Advanced Techniques of Theory of Constraints and Activity Based
Total Page:16
File Type:pdf, Size:1020Kb
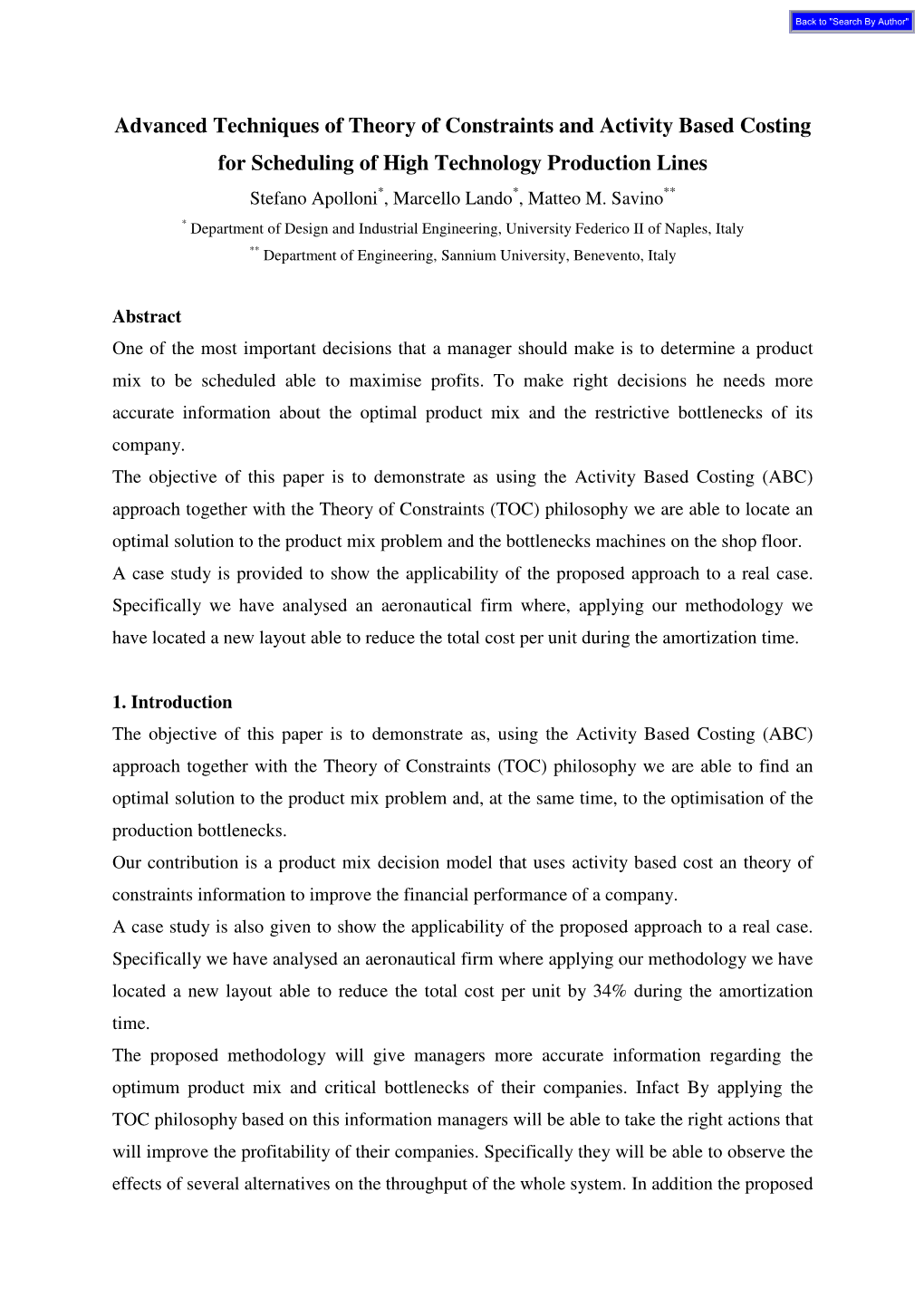
Load more
Recommended publications
-
The Cambridge Handbook of Phonology
This page intentionally left blank The Cambridge Handbook of Phonology Phonology – the study of how the sounds of speech are represented in our minds – is one of the core areas of linguistic theory, and is central to the study of human language. This state-of-the-art handbook brings together the world’s leading experts in phonology to present the most comprehensive and detailed overview of the field to date. Focusing on the most recent research and the most influential theories, the authors discuss each of the central issues in phonological theory, explore a variety of empirical phenomena, and show how phonology interacts with other aspects of language such as syntax, morph- ology, phonetics, and language acquisition. Providing a one-stop guide to every aspect of this important field, The Cambridge Handbook of Phonology will serve as an invaluable source of readings for advanced undergraduate and graduate students, an informative overview for linguists, and a useful starting point for anyone beginning phonological research. PAUL DE LACY is Assistant Professor in the Department of Linguistics, Rutgers University. His publications include Markedness: Reduction and Preservation in Phonology (Cambridge University Press, 2006). The Cambridge Handbook of Phonology Edited by Paul de Lacy CAMBRIDGE UNIVERSITY PRESS Cambridge, New York, Melbourne, Madrid, Cape Town, Singapore, São Paulo Cambridge University Press The Edinburgh Building, Cambridge CB2 8RU, UK Published in the United States of America by Cambridge University Press, New York www.cambridge.org Information on this title: www.cambridge.org/9780521848794 © Cambridge University Press 2007 This publication is in copyright. Subject to statutory exception and to the provision of relevant collective licensing agreements, no reproduction of any part may take place without the written permission of Cambridge University Press. -
IEEM 2017 Program
Contents Welcome 1 Message 2 Organizers & Committees Program 6 Overview 13 11-Dec 27 12-Dec 47 Abstracts 126 Author Index Conference Venue SUNTEC Singapore Plenaries 1 Raffles Boulevard, Suntec City, 8 Workshop Singapore 039593 9 Keynotes Tel: +65 6337 2888 General Info 5 Venue Layout 11 Presenter Guides 12 Conference Dinner 131 Contacts & Tel Singapore Guide 132 Getting to SUNTEC 133 Transportation in Singapore 134 Singapore Mass Rapid Transit Map 135 Experience Singapore Welcome Message Dear Participants, A very warm welcome to you to the 2017 IEEE International Conference on Industrial Engineering and Engineering Management (IEEM2017) to be held from 10-13 December 2017 in Singapore. Some eleven years ago, the first IEEM was held in Singapore in 2007. We were encouraged by the support and enthusiasm of our colleagues in Asia and had organized the conference every year without fail since then. It has grown into a high-quality conference in the fields of industry engineering and engineering management, with participants from all corners of the world. For this we are very gratefully to authors, reviewers, participants, and also our co-hosts in Hong Kong, Macau, Bali, Bangkok and Kuala Lumpur during this period. We can now confidently say that IEEM brings together the community’s most innovative thinkers and dynamic researchers from around the world to share the latest research findings in industrial engineering and engineering management. This year, IEEM2017 received nearly 1000 submissions from more than 50 countries. As in the past, each paper was sent to at least three reviewers. The acceptance decisions were based on at least two consistent recommendations, ensuring the quality and standard of the conference. -
008-0518 Theory of Constraints Contributions to Outbound Logistics Fernando Bernardi De Souza São Paulo State University
008-0518 Theory of Constraints contributions to outbound logistics Fernando Bernardi de Souza São Paulo State University (UNESP) Av. Eng. Luiz Edmundo C. Coube 14-01 Bauru, SP, 17033-360 - Brazil [email protected] Tel: 55 (14) 3103-6122 Sivio R. I. Pires Methodist University of Piracicaba (UNIMEP) Rodovia do Açúcar, Km 156 Piracicaba, SP, 13400-911 - Brazil [email protected] Tel.: 55 (14) 3124-1515 POMS 19th Annual Conference La Jolla, California, U.S.A. May 9 to May 12, 2008 Abstract This article aims to present the main contributions of the Theory of Constraints (TOC) to outbound (distribution) logistics. It presents the thesis defended by TOC, according to which the current ways of managing outbound logistics, based mainly on sales forecasts, batching policies, and indicators that do not privilege the supply chain performance as a whole, lead to difficulties in handling the trade-off between logistics (stock and transportation) costs and stock-outs levels. This conventional logistics management is labeled by TOC as pushed distribution, in contrast with its defended approach called pulled distribution. Considering the few scientific texts existing on the subject, this article claims to present, based on a theoretical research, the technical aspects of the approach suggested by TOC and discuss the assumptions it is based on, in an attempt to contribute to the expansion of outbound logistics knowledge and widen the analysis of supply chain management. Key words: Outbound logistics; distribution; pull system; Theory of Constraints. 1. Introduction Since its inception about two decades ago, the Theory of Constraints (TOC) has developed quickly and stood its ground as an important model for business management (WATSON et al, 2007). -
Someone Else Will. That's Guarantee!”
RIP G el “your customers are somebody else’s prospects. If you won’t take care of them, someone else will. That’s guarantee!” Service Quality Excellence Masterclass el Maximizing profit & achieving competitive advantage by delivering a level of service that will rise above & beyond customer expectations RIP th th 27 & 28 July 2012 G Mumbai, India Book & Pay per Delegate: Book & Pay before 19th May 2012 - INR 27950 Net + 12.36 % service tax Book & Pay after 19th May 2012 - INR 29950 Net + 12.36 % service tax *3 or more delegates 10% discount. Investment is per person for 2 days non residential conference. Payments have to be processed in 5 working days customers from booking. TDS/ Taxes needs to be added on the Net amount as above “The way to Investment for International clients is USD 900 Net + 12.36 % Service Tax lies in heart & wallet how well we initially serve our customers & deliver quality service” GRIPel course leader: Neil Known in short as Neil helps organizations deliver superior customer experience, transform businesses & execute business strategy. Neil has served in various leadership capacities in organizations like HSBC, Bank of America, Whirlpool Corporation, Standard Chartered Bank & TVS Motors. During his tenure, he has led a wide variety of enterprise-level change deployment programs in manufacturing & service environments. His last assignment was with HSBC as Senior Vice President for Customer Experience & Business Transformation. Prior to this, he led Quality & Productivity Unit for Bank of America-India. In both these roles, as enterprise deployment leader, he managed a large team of experts & senior resources with varied experience & background. -
Theory of Constraints (TOC) As an Operations Improvement Methodology at the Private Healthcare Sector in Cyprus Spyridon Bonatsos
Theory of constraints (TOC) as an operations improvement methodology at the private healthcare sector in Cyprus Spyridon Bonatsos To cite this version: Spyridon Bonatsos. Theory of constraints (TOC) as an operations improvement methodology at the private healthcare sector in Cyprus. Business administration. Université de Strasbourg, 2019. English. NNT : 2019STRAB021. tel-02965900 HAL Id: tel-02965900 https://tel.archives-ouvertes.fr/tel-02965900 Submitted on 13 Oct 2020 HAL is a multi-disciplinary open access L’archive ouverte pluridisciplinaire HAL, est archive for the deposit and dissemination of sci- destinée au dépôt et à la diffusion de documents entific research documents, whether they are pub- scientifiques de niveau recherche, publiés ou non, lished or not. The documents may come from émanant des établissements d’enseignement et de teaching and research institutions in France or recherche français ou étrangers, des laboratoires abroad, or from public or private research centers. publics ou privés. Université de Strasbourg Ecole Doctorale Augustin Cournot HuManiS (ED 221) THESE POUR L’ OBTENTION DU DOCTORAT EN SCIENCES DE GESTION Application de la Théorie des contraintes (TOC) dans le secteur des soins de santé privé à Chypre THESE présentée par: Spyridon Bonatsos Soutenue le: 20 March 2019 “τα πάντα ρεῖ” – “Everything flows.” Heraclitus JURY Directeur de thése Thierry Nobre Professeur, Université de Strasbourg Rapporteurs Irène G eorgescu Professeur, Université de Montpellier François M eyssonier Professeur, Université de Nantes Membres Philippe Wieser Professeur, Ecole Polytechnique Fédérale de Lausanne Christophe Baret Professeur, Université de Aix Marseille Acknowledgments With this opportunity, I would like to convey my sincere thanks and gratitude to the University of Strasbourg for honoring me with accepting my enrollment to the doctoral program. -
Redalyc.THE THEORY of CONSTRAINTS and the SMALL FIRM: an ALTERNATIVE STRATEGY in the MANUFACTURING MANAGEMENT
RAI - Revista de Administração e Inovação ISSN: 1809-2039 [email protected] Universidade de São Paulo Brasil Pozo, Hamilton; Takeshy Tachizawa, Elio Takeshi; Picchiai, Djair THE THEORY OF CONSTRAINTS AND THE SMALL FIRM: AN ALTERNATIVE STRATEGY IN THE MANUFACTURING MANAGEMENT RAI - Revista de Administração e Inovação, vol. 6, núm. 3, septiembre-diciembre, 2009, pp. 5-25 Universidade de São Paulo São Paulo, Brasil Available in: http://www.redalyc.org/articulo.oa?id=97312500002 How to cite Complete issue Scientific Information System More information about this article Network of Scientific Journals from Latin America, the Caribbean, Spain and Portugal Journal's homepage in redalyc.org Non-profit academic project, developed under the open access initiative 5 ARTICLES THE THEORY OF CONSTRAINTS AND THE SMALL FIRM: AN ALTERNATIVE STRATEGY IN THE MANUFACTURING MANAGEMENT Hamilton Pozo Pós-Doutor em Administração pela Universidade de São Paulo – FEA/USP Coordenador e Pesquisador no Projeto de implantação de mestrado profissional na Faculdade Campo Limpo Paulista – FACCAMP E-mail: [email protected] [Brasil] Elio Takeshi Takeshy Tachizawa Doutor em Administração de Empresas pela Fundação Getúlio Vargas – FGV Professor da Faculdade Campo Limpo Paulista – FACCAMP E-mail: [email protected] [Brasil] Djair Picchiai Doutor em Administração de Empresas pela Fundação Getúlio Vargas – FGV Professor da Fundação Getúlio Vargas – FGV e professor da Faculdade Campo Limpo Paulista – FACCAMP E-mail: [email protected] [Brasil] Abstract The aim of this article is to study the practical application of the Theory of Constraints (TOC) and to identify some of the main strategies related to this application. It seeks to prove that this theory does not treat organizations as a collection of independent processes, but rather as an integrated system. -
Using Theory of Constraints to Control Manufacturing Systems
ering & ine M g a n n E a Panizzolo and Garengo l g , Ind Eng Manage 2013, 2:3 a i e r m t s e DOI: 10.4172/2169-0316.1000111 u n d t n I Industrial Engineering & Management ISSN: 2169-0316 Research Article Open Access Using Theory of Constraints to Control Manufacturing Systems: A Conceptual Model Roberto Panizzolo1* and Patrizia Garengo2 1Department of Management and Engineering, University of Padua, Italy 2Department of Industrial Engineering, University of Padua, Italy Abstract Since the Goldratt and Cox’s (1984) seminal study, Theory of Constrains has evolved from a simple production scheduling software into a management philosophy, with practices and principles spanning a multitude of operation management disciplines. A variety of studies has investigated how production control is carried out in a Theory of Constrains environment, but most of research available lacks in providing an overall vision of this issue. In order to contribute to this gap, using theoretical investigation and the empirical study of five case studies, this article compares the characteristics of TOC with those typical of three shop floor control systems, i.e. MRP, JIT and Daily Rate. As result, the research identifies an interpretative framework based on the distinguishing characteristics of Theory of Constrains. The framework supports the analysis of the nature and scope of these four systems by highlighting the main differences between them. Keywords: Operations management; Theory of constraints; Drum- differences are pertinent to the third level of the manufacturing buffer-rope; MRP; JIT; Daily rate planning and control system, the so-called production executive Introduction control or shop floor control sub-system. -
Stach Et Al., 2005)
ENHANCING THE QUALITY OF PLANNING OF SOFTWARE DEVELOPMENT PROJECTS Marco Antônio Amaral Féris A thesis submitted for the degree of Doctor of Philosophy of The Australian National University September 2015 STATEMENT OF ORIGINALITY I certify that the thesis entitled Enhancing the Quality of Planning of Software Development Projects submitted for the degree of Doctor of Philosophy of the Australian National University is an original work, which is the result of my own independent intellectual effort. Where reference is made to the work of others, due acknowledgment is given. ------------------------------------------------------------- Marco Antônio Amaral Féris ANU College of Business and Economics The Australian National University March 2015 Enhancing the Quality of Planning of Software Development Projects iii ACKNOWLEDGEMENTS I dedicate this thesis and the completion of my PhD degree to the two most important and influential women in my life: my wife and my mother. Words cannot express how grateful I am to my wife, Solange Braga Manto, who has encouraged and supported me tirelessly in my academic pursuits. She has allowed me to put our life on hold and to sacrifice our time together so I could strive to fulfil my dream. My mother, Dulce Helena Cabral Amaral, has instilled in me the confidence that I can accomplish anything that I strive for. Although she cannot be physically present to share in the celebration of the completion of this degree, the memories of her and her love and support will sustain me, as it has in the past, for the remainder of my years. It is with particular appreciation that I wish to thank my Chief Supervisor, Associate Professor Ofer Zwikael, for his diligent assistance with this study and for setting standards of academic excellence to which I aspire. -
Application of the Theory of Constraints for Project Management
Management and Production Engineering Review Volume 8 • Number 3 • September 2017 • pp. 87–95 DOI: 10.1515/mper-2017-0031 APPLICATION OF THE THEORY OF CONSTRAINTS FOR PROJECT MANAGEMENT Justyna Trojanowska, Ewa Dostatni Poznan University of Technology, Chair of Management and Production Engineering, Poland Corresponding author: Justyna Trojanowska Poznan University of Technology Chair of Management and Production Engineering Piotrowo 3, 60-965 Poznan, Poland phone: (+48) 61 647-59-91 e-mail: [email protected] Received: 22 August 2016 Abstract Accepted: 27 February 2017 The large variability of internal and external factors is a serious problem hampering pro- duction management. To meet the standards and at the same time ensure the viability of production it is necessary to quickly respond to problems that arise during production processes, and to adequately correct plans. Measures taken in the management of madeto- order production are frequently single and unique, and therefore resemble the features of project management. The paper discusses the project management method derived from the theory of constraints – CCPM. The paper describes an original algorithm for CCPM im- plementation and presents the results of success CCPM implementation in a company from the Wielkopolska region. The implementation of CCPM resulted in improved timeliness of order delivery, improved communication and standardization of processes related to order delivery. Keywords project management, theory of constraints, critical chain project management. Introduction Project management is a management method whose aim is to effectively reach the project objec- One of the main challenges facing SMEs in made tive within the specified time and a fixed budget [7]. -
Applying Theory of Constraints Tools to Focus Lean Development
Boeing Defense, Space & Security | Wichita Engineering November 16, 2010 Applying Theory of Constraints Tools to Focus Lean Development National Defense Industrial Association 10th Annual CMMI Technology Conference & User Group Software Engineering Institute Carnegie Mellon University Tim Oltman Boeing Defense, Space & Security Wichita, Kansas Introduction Boeing Defense, Space & Security | Wichita Engineering Tim Oltman Boeing Defense, Space & Security Wichita, Kansas Engineering Analysis & Integration Lean Engineering Six Sigma Black Belt [email protected] Phone (316) 209-6183 Boeing Engineering Analysis & Integration Team (AIT) in Wichita Kansas, where he is responsible for Lean support of Lean+ 10X and process improvement projects across a variety of Engineering disciplines. Tim is Theory of Constraints International Certification Organization (TOCICO) certified in the Thinking Process tools, a Boeing Six Sigma Black Belt and heads the Wichita site Six Sigma Steering Committee. Tim has a B.S. in Industrial Engineering from the University of Nebraska and an M.B.A. in Operations Management from National University. Tim has over 25 years of Aerospace experience with General Dynamics, Raytheon and Boeing. Tim has been published and a presenter at the 1999 AEROFAST conference. Tim received an Institute of Industrial Engineers process improvement award for a Statistical Process Control project he implemented to reduce office process flow time. 2 BOEING PROPRIETARY – Distribution Limited to Boeing Personnel Theory of Constraints (TOC) Definition Boeing Defense, Space & Security | Wichita Engineering TOC is a management philosophy introduced by Dr. Eliyahu M. Goldratt in his 1984 book The Goal, that is geared to help organizations continually achieve their goal. Based upon the contention that any manageable system is limited in achieving more of its goal by a small number of constraints (& that there is always at least one). -
Theory of Constraints Case Study in the Make-To-Order Environment
Journal of Industrial Engineering and Management JIEM, 2021 – 14(1): 72-85 – Online ISSN: 2013-0953 – Print ISSN: 2013-8423 https://doi.org/10.3926/jiem.3283 Theory of Constraints Case Study in the Make-to-Order Environment Aitor Orue , Aitor Lizarralde , Itxaso Amorrortu , Unai Apaolaza Mondragon Unibertsitatea (Spain) [email protected], [email protected], [email protected], [email protected] Received: July 2020 Accepted: November 2020 Abstract: Purpose: The theory of constraints (TOC) drum-buffer-rope methodology is appropriate when managing a production plant in complex environments, such as make-to-order (MTO) scenarios. However, some difficulties have been detected in implementing this methodology in such changing environments. This case study analyses a MTO company to identify the key factors that influence the execution of the third step of TOC. It also aims to evaluate in more depth the research started by Lizarralde et al. (2020) and compare the results with the existing literature. Design/methodology/approach: The case study approach is selected as a research methodology because of the need to investigate a current phenomenon in a real environment. Findings: In the case study analysed, the protective capacity of non-bottleneck resources is found to the key factor when subordinating the MTO system to a bottleneck (BN). Furthermore, it coincides with one of the two key factors defined by the literature, namely protective capacity and protective inventory. Originality/value: The three key contributions of this study focus on the MTO environment as follows. The first is about identifying the key factors in subordinating the system to the BN (step 3, TOC) according to the existing literature which have been identified through a systematic literature review. -
Theory of Constraints and Six Sigma: Investigating Differences and Similarities for Continuous Improvement
INDEPENDENT JOURNAL OF MANAGEMENT & PRODUCTION (IJM&P) http://www.ijmp.jor.br v. 5, n. 2, February – May 2014. ISSN: 2236-269X DOI: 10.14807/ijmp.v5i2.150 THEORY OF CONSTRAINTS AND SIX SIGMA: INVESTIGATING DIFFERENCES AND SIMILARITIES FOR CONTINUOUS IMPROVEMENT Diego Augusto de Jesus Pacheco University Federal of Rio Grande do Sul, UFRGS – Brazil E-mail: [email protected] Submission: 04/10/2013 Revision: 19/10/2013 Accept: 01/11/2013 ABSTRACT The main objective of this study is to analyse some points of convergence and divergence between the Theory of Constraints and Six Sigma when used in an integrated manner for the continuous improvement of operating manufacturing systems. This research also aims to advance a better understanding of the fundamental principles of such methodologies by performing a comparative analysis of critical issues. The focus of the discussion of this study is to review the literature to identify the mains similarities and differences between these two approaches when applied in an integrated way in productive systems. To conduct this research, we carry out a broad literature review of the state of the art on the topic of Operations Management. The results of this study suggest that the Theory of Constraints and Six Sigma have many complementary elements that overlap and that a vast field of research must be explored on this issue. As a result, this study conducts a comparative analysis of 28 critical criteria of the Theory of Constraints and Six Sigma to understand these approaches. Keywords: Theory of Constraints, Six Sigma, Continuous Improvement. [http://creativecommons.org/licenses/by/3.0/us/] Licensed under a Creative Commons Attribution 3.0 United States License 331 INDEPENDENT JOURNAL OF MANAGEMENT & PRODUCTION (IJM&P) http://www.ijmp.jor.br v.