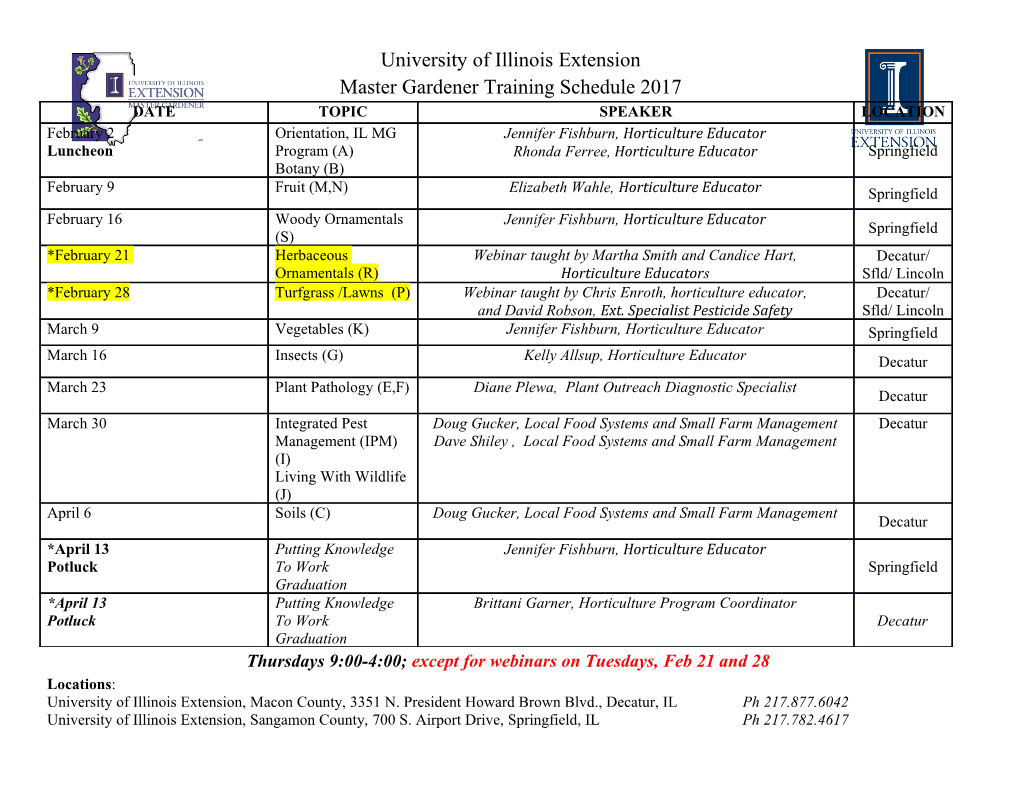
Journal of Intelligent Manufacturing https://doi.org/10.1007/s10845-018-1399-6 Industrial feedforward control technology: a review Lu Liu1 · Siyuan Tian2 · Dingyu Xue3 · Tao Zhang2 · YangQuan Chen4 Received: 22 September 2017 / Accepted: 9 February 2018 © Springer Science+Business Media, LLC, part of Springer Nature 2018 Abstract In the control field, most of the research papers focus on feedback control, but few of them have discussed about feedforward control. Therefore, a review of the most commonly used feedforward control algorithms in industrial processes is necessary to be carried out. In this paper, in order to benefit researchers and engineers with different academic backgrounds, two most representative kinds of feedforward controller design algorithms and some other typical industrial feedforward control benchmarks are presented together with their characteristics, application domains and informative comments for selection. Moreover, some frequently concerned problems of feedforward control are also discussed. An industrial data driven example is presented to show how feedforward controller works to improve system performance and achieve the maximum economic profits. Keywords Feedforward control · Industrial application · Disturbance rejection · Reference tracking · Temperature control Introduction forward control. In this paper, the characteristics and applica- tion domains of the most representative feedforward control Control actions can be mainly divided into two categories, algorithms and some benchmarks in industrial processes are feedback control and feedforward control. Normally, our presented in detail, in order to make researchers and engi- attention is concentrated on feedback control because it can neers with different academic backgrounds get faster and stabilize a system and satisfy some robustness requirements more comprehensive understanding of feedforward control. as well as saturation limitations in the meantime. However, The basic concept of feedforward control which was used when a large disturbance appears or a perfect tracking perfor- in the boiler drums’ three-element level control loop (Seborg mance is required in a control system, feedforward control is et al. 2010) can be traced back to as early as 1925. But it also indispensable, especially in industrial processes. Many has not been widely applied in industrial processes until research papers and books have shown significant improve- 1960s (Shinskey and Levine 1996). Ever since, feedfor- ments on system control performances after applying feed- ward control has become one of the most commonly used forward control (Marlin 2000; Fujimoto et al. 2001; Isermann control algorithm in industry field (Cori and Maffezzoni 2013; Zhou et al. 1996; Elliott and Sutton 1996; Seborg et al. 1984; Abukhalifeh et al. 2005; Seborg et al. 2010; Chue and 2010; Seidler et al. 2004). But most of the research works Hugunin 2010;Lietal.2009). However, feedforward con- have skated over the details of when and how to perform feed- trollers are always designed based on the inverses of transfer functions of the controlled systems, so they are susceptible B Lu Liu to have low tolerance on model errors and are easy to be [email protected] involved in system stability problems (Goodwin et al. 2001). 1 School of Marine Science and Technology, Northwestern A complete feedforward-driven system should be able to Polytechnical University, Xi’an 710072, China detect disturbance and take action in advance, but it will not 2 Lam Research Corporation, 4650 Cushing Parkway, Fremont, be able to adjust the system performance (Johansson 2003). CA 94538, USA Thus, feedforward control systems usually need the supple- 3 Department of Information Science and Engineering, ment of some certain kinds of feedback control. Therefore, Northeastern University, Shenyang 110819, China it should be remarked that the feedforward controllers pre- 4 Mechatronics, Embedded Systems and Automation (MESA) sented in this paper are designed for the systems which have Lab, School of Engineering, University of California, already been stablized by feedback controllers. Merced, 5200 North Lake Road, Merced, CA 95343, USA 123 Journal of Intelligent Manufacturing According to different control objectives, there are primar- output. Even when there are model uncertainties in the con- ily two kinds of feedforward controllers, which are aiming trolled system, feedforward control can usually decrease the at disturbance rejection and perfect tracking respectively. impact of disturbance more effectively than feedback control The former one which has been frequently used in chemical (Brosilow and Joseph 2002). Figure 1 gives a graphic under- processes can detect and eliminate disturbance immediately standing of how feedforward controller works to eliminate when the disturbance comes into the system (Jinzenji et al. disturbance impact in a feedforward-feedback control sys- 2001; Elliott 2000; Kempf and Kobayashi 1999; Ghosh and tem. Once a disturbance signal enters the system, it will be Narayanan 2007; Yanand Shiu 2008; Anibal Valenzuela et al. eliminated immediately by the feedforward controller with- 2007). Without the disturbance rejection feedforward con- out any impact on the system output. Otherwise, if there troller in the control loop, the system will try to eliminate is only feedback controller in the control loop, the distur- the disturbance influence after it has passed through all the bance will travel through all the control path to generate an way of the system and generated an error signal. Another error signal and drive the feedback controller react. More- typical feedforward controller which is aiming at improv- over, the long time delay generated in the path of disturbance ing reference tracking performance has also been extensively travelling will cause unnecessary impacts on system output utilized in different domains (O’Brien and Broussard 1979; performance which may lead to overcorrections and may Tomizuka 1987; Fujimoto et al. 2001; Song et al. 2005; Fuji- even cause oscillations on the controlled variables. These moto et al. 2000; Tsao and Tomizuka 1987;Klanˇcar and impacts are significant in industry processes and will influ- Škrjanc 2007;Lietal.2016; Stojanovic and Nedic 2016; ence the system economic benefits. Nedic et al. 2015; Marconi and Isidori 2000; Ang et al. Corripio (2000) has given a criterion to help measure the 2007). It helps the systems achieve perfect tracking perfor- controllability of feedback controllers, namely the ratio of the mance without the change of original closed-loop structure. system dead time to the process model time constant. When We will review the detailed characteristics of these two kinds the value of the criterion is equal or greater than one, feed- of feedforward controllers as well as some benchmarks in the back control usually cannot eliminate the effect caused by following sections. measured disturbance. On this condition, feedforward con- The rest of this paper is organized as follows. Feedforward trol strategy can achieve the greatest improvement on control controller design technologies for disturbance rejection and performance. Another vital point in the decision process of reference tracking as well as their characteristics and appli- whether a feedforward controller is necessary or not is the cation domains are presented in sections “Feedforward con- economic benefit, which usually comes first in industry pro- troller for disturbance rejection” and “Feedforward controller cess (Brosilow and Joseph 2002). Therefore, the decision of for reference tracking” respectively; section “Feedforward whether to use feedforward control or not in a control loop control for MIMO systems” introduces some feedforward also highly depends on the degree of the system performance control algorithms for MIMO (Multi-Input-Multi-Output) improvement in the output to the additional cost of the con- systems; some other typical feedforward control technolo- troller implementation and maintenance. gies used in industrial processes are presented in section Moreover, the design of an efficient feedforward compen- “Feedforward control in industrial application”; section sator requires fairly high accuracy on the controlled process “Other questions of feedforward control” discusses some model and all possible disturbances dynamic models. These frequently encountered problems about feedforward control; are normally hard to be achieved in a real process. There- section “Example” gives an industrial data driven example to fore, a more reasonable method is only adding feedforward show how to use feedforward control; finally, the conclusions controller for those vital disturbances and making the feed- are drawn in section “Conclusion”. back controller deal with other minor disturbances as well as model inaccuracy. Feedforward controller for disturbance Tuning of feedforward controller for disturbance rejection rejection Why and when to use feedforward controller for A manually tuned feedforward control system example is disturbance rejection shown in Fig. 2 (Altmann 2005). When a disturbance enters, it will be detected by the process operator. Then after mea- Feedback control is usually necessary in a system control suring the disturbance, the operator will make changes of the loop, however, feedforward controller is also indispensable manipulated variable, such as flow rate, based on his knowl- when a major disturbance appears in the system. In most edge of the process to minimize
Details
-
File Typepdf
-
Upload Time-
-
Content LanguagesEnglish
-
Upload UserAnonymous/Not logged-in
-
File Pages15 Page
-
File Size-