Footwear Pattern Making
Total Page:16
File Type:pdf, Size:1020Kb
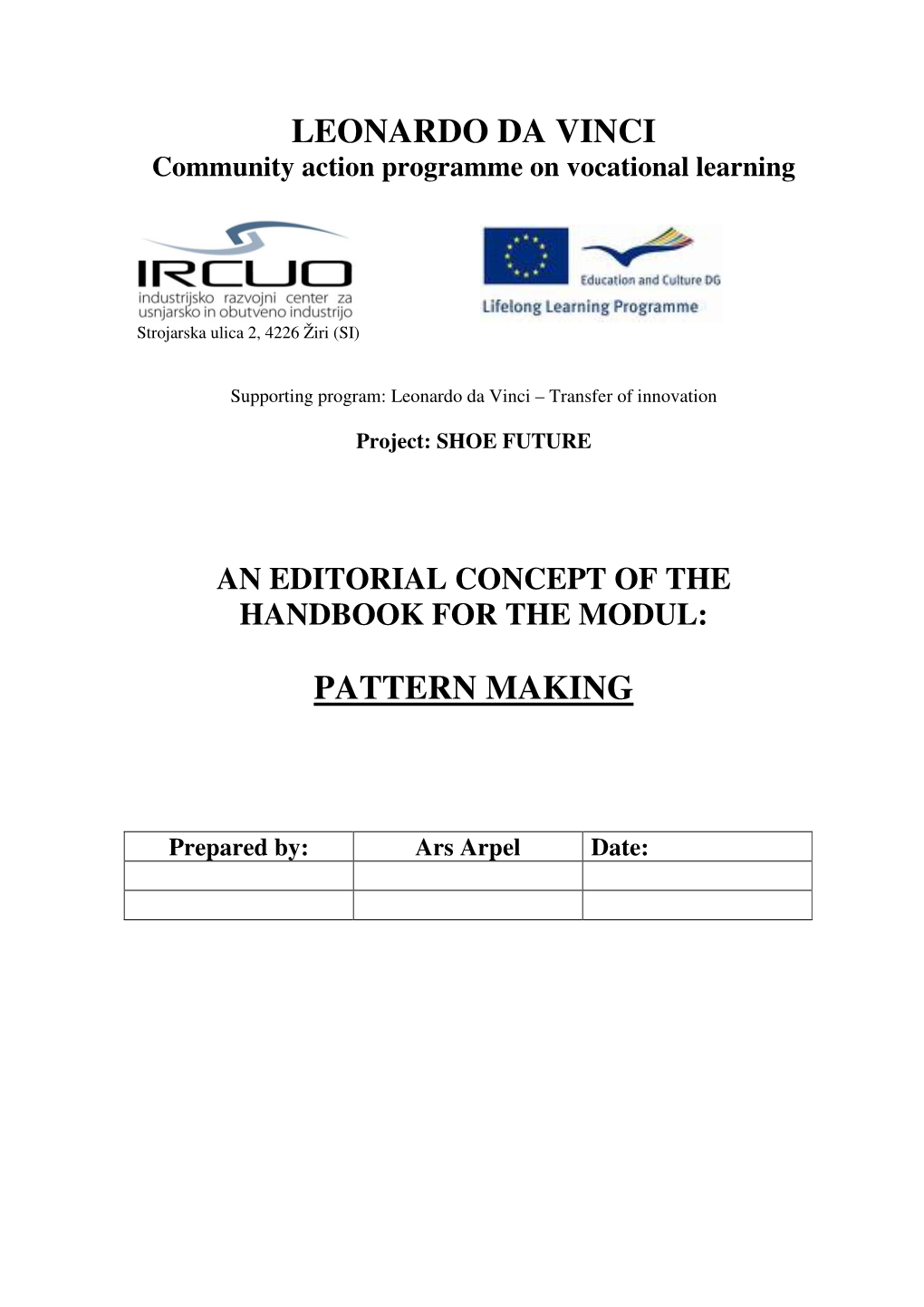
Load more
Recommended publications
-
BRAND PACK 2020 “Grenson Is an Old Company with a Young Heart
BRAND PACK 2020 “ Grenson is an old company with a young heart. We believe that craftsmanship and design go hand in hand” Tim Little, CEO & Creative Director Grenson was born in 1866 in Rushden, Northamptonshire. William Green, the founder, started making high quality shoes for London Gentlemen and was so successful that he soon had to build a factory and the company grew from there. Throughout the twentieth Century the company expanded, making a huge contribution to both war efforts along the way. By the Millennium however, like many British shoe companies, the business began to run out of steam. Recently Grenson has undergone a new lease of life, helped by their focus on quality and modern design whilst never losing sight of their impressive heritage. HERITAGE + BACKGROUND 1866 1939 - 1945 William Green begins making shoes in a loft above Once again the company is called into action to the Corn Merchants in Rushden, Northamptonshire. make shoes and boots for the soldiers in WWII. 1874 1950 William Green discovers the Goodyear Welted Hayden Green discovers moccasins in America. He method of shoemaking. visits India where the best hand-stitching skills are found to make a collection that gives the company 1895 a new lease of life during the post war depression. The business made the move to a state of the art new factory at Queen Street, Rushden. 1960 - 2005 Grenson creates many innovative products such as 1913 exotic skin shoes in the 60’s and 70’s, but eventually The business decided to move with the times by begins to decline due to the growing number of developing a “modern brand name” GRENSON is born. -
Boots and Shoes
COMPILERS NOTES The following is a faithful digitalization of volume VI of F.Y. Golding’s BOOTS AND SHOES. I have taken the liberty of using this original blank page to comment on the material within. Insofar as I was able, I have endeavoured to preserve the original appearance, formatting, kerning, spacing, etc,. of the original work. Sometime, however, this was simply not possible. The typefaces used in the original text are not precisely duplicated in any of the font sets to which I have access. Then too, the spacing between chapter, paragraph, and graphic elements is often inconsistent within the original text. Sometimes a chapter heading will be set an inch and a quarter below the edge of the page, sometime an inch and a half. Sometimes, using a given set of paragraph styles, a page would format almost to the exact word at the bottom margin...and then the next page would run over or come up substantially short. Nevertheless, I have preserved page numbers and the contents of those pages to fairly close extent. Beyond that, nothing has been added or subtracted from the text as it is contained in the original volumes in my possession. It is my fervent hope that this work will help to preserve the Trade and make this invaluable resource more accessible to those students seeking to learn from the past masters. DWFII BOOTS AND SHOES THEIR MAKING MANUFACTURING AND SELLING VOLUME VI BESPOKE BOOTMAKING J. BALL HANDSEWN BOOTMAKING H. ROLLINSON, A.B.S.I. BOOTS AND SHOES THEIR MAKING MANUFACTURE AND SELLING A WORK IN EIGHT VOLUMES DEALING WITH PATTERN CUTTING AND MAKING. -
Gulfstream – Nonstop
VOLUME 02 EDITION 2012 LUXE KICKS DESTINATION DUBAI FLY-BY-WIRE Sole Men Bespoke Italian shoes hit their stride By LIz GroSSMAn fter starring in a span of criti- Bontoni’s standard of craftsman- cally acclaimed films in the ’90s, ship ranks among the highest of any Daniel Day-Lewis disappeared bespoke Italian shoemaker. from the public eye. From 1999 to 2000, the eccentric, reclusive actor wasn’t preparing for a role; rather he was holed up as a dili- gent apprentice at a cobbler’s studio in Florence, Italy. His mentor? Master shoemaker Stefano Bemer, who passed away in July. Bemer handcrafted bespoke men’s shoes with waxed, handwoven flat laces; used calf or exotic leathers like crocodile, stingray, sharkskin or ostrich; and sent the finished work of art to his clients in a monogrammed wooden box. Throughout his life, the shoe- maker taught other celebrities like Andy Garcia and designer Gianfranco Ferré the art of measuring, cutting, stitching and constructing bespoke men’s shoes. But it was Day-Lewis who showed up at 8 a.m. daily for almost a year, and reportedly became disturbed when a stitch wasn’t exactly right. Day-Lewis, also an avid woodworker, may very well have an eye for craftsman- ship, but chances are Bemer helped fuel his passion for shoemaking. A legend in the shoes are still turned out of a tiny bottega in aspect of the shoe, from the height of bespoke world of Italian shoes, Bemer’s the town of Montegranaro, located in the the heel, to the design of the medallion, devotion and talent will be sorely missed, Le Marche region of east-central Italy. -
Roc Background Document: Boot and Shoe Manufacture and Repair
NTP REPORT ON CARCINOGENS BACKGROUND DOCUMENT for BOOT AND SHOE MANUFACTURE AND REPAIR FINAL MARCH 1999 Prepared for the December 2-3, 1998, Meeting ofthe Report on Carcinogens Subcommittee ofthe NTP Board ofScientific Counselors Prepared by Integrated Laboratory Systems Post Office Box 13501 Research Triangle Park, North Carolina 27709 NIEHS Contract No. N01-ES-25346 NTP Report on Carcinogens 1998 Background Document for Boot and Shoe Manufacture and Repair TABLE OF CONTENTS Summary Statement ............................................................................................... 1 1.0 IDENTIFICATION .••••••.••.••••.•.••.•••••••.•••••••.•.••••••••••••••••••••••••••••••••.•••••••••••••••••• 2 1.1 Dust........................................................................................................... 2 1.2 Other Atmospheric Contaminants ........................................................ 2 1.3 Industrial Chemicals .............................................................................. 2 1.3.1 Adhesives .................................................................................... 2 1.3.2 Cleaners ...................................................................................... 3 1.3.3 Finishes ....................................................................................... 3 Table 1-1 Known and Suspected Carcinogens Associated with Boot and Shoe Production ................................................................. 3 2.0 HUMAN EXPOSURE •.•.••.•.•....••.•..••••.•.••.•.••.•.••••••.••••••••••.•••••••.•••••••••••••••••••••.• -
ALLEN EDMONDS INTRODUCES the HONORS COLLECTION™ New Golf Shoe & Accessories Line Debut at PGA Merchandise Show
For distribution/marketing inquiries contact: For news media inquiries contact: Warren Vail Kevin Donnellon [email protected] [email protected] 858-688-9384 312-560-8065 ALLEN EDMONDS INTRODUCES THE HONORS COLLECTION™ New Golf Shoe & Accessories Line Debut at PGA Merchandise Show Port Washington, WI (January 20, 2010) – The Allen Edmonds Shoe Corporation, the leading American-based manufacturer of premium men’s footwear and accessories, is introducing the Honors Collection™, a new line of golf shoes and accessories for the 2011 golf season. The new Honors Collection of golf shoes brings almost a century of classic, handcrafted style, unrivaled comfort and time-tested performance to the sport of golf. The shoes will be handcrafted in the USA, using Goodyear 360-degree welted construction for greater stability while maintaining flexibility. They feature the finest premium leathers and heated cork between the insole and outsole for custom-like orthotic comfort as only Allen Edmonds can do. “Built by hand using the traditional shoe craftsmanship methods, the Honors Collection is for the man who respects style and wants a performance golf shoe to match his game,” says Colin Hall, Chief Marketing Officer of Allen Edmonds. “Our shoes are remarkably different than the sports shoes most companies now offer. The Honors Collection represents a return to classic, elegant shoes that reflect a refined gentleman’s approach to golf.” “Allen Edmonds -- an American-based, leading men’s dress shoe maker -- is experiencing business resurgence, and our new Honors Collection golf shoes exemplify our dedication to outfitting American businessmen who enjoy golf and appreciate style and comfort,” says Hall. -
Nike Sock-Like Flyknit Transforming Shoes As Shares Rise: R Etail1
(BN) Nike Sock-Like Flyknit Transforming Shoes as Shares Rise: R etail1 +------------------------------------------------------------------------------+ Nike Sock-Like Flyknit Transforming Shoes as Shares Rise: Retail 2012-03-07 05:00:01.4 GMT By Matt Townsend March 7 (Bloomberg) -- Nike Inc.’s latest running shoe got its start when designers tried to solve a longstanding request from athletes: make shoes as comfortable as socks. “We think a lot about what-ifs,” said Ben Shaffer, studio director of Nike’s so-called innovation kitchen. “This was a what-if. What if we made sock shoes?” Nike had tried bringing sock attributes to shoes before, starting in the 1980s with a flimsy mesh sneaker called the Sock Racer. More attempts followed, and while offering comfort, they were insufficiently durable for running and other sports. The world’s largest sporting-goods maker now says it has the solution with Flyknit, a 5.6-ounce running shoe made from synthetic yarn woven together by a knitting machine. Besides giving Nike an edge in the fast-growing lightweight running category, executives say the new weaving process could cut costs enough to move production outside Asia and one day allow anyone to personalize shoes to their exact specifications. “This is a complete game changer,” said Charlie Denson, president of the Nike brand, while holding a Flyknit after its debut in New York last month. The process cuts costs so much “that eventually we could make these shoes anywhere in the world, which makes things very interesting.” Flyknit, which costs $150 and hits U.S. stores in July, is the latest product aimed at the minimalist running movement, whose devotees advocate lightweight shoes to reduce injuries. -
Sewing Machine Needles and Awls for Shoemaking Machine Needles and Awls from Groz-Beckert for Shoemaking
Sewing Machine needles and awls for shoemaking Machine needles and awls from Groz-Beckert for shoemaking Groz-Beckert has been a reliable partner across the textile value chain since 1852. Sewing machine needles have been part of the product range for more than 30 years. This also includes shoe machine needles and awls used for shoemaking and for processing soles. Shoes have been with us for thousands of years. Whether moccasin or sport shoe, boot or sandal, safety shoe or elegant low shoe – good wearing characteristics, durability and sharp looks top the list in footwear. Sewing and shoe machine needles from Groz-Beckert help make shoes to precisely fulfill these requirements. It’s not just fancy seams that come out perfect, welt seams on welted shoes also deliver on what they promise. 2 Contents Machine needles and awls from Groz-Beckert for shoemaking 2 Shoemaking 4 The structure of a shoe 5 Sewing applications for shoemaking 6 Shoe machine needles and awls from Groz-Beckert for the manufacture of shoe bottoms and soles 10 The classification of shoe machine needles and awls 11 The point styles of shoe machine needles and awls 12 Sewing machine needles for processing shoe uppers 13 Point styles for shoemaking 14 Recommended points for upper processing 15 More services from Groz-Beckert 16 Shoemaking During pre-industrial times, cobblers 1. Development and design 2. Cutting and preparing 3. Sewing room made shoes entirely by hand. Even today, in times of industrial mass production, a The trims are made from wood or plastic. Then the The upper parts are cut to size. -
1 All Rights Reserved by Sveta Kletina © Copyright 2014
1 ALL RIGHTS RESERVED BY SVETA KLETINA © COPYRIGHT 2014 INTRODUCTION: LAST MEASUREMENTS AND BASIC PATTERN.............................................................. 3 BALLERINA FLAT SHOES COURSE ............................................................................................................. 4 HIGH HEEL PUMP SHOES COURSE ........................................................................................................... 5 FASHIONABLE BALLET FLAT SHOES FROM FABRIC COURSE ................................................................... 7 OXFORD WOMEN SHOES COURSE .......................................................................................................... 9 ANKLE WOMEN BOOT COURSE ............................................................................................................. 11 HIGH WOMEN BOOT COURSE ............................................................................................................... 12 UNISEX SANDALS COURSE ..................................................................................................................... 14 CHANGE YOUR LAST FORM ................................................................................................................... 16 MAKING HEELS COURSE ........................................................................................................................ 17 CREATING ALTERNATIVE BESPOKE OUTSOLE COURSE ......................................................................... 18 CREATING HANDMADE MIDSOLE COURSE .......................................................................................... -
Design and Development of Appropriate Tyre Sandal Shoe. Case of Rural Peoples Around Bahir Dar City
GSJ: Volume 7, Issue 2, February 2019 ISSN 2320-9186 331 Design and development of appropriate tyre sandal shoe. Case of rural peoples around Bahir Dar city. Mr. Fitsum Etefa Lecturer (Msc. in Leather product Design and Engineering) Leather Engineering Department [email protected] Ethiopian Institute of Textile and Fashion Technology (EiTEX) Bahir Dar University Bahir Dar, Ethiopia Copyright: The author declares that there is no conflict of interest regarding the publication of this paper. GSJ© 2019 www.globalscientificjournal.com GSJ: Volume 7, Issue 2, February 2019 ISSN 2320-9186 332 Abstract The current study was conducted with the objective of designing and developing appropriate tyre sandal shoe for rural people around Bahir Dar city, Ethiopia. The study was carried out through questionnaire, interview and observational study. The researcher identified the existing situations and problem happened on tyre sandal users in the area. The current tyre sandal worn by rural people around Bahir Dar city not comfortable for their feet, due to rough surface and hardness of tyre straps and it caused a dry foot and foot crack related problem around their forepart and heel area of foot. More specifically, these tyre sandals are heavy in weight and the straps frequently tend to break at the connecting points, due to poor nail or tack attachment of tyre sole and tyre straps. Based on data analysis, the researcher designed and developed four appropriate shoe collections. Target group showed their willingness to use all shoe collection. The Author gave training on production of new shoe collection for tyre sandal producers in the area. -
The Localization of Footwear Production Networks in Timiș County, Romania
Faculty of Geosciences Master in Human Geography and Planning Who is making your shoes? The localization of footwear production networks in Timiș County, Romania Andrea Ferloni Student number: 3206408 Supervisor: Andrea Morrison Co-supervisor: Ron Boschma Academic year 2009-2010 I sit at a mahogany table from Honduras. The carpet on which it stands has been manufactured at Kidderminster in England from wool brought by a sailor from the River Plate or New South Wales. The tea in a Berlin porcelain cup came from China or Assam, the coffee from Java, the sugar from Lower Saxony, Brazil or Cuba. I smoke Puerto Rican tobacco in my pipe whose stem grew in Hungary, the material for its Meerschaum bowl, carved in Thuringia, was dug in Asia Minor, the amber mouth piece came from the Baltic Sea, and the silver for the rim from the silver mines of the Erzgebirge, Harz or perhaps Potosi [Peru]... Karl Andree, quoted in Barnes and Shepperd (2000, p.3) Table of contents Table of contents i List of tables iv List of figures iv List of maps v Chapter 1 1 1.1- Theoretical background and scientific relevance 2 1.2- Societal relevance 4 1.3- Goal and research questions 5 1.4- Plan of the work 5 Chapter 2- Theoretical framework 6 2.1- Economic geography 6 2.1.1- The resurgence of regions 8 2.1.2- Knowledge externalities, innovation and institutions. 11 2.1.3-Evolutionary economic geography 13 2.1.4-The paradox of agglomeration: an ongoing debate 16 2.1.5-Taking stock, moving forward 20 2.2- Value chains and production networks 21 2.2.1-Governance: is there -
A Manual of Shoemaking and Leather and Rubber Products
m I . S l/itf 6 ^ f 0-^4^ /i.7 .d^ ^ rur^ M^ '1- A MANUAL OF SHOEMAKING An Old-Fashioned Shoemaker. Frontispiece. A MANUAL OF SHOEMAKma AND LEATHEK AND RUBBEE PEODUCTS BY WILLIAM H. DOOLEY PRESrCIPAL OF THE LOWELL INDUSTRIAL SCHOOL ILLUSTRATED BOSTON LITTLE, BROWN, AND COMPANY 1912 1 <^^. Copyright, 1912, By Little, Brown, and Company. All rights reserved. Published, September, 1912. Bsmmooum PREFACE The author was asked in 1908 by the Lynn Commission on Industrial Education to make an investigation of European shoe schools and to assist the Commission in preparing a course of study for the proposed shoe school in the city of Lynn. A close investigation showed that there were sev- eral textbooks on shoemaking published in Europe, but that no general textbook on shoemaking had been issued in this country adapted to meet the needs of industrial, trade, and commercial schools or those who have just entered the rubber, shoe, and leather trades. This book is written to meet this need. Others may find it of interest. The author is under obligations to the following persons and firms for information and assistance in preparing the book, and [v] PREFACE for permission to reproduce photographs and information from their publications: Mr. J. H. Finn, Mr. Frank L. West, Head of Shoemaking Department, Tuskegee, Ala., Mr. Louis Fleming, Mr. F. Garrison, Presi- dent of Shoe and Leather Gazette, Mr. Arthur L. Evans, The Shoeman, Mr. Charles F. Cahill, United Shoe Machinery Company, Hood Rubber Company, Bliss Shoe Com- pany, American Hide and Leather Com- pany, Regal Shoe Company, the publishers of Hide and Leather, American Shoemaking, Shoe Repairing, Boot and Shoe Recorder, The Weekly Bulletin, and the New York Leather Belting Company. -
ALLEN EDMONDS INTRODUCES NEW STYLES for FALL One New Collection, Plus Additions to Casual, Weekend, and Boot Lines
FOR IMMEDIATE RELEASE Images Available Contact: Colin Hall Images can be downloaded from Office: 262-235-6672 http://www.winsbyinc.com/ae/pr/fallline_pr.html [email protected] through December 2010 ALLEN EDMONDS INTRODUCES NEW STYLES FOR FALL One New Collection, plus Additions to Casual, Weekend, and Boot Lines Port Washington, WI (August 26, 2010)—Allen Edmonds is introducing a new collection for fall 2010—the Dress Orthotics Collection—plus new styles that enhance existing collections. With the new Dress Orthotics Collection, men can enjoy the comfort of orthotics without sacrificing style. “Allen Edmonds customers continually ask us to combine particular features with the fashionable styles they expect from their Allen Edmonds shoes,” notes Colin Hall, chief marketing officer at Allen Edmonds. “We answered their requests this season with the Dress Orthotics Collection.” Just What the Doctor Ordered The Dress Orthotics Collection, new for fall, combines the very best features of Allen Edmonds classic shoes with convenient removable footbeds. This allows you to insert your own orthotic insoles for a custom fit. And even if you don’t have custom orthotics, the footbeds add a layer of comfort for all-day wear. No longer do you have to sacrifice style for comfort. The Parliament is a six eyelet dress lace-up with flowing perforation detail and is available in black calf and saddle brown calf. The Benton is a classic cap- toe blucher lace-up available in black calf and chili burnished calf. The Larkin is a penny loafer slip-on that is constructed using a 270° welt for a narrower heel.