples; capable of measuring a majority of the elements in the periodic table. This technique was first devised in the early 1970s and now boasts an install base of more than 50,000 units. It is a type of emission spectroscopy that uses an Inductively Coupled Plasma (ICP) to excite the sample to produce ions that emit electromagnetic radiation at wavelengths characteristic of particular elements in the sample. Solving key challenges The intensity of this emission is indicative of the concentration of the element in ICP-OES within the sample. ICP-OES, a very versatile technique, allows reliable, simultaneous, and sequential analysis of multiple elements. Its stability offers • Gas Flow Measurement & Control high sensitivity and low limits for detection of a majority of elements. • Diffraction Gratings The ICP-OES instrument has two main subsystems – the ICP and the optical spectrometer. In the ICP subsystem, a precisely controlled amount of • Custom Vacuum Machining Argon gas supplied to a torch coil is ionized, generating plasma. The optical • Integrated Optical Subassemblies subsystem consists of a light source, a spectrophotometer and a detector. As the electrons are excited by the extreme heat of the plasma (up to 7,000K), • Vibration Isolation Systems they reach an excited energy state. When they drop back to ground energy • Optical Components level, some energy is emitted as photons. -
Re-Engineering Calibration in Optical Spectroscopy
RE-ENGINEERING CALIBRATION IN OPTICAL SPECTROSCOPY Randy J. Pell, Michael F. Roberto, L. Scott Ramos, and Brian G. Rohrback Infometrix, Inc. 11807 North Creek Parkway S #B-111 Bothell, WA 98011 KEYWORDS Calibration, Chemometrics, Best Practices, Spectroscopy, Refining, PLS, Modeling ABSTRACT A project has been undertaken to assess how to reduce the amount of effort devoted to maintaining and optimizing spectroscopic model performance in support of refinery and chemical plant labs. Over the last five years, a series of algorithmic approaches have been examined with the goal of streamlining the process of chemometric model construction to make the models significantly more robust when put into routine practice. This effort generated the following observations: 1. Even though there are published “Best Practices” for generating chemometric models, these practices are infrequently followed; 2. Recalibration of an optical spectrometer is frequently required due to changes in crude slates and blending component composition; 3. Even if a calibration was performed properly during initial installation, staffing changes and lack of training has undermined recalibrations; and 4. It is of benefit to minimize software maintenance frequency to control product giveaway. This paper focuses on a multi-organization effort leading to an improvement in calibration procedures for on-line and laboratory multiwavelength spectrometers. Here the authors detail the process of calibration and demonstrate a path to build calibrations that are more reliable and potentially less sensitive to process shifts. Much of this improvement can be attained without requiring replacement of either the hardware or software in place. Additional improvement in calibration quality is available through the use of well-referenced methods that constitute the best technologies available. -
Scoping Study to Expedite Development of a Field Deployable and Portable Instrument For
LBNL-2001050 Scoping study to expedite development of a field deployable and portable instrument for UF6 enrichment assay Final Report July 2017 George Chan John Valentine Richard Russo Lawrence Berkeley National Laboratory This document was prepared as an account of work sponsored by the United States Government. While this document is believed to contain correct information, neither the United States Government nor any agency thereof, nor the Regents of the University of California, nor any of their employees, makes any warranty, express or implied, or assumes any legal responsibility for the accuracy, completeness, or usefulness of any information, apparatus, product, or process disclosed, or represents that its use would not infringe privately owned rights. Reference herein to any specific commercial product, process, or service by its trade name, trademark, manufacturer, or otherwise, does not necessarily constitute or imply its endorsement, recommendation, or favoring by the United States Government or any agency thereof, or the Regents of the University of California. The views and opinions of authors expressed herein do not necessarily state or reflect those of the United States Government or any agency thereof or the Regents of the University of California. Final Report: Scoping study to expedite development of a field deployable and portable instrument for UF6 enrichment assay George Chan, John Valentine, and Richard Russo Lawrence Berkeley National Laboratory This work was performed under the auspices of the U.S. Department of Energy by Lawrence Berkeley National Laboratory under Contract DE-AC02-05CH11231. The project was funded by the Safeguards Technology Development Program in the U.S. Department of Energy/National Nuclear Security Administration’s (DOE/NNSA’s) Office of Nonproliferation and Arms Control (NPAC). -
High-Performance Ultra-Thin Spectrometer Optical Design Based on Coddington's Equations
sensors Letter High-Performance Ultra-Thin Spectrometer Optical Design Based on Coddington’s Equations Zhiwei Feng 1, Guo Xia 2,3,4,*, Rongsheng Lu 1, Xiaobo Cai 1, Hao Cui 1 and Mingyong Hu 2,3,4 1 School of Instrument Science and Opto-Electronics Engineering, Hefei University of Technology, Hefei 230009, China; [email protected] (Z.F.); [email protected] (R.L.); [email protected] (X.C.); [email protected] (H.C.) 2 Academy of Opto-Electric Technology, Hefei University of Technology, Hefei 230009, China; [email protected] 3 Special Display and Imaging Technology Innovation Center of Anhui Province, Hefei 230009, China 4 National Engineering Laboratory of Special Display Technology, Hefei 230009, China * Correspondence: [email protected] Abstract: A unique method to design a high-throughput and high-resolution ultrathin Czerny–Turner (UTCT) spectrometer is proposed. This paper reveals an infrequent design process of spectrometers based on Coddington’s equations, which will lead us to develop a high-performance spectrometer from scratch. The spectrometer is composed of cylindrical elements except a planar grating. In the simulation design, spot radius is sub-pixel size, which means that almost all of the energy is collected by the detector. The spectral resolution is 0.4 nm at central wavelength and 0.75 nm at edge wavelength when the width of slit is chosen to be 25 µm and the groove density is 900 lines/mm. Keywords: optical design; Czerny–Turner spectrometer; cylindrical lens 1. Introduction Citation: Feng, Z.; Xia, G.; Lu, R.; Cai, X.; Cui, H.; Hu, M. -
Digital Fourier Transform Spectroscopy: a High-Performance, Scalable Technology for On-Chip Spectrum Analysis
Digital Fourier transform spectroscopy: a high-performance, scalable technology for on-chip spectrum analysis Derek M. Kita1,*, Brando Miranda2, David Favela3, David Bono1, Jérôme Michon1, Hongtao Lin1, Tian Gu1 and Juejun Hu1,* 1Department of Materials Science & Engineering, Massachusetts Institute of Technology, Cambridge, Massachusetts, USA 2Center for Brains, Minds & Machines, Massachusetts Institute of Technology, Cambridge, Massachusetts, USA 3Department of Mechanical Engineering, Massachusetts Institute of Technology, Cambridge, Massachusetts, USA *[email protected], [email protected] Introductory paragraph Optical spectrum analysis is the cornerstone of spectroscopic sensing, optical network performance monitoring, and hyperspectral imaging. While conventional high-performance spectrometers used to perform such analysis are often large benchtop instruments, on-chip spectrometers have recently emerged as a promising alternative with apparent Size, Weight, and Power (SWaP) advantages. Existing on-chip spectrometer designs, however, are limited in spectral channel count and signal-to-noise ratio (SNR). Here we demonstrate a transformative on-chip digital Fourier transform (dFT) spectrometer that can acquire high-resolution spectra via time- domain modulation of a reconfigurable Mach-Zehnder interferometer. The device, fabricated and packaged using industry-standard silicon photonics technology, claims the multiplex advantage to dramatically boost SNR and unprecedented scalability capable of addressing exponentially increasing numbers