STABILIZATION of Β-CRISTOBALITE in the Sio2-Alpo4-BPO4 SYSTEM
Total Page:16
File Type:pdf, Size:1020Kb
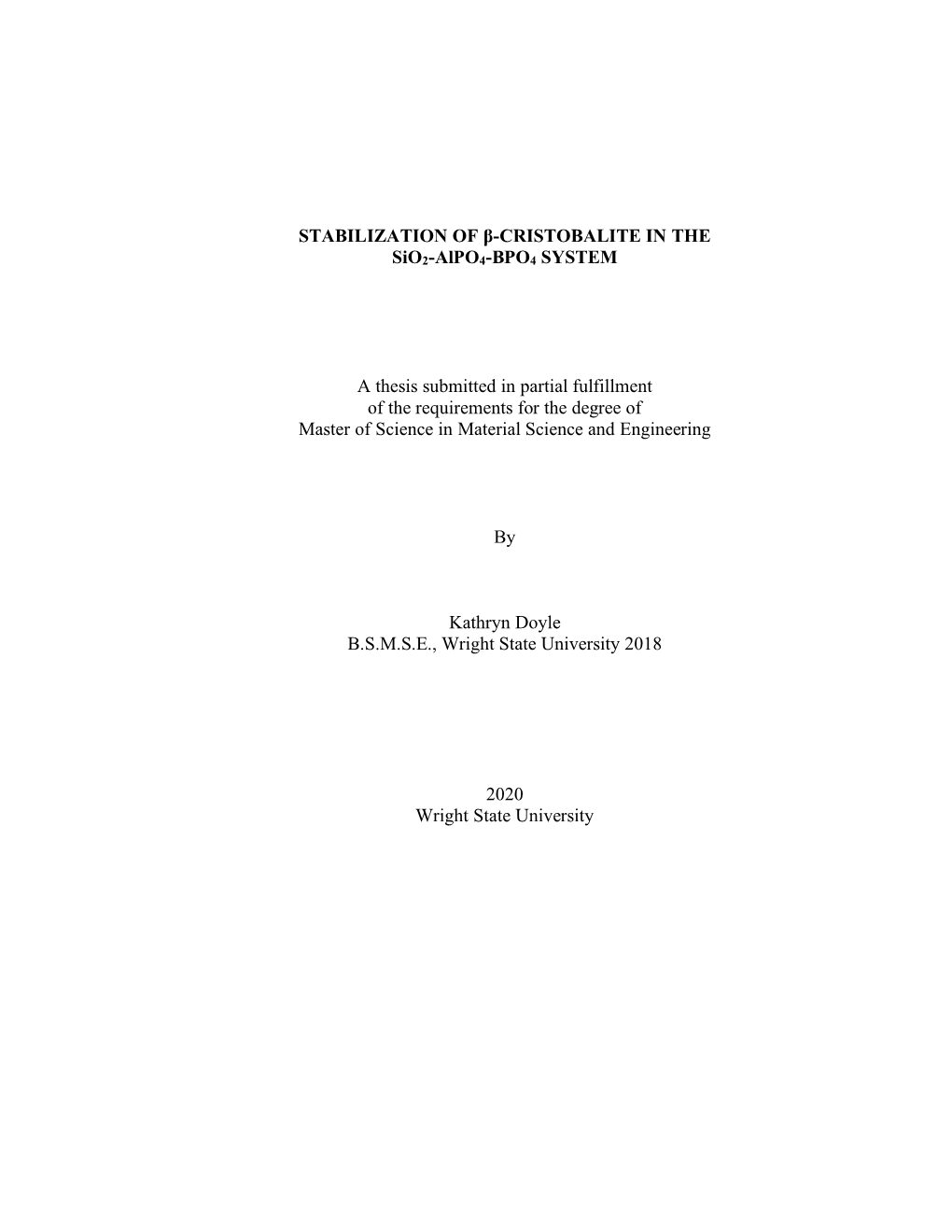
Load more
Recommended publications
-
Crystalline Silica, Cristobalite (CAS No
Crystalline Silica, Quartz (CAS No. 14808-60-7) Crystalline Silica, Cristobalite (CAS No. 14464-46-1) Crystalline Silica, Tridymite (CAS No. 15468-32-3) Diatomaceous earth (CAS No. 61790-53-2) This dossier on crystalline silica, quartz, cristobalite and tridymite and diatomaceous earth presents the most critical studies pertinent to the risk assessment of these substances in their use in drilling muds and cement additives. This dossier does not represent an exhaustive or critical review of all available data. The majority of information presented in this dossier was obtained from the ECHA database that provides information on chemicals that have been registered under the EU REACH (ECHA). Where possible, study quality was evaluated using the Klimisch scoring system (Klimisch et al., 1997). For the purpose of this dossier, crystalline silica, quartz (CAS No. 14808-60-7) has been reviewed as representative of crystalline silica cristobalite and tridymite. Crystalline silica, quartz is also considered representative of diatomaceous earth, as they both consist mainly of silicon dioxide. Screening Assessment Conclusion – Crystalline silica, quartz, cristobalite and tridymite and diatomaceous earth are classified as tier 1 chemicals and require a hazard assessment only. 1 BACKGROUND Crystalline silica is a common mineral found in the earth's crust. Materials like sand, stone, concrete and mortar contain crystalline silica. It is also used to make products such as glass, pottery, ceramics, bricks and artificial stone. Silica, in the form of sand, is used as the main ingredient in sand casting for the manufacture of metallic components in engineering and other applications. The high melting point of silica enables it to be used in such applications. -
Understanding the Art of Quartz
AIA & IDCEC Continuing Education Program UNDERSTANDING THE ART OF QUARTZ PRESENTED BY: AND 1 Hanwha L&C | Surfaces is a Registered Provider with The American Institute of Architects Continuing Education Systems (AIA/CES) and Interior Designers Continuing Education Council (IDCEC). Credit(s) earned on completion of this program will be reported to AIA/CES for AIA members or to IDCEC for IIDA, ASID or IDC members. Certificates of Completion for both members and non- members are available upon request. This program is registered with AIA/CES and IDCEC for continuing professional education. As such, it does not include content that may be deemed or construed to be an approval or endorsement by the AIA or the IDCEC of any material of construction or any method or manner of handling, using, distributing or dealing in any material or product. Questions related to specific materials, methods and services will be addressed at the conclusion of this presentation. This presentation is protected by US and International copyrights laws. Reproduction, distribu- tion, display and use of the presentation without written permission of the speaker is prohibited. Hanwha L&C | Surfaces 2016. 2 AIA & IDCEC Continuing Education Program ∆ Format: Presented f2f in real-time ∆ Course Credit: ◊ AIA: 1 Learning Unit (LU) ◊ Course #: 004QS ◊ IDCEC: .1 Health & Safety ◊ Course #: 40276 ◊ RAIC: 1 Self-Reporting Hour Δ Completion Certificate: ◊ A copy will be provided to you by email, fax, or mail upon request. 3 Learning Objectives ∆ Gain knowledge about natural quartz surfacing: ◊ Composition and Uses ◊ Product Characteristics ◊ Manufacturing and Fabrication ◊ Application and Design Options 4 INTRODUCTION TO QUARTZ Quartz Facts ∆ Quartz is the 4th hardest crystalline mineral on Earth, and it is found abundantly all over the world in a variety of forms. -
Fall 2015 Gems & Gemology
FALL 2015 VOLUME LI THE UARTERLY JOURNAL OF THE GEMOLOGICAL INSTITUTE OF AMERICA Colombian Trapiche Emeralds Large Colorless HPHT-Grown Synthetic Diamonds Diamonds from the Letšeng Mine Fall 2015 VOLUME 51, No. 3 EDITORIAL 221 Trapiche and More... Duncan Pay FEATURE ARTICLES 222 Colombian Trapiche Emeralds: Recent Advances in Understanding Their Formation Isabella Pignatelli, Gaston Giuliani, Daniel Ohnenstetter, Giovanna Agrosì, pg. 254 Sandrine Mathieu, Christophe Morlot, and Yannick Branquet Proposes a model for trapiche emerald formation based on petrographic, spectroscopic, and chemical examination. 260 Large Colorless HPHT-Grown Synthetic Gem Diamonds from New Diamond Technology, Russia Ulrika F.S. D’Haenens-Johansson, Andrey Katrusha, Kyaw Soe Moe, Paul Johnson, and Wuyi Wang pg. 270 Examines a new source of colorless and near-colorless gem-quality HPHT synthetic diamonds using spectroscopic and gemological analysis. 280 Letšeng’s Unique Diamond Proposition Russell Shor, Robert Weldon, A.J.A. (Bram) Janse, Christopher M. Breeding, and Steven B. Shirey Explores the history, geology, and current production of this unique source of large diamonds. NOTES AND NEW TECHNIQUES 300 Origin Determination of Dolomite-Related White Nephrite through Iterative-Binary Linear Discriminant Analysis Zemin Luo, Mingxing Yang, and Andy H Shen A technique for origin identification based on statistical analysis and LA-ICP-MS spectrometry. pg. 293 REGULAR FEATURES 312 Lab Notes Unusual graining structure in pink diamond • Yellow HPHT-treated rough diamond -
Minnesota's Mineral Resources
CHAPTER • 9 Minnesota's Mineral Resources IN MINNESOTA the production of iron ore is far more valuable economically than the total of all other mineral products, but im portant industries are based on Minnesota's other geological forma tions as well. Architectural, monumental, and structural stone are produced from granite, limestone, dolomite, and other Minnesota rocks. Gravel and sand are excavated and processed, and clay is used for many ceramic products. :Manganese in important amounts occurs in the iron ores of the Cuyuna district. Finally, although they are often not thought of as mineral products, two of our most im portant mineral resources are water and soil. The iron ores and mining operations of the Mesabi, Vermilion, and Cuyuna iron-bearing districts and of the southeastern lYlinnesota counties will be discussed in detail in later chapters, but a few sta tistics on Minnesota's iron ore industry may remind us how impor tant this geological heritage is. The following is an estimate of Min nesota's iron ore reserves, made on lYlay 1, 1961: Gross Tons Mesabi Range 500,799,179 Vermilion Range 9,755,974 Cuyuna Range 36,530,000 Fillmore County 'il,860,337 Total iron ore 549,945,490 172 MI NESOTA'S MINERAL RESOURCES The total production of iron ore in Minne ota to January 1, 1962, was 2,529,737,553 tons. Total taxes paid on iron ore to January 1, 1961 , were approximately $1,257,448,400, a very important source of funds for the state government. Slightly over 60 per cent of the total iron ore produced in the United States has come from l\1inne- ota. -
Symposium on Agate and Cryptocrystalline Quartz
Symposium on Agate and Cryptocrystalline Quartz September 10 – 13, 2005 Golden, Colorado Sponsored by Friends of Mineralogy, Colorado Chapter; Colorado School of Mines Geology Museum; and U.S. Geological Survey 2 Cover Photos {top left} Fortification agate, Hinsdale County, Colorado, collection of the Geology Museum, Colorado School of Mines. Coloration of alternating concentric bands is due to infiltration of Fe with groundwater into the porous chalcedony layers, leaving the impermeable chalcedony bands uncolored (white): ground water was introduced via the symmetric fractures, evidenced by darker brown hues along the orthogonal lines. Specimen about 4 inches across; photo Dan Kile. {lower left} Photomicrograph showing, in crossed-polarized light, a rhyolite thunder egg shell (lower left) a fibrous phase of silica, opal-CTLS (appearing as a layer of tan fibers bordering the rhyolite cavity wall), and spherulitic and radiating fibrous forms of chalcedony. Field of view approximately 4.8 mm high; photo Dan Kile. {center right} Photomicrograph of the same field of view, but with a 1 λ (first-order red) waveplate inserted to illustrate the length-fast nature of the chalcedony (yellow-orange) and the length-slow character of the opal CTLS (blue). Field of view about 4.8 mm high; photo Dan Kile. Copyright of articles and photographs is retained by authors and Friends of Mineralogy, Colorado Chapter; reproduction by electronic or other means without permission is prohibited 3 Symposium on Agate and Cryptocrystalline Quartz Program and Abstracts September 10 – 13, 2005 Editors Daniel Kile Thomas Michalski Peter Modreski Held at Green Center, Colorado School of Mines Golden, Colorado Sponsored by Friends of Mineralogy, Colorado Chapter Colorado School of Mines Geology Museum U.S. -
Stishovite and Seifertite in Lunar Meteorite Northwest Africa 4734
71st Annual Meteoritical Society Meeting (2008) 5058.pdf FIRST EVIDENCE OF HIGH PRESSURE SILICA: STISHOVITE AND SEIFERTITE IN LUNAR METEORITE NORTHWEST AFRICA 4734. H. Chennaoui Aoudjehane1-2, A. Jambon2 1Université Hassan II Aïn Chock, Laboratoire Géosciences, BP 5366 Maârif Casa- blanca Morocco (e-mail: [email protected]), 2Université Pierre et Marie Curie-Paris6 and IPGP Laboratoire MAGIE, Case 110, 4 place Jussieu, 75252 Paris France. Introduction: Silica is a rare phase in lunar rocks; it has been described as either quartz, cristobalite and/or tridymite [1]. Northwest Africa 4734, is an uncommon type of lunar rock, which may be launched paired with the LaPaz Icefield Lunar Mare basalts found in 2002-03 in Antarctica [2-6], it is a coarse grained rock of basaltic composition, exhibits a number of sig- nificant shock features, such as PDFs, extensive fracturation of pyroxene, impact melt pockets and transformation of plagioclase to maskelynite; silica is present as a minor phase. Analytical procedures: We studied the speciation of silica polymorphs to characterize the shock, using SEM imaging, Ra- man spectroscopy, CL imaging and spectroscopy. Further details can be found in [7]. Results: According to the CL spectra [7-9], cristobalite, tridymite, high-pressure silica glass, stishovite and seifertite, are all present. Special emphasis is made on stishovite and seifertite, which, like in shergottites, exhibit specific textural features [7]. Cathodoluminescence spectra characteristic of high-pressure sil- ica phases: glass, stishovite and seifertite have been recorded in addition to the original low-pressure phases. The remanence of cristobalite and tridymite underscores a significant heterogeneity of the shock supported by the rock. -
Long Suspected Theory About the Moon Holds Water 14 June 2018
Long suspected theory about the moon holds water 14 June 2018 Moganite was found in only one of those 13 samples, confirming the team's theory that it could not have formed in the African desert. "If terrestrial weathering had produced moganite in the lunar meteorite, there should be moganite present in all the samples that fell to Earth around the same time. But this was not the case," says Kayama. Photograph of lunar meteorite NWA 2727. Credit: Masahiro Kayama, Tohoku University A team of Japanese scientists led by Masahiro Kayama of Tohoku University's Frontier Research Institute for Interdisciplinary Sciences, has discovered a mineral known as moganite in a lunar Sectional photograph of lunar meteorite NWA 2727. meteorite found in a hot desert in northwest Africa. Credit: Masahiro Kayama, Tohoku University This is significant because moganite is a mineral that requires water to form, reinforcing the belief that water exists on the Moon. He adds that part of the moganite had changed into the high-pressure SiO2 minerals stishovite and "Moganite is a crystal of silicon dioxide and is coesite, which he believes was most likely formed similar to quartz. It forms on Earth as a precipitate through heavy impact collisions on the Moon when alkaline water including SiO2 is evaporated under high pressure conditions," says Kayama. This is the first time that moganite has been "The existence of moganite strongly implies that detected in lunar rocks. The researchers say the there is water activity on the Moon." meteorites probably came from an area of the Moon called Procellarum Terrane, and that the Kayama and his team analyzed 13 of the lunar moganite was formed through the process of water meteorites using sophisticated methods to evaporation in strong sunlight. -
Moon Minerals a Visual Guide
Moon Minerals a visual guide A.G. Tindle and M. Anand Preliminaries Section 1 Preface Virtual microscope work at the Open University began in 1993 meteorites, Martian meteorites and most recently over 500 virtual and has culminated in the on-line collection of over 1000 microscopes of Apollo samples. samples available via the virtual microscope website (here). Early days were spent using LEGO robots to automate a rotating microscope stage thanks to the efforts of our colleague Peter Whalley (now deceased). This automation speeded up image capture and allowed us to take the thousands of photographs needed to make sizeable (Earth-based) virtual microscope collections. Virtual microscope methods are ideal for bringing rare and often unique samples to a wide audience so we were not surprised when 10 years ago we were approached by the UK Science and Technology Facilities Council who asked us to prepare a virtual collection of the 12 Moon rocks they loaned out to schools and universities. This would turn out to be one of many collections built using extra-terrestrial material. The major part of our extra-terrestrial work is web-based and we The authors - Mahesh Anand (left) and Andy Tindle (middle) with colleague have build collections of Europlanet meteorites, UK and Irish Peter Whalley (right). Thank you Peter for your pioneering contribution to the Virtual Microscope project. We could not have produced this book without your earlier efforts. 2 Moon Minerals is our latest output. We see it as a companion volume to Moon Rocks. Members of staff -
Origin of Fibrosity and Banding in Agates from Flood Basalts: American Journal of Science, V
Agates: a literature review and Electron Backscatter Diffraction study of Lake Superior agates Timothy J. Beaster Senior Integrative Exercise March 9, 2005 Submitted in partial fulfillment of the requirements for a Bachelor of Arts degree from Carleton College, Northfield, Minnesota. 2 Table of Contents AGATES: A LITERATURE REVEW………………………………………...……..3 Introduction………………....………………………………………………….4 Structural and compositional description of agates………………..………..6 Some problems concerning agate genesis………………………..…………..11 Silica Sources…………………………………………..………………11 Method of Deposition………………………………………………….13 Temperature of Formation…………………………………………….16 Age of Agates…………………………………………………………..17 LAKE SUPERIOR AGATES: AN ELECTRON BACKSCATTER DIFFRACTION (EBSD) ANALYSIS …………………………………………………………………..19 Abstract………………………………………………………………………...19 Introduction……………………………………………………………………19 Geologic setting………………………………………………………………...20 Methods……………………………………………………...…………………20 Results………………………………………………………….………………22 Discussion………………………………………………………………………26 Conclusions………………………………………………….…………………26 Acknowledgments……………………………………………………..………………28 References………………………………………………………………..……………28 3 Agates: a literature review and Electron Backscatter Diffraction study of Lake Superior agates Timothy J. Beaster Carleton College Senior Integrative Exercise March 9, 2005 Advisor: Cam Davidson 4 AGATES: A LITERATURE REVEW Introduction Agates, valued as semiprecious gemstones for their colorful, intricate banding, (Fig.1) are microcrystalline quartz nodules found in veins and cavities -
John S. White Mineral and Gem Collections GENERAL Nephrite Boulder – Trinity County, California Pyrite Navajun, Logroño, Spain 20-11-3
John S. White Mineral and Gem Collections GENERAL Nephrite boulder – Trinity County, California Pyrite Navajun, Logroño, Spain 20-11-3 12 cm Figured specimen (12) Beryl var. emerald – Crabtree Mountain emerald mine, Mitchell Co., N.C. G5-9-12 5 cm Ocean jasper – Cabamby mine, Majunga, Madagascar – G10-9-1 4.3 cm Ocean jasper – Cabamby mine, Majunga, Madagascar G11-2-3 4 cm Andalusite, variety chiastolite – China 10-2-43 2.7 cm Graphic granite – Madagascar 17-9-3 4.5 cm Garnet color suite – mixed localities G8-11-1 Sasha Siemel Beryl Jaguar hunter Governador Valadares & Minas Gerais, Brazil Mineral dealer 19-4-2 & 19-5-4 These specimens were sold by Sasha Siemel to friends of mine at a mineral show in Doylestown, PA, 1956 Gas bubble in fluorite Cave-in-Rock, Illinois 4-12-3 Russell Feather photo Regional Collection Pennsylvania – Maryland - Virginia Magnetite – Grace mine, Morgantown, PA 4-6-1 6.5 cm Rutile – Parkesburg, Chester County, PA 3-9-16 5 cm Dolomite - Ober & Binkley quarry, E. Petersburg, Lancaster Co., PA 17-2-6 10.5 cm Pyromorphite – Wheatley mine, Phoenixville, Chester Co., PA 6-6-9 9 cm Analcime & Apophyllite – Cornwall mine, Cornwall, Lebanon County, PA 20-10-15 10 cm Quartz – Reading anthracite mine, near St. Clair, Schuykill Co., PA 19-9-7 10 cm Fluorapatite & Actinolite – Silver Hill quarry, Brecknock Twp., Lancaster Co., PA 18-2-18 11.5 cm Wavellite – Mt. Pleasant Mills quarry, Perry Twp., Snyder Co., PA 18-2-19 4 cm Strontianite – Oak Hill quarry, Centre County, PA 21-11-1 5.5 cm Strontianite – Tonoloway limestone, Mt. -
Cristobalite Sio2 C 2001 Mineral Data Publishing, Version 1.2 ° Crystal Data: Tetragonal, Pseudocubic
Cristobalite SiO2 c 2001 Mineral Data Publishing, version 1.2 ° Crystal Data: Tetragonal, pseudocubic. Point Group: 422: As pseudo-octahedral crystals, to 4 mm, with 110 and 331 , rarely pseudocubic. Commonly dendritic to skeletal; as spherulites to sefveragl cm; ¯fbrougs or microcrystalline (\opal"), massive. Twinning: On 111 , common, interpenetrant, polysynthetic, repeated. f g Physical Properties: Tenacity: Brittle. Hardness = 6{7 D(meas.) = 2.32{2.36 D(calc.) = 2.33 Optical Properties: Transparent. Color: Colorless, white, milky white to yellowish; in transmitted light, colorless. Luster: Vitreous. Optical Class: Uniaxial ({). ! = 1.487 ² = 1.484 Cell Data: Space Group: P 41212: a = 4.9709(1) c = 6.9278(2) Z = 4 X-ray Powder Pattern: Synthetic. 4.05 (100), 2.485 (20), 2.841 (13), 3.135 (11), 1.870 (7), 2.465 (5), 2.118 (5) Chemistry: (1) SiO2 [99.13] TiO2 0.38 Al2O3 0.18 FeO 0.09 MnO < 0.02 MgO < 0.03 CaO < 0.02 Na2O 0.05 K2O 0.17 P2O5 < 0.03 Total [100.00] (1) Mare Imbrium, Moon; by electron microprobe, SiO2 by di®erence. Polymorphism & Series: Quartz, tridymite, coesite, and stishovite are polymorphs; inverts from high- or ¯-cristobalite at 268 ±C or below. Occurrence: In vesicles and lithophysae; a late-crystallizing phase in basaltic to rhyolitic volcanic rocks; from acid-sulfate-type hydrothermal alteration of volcanic rocks; precipitated by hot springs. By contact metamorphism of sandstone; developed during diagenesis, recrystallized from siliceous sedimentary rocks. Association: Tridymite, quartz, sanidine, anorthoclase, fayalite, magnetite, kaolinite, alunite, \opal." Distribution: On Cerro San Crist¶obal, near Pachuca, Hidalgo, and in the Sant¶³n mine, Santa Caterina, Guanajuato, Mexico. -
Appendix a Recovery of Ejecta Material from Confirmed, Probable
Appendix A Recovery of Ejecta Material from Confirmed, Probable, or Possible Distal Ejecta Layers A.1 Introduction In this appendix we discuss the methods that we have used to recover and study ejecta found in various types of sediment and rock. The processes used to recover ejecta material vary with the degree of lithification. We thus discuss sample processing for unconsolidated, semiconsolidated, and consolidated material separately. The type of sediment or rock is also important as, for example, carbonate sediment or rock is processed differently from siliciclastic sediment or rock. The methods used to take and process samples will also vary according to the objectives of the study and the background of the investigator. We summarize below the methods that we have found useful in our studies of distal impact ejecta layers for those who are just beginning such studies. One of the authors (BPG) was trained as a marine geologist and the other (BMS) as a hard rock geologist. Our approaches to processing and studying impact ejecta differ accordingly. The methods used to recover ejecta from unconsolidated sediments have been successfully employed by BPG for more than 40 years. A.2 Taking and Handling Samples A.2.1 Introduction The size, number, and type of samples will depend on the objective of the study and nature of the sediment/rock, but there a few guidelines that should be followed regardless of the objective or rock type. All outcrops, especially those near industrialized areas or transportation routes (e.g., highways, train tracks) need to be cleaned off (i.e., the surface layer removed) prior to sampling.