Journal Paper Format
Total Page:16
File Type:pdf, Size:1020Kb
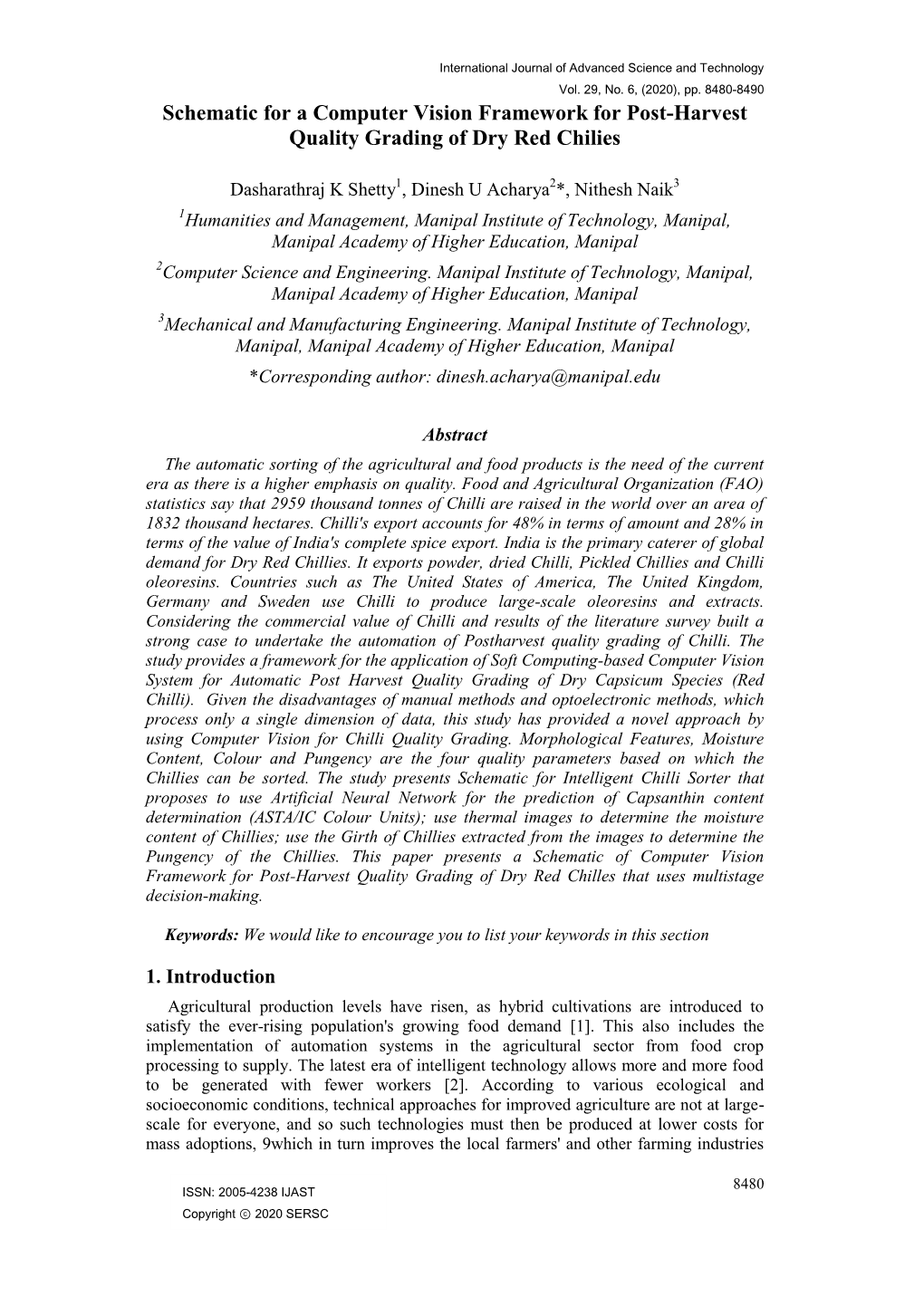
Load more
Recommended publications
-
International Journal of Advanced Scientific and Technical Research
International Journal of Advanced Scientific and Technical Research Issue 3 volume 2, March-April 2013 Available online on http://www.rspublication.com/ijst/index.html ISSN 2249-9954 CAPSAICIN AND COLOUR EXTRACTION FROM DIFFERENT VERITIES OF GREEN AND RED CHILLI PEPPERS OF ANDHRAPRADESH DR. M. VIJAYA BHASKARA REDDY AND P. SASIKALA Corresponding author: Dr. M. Vijaya Bhaskara Reddy Study Investigator, Dept. of LPM, College of veterinary Science, Sri Venkateswara Veterinary University Tirupati-517502, Andhra Pradesh, India, Email: Cell: +91- 7396120530 Co- Author: P. Sasikala Dept. of LPM, College of veterinary Science, Sri Venkateswara Veterinary University, Tirupati-517502, Andhra Pradesh, India ______________________________________________________________________________ ABSTRACT Twelve different chilli varieties at three different stages (green, red ripe, red dry) were collected. The chillies were subjected for the estimation and extraction of capsaicin and colour. The estimation of capsaicin was done in the laboratory to determine the pungency for each chilli variety collected. The pungency level was given in Scoville units. The chilli sample which has the highest pungency was subjected for the extraction of capsaicin. From the pericarp of the chilli the colour was extracted and the colour intensity was found according to the ASTA (American Spice Trade Association) and CU (Colour Units). The large scale industrial extraction procedure for the extraction of capsaicin and colour was collected. Key words: Green and Red Chilli Samples, Capsaicin, Colour Oleoresin. ______________________________________________________________________________ INTRODUCTION In India, Pepper is an important agricultural crop, not only because of its economic importance, but also for the nutritional value of its fruits, mainly due to the fact that they are an excellent source of natural colors and antioxidant compounds (Nevarro et al., 2006). -
Red Chilli Prices to Decline Marginally During Harvest India Is the Largest
Tamil Nadu Agricultural University Coimbatore – 641 003 Dr. Ravi Kumar Theodore, Ph.D., Phone: 0422 - 6611302 Public Relations Officer & Fax: 0422 – 2431821 Professor (Agrl. Extension) E-mail: [email protected] To Date: 5-11-2012 The Editor, Sir, I request that the following matter may kindly be published in your esteemed daily: Red Chilli Prices to Decline Marginally During Harvest India is the largest producer, consumer and exporter of chili, which contributes to 25% of total world production. India has produced about 12.50 lakh tonnes of chilli during 2011-12. Next to India, China is the major producer of chilli in the world. During 2010, Chinese chilli production declined sharply because of unfavorable weather conditions which became an advantage for Indian chilli exporters. In India, chillies are grown in almost all the states. Andhra Pradesh is the largest producer of chilli in India contributing to about 30% to the total area under chilli, followed by Karnataka (20%), Orissa (9%), Tamil Nadu (8%), Maharashtra (1%), and other States contributing 18 %. Chillies grown in India have many special features. The Byadagi and Guntur sannam varieties are known for its natural colour. Mizoram and some areas of Manipur chilli are famous for their spiciness. Byadagi chilli is used for extracting oil. 10-15% of total domestic production is meant for exports with domestic consumption of 85-90%. India exports chilli in various processed forms like chilli powder, dried chillies, chilly pickles, chilli paste, flaked chilli, etc., and it is mainly exported to Sri Lanka, USA, Nepal, Mexico, Malaysia, Bangladesh, UAE, Indonesia and China. -
Effect of Drying Methods on Seed Quality of Byadagi Chilli
Bulletin of Environment, Pharmacology and Life Sciences Bull. Env. Pharmacol. Life Sci., Vol 7 [4] April 2018 : 27-29 ©2018 Academy for Environment and Life Sciences, India Online ISSN 2277-1808 Journal’s URL:http://www.bepls.com CODEN: BEPLAD Global Impact Factor 0.876 Universal Impact Factor 0.9804 NAAS Rating 4.95 ORIGINAL ARTICLE OPEN ACCESS Effect of Drying Methods on Seed Quality of Byadagi Chilli Krishna D. Kurubetta *, M. H. Tatagar, T. B. Allolli, R. K. Mesta, M. Abdul Kareem and K. Sweta * Assistant Professor of Agronomy, Horticulture Research and Extension Station, Devihosur- 581110, Haveri , Karnataka . e-mail: [email protected] ABSTRACT The pooled results of the two year experimentation revealed that, among the different methods of drying chilli, significantly highest per cent (85%) of germination was noticed with treatment (T6) drying on surface washed with dung slurry and field emergence(77%) with drying on cement concrete floor and drying on polythene tarpaulin sheet. The high temperature during drying period will affect the seed quality parameters. Key words : Drying methods, Seed quality, Chilli Seed, Bydagi Chilli Received 11.02.2018 Revised 02.03.2018 Accepted 26.04.2018 INTRODUCTION Drying is one of the essential unit operations performed to increase the shelf life of agricultural / horticultural produce and it is one of the most practical methods of preserving food and the quality of horticultural produce. If the drying process is not completed fast enough, growth of microorganisms will take place as a result of the high relative humidity [1-2]. This often leads to severe deterioration of the quality of the product. -
Processing of Byadgi Chilli
PROCESSING OF BYADGI CHILLI 1 INTRODUCTION ❑ Byadgi or Byadagi chilli is a famous variety of chilli in Karnataka state. ❑ It is a long (12-15 cm) and thin variety of chilli. The fruits have characteristic red colour and wrinkles on the surface. ❑ This variety of chilli is extensively grown and marketed in Byadgi, a town in the Haveri district of Karnataka state. Hence, the name of the variety is Byadgi chilli 2 GENERAL CHARACTERISTICS OF BYADGI CHILLI ❑ Byadgi chillies are famous for its aroma and deep red colour. ➢ Colour: 150000 - 250000 CU (Colour Units) or 80 - 130 ASTA ❑ Bydagi chillies have mild pungency and moderate seed content. ➢ The capsaicin content: 0.8 - 1.3%, Oleoresin: 12 – 15% ➢ Pungency: 8000 - 15000 SHU (Scoville Heat Units). ❑ Byadgi chillies are the Geographical Indication product of Karnataka. ❑ Grown in Dharwad, Gadag, Haveri , Bellary, Raichur and Gulbarga districts of Karnamataka and Karnool and Adhoni districts of Andhra Pradesh ➢ Yield: 0.5-1.25 MT/ha (rain-fed), 3.75-5.00 MT/ha (Irrigated) 3 VARIETIES OF BYADGI CHILLI Byadgi Kaddi Byadgi Dabbi Other varieties Dyavanur Delux Noolvi Dabbi Kubhsi Dabbi Antur Bentur Dabbi 4 CULTIVATION OF BYADGI CHILLIES ❑ Soil ➢ Well drained loamy soils ➢ Black and red lateritic soils rich in potash having a pH of 5.5-6.5 ❑ Climate ➢ 20-38ºC with warm humid conditions during the growth of plant ➢ Dry weather conditions during maturity of fruits. ❑ Sowing : May-June month ➢ Transplanting 30-45 days old seedlings on raised beds of 1 m width. ➢ Seed rate: 1.0 - 1.25 kg/ha, 40 - 45 days seedlings ❑ Harvesting ➢ November - January months ➢ Fruits are picked when they turn bright red colour. -
Hot Chili Chili Tool Oa., Styrke & Scoville – 3 – Rev
Hot Chili Chili tool oa., Styrke & Scoville – 3 – rev. 1.2 Stor liste med relativ styrke og Scoville værdi (..eller den lille gruppe oversigt med kendte chili) Styrke Navne Scoville Noter ▪ Ren Capsaicin 16,000,000 12 ▪ Carolina Reaper 2,200,000 ▪ Trinidad Moruga Scorpion 2,009,231 ▪ ▪ 7 Pot Douglah 1,853,396 10++++ til 12 ▪ Trinidad Scorpion Butch T 1,463,700 ▪ Naga Viper Pepper 1,382,118 ▪ 7 Pot Barrackpore 1,300,000 ▪ 7 Pot Jonah 1,200,000 ▪ 7 Pot Primo 1,200,000 ▪ New Mexico Scorpion 1,191,595 ▪ Infinity Chili 1,176,182 ▪ Bedfordshire Super Naga 1,120,000 ▪ ▪ Dorset Naga chili 1,100,000 ▪ Naga Jolokia 1,100,000 ▪ Naga Morich 1,100,000 ▪ Spanish Naga Chili 1,086,844 ▪ 7 Pot Madballz 1,066,882 ▪ Bhut Jolokia chili 1,041,427 ▪ Chocolate Bhut Jolokia 1,001,304 ▪ 7 Pot Brain Strain 1,000,000 ▪ Bhut Jolokia Indian Carbon 1,000,000 ▪ Trinidad Scorpion 1,000,000 ▪ Raja Mirch 900,000 ▪ Habanaga chili 800,000 ▪ Nagabon Jolokia 800,000 ▪ Red Savina Habanero 580,000 10++++ Chili Home Side 1/12 Hot Chili Chili tool oa., Styrke & Scoville – 3 – rev. 1.2 10+++ og 10++++ ▪ Fatalii 500,000 10++++ ▪ Aji Chombo 500,000 ▪ Pingo de Ouro 500,000 ▪ Aribibi Gusano 470,000 ▪ Caribbean Red Habanero 400,000 ▪ Chocolate Habanero 350,000 10++++ ▪ Datil chili 350,000 10++++ ▪ Habanero 350,000 ▪ Jamaican Hot chili 350,000 ▪ Madame Jeanette chili 350,000 ▪ Rocoto chili 350,000 ▪ Scotch Bonnet 350,000 10+++ ▪ Zimbabwe Bird Chili 350,000 ▪ Adjuma 350,000 ▪ Guyana Wiri Wiri 350,000 10+++ ▪ Tiger Paw 348,634 ▪ Big Sun Habanero 325,000 ▪ Orange Habanero 325,000 9 og 10+++ ▪ Mustard Habanero 300,000 ▪ Devil’s Tongue 300,000 10++++ ▪ Orange Rocoto chili 300,000 10++ ▪ Paper Lantern Habanero 300,000 ▪ Piri Piri 300,000 8-10 ▪ Red Cheese 300,000 ▪ Red Rocoto 300,000 10++ ▪ Tepin chili 300,000 ▪ Thai Burapa 300,000 ▪ White Habanero 300,000 9-10 ▪ Yellow Habanero 300,000 ▪ Texas Chiltepin 265,000 ▪ Pimenta de Neyde 250,000 ▪ Maori 240,000 ▪ Quintisho 240,000 Chili Home Side 2/12 Hot Chili Chili tool oa., Styrke & Scoville – 3 – rev. -
Hot Pepper (Capsicum Spp.) – Important Crop on Guam
Food Plant Production June 2017 FPP-05 Hot Pepper (Capsicum spp.) – Important Crop on Guam Joe Tuquero, R. Gerard Chargualaf and Mari Marutani, Cooperative Extension & Outreach College of Natural & Applied Sciences, University of Guam Most Capsicum peppers are known for their spicy heat. Some varieties have little to no spice such as paprika, banana peppers, and bell peppers. The spice heat of Capsicum peppers are measured and reported as Scoville Heat Units (SHU). In 1912, American pharmacist, Wilbur Scoville, developed a test known as the, Scoville Organoleptic Test, which was used to measure pungency (spice heat) of Capsicum peppers. Since the 1980s, pungency has been more accurately measured by high-performance liquid chromatography Source: https://phys.org/news/2009-06-domestication- (HPLC). HPLC tests result in American Spice Trade capsicum-annuum-chile-pepper.html Association (ASTA) pungency units. ASTA pungency Introduction units can be converted to SHU. Table 2 displays Sco- Hot pepper, also known as chili, chilli, or chile pepper, ville Heat Units of various popular Capsicum peppers is a widely cultivated vegetable crop that originates (Wikipedia, 2017). from Central and South America. Hot peppers belong to the genus Capsicum. There are over 20 species under the genus Capsicum. There are five major domesticated species of peppers that are commercially cultivated (Table 1), and there are more than 50,000 varieties. Fig. 1 depicts a unqiue, citrus-flavored variety of Capsicum baccatum hot pepper, known as Lemon Drop (aji-type), popular for seasoning in Peru (Wikipedia, 2017). Table 1. The five major domesticated Capsicum species of pepper with examples of commonly known types of pepper. -
GOVERNMENT of INDIA GEOGRAPHICAL INDICATIONS JOURNAL NO. 36 September 23, 2010 / ASHWIN 30, SAKA 1932
1 GOVERNMENT OF INDIA GEOGRAPHICAL INDICATIONS JOURNAL NO. 36 September 23, 2010 / ASHWIN 30, SAKA 1932 2 INDEX S.No. Particulars Page No. 1. Official Notices 4 2. G.I Application Details 5 3. Public Notice 4. Byadagi Chilli 5. Scotch Whisky 6. Prosciutto di Parma 7. General Information 8. Registration Process 3 OFFICIAL NOTICES Sub: Notice is given under Rule 41(1) of Geographical Indications of Goods (Registration & Protection) Rules, 2002. 1. As per the requirement of Rule 41(1) it is informed that the issue of Journal 36 of the Geographical Indications Journal dated 23rd September 2010 / Ashwin 30, Saka 1932 has been made available to the public from 23rd September 2010. 4 G.I. Geographical Indication Class Goods App.No. 1 Darjeeling Tea (word) 30 Agricultural 2 Darjeeling Tea (Logo) 30 Agricultural 3 Aranmula Kannadi 20 Handicraft 24, 25 & 4 Pochampalli Ikat Textile 27 5 Salem Fabric 24 Textile 6 Payyannur Pavithra Ring 14 Handicraft 7 Chanderi Fabric 24 Textile 8 Solapur Chaddar 24 Textile 9 Solapur Terry Towel 24 Textile 10 Kotpad Handloom fabric 24 Textile 24, 25 & 11 Mysore Silk Textile 26 12 Kota Doria 24 & 25 Textile 13 Mysore Agarbathi 3 Manufactured 14 Basmati Rice 30 Agricultural 15 Kancheepuram Silk 24 & 25 Textile 16 Bhavani Jamakkalam 24 Textile 17 Navara - The grain of Kerala 30 Agricultural 18 Mysore Agarbathi "Logo" 3 Manufactured 19 Kullu Shawl 24 Textile 20 Bidriware 6, 21 & 34 Handicraft 21 Madurai Sungudi Saree 24 & 25 Textile 23, 24 & 22 Orissa Ikat Textile 25 23 Channapatna Toys & Dolls 28 Handicraft 19, 20, -
Quality Assesment of Selected Commercial Brand of Chilli Powder in Andhrapradesh Region
IOSR Journal Of Pharmacy (e)-ISSN: 2250-3013, (p)-ISSN: 2319-4219 Volume 10, Issue 1 Series. I (January 2020), PP. 47-63 www.iosrphr.org Quality Assesment of Selected Commercial Brand of Chilli Powder in Andhrapradesh Region Phanindra.N*,M.Mounika,rama rao.N Chalapathi institute of pharmaceutical sciences,Guntur Received 20 January 2020; Accepted 10 February 2020 ABSTRACT: Analysed quality parameters of different commercial brand red chilli powders (Capsicum annuum L) collected from Guntur Mirchi yard, Guntur, Andhra Pradesh. The quality parameters of moisture content, pH, total ash content, acid soluble ash content, ascorbic acid content, minerals (sodium, potassium, calcium), capsaicin content and ASTA colour value were assessed which are directly related to quality, processing technique, storage condition, packaging of chilli powder. In different varieties of chilli powders moisture content, ash content and ASTA colour values differ significantly between 1.6 to 8.6%, 3.6 to 7.3% and to 76.45 ASTA. Capsaicin content was estimated by colorimetric method and R2 shows 0.9978, which shows developed method was linear. In addition, a minimum of 1 mcg/mL capsaicinoids can be detected and developed method can efficiently analyze a great quantity of samples in a short time. Based on the capsaicin content and colour value of different red chilli powders provides useful information for buyers of chilli exporters and industrial applications. KEYWORDS: Capsicum annuum L., Capsaicin, Ash value, ASTA colour value. I. INTRODUCTION Chilli (Capsicum annuum L.) is an important vegetable cum spice crop grown in almost all parts of tropical and subtropical regions of the world. -
Methods of Drying on Fruit Quality of Byadagi Chilli
Journal of Pharmacognosy and Phytochemistry 2020; Sp 9(6): 506-508 E-ISSN: 2278-4136 P-ISSN: 2349-8234 www.phytojournal.com Methods of drying on fruit quality of Byadagi JPP 2020; Sp 9(6): 506-508 Received: 20-09-2020 chilli Accepted: 22-10-2020 Krishna D Kurubetta Krishna D Kurubetta, M Abdul Kareem, TB Allolli, RK Mesta, MH Assistant Professor of Tatagar and K Sweta Agronomy, Horticulture Research and Extension Station, Devihosur, Haveri, Karnataka, DOI: https://doi.org/10.22271/phyto.2020.v9.i6Sk.14009 India Abstract M Abdul Kareem The experiment was conducted to study the effect of different drying methods in red chilli (Byadagi Assistant Professor of dabbi) at Horticultural Research and Extension Station, Devihosur, Haveri, Karnataka, during 2016 and Agronomy, Horticulture 2017 in rabi season. Drying in solar tunnel dryer method is found to be the best option in field situation Research and Extension Station, for reducing the average drying period (6.0 days) and significantly least per cent of white fruits (7.5 %), Devihosur, Haveri, Karnataka, as compare to other treatments. This was mainly due to increased average maximum temperature (54.2 India 0C), minimum temperature (29.2 0C) and reduced relative humidity (57 %) compared to outside 0 0 temperature (Tmax - 36 C & Tmin-18 C and RH – 74%). This resulted in rapid loss of moisture from the TB Allolli fruits and ultimately reduced the drying period and fruit whitening. The fruit quality parameters were not Assistant Professor of Agronomy, Horticulture significantly affected by the methods of drying in chilli. Research and Extension Station, Devihosur, Haveri, Karnataka, Keywords: Drying methods, fruit quality, chilli fruit, Bydagi chilli India Introduction RK Mesta India is the largest producer and consumer of dry chillies. -
Economics of Value Addition in Oleoresin: Implications for Access and Benefit Sharing of Byadagi Chilli in Karnataka
1 Economics of value addition in Oleoresin: Implications for Access and Benefit Sharing of Byadagi Chilli in Karnataka Report submitted to The Karnataka Biodiversity Board Ground Floor, Vanavikas 18th Cross Malleshwaram Bangalore 560003 Email: [email protected] By MG Chandrakanth1, Shrikantha Mulimani1, H Karibasappa1, H Sadhana2, RS Kulkarni3, Khalil Shah4, AV Manjunatha4, MH Tatagar5, A Mohan Rao6, Mahadev G Bhat7 and Ramachandra Bhatta2 1. Department of Agricultural Economics, University of Agricultural Sciences, Bangalore 2. Department of Fishery Economics, Fishery College, Mangalore 3. Professor of Genetics and Plant Breeding (Retd), UAS Bangalore 4. Institute for Social and Economic Change, Bangalore 5. Professor of Entomology, UAS Dharwad 6. Professor of Genetics and Plant Breeding, UAS Bangalore 7. Professor of Environmental Economics, Florida International University, Miami Contact email: [email protected] Phone number: 9449486018 Sep 2015 2 Contents Economics of value addition in Oleoresin: Case study of Byadagi chilli in Karnataka Particulars Page No. 1 Preamble 3 2 India leads in Chilli Exports 3 3 Study Objective 4 4 Oleoresin 4 5 Trends in area, production, productivity of Chilli in Karnataka 4 6 Spurt in production of chilli due to demand for oleoresins 6 7 Major chilli producing districts of Karnataka 6 8 Area and production of chilli in Bellary 6-7 9 Figures of area, production, productivity 8-9 9 Economics of rainfed chilli cultivation in Karnataka 10 10 Economics of irrigated chilli cultivation in Karnataka 11 -
Quality Assessment of Selected Commercial Brand of Chilli Powder in Bangladesh
MOJ Food Processing & Technology Research Article Open Access Quality assessment of selected commercial brand of chilli powder in Bangladesh Abstract Volume 3 Issue 2 - 2016 The present study was carried out to reveal the quality assessment of the chilli powder. 1 2 The samples collected from market used in this investigation were commercial brand Abdullah Al Mamun, Masuma Afrin Aynee, 3 1 of chilli powder in Bangladesh. The quality parameters of moisture content, ash Dipika Majumder, Md Mokaddes Ali, Md content, acid soluble ash content, refractive index, volatile fat were assessed which Showkat Hossen,1 Khodadad Maruf1 are directly related to quality, processing technique, storage condition, packaging, 1Faculty of Food Science & Technology, Chittagong Veterinary microbial load of chilli powder. The moisture content and ash content of chilli powder and Animal Sciences University, Bangladesh were about 4.40-6.00% and 5.28-6.19% respectively. Then microbiological tests such 2Department of Applied Chemistry and Chemical Technology, as TPC, mold count, coliform count, and salmonella were accomplished. Total mold Chittagong Veterinary and Animal Sciences University, count was found ranged from 1.0×103 to 3.1×103. Coliform was also detected, where Bangladesh 3 all samples were free from Salmonella. Department of Applied Food Science and Nutrition, Chittagong Veterinary and Animal Sciences University, Bangladesh Keywords: chilli powder, volatile fat, acid insoluble ash, moisture content, mold count, coliform count Correspondence: Abdullah Al Mamun, Faculty of Food Science & Technology, Chittagong Veterinary & Animal Sciences University (CVASU), Khulshi-4225, Chittagong, Bangladesh, Tel +8801798327525, Email [email protected] Received: October 16, 2016 | Published: December 01, 2016 Abbreviations: CFU, colony forming unit; G, gram; TPC, total Warm and humid condition is favorable for microbial growth. -
Gloria Exports Pvt Ltd (Agro Division) Office No. 6, Arena 1, Poonam Garden, Off Mira Bhy Road, Mira Road East – 401107
Gloria Exports Pvt Ltd (Agro Division) Office No. 6, Arena 1, Poonam Garden, Off Mira Bhy Road, Mira Road East – 401107. Tel: +91 9167075571 | W: www.gloriaexports.com | E: [email protected] Skype: gloria.exports.agro About us Gloria Exports Pvt Ltd is a professional managed private limited company having vast experience in exports of veterinary formulations, feed supplements, agricultural commodities, spices, Coir products, Shrink/Stretch Films, Tarpaulins, Coconut based Charcoal/Carbon and leather products. We pride ourselves in being market leaders in distributions of comprehensive range of products. We offer high quality products with varied varieties at competitive pricing. We have a team of qualified professionals with rich experience in their respective domains. This enables us to follow the best industry practices from production of goods till dispatch of products. All these are further supported by excellent warehousing facilities with strong logistic supports enabling timely delivery of products. Each product undergoes strict quality control measures and is closely monitored to meets the quality standards. Thus ensuring the good exported to clients is of highest premium quality. CUSTOMER IS THE KING and we truly believe in this phrase. We would never exist, if we didn’t have a dedicated customer base. These customers have stayed with us due to our superior customer services. We believe that it’s important to build and maintain customers. This is achieved through constant innovation and attending to changing needs and expectations