Ultralow Noise of Quantum-Dot Mode-Locked Lasers
Total Page:16
File Type:pdf, Size:1020Kb
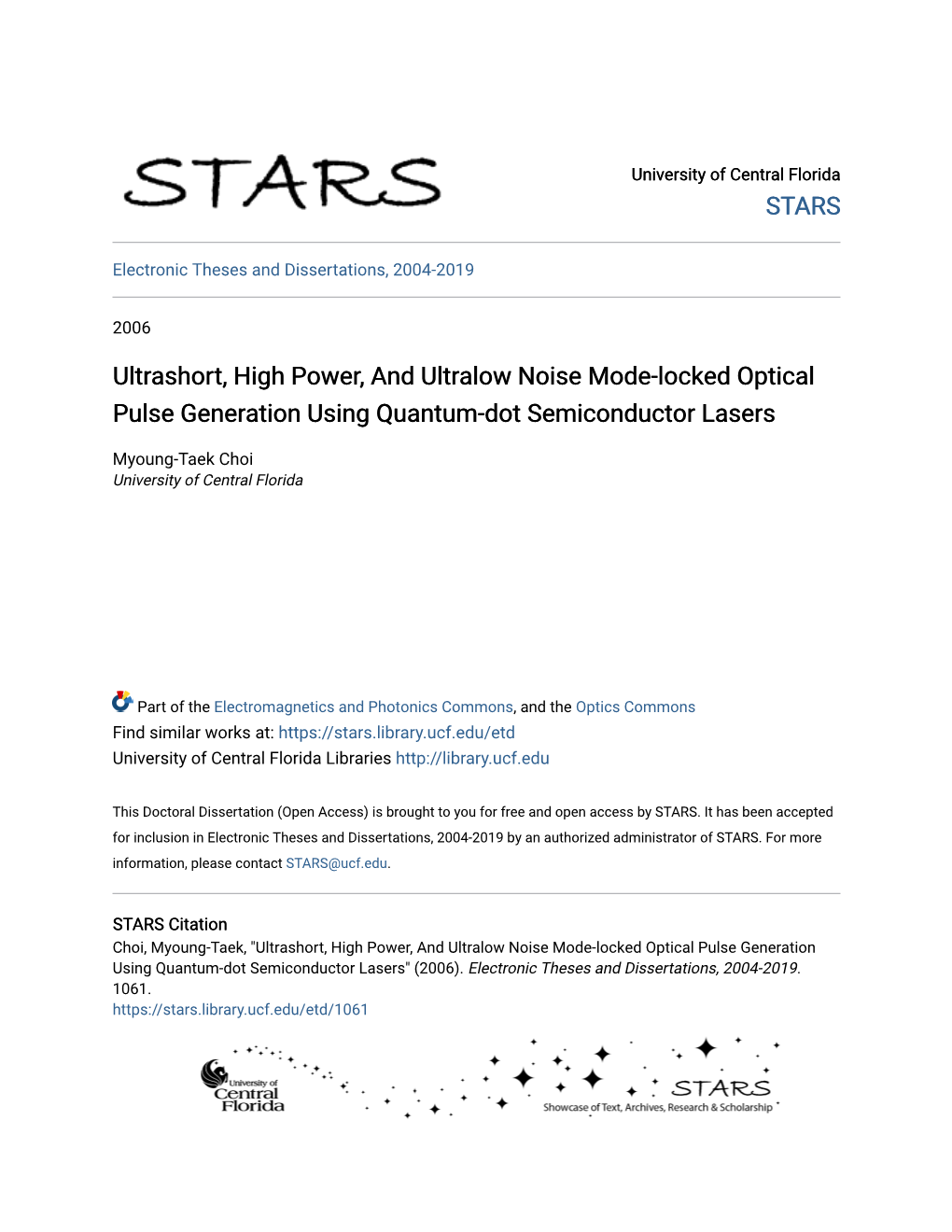
Load more
Recommended publications
-
Laser Linewidth, Frequency Noise and Measurement
Laser Linewidth, Frequency Noise and Measurement WHITEPAPER | MARCH 2021 OPTICAL SENSING Yihong Chen, Hank Blauvelt EMCORE Corporation, Alhambra, CA, USA LASER LINEWIDTH AND FREQUENCY NOISE Frequency Noise Power Spectrum Density SPECTRUM DENSITY Frequency noise power spectrum density reveals detailed information about phase noise of a laser, which is the root Single Frequency Laser and Frequency (phase) cause of laser spectral broadening. In principle, laser line Noise shape can be constructed from frequency noise power Ideally, a single frequency laser operates at single spectrum density although in most cases it can only be frequency with zero linewidth. In a real world, however, a done numerically. Laser linewidth can be extracted. laser has a finite linewidth because of phase fluctuation, Correlation between laser line shape and which causes instantaneous frequency shifted away from frequency noise power spectrum density (ref the central frequency: δν(t) = (1/2π) dφ/dt. [1]) Linewidth Laser linewidth is an important parameter for characterizing the purity of wavelength (frequency) and coherence of a Graphic (Heading 4-Subhead Black) light source. Typically, laser linewidth is defined as Full Width at Half-Maximum (FWHM), or 3 dB bandwidth (SEE FIGURE 1) Direct optical spectrum measurements using a grating Equation (1) is difficult to calculate, but a based optical spectrum analyzer can only measure the simpler expression gives a good approximation laser line shape with resolution down to ~pm range, which (ref [2]) corresponds to GHz level. Indirect linewidth measurement An effective integrated linewidth ∆_ can be found by can be done through self-heterodyne/homodyne technique solving the equation: or measuring frequency noise using frequency discriminator. -
Narrow Line Width Frequency Comb Source Based on an Injection-Locked III-V-On-Silicon Mode-Locked Laser
Narrow line width frequency comb source based on an injection-locked III-V-on-silicon mode-locked laser Sarah Uvin,1;2;∗ Shahram Keyvaninia,3 Francois Lelarge,4 Guang-Hua Duan,4 Bart Kuyken1;2 and Gunther Roelkens1;2 1Photonics Research Group, Department of Information Technology, Ghent University - imec, Sint-Pietersnieuwstraat 41, 9000 Ghent, Belgium 2Center for Nano- and Biophotonics (NB-Photonics), Ghent University, Ghent, Belgium 3Fraunhofer Heinrich-Hertz-Institut Einsteinufer 37 10587, Berlin, Germany 4III-V lab, a joint lab of Alcatel-Lucent Bell Labs France, Thales Research and Technology and CEA Leti, France ∗[email protected] Abstract: In this paper, we report the optical injection locking of an L-band (∼1580 nm) 4.7 GHz III-V-on-silicon mode-locked laser with a narrow line width continuous wave (CW) source. This technique allows us to reduce the MHz optical line width of the mode-locked laser longitudinal modes down to the line width of the source used for injection locking, 50 kHz. We show that more than 50 laser lines generated by the mode-locked laser are coherent with the narrow line width CW source. Two locking techniques are explored. In a first approach a hybrid mode-locked laser is injection-locked with a CW source. In a second approach, light from a modulated CW source is injected in a passively mode-locked laser cavity. The realization of such a frequency comb on a chip enables transceivers for high spectral efficiency optical communication. © 2016 Optical Society of America OCIS codes: (250.5300) Photonic integrated circuits; (140.4050) Mode-locked lasers. -
Arxiv:2106.00060V1 [Physics.Optics] 31 May 2021
Self-injection locking of the gain-switched laser diode Artem E. Shitikov1,∗ Valery E. Lobanov1, Nikita M. Kondratiev1, Andrey S. Voloshin2, Evgeny A. Lonshakov1, and Igor A. Bilenko1,3 1Russian Quantum Center, 143026 Skolkovo, Russia 2Institute of Physics, Swiss Federal Institute of Technology Lausanne (EPFL), CH-1015 Lausanne, Switzerland and 3Faculty of Physics, Lomonosov Moscow State University, 119991 Moscow, Russia (Dated: April 2021) We experimentally observed self-injection locking regime of the gain-switched laser to high-Q optical microresonator. We revealed that comb generated by the gain-switched laser experiences a dramatic reduce of comb teeth linewidths in this regime. We demonstrated the Lorentzian linewidth of the comb teeth of sub-kHz scale as narrow as for non-switched self-injection locked laser. Such setup allows generation of high-contrast electrically-tunable optical frequency combs with tunable comb line spacing in a wide range from 10 kHz up to 10 GHz. The characteristics of the generated combs were studied for various modulation parameters - modulation frequency and amplitude, and for parameters, defining the efficiency of the self-injection locking - locking phase, coupling efficiency, pump frequency detuning. I. INTRODUCTION In this work, we developed the first microresonator stabilized gain-switched laser operating in the SIL Narrow-linewidth lasers are in increasing demand in regime. We demonstrated experimentally high-contrast science and bleeding edge technologies as they give a electrically tuned optical frequency combs with line competitive advantage in such areas as coherent com- spacing from 10 kHz to 10 GHz. It was revealed that munications [1], high-precision spectroscopy [2, 3], op- SIL leads to a frequency distillation of each comb teeth tical clocks [4, 5], ultrafast optical ranging [6–8] and and consequently increase the comb contrast. -
2.6 Q-Switched Erbium-Doped Fiber Laser
COPYRIGHT AND CITATION CONSIDERATIONS FOR THIS THESIS/ DISSERTATION o Attribution — You must give appropriate credit, provide a link to the license, and indicate if changes were made. You may do so in any reasonable manner, but not in any way that suggests the licensor endorses you or your use. o NonCommercial — You may not use the material for commercial purposes. o ShareAlike — If you remix, transform, or build upon the material, you must distribute your contributions under the same license as the original. How to cite this thesis Surname, Initial(s). (2012) Title of the thesis or dissertation. PhD. (Chemistry)/ M.Sc. (Physics)/ M.A. (Philosophy)/M.Com. (Finance) etc. [Unpublished]: University of Johannesburg. Retrieved from: https://ujcontent.uj.ac.za/vital/access/manager/Index?site_name=Research%20Output (Accessed: Date). Development, characterisation and analysis of an active Q-switched fiber laser based on the modulation of a fiber Fabry-Perot tunable filter By KABOKO JEAN-JACQUES MONGA DISSERTATION Submitted for partial fulfillment of the requirements for the degree DOCTOR OF PHILOSOPHY in ELECTRICAL AND ELECTRONIC ENGINEERING SCIENCES in the FACULTY OF ENGINEERING at the UNIVERSITY OF JOHANNESBURG STUDY LEADERS: Dr. Rodolfo Martinez Manuel Pr. Johan Meyer April 2018 Abstract The field of fiber lasers and fiber optic devices has experienced a sustained rapid growth. In particular, all-fiber Q-switched lasers offer inherent advantages of relatively low cost, compact design, light weight, low maintenance, and increased robustness and simplicity over other fiber laser systems. In this thesis, a design of a new Q-switching approach in all-fiber based laser is proposed. -
Cavity Ring-Down Spectrometer for High-Fidelity Molecular Absorption Measurements
Journal of Quantitative Spectroscopy & Radiative Transfer 161 (2015) 11–20 Contents lists available at ScienceDirect Journal of Quantitative Spectroscopy & Radiative Transfer journal homepage: www.elsevier.com/locate/jqsrt Cavity ring-down spectrometer for high-fidelity molecular absorption measurements H. Lin a,b, Z.D. Reed a, V.T. Sironneau a, J.T. Hodges a,n a National Institute of Standards and Technology, Gaithersburg, MD, USA b National Institute of Metrology, Beijing 100029, China article info abstract Article history: We present a cavity ring-down spectrometer which was developed for near-infrared Received 26 January 2015 measurements of laser absorption by atmospheric greenhouse gases. This system has Received in revised form several important attributes that make it possible to conduct broad spectral surveys and 23 March 2015 to determine line-by-line parameters with wide dynamic range, and high spectral Accepted 24 March 2015 resolution, sensitivity and accuracy. We demonstrate a noise-equivalent absorption Available online 1 April 2015 coefficient of 4 Â 10 À12 cmÀ1 HzÀ1/2 and a signal-to-noise ratio of 1.5 Â 106:1 in an Keywords: absorption spectrum of carbon monoxide. We also present high-resolution measurements Cavity ring-down spectroscopy of trace methane in air spanning more than 1.2 THz and having a frequency axing with an Line shape uncertainty less than 100 kHz. Finally, we discuss how this system enables stringent tests Carbon dioxide of advanced line shape models. To illustrate, we measured an air-broadened carbon Speed dependent effects dioxide transition over a wide pressure range and analyzed these data with a multi- spectrum fit of the partially correlated, quadratic speed-dependent Nelkin–Ghatak profile. -
Advanced Semiconductor Lasers
INSTITUT NATIONAL DES SCIENCES APPLIQUÉES ADVANCED SEMICONDUCTOR LASERS Frédéric Grillot Université Européenne de Bretagne Laboratoire CNRS FOTON 20 avenue des buttes de Coesmes 35043 Rennes Cedex [email protected] Second Version - Year 2010 2 Contents 1 Basics of Semiconductor Lasers 7 1.1 Principle of Operation . .7 1.1.1 Radiative Transitions in a Semiconductor . .7 1.1.2 Optical Gain and Laser Cavity . .9 1.1.3 Output Light-Current Characteristic . 11 1.1.4 Carrier Confinement . 13 1.1.5 Optical Field Confinement and Spatial Modes . 15 1.1.6 Near- and Far-Field Patterns . 17 1.2 Quantum Well Lasers . 18 1.3 Quantum Dot Lasers . 20 1.4 Single-Frequency Lasers . 23 1.4.1 Short-Cavity Lasers . 23 1.4.2 Coupled-Cavity Lasers . 23 1.4.3 Injection-Locked Lasers . 24 1.4.4 DBR Lasers . 25 1.4.5 DFB Lasers . 26 2 Advances in Measurements of Physical Parameters of Semiconductor Lasers 31 2.1 Measurements of the Optical Gain . 31 2.1.1 Determination of the Optical Gain from the Amplified Spontaneous Emission . 32 2.1.2 Determination of the Optical Gain from the True Spontaneous Emission 34 2.2 Measurement of the Optical Loss . 36 2.3 Measurement of the Carrier Leakage in Semiconductor Lasers . 37 2.3.1 Optical Technique of Studying the Carrier Leakage . 37 2.3.2 Electrical Technique of Studying Carrier Leakage . 38 2.4 Electrical and Optical Measurements of RF Modulation Response below Thresh- old.......................................... 40 2.4.1 Determination of the Carrier Lifetime from the Device Impedance . -
Laser Linewidth at the Sub-Hertz Level
NPL Report CLM 8 September1999 Laser Linewidth at the sub-Hertz Level M. Roberts P. Thy lor P. Gill Centre for Length Metrology National Physical Laboratory Teddington, Middlesex, TWll OLW Abstract A number of fields require state of the art low noise laser systems. The report has been written to aid the development of a laser source with a sub-hertz linewidth. The report brings together the most recent work in the field of laser stabilisation, along with a description of the rele- vant basic principles. There are explanations of the parameters used to describe laser noise and stability (power spectral density, Allan vari- ance, linewidth, modulation index). The effects of perturbation on a laser (plus reference cavity) system are discussed, including vibration, acoustic noise, thermal effects and opto-electrical considerations. The report concludes with a recommended laser system, drawing on the facts learnt during the process of writing this report. NPL Report CLM 8 @Crown Copyright 1999 Reproduced by permissionof the Controller of HMSO ISSN 1369-6777 Extracts from this report may be reproduced provided the source is acknowledged and the extract is not taken out of context Authorised for publication on behalf of the Managing Director of NPL by Dr David Robinson 1 Introd uction 1 1.11.21.3 AssumptionsOmissionsLaser Noise Requirements. ... 1 2 2 1.4 Choice of Laser/Servo Electronics 3 1.61.51.7 TheReferenceReport State summary.List.of the Art. 4 4 6 2 Noise 9 2.1 Measurementtechniques """"""' "'.. 9 2.32.2 2.3.12.1.12.2.12.2.22.2.4FrequencyCharacterisation2.2.3 AllanvarianceRelatingTheRelatingModulationPower Modulationfour Spectral Spectralmeasurementof index,Frequency Density.Analysis. -
Short Wave Infrared Cavity Ring Down Spectroscopy (SWIR CRDS) Sensor
PNNL-14475 Chemical Sensing Using Infrared Cavity Enhanced Spectroscopy: Short Wave Infrared Cavity Ring Down Spectroscopy (SWIR CRDS) Sensor R. M. Williams J.S. Thompson W.W. Harper T.L. Stewart P.M. Aker October 2003 Prepared for the U.S. Department of Energy under Contract DE-AC06-76RL01830 DISCLAIMER This report was prepared as an account of work sponsored by an agency of the United States Government. Neither the United States Government nor any agency thereof, nor Battelle Memorial Institute, nor any of their employees, makes any warranty, express or implied, or assumes any legal liability or responsibility for the accuracy, completeness, or usefulness of any information, apparatus, product, or process disclosed, or represents that its use would not infringe privately owned rights. Reference herein to any specific commercial product, process, or service by trade name, trademark, manufacturer, or otherwise does not necessarily constitute or imply its endorsement, recommendation, or favoring by the United States Government or any agency thereof, or Battelle Memorial Institute. The views and opinions of authors expressed herein do not necessarily state or reflect those of the United States Government or any agency thereof. PACIFIC NORTHWEST NATIONAL LABORATORY operated by BATTELLE for the UNITED STATES DEPARTMENT OF ENERGY under Contract DE-AC06-76RL01830 Printed in the United States of America Available to DOE and DOE contractors from the Office of Scientific and Technical Information, P.O. Box 62, Oak Ridge, TN 37831-0062; ph: (865) 576-8401 fax: (865) 576-5728 email: [email protected] Available to the public from the National Technical Information Service, U.S. -
Laser Diode Cavity Ring-Down Spectroscopy Using Acousto-Optic Modulator Stabilization B
Laser diode cavity ring-down spectroscopy using acousto-optic modulator stabilization B. A. Paldus, J. S. Harris, J. Martin, J. Xie, and R. N. Zare Citation: J. Appl. Phys. 82, 3199 (1997); doi: 10.1063/1.365688 View online: http://dx.doi.org/10.1063/1.365688 View Table of Contents: http://jap.aip.org/resource/1/JAPIAU/v82/i7 Published by the American Institute of Physics. Additional information on J. Appl. Phys. Journal Homepage: http://jap.aip.org/ Journal Information: http://jap.aip.org/about/about_the_journal Top downloads: http://jap.aip.org/features/most_downloaded Information for Authors: http://jap.aip.org/authors Downloaded 01 Jun 2013 to 171.64.124.91. This article is copyrighted as indicated in the abstract. Reuse of AIP content is subject to the terms at: http://jap.aip.org/about/rights_and_permissions Laser diode cavity ring-down spectroscopy using acousto-optic modulator stabilization B. A. Paldus and J. S. Harris, Jr. Department of Electrical Engineering, Stanford University, Stanford, California 94305-4070 J. Martin,a) J. Xie,b) and R. N. Zarec) Department of Chemistry, Stanford University, Stanford, California 94305-5080 ~Received 28 April 1997; accepted for publication 23 June 1997! By using an acousto-optic modulator, we have stabilized a free-running continuous wave ~CW! laser diode in the presence of strong reflections from a high finesse Fabry–Perot resonator. The laser diode linewidth can be stabilized from several MHz, for high resolution spectroscopy of species at low pressures, to several hundred MHz, for lower resolution spectroscopy of species at atmospheric pressures. We demonstrated CW cavity ring-down spectroscopy of water vapor at both 1 atm and 5 Torr. -
Effect of Laser Lineshape on the Quantitative Analysis of Cavity Ring-Down Signals A
Laser Physics, Vol. 12, No. 8, 2002, pp. 1065–1072. LASER Original Text Copyright © 2002 by Astro, Ltd. Copyright © 2002 by MAIK “Nauka /Interperiodica” (Russia). SPECTROSCOPY Effect of Laser Lineshape on the Quantitative Analysis of Cavity Ring-Down Signals A. P. Yalin and R. N. Zare Department of Mechanical Engineering and Department of Chemistry, Stanford University, Stanford, CA, 94305 USA e-mail: [email protected] Received October 8, 2001 Abstract—In cavity ring-down spectroscopy (CRDS) the finite spectral width of the laser pulse leads to a ring- down signal in which the decay is not strictly exponential. Nevertheless, the simple assumption of a single- exponential form is the method used in almost all analyses. This paper provides a generalized treatment of the errors introduced by such an approach. We re-examine the equations governing the ring-down signals and show that the problem may be parameterized with two dimensionless variables: the laser linewidth normalized by the absorption linewidth, and the peak sample absorbance normalized by the empty cavity loss. For different values of these two parameters, we simulate multi-exponential ring-down signals and the errors introduced by fitting them with single-exponential signal profiles. We examine the validity of analyzing CRDS data assuming a sin- gle-exponential form, both with an uncorrected and an effective absorption lineshape. We show that the effec- tive lineshape is rigorously correct in the early-time (or weak-absorption) limit, and that for a peak based anal- ysis, it gives better results than the uncorrected lineshape in all cases. We find that analysis using the area is comparably robust to analysis using the peak with an effective lineshape, and thus recommend the former, as it does not require knowledge of lineshapes. -
UNIVERSITY of CALIFORNIA Santa Barbara Heterogeneous Integration
UNIVERSITY OF CALIFORNIA Santa Barbara Heterogeneous Integration for Reduced Phase Noise and Improved Reliability of Semiconductor Lasers A dissertation submitted in partial satisfaction of the requirements for the degree Doctor of Philosophy in Electrical and Computer Engineering by Sudharsanan Srinivasan Committee in charge: Professor John Bowers, Chair Professor Larry Coldren Professor Luke Theogarajan Professor Rod Alferness June 2015 The dissertation of Sudharsanan Srinivasan is approved. ____________________________________________ Larry Coldren ____________________________________________ Luke Theogarajan ____________________________________________ Rod Alferness ____________________________________________ John Bowers, Committee Chair June 2015 Heterogeneous Integration for Reduced Phase Noise and Improved Reliability of Semiconductor Lasers Copyright © 2015 by Sudharsanan Srinivasan iii Dedicated to my parents Srinivasan and Lakshmi iv ACKNOWLEDGEMENTS I will be forever grateful to my adviser, Prof. John Bowers, for all his help throughout my time at UCSB. To begin, he provided an excellent opportunity to perform cutting edge research in photonics by accepting my application to join his group. His passion for research is something that all his students strive to achieve. I have certainly grown to see him as a role model for me on how to be an effective researcher, through determination and constant hard work. His commitment to provide every student in his group a fair chance of reaching his/ her project goals even if it requires purchasing state of the art equipment or other material is commendable. His intuition to research methodology is unique and has prevented many distractions or tangential pursuits and hurdles in my research. I would also like to thank him for giving me exposure to the broader research community through conference travels, even if I did not have a paper to present. -
Compact Narrow Linewidth Actively Q-Switched Er‒ Yb Double-Clad
Article Compact Narrow Linewidth Actively Q-Switched Er– Yb Double-Clad Fiber Laser Berenice Posada-Ramírez 1, Manuel Durán-Sánchez 2, Ricardo I. Alvarez-Tamayo 3, Jared Alaniz- Baylón 1, Guillermo Salceda-Delgado 4, Evgeny A. Kuzin 1, and Baldemar Ibarra-Escamilla 1,* 1 Instituto Nacional de Astrofísica, Ó ptica y Electrónica, Luis Enrique Erro 1, Sta. María Tonantzintla, Puebla 72824, Mexico; [email protected] (B.P.-R.); [email protected] (J.A.-B.); [email protected] (E.A.K.) 2 CONACyT—Instituto Nacional de Astrofísica, Ó ptica y Electrónica, Luis Enrique Erro 1, Sta. María Tonantzintla, Puebla 72824, Mexico; [email protected] 3 CONACyT—Universidad Autónoma de Nuevo León, Av. Universidad S/N San Nicolás de los Garza, Nuevo León 66451, Mexico; [email protected] 4 Universidad Autónoma de Nuevo León, Av. Universidad S/N San Nicolás de los Garza, Nuevo León 66451, Mexico; [email protected] * Correspondence: [email protected]; Tel.: +52-222-247-2940 Academic Editors: Giancarlo C. Righini and Shibin Jiang and Francesco Prudenzano Received: 30 March 2017; Accepted: 29 May 2017; Published: 3 June 2017 Abstract: Actively Q-switched laser operation of a narrow linewidth compact fiber laser based on an Er–Yb double-clad fiber is presented. The laser linewidth as a function of the repetition rate and the Q-switched pulses characteristics for different pump powers are experimentally analyzed. Stable Q-switched laser operation with spectral laser linewidth of 73 pm in a repetition rate range from 90 to 270 kHz is obtained. The minimum pulse duration of 178 ns, maximum peak power of 30.5 W, and maximum pulse energy of 5.4 µJ are observed.