Design Refinement and Modeling Methods for Highly-Integrated Hypersonic Vehicles
Total Page:16
File Type:pdf, Size:1020Kb
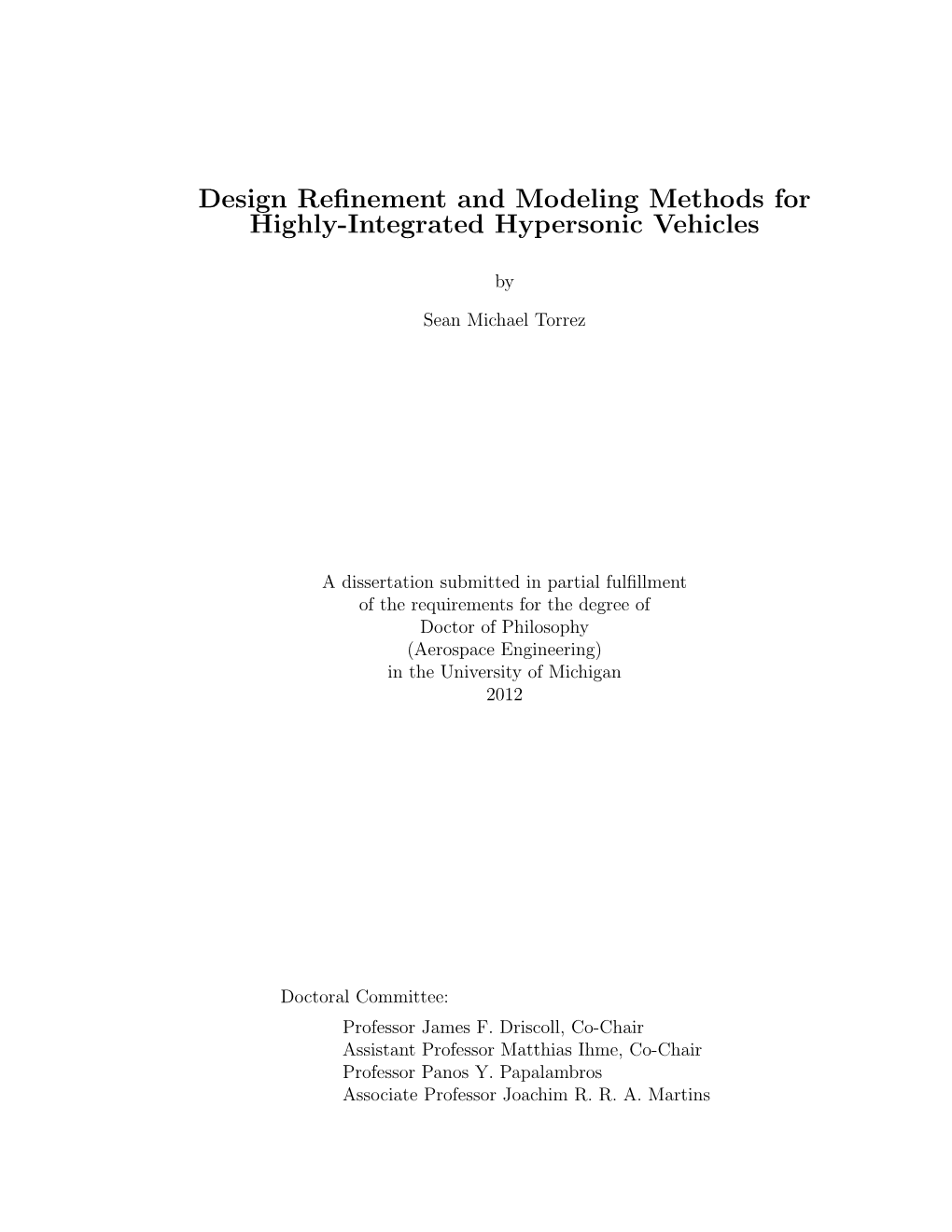
Load more
Recommended publications
-
Aerodynamic Characteristics of Two Waverider-Derived Hypersonic Cruise Configurations
NASA Technical Paper 3559 Aerodynamic Characteristics of Two Waverider-Derived Hypersonic Cruise Configurations Charles E. Cockrell, Jr., Lawrence D. Huebner, and Dennis B. Finley July 1996 NASA Technical Paper 3559 Aerodynamic Characteristics of Two Waverider-Derived Hypersonic Cruise Configurations Charles E. Cockrell, Jr. and Lawrence D. Huebner Langley Research Center • Hampton, Virginia Dennis B. Finley Lockheed-Fort Worth Company • Fort Worth, Texas National Aeronautics and Space Administration Langley Research Center • Hampton, Virginia 23681-0001 July 1996 Available electronically at the following URL address: http:lltechreports.larc.nasa.govlltrslitrs.html Printed copies available from the following: NASA Center for AeroSpace Information National Technical Information Service (NTIS) 800 Elkridge Landing Road 5285 Port Royal Road Linthicum Heights, MD 21090-2934 Springfield, VA 22161-2171 (301) 621-0390 (703) 487-4650 Abstract An evaluation was made of the effects of integrating the required aircraft compo- nents with hypersonic high-lift configurations known as waveriders to create hyper- sonic cruise vehicles. Previous studies suggest that waveriders offer advantages in aerodynamic performance and propulsionairframe integration (PAl) characteristics over conventional non-waverider hypersonic shapes. A wind-tunnel model was devel- oped that integrates vehicle components, including canopies, engine components, and control surfaces, with two pure waverider shapes, both conical-flow-derived wave- riders for a design Mach number of 4.0. Experimental data and limited computational fluid dynamics (CFD) solutions were obtained over a Mach number range of 1.6 to 4.63. The experimental data show the component build-up effects and the aero- dynamic characteristics of the fully integrated configurations, including control sur- face effectiveness. -
Science & Technology Trends 2020-2040
Science & Technology Trends 2020-2040 Exploring the S&T Edge NATO Science & Technology Organization DISCLAIMER The research and analysis underlying this report and its conclusions were conducted by the NATO S&T Organization (STO) drawing upon the support of the Alliance’s defence S&T community, NATO Allied Command Transformation (ACT) and the NATO Communications and Information Agency (NCIA). This report does not represent the official opinion or position of NATO or individual governments, but provides considered advice to NATO and Nations’ leadership on significant S&T issues. D.F. Reding J. Eaton NATO Science & Technology Organization Office of the Chief Scientist NATO Headquarters B-1110 Brussels Belgium http:\www.sto.nato.int Distributed free of charge for informational purposes; hard copies may be obtained on request, subject to availability from the NATO Office of the Chief Scientist. The sale and reproduction of this report for commercial purposes is prohibited. Extracts may be used for bona fide educational and informational purposes subject to attribution to the NATO S&T Organization. Unless otherwise credited all non-original graphics are used under Creative Commons licensing (for original sources see https://commons.wikimedia.org and https://www.pxfuel.com/). All icon-based graphics are derived from Microsoft® Office and are used royalty-free. Copyright © NATO Science & Technology Organization, 2020 First published, March 2020 Foreword As the world Science & Tech- changes, so does nology Trends: our Alliance. 2020-2040 pro- NATO adapts. vides an assess- We continue to ment of the im- work together as pact of S&T ad- a community of vances over the like-minded na- next 20 years tions, seeking to on the Alliance. -
The Lapcat-Mr2 Hypersonic Cruiser Concept
THE LAPCAT-MR2 HYPERSONIC CRUISER CONCEPT J. Steelant and T. Langener* * ESA-ESTEC, Keplerlaan 1, 2201 AZ Noordwijk, Netherlands Vehicle Design, Hypersonic Flight, Combined Cycle Engine, Dual-Mode Ramjet Abstract thus bringing the elliptical combustor cross section to a circular cross-section. During Ramjet-mode, this This paper describes the MR2, a Mach 8 nozzle was used as a combustor that thermally cruise passenger vehicle, conceptually designed for choked, allowing for supersonic expansion in the antipodal flight from Brussels to Sydney in less than second nozzle. The second nozzle itself was 4 hours. This is one of the different concepts studied streamtraced from an axisymmetric isentropic within the LAPCAT II project [1]. It is an evolution expansion and truncated to a suitable length. Both of a previous vehicle, the MR1 based upon a dorsal nozzles were designed for cruise conditions. mounted engine, as a result of multiple optimization The final vehicle is shown below in Figure 1 iterations [2] leading to the MR2.4 concepts. The while specific details of the design are expanded main driver was the optimal integration of a high upon in the next section. performance propulsion unit within an aerodynamically efficient wave rider design, whilst guaranteeing sufficient volume for tankage, payload and other subsystems. Introduction The aerodynamics for the MR2 is a waverider form based upon an adapted osculating cone method enabling to construct the vehicle from the leading edge while reducing integration problems between the aerodynamics and the intake. The intake was constructed using Figure 1 MR2 Vehicle streamtracing methods from an axisymmetric inward turning compression surface and was integrated on top of the waverider in a dorsal layout. -
From Leo to the Planets Using Waveriders
AlAA, 99-4803 From Leo. to th.e Planets Using Waveriders ‘. A. D. McRonald,J1 E. Randolph., Jet PropulsionLaboratory CaliforniaInstitute of Technology. M.‘J. Lewis Universityof Maryland E. p. Bbnfiglio,J:Longuski .- PurdueUn iversity I’ P.Kolodziej NASA-AmesResearch Center th International’ Space Planes and Hypersonic Systems arid Technologies Conference. and _ 3rd Weakly Ionized-Gases Workshop l-5. November 1’999 Norfolk, VA For permiss/on to copy or republish, contact the American Institute of Aeronautics and Astronautics 1801 Alexander Bell Drive, Suite 500, Reston, VA 20191 (c)l999 American Institute of Aeronautics & Astronautic‘s or publisher! with permission of author(s) and/or authdr(s)’ sponsoring organization. t i AIAA-99-4803 . FROM LEO TO THE PLANETS USING WAVERIDERS A. D. McRonald, J. E. Randolph Jet PropulsionLaboratory California Institute of Technology. M. J. Lewis University of Maryland E. P. Bonfiglio, J. Longuski PurdueUniversity P.Kolodziej Ames ResearchCenter ABSTRACT control surfaces, along with engines and propellant to escapefrom Earth, Other advantagesof this A revolution& interplanetary transportation techniqueover normalinterplanetary delivery methods techniqueknown as Aero-Gravity Assist (AGA) has will be discussed. beenstudied by JPL and others to enablerelatively, short trip times betweenEarth andthe other planets. INTRODUCTION AND BACKGROUND It takes advantageof an advancedhypersonic vehicle known as a waverider that uses its high lift to fly The idea to employ the terrestrialplanets as an energy through the atmospheresof Venus and Mars to sourceusing aero-gravity-assist(AGA) maneuversto provide exceptionally large velocity changesusing significantly increasethe velocity of interplanetary gravity-assist maneuvers. The concept has been spacecraft was first discussed for the Stat-probe understudy in a joint programbetween JPL and the mission to the sun] in 1982. -
Design Processes and Criteria for the X-51A Flight Vehicle Airframe
UNCLASSIFIED/UNLIMITED Design Processes and Criteria for the X-51A Flight Vehicle Airframe Jeffery Lane Boeing Integrated Defense Systems 5301 Bolsa Ave. M/C H010-B017 Huntington Beach, CA 92647 USA [email protected] ABSTRACT Flight vehicle airframes in today’s advanced flight systems are required to optimally integrate a variety of multi-functional requirements to maximize effectiveness with acceptable risk. The X-51A airframe design process and criteria draw upon decades of successful design of both manned and unmanned flight vehicles for production and experimental intent. This paper summarizes the X-51A vehicle mission requirements, system design, design processes used for airframe synthesis, design safety factors, success criteria and issues facing the incorporation of advanced optimization techniques in the development of airframes for vehicles such as the X-51A. 1.0 INTRODUCTION The X-51A program is a jointly funded project sponsored by two US government agencies: the Air Force Research Laboratory (AFRL) and the Defense Advanced Research Projects Agency (DARPA) with AFRL as the lead project office [1]. The fundamental objective of the X-51A flight test program is to flight demonstrate the USAF Hypersonic Technology (HyTech) scramjet engine being developed by Pratt & Whitney Rocketdyne under contract to the AFRL (Figure 1). The scramjet engine is based on a hydrocarbon fuel that ignites and operates in both acceleration and cruise modes in the Mach 4.5 to 6.5 range. The engine flowpath is cooled using fuel to both maintain tolerable flowpath temperatures as well as “crack” the fuel to facilitate ignition once it is injected into the combustion region of the scramjet engine. -
Flying Machines of the Future
Flying machines of the future Boeing’s Phantom s a massive hybrid neutrally the stuff of science fiction? No. Just buoyant aircraft delivers oversized a glimpse at some of the capabilities and Works looks into the A pipeline equipment north of the applications of projects in various stages future to come up with Arctic Circle, a homeowner uses the of development by employees of Phantom Internet to check the cheapest time to Works, the division of Boeing Defense, some ‘pretty cool stuff’ run a load of laundry. Space & Security charged with advanced by Marc Sklar At 65,000 feet (19,800 meters) over development. With a team of only about a battlefield, a liquid-hydrogen-powered 2,000 employees, Phantom Works has aircraft keeps tabs on troop movements numerous programs and initiatives going GRAPHICS: (Above) the Phantom Ray and helps control unmanned attack at any one time in fields as varied as unmanned flying test bed, shown in an artist’s concept, is 36 feet (11 meters) long aircraft flying from carriers 500 miles aviation, space, energy management, with a wingspan of 50 feet (15 meters). It (800 kilometers) offshore. and military and intelligence operations. is scheduled for systems, ground and flight officials in a major city monitor “What we do is look into the future tests this year. MICK MONAHAN/BOEING massive security operations for a global and work with our customers to determine (Right) Phantom Works and SkyHook sports event, while hundreds of miles where capability gaps may exist,” said International are developing this neutrally above, nanosatellites—each the size Darryl Davis, Phantom Works president. -
System Design and Optimization of a Hypersonic Launch Vehicle
System Design and Optimization of a Hypersonic Launch Vehicle A project present to The Faculty of the Department of Aerospace Engineering San Jose State University in partial fulfillment of the requirements for the degree Master of Science in Aerospace Engineering By Matthew Ringle May 2014 approved by Dr. Papadopoulos Faculty Advisor TABLE OF CONTENTS Table of Contents .......................................................................................................................... 1 List of Figures ................................................................................................................................ 3 List Of Tables ................................................................................................................................ 4 1.0 Literature Review ................................................................................................................... 5 1.1 Background ...................................................................................................................... 5 1.2 Waverider ......................................................................................................................... 6 1.3 Winged Bodies .................................................................................................................. 6 1.4Blunt Reentry Bodies ....................................................................................................... 7 2.0 Problem Statement................................................................................................................. -
Performance Analysis of Skip-Glide Trajectories for Hypersonic Waveriders in Planetary Exploration
University of Tennessee, Knoxville TRACE: Tennessee Research and Creative Exchange Masters Theses Graduate School 5-2008 Performance Analysis of Skip-Glide Trajectories for Hypersonic Waveriders in Planetary Exploration Ngoc-Thuy Dang Nguyen University of Tennessee - Knoxville Follow this and additional works at: https://trace.tennessee.edu/utk_gradthes Part of the Aerospace Engineering Commons Recommended Citation Nguyen, Ngoc-Thuy Dang, "Performance Analysis of Skip-Glide Trajectories for Hypersonic Waveriders in Planetary Exploration. " Master's Thesis, University of Tennessee, 2008. https://trace.tennessee.edu/utk_gradthes/416 This Thesis is brought to you for free and open access by the Graduate School at TRACE: Tennessee Research and Creative Exchange. It has been accepted for inclusion in Masters Theses by an authorized administrator of TRACE: Tennessee Research and Creative Exchange. For more information, please contact [email protected]. To the Graduate Council: I am submitting herewith a thesis written by Ngoc-Thuy Dang Nguyen entitled "Performance Analysis of Skip-Glide Trajectories for Hypersonic Waveriders in Planetary Exploration." I have examined the final electronic copy of this thesis for form and content and recommend that it be accepted in partial fulfillment of the equirr ements for the degree of Master of Science, with a major in Aerospace Engineering. Gary A. Flandro, Major Professor We have read this thesis and recommend its acceptance: Kenneth R. Kimble, John S. Steinhoff Accepted for the Council: Carolyn R. Hodges -
High Pressure Zone Capture Wing Configuration for High Speed Air Vehicles
APCOM & ISCM 11-14th December, 2013, Singapore High Pressure Zone Capture Wing Configuration for High Speed Air Vehicles *K. Cui, G.L. Li, S.C. Hu, Z.P. Qu State Key Laboratory of High Temperature Gas Dynamics, Institute of Mechanics, CAS, Beijing 100190, China *Corresponding author: [email protected] Abstract To aim at design requirements of large capacity, high lift, low drag, and high lift-to-drag ratio for high air vehicles, a new aerodynamic configuration concept, named high pressure zone capture wing (HCW) configuration is firstly proposed in this paper. By comparison with traditional lift body or waverider configurations, the new feature of the HCW configuration is to introduce a surface wing, which is upon the airframe of the vehicle and paralleled with the free stream. In high speed cruising conditions, the HCW can capture the high pressure zone compressed by the upper surface of the vehicle. Thus the lift of the vehicle can get a considerable compensation due to the large pressure difference between the upper and the lower surface of the HCW. The lift-to-drag ratio can also obtain a large improvement as a result. Besides, the increase of the volume and the weight of the vehicle will lead to higher lift of the HCW. Therefore, a self-compensation effect between the lift and the weight of the vehicle is achieved. The theoretical derivation is made in the two-dimensional condition and some three-dimensional conceptual configurations are designed. Their aerodynamic performances were as well as evaluated by computational fluid dynamics. The results clearly demonstrate the high performance of the HCW configuration. -
Tackling the Extreme Challenges of Air-Breathing Hypersonic Vehicle Design, Technology, and Flight
Tackling the Extreme Challenges of Air-Breathing Hypersonic Vehicle Design, Technology, and Flight Mathematics, Computing & Design Symposium Honoring Antony Jameson’s 80 th Birthday Stanford University, CA 21 November, 2014 Dr. Kevin G. Bowcutt Senior Technical Fellow Chief Scientist of Hypersonics The Boeing Company BOEING is a trademark of Boeing Management Company. Copyright © 2014 Boeing. All rights reserved. VKI STO-AVT-234 | 3/26/2014 | 1 Past Hypersonics – Rocket-Boosted Gliders Engineering, Operations & Technology | Boeing Research & Technology Platform Performance Technology X-15 Rocket Plane Space Shuttle Orbiter Space Capsules Ballistic Reentry Vehicles BOEING is a trademark of Boeing Management Company. Copyright © 2014 Boeing. All rights reserved. VKI STO-AVT-234 | 2 Extremely High Boost Speed Required to Glide Across Continents or Oceans Engineering, Operations & Technology | Boeing Research & Technology Platform Performance Technology BOEING is a trademark of Boeing Management Company. Copyright © 2014 Boeing. All rights reserved. VKI STO-AVT-234 | 3 Present and Future Hypersonics – The Development and Application of Hypersonic Air-Breathing Propulsion Engineering, Operations & Technology | Boeing Research & Technology Platform Performance Technology High Speed Missiles High Speed A/C Affordable Space Access Large (10-20 klb) Small (100-500 lb) Mach 5-7 Cruise Mach 10-20 Glide Mach 6-7 Cruise Payload Payload • Hundreds of miles in • Global range • Routine and affordable minutes/global range in in ~ 2 hours space launch under an hour • High utilization • Lighter weight permits • High kinetic energy rate horizontal takeoff • Increased survivability • Aircraft-like operations and maintenance • Throttling provides flexible operation • Operational flexibility and safety BOEING is a trademark of Boeing Management Company. Copyright © 2014 Boeing. -
Brazilian 14-X Hypersonic Waverider Scramjet Aerospace Vehicle Dimensional Design at Mach Number 10
ISSN 2176-5480 22nd International Congress of Mechanical Engineering (COBEM 2013) November 3-7, 2013, Ribeirão Preto, SP, Brazil Copyright © 2013 by ABCM BRAZILIAN 14-X HYPERSONIC WAVERIDER SCRAMJET AEROSPACE VEHICLE DIMENSIONAL DESIGN AT MACH NUMBER 10 Felipe Jean da Costa Instituto Tecnológico de Aeronáutica/ITA - Praça Marechal Eduardo Gomes, nº 50 Vila das Acácias CEP. 12.228-900 São José dos Campos, SP - Brasil [email protected] Paulo Gilberto de Paula Toro Tiago Cavalcanti Rolim Giannino Ponchio Camillo Instituto de Estudos Avançados/IEAv - Trevo Coronel Aviador José Alberto Albano do Amarante, nº1 Putim CEP. 12.228-001 São José dos Campos, SP - Brasil. [email protected] [email protected] [email protected] Abstract. The 14-X Hypersonic Aerospace Vehicle, VHA 14-X, designed at the Prof. Henry T. Nagamatsu Laboratory of Aerothermodynamics and Hypersonic, at the Institute for Advanced Studies (IEAv), is part of the continuing effort of the Department of Aerospace Science and Technology (DCTA), to develop a technological demonstrator using: i) “waverider” technology to provide lift to the aerospace vehicle, and ii) “scramjet” technology to provide hypersonic airbreathing propulsion system based on supersonic combustion. Aerospace vehicle using “waverider” technology obtains lift using the shock wave, formed during supersonic/hypersonic flight through the Earth´s atmosphere, which originates at the leading edge and it is attached to the bottom surface of the vehicle, generating a region of high pressure, resulting in high lift and low drag. Atmospheric air, pre-compressed by the shock wave, which lies between the shock wave and the leading edge of the vehicle may be used in hypersonic airbreathing propulsion system based on ”scramjet” technology. -
On the Low Speed Longitudinal Stability of Hypersonic Waveriders
On the Low Speed Longitudinal Stability of Hypersonic Waveriders A Thesis submitted to the University of Sydney for the Degree of Doctor of Philosophy, from the School of Aerospace, Mechanical & Mechatronic Engineering Jonathan J. Jeyaratnam SID: May 2020 Abstract The development of hypersonic civilian transport aircraft requires solutions to a num- ber of challenging problems in the areas of aerothermodynamics, control, aeroelasticity, propulsion and many others encountered at high Mach number flight. The majority of research into hypersonic vehicle design has therefore rightly focused on solutions to these issues. The desire for good aerodynamic performance at high Mach numbers, most often defined by the lift to drag ratio, results in slender vehicle designs which minimise drag and take advantage of compression lift through attached shock waves along the leading edge. These so-called waverider designs show good promise for high aerody- namic efficiency and potential for long range transport applications. However a civilian transport aircraft that travels at hypersonic speeds requires satisfactory stability and handling qualities across the entire flight trajectory. The stability and handling of wa- verider shapes at the low speeds encountered at the take-off and landing phases of flight is not well studied. The stability of an aircraft is characterised by the aerodynamic stability derivatives. Only a few existing studies have looked at these low speed derivatives for waverider designs and no research has been found on the dynamic damping derivatives even though these are important to characterising the handling qualities of a vehicle. The work presented here covers the use of various high fidelity methods to extract these derivatives for a particular vehicle, the Hexafly-Int hypersonic glider.