Use of EVOH for Food Packaging Applications
Total Page:16
File Type:pdf, Size:1020Kb
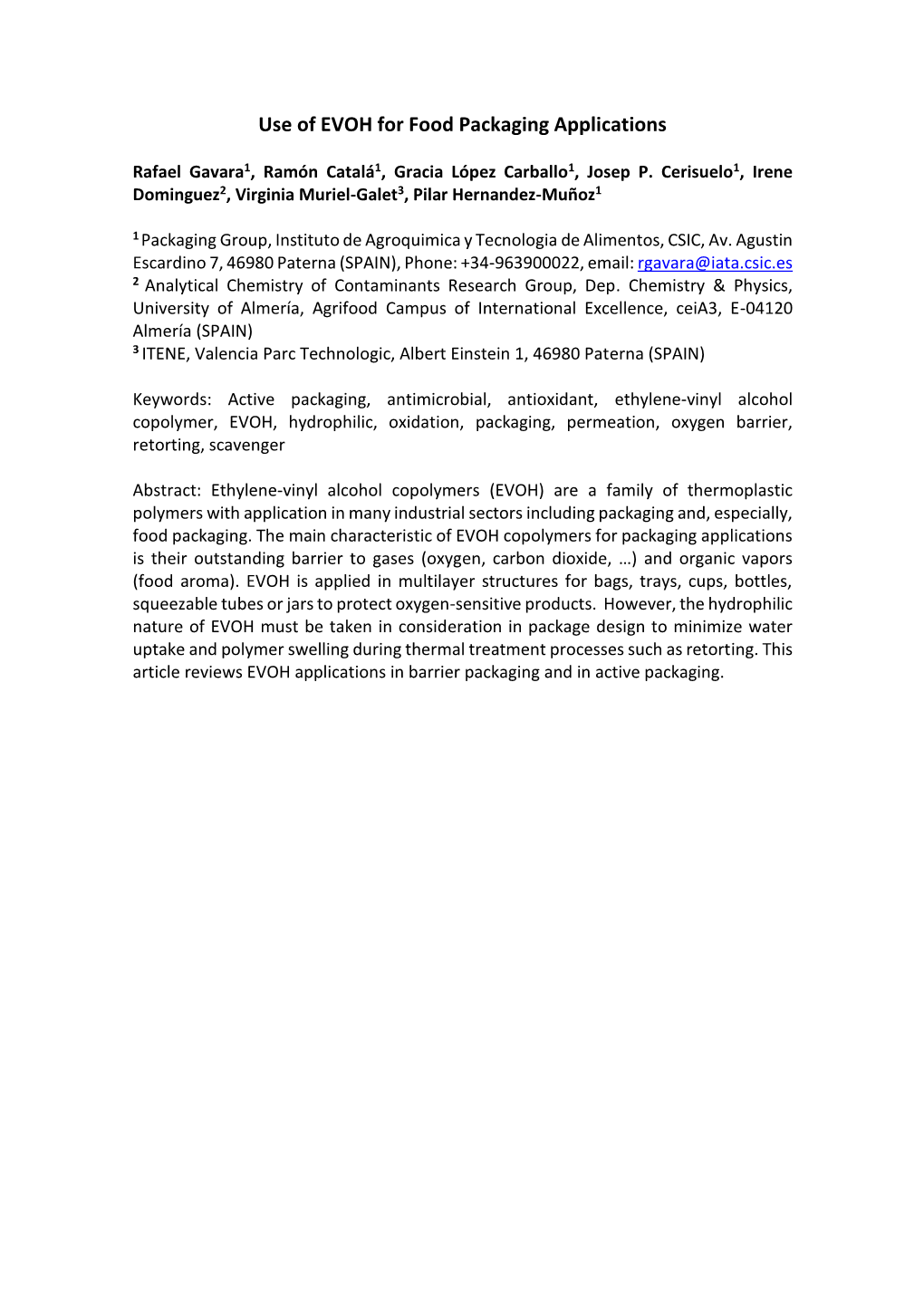
Load more
Recommended publications
-
SARAN™ Polyvinylidene Chloride (PVDC) Resins
Product Safety Assessment SARAN™ Polyvinylidene Chloride (PVDC) Resins Product Safety Assessment documents are available at www.dow.com/productsafety/assess/finder.htm. Select a Topic: Names Product Overview Manufacture of Product Product Description Product Uses Exposure Potential Health Information Environmental Information Physical Hazard Information Regulatory Information Additional Information References Names CAS Nos. 25038-72-6, 9011-06-7 Vinylidene chloride copolymer SARAN polyvinylidene chloride (PVDC) resins Vinylidene chloride/methyl acrylate copolymer SARAN resins Vinylidene chloride/vinyl chloride copolymer Back to top Product Overview SARAN™ resins are white, odorless granules.1 These resins are polyvinylidene chloride (PVDC) copolymers made from polymerizing vinylidene chloride with comonomers like vinyl chloride and alkyl acrylates.2 For further information, see Product Description. SARAN resins are used extensively in packaging applications for food, pharmaceuticals, hygiene products, and sterilized medical products. They offer excellent barrier performance to moisture, oxygen, and odors.3 For further information, see Product Uses. Because SARAN resins are used extensively in food packaging, it is possible for consumers to come into contact with them. Workplace exposure is also possible.4 For further information, see Exposure Potential. SARAN resins are essentially nonirritating to the eyes and skin. Dust from SARAN products may cause temporary mechanical irritation to the skin and eyes under extreme conditions. However, the products are considered to present no significant health hazard.5 For further information, see Health Information. SARAN resins are expected to be inert in the environment. They are unlikely to accumulate in the food chain, and are practically nontoxic to aquatic organisms on an acute basis.6 For further information, see Environmental Information. -
Plastic Materials List Original.Xlsx
Partec Institute 1030 Cavendish Rd. Mt. Gravatt East. Brisbane Qld 4122 Ph 07 3849 7878. www.partec.qld.edu.au ABREVIATIONS OF POLYMER MATERIALS AAS acrylonitrile acrylic styrene PE polyethylene ABS acrylonitrile butadiene styrene PEO poly (ethylene oxide) AES acrylonitrile ethylene ester PEP polyethylene propylene A/MMA acrylonitrile / methyl methacrylate PESU polyether sulphone AS acrylonitrile styrene PET polyethylene terephthalate ASA acrylonitrile styrene acrylate PETP crystaline pet (tetramethylene terephthalate) BMC bulk moulding compound PEX polyethylene crosslinked CA cellulose acetate PF phenol formaldehyde resin CAB cellulose acetate butyrate PI polyimide CAP cellulose acetate propionate PIB polyisobutylene CF cresol formadehyde PMMA polymethyl methacrylate CLPE chlorinated polyethylene PMP poly (4-methylpentene- I ) CLPVC /CPVC chlorinated polyvinyl chloride POB polypoxybenzoate CMC carboxymethyl cellulose POM polyoxymethylene (polyacetal) CN cellulose nitrate PP polypropylene CP cellulose propionate PPC polypropylene compound CPE chlorinated polyethylene PPE polypropylene ethylene CS casein PPF polypropylene foam DAP diallyl phthalate PPO polyphenylene oxide modified DMC dough molding compound PPDX polypropylene oxide EC ethyl cellulose PPS polyphenylene sulphide E/EA, EEA ethylene / ethyl acetate PPSU polyphenylene sulphone EEBC polyester (ether ester block copolymer) PS polystyrene E / MA ethylene methacrylate acid PSU polysulphone EP epoxide, epoxy resin PTFE polytetrafluoethylene EPS polystyrene - expandable ethylene -
Table 1. SOME NAMES and ABBREVIATIONS of Plastics and Elastomers
TABlE 1. SOME NAMES AND ABBREVIATIONS OF PlASTICS AND ElASTOMERS. Common name Abbreviation Acetal (homopolymer and copolymer) POM-H and POM-K Acrylate styrene acrylonitrile ASAorAAS Acrylate modified styrene acrylonitrile ASAorAAS Acrylic acid ester rubber ACM Acrylonitrile butadiene rubber or nitrile butadiene rubber NBR Acrylonitrile butadiene styrene ABS Acrylonitrile styrene/chlorinated polyethylene ACS Acrylonitrile methyl methacrylate AMMA Acrylonitrile styrene/EPR rubber or, acrylonitrile ethylene propylene styrene AES Alpha methyl styrene AMS Atactic polypropylene APPorPP-A Butadiene rubber or, cis-1,4-polybutadiene rubber or, polybutadiene rubber BR Butadiene styrene block copolymer BDS Butyl rubber IIR Bulk molding compound BMC Casein formaldehyde CF Cellulose acetate CA Cellulose acetate butyrate CAB Cellulose acetate propionate CAP Cellulose nitrate CN Chlorinated polyethylene CPEorCM Chlorinated polyvinyl chloride CPVC or, PVC-C Chloro-polyethylene or, chlorinated polyethylene. CM or CPE or, PE-C Chloroprene rubber or, polychloroprene rubber CR Chlorotrifluoroethylene ethylene copolymers ECfFE Cis-polyisoprene or, cis-1,4-polyisoprene IR Coumarone indene resins CIR Diallyl phthalate DAP Diallyl isophthalate DAIP Dough molding compound DMC Elastomeric alloy melt processable rubber EA-MPR Elastomeric alloy thermoplastic vulcanizate EA-TPV Epichlohydrin rubber CHR Epoxy or, epoxide EP Epoxy or, epoxide, with glass fiber EPGF Ethyl cellulose EC Ethylene acryic acid EAA Ethylene propylene diene monomer (an EPR terpolymer) EPDM -
Bio-Based and Biodegradable Plastics – Facts and Figures Focus on Food Packaging in the Netherlands
Bio-based and biodegradable plastics – Facts and Figures Focus on food packaging in the Netherlands Martien van den Oever, Karin Molenveld, Maarten van der Zee, Harriëtte Bos Rapport nr. 1722 Bio-based and biodegradable plastics - Facts and Figures Focus on food packaging in the Netherlands Martien van den Oever, Karin Molenveld, Maarten van der Zee, Harriëtte Bos Report 1722 Colophon Title Bio-based and biodegradable plastics - Facts and Figures Author(s) Martien van den Oever, Karin Molenveld, Maarten van der Zee, Harriëtte Bos Number Wageningen Food & Biobased Research number 1722 ISBN-number 978-94-6343-121-7 DOI http://dx.doi.org/10.18174/408350 Date of publication April 2017 Version Concept Confidentiality No/yes+date of expiration OPD code OPD code Approved by Christiaan Bolck Review Intern Name reviewer Christaan Bolck Sponsor RVO.nl + Dutch Ministry of Economic Affairs Client RVO.nl + Dutch Ministry of Economic Affairs Wageningen Food & Biobased Research P.O. Box 17 NL-6700 AA Wageningen Tel: +31 (0)317 480 084 E-mail: [email protected] Internet: www.wur.nl/foodandbiobased-research © Wageningen Food & Biobased Research, institute within the legal entity Stichting Wageningen Research All rights reserved. No part of this publication may be reproduced, stored in a retrieval system of any nature, or transmitted, in any form or by any means, electronic, mechanical, photocopying, recording or otherwise, without the prior permission of the publisher. The publisher does not accept any liability for inaccuracies in this report. 2 © Wageningen Food & Biobased Research, institute within the legal entity Stichting Wageningen Research Preface For over 25 years Wageningen Food & Biobased Research (WFBR) is involved in research and development of bio-based materials and products. -
EVOH): a Review
Polymer Reviews ISSN: 1558-3724 (Print) 1558-3716 (Online) Journal homepage: https://www.tandfonline.com/loi/lmsc20 Recent Updates on the Barrier Properties of Ethylene Vinyl Alcohol Copolymer (EVOH): A Review Caroline Maes, Wout Luyten, Geert Herremans, Roos Peeters, Robert Carleer & Mieke Buntinx To cite this article: Caroline Maes, Wout Luyten, Geert Herremans, Roos Peeters, Robert Carleer & Mieke Buntinx (2018) Recent Updates on the Barrier Properties of Ethylene Vinyl Alcohol Copolymer (EVOH): A Review, Polymer Reviews, 58:2, 209-246, DOI: 10.1080/15583724.2017.1394323 To link to this article: https://doi.org/10.1080/15583724.2017.1394323 © 2018 The Author(s). Published by Taylor & Accepted author version posted online: 24 Francis Group, LLC Oct 2017. Published online: 18 Jan 2018. Submit your article to this journal Article views: 3240 View related articles View Crossmark data Citing articles: 14 View citing articles Full Terms & Conditions of access and use can be found at https://www.tandfonline.com/action/journalInformation?journalCode=lmsc20 POLYMER REVIEWS 2018, VOL. 58, NO. 2, 209–246 https://doi.org/10.1080/15583724.2017.1394323 REVIEW Recent Updates on the Barrier Properties of Ethylene Vinyl Alcohol Copolymer (EVOH): A Review Caroline Maes a,b, Wout Luytena, Geert Herremansa, Roos Peetersb, Robert Carleerc, and Mieke Buntinxb aKuraray–Eval Europe NV, Haven 1053 Nieuwe Weg 1, Bus 10, Zwijndrecht, Belgium; bHasselt University, Packaging Technology Center IMO-IMOMEC, Wetenschapspark 27, Diepenbeek, Belgium; cHasselt University, Applied and Analytical Chemistry IMO-IMOMEC, Agoralaan Building D, Diepenbeek, Belgium ABSTRACT ARTICLE HISTORY The gas barrier properties of ethylene vinyl alcohol copolymer (EVOH) Received 26 June 2017 against oxygen, carbon dioxide and water vapor have been Accepted 15 October 2017 widely investigated in relation to different material characteristics, KEYWORDS environmental conditions and new processing technologies. -
Iiihiihiii Iiii
IIIHIIHIIIUS005470624A IIII United States Patent (19) 11) Patent Number: 5,470,624 Oreglia et al. 45 Date of Patent: Nov. 28, 1995 54) OSTOMY FILM 4,525,396 6/1985 Takasa et al. ............................. 428/35 4,606,970 8/1986 ... 428/301 75) Inventors: Aurelio Oreglia, Como; Paolo Vietto, 4,687,692 8/1987 ... 428/137 Legnano, both of Italy 4,975,316 12/1990 ... 428/247 5,110,643 5/1992 73) Assignee: W. R. Grace & Co.-Conn., Duncan, FOREIGN PATENT DOCUMENTS S.C. 061.459 7/1988 Australia. 0600363 12/1988 Australia. 21 Appl. No.: 419,786 0621,048 4/1989 Australia. 22 Filed: Apr. 11, 1995 O167956 1/1986 European Pat. Off.. 0273611 7/1988 European Pat. Off.. Related U.S. Application Data 0318025 5/1989 European Pat. Off.. 60-206622 10/1985 Japan. 62) Division of Ser. No. 363,565, Dec. 22, 1924, which is a 2023494 1/1980 United Kingdom. continuation of Ser. No. 951,034, Sep. 24, 1992, abandoned, 2064333 6/1981 United Kingdom. which is a continuation of Ser. No. 626,368, Dec. 12, 1990, 2115291 9/1983 United Kingdom. abandoned. 21221.34 1/1984 United Kingdom . 213843. 10/1984 United Kingdom. (30) Foreign Application Priority Data 221 1196 6/1989 United Kingdom. Dec. 13, 1989 (GB) United Kingdom ................... 892.8221 O164438 12/1989 WIPO. (51). Int. Cl.' ........................... B29D 23/00; B32B 27/36; Primary Examiner-George F. Lesmes D04H 1/58 Assistant Examiner-Kathryne E. Shelborne 52 U.S. Cl. ....................... 428/36.1; 428/36.2; 428/36.6; Attorney, Agent, or Firm-Thomas C. -
5183861.Pdf (200.1Kb)
l|||||llllllll||||||ll||||l|||||||||||||||llllllllllIllllllllllllllllllllll . U5005183861A Ulllted States Patent [19] [11] Patent Number: - 5,183,861 Riffle et a1. ’ [45] Date of Patent: Feb. 2, 1993 [54] POLYALKYLOXAZOLINE/POLYLACIONE [56] References Cited ANDCOPOLYMERS, USES PROCESSES FOR MAKING 1 US. PATENT DOCUMENTS 3,375,231 3/1968 Fukui et al. ......................... 525/415 . 4659 777 4/1987 Riflle et a1. 525/100 [75] Inventors: JudySinging“; S. lefle; Andrew Gurudus E. D. Brink, an of 4,910,268 ’ ’ 3/1990 Kobayash: - 525/411 Blacksburg, Va. OTHER PUBLICATIONS J. Appl. Polymer Sci, vol. 31, 1189-1197 (1986). [73] Assignee: Virginia Tech Intellectual Properties, Primary Examiner—~Ana L. Carrillo Inc., Blacksburg, Va. Attorney, Agent, or Firm—Richard P. Fennelly; Louis [211 App]. No.: 355,709 A' Moms [57] ABSTRACT [22] Filed: May 23, 1989 Block copolymers of polyoxazoline and polylactone moieties can be used as polymeric compatibilizers for [51] Int. Cl.5 .............................................. C08G 63/91 polyamides and polyolefins. [52] US. Cl. ............................... 525/413; 525/415 [58] Field of Search 525/413, 415 4 Claims, No Drawings 5,183,861 1 POLYALKYLOXAZOLINE/POLYLACT ONE ~ —[N-CH2CH21,.. COPOLYMERS, PROCESSES FOR MAKING, AND C(O)R USES R is aryl, alkyl or hydrogen. The subscript n can BACKGROUND OF THE INVENTION where range from a minimum of about 5 to a maximum of 1. Field of the Invention about 1000. The present invention relates to novel copolymers For example, poly(2-ethyloxazoline)/polycaprolac- suitable for use as polymeric compatibilizers. 10 tone block copolymers possessing the general structure 2. Description of the Prior Art described above can be synthesized by first polymeriz- The blending of certain types of copolymer composi- ing ethyl oxazoline using benzyl iodide as the initiator, tions (e.g., block copolymers) with other polymers ei- then terminating the reaction product with potassium This produces a primary hy- ther homopolymers or copolymers, is an industrially hydroxide or ammonia. -
United States Patent (19) 11 Patent Number: 4,585,701 Bartoszek Et Al
United States Patent (19) 11 Patent Number: 4,585,701 Bartoszek et al. (45) Date of Patent: Apr. 29, 1986 54) COMPOSITES OF POLYVINYLIDENE 3,524,906 8/1970 Schmitt et al. ...................... 525/199 FLUORDE ALLOYS AND 3,968, 196 7/1976 Wiley .............. ... 264/171. THERMOPLASTC POLYMERS AND THEIR 4,051,293 9/1977 Wiley .............................. 428/421 X PREPARATION 4,215,177 7/1980 Strassel ........................ 428/424.6 X 4,221,757 9/1980 Strassel ............................... 264/171 75 Inventors: Edward J. Bartoszek, Jeffersonville, 4,226,904 10/1980 Olivier et al... ... 156/322 X Pa.; Steven F. Mones, Newark, Del. 4,289,560 9/1981. Simons ............ ... 156/244.18 73) Assignee: Pennwalt Corporation, Philadelphia, 4,291,099 9/1981 Strassel ... ... 428/421 4,317,860 3/1982 Strassel ....... ... 428/42 Pa. 4,317,861 3/1982 Kidoh et al. ........................ 428/421 21) Appl. No.: 580,483 FOREIGN PATENT DOCUMENTS 22 Filed: Feb. 15, 1984 0060421 9/1982 European Pat. Off. ............ 264/171 51 Int. Cl'.............................................. B32B 27/08 OTHER PUBLICATIONS 52 U.S. C. ...................................... 428/421; 264/37; 264/171; 264/176 R; 428/424.2; 428/424.6; Pennwalt Technical Data Sheet, "KYNAR(R)/Acrylic 428/424.8 Alloys RC-9637 and RC-9638', 7/22/80. 58 Field of Search .................. 428/421, 424.6, 424.2, 428/424.8; 525/199; 264/171, 176 R, 37; Primary Examiner-Thomas J. Herbert 156/322, 244.18 (57) ABSTRACT 56) References Cited Composites of polyvinylidene fluoride alloys, and in U.S. PATENT DOCUMENTS compatible thermoplastic polymers are prepared by 3,253,060 5/1966 Koblitz et al. -
PVDC – New Developments, New Opportunities
PVDC – New Developments, New Opportunities Kirk Paisley SolVin, a division of Solvay Advanced Polymers, L.L.C. Alpharetta, Georgia Introduction The information in this presentation will provide basic background information on the use of PVDC resins and coatings in packaging applications. It will also give data on new grades of PVDC resins and latex, which can lead to the development of new packaging films by flexible packaging converters and film manufacturers. Background Polyvinylidene chloride (PVDC) resins and coatings have been a part of the flexible packaging world for more than 50 years, with a unique combination of functional characteristics that has found numerous applications. It is available in a variety forms: • Aqueous dispersions, or latex, for coating on a number of different film and paper substrates, • Extrudable powders, for monolayer or multilayer films and sheet, and • Soluble powders, for solvent-based coatings on films. Extrudable PVDC Powder Soluble PVDC Powder Aqueous PVDC Dispersion According to 2004 estimates1, approximately 160,000 metric tons of PVDC are used annually around the world in extruded, coextruded, coated and laminated structures. In a study of high barrier packaging films released in late 20052, PVDC was reported to be the leading barrier polymer in high performance packaging films. For example, in dry food packaging, PVDC-coated BOPP films hold a 53% share of barrier films used to package dry foods. Also, the forecasted growth for PVDC-coated PET films is a healthy 9% per year, driven primarily -
Manual on Food Packaging for Small and Medium Size Enterprises in Samoa
Manual on Food Packaging for Small and Medium Size Enterprises in Samoa Manual on Food Packaging for Small and Medium-Size Enterprises in Samoa Prepared with the cooperation of the Small and Medium Food Enterprises in Samoa by FAO Consultant Richard Beyer. Food and Agriculture Organization of the United Nations Sub-Regional Office for the Pacific Islands Apia, 2012 About this manual This manual was prepared under funding support by FAO Technical Cooperation Programme project TCP/SAM/3203. It is based on consultation with a number of small and medium size enterprises (SMEs) in Samoa during July 2012. The layout is such that specific packaging information is included in the first chapter, while the second chapter relates to findings in Samoa and highlights points where there is common ground. The third chapter builds on chapter two and suggests strategies for consideration by SMEs. It has been the intention to include a number of areas where quality can be improved and maintained inexpensively and with it a closer match between packaging, shelf-life and consumer expectation. The ultimate aim is to enable processors to select the most appropriate packing for their products and thereby become more profitable and successful in both local and export markets. It is to be recognised that the packaging industry is very dynamic and new combination of components are becoming available on a frequent basis and thus this only reflects the current state of packaging and would need periodic updating. All comments and feedback are welcome and should be sent to [email protected] and [email protected]. -
Portal Vein Embolization with Ethylene-Vinyl Alcohol Copolymer for Contralateral Lobe Hypertrophy Before Liver Resection: Safety, Feasibility and Initial Experience
809 Original Article Portal vein embolization with ethylene-vinyl alcohol copolymer for contralateral lobe hypertrophy before liver resection: safety, feasibility and initial experience Sébastien Gautier1, Olivier Chevallier1, Charles Mastier2, Philippe d’Athis3, Nicolas Falvo1, Frank Pilleul2, Marco Midulla1, Patrick Rat4, Olivier Facy4, Romaric Loffroy1 1Department of Vascular and Interventional Radiology, Image-Guided Therapy Center, ImViA Laboratory-EA 7535, François-Mitterrand University Hospital, Dijon, France; 2Department of Interventional Radiology and Oncology, Léon Bérard Cancer Center, Lyon, France; 3Department of Epidemiology and Biostatistics, François-Mitterrand University Hospital, Dijon, France; 4Department of Digestive and Oncologic Surgery, François- Mitterrand University Hospital, Dijon, France Correspondence to: Prof. Romaric Loffroy, MD, PhD, FCIRSE. Department of Vascular and Interventional Radiology, Image-Guided Therapy Center, ImViA Laboratory-EA 7535, François-Mitterrand University Hospital, 14 Rue Paul Gaffarel, BP 77908, 21079 Dijon Cedex, France. Email: [email protected]. Background: To report our preliminary experience with preoperative portal vein embolization (PVE) using liquid ethylene vinyl alcohol (EVOH) copolymer. Methods: Retrospectively review of patients with primary or secondary liver malignancies scheduled for extensive hepatectomy after the induction of future liver remnant (FLR) hypertrophy by right or left PVE with EVOH as the only embolic agent between 2014 and 2018 at two academic centers. Cross-sectional imaging liver volumetry data obtained before and 3–6 weeks after PVE were used to assess the FLR volume (FLRV) increase, degree of FLR hypertrophy and the FLR kinetic growth rate (KGR). Results: Twenty-six patients (17 males; mean age, 58.7±11 years; range, 32–79 years) were included. The technical and clinical success rate was 100%. -
Ethylene-Vinyl Acetate
Ethylene-vinyl acetate From Wikipedia, the free encyclopedia Ethylene-vinyl acetate Names Other names Poly(ethylene-vinyl acetate); Poly(ethylene-co-vinyl acetate); Polyethylene-vinyl acetate copolymer Identifiers CAS Registry Number 24937-78-8 Abbreviations EVA; PEVA PubChem 32742 UNII 4OKC630HS6 Properties Chemical formula (C2H4)n(C4H6O2)m Molar mass Variable Ethylene-vinyl acetate (EVA), also known as poly(ethylene-vinyl acetate) (PEVA), is the copolymer of ethylene and vinyl acetate. The weight percent vinyl acetate usually varies from 10 to 40%, with the remainder being ethylene. It is a polymer that approaches elastomeric ("rubber-like") materials in softness and flexibility. This is distinct from a thermoplastic, in that the material is cross-linking, ergo difficult to recycle.[1][2][3] The material has good clarity and gloss, low-temperature toughness, stress-crack resistance, hot-melt adhesive waterproof properties, and resistance to UV radiation. EVA has a distinctive vinegar-like odor and is competitive with rubber and vinyl products in many electrical applications. Applications Hot melt adhesives, hot glue sticks, and top of the line soccer cleats are usually made from EVA, usually with additives like wax and resin. EVA is also used as a clinginess-enhancing additive in plastic wraps. Craft foam sheets are made of EVA and these foam sheets are popularly used for children's foam stickers. EVA is also used in biomedical engineering applications as a drug delivery device. The polymer is dissolved in an organic solvent (e.g., dichloromethane). Powdered drug and filler (typically an inert sugar) are added to the liquid solution and rapidly mixed to obtain a homogeneous mixture.