Compressed Air Treatment (Dryers and Filters)
Total Page:16
File Type:pdf, Size:1020Kb
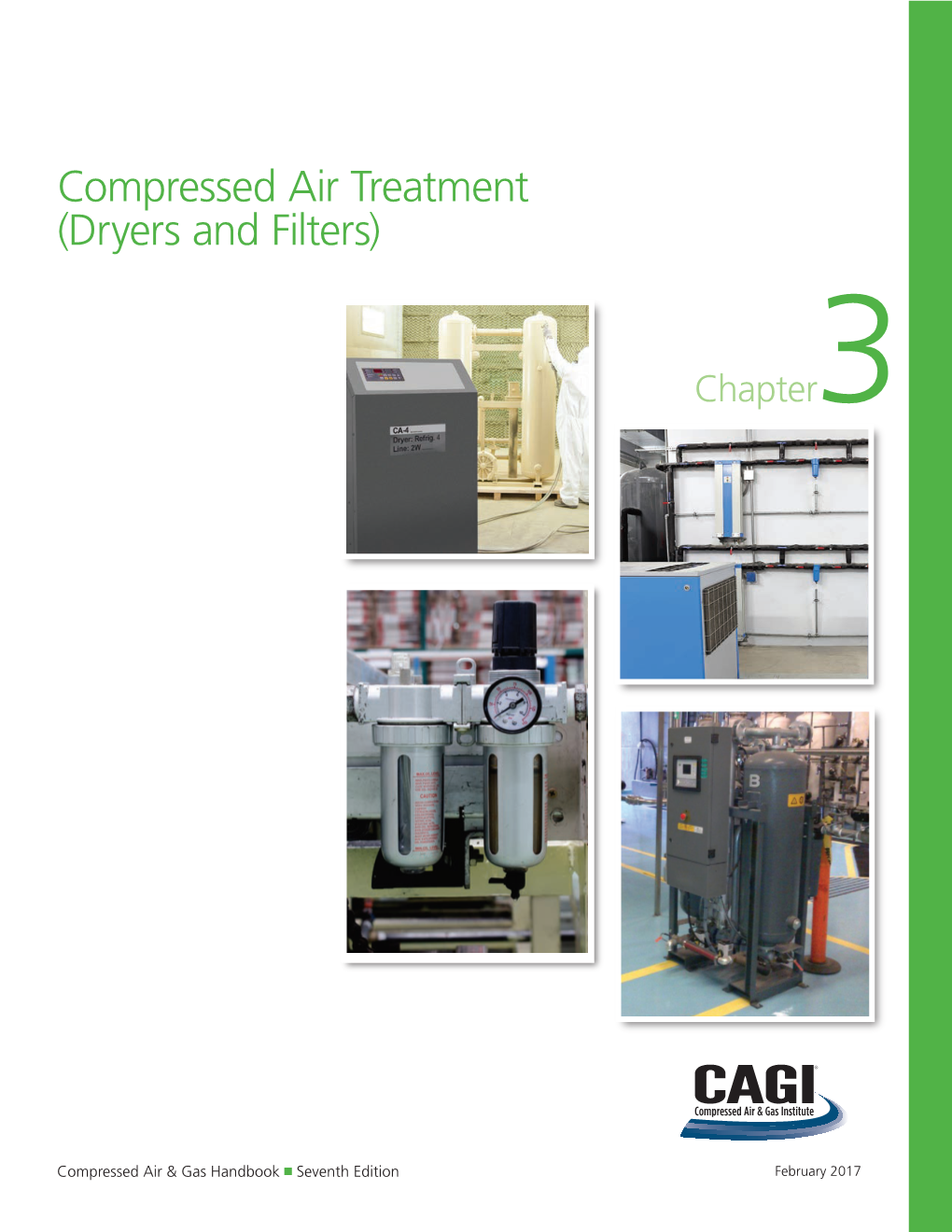
Load more
Recommended publications
-
9400, 9500 and 9600 Maximizer and Sidehill Combines
FILTER OVERVIEW WITH SERVICE INTERVALS AND CAPACITIES 9400, 9500 and 9600 Maximizer and Sidehill Combines ENGINE ENGINE PRIMARY AIR FILTER SECONDARY AIR FILTER (9400 Combine Serial Numbers -655288, (9400 Combine Serial Numbers -655288, 9500 Combine Serial Numbers -645200, 9500 Combine Serial Numbers -645200, 9600 Combine Serial Numbers -645300) – AR80652, 9600 Combine Serial Numbers -645300) – AR80653, AR81313 AR82915 SECONDARY AIR FILTER PRIMARY AIR FILTER (9400 Combine Serial Numbers 655289-, (9400 Combine Serial Numbers 655289-, 9500 Combine Serial Numbers 645201-665977, 9500 Combine Serial Numbers 645201-665977, 9600 Combine Serial Numbers 645301-666172) – AR70107 9600 Combine Serial Numbers 645301-666172) – SECONDARY AIR FILTER AR70106 (9500 Combine Serial Numbers 665978-, PRIMARY AIR FILTER 9600 Combine Serial Numbers 666173-) – AR95759 (9500 Combine Serial Numbers 665978-, Change only with primary filter. 9600 Combine Serial Numbers 666173-) – AR95758 Change annually and clean or change as required. ENGINE OIL FILTER (9500, 9600) – RE57394 OIL FILTER (9400) – T19044 For Engine 6359T Upto Combine Serial Numbers ( -640100) OIL FILTER (9400) – RE59754 CAB For Engine 6068HH050 From Combine Serial Numbers (701246 -) RECIRCULATION AIR FILTER (9400, 9500 AND 9600) – AH115836 OIL FILTER (9400) – AH128448 For Upto Combine Serial Numbers ( -650370) Clean or replace every 200 hours and as required. Replace every 250 hours or once a season, whichever occurs first. Fill crankcase with seasonal viscosity grade oil or Torq-Gard Supreme™ (250 hours change interval). Change oil every 500 hours when using John Deere Plus-50™ II engine oil and a John Deere filter Note: Change oil every 100 hours if fuel contain more than 0.5% sulfur. ENGINE CAB ENGINE FUEL WATER SEPARATOR FILTER AIR FILTER, STANDARD HYDRAULIC / HYDROSTATIC / FUEL FILTER (9500,9600) – AR86745 (9400, 9500 AND 9600) – AH115833 (9400, 9500 ANDT 9600) – AT81478 ENGINE GEARCASE FUEL FILTER (9400) – AR86745 AIR FILTER, FOR OPERATORS WITH ALLERGIES Replace every 500 hours and as required. -
Effects of Temperature and Relative Humidity on Filter Loading by Simulated Atmospheric Aerosols & COVID-19 Related Mask and Respirator Filtration Study
Effects of Temperature and Relative Humidity on Filter Loading by Simulated Atmospheric Aerosols & COVID-19 Related Mask and Respirator Filtration Study A DISSERTATION SUBMITTED TO THE FACULTY OF THE UNIVERSITY OF MINNESOTA BY Chenxing Pei IN PARTIAL FULFILLMENT OF THE REQUIREMENTS FOR THE DEGREE OF DOCTOR OF PHILOSOPHY Dr. David Y.H. Pui, Advisor August 2020 © Chenxing Pei 2020 Acknowledgments First and foremost, I am deeply indebted to my advisor, Professor David Y. H. Pui, for his continuous guidance, mentoring, and inspiration throughout my undergraduate and graduate studies. He provided me with the encouragement and freedom to work on any filtration related studies that interested me. His support, patience, and trust have made my years spent in the Particle Technology Laboratory an enjoyable, enriching, and memorable experience in my life. I would like to express my deepest appreciation to my committee members: Prof. Thomas Kuehn, Prof. David Kittelson, and Prof. Kevin Janni for reviewing my dissertation, offering insightful comments and suggestions, and serving on my Ph. D. exam committees. I am extremely grateful to my committee members not only for their time and extreme patience, but for their intellectual contributions to my development as a scientist. I would also like to thank Dr. Qisheng Ou, whose help cannot be overestimated. Dr. Ou provided me with the tools that I needed to choose the right direction and successfully complete my dissertation. Special thanks to Dr. Young H. Chung, who led to many interesting and motivating discussions. His help and advice were invaluable for my research and life. Thanks also to Weiqi Chen, who collaborated with me on the smart sensor project. -
Cabin Air Quality Brief
Briefing paper Cabin air quality – Risk of communicable diseases transmission The overall risk of contracting a disease from an ill person onboard an airplane is similar to that in other confined areas with high occupant density, such as a bus, a subway, or movie theatre for a similar time of exposure. anywhere where a person is in close contact with others. That said, the risk on airplanes is probably lower than in many confined spaces because modern airplanes have cabin air filtration systems equipped with HEPA filters. HEPA or high efficiency particulate air filters have similar performance to those used to keep the air clean in hospital operating rooms and industrial clean rooms. These filters are very effective at trapping microscopic particles as small as bacteria and viruses. HEPA filters are effective at capturing greater than 99 percent of the airborne microbes in the filtered air. Filtered, recirculated air provides higher cabin humidity levels and lower particulate levels than 100% outside air systems. The cabin air system is designed to operate most efficiently by delivering approximately 50 percent outside air and 50 percent filtered, recirculated air. This normally provides between 15 to 20 cubic feet of total air supply per minute per person in economy class. The total air supply is essentially sterile and particle-free. Cabin air circulation is continuous. Air is always flowing into and out of the cabin. Total airflow to the cabin is supplied at a bulk flow rate equivalent to 20 to 30 air changes per hour. This provides temperature control and minimizes temperature gradients within the cabin. -
Premium Wood Fireplaces
PREMIUM WOOD FIREPLACES ALL MODELS 2020 EPA CERTIFIED 1 Reimagine the (HEART)H of Your Home CATALYTIC TECHNOLOGY All Fireplace Xtrordinair™ wood fireplaces use state of the art catalytic technology. This allows our large capacity wood fire- places to produce highly efficient, clean fires in all burn settings. This bulletproof technology achieves roaring fires with super-long burn times and very high BTUs ranges, making it the perfect system for these powerhouse home heaters. CORD WOOD TESTING All of our wood fireplaces are 2020 EPA certified using the new EPA CORD WOOD protocol rather then the CRIB WOOD protocal that most other manufacturers test to. By testing with CORD WOOD you get a true real world measurement of how well the fireplace will burn and perform in your home. The 44 Elite™ is shown with the Classic Arch™ double door face. 2 CHAPTERS 1. Meet the Peak of Wood Fireplace Design Explore the 42 Apex™ & 42 Apex™ Clean Face Page 4 2. 42 Apex™ with Decorative Faces Page 6 3. Powerhouse Heaters, Elegant Style Elite™ Fireplaces are More than just a Name Page 10 4. 36 Elite™ Page 12 5. 44 Elite™ Page 14 6. Custom Shop Faces Page 18 8. How They Work 8. The 42 Apex™ Model 8. Page 20 8. The Elite™ Models Page 21 8. Framing 42 Apex™ Fireplace Framing Page 22 Elite™ Fireplace Framing Page 23 3 CHAPTER 1 __ Meet the Peak of Wood Fireplace Design Explore the 42 Apex™ The 42 Apex™ Wood Fireplace delivers natural convection heat efficiently throughout your home and offer a sleek, rectangular door and viewing area. -
HEPA Vs Electrostatic Getting Terms and Technologies Right Efficiency
HEPA vs Electrostatic Many articles try to compare HEPA and Electrostatic filtration. It seems that every article chooses one or the other rather than comparing the two. Sometimes HEPA is the clear choice for a filtration system. Other times an Electrostatic precipitator is a better fit for the air quality issues in a space. In this article we will try to present a clear comparison without bias. The only goal is to help you become a well-informed consumer. Getting terms and technologies right Before we get started let’s clarify our terms and technologies. Not all manufacturers use the right terms when describing the tecnologies. To more clearly understand our comparison, we will take a brief look at both technologies in the HEPA vs Electrostatic comparison. HEPA type and true HEPA Many air purifier manufacturers misuse the term HEPA. They refer to air filters that remove less than 99.97% of dust particles as a HEPA filter. While many of these HEPA type filters may do an adequate job, they should not be referred to as HEPA. When comparing a HEPA Air filter to an electrostatic air purifier, be sure the filter contained is true HEPA. Be certain that it is rated for 99.97% removal of dust particles 0.3 to 10 microns. Electrostatic precipitator and electrostatic media There it is a common misunderstanding that all Electrostatic filtration is the same. There are two basic types of Electrostatic filtration. One is electrostatically charged filter media, and the other is an Electrostatic precipitator. Electrostatic media is created by giving a normal filter an electrostatic charge. -
70 Series Four-Wheel Drive Tractors - 8570, 8770, 8870, 8970
FILTER OVERVIEW WITH SERVICE INTERVALS AND CAPACITIES 70 Series Four-Wheel Drive Tractors - 8570, 8770, 8870, 8970 ENGINE ENGINE CAB OIL FILTER FUEL FILTER RECIRCULATION AIR FILTERS DZ101880 (8570) AR86745 (8570, 8770, 8870) R112458 RE44647 (8770, 8870, 8970) RE160384 (8970) Replace annually or as required. Initial oil and filter change at 100 hours FUEL WATER SEPARATOR and then after every 250 hours. (IF EQUIPPED) Extend service interval by 50 hours RE508633 (8570, 8770, 8870) when using John Deere Torq-Gard Replace after every 500 hours Supreme Plus-50 engine oil and or as required. a John Deere oil filter. (Click here for capacity) CAB FRESH AIR FILTER RE24619 (STANDARD) RE67829 (HEAVY-DUTY) Replace annually or as required. ENGINE SECONDARY AIR FILTER AR70107 (8570) AR95759 (8770, 8870, 8970) Replace annually or as required. Do not clean. ENGINE PRIMARY AIR FILTER TRANSMISSION/HYDRAULIC AR70106 (8570) OIL FILTER RE38965 AR95758 (8770, 8870, 8970) ENGINE CLEAN-UP OIL FILTER AT112393 Replace annually, after six cleanings, Replace after every 250 hours, as required COOLANT FILTER or as indicated - Power Shift as required or as indicated. (IF EQUIPPED) Replace after every 750 hours, as required RE11992 (8770, 8870) or as indicated - 12 speed & 24 speed. RE42052 (8970) SCREEN Replace after every 1500 hours. RE35540 - POWER SHIFT (Click here for capacity) R53169 - 12 SPEED & 24 SPEED Clean after every 1500 hours. (Click here for capacity) December 2018. Subject to change without notice. https://www.deere.com/en_US/parts/parts_by_industry/ag/fmi/filter_maintenance_information.page CAPACITIES 70 Series Four-Wheel Drive Tractors - 8570, 8770, 8870, 8970 CAPACITIES (Approximate): Crankcase including Filter: Plus-50™ II Fuel Tank: 8570......................................................................... -
Air Filter Commercial Fibrous Air Filter Transparent Air Filter
ARTICLE Received 1 Sep 2014 | Accepted 6 Jan 2015 | Published 16 Feb 2015 DOI: 10.1038/ncomms7205 Transparent air filter for high-efficiency PM2.5 capture Chong Liu1,*, Po-Chun Hsu1,*, Hyun-Wook Lee1, Meng Ye2, Guangyuan Zheng3, Nian Liu4, Weiyang Li1 & Yi Cui1,5 Particulate matter (PM) pollution has raised serious concerns for public health. Although outdoor individual protection could be achieved by facial masks, indoor air usually relies on expensive and energy-intensive air-filtering devices. Here, we introduce a transparent air filter for indoor air protection through windows that uses natural passive ventilation to effectively protect the indoor air quality. By controlling the surface chemistry to enable strong PM adhesion and also the microstructure of the air filters to increase the capture possibilities, we achieve transparent, high air flow and highly effective air filters of B90% transparency with 495.00% removal of PM2.5 under extreme hazardous air-quality conditions (PM2.5 mass concentration 4250 mgmÀ 3). A field test in Beijing shows that the polyacrylonitrile trans- parent air filter has the best PM2.5 removal efficiency of 98.69% at high transmittance of B77% during haze occurrence. 1 Department of Materials Science and Engineering, Stanford University, Stanford, California 94305, USA. 2 Department of Civil and Environmental Engineering, Stanford University, Stanford, California 94305, USA. 3 Department of Chemical Engineering, Stanford University, Stanford, California 94305, USA. 4 Department of Chemistry, Stanford University, Stanford, California 94305, USA. 5 Stanford Institute for Materials and Energy Sciences, SLAC National Accelerator Laboratory, 2575 Sand Hill Road, Menlo Park, California 94025, USA. * These authors contributed equally to this work. -
Heat Transfer and Flow Characteristics of Condensing Refrigerants in Small-Channel Cross-Flow Heat Exchangers
Heat Transfer and Flow Characteristics of Condensing Refrigerants in Small-Channel Cross-Flow Heat Exchangers D. C. Zietlow and C. O. Pedersen ACRC TR-73 April 1995 For additional information: Air Conditioning and Refrigeration Center University of Illinois Mechanical & Industrial Engineering Dept. 1206 West Green Street Urbana, IL 61801 Prepared as part ofACRC Project 03 Condenser Performance (217) 333-3115 C. O. Pedersen, Principal Investigator The Air Conditioning and Refrigeration Center was founded in 1988 with a grant from the estate ofRichard W. Kritzer, the founder ofPeerless of America Inc. A State of Illinois Technology Challenge Grant helped build the laboratory facilities. The ACRC receives continuing supportfrom the Richard W. Kritzer Endowment and the National Science Foundation. The following organizations have also become sponsors of the Center. Acustar Division of Chrysler Amana Refrigeration, Inc. Brazeway, Inc. Carrier Corporation Caterpillar, Inc. Delphi Harrison Thermal Systems E. I. du Pont de Nemours & Co. Eaton Corporation Electric Power Research Institute Ford Motor Company Frigidaire Company General Electric Company Lennox International, Inc. Modine Manufacturing Co. Peerless of America, Inc. U. S. Army CERL U. S. Environmental Protection Agency Whirlpool Corporation For additional iriformation: Air Conditioning & Refrigeration Center Mechanical & Industrial Engineering Dept. University ofIllinois 1206 West Green Street Urbana IL 61801 2173333115 ABSTRACT This study is the first to model and experimentally validate refrigerant inventory of R134a in small-channel cross-flow condenserst. This heat exchanger is used in automotive applications and uses smaller internal volumes than conventional heat exchangers to perform the same task. Since the cost of refrigerants continues to rise due to the phase out of chlorofluorocarbons (CFCs), internal volume becomes a key design parameter. -
An Air Filter Sensor for Heating and Air Conditioning Units
3648 AN AIR-FILTER SENSOR FOR HOME-USED AIR CONDITIONERS Cheng Y. Lin, Gary R. Crossman, Alok K. Verma Department of Engineering Technology Old Dominion University Norfolk, Virginia Abstract This paper presents a successful senior project of instrumentation developed in a Mechanical Engineering Technology senior capstone course. Students were encouraged to approach the problem of designing an air-filter sensor and to propose an optimum and practical solution for the problem. Work includes conceptual design and analysis, implementation, tests and modifications. When an air filter is used in a home air conditioner, inhabitants often forget when to replace it until the cooling or heating capacity is obviously reduced. If the filter remains in service, the efficiency of the cooling/heating system will continue decreasing while the electricity bill will significantly increase. In some worst cases, the air quality will also be affected. This paper presents an idea of designing and fabricating an air-filter sensor to alleviate this problem. The sensor will send a warning signal when the filter collects a specific amount of dust in the air filter. It can be easily installed and only consumes a negligible amount of electricity. A photo sensor with an infrared LED emitter and receiver is used in this design. As the infrared LED can transmit through most of the home-used air filter to its receiver, a signal will be sent out when a specified amount of dust is collected in the filter and the light is blocked from the emitter to the receiver. The emitter and receiver are mounted on a simple fixture and can be easily fitted on an air filter. -
The Ultimate Air Cleaning Machine Erik Air Purifier User Guide
To Buy: Contact Sylvane at 800-934-9194 or visit www.sylvane.com For Product Support: Contact Oransi at 888.281.3948 The Ultimate Air Cleaning Machine Erik Air Purifier User Guide Made in USA Safety Precautions. READ ALL INSTRUCTIONS BEFORE USING THIS APPLIANCE. TO REDUCE THE RISK OF FIRE, ELECTRIC SHOCK, OR INJURY: 1. Do not attempt to service the air purifier in any way other than to replace or clean the air filter. 2. This product operates at 120V AC, 60Hz only. 3. Always unplug the power cord from the electrical outlet when the air purifier is not in use or when changing the filter. 4. Never run the air purifier unless it is fully assembled. 5. Do not alter the plug in any way. 6. Always turn off the air purifier before unplugging the air purifier from outlet. 7. Do not place the cord near a heated surface. 8. Never operate the air purifier if the plug or cord is damaged or appears damaged. Only qualified service personnel should ever replace or attempt to replace a damaged power cord. 9. Never use the power cord to pick up, carry, drag, pull, or lift the air purifier. Do not pull the cord against or around sharp corners and edges. 10. Always remove the plug from its power outlet by holding onto the plug itself and pulling gently. 11. Use care when operating the air purifier by keeping all foreign objects, fingers, body parts, hair, loose clothing, jewelry, etc away from openings. 12. Do not drop items into the air purifier. -
Impact on of Air-Filter Condition HVAC Equipment
ORNL/TM-9894 Impact of Air-Filter Condition on HVAC Equipment L. Jung 1 ORNL/TM-9894 Engineering Technology Division IMPACT OF AIR-FILTER CONDITION ON HVAC EQUIPMENT L. Jung Date Published - September 1987 Prepared for the U.S. ARMY FACILITIES ENGINEERING SUPPORTAGENCY Fort Belvoir,, Virginia 22060 ARMY CONSERVATIONEQUIPMENT TESTING PROGRAM TASK ORDER/WORKDIRECTIVE NO. 0003 Prepared by the OAK RIDGE NATIONAL LABORATORY Oak Ridge, Tennessee 37831 operated by MARTIN MARIETTA ENERGY SYSTEMS, INC. for the , U.S. DEPARTMENTOF ENERGY under Contract No. DE-AC05-840R21400 iii CONTENTS Page EXECUTIVE SUMMARY ................................................ V ABSTRACT ......................................................... 1 1. INTRODUCTION ................................................. 1 1.1 Purpose ................................................. 1 . 1.2 Scope ................................................... 1 1.3 Background and Methodology .............................. 2 2. AIR-FILTER PURPOSE, TESTING, TYPES, AND SELECTION ............ 4 2.1 Air-Filter Purpose ...................................... 4 2.2 Air-Filter Testing ...................................... 4 2.3 Filter Types ............................................ 5 2.4 Air-Filter Selection .................................... 9 3. FUNDAMENTALSOF HVAC SYSTEMS ................................. 10 3.1 Refrigeration Cycle ..................................... 10 3.2 Other Cooling Systems ................................... 11 3.3 Heat Pump .............................................. -
Guide to Buying a HEPA Air Purifier
What to Consider When Buying a HEPA Air Purifier What is a HEPA Air Filtration Unit? True High Efficiency Particulate Air (HEPA) filtration units are designed to capture at least 99.97 percent of fine airborne particles larger than at least 0.3 micrometer (0.00001 inch) as specified by the United States Department of Energy. Ultra-fine particles are things like dust, pollen, mold, asbestos, and hazardous pollutants in wildfire smoke. The fine particles are the most common and dangerous components of wildfire smoke. HEPA filtration units are generally equipped with replaceable pre‐filters that also remove larger particulate matter, such as pollen and dust. Filtration units range in size from small portable units up to central heating and cooling systems for entire buildings. Effectiveness depends largely upon how much filtered air they deliver over a given period into a specified space. Why Use a HEPA Filter? Indoor air pollution comes from a combination of particulate matter including dust, mold, pet dander and particles from smoke and cooking stoves. Particulate matter may also include pollutants from vehicle exhaust, smoke, and chemical fumes and can be far worse than the pollution outside. Using a quality HEPA filter can help trap these pollutants and create a cleaner indoor environment. If you or someone in your family suffers from asthma or severe allergies, using a HEPA air purifier can significantly improve your quality of life inside your home. How to Use a HEPA Air Purifier To use an air purifier follow these steps: 1. Allow it to run 24 hours a day 2.