Oxfam America
Total Page:16
File Type:pdf, Size:1020Kb
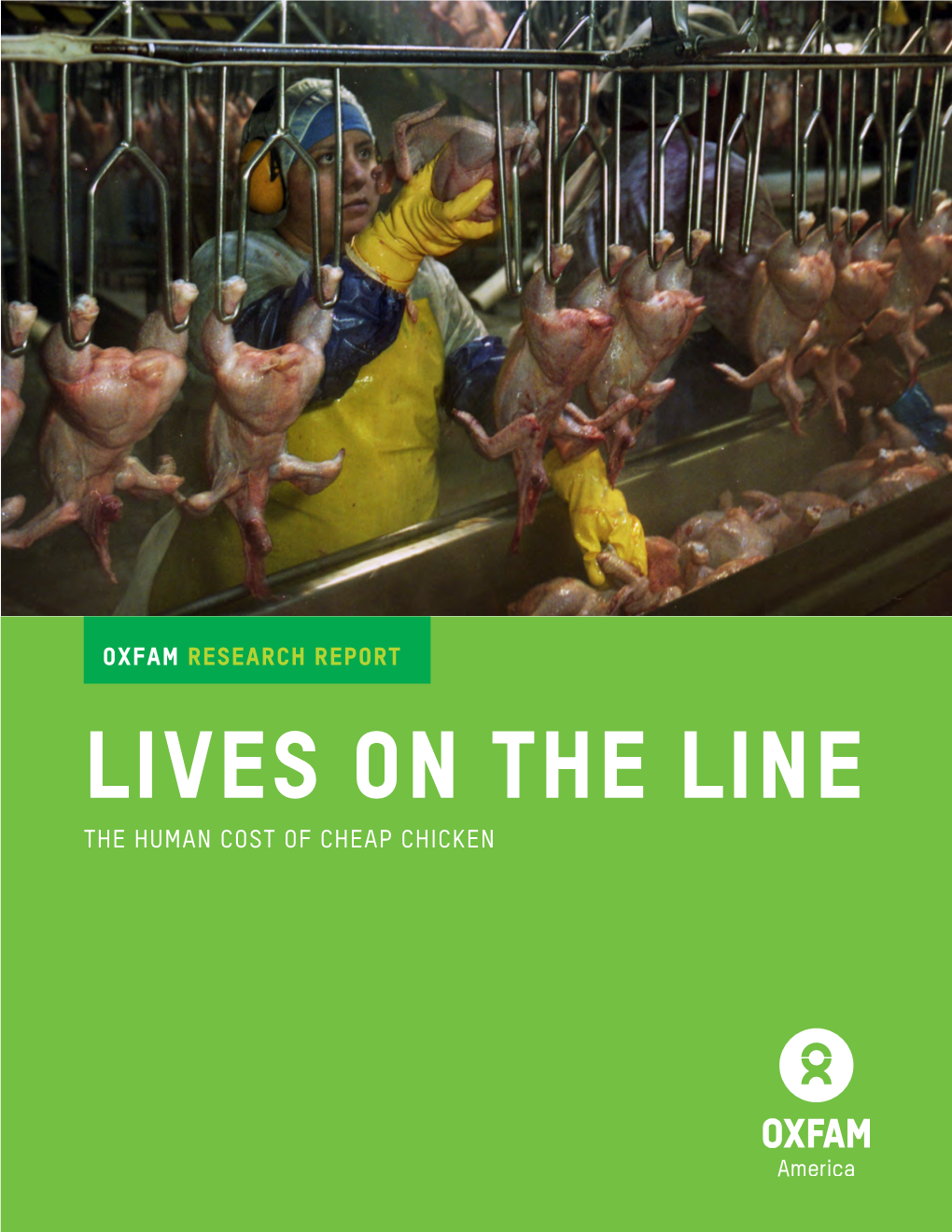
Load more
Recommended publications
-
Chegginhouse-19.Pdf
CHICKENThe orThe “LEGENDARY WINGS” egg® “AWARD WINNING BREAKFAST”e “AFFORDABLE DINNERS” 24 open HOURS in season in drinks old fashioned milkshake 5.49 with whipped cream & cherry choose chocolate, vanilla, b&w, strawberry, SERVING 0reo© or ask about the shake of the day! THE MASSES make it a malted .29 root beer float 4.29 ruby red grapefruit, BREAKFAST, iced tea 2.79 apple, tomato or cranberry (unsweetened, sweet or raspberry) juices 2.29/3.29 LUNCH, Sodas, lemonade, whole or skim milk 2.29/3.29 iced tea, hot tea chocolate milk 2.49/3.49 coffee and iced coffee DINNER & 2.79 are bottomless! LATE NIGHT 100% Colombian Coffee 2.59 flavorize your soda .29 hazelnut Coffee 2.79 (chocolate, cherry, vanilla, strawberry) FARE SINCE iced coffee- tall glass of ice cold Arnold Palmer-fresh squeezed lemonade and iced tea (sweet or unsweet) 3.49 100% Columbian Coffee 2.99 1991 flavorize (caramel, hazelnut, French vanilla) .29 fresh squeezed lemonade 3.49 hot tea 2.29, green tea 2.49 fresh squeezed 0J 2.79/3.79 hot cocoa 2.29 Breakfast served any time! Add A Pancake omelets For $2.29 If you want to make an omelet you gotta break some eggs…3 of 'em grade-A extra large, served with home fries and toast new Pierogi Omelet mashed potatoes, onion, bacon, cheddar, served with a side of sour cream 9.99 Midwestern Omelet onion, green pepper, country ham new The Lumberjack Omelet fried chicken tenders, bacon and cheddar cheese 9.59 and pepper jack cheese, topped with country sausage gravy, served with a buttermilk biscuit 10.99 buffalize it! choose one of our -
March 17, 2018 Supplement to IFT Publications
MWM1 March 17, 2018 www.MidwestMarketer.com Supplement to IFT Publications Cattle gather in the mist on a Jasper County, Iowa, farm. Photo submitted by Tim Perry MWM2 2 www.MidwestMarketer.com / March 17, 2018 MIDWEST MARKET REPORT A Pox On This Column Weekly Avg. Price Comparisons Source: USDA, along with the Iowa man in Wahoo, Neb., March 10, 2018 and Missouri Departments of Agriculture said he ate all the eggs A he could. He felt it Iowa South Dakota was his contribution to beef FEEDER STEERS Med/Lg 1 March 12 FEEDER STEERS Med/Lg 1 March 12 sales; every egg he ate was one Wt Range Avg. Wt Price Range Avg. Price Wt Range Avg. Wt Price Range Avg. Price 374-398 381 204.00-215.00 210.13 408-437 423 199.00-202.00 200.55 less chicken! 411-440 424 190.00-213.00 203.64 518-524 523 180.00-195.00 190.38 569-599 583 172.00-205.50 194.17 People take chickens per- 456-499 482 193.00-213.50 200.67 608-649 631 166.00-184.50 173.39 500-548 523 183.00-209.50 193.60 651-697 680 157.50-177.50 169.09 sonally. My brother, Bob, had 555-598 578 177.50-196.00 186.75 700-749 734 152.00-162.50 155.55 633-638 637 168.00-172.00 170.00 750-797 778 139.00-156.50 148.26 a rooster named Oscar. They 668-692 678 158.00-167.25 162.14 801-845 822 135.50-153.50 146.46 hated each other! 700-740 721 148.25-164.00 155.48 852-897 871 127.00-147.25 138.96 753-798 776 137.50-157.00 149.87 901-949 926 130.25-143.00 139.15 Lots of kids like Big Bird 803-849 821 131.00-148.00 143.06 951-994 973 130.00-135.00 132.33 on Sesame Street. -
Specialty Foods Catalog
SPECIALTY FOODS CATALOG 1 Prices Subject to Change at Any Time Table of Contents 406 Market Place is pleased to be able to provide Specialty Food items to meet the ever-changing demands of your customers and to bring new and exciting products to your kitchen and menu. From Alligator to Zabutons we can source it for you. All Specialty items are special order, Monday – Tuesday for Delivery by Thursday – Saturday. Allow at least 4 days turn around. BISON …………………………………………………………………Page 3 ELK/VENISON……………………………………………………….Page 4 WILD BOAR…………………………………………………………..Page 5 POULTRY……………………………………………………………..Page 6 SALAMI ….……………………………………………………………Page 7 SAUSAGES …………………………………………………………..Page 8 PRODUCE……………………………………………………………..Page 9 RETAIL…………………………………………………………………Page 10 Abbreviations and Meanings: (1-2, 10#) = Product Weight Range, Case Size Red Price = Sale Item 2 Prices Subject to Change at Any Time Bison - North American Free Range, USDA Inspected and Humanely Raised. A healthy option, low-cholesterol, sweet to the taste sure to enhance any menu. Custom cuts available upon request. North American Bison – Primals (Primal Weight, Case Weight) Ribeye Boneless (8-10#, 30#) $21 0024246 Tenderloin Cow (5-6#, 16#) $25 0024269 Chuck (18-20#, 40#) $14 0024209 New York Strip Loin (5-6#, 18#) $20 0024232 Flank Steak (35#) $14 0024219 Short Ribs B/I (8pc/4pk 30#) $9 0024254 North American Bison - Portion Cuts Tomahawk Rib Chop 20-28oz/14 piece $28 0024148 Porterhouse Steak (16oz, 10#) $27 0024046 NY Strip Loin (8,10, 12oz, 10#) $26 0024030 Top Sirloin Steak (8,10, 12oz, 10#) $26 0024071 Osso Bucco 1” (20#) $14 0024032 Stew Meat Diced (2/5#) $13 0024059 3 Prices Subject to Change at Any Time Elk & Venison – Sourced from New Zealand farm raised and sustainable. -
Ml-IIL & BREEZE
• Ml-IIL & BREEZE • • • • -J Volume 76 March 25, 1939 Number 6 can young folks get started farming for them selves? The answer to this question is what so many o{ our young farm people are searching for How Some today. of them have become discouraged. Too often we hear, "A young man can't get started farm ing today as he could years ago." Perhaps the question can't be answered to the satisfac tion of all of us. But we can locate the principal drawbacks to beginner farmers today and point out the necessities to ' their successful set-up. What is. even more valuable, we can find farmers who have started in- recent years, have stuck with it, and will tell you the important reasons why they succeeded. What did a young man or a young couple need in the way of farming equipment when they started 30 or more years ago? According to information gleaned from our elders, the young man worked by the month, or worked for his father, until he had accumulated the worth or owner ship of a team of horses, harness and a wagon. Then if he could borrow or buy enough horse-drawn machinery he could rent a small farm and [Continued on Page 19] E. E. Witt bought a few stock cows when he started farming. He uses a Milking Shorthorn bull and milks several of the cows. He raises roughage and groin and feeds hoy at this open bunk, with the stocks as a windbreak, This Newfoundland dog, top, reduces the rabbit population and helps with handling livestock. -
RSA 2006 Restaurant Guide Schneier & Cooper
RSA 2006 Restaurant Guide 2006 Restaurant RSA Schneier & Cooper RestaurantRestaurant GuideGuide Bruce Schneier & Karen Cooper RSA Conference 2006 McEnery Convention Center • San José, CA Codes Used in this Guide Distance Price A Short walk $ Cheap B Walking distance $$ Reasonable C Car required $$$ Expensive D Long car ride $$$$ Very expensive E In another city F On another continent Codes AT Afternoon Tea LL Open Late (11 pm) B Breakfast LLL Open Very Late (12:30 am) BW Beer and Wine Only LM Live Music CO Cash Only NO No Alcohol D Dinner NR No Reservations DA Dancing OS Outdoor Seating DL Delivers R Romantic FB Full Bar RE Reservations Essential GG Good for Groups RL Reservations Recommended for Large Parties HWQ High Weirdness Quotient RR Reservations Recommended IWL Impressive Wine List TO Takeout KF Kid Friendly TOO Takeout Only L Lunch RSA 2006 Restaurant Guide 13–17 February 2006 McEnery Convention Center San José, California Bruce Schneier and Karen Cooper Guide written by Bruce Schneier and Karen Cooper Cover Art: Geri Sullivan Copyediting and Proofreading: Beth Friedman Design and Layout: Beth Friedman and Geri Sullivan Copyright 2006 Bruce Schneier and Karen Cooper Table of Contents Welcome Introduction Using the Guide ............................................................................... 2 Hours ................................................................................................ 3 Why Us?............................................................................................ 3 What We Missed .............................................................................. -
Will Plant-Based Proteins Brewed in Bioreactors Save the Planet?
BUSINESS TECHNOLOGY The Austrian family business Fleischlos (“Meatless”) grows king oyster mushrooms and turns them into sausages and other products that taste like meat, but are From Lab entirely plant-based. to Fork Will plant-based proteins brewed in bioreactors save the planet? by Andrew Standen-Raz o the late chef Anthony “We know from retailers like Spar that Bourdain, “Life with- 80% of the veggie products are bought by out veal stock, pork fat, meat-eaters who want variety,” confirms sausage, organ meat, Felix Hnat, an environmental economist demi-glace, or even and chairman of the Vegan Society Austria stinky cheese is not a (VGÖ). Plant-based familiar favorites are life worth living.” drawing in omnivorous “flexitarians” Vegetarians, he wrote in Kitchen Confi- tempted by ice cream, fish and chips, fried dential, “are the enemy of everything good chicken, scallops and even foie gras – Tand decent in the human spirit, an affront to all made with vegetable protein. Billionaires all I stand for – the pure enjoyment of food.” like Bill Gates and Richard Branson are Bourdain was no kinder toward vegans, investors in competing plant-based burg- calling them vegetarians’ “Hezbollah-like ers. Celebrities help, too. The increasingly splinter-faction.” popular “Veganuary” vegan month this In the ’90s, when a veggie plate meant year attracted Jay Z and Beyonce, who soggy courgettes, it was easy for the red lasted 22 days. meat guys to laugh along to Denis Leary’s “Should the methods we invented at the standup routine No Cure for Cancer. start of the Industrial Revolution always be “Eggplant tastes like eggplant, but meat the right answer to everything?” asks tastes like murder. -
CHRISTMAS ORDER FORM Please Help Us Help You This Way the Pies Turn out with That Delightful Freshly- by Ordering Early
Home Entertaining ~ Ideas for the New Year Catering at Christmas can be a tiring business, so theres every reason to make the first weeks of the New Year a little more relaxing by letting ORDER FORM Greens do the work... Please: Perfect pies for your freezer complete your order details How about stocking up the freezer with some of overleaf; Greens famous pies? then tear off this Form and We will supply them to you green - that is with the return it to Greens as filling cooked and the pastry ready to bake in your own soon as possible ~ oven. CHRISTMAS ORDER FORM please help us help you This way the pies turn out with that delightful freshly- by ordering early. baked quality....perfect fillings and deliciously flaky pastry. (Cooking times guidance on the website or Please note the final order date: please ask for our Pies leaflet). SEASONAL FAVOURITES * HOME ENTERTAINING IDEAS With our huge range to choose from, there is some- Thursday December 12th thing for everyone.... If you need any help or advice, Chicken & Mushroom Steak & Kidney Chicken Chasseur Steak & Mushroom we are always happy to help Chicken & Leek Steak & Guinness Chicken Curry Peppered Steak 0118 984 2063 Chicken & Apricot Steak & Stilton Chicken & Asparagus Just Steak Just Chicken Minced Beef & Onion Ham & Chicken Spicy Lamb Greek Lamb Chicken & Vegetable Lamb & Rosemary Garden Vegetable Game 2013 Send it by post (or drop it in) to: Chef-prepared specialities Greens of Pangbourne, For an extra-special change, why not try one of our eady dishes, which can even be prepared in your own 10 Whitchurch Road. -
Agriculture Decisions
AGRICULTURE DECISIONS Volume 61 July - December 2002 Part One (General) Pages 447 - 785 THIS IS A COMPILATION OF DECISIONS ISSUED BY THE SECRETARY OF AGRICULTURE AND THE COURTS PERTAINING TO STATUTES ADMINISTERED BY THE UNITED STATES DEPARTMENT OF AGRICULTURE AGRICULTURE DECISIONS AGRICULTURE DECISIONS is an official publication by the Secretary of Agriculture consisting of decisions and orders issued in adjudicatory administrative proceedings conducted for the Department under various statutes and regulations. Selected court decisions concerning the Department's regulatory programs are also included. The Department is required to publish its rules and regulations in the Federal Register and, therefore, they are not included in AGRICULTURE DECISIONS. Beginning in 1989, AGRICULTURE DECISIONS is comprised of three Parts, each of which is published every six months. Part One is organized alphabetically by statute and contains all decisions and orders other than those pertaining to the Packers and Stockyards Act and the Perishable Agricultural Commodities Act, which are contained in Parts Two and Three, respectively. The published decisions and orders may be cited by giving the volume number, page number and year, e.g., 1 Agric. Dec. 472 (1942). It is unnecessary to cite a decision's docket number, e.g., AWA Docket No. 99-0022, and the use of such references generally indicates that the decision has not been published in AGRICULTURE DECISIONS. Consent decisions entered subsequent to December 31, 1986, are no longer published. However, a list of consent decisions is included. Consent decisions are on file and may be inspected upon request made to the Hearing Clerk, Office of Administrative Law Judges. -
Down the Rabbit Hole – Eatocracy - CNN.Com Blogs
Down the rabbit hole – Eatocracy - CNN.com Blogs Home | Video | NewsPulse | U.S. | World | Politics | Justice | Entertainment | Tech | Health | Living | Travel | Opinion | iReport | Money | Sports Recent Posts 5@5– Chef David Bazirgan Down the rabbit hole February 8th, 2011 Down the rabbit hole 01:15 PM ET Box lunch Rabbit meat is delicious. I wish I didn't know that. Share Vintage Cookbook Vault: Night life eggs Comments (442 comments) Rabbits bond for life. For most, instinct drives them to seek out another creature - Breakfast buffet Permalink usually one of their own kind, but it’s been known to encompass cats, guinea pigs, Coffee klatsch dogs or even birds. They’ll groom, cuddle and grieve palpably upon the other’s Fame Bites - Aubrey Plaza Tweet absence or loss. 5@5 - Jeff Segal Claudette, my nine-ish year old Hotot / dwarf mix (pictured above) is, as I was Podcast – Out to Lunch: Tacos beyond the box and Bell informed by my local rabbit rescue guru, bonded to me. She expresses this via chin Bargain bourbon: Wham, dram, thank you ma'am rubs to shoes I’ve not previously worn around her (rabbits have scent glands with which they mark territory), a distinct drop-off in the bitchy behavior she demonstrates Eatocracy on Twitter follow » to nearly all other humans she’s encountered, and tooth-grinding purrs as I stroke her silken fur. We belong to each other. Down the rabbit hole: why some folks At the same time, I can’t pretend that the most astonishing bite of food I ate in 2009 feel funny eating bunny & others say wasn’t a smoked rabbit kidney. -
Thelandlubbers TM Fresh Oysters - Seasonal (Raw Or Steamed) One Foot In-One Foot out
(954)(954) 584-1637 584-16375 available faxfax (954) (954) 505-3424 505-3424 Dinner Menu all day RusticInn.comRusticInn.com The TM For Appetizers Crab Center Entrées Garlic Crab Central House Specialties TheLandlubbers TM Fresh Oysters - Seasonal (Raw or Steamed) One Foot In-One Foot Out ................................ 38.50 Ribs Better Than a Rib House ................................. 25.50 One half-split lobster, broiled with clam stuffing (contains bacon) Bar-B-Que ribs, one full rack of slow-cooked then grilled just right and basted with 1/2 Doz. ....................... 11.00 Full Doz. .......................22.00 Alaska Queen and a New York Strip Steak (USDA Choice Cut Beef). Served our very own bar-b-que sauce. Served with seasoned fries and fresh corn bread. Top Neck Clams (Raw or Steamed) with parsley buttered potatoes. Surf and Turf for the Crew ................................... 24.50 1/2 Doz. ....................... 9.50 Full Doz. ...................... 19.00 Crab Legs Slow cooked ribs basted with our own bar-b-que sauce and hooked with fresh From the Bering Sea in Alaska “Admirals” PLatter ................... 44.95 grilled Mahi-Mahi (Dolphin) basted with olive oil, garlic and herbs. Fried Calamari ...................................................10.50 and served with parsley buttered New York Strip Steak (USDA Choice Cut Beef) paired Served with seasoned fries and fresh corn bread. Breaded and deep fried rings. potatoes. 52.00 with ONE of the following: 1/2 pound Alaska King crab legs, 1/2 pound Dungeness garlic New York Strip Steak ...........................................28.95 Clams Oreganata ............................................ .11.25 crab cluster or broiled lobster tail. Served with USDA Choice Cut of Beef grilled to perfection and served with saute d onions Whole clam on the half-shell baked with breading and oregano. -
Tastes Like Chicken?
Annals of Improbable Research Tastes Like Chicken? by Joe Staton Museum of Comparative Zoology Harvard University, Cambridge, Massachusetts Photos by A. Kaswell he field of culinary evolution faces one great dilemma: why do most cooked, exotic meats taste like Tcooked Gallus gallus, the domestic chicken?1 It is curious that so many animals have a similar taste. Did each species evolve this trait independently or did they all inherit it from a common ancestor? That is the burning question. Evolutionary Theory: Some Background First, some tasty technical background. The different traits of an organism (its hair or lack thereof, its teeth or lack thereof, its lungs or lack thereof, its taste, its color, etc.) can have distinctly different evolutionary origins. Some of an organism's traits are inherited from many, many, many, many (thousands, or millions, even) generations of ancestors. Other of its traits developed late in the evolutionary history. If you compare the traits of two different kinds of organisms, you may find that: 1. Some of the things they have in common were inherited from a common ancestor; while 2. Other things they have in common were not inherited from any common ancestor— but happened to have A meat counter featuring some of the author's favorites, including turtle, emu and boar. July/August 1998 Vol. 4, No. 4 Special Animal Behavior Issue 5 Annals of Improbable Research developed independently for each organism. Modern evolutionary analysis helps us try to sort out and understand the true origins of all sorts of traits. Here's how you do it. -
Future Directions in the Meat Industry: the Next 50 Years
A M S A H I S T O R I C A L P E R S P E C T I V E Future Directions in the Meat Industry: The Next 50 Years BILL BUCKNER* It is indeed a pleasure to be here at this year’s Reciprocal improving their diet. And the way they often do that is by Meat Conference. I think anyone would be honored to be a incorporating more meat into their diet. In other words, our speaker at an event that celebrates the 50th anniversary of meat industry will be part of the broad effort to raise living the American Meat Science Association’s annual meeting. standards worldwide. I have been asked to dust off my crystal ball and take a In the day to day grind, we sometimes lose sight of the look at the future directions in the meat industry. I hope to role we play in the world economy. We sometimes forget intrigue you about what the next 50 years might be like. that what we do benefits many people around the world– Before man landed on the moon, no one could picture ex- and that we will benefit many, many more in the years ahead. actly what that would look like. But many people thought Along the way, we will be presented with opportunities. To about it. They wondered how it might happen. They thought capture those opportunities, we must create and add more and thought and thought. And one day it came true. Man value. We must continue shifting away from being a com- did walk on the moon.