Problems in High-Shock Measurement
Total Page:16
File Type:pdf, Size:1020Kb
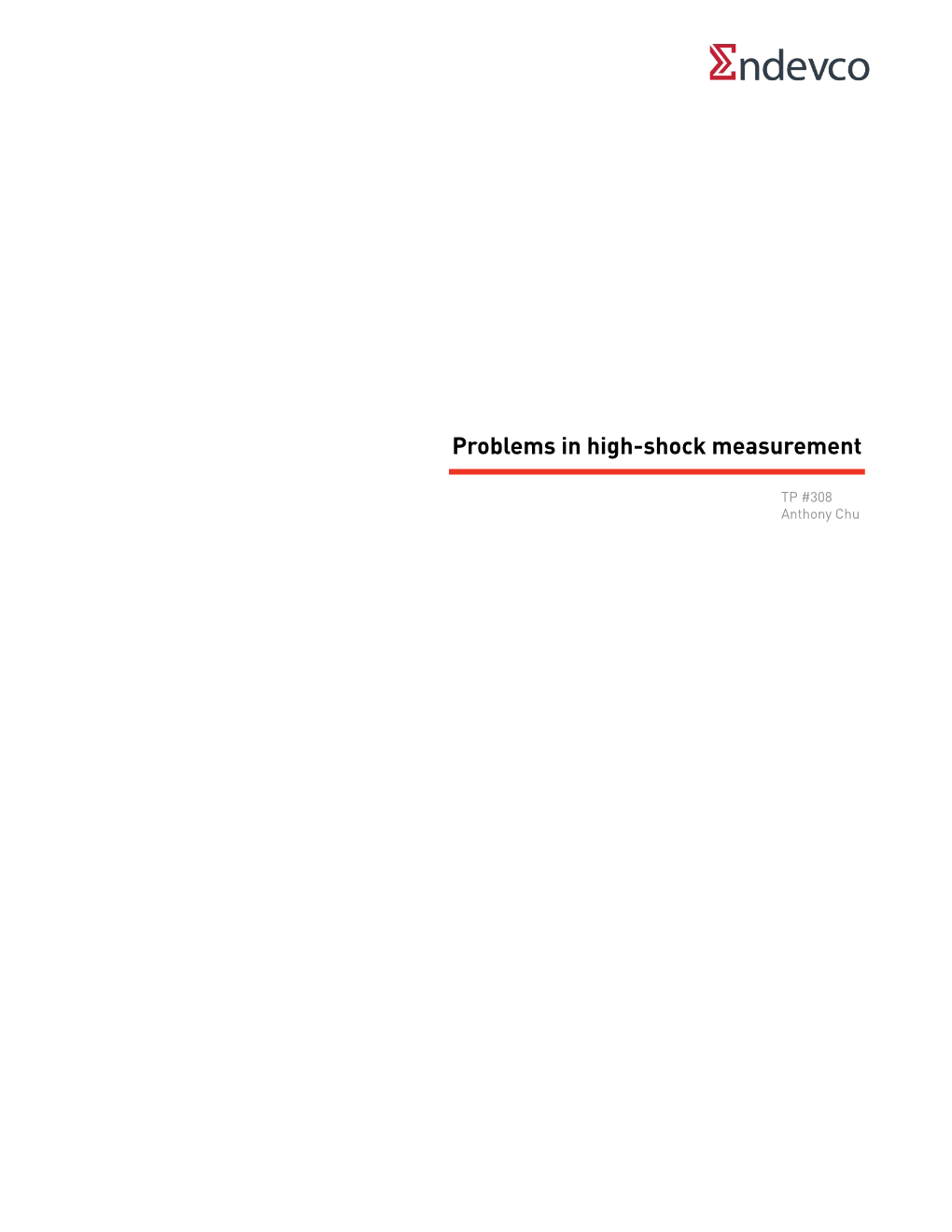
Load more
Recommended publications
-
SSB-Filters (PART 4)
--------- ELECTRONICS --------------------- SSB-FilterS (PART 4) ELECTRONICS This is the fourth article of a tivity and stability characteristics, with mtmaturization of equipment. This is the fourth article of a series from a training course written but their large size makes them Also to the advantage of the me series from a training course written by Collins Radio Company for per subject to shock or vibration de· chanical filter is a Q in the order by Collins Radio Company for per- sonnel concerned with single side terioration. Also, their cost is of 10,000 which is about 100 times sonnel concerned with single side- band communications. quite high. the Q obtainable with electrical band communications. Both SSB transmitters and SSB Newer crystal filters are being elements. Both SSB transmitters and SSB developed that have extended fre receivers require very selective receivers require very selective Although the commercial use of bandpass filters in the region of bandpass filters in the region of quency range and are smaller. These mechanical filters is relatively 100 to 500 kilocycles. 100 to 500 kilocycles. newer crystal filters are more ac new, the basic principles on which In receivers, a high order of ad- In receivers, a high order of ad ceptable for use in SSB equipment. they are based is well established. jacent channel rejection is required jacent channel rejection is required LC Filters The mechanical filter is a me if channels are to be closely spaced if channels are to be closely spaced LC filters have been used at IF chanically resonant device that re to conserve spectrum space. -
Mechanical Engineering 310 Documentation 2018-2019
P a g e | 1 X Y L E M MECHANICAL ENGINEERING 310 DOCUMENTATION 2018-2019 Mechanical Engineering Design Group 416 Escondido Mall Stanford University Stanford, CA 94305- 2203 http://me310.stanford.edu Team Xylem: Adit Desai Fay Nicole Colah Okkeun Lee Tin Jing jie Dai Jiang Mika Julin Nina Saarikoski Samuel Moy Timo Moyer 1 Executive Summary This report summarizes the work completed by the Stanford University (SU) and Aalto University (AU) Teams during the 2018-19 Academic Year for ME310 with our corporate sponsor Xylem Inc. In Autumn Quarter 2018, the SU team explored the concept of a modified drip irrigation system designed to reduce the amount of water lost due to evaporation during irrigation, and an oyster based water filtration system which aimed to replicate the mucus in oysters to trap contaminants to purify water. In Winter Quarter 2019, the SU team explored the concept of a human powered personal and floor-based filtration system, which achieved flow rates of up to 80 times faster as compared to gravity fed methods. In Spring Quarter 2019 after the Winter Break in Aalto University, the SU and AU teams converged on a final product design concept and user, which was a low cost, modular and highly maintainable water filtration system which could remove heavy metals, pathogens and sediments from contaminated waters. The filtration system was designed such that clean drinking water could be provided to rural children in developing countries who did not have access to an electrical supply. A key nature-inspired filtration technology of this system was the usage of microalgae (Chlorella Vulgaris) for batch removal of heavy metals, where literature research reported that small quantities of such algae are able to remove significant quantities (~88%) of heavy metals from contaminated waters within 30 minutes. -
Note on Mechanical Filtration and Gravitation Filtration (Paper & Discussion)
69 Victorian Institute of Engineers. A FEW NOTES ON MECHANICAL FILTRATION IN CONNECTION WITH WATER SUPPLIES. Read by MR. GEORGE SWINBURNE, 7M August, 1901. In this short paper I make no pretence at originality, but with a view to initiating discussion, will endeavour to give the result of a few enquiries on this important matter in which I have taken a little interest. The system adopted in older countries of filtering through sand beds is not adaptable to Australian conditions in the great majority of cases; yet there is no doubt that something must be done in the near future to better the condition of water supply in the smaller towns of Australia. In the large centres of population, where watershed areas are preserved, a good state of things _ mày exist, but in the country districts, the only available supplies are from doubtful springs, lather stagnant rivers which have already been polluted further up, or dams open to dust storms and all kinds of impurities, which are only filled when it rains in the immediate neighbourhood. It is rarely that the people themselves take much interest in the question, except to grumble when things are very bad. To engineers and sanitary authorities it is one of the most important questions in our modern life. Pure water means good health, but half the population of this continent is content to put up with Typhoid and the ills attending a supply of bad water, rather than help or pay to have the supply placed on the best possible footing. In my opinion this state of things exists on account of the supplies being in the hands of the local authorities or trusts, and the members not realising the importance of the matter. -
Inf 5490 Rf Mems
INF 5490 RF MEMS LN10: Micromechanical filters Spring 2011, Oddvar Søråsen Jan Erik Ramstad Department of Informatics, UoO 1 Today’s lecture • Properties of mechanical filters • Visualization and working principle • Modeling • Examples • Design procedure • Mixer 2 Mechanical filters • Well-known for several decades – Jmfr. book: ”Mechanical filters in electronics”, R.A. Johnson, 1983 • Miniaturization of mechanical filters makes it more interesting to use – Possible by using micromachining – Motivation Fabrication of small integrated filters: ”system-on-chip” with good filter performance 3 Filter response 4 Several resonators used • One silingle resonathtor has a narrow BP- response – Good for d e fini ng oscill a tor frequency – Not good for BP-filter • BP-filters are implemented by coupling resonators in cascade – Gives a wider pass band than using one single resonating structure – 2 or more micro resonators are used • Each of comb type or c-c beam type (or other types) – Connected by soft springs 5 Filter order • NbNumber o f resonators, n, defines the filter order – Order = 2 * n – Sharper ”roll-off” to stop band when several resonators are used • ”sharper filter” 6 Micromachined filter properties • + CtCompact ilimplemen ttitation – ”on-chip” filter bank possible • + Hig h Q -ftfactor can bbidbe obtained • + Low-loss BP-filters can be implemented – The individual resonators have low loss – Low total ”Insertion loss, IL” • IL: Degraded for small bandwidth • IL: Improved for high Q-factor 7 ”Insertion loss ” IL: Degraded for small -
ETD Template
DESIGN ISSUES IN ELECTROMECHANICAL FILTERS WITH PIEZOELECTRIC TRANSDUCERS by Michael P. Dmuchoski B.S. in M.E., University of Pittsburgh, 2000 Submitted to the Graduate Faculty of School of Engineering in partial fulfillment of the requirements for the degree of Master of Science University of Pittsburgh 2002 UNIVERSITY OF PITTSBURGH SCHOOL OF ENGINEERING This thesis was presented by Michael P. Dmuchoski It was defended on December 11, 2002 and approved by Dr. Jeffrey S. Vipperman, Professor, Mechanical Engineering Department Dr. Marlin H. Mickle, Professor, Electrical Engineering Department Dr. William W. Clark, Professor, Mechanical Engineering Department Thesis Advisor ii ________ ABSTRACT DESIGN ISSUES IN ELECTROMECHANICAL FILTERS WITH PIEZOELECTRIC TRANSDUCERS Michael P. Dmuchoski, MS University of Pittsburgh, 2002 The concept of filtering analog signals was first introduced almost one hundred years ago, and has seen tremendous development since then. The majority of filters consist of electrical circuits, which is practical since the signals themselves are usually electrical, although there has been a great deal of interest in electromechanical filters. Electromechanical filters consist of transducers that convert the electrical signal to mechanical motion, which is then passed through a vibrating mechanical system, and then transduced back into electrical energy at the output. In either type of filter, electrical or electromechanical, the key component is the resonator. This is a two-degree-of-freedom system whose transient response oscillates at its natural frequency. In electrical filters, resonators are typically inductor-capacitor pairs, while in mechanical filters they are spring-mass systems. By coupling the resonators correctly, the desired filter type (such as bandpass, band-reject, etc.) or specific filter characteristics (e.g. -
Design and Simulation of an IF MEMS Filter Based on Face Shear Mode Square Resonator
International Journal of Smart Grid and Clean Energy Design and Simulation of an IF MEMS Filter Based on Face Shear Mode Square Resonator Junwen Jiang, Jingfu Bao*, Yijia Du School of Electronic Engineering, University of Electronic Science and Technology of China, Chengdu 611731, China Abstract Intermediate frequency (IF) Filters with IC (Integrated circuit) compatibility, narrow bandwidth and large stop band rejection are in need for wireless communications. This paper presents the design and simulation of a 70 MHz IF Micro-electro-mechanical filter using two identical face shear mode square resonators. By carefully designing the supporting structure of the resonators, a quality factor above 100,000 is achieved in the best designed resonator. With these face shear mode square resonators, three filters are designed and the simulated transmission response shows that these filters can obtain unterminated transmission passbands of about 25 kHz to 35 kHz with the centre frequency of 70 MHz, which represents a 0.036% to 0.05% bandwidth. This ultra narrow bandwidth IF bandpass filter can be an attractive candidate for wireless receivers. Keywords: Micro-electro-mechanical system, intermediate frequency filters, square resonator 1. Introduction With the advantage of low power consumption, exceptionally high quality factor, and Integrated circuit (IC) compatibility, MEMS (Micro-electro-mechanical system) resonator and filters have become attractive as frequency generation and selection components for wireless communication systems. Typically for front end transceiver, there exist a number of high-Q off-chip components that limit the development of system on chip (SOC), however, these components are replaceable by MEMS structures and devices. MEMS resonators can be served to construct MEMS oscillators as well as high-Q ultra narrow bandwidth filters, which are attractive in wireless front end receiver to achieve better signal selection. -
UC Berkeley UC Berkeley Electronic Theses and Dissertations
UC Berkeley UC Berkeley Electronic Theses and Dissertations Title Frequency Tunable MEMS-Based Timing Oscillators and Narrowband Filters Permalink https://escholarship.org/uc/item/3mq7068h Author Barrow, Henry Galahad Publication Date 2015 Peer reviewed|Thesis/dissertation eScholarship.org Powered by the California Digital Library University of California Frequency Tunable MEMS-Based Timing Oscillators and Narrowband Filters By Henry Galahad Barrow A dissertation submitted in partial satisfaction of the requirements for the degree of Doctor of Philosophy in Engineering - Electrical Engineering and Computer Sciences in the Graduate Division of the University of California, Berkeley Committee in charge: Professor Clark T.-C. Nguyen, Chair Professor Kristofer Pister Professor Liwei Lin Fall 2015 © Copyright 2015 Henry Galahad Barrow All rights reserved Abstract Frequency Tunable MEMS-Based Timing Oscillators and Narrowband Filters By Henry Galahad Barrow Doctor of Philosophy in Electrical Engineering and Computer Sciences University of California, Berkeley Professor Clark T.-C. Nguyen, Chair There is little question that the commercial success of smartphones has substantially increased the volume of products utilizing Micro Electro Mechanical Systems (MEMS) technology, especially accelerometers, gyroscopes, bandpass filters, and microphones. The Internet of Things (IoT), a more recent driver for small, low power microsystems, seems poised to provide an even bigger market for these and other potential products based on MEMS. Given that the IoT will likely depend heavily on massive sensor networks using nodes for which battery replacement might not be practical, cost and power consumption become even more important. As already known for existing sensor networks, sleep/wake cycles will likely be instrumental to maintaining low sensor node power consumption in the IoT, and if so, then the clocks that must continuously run to synchronize sleep/wake events often become the bottlenecks to ultimate power consumption. -
Frequency Tunable MEMS-Based Timing Oscillators and Narrowband Filters
Frequency Tunable MEMS-Based Timing Oscillators and Narrowband Filters Henry Barrow Electrical Engineering and Computer Sciences University of California at Berkeley Technical Report No. UCB/EECS-2015-255 http://www.eecs.berkeley.edu/Pubs/TechRpts/2015/EECS-2015-255.html December 18, 2015 Copyright © 2015, by the author(s). All rights reserved. Permission to make digital or hard copies of all or part of this work for personal or classroom use is granted without fee provided that copies are not made or distributed for profit or commercial advantage and that copies bear this notice and the full citation on the first page. To copy otherwise, to republish, to post on servers or to redistribute to lists, requires prior specific permission. Frequency Tunable MEMS-Based Timing Oscillators and Narrowband Filters By Henry Galahad Barrow A dissertation submitted in partial satisfaction of the requirements for the degree of Doctor of Philosophy in Engineering - Electrical Engineering and Computer Sciences in the Graduate Division of the University of California, Berkeley Committee in charge: Professor Clark T.-C. Nguyen, Chair Professor Kristofer Pister Professor Liwei Lin Fall 2015 © Copyright 2015 Henry Galahad Barrow All rights reserved Abstract Frequency Tunable MEMS-Based Timing Oscillators and Narrowband Filters By Henry Galahad Barrow Doctor of Philosophy in Electrical Engineering and Computer Sciences University of California, Berkeley Professor Clark T.-C. Nguyen, Chair There is little question that the commercial success of smartphones has substantially increased the volume of products utilizing Micro Electro Mechanical Systems (MEMS) technology, especially accelerometers, gyroscopes, bandpass filters, and microphones. The Internet of Things (IoT), a more recent driver for small, low power microsystems, seems poised to provide an even bigger market for these and other potential products based on MEMS. -
Glossary of Terms and Acronyms for Vacuum Coating Technology
Society of Vacuum Coaters Glossary of Terms and Acronyms for Vacuum Coating Technology Abridged with permission from The Foundations of Vacuum Coating Technology by Donald M. Mattox Noyes Publications/William Andrew Publishing (2003) ISBN 0-8155-1495-6 2 Society of Vacuum Coaters Glossary of Terms A Applied bias (PVD technology) An electrical potential applied from an external source. See Bias. Abnormal glow discharge (plasma) The DC glow discharge where Arc A high-current, low-voltage electrical discharge between two the cathode spot covers the whole cathode and an increase in the electrodes or between areas at different potentials. See Arc source. voltage increases the cathode current density. This is the type of Arc, gaseous An arc formed in a chamber containing enough gas- glow discharge used in most plasma processing. See Normal glow eous species to aid in establishing and maintaining an electrical discharge. arc. See Arc, vacuum. Abrasion test (characterization) Testing film adhesion and abrasion Arc, vacuum An arc formed in a vacuum such that all of the ionized resistance by rubbing, impacting or sliding in contact with another species originate from the arc electrodes. See Arc, gaseous. surface or surfaces. Examples: Tumble test, Tabor test, Eraser test. Arc suppression Techniques for quenching an arc before it becomes too destructive. These include: shutting-off the power or introduc- Abrasive cleaning The removal of surface material (gross clean- ing a voltage pulse with an opposite polarity. ing), including contamination, by an abrasive action. Arc vapor deposition (Physical vapor deposition, vacuum deposition Abrupt-type interface (film formation) The interface that is formed processes) Film deposition process where the source of vapor is between two materials (A and B) when there is no diffusion or chemi- from arc vaporization. -
Single-Sideband Filters [Ham-Radio 1968-08 8P]
single-sideband filters In a single-sideband transmitter, the signal I coming from the balanced modulator is not 0 m yet an ssb signal; it still has both sidebands. Although the carrier has been suppressed, it is a0 A called a double-sideband suppressed-carrier The filters required ; signal. The job of removing the unwanted -w Z sideband is left to a device known simply for generating a ssb signal g as a filter. In a communications receiver, incoming r; signals must be sorted out by the tuned cir- fall into .- cuits of the rf and i-f sections. These coil- -0 P. capacitor combinations may allow adjacent two general categories, signals through almost as well as the desired V10 ones; their response is too broad. Removing crystal and mechanical; g those unwanted "side" frequencies is the job of a filter. 2 4 In a single-sideband receiver, every con- here is a. version the signal goes through generates an 3 unnecessary extra sideband because of the m a description of both nature of the heterodyning process. To re- 7- cover the modulation, the ssb detector needs only the original sideband. The job of elimi- nating the unwanted sideband is turned over to-you guessed it-a filter. On the schematic diagram of a modern ham receiver or transmitter, the filter is 40 august 1968 identified merely by a box labeled F1, F2 or 60-dB point. The ratio between the two FLI, FL2, etc. The filter circuit is almost never bandwidths is called the shape factor. The shown. Nor is the type of filter indicated. -
Mechanical Filters-A Review of Progress
IEEE TRANSACTIONS ON SONICS AXD ULTRASONICS, VOL. SU-18, NO. 3, JULY 1971 155 Mechanical Filters-A Review of Progress ROBERTA. JOHNSON, MEMBER, IEEE, MANFRED BORNER, AKD MASASIII KONKO, MEMBER, IEEE - Abstract-This paper isareview of electromechanicalbandpass 0 filter, resonator, and transducer development. Filter typesdiscussed include intermediate and low-frequency configurations composed of rod, disk,and flexure-barresonators and magnetostrictive ferrite g and piezoelectricceramic transducers. The resonators and trans- ducers areanalyzed in terms of theirdynamic and material char- 2 2o acteristics. The paper also includes methods of realizing attenuation 2 poles at real and complex frequencies. The last section is a look at future developments. future 30 1 I II l I I 1 IXTRODUCTIOX 100 2W 300 500 1 OW 2000 30W 5ooo FREGUENCY (Hz1 ORE THAN 20 years haw passed since the first Fig. 1. Improvementin phonograph design through the use of practical mechanical filters were introduced by filter design metl~ods[61. Adler [l],Roberts [2], andDoelz [3]. These fibers met an existing need for greater selectivity in the IF stages of AM and SSB receiversdesigned for voice n m / FLEXURE (F" communication. Rlodern receivers and telephone commu- nication equipments carry not only voice but data mes- sages as well, thus requiring lower passband ripple and well-definedand stable passband limits. In addition, greaterselectivity and lon.er loss areoften required. Mcchanic:~l filter development has kept pace with the demands of communicationengineers. For instance, filtershaving passband-~,ipple requirements of 0.5 dB or less or 60/3-dB bandwidthratios of 1.3/1 arenot unusual. Package size has also heen reduced; a 10-pole filter can be designed into a l-c1n3 package. -
Water Level and Wave Height Estimates at NOAA Tide Stations from Acoustic and Microwave Sensors
NOAA Technical Report NOS CO-OPS 075 Water Level and Wave Height Estimates at NOAA Tide Stations from Acoustic and Microwave Sensors Microwave water level sensors at La Jolla California. Silver Spring, Maryland June 2014 noaa National Oceanic and Atmospheric Administration U.S. DEPARTMENT OF COMMERCE National Ocean Service Center for Operational Oceanographic Products and Services Center for Operational Oceanographic Products and Services National Ocean Service National Oceanic and Atmospheric Administration U.S. Department of Commerce The National Ocean Service (NOS) Center for Operational Oceanographic Products and Services (CO-OPS) provides the National infrastructure, science, and technical expertise to collect and distribute observations and predictions of water levels and currents to ensure safe, efficient and environmentally sound maritime commerce. The Center provides the set of water level and tidal current products required to support NOS’ Strategic Plan mission requirements, and to assist in providing operational oceanographic data/products required by NOAA’s other Strategic Plan themes. For example, CO-OPS provides data and products required by the National Weather Service to meet its flood and tsunami warning responsibilities. The Center manages the National Water Level Observation Network (NWLON), a national network of Physical Oceanographic Real-Time Systems (PORTS®) in major U. S. harbors, and the National Current Observation Program consisting of current surveys in near shore and coastal areas utilizing bottom mounted