Introduction
Total Page:16
File Type:pdf, Size:1020Kb
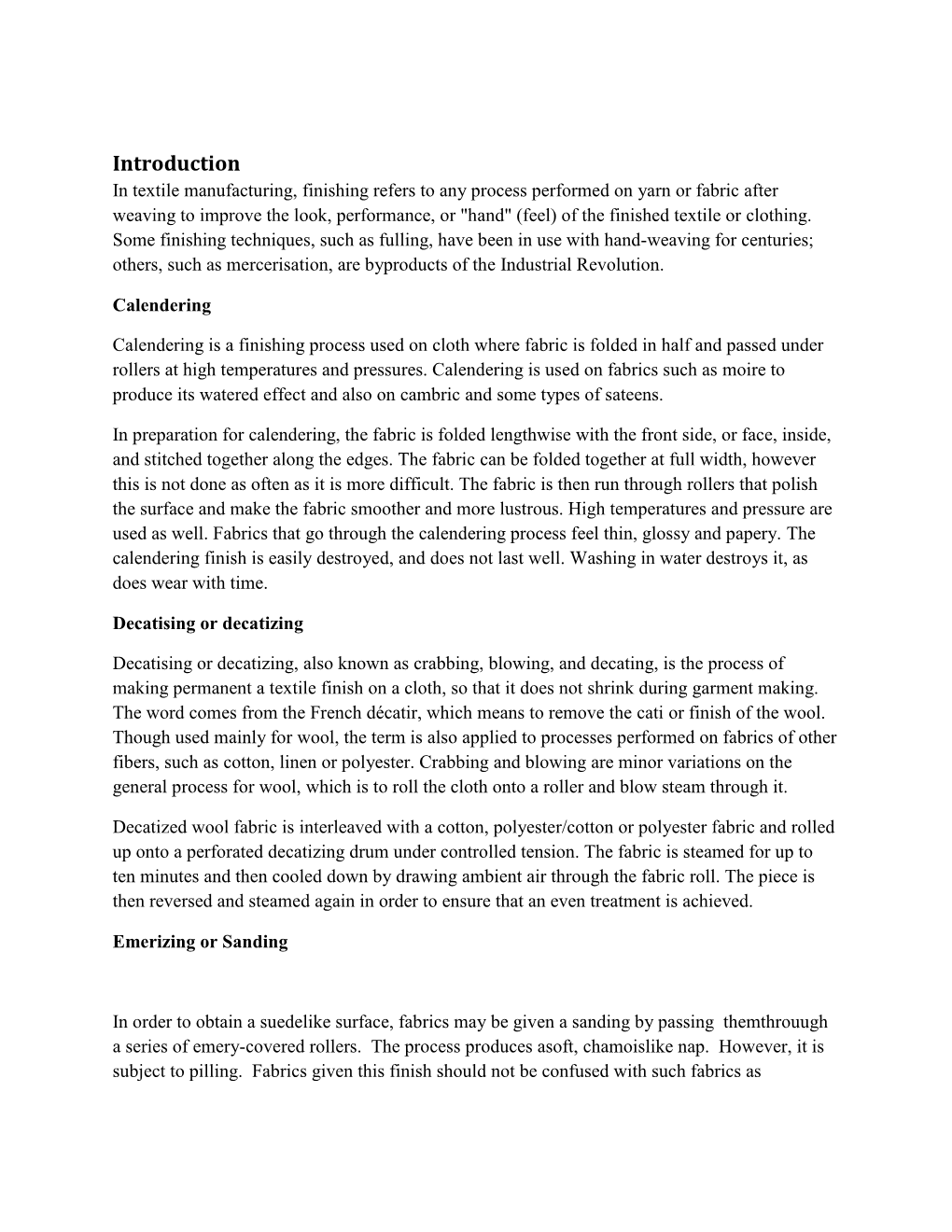
Load more
Recommended publications
-
Functional Textile Technologies Spring 2021 Power up Your Textiles with Heiq’S High-Performance Technologies
Functional Textile Technologies Spring 2021 Power up your textiles with HeiQ’s high-performance technologies HeiQ Smart Temp – Intelligent thermoregulation Article No. Product Name Description Properties Application Fiber Type Chemical Basis Charge / Form Provides enhanced thermal Durable dynamic evapo- Exhaust & pad All Special hydro functiona- Nonionic / comfort, keeps moisture from ration and cooling effect (1-4% w.o.f.) lized copolymer Liquid 17907 HeiQ Adaptive AC-06 accumulating between fabric adjusted according to and the skin tem- perature. Overall enhanced performance Provides enhanced thermal Durable dynamic evapo- Exhaust & pad Mainly for synthetics, Hydro-functionalized Nonionic / comfort, keeps moisture from ration and cooling effect (1-3% w.o.f.) PES and PES rich fiber resin polymer Liquid 17902 HeiQ Adaptive AC-03 accumulating between fabric adjusted according to blends and the skin temperature Highly effective in enhancing Breakthrough dual-effect Print application All Thermofunctional Nonionic / thermal comfort for a wide technology, combining (20-40 g/m2) polymer, vegetable oil Liquid range of textiles, especially cooling on contact and derived 19602 HeiQ Cool Touch SWS bedding. More than 50% continuous evaporative bio-based materials, in USDA cooling effect, soft hand- certification in process. feel, good hydrophilicity Application recommendations Polyester (PES) – HeiQ Adaptive AC-06 in combination with: Article No. Product Name Description Properties Application Fiber Type Chemical Basis Charge / Form Soft/cool touch with wicking, Resistant to mild washing, Exhaust & pad PES & blends, also on Ethoxylated carboxylic Nonionic / antistatic and soil release pro- no yellowing if separately (1-6% w.o.f.) polyamide acid Liquid emulsion 16205 HeiQ Hydro SHF perties on synthetics applied, color intensifica- tion in print pastes 8 Polyamide (PA) – HeiQ Adaptive AC-06 in combination with: Article No. -
Lenzing Modal ® and Lenzing Viscose ® Pre-Treatmet, Dyeing
LENZING MODAL® AND LENZING VISCOSE® PRE-TREATMET, DYEING,FINISHING DYEING / FINISHING PROCESSING GUIDELINES DYEING / FINISHING 1 General Instructions for Pre-treatment As with all textiles made of cellulose fibers the best results - luster / drape / handle - are achieved when all wet processes are conducted with low levels of pressure and stretching. This is also true of Lenzing Modal® fibers which are however considerably less sensitive than normal viscose fibers 1.1 Relaxation Hot water shrinkage of yarns and fabrics Processing Condition Fiber Origin carded Lenzing Viscose® Lenzing Modal® cotton Yarn / twisted yarn shrinkage (hot water 96°C) Fiber fineness Ring yarn Nm 50 -2.0/-2.5 -1.5/-2.0 -1.5/-2.0 Ring yarn Nm 70 -3.0 -2.0 -2.0 Rotor yarn Nm 50 -2.5 -2.5 Rotor yarn Nm 40 -2.5/-3.0 -1.5/-2.0 Plied yarn (ring) Nm 40/2 -3.5/-4.0 -2.5/-3.0 Fabrics (warp shrinkage wash 60°C) Fabrics made of Nm 50 (Ring) Fiber titre 1.7 dtex desized -3.0 -1.5 finished + sanforized -1.0 -0.5 (continuously) Fabrics made of Nm 50 (Ring) Fiber titre 1.3 dtex desized -5.5 -3.0 finished + sanforized -1.5 -0.5 (continuously) Fabrics made of Nm 70 (Ring) Fiber titre 1.7 dtex desized -12.0 -8.0 -6.0 finished + sanforized -1.5 -1.0 +/-0 (discontinuously) PROCESSING - 2 / 16 - GUIDELINES DYEING / FINISHING The fabric tensions at the preliminary textile stages should be reduced during the pre-treatment stage, i.e. -
The Effect of Air, Ar and O2 Plasmas on the Electrical Resistivity And
fibers Article The Effect of Air, Ar and O2 Plasmas on the Electrical Resistivity and Hand-Feel Properties of Polyester/Cotton Blend Fabric Baye Berhanu Yilma 1,2, Joern Felix Luebben 2,* and Govindan Nalankilli 1 1 Ethiopian Institute of Textile and Fashion Technology [EiTEX], Bahir Dar University, Bahir Dar 644, Ethiopia; [email protected] (B.B.Y.); [email protected] (G.N.) 2 Material and Process Engineering [MPE], Albstadt-Sigmaringen University, 72458 Albstadt, Germany * Correspondence: [email protected]; Tel.: +49-(0)-7571-732-9565 Received: 20 December 2019; Accepted: 13 February 2020; Published: 24 February 2020 Abstract: The conventional chemical-based antistatic agents possess ecological and technological drawbacks, such as altering the bulk characteristics, flammability, and toxicity, but not the cost effective process. Recently, using conductive metal fibers in the woven structure also affects the mechanical properties of the fabric. To overcome these challenges, plasma treatment needs to be quite an effective method. In this study, polyester/cotton (P/C), 65/35%, blend fabric was treated in a vacuum-plasma-chamber using air, argon and oxygen. The electro-physical property of the samples were evaluated by measuring the surface and volume resistivities (ρs, ρv) using textile electrode Tera Ohmmeter (TO-3). Textile Softness Analyzer (TSA) has also been used to investigate hand-feel properties of the fabric. After treatment, the results revealed that the surface resistivity was reduced by 35.5% in the case of O2, 27.3% for air and 18.4% for Ar, and also volume resistivity was decreased by 40.9%, 20.3% and 20% after O2, air and Ar-plasma, respectively, whereas hand-feel properties are slightly affected at a higher power level and treatment time. -
26. Dry Finishing of Wool Fabrics
26. Dry Finishing of Wool Fabrics Mike Pailthorpe Learning objectives By the end of this lecture, you should be able to: • Describe the various methods that are available for the drying of wool fabrics. • Understand the need for conditioning wool fabrics after drying. • Outline the methods used in the brushing of wool fabrics. • Describe the process of shearing. • Outline the principles involved in the decatising of wool fabrics. • Explain the need for the steaming of wool fabrics. Key terms and concepts Drying, conditioning, raising, shearing, singeing, pressing, decatising, steaming, perching. Introduction The so called dry finishing processes for wool fabrics follow on after hydroextraction and scutching, beginning with drying. One of the objects in wool fabric finishing is to dry the fabric only once, thereby making substantial energy savings. Drying is the process of removing water from wool textiles via the application of heat energy. The three methods of transferring heat energy from one object to another are conduction, convection and radiation. However, for a variety of reasons, convection dryers are preferred for wool fabrics, with the stenter being the most widely used drying machine. After drying the wool fabrics must be conditioned to a regain of 14-16% before further processing. Depending upon the finish required, the wool fabrics may then either be shorn to remove surface fibres or brushed to create a pile of surface fibres. The brushed pile may be shorn to cut the pile fibres to a uniform height or to achieve a sculptured pattern. The wool fabrics are then pressed using either flat, rotary or belt presses to achieve the desired appearance, lustre and handle characteristics. -
Textile Knowledge of Selected Salespersonnel
TEXTILE KNOWLEDGE OF SELECTED SALESPERSONNEL By MICHELE ANN CALDWELL Bachelor of Science .University of California - Davis Davis, California . 1975 Submitted to the Faculty of the Graduate College of the Oklahoma State University in partial fulfillment of the requirements for the Degree of MASTER OF SCIENCE July, 1977 TEXTILE KNOWLEDGE OF SELECTED SALES PERSONNEL Thesis Approved: 989120 ii ACKNOWLEDGMENTS I would like to express appreciation to my major adviser, Dr. Grovalynn Sisler, for her assistance and advice in directing the thesis. I also wish to express thanks to the members of my committee, Dr. Lavonne Matern and Dr. Margaret Callsen, for their encouragement and suggestions. In addition, thanks are extended to Dr. Nick Stinnett for his advice with the statistical analysis of the study, to the man agers of the participating stores, and to all of the salespeople who participated in the study. Their approval and cooperation made the study possible. To my friends and family, I wish to express my gratitude and appreciation for their friendship and encouragement during my graduate studies. I wish to express a special note of thanks to my parents, Mr. and Mrs. Harold W. Caldwell, for their continuing patience, under standing, encouragement and strong support. iii TABLE OF CONTENTS Chapter Page I. INTRODUCTION 1 Purpose and Objectives 3 Hypotheses • . 3 Definition of Terms 3 Procedure 4 Limitations • . 5 Organization of the Study 5 II. REVIEW OF LITERATURE 7 Textile Market . 7 Textile Fibers . 9 Fabric Construction 14 Textile Finishes . 16 Textile Care Knowledge • . 18 Consumerism and the Salesperson 20 Summary . 22 III. METHOD AND PROCEDURE 24 Description of Sample 24 Development of Instrument 25 Collection of Data . -
Sanmar Glossary of Terms August 2019 1X1 Rib Knit. This Narrow Rib
SanMar Glossary of Terms August 2019 1x1 Rib Knit. This narrow rib has a soft, fine hand and retains its slim fit. 2x1 Rib Knit. Textured rib knit with a comfortable stretch—made to be worn alone or layered. 2-Way Zipper. A zipper with two zipper pulls so the garment can be unzipped from either direction. 3-in-1 Jacket. A jacket that consists of two jacket layers that zip together. You can wear either jacket layer separately, or zip them together for extra warmth and weather protection. 4-Needle Stitching. A finish commonly used on a sleeve or bottom hem that uses four needles to create parallel rows of visible stitching, giving the garment a cleaner, more finished look, as well as adding durability. 4-Way Stretch. A fabric that stretches both on the crosswise and lengthwise grains of the fabric. Also called mechanical stretch, except mechanical stretch doesn’t use spandex or other stretch yarns. Air Jet Yarn. A type of open-end spinning that uses a stationary tube in which jets of air are directed to cause fibers to twist thereby forming a yarn. This process definitely influences the soft hand feel of the fabric while maintaining excellent resistance to pilling. Airlume Combed and Ring Spun Cotton (BELLA+CANVAS). 100% Airlume combed and ring spun cotton, 32 singles. BELLA+CANVAS removes 2.5x more impurities than standard ring spun cotton and uses only long cotton staples, which means there are less stray fibers when the yarn is spun, resulting in a smoother print surface. All-Weather Microfiber. -
TEXTILE DYEING and PRINTING B.A/ B.Sc
TEXTILE DYEING AND PRINTING B.A/ B.Sc. / B.Com. Part -1 -2016 Scheme : B.Sc. B.A./ B.Com. Nomenclature Dur. Max./Min. Marks Max./Min. Marks No. of Periods Paper-I Weaving and Mkt. 3 hrs 75 27 65 24 3 Paper-II Designing & Dyeing 3 hrs 75 27 65 24 3 Practical 4 hrs 75 27 70 26 4/ Batch PAPER- 1 (Weaving and Marketing) Duration: 3 hrs Max. Marks: (Sc)-75/(Arts/Comm.)-65 Note: The question paper will contain three sections as under- Section-A: One compulsory question with 10 parts, having 2 parts from each unit, short answer in 20 words for each part. 10 (Sc.)/05 (Arts/Comm.) Section-B: 10 questions, 2 questions from each unit, 5 questions to be attempted, taking one from each unit, answer approximately in 250 words. 35 (Sc.)/35 (Arts/Comm.) Section-C: 04 questions (question may have sub division) covering all units but not more than one question from each unit, descriptive type answer in about 500 words, 2 questions to be attempted. 30 (Sc.)/25 (Arts/Comm.) UNIT-1 Introduction to Textile Classification of textile fibers General properties of textile fibers Identification of textile fibers UNIT-2 Natural Fibers-Manufacture, Chemical composition, general properties & Flowchart-cotton, silk, wool Manmade Fibers- Manufacture, Chemical composition, general properties & Flowchart - Rayon, Nylon, Polyester UNIT-3 Preparatory processes (a) Scouring (b) Bleaching (i) bleaching of cotton, silk, nylon (ii) Optical bleaching agents (c) Desizing (i) Acid desizing ( ii) Rot steeping ( iii) enzymatic desizing (d) Singing (i) gas singing (ii) Plate signing (iii) roller singing (e) Mercerization-Historical significance & introduction Action of Caustic Soda on Cotton fibre, Nature of Change occurring in cotton fibres UNIT-4 (a) Introduction to weaving Terms used in weaving Loom & it’s parts Elementary weaves and their derivatives Plain weave- Rib, Basket Twill weave-Right hand & Left hand Satin weaves- Satin & sateen (b) Weave Representation : Weaving plan,Various Drafts and Peg Plans UNIT-5 Meaning, nature& scope of marketing Role & importance of marketing in modern economy. -
SILVADUR™ Application Guidelines
Nutrition & Biosciences SILVADUR™ FLEX Application Guidelines Pad it. Exhaust it. SILVADUR™ Antimicrobial Means Easy Application. First Time. Every Time. May 07, 2020 SILVADUR™ Antimicrobial is a liquid formulation that can be easily applied to any natural or synthetic fiber using most industry standard equipment for pad or exhaust methods. Simply defined, the pad process involves passing a fabric through a bath containing an antimicrobial product and water. The fabric is then dried to remove any excess water, leaving the antimicrobial product on the fabric. The exhaust method, on the other hand, is a batch process where fabric, garment, or yarn either in a static or dynamic set up is soaked in a circulated or non-circulated bath containing the antimicrobial product and water, and the antimicrobial product is transferred to the textile. Any excess water in the fabric is then removed and the fabric is dried, leaving the antimicrobial product on the fabric. SILVADUR™ antimicrobial efficacy and wash durability performance when applied on a variety of textiles using either pad or exhaust methods has been extensively validated globally using internationally accepted standard methods. etc. SILVADUR™ Application Level SILVADUR™ products can be applied using most industry standard conditions. If co-application of SILVADUR and auxiliary finishing chemicals is required, compatibility of the application solution should be determined in the laboratory prior to production-scale trials. It is highly recommended that SILVADUR™ be applied prior to any sacrificial, non-durable treatments during chemical finishing (e.g., before repellents, moisture wicking additives, softeners, etc.). Complete rinsing and neutralization of fabric prior to the addition of SILVADUR™ product is required in order to achieve the highest durability of the final silver-polymer system. -
Denim – Construction and Common Terminology
Denim – Construction and Common Terminology Denim Construction Denim is made from rugged tightly woven twill, in which the weft passes under two or more warp threads. Lengthwise, yarns are dyed with indigo or blue dye; horizontal yarns remain white. The yarns have a very strong twist to make them more durable, but this also affects the denim’s color. The yarns are twisted so tightly that the indigo dye usually colors only the surface, leaving the yarns center white. The blue strands become the threads that show on the outside of your denim, and the white are the ones that make the inside of your denim look white. This produces the familiar diagonal ribbing identifiable on the reverse of the fabric. Through wear, the indigo yarn surface gives way, exposing the white yarn underneath which causes denim to fade. Jeans are basic 5 pockets pants, or trousers, made from denim. The word comes from the name of a sturdy fabric called serge, originally made in Nimes, France. Originally called serge de Nimes (fabric of Nimes), the name was soon shortened to denim (de Nimes). Denim was traditionally colored blue with natural indigo dye to Black denim make blue Jeans, though “jean” then denoted a different, lighter cotton textile; the contemporary use of jean comes from the French word for Genoa, Italy, where the first denim trousers were made. Jeans transcend age, economic and style barriers. Washes, embellishments, leg openings and labels fluctuate with fashion whims, but jeans themselves have reached iconic status. Cross hatch denim Common terminology used in Denim fabric construction and processing ANTI-TWIST is a step in the finishing process, before sanforization, that corrects denim’s natural tendency to twist in the direction of the diagonal twill weaves. -
Appendix I Introductory Notes to the List in Annex Ii
APPENDIX I INTRODUCTORY NOTES TO THE LIST IN ANNEX II Note 1 — General introduction This Annex lays down under which products shall be considered to originate in the beneficiary country concerned. There are four different types of rule, which vary according to the product: (a) through working or processing a maximum content of non-originating materials is not exceeded; (b) through working or processing the 4-digit Harmonized System heading or 6-digit Harmonized System sub-heading of the manufactured products becomes different from the 4-digit Harmonized System heading or 6-digit sub-heading respectively of the materials used; (c) a specific working and processing operation is carried out; (d) working or processing is carried out on certain wholly obtained materials. Note 2 — The structure of the list 2.1 Columns 1 and 2 describe the product obtained. Column 1 gives the chapter number, 4-digit heading or 6-digit sub-heading number used in the Harmonized System, as appropriate. Column 2 gives the description of goods used in that system for that heading or chapter. For each entry in columns 1 and 2, subject to Note 2.4, one or more rules ("qualifying operations") are set out in column 3. These qualifying operations concern only non-originating materials. Where, in some cases, the entry in column 1 is preceded by "ex", this signifies that the rule in column 3 applies only to the part of that heading as described in column 2. 2.2 Where several Harmonized System headings or sub-headings are grouped together in column 1 or a chapter number is given and the description of products in column 2 is therefore given in general terms, the adjacent rule in column 3 applies to all products which, under the Harmonized System, are classified in headings of the chapter or in any of the headings or sub-headings grouped together in column 1. -
1 II-B/1.2/494 OUTPUT O.5.1: Documented Analysis in Each
ENPI Project Number II-B/1.2/494 OUTPUT O.5.1: Documented analysis in each subsector. Identification of manufacturing processes which are causing problems in each subsector and quantification of environmental impacts. OUTPUT O.5.2: Documented analysis in environmental legislation in each country. OUTPUT O.5.3: Documented analysis of entities specialized in textile. SUSTEXNET - SUITANABLE TEXTILE MEDITERRANEAN NETWORK 1 EXECUTIVE SUMMARY Output 5.1 (Documented analysis in each subsector - manufacturing processes and problems), Output 5.2 (Documented analysis in environmental legislation) and Output 5.3 (Documented analysis of entities specialized in textile) have been achieved at the same time and with the same work done by all partners. Each couple of partners from each country -Spain, Italy, Tunisia and Egypt- were committed to develop an accurate analysis of the main technical/economic/social problems of its own textile sector, in order to detect technological / economic / environmental / social gaps to be covered along the value chain at local, regional and multi-country level. The most useful method to reach these outputs was a whole analysis per country that included all the issues to be considered. This analysis was structured as follows: A.5.1. METHODOLOGIES FOR FURTHER DIAGNOSTICS IN SPINNING/WEAVING PROCESSES. A.5.2. METHODOLOGIES FOR FURTHER DIAGNOSTICS IN DYEING/PRINTING/FINISHING PROCESSES. A.5.3. METHODOLOGIES FOR FURTHER DIAGNOSTICS IN LOGISTIC AND DISTRIBUTION NETWORKS (These chapters generated O.5.1). A5.4. STUDY OF ENVIRONMENTAL LEGISLATION IN EACH AREA AND ESTABLISHMENT OF COMMON VALUES OF ENVIRONMENTAL IMPACT (These chapter generated O.5.2). A5.5. STUDY OF EDUCATION, TRAINING AND TECHNOLOGICAL ENTITIES SPECIALIZED IN TEXTILE FIELDS IN EACH AREA, AND METHODOLOGIES FOR OPTIMIZING/INCREASE WORKING FORCE RESOURCES (These chapter generated O.5.3). -
Clean Trends in Textile Wet Processing Dalia F
Science ile & Ibrahim, J Textile Sci Eng 2012, 2:5 xt e E T n f g i DOI: 10.4172/2165-8064.1000e106 o n l e a e n r r i n u Journal of Textile Science & Engineering g o J ISSN: 2165-8064 Editorial OpenOpen Access Access Clean Trends in Textile Wet Processing Dalia F. Ibrahim* Faculty of Applied Arts, Helwan University, Cairo, Egypt Textile industries are facing a challenging condition in the field of quality and productivity, due to the globalization of the world market. The highly competitive atmosphere and as the ecological parameters becoming more stringent, it becomes the prime concern of the textile processor to be conscious about quality and ecology. Again the guidelines for the textile processing industries by the pollution control boards create concern over the environment-friendliness of the processes, making it essential for innovations and changes in the processes [1]. Textile wet processing, is consider as a big and important sector in textile industry, with a wide range of procedures, which affect the final product appearance and quality. Wet processing occurs at various stages in the creation of textiles, as shown in Figure 1. This is the most widely used wet processing flow-chart on the Figure 2 contemporary textile industry. As textile industry is searching for innovative production techniques to improve the product quality, liquids and gaseous media. With reference to the properties of human as well as society requires new finishing techniques working in ear, high frequency inaudible oscillations are ultrasonic or supersonic. environmental respect [2]. In other words, while the normal range of human hearing is in between 16 Hz and 16 kHz, ultrasonic frequencies lie between 20 kHz and 500 Through this review article, we focus on the most innovated trends MHz.