Mechanical Diode Based Ultrasonic Atomic Force Microscopy
Total Page:16
File Type:pdf, Size:1020Kb
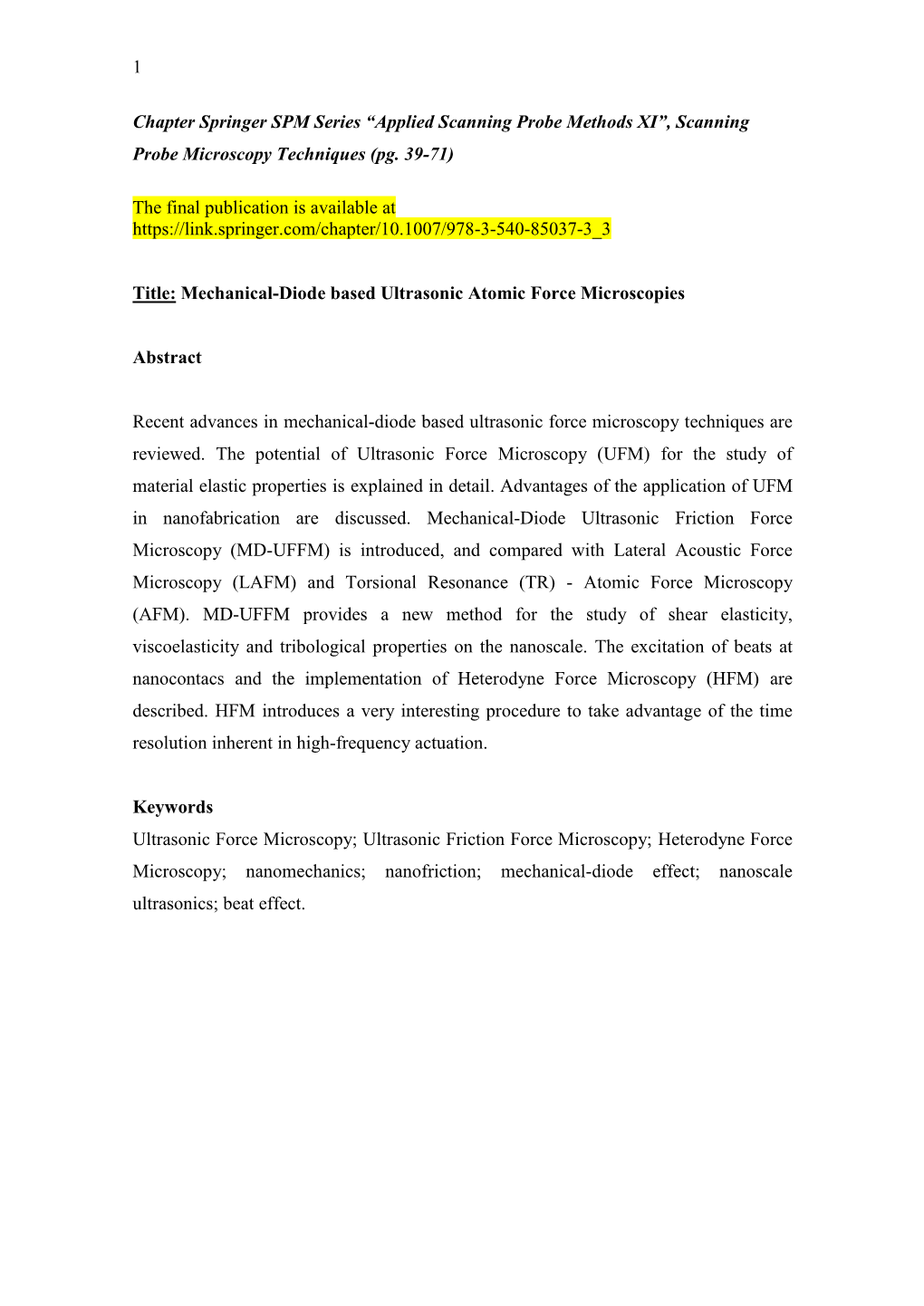
Load more
Recommended publications
-
60 Ghz Wireless Link Implementing an Electronic Mixer Driven by a Photonically Integrated Uni- Traveling Carrier Photodiode at the Receiver
60 GHz Wireless Link Implementing an Electronic Mixer Driven by a Photonically Integrated Uni- Traveling Carrier Photodiode at the Receiver Ahmad W. Mohammad1, Katarzyna Balakier1, Haymen Shams1, Frédéric van Dijk2, Chin-Pang Liu1, Chris Graham1, Michele Natrella1, Xiaoli Lin1, Alwyn J. Seeds1, and Cyril C. Renaud1 1Department of Electronic and Electrical Engineering, University College London, Torrington Place, London, WC1E 7JE, UK 2III-V Lab, a joint Laboratory of "Nokia Bell Labs", "Thales Research & Technology" and "CEA-LETI", Palaiseau, France Abstract— We report the first 60 GHz wireless link emitted power and the large bandwidth [7]. However, the UTC- implementing a uni-traveling carrier photodiode (UTC-PD) at PD exhibits a poor performance as an optoelectronic mixer the transmitter and a photonic integrated chip incorporating a because of its significant frequency conversion loss; a UTC-PD at the receiver. In this demonstration, a 64.5 GHz signal conversion loss of 32 dB at 100 GHz has been demonstrated carrying 1 Gbps on-off keying (OOK) data was generated by using this type of photodiode [8]. On the other hand, Schottky- heterodyning two optical tones into the transmitter UTC-PD. The based electronic mixers have demonstrated less than 5 dB signal was transmitted using a 24 dBi gain parabolic antenna conversion loss at 180 GHz [9]. However, a Schottky-based over a wireless distance of three metres before reaching an mixer requires a high frequency electronic local oscillator identical receiver antenna. At the receiver, an electronic mixer (LO), which can be expensive and may restrict frequency was used to down-convert the received signal into an agility of the receiver, while a UTC-PD mixer is widely intermediate frequency of 12.5 GHz. -
Remote, Displacement Measurement Using A
REMOTE, DISPLACEMENT MEASUREMENT USING A MODULATED LASER SYSTEM by G. M. S. JOYNES A thesis submitted for the Degree of Doctor of Philosophy at the University of Surrey August 1973 ProQuest Number: 10800195 All rights reserved INFORMATION TO ALL USERS The quality of this reproduction is dependent upon the quality of the copy submitted. In the unlikely event that the author did not send a com plete manuscript and there are missing pages, these will be noted. Also, if material had to be removed, a note will indicate the deletion. uest ProQuest 10800195 Published by ProQuest LLC(2018). Copyright of the Dissertation is held by the Author. All rights reserved. This work is protected against unauthorized copying under Title 17, United States C ode Microform Edition © ProQuest LLC. ProQuest LLC. 789 East Eisenhower Parkway P.O. Box 1346 Ann Arbor, Ml 48106- 1346 ABSTRACT A study has been made of the principles involved in displacement measurement using optical methods, with particular emphasis on intensity - modulated laser beam techniques. Some of the compromises in performance possible in differing situations are discussed. Previous research has dealt with an approach using coherent optical interference. The two methods are compared theoretically, and it is shown that certain advantages are possessed by the Modulated Beam technique. An important component in the system discussed is the Intensity Modulator. Methods of electro-optic modulation have been studied, and a modulator using Lithium. Niobate has been designed and built. It requires low modulation voltages, operates in the v.h.f. region, and has the important advantage over similar modulators in that it is completely insensitive to temperature. -
Current Times Ent Times
Bhilai Institute of Technology, Durg CURRENT TIMES Power of Technology The In-house Quarterly News letter of Electrical Engineering Department Chief Patron July 2017 Sh. I.P.Mishra Patron Vision Mission Dr Arun Arora Advisor To create intellectually stimulating environment To contribute to the nation, by for learning, research and promotion of Advisory Board delivering quality education and professional and ethical values, to develop a creating globally competent sense of responsibility, discipline and interest Dr (Mrs) A.P.Huddar professionals to serve the industry amongst students in various activities leading to Dr (Mrs ) S.Ray and society. the welfare of the industry and society at large Dr S.P.Shukla and to empower the students through lifelong Dr S.K.Sahu learning for self up-gradation and societal Dr (Mrs) A. Gupta upliftment. Dr (Mrs) S.Tripathi Dr G.C.Biswal Prof. Uma P. Balaraju Program Educational Objectives (PEOs) Prof.Gourav Sharma PEO-1 To impart sound foundation in Mathematics, Applied Science and Engineering Prof. Alok Kumar to the graduates, which enables them to formulate, solve and analyze the problems in Prof. J.Panigrahi Electrical Engineering. Prof. Shraddha PEO-2 To develop analyzing skill amongst graduates for technical interpretation, Kaushik designing and implementation of ideas. Prof. G.Shankar PEO-3 To promote students for taking up new responsibilities and challenges in Prof. Jyotsana Kaiwart multidisciplinary projects. Editor Dr N.Tripathi Editorial Dear Readers, Student Editor Nitish Patel Warm welcome to new edition of “Current Times”. India has taken steps towards goods Akanksha Hota and service taxes replacing several existing taxes. -
Optoelectronic Devices and Signal Processing
Karlsruhe Series in Photonics & Communications, Vol. 24 Tobias Harter Wireless THz Communications: Optoelectronic Devices and Signal Processing Tobias Harter Wireless Terahertz Communications: Optoelectronic Devices and Signal Processing Karlsruhe Series in Photonics & Communications, Vol. 24 Edited by Profs. C. Koos, W. Freude and S. Randel Karlsruhe Institute of Technology (KIT) Institute of Photonics and Quantum Electronics (IPQ) Germany Wireless Terahertz Communications: Optoelectronic Devices and Signal Processing by Tobias Harter Karlsruher Institut für Technologie Institut für Photonik und Quantenelektronik Wireless Terahertz Communications: Optoelectronic Devices and Signal Processing Zur Erlangung des akademischen Grades eines Doktor-Ingenieurs von der KIT-Fakultät für Elektrotechnik und Informationstechnik des Karlsruher Instituts für Technologie (KIT) genehmigte Dissertation von Tobias Harter, M.Sc. Mündliche Prüfung: 28. November 2019 Hauptreferent: Prof. Dr. Christian Koos Korreferenten: Prof. Dr. Dr. h. c. Wolfgang Freude Prof. Dr. Guillermo Carpintero-del-Barrio Impressum Karlsruher Institut für Technologie (KIT) KIT Scientific Publishing Straße am Forum 2 D-76131 Karlsruhe KIT Scientific Publishing is a registered trademark of Karlsruhe Institute of Technology. Reprint using the book cover is not allowed. www.ksp.kit.edu This document – excluding the chapters 3 to 5, C to E, the cover, pictures and graphs – is licensed under a Creative Commons Attribution-Share Alike 4.0 International License (CC BY-SA 4.0): https://creativecommons.org/licenses/by-sa/4.0/deed.en The cover page is licensed under a Creative Commons Attribution-No Derivatives 4.0 International License (CC BY-ND 4.0): https://creativecommons.org/licenses/by-nd/4.0/deed.en Print on Demand 2021 – Gedruckt auf FSC-zertifiziertem Papier ISSN 1865-1100 ISBN 978-3-7315-1083-3 DOI 10.5445/KSP/1000128941 Table of Contents Kurzfassung ...................................................................................................... -
5 Gbps Wireless Transmission Link with an Optically Pumped Uni-Traveling Carrier Photodiode Mixer at the Receiver
Vol. 26, No. 3 | 5 Feb 2018 | OPTICS EXPRESS 2884 5 Gbps wireless transmission link with an optically pumped uni-traveling carrier photodiode mixer at the receiver AHMAD W. MOHAMMAD,* HAYMEN SHAMS, KATARZYNA BALAKIER, CHRIS GRAHAM, MICHELE NATRELLA, ALWYN J. SEEDS, AND CYRIL C. RENAUD Department of Electronic and Electrical Engineering, University College London, Torrington Place, London, WC1E 7JE, UK *[email protected] Abstract: We report the first demonstration of a uni-traveling carrier photodiode (UTC-PD) used as a 5 Gbps wireless receiver. In this experiment, a 35.1 GHz carrier was electrically modulated with 5 Gbps non-return with zero on-off keying (NRZ–OOK) data and transmitted wirelessly over a distance of 1.3 m. At the receiver, a UTC-PD was used as an optically pumped mixer (OPM) to down-convert the received radio frequency (RF) signal to an intermediate frequency (IF) of 11.7 GHz, before it was down-converted to the baseband using an electronic mixer. The recovered data show a clear eye diagram, and a bit error rate (BER) of less than 10−8 was measured. The conversion loss of the UTC-PD optoelectronic mixer has been measured at 22 dB. The frequency of the local oscillator (LO) used for the UTC-PD is defined by the frequency spacing between the two optical tones, which can be broadly tuneable offering the frequency agility of this photodiode-based receiver. Published by The Optical Society under the terms of the Creative Commons Attribution 4.0 License. Further distribution of this work must maintain attribution to the author(s) and the published article’s title, journal citation, and DOI. -
HBT, Mixer, Opto-Electronic, Nearly Gaussian Doping Profile, Linear Grading Composition, Current Gain, Base Transit Time
Electrical and Electronic Engineering 2016, 6(2): 30-38 DOI: 10.5923/j.eee.20160602.03 Conversion Gain Improvement of InP/InGaAs HBT Opto-Electronic Mixer Using Nearly Gaussian Doping Profile and Linear Grading of Composition in Base Region Hassan Kaatuzian, Keyvan Farhang Razi* Photonics Research Laboratory (P.R.L), Electrical Engineering Department, Amirkabir University of Technology, Tehran, Iran Abstract Conversion gain improvement of an integrated opto-electronic mixer consisting of InP/InGaAs heterojunction bipolar transistors(HBTs) in single and cascode configuration is estimated in this paper. The effects of two methods are analyzed for this purpose. Two important factors for determining the performance of a transistor are base transit time ( ) and current gain( ). In first method, the uniform base doping profile is modified to nearly Gaussian base doping profile and by this modification base transit time is decreased and current gain is increased from 130 to 306. In second method, linear grading of compositionβ of the base is proposed to enhance current gain and decrease base transit time. In second method current gain is increased from 130 to 292. Another important factor for determining performances of a transistor is base width. By decreasing base width up to 250 A, current gain can be increased up to 614 and 553 in first and second methods respectively. The dependence of diffusion constant, doping concentration and temperature is considered in the first method. The modified transistors are inserted in the structure of single and cascode Opto-Electronic mixers and after software simulation, considerable improvement of up and down conversion gains of mixer are obtained. -
Modulation Locking Subsystems for Gravitational Wave Detectors
Modulation Locking Subsystems for Gravitational Wave Detectors Benedict John Cusack September 2004 Thesis submitted for the degree of Master of Philosophy at the Australian National University Declaration I certify that the work contained in this thesis is, to the best of my knowledge, my own original research. All material taken from other references is explicitly acknowledged as such. I certify that the work contained in this thesis has not been submitted for any other degree. Benedict Cusack September, 2004 The Road Not Taken Two roads diverged in a yellow wood, And sorry I could not travel both And be one traveller, long I stood And looked down one as far as I could To where it bent in the undergrowth; Then took the other, as just as fair, And having perhaps the better claim, Because it was grassy and wanted wear; Though as for that the passing there Had worn them really about the same, And both that morning equally lay In leaves no step had trodden black. Oh, I kept the first for another day! Yet knowing how way leads on to way, I doubted if I should ever come back. I shall be telling this with a sigh Somewhere ages and ages hence; Two roads diverged in a wood, and I — I took the one less travelled by, And that has made all the difference. Robert Frost, 1920. Acknowledgements I don’t think I ever doubted that this document would one day come into existence, it is more that I couldn’t see for a long time what would fill it. -
Integrated Photonics for Millimetre Wave Transmitters and Receivers”
University College London Department of Electrical and Electronics Engineering PhD Thesis “Integrated photonics for millimetre wave transmitters and receivers” By Ahmad Wasfi Mahmoud Mohammad Supervised by Prof. Cyril C. Renaud Prof. John E. Mitchell ‘I, Ahmad Wasfi Mahmoud Mohammad, confirm that the work presented in this thesis is my own. Where information has been derived from other sources, I confirm that this has been indicated in the thesis'. February 2019 To the memory of my mother Wajiha Rushdi Mohammad 2 Abstract This PhD thesis entitled “Integrated photonics for millimetre wave transmitters and receivers” aimed at investigating the possibility of employing the uni-traveling carrier photodiode (UTC-PD) in millimetre wave (MMW) wireless receivers and, eventually, demonstrating a photonic integrated transceiver, by exploiting the concept of optically-pumped mixing (OPM). Previously, the UTC-PD has been successfully demonstrated as an OPM, by mixing an optically-generated local oscillator (LO) with a high frequency RF signal to generate a replica of the RF signal at a low intermediate frequency (IF), defined by the difference between the LO and the RF signal. This concept forms the foundation of this PhD thesis. The principal idea is to deploy the UTC-PD mixer in MMW wireless receivers to down-convert the high frequency data signal into a low frequency IF, where it can be easily processed and recovered. The main challenge to this approach is the low conversion efficiency of the UTC-PD mixer. For example, a conversion loss of 32 dB has been reported at 100 GHz. Also, the detection bandwidth in previous demonstrations was very narrow (around 100 Hz), which is too narrow to be useful in high-speed data communications. -
2016 Reprints of Professor Larry A
Research in Optoelectronics (A) 2016 Reprints of Professor Larry A. Coldren and Collaborators ECE Technical Report 17-01 Department of Electrical & Computer Engineering University of California, Santa Barbara Research in Optoelectronics (A) Reprints published in 2016 by Professor Larry A. Coldren and Collaborators Published as Technical Report # ECE 17-01 of The Department of Electrical & Computer Engineering The University of California Santa Barbara, CA 93106 Phone: (805) 893-4486 Fax: (805) 893-4500 E-mail: [email protected] http://www.ece.ucsb.edu/Faculty/Coldren/ Introduction: The attached contains papers published by Professor Coldren and collaborators in various journals and conferences in calendar year 2016. Any publication on which Prof. Coldren is named as a co-author is included. The work has a focus on III-V compound semiconductor materials as well as the design and creation of photonic devices and circuits using these materials. The characterization of these devices and circuits within systems environments is also included. As in the past, the reprints have been grouped into several areas. This year these are all within the Photonic Integrated Circuits (PICs) category. Subcategories called out are A. Reviews of Applications, B. SOAs and Phase-Sensitive Amplifiers, and C. Signal Processing with Active Micro-ring Filters. The work was performed with funding from a couple of federal grants, some gift funds from industry, and support from the Kavli Endowed Chair in Optoelectronics and Sensors. Some of the PIC work was funded by the MTO Office of DARPA via a subcontract from UC-Davis and a GOALI from NSF together with support from Freedom Photonics. -
A 300-Ghz Wireless Link Employing a Photonic Transmitter and an Active
A 300-GHz wireless link employing a photonic transmitter and an active electronic receiver with a transmission bandwidth of 54 GHz Iulia Dan, Vinay Chinni, Pascal Szriftgiser, Emilien Peytavit, Jean-François Lampin, Malek Zegaoui, Mohammed Zaknoune, Guillaume Ducournau, Ingmar Kallfass To cite this version: Iulia Dan, Vinay Chinni, Pascal Szriftgiser, Emilien Peytavit, Jean-François Lampin, et al.. A 300-GHz wireless link employing a photonic transmitter and an active electronic receiver with a transmission bandwidth of 54 GHz. IEEE Transactions on Terahertz Science and Technology, Institute of Electrical and Electronics Engineers, 2020, 10, pp.271-281. 10.1109/tthz.2020.2977331. hal-02997786 HAL Id: hal-02997786 https://hal.archives-ouvertes.fr/hal-02997786 Submitted on 26 Nov 2020 HAL is a multi-disciplinary open access L’archive ouverte pluridisciplinaire HAL, est archive for the deposit and dissemination of sci- destinée au dépôt et à la diffusion de documents entific research documents, whether they are pub- scientifiques de niveau recherche, publiés ou non, lished or not. The documents may come from émanant des établissements d’enseignement et de teaching and research institutions in France or recherche français ou étrangers, des laboratoires abroad, or from public or private research centers. publics ou privés. 1 300 GHz Wireless Link Employing a Photonic Transmitter and an Active Electronic Receiver with a Transmission Bandwidth of 54 GHz Iulia Dan, Vinay Chinni, Pascal Szriftgiser, Emilien Peytavit, Jean-Franc¸ois Lampin, Malek Zegaoui, Mohammed Zaknoune, Guillaume Ducournau, and Ingmar Kallfass Abstract—In this paper, we present a 300 GHz wireless link 425 GHz composed of a photonic uni-traveling-carrier diode transmitter [10] 300 GHz and an active electronic receiver based on millimeterwave in- 240 GHz 300 GHz 237.5 GHz [9] tegrated circuits fabricated in an InGaAs metamorphic high [5] [4] electron mobility transistor technology. -
Professional Report
TOWARD OPTICAL ARCHITECTU R ES IN RADAR SYSTEM DESIGN FOR ULTRALIGHT UNMANNED AERIAL VEHICLES Alexander Sharp A thesis submitted in partial fulfillment of the requirements for the degree of Master of Engineering Science The University of Adelaide 2009 Date: April 11th 2011 School of Electrical and Electronic Engineering The University of Adelaide ABS TRACT A thesis is presented on the deployment of radar systems on ultra light unmanned aerial vehicles which are compact and lightweight. Deployment upon a small frame presents significant problems due to the size, weight and power (SWaP) requirements of components and which are addressed in this work. Traditional pulsed radar is inadequate due to these considerations and alternatively, a frequency modulated continuous wave (FMCW) radar architecture is proposed. Optical systems, due to their light weight, bandwidth and resistance to interference are a possible implementation for the radar front end. Optical architecture implementations suffer from low signal to noise ratio and low spurious free dynamic range. Employment of an optical architecture for a narrow band radar would be inefficient and its performance would be substandard. Instead a focus on a wide bandwidth is pursued. The advantages of deploying a wide bandwidth, frequency agile radar are its resistance to jamming and the receiver‟s usefulness as a radar warning receiver. An investigation into optical systems discovers an optical architecture that is highly resistant to environmental changes making it robust, easy to maintain and inexpensive to deploy. A COTS based beam forming array is designed within the optical system. The beam former allows for multiple apertures and multiple beams, a feature previously limited to expensive, complex array architectures. -
Audio Electronics SUB-MODULE: 4.1 Amplification Systems
TECHNOLOGY ElJUCl\.TION Grades 9-12 PROCRl1.M/COURSE Electronics/Audio DRAFT / INDUSTRIAL ARTS EDUCATION Module of Instruction PHASE - Concentration ELEMENT - Technology AREA OF CONCENTRATION: Electronics MODULE: 4.0 Audio Electronics SUB-MODULE: 4.1 Amplification Systems TOPICS: Amplifier Theory Amplifier Applications PREREQUISITES: None Prepared by Howard Sasson George Legg Robert F. Caswell James Goldstine Joseph Sarubbi Sandra P. Sommer Bruce G. Kaiser Reprinted 1997 '• TOTAL TEACHING TIME: 30 Hours (8 Weeks) _) THE UNIVERSITY OF THE STATE OF NEW YORK Regents of The University CARL T. HAYDEN, Chancellor, A.B., J.D............................................................. Elmira LOUISE P. MA'ITEONI, Vice Chancellor, B.A., M.A., Ph.D. ............................... , Bayside JORGE L. BATISTA, B.A., J.D. ............................................................................... Bronx J. EDWARD MEYER, B.A., LL.B ........................................................................... Chappaqua R. CARLOS CARBALLADA, Chancellor Emeritus, B.S ............... :· ........................... Rochester ADELAIDE L. SANFORD, B.A., M.A., P.D.............................................................. Hollis DIANE O'NEILL MCGIVERN, B.S.N., M.A., Ph.D. .............................................. Staten Island SAUL B. COHEN, B.A., M.A., Ph.D ....................................................................... New Rochelle JAMES C. DAWSON, A.A., -B.A., M.S., Ph.D. ........................................................ Peru ROBERT