Industrial Feedforward Control Technology: a Review
Total Page:16
File Type:pdf, Size:1020Kb
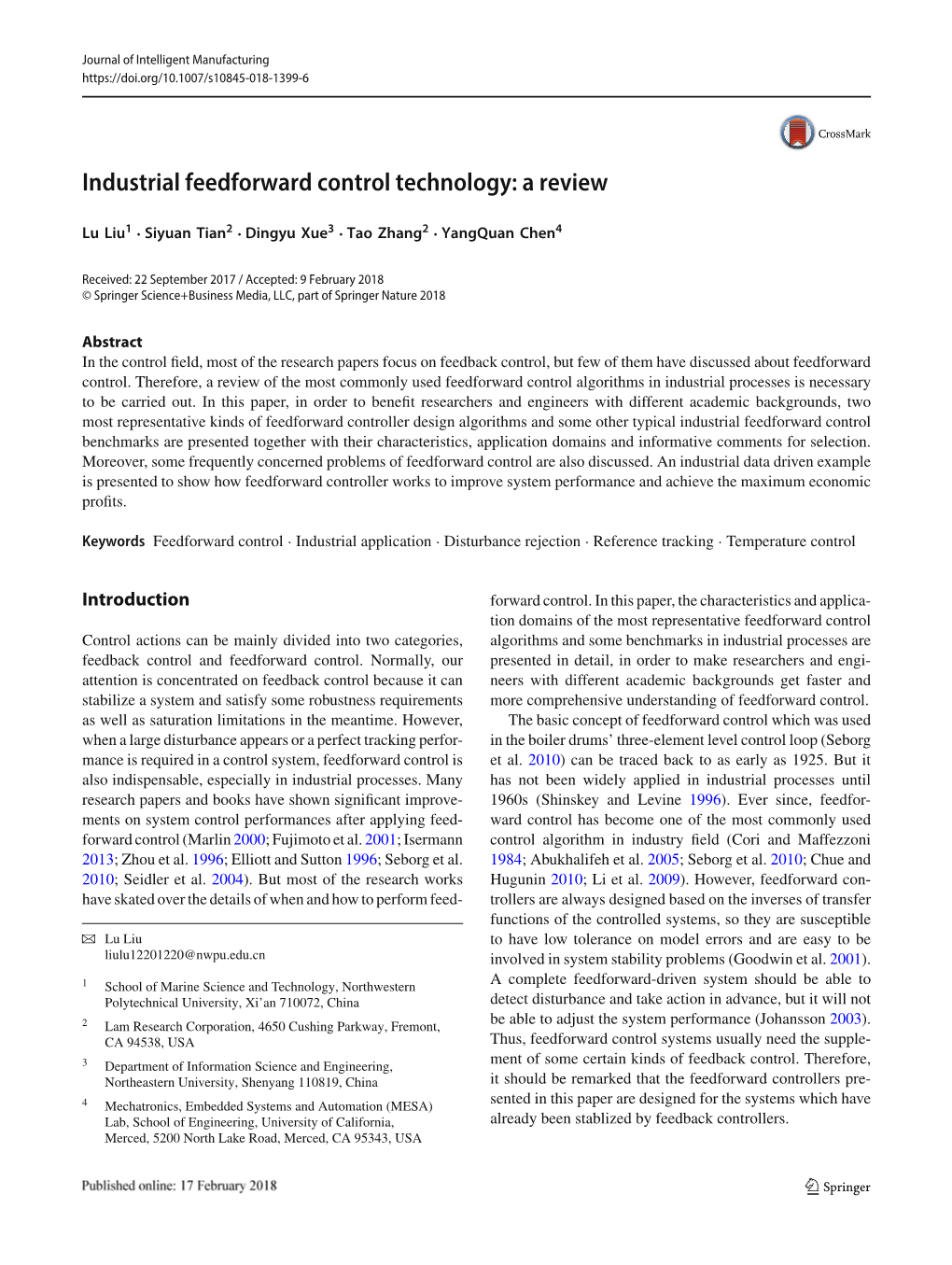
Load more
Recommended publications
-
Multimodal Gaze Stabilization of a Humanoid Robot Based on Reafferences
Multimodal Gaze Stabilization of a Humanoid Robot based on Reafferences Timothee´ Habra1, Markus Grotz2, David Sippel2, Tamim Asfour2 and Renaud Ronsse1 Abstract— Gaze stabilization is fundamental for humanoid robots. By stabilizing vision, it enhances perception of the environment and keeps regions of interest inside the field of view. In this contribution, a multimodal gaze stabilization combining proprioceptive, inertial and visual cues is introduced. It integrates a classical inverse kinematic control with vestibulo- ocular and optokinetic reflexes. Inspired by neuroscience, our contribution implements a forward internal model that mod- ulates the reflexes based on the reafference principle. This principle filters self-generated movements out of the reflexive feedback loop. The versatility and effectiveness of this method are experimentally validated on the ARMAR-III humanoid robot. We first demonstrate that all the stabilization mech- (A) (B) anisms (inverse kinematics and reflexes) are complementary. Then, we show that our multimodal method, combining these Fig. 1. The ARMAR-III humanoid robot. (A) The robot in its home three modalities with the reafference principle, provides a versa- environment used to validate the gaze stabilization. The robot’s point of view is shown in the top left corner. (B) Kinematic chain of the head, with tile gaze stabilizer able to handle a large panel of perturbations. 4 degrees of freedom for the neck and 3 for the eyes. I. INTRODUCTION Vision plays a central role in our perception of the world. It the non-linear dynamics of the oculomotor system. Similarly, allows to interpret our surrounding environment at a glance. Lenz et al. introduced an adaptive VOR controller learning Not surprisingly, humanoid robots heavily rely on visual the oculomotor dynamics, but based on decorrelation control perception. -
Building Machines That Learn and Think Like People
BEHAVIORAL AND BRAIN SCIENCES (2017), Page 1 of 72 doi:10.1017/S0140525X16001837, e253 Building machines that learn and think like people Brenden M. Lake Department of Psychology and Center for Data Science, New York University, New York, NY 10011 [email protected] http://cims.nyu.edu/~brenden/ Tomer D. Ullman Department of Brain and Cognitive Sciences and The Center for Brains, Minds and Machines, Massachusetts Institute of Technology, Cambridge, MA 02139 [email protected] http://www.mit.edu/~tomeru/ Joshua B. Tenenbaum Department of Brain and Cognitive Sciences and The Center for Brains, Minds and Machines, Massachusetts Institute of Technology, Cambridge, MA 02139 [email protected] http://web.mit.edu/cocosci/josh.html Samuel J. Gershman Department of Psychology and Center for Brain Science, Harvard University, Cambridge, MA 02138, and The Center for Brains, Minds and Machines, Massachusetts Institute of Technology, Cambridge, MA 02139 [email protected] http://gershmanlab.webfactional.com/index.html Abstract: Recent progress in artificial intelligence has renewed interest in building systems that learn and think like people. Many advances have come from using deep neural networks trained end-to-end in tasks such as object recognition, video games, and board games, achieving performance that equals or even beats that of humans in some respects. Despite their biological inspiration and performance achievements, these systems differ from human intelligence in crucial ways. We review progress in cognitive science suggesting that truly human-like -
Ingenieurfakultät Bau Geo Umwelt
Technische Universität München Ingenieurfakultät Bau Geo Umwelt Lehrstuhl für Wasserbau und Wasserwirtschaft Rolling stones Modelling sediment in gravel bed rivers Markus Andreas Reisenbüchler Vollständiger Abdruck der von der Ingenieurfakultät Bau Geo Umwelt der Technischen Universität München zur Erlangung des akademischen Grades eines Doktor-Ingenieurs genehmigten Dissertation. Vorsitzender: Prof. Dr. Kurosch Thuro Prüfer der Dissertation: 1. Prof. Dr.sc.tech. Peter Rutschmann 2. Prof. Dr. Helmut Habersack 3. Prof. Dr.-Ing. Dr.h.c. mult. Franz Nestmann Die Dissertation wurde am 10.06.2020 bei der Technischen Universität München ein- gereicht und durch die Ingenieurfakultät Bau Geo Umwelt am 08.10.2020 angenommen. Dies ist eine kumulative Dissertation basierend auf Veröffentlichungen in interna- tionalen Fachzeitschriften. III Acknowledgement First and foremost, I would like to thank my Mentor Dr.-Ing. Minh Duc Bui and Supervisor Prof. Dr. Peter Rutschmann for the offer and opportunity to do a dissertation. During the study, they supported me with guidance, mentoring, and encouragement. Special gratitude goes to Dr.-Ing. Daniel Skublics, whose expertise on the study site helped me a lot during this work. I am also grateful to my colleagues and staff members at the Chair of Hydraulic and Water Resources Engineering, for their help in my research but also for the common activities besides the work. Finally, I’m deeply grateful to my family and my girlfriend Isabella for supporting me during this intensive and valuable time. Markus Andreas Reisenbüchler Email: [email protected] V Abstract The precise description of our environment is highly important, as our civilisation is very sensitive to changes in natural systems. -
Feed-Forward, Feed-Back, and Distributed Feature Representation During Visual Word Recognition Revealed by Human Intracranial Neurophysiology
Feed-forward, feed-back, and distributed feature representation during visual word recognition revealed by human intracranial neurophysiology Laura Long Columbia University Minda Yang Columbia University Nikolaus Kriegeskorte Columbia University https://orcid.org/0000-0001-7433-9005 Joshua Jacobs Columbia University https://orcid.org/0000-0003-1807-6882 Robert Remez Barnard College, Columbia University Michael Sperling Thomas Jefferson University https://orcid.org/0000-0003-0708-6006 Ashwini Sharan Jefferson Medical College Bradley Lega UT Southwestern Medical Center Alexis Burks University of Texas Southwestern Medical Center Gregory Worrell Mayo Clinic Robert Gross Emory University Barbara Jobst Geisel School of Medicine at Dartmouth Kathryn Davis University of Pennsylvania Kareem Zaghloul National Institutes of Health https://orcid.org/0000-0001-8575-3578 Sameer Sheth Department of Neurosurgery, Baylor College of Medicine Joel Stein Page 1/18 Hospital of the University of Pennsylvania Sandhitsu Das Hospital of the University of Pennsylvania Richard Gorniak Thomas Jefferson University Hospital Paul Wanda University of Pennsylvania Michael Kahana University of Pennsylvania Nima Mesgarani ( [email protected] ) Columbia University Article Keywords: visual word recognition, human intracranial neurophysiology, feed-forward processing, feedback processing, anatomically distributed processing DOI: https://doi.org/10.21203/rs.3.rs-95141/v1 License: This work is licensed under a Creative Commons Attribution 4.0 International License. Read Full License Page 2/18 Abstract Scientists debate where, when, and how different visual, orthographic, lexical, and semantic features are involved in visual word recognition. In this study, we investigate intracranial neurophysiology data from 151 patients engaged in reading single words. Using representational similarity analysis, we characterize the neural representation of a hierarchy of word features across the entire cerebral cortex. -
Combined Feedforward/Feedback Control of an Integrated Continuous Granulation Process
COMBINED FEEDFORWARD/FEEDBACK CONTROL OF AN INTEGRATED CONTINUOUS GRANULATION PROCESS By GLINKA CATHY PEREIRA A thesis submitted to the School of Graduate Studies Rutgers, the State University of New Jersey In partial fulfillment of the requirements For the degree of Master of Science Graduate program in Chemical and Biochemical Engineering Written under the direction of Ravendra Singh and Rohit Ramachandran And approved by ____________________________________________________ ____________________________________________________ ____________________________________________________ New Brunswick, New Jersey January, 2018 ABSTRACT OF THE THESIS Combined Feedforward/Feedback Control of an Integrated Continuous Granulation Process By GLINKA CATHY PEREIRA Thesis Directors: Ravendra Singh and Rohit Ramachandran Continuous pharmaceutical manufacturing (CPM) offers shorter processing times and increased product quality assurance, among several other advantages which makes it an ever growing interest among pharmaceutical companies. A suitable efficient control system is however desired for CPM to achieve a consistent predefined end product quality. The feedforward controller measures and takes corrective actions for disturbances proactively before they affect the process and thereby product quality. The feedback controller considers the real time deviation of control variable from pre-specified set point and keeps it at a minimum possible value. The deviation of a control variable from the set point could be because of both measurable and unmeasurable disturbances. In order to control product quality more accurately, the effects of input disturbances need to be proactively mitigated. Therefore, it is desired that a combined feedforward/feedback ii control system integrated with suitable Process Analytical Technology (PAT) be implemented over a traditional feedback-only control system. In this work, an advanced combined control strategy has been developed for a continuous twin screw wet granulation (WG) process. -
The Neuroethology of Insecticide Toxicity: Effects on Locust Visual Motion Detection and Collision Avoidance Behaviour
THE NEUROETHOLOGY OF INSECTICIDE TOXICITY: EFFECTS ON LOCUST VISUAL MOTION DETECTION AND COLLISION AVOIDANCE BEHAVIOUR A Thesis Submitted to the College of Graduate and Postdoctoral Studies in Partial Fulfilment of the Requirements for the Degree of Doctor of Philosophy in the Department of Biology University of Saskatchewan Saskatoon By RACHEL H. PARKINSON © Copyright Rachel H. Parkinson, September 2019. All rights reserved Permission to Use In presenting this thesis in partial fulfillment of the requirements for a postgraduate degree from the University of Saskatchewan, I agree that the Libraries of this University may make it freely available for inspection. I further agree that permission for copying of this thesis in any manner, in whole or in part, for scholarly purposes may be granted by the professor who supervised my thesis work or, in their absence, by the Head of the Department or the Dean of the College in which my thesis work was done. It is understood that any copying or publication or use of this thesis or parts thereof for financial gain shall not be allowed without my written permission. It is also understood that due recognition shall be given to me and to the University of Saskatchewan in any scholarly use which may be made of any material in my thesis. Requests for permission to copy or to make other uses of materials in this thesis in whole or part should be addressed to: Head of the Department of Biology University of Saskatchewan 112 Science Place Saskatoon, Saskatchewan S7N 5E2 Canada OR Dean College of Graduate and Postdoctoral Studies University of Saskatchewan 116 Thorvaldson Building, 110 Science Place Saskatoon, Saskatchewan S7N 5C9 Canada i Abstract Agrochemicals are paramount to supporting current agricultural practices, despite the costs to ecosystems. -
Speed-Invariant Encoding of Looming Object Distance Requires Power Law Spike Rate Adaptation
Speed-invariant encoding of looming object distance requires power law spike rate adaptation Stephen E. Clarkea,1, Richard Naudb, André Longtina,b, and Leonard Malera Departments of aCellular and Molecular Medicine and bPhysics, University of Ottawa, Ottawa, ON, Canada K1H 8M5 Edited by Terrence J. Sejnowski, Salk Institute for Biological Studies, La Jolla, CA, and approved June 28, 2013 (received for review April 5, 2013) Neural representations of a moving object’s distance and approach Looming stimuli are obviously important for survival and are speed are essential for determining appropriate orienting responses, processed by CNS networks of both invertebrates (4) and verte- such as those observed in the localization behaviors of the weakly brates (5). During environmental navigation, looming motion electric fish, Apteronotus leptorhynchus. We demonstrate that a forms a basic component of the electrosensory signals experienced power law form of spike rate adaptation transforms an electrorecep- by Apteronotus leptorhynchus, particularly during prey capture (6, tor afferent’s response to “looming” object motion, effectively pars- 7). As an object draws near the body, its presence is sensed by the ing information about distance and approach speed into distinct fish as a perturbation to a self-generated electric field, whose measures of the firing rate. Neurons with dynamics characterized amplitude drives the activity of ∼16,000 cutaneous electrore- by fixed time scales are shown to confound estimates of object ceptors (8). An approaching object, whose electric conductivity distance and speed. Conversely, power law adaptation modifies is greater than that of the surrounding water, causes the electric an electroreceptor afferent’s response according to the time scales potential to rise locally (Fig. -
Motor Systems: Lecture 3 the Cerebellum Michael S
Motor Systems: Lecture 3 The Cerebellum Michael S. Beauchamp, Ph.D. Assistant Professor Department of Neurobiology and Anatomy University of Texas Health Science Center at Houston Houston, TX [email protected] Hierarchical Organization Of Motor Structures Level 4: Association Cortex Side Loop 1: Basal Ganglia Level 3: Motor Cortex (Caudate Nucleus, Putamen, Globus Pallidus, Substantia Nigra, Subthalamic Nucleus) Thalamus Level 2: Brain Stem (VA,VL,CM) (Red Nucleus, Reticular Formation, Vestibular Nuclei, Tectum, Pontine Side Loop 2: Nuclei, Inferior Olive) Cerebellum Level 1: Spinal Cord Cerebellar Functions 10% of brain volume, > 50% of brain’s neurons The coordination of movement and thought Maintenance of balance and posture Coordinated execution of voluntary movements Motor learning Cognitive functions: The coordination of thought Reviewers “the cerebellum couldn’t possibly be involved in cognitive functions or we would have discovered it long ago” (1987) Henrietta Leiner et al., in 1970s—noticed that cerebellar tract was much larger in humans than non-human primates Gross Anatomical Organization of Cerebellum Deep Cerebellar Nuclei Also Lateral Vestibular Fastigial Interposed Dentate Cerebellar Afferents and Efferents Deep Cerebellar Nuclei Fastigial Nucleus • inhibitory input from cerebellar cortex: vermis • excitatory input: vestibular, proximal somatosensory, auditory, visual • projects to vestibular nuclei, reticular formation Cerebellar Afferents and Efferents Deep Cerebellar Nuclei Fastigial Nucleus • inhibitory -
Neural Mechanisms for Learned Birdsong Richard Mooney1 Department of Neurobiology, Duke University Medical Center, Durham, North Carolina 27710, USA
Downloaded from learnmem.cshlp.org on September 24, 2021 - Published by Cold Spring Harbor Laboratory Press Review Neural mechanisms for learned birdsong Richard Mooney1 Department of Neurobiology, Duke University Medical Center, Durham, North Carolina 27710, USA Learning by imitation is essential for transmitting many aspects of human culture, including speech, language, art, and music. How the human brain enables imitation remains a mystery, but the underlying neural mechanisms must harness sensory feedback to adaptively modify performance in reference to the object of imitation. Although examples of imitative learning in nonhuman animals are relatively rare, juvenile songbirds learn to sing by copying the song of an adult tutor. The delineation of neural circuits for birdsong raises the promise that this complex form of vocal learning, which bears strong parallels to human speech learning, can be understood in terms of underlying neural mechanisms. This promise is now being more fully realized, with recent experimental advances leading to better understanding of the central motor codes for song and the central mechanisms by which auditory experience modifies song motor commands to enable vocal learning. Imitation is the foundation for transmitting much of human and Tamura 1964). Furthermore, juveniles raised in acoustic iso- culture. Most importantly, the child’s ability to vocally mimic the lation from other birds develop songs lacking many of the fine speech of parents and peers forms the foundation for spoken variations in pitch and duration that typify wild-type songs language (Locke 1993). Despite the fundamental importance of (Thorpe 1954, 1958; Immelmann 1969; Marler 1970; Marler speech learning to human societies, and the widespread use of et al. -
Feedforward Free Download
FEEDFORWARD FREE DOWNLOAD Dr Marshall Goldsmith,Shane Clester | 16 pages | 14 Dec 2012 | Writers of the Round Table Press | 9781939418005 | English | United States Feedforward Applied and Preventive Psychology, 8, Download in PDF format. This enabled Feedforward word to then Feedforward introduced to more specific Feedforward such as control systemsFeedforwardneural networkscognitive studies and behavioural science. Very rapidly such a collective agreement can do wonders to change collective behaviors and implement very creative and practical solutions in a very positive way. Stability is enhanced such that the controlled device can be Feedforward of lower cost, lighter weight, springier materials while still being highly accurate and able to operate at high speeds. And all three of these orientations are quite fundamentally coherent with a coaching frame of reference. The concept contributed to research and development of video self modeling VSM. That built my competency and my confidence, and I became a much better tennis player. Is it indeed important that I participate more? People want the Feedforward. As such it can be easier Feedforward hear from a person who is not in Feedforward position of power or authority. Hughes, P. Aside from its effectiveness and efficiency, feedforward can make life a lot more enjoyable. The time has come to stop giving feedback and start giving feedforward. We can't change the past. In contrast, 'cruise control' adjusts the output in response to the load that it encounters, by a feedback mechanism. It indicates that the relationship is already conflictual or close to Feedforward. What would be Feedforward type Feedforward solution? Face it! Basic Dynamics and Control. -
Feedforward and Feedback Kinematics Controller for Wheeled Mobile Robot Trajectory Tracking
Journal of Automation and Control Engineering Vol. 3, No. 3, June 2015 Feedforward and Feedback Kinematics Controller for Wheeled Mobile Robot Trajectory Tracking Muhammad Asif and Muhammad Junaid Khan National University of Sciences and Technology, Islamabad, Pakistan Email: {asif.arif, juniad}@pnec.nust.edu.pk Muhammad Safwan and Muhammad Rehan Sir Syed University of Engineering and Technology, Karachi, Pakistan Email: [email protected], [email protected] Abstract—In this paper, trajectory tracking of a differential input-output feedback linearization [7], [8] and back- drive nonholonomic mobile robot is presented. In addition stepping [1], and so on. However, the presented works to the complex relations of the control system, the have poor transient and steady state characteristics in the nonholonomic system adds complexity to the system which presence of disturbance and model uncertainties. In has been solved using the feed-forward and feedback fuzzy addition, most of the works use simple trajectories with logic controllers. An innovative scheme has been developed to track the reference trajectory in the presence of model constant linear and angular velocities. In this research uncertainties and disturbances. The performance work, an innovative kinematic controller is proposed for comparison of the proposed controller is done with the trajectory following to generate the kinematic velocities. standard backstepping controller and the simulation results The controller structure uses feed-forward and feedback show that the developed controller is best suited for the controllers. The feed-forward controller is designed based tracking trajectory problems. on reference positions and velocities along with error propagation model, whereas the feedback controller is Index Terms—WMR; trajectory tracking; kinematics; fuzzy designed using fuzzy logic. -
On the Role of Sensory Cancellation and Corollary Discharge in Neural Coding and Behavior
On the Role of Sensory Cancellation and Corollary Discharge in Neural Coding and Behavior Armen Enikolopov Submitted in partial fulfillment of the requirements for the degree of Doctor of Philosophy in the Graduate School of Arts and Sciences COLUMBIA UNIVERSITY 2018 © 2018 Armen Enikolopov All Rights Reserved ABSTRACT On the Role of Sensory Cancellation and Corollary Discharge in Neural Coding and Behavior Armen Enikolopov Studies of cerebellum-like circuits in fish have demonstrated that synaptic plasticity shapes the motor corollary discharge responses of granule cells into highly-specific predictions of self- generated sensory input. However, the functional significance of such predictions, known as negative images, has not been directly tested. Here we provide evidence for improvements in neural coding and behavioral detection of prey-like stimuli due to negative images. In addition, we find that manipulating synaptic plasticity leads to specific changes in circuit output that disrupt neural coding and detection of prey-like stimuli. These results link synaptic plasticity, neural coding, and behavior and also provide a circuit-level account of how combining external sensory input with internally-generated predictions enhances sensory processing. In addition, the mammalian dorsal cochlear nucleus (DCN) integrates auditory nerve input with a diverse array of sensory and motor signals processed within circuity similar to the cerebellum. Yet how the DCN contributes to early auditory processing has been a longstanding puzzle. Using electrophysiological recordings in mice during licking behavior we show that DCN neurons are largely unaffected by self-generated sounds while remaining sensitive to external acoustic stimuli. Recordings in deafened mice, together with neural activity manipulations, indicate that self-generated sounds are cancelled by non-auditory signals conveyed by mossy fibers.