Iiihiihiii Iiii
Total Page:16
File Type:pdf, Size:1020Kb
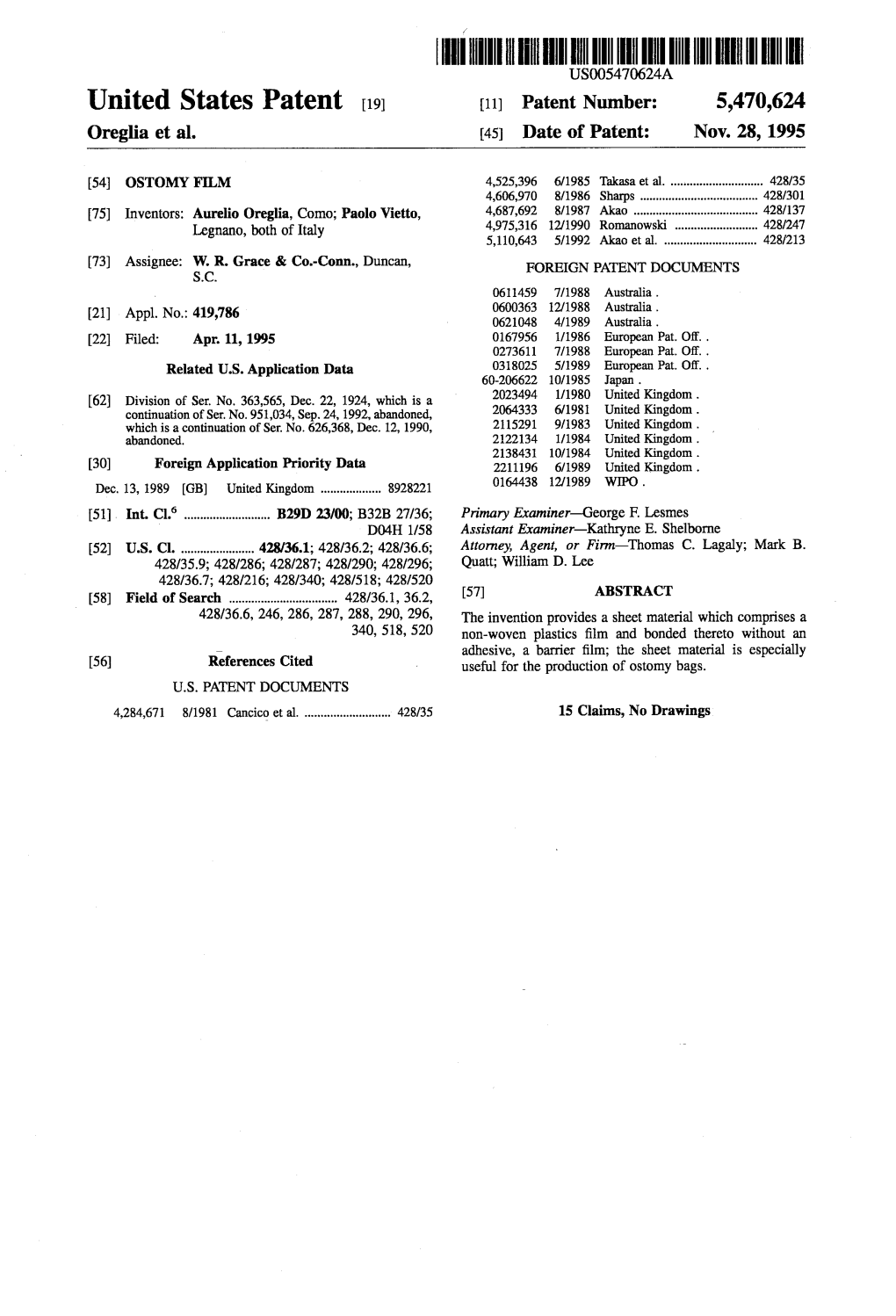
Load more
Recommended publications
-
SARAN™ Polyvinylidene Chloride (PVDC) Resins
Product Safety Assessment SARAN™ Polyvinylidene Chloride (PVDC) Resins Product Safety Assessment documents are available at www.dow.com/productsafety/assess/finder.htm. Select a Topic: Names Product Overview Manufacture of Product Product Description Product Uses Exposure Potential Health Information Environmental Information Physical Hazard Information Regulatory Information Additional Information References Names CAS Nos. 25038-72-6, 9011-06-7 Vinylidene chloride copolymer SARAN polyvinylidene chloride (PVDC) resins Vinylidene chloride/methyl acrylate copolymer SARAN resins Vinylidene chloride/vinyl chloride copolymer Back to top Product Overview SARAN™ resins are white, odorless granules.1 These resins are polyvinylidene chloride (PVDC) copolymers made from polymerizing vinylidene chloride with comonomers like vinyl chloride and alkyl acrylates.2 For further information, see Product Description. SARAN resins are used extensively in packaging applications for food, pharmaceuticals, hygiene products, and sterilized medical products. They offer excellent barrier performance to moisture, oxygen, and odors.3 For further information, see Product Uses. Because SARAN resins are used extensively in food packaging, it is possible for consumers to come into contact with them. Workplace exposure is also possible.4 For further information, see Exposure Potential. SARAN resins are essentially nonirritating to the eyes and skin. Dust from SARAN products may cause temporary mechanical irritation to the skin and eyes under extreme conditions. However, the products are considered to present no significant health hazard.5 For further information, see Health Information. SARAN resins are expected to be inert in the environment. They are unlikely to accumulate in the food chain, and are practically nontoxic to aquatic organisms on an acute basis.6 For further information, see Environmental Information. -
Plastic Materials List Original.Xlsx
Partec Institute 1030 Cavendish Rd. Mt. Gravatt East. Brisbane Qld 4122 Ph 07 3849 7878. www.partec.qld.edu.au ABREVIATIONS OF POLYMER MATERIALS AAS acrylonitrile acrylic styrene PE polyethylene ABS acrylonitrile butadiene styrene PEO poly (ethylene oxide) AES acrylonitrile ethylene ester PEP polyethylene propylene A/MMA acrylonitrile / methyl methacrylate PESU polyether sulphone AS acrylonitrile styrene PET polyethylene terephthalate ASA acrylonitrile styrene acrylate PETP crystaline pet (tetramethylene terephthalate) BMC bulk moulding compound PEX polyethylene crosslinked CA cellulose acetate PF phenol formaldehyde resin CAB cellulose acetate butyrate PI polyimide CAP cellulose acetate propionate PIB polyisobutylene CF cresol formadehyde PMMA polymethyl methacrylate CLPE chlorinated polyethylene PMP poly (4-methylpentene- I ) CLPVC /CPVC chlorinated polyvinyl chloride POB polypoxybenzoate CMC carboxymethyl cellulose POM polyoxymethylene (polyacetal) CN cellulose nitrate PP polypropylene CP cellulose propionate PPC polypropylene compound CPE chlorinated polyethylene PPE polypropylene ethylene CS casein PPF polypropylene foam DAP diallyl phthalate PPO polyphenylene oxide modified DMC dough molding compound PPDX polypropylene oxide EC ethyl cellulose PPS polyphenylene sulphide E/EA, EEA ethylene / ethyl acetate PPSU polyphenylene sulphone EEBC polyester (ether ester block copolymer) PS polystyrene E / MA ethylene methacrylate acid PSU polysulphone EP epoxide, epoxy resin PTFE polytetrafluoethylene EPS polystyrene - expandable ethylene -
Table 1. SOME NAMES and ABBREVIATIONS of Plastics and Elastomers
TABlE 1. SOME NAMES AND ABBREVIATIONS OF PlASTICS AND ElASTOMERS. Common name Abbreviation Acetal (homopolymer and copolymer) POM-H and POM-K Acrylate styrene acrylonitrile ASAorAAS Acrylate modified styrene acrylonitrile ASAorAAS Acrylic acid ester rubber ACM Acrylonitrile butadiene rubber or nitrile butadiene rubber NBR Acrylonitrile butadiene styrene ABS Acrylonitrile styrene/chlorinated polyethylene ACS Acrylonitrile methyl methacrylate AMMA Acrylonitrile styrene/EPR rubber or, acrylonitrile ethylene propylene styrene AES Alpha methyl styrene AMS Atactic polypropylene APPorPP-A Butadiene rubber or, cis-1,4-polybutadiene rubber or, polybutadiene rubber BR Butadiene styrene block copolymer BDS Butyl rubber IIR Bulk molding compound BMC Casein formaldehyde CF Cellulose acetate CA Cellulose acetate butyrate CAB Cellulose acetate propionate CAP Cellulose nitrate CN Chlorinated polyethylene CPEorCM Chlorinated polyvinyl chloride CPVC or, PVC-C Chloro-polyethylene or, chlorinated polyethylene. CM or CPE or, PE-C Chloroprene rubber or, polychloroprene rubber CR Chlorotrifluoroethylene ethylene copolymers ECfFE Cis-polyisoprene or, cis-1,4-polyisoprene IR Coumarone indene resins CIR Diallyl phthalate DAP Diallyl isophthalate DAIP Dough molding compound DMC Elastomeric alloy melt processable rubber EA-MPR Elastomeric alloy thermoplastic vulcanizate EA-TPV Epichlohydrin rubber CHR Epoxy or, epoxide EP Epoxy or, epoxide, with glass fiber EPGF Ethyl cellulose EC Ethylene acryic acid EAA Ethylene propylene diene monomer (an EPR terpolymer) EPDM -
Bio-Based and Biodegradable Plastics – Facts and Figures Focus on Food Packaging in the Netherlands
Bio-based and biodegradable plastics – Facts and Figures Focus on food packaging in the Netherlands Martien van den Oever, Karin Molenveld, Maarten van der Zee, Harriëtte Bos Rapport nr. 1722 Bio-based and biodegradable plastics - Facts and Figures Focus on food packaging in the Netherlands Martien van den Oever, Karin Molenveld, Maarten van der Zee, Harriëtte Bos Report 1722 Colophon Title Bio-based and biodegradable plastics - Facts and Figures Author(s) Martien van den Oever, Karin Molenveld, Maarten van der Zee, Harriëtte Bos Number Wageningen Food & Biobased Research number 1722 ISBN-number 978-94-6343-121-7 DOI http://dx.doi.org/10.18174/408350 Date of publication April 2017 Version Concept Confidentiality No/yes+date of expiration OPD code OPD code Approved by Christiaan Bolck Review Intern Name reviewer Christaan Bolck Sponsor RVO.nl + Dutch Ministry of Economic Affairs Client RVO.nl + Dutch Ministry of Economic Affairs Wageningen Food & Biobased Research P.O. Box 17 NL-6700 AA Wageningen Tel: +31 (0)317 480 084 E-mail: [email protected] Internet: www.wur.nl/foodandbiobased-research © Wageningen Food & Biobased Research, institute within the legal entity Stichting Wageningen Research All rights reserved. No part of this publication may be reproduced, stored in a retrieval system of any nature, or transmitted, in any form or by any means, electronic, mechanical, photocopying, recording or otherwise, without the prior permission of the publisher. The publisher does not accept any liability for inaccuracies in this report. 2 © Wageningen Food & Biobased Research, institute within the legal entity Stichting Wageningen Research Preface For over 25 years Wageningen Food & Biobased Research (WFBR) is involved in research and development of bio-based materials and products. -
5183861.Pdf (200.1Kb)
l|||||llllllll||||||ll||||l|||||||||||||||llllllllllIllllllllllllllllllllll . U5005183861A Ulllted States Patent [19] [11] Patent Number: - 5,183,861 Riffle et a1. ’ [45] Date of Patent: Feb. 2, 1993 [54] POLYALKYLOXAZOLINE/POLYLACIONE [56] References Cited ANDCOPOLYMERS, USES PROCESSES FOR MAKING 1 US. PATENT DOCUMENTS 3,375,231 3/1968 Fukui et al. ......................... 525/415 . 4659 777 4/1987 Riflle et a1. 525/100 [75] Inventors: JudySinging“; S. lefle; Andrew Gurudus E. D. Brink, an of 4,910,268 ’ ’ 3/1990 Kobayash: - 525/411 Blacksburg, Va. OTHER PUBLICATIONS J. Appl. Polymer Sci, vol. 31, 1189-1197 (1986). [73] Assignee: Virginia Tech Intellectual Properties, Primary Examiner—~Ana L. Carrillo Inc., Blacksburg, Va. Attorney, Agent, or Firm—Richard P. Fennelly; Louis [211 App]. No.: 355,709 A' Moms [57] ABSTRACT [22] Filed: May 23, 1989 Block copolymers of polyoxazoline and polylactone moieties can be used as polymeric compatibilizers for [51] Int. Cl.5 .............................................. C08G 63/91 polyamides and polyolefins. [52] US. Cl. ............................... 525/413; 525/415 [58] Field of Search 525/413, 415 4 Claims, No Drawings 5,183,861 1 POLYALKYLOXAZOLINE/POLYLACT ONE ~ —[N-CH2CH21,.. COPOLYMERS, PROCESSES FOR MAKING, AND C(O)R USES R is aryl, alkyl or hydrogen. The subscript n can BACKGROUND OF THE INVENTION where range from a minimum of about 5 to a maximum of 1. Field of the Invention about 1000. The present invention relates to novel copolymers For example, poly(2-ethyloxazoline)/polycaprolac- suitable for use as polymeric compatibilizers. 10 tone block copolymers possessing the general structure 2. Description of the Prior Art described above can be synthesized by first polymeriz- The blending of certain types of copolymer composi- ing ethyl oxazoline using benzyl iodide as the initiator, tions (e.g., block copolymers) with other polymers ei- then terminating the reaction product with potassium This produces a primary hy- ther homopolymers or copolymers, is an industrially hydroxide or ammonia. -
United States Patent (19) 11 Patent Number: 4,585,701 Bartoszek Et Al
United States Patent (19) 11 Patent Number: 4,585,701 Bartoszek et al. (45) Date of Patent: Apr. 29, 1986 54) COMPOSITES OF POLYVINYLIDENE 3,524,906 8/1970 Schmitt et al. ...................... 525/199 FLUORDE ALLOYS AND 3,968, 196 7/1976 Wiley .............. ... 264/171. THERMOPLASTC POLYMERS AND THEIR 4,051,293 9/1977 Wiley .............................. 428/421 X PREPARATION 4,215,177 7/1980 Strassel ........................ 428/424.6 X 4,221,757 9/1980 Strassel ............................... 264/171 75 Inventors: Edward J. Bartoszek, Jeffersonville, 4,226,904 10/1980 Olivier et al... ... 156/322 X Pa.; Steven F. Mones, Newark, Del. 4,289,560 9/1981. Simons ............ ... 156/244.18 73) Assignee: Pennwalt Corporation, Philadelphia, 4,291,099 9/1981 Strassel ... ... 428/421 4,317,860 3/1982 Strassel ....... ... 428/42 Pa. 4,317,861 3/1982 Kidoh et al. ........................ 428/421 21) Appl. No.: 580,483 FOREIGN PATENT DOCUMENTS 22 Filed: Feb. 15, 1984 0060421 9/1982 European Pat. Off. ............ 264/171 51 Int. Cl'.............................................. B32B 27/08 OTHER PUBLICATIONS 52 U.S. C. ...................................... 428/421; 264/37; 264/171; 264/176 R; 428/424.2; 428/424.6; Pennwalt Technical Data Sheet, "KYNAR(R)/Acrylic 428/424.8 Alloys RC-9637 and RC-9638', 7/22/80. 58 Field of Search .................. 428/421, 424.6, 424.2, 428/424.8; 525/199; 264/171, 176 R, 37; Primary Examiner-Thomas J. Herbert 156/322, 244.18 (57) ABSTRACT 56) References Cited Composites of polyvinylidene fluoride alloys, and in U.S. PATENT DOCUMENTS compatible thermoplastic polymers are prepared by 3,253,060 5/1966 Koblitz et al. -
PVDC – New Developments, New Opportunities
PVDC – New Developments, New Opportunities Kirk Paisley SolVin, a division of Solvay Advanced Polymers, L.L.C. Alpharetta, Georgia Introduction The information in this presentation will provide basic background information on the use of PVDC resins and coatings in packaging applications. It will also give data on new grades of PVDC resins and latex, which can lead to the development of new packaging films by flexible packaging converters and film manufacturers. Background Polyvinylidene chloride (PVDC) resins and coatings have been a part of the flexible packaging world for more than 50 years, with a unique combination of functional characteristics that has found numerous applications. It is available in a variety forms: • Aqueous dispersions, or latex, for coating on a number of different film and paper substrates, • Extrudable powders, for monolayer or multilayer films and sheet, and • Soluble powders, for solvent-based coatings on films. Extrudable PVDC Powder Soluble PVDC Powder Aqueous PVDC Dispersion According to 2004 estimates1, approximately 160,000 metric tons of PVDC are used annually around the world in extruded, coextruded, coated and laminated structures. In a study of high barrier packaging films released in late 20052, PVDC was reported to be the leading barrier polymer in high performance packaging films. For example, in dry food packaging, PVDC-coated BOPP films hold a 53% share of barrier films used to package dry foods. Also, the forecasted growth for PVDC-coated PET films is a healthy 9% per year, driven primarily -
Manual on Food Packaging for Small and Medium Size Enterprises in Samoa
Manual on Food Packaging for Small and Medium Size Enterprises in Samoa Manual on Food Packaging for Small and Medium-Size Enterprises in Samoa Prepared with the cooperation of the Small and Medium Food Enterprises in Samoa by FAO Consultant Richard Beyer. Food and Agriculture Organization of the United Nations Sub-Regional Office for the Pacific Islands Apia, 2012 About this manual This manual was prepared under funding support by FAO Technical Cooperation Programme project TCP/SAM/3203. It is based on consultation with a number of small and medium size enterprises (SMEs) in Samoa during July 2012. The layout is such that specific packaging information is included in the first chapter, while the second chapter relates to findings in Samoa and highlights points where there is common ground. The third chapter builds on chapter two and suggests strategies for consideration by SMEs. It has been the intention to include a number of areas where quality can be improved and maintained inexpensively and with it a closer match between packaging, shelf-life and consumer expectation. The ultimate aim is to enable processors to select the most appropriate packing for their products and thereby become more profitable and successful in both local and export markets. It is to be recognised that the packaging industry is very dynamic and new combination of components are becoming available on a frequent basis and thus this only reflects the current state of packaging and would need periodic updating. All comments and feedback are welcome and should be sent to [email protected] and [email protected]. -
Interaction Between Vinyl Acetate-Ethylene Latex Stabilized with Polyvinyl Alcohol and Portland Cement
Interaction between Vinyl Acetate-Ethylene Latex stabilized with Polyvinyl Alcohol and Portland Cement vorgelegt von M. Sc. Yu Jin aus Wuhan, V.R. China von der Fakultät VI – Planen Bauen Umwelt der Technischen Universität Berlin zur Erlangung des akademischen Grades Doktor der Ingenieurwissenschaften - Dr. -Ing. - genehmigte Dissertation Promotionsausschuss: Vorsitzender: Prof. Dr. Frank U. Vogdt Gutachter: Prof. Dr. habil. Oliver Weichold Gutachter: Prof. Dr. habil. Dietmar Stephan Gutachter: Dr. habil. Wolf-Dieter Hergeth Tag der wissenschaftlichen Aussprache: 07.10.2015 Berlin 2016 Acknowledgements First I would like to express my heartfelt gratitude to Prof. Dr. Dietmar Stephan for giving me the opportunity to conduct my doctoral work at the chair of building materials and construction chemistry at TU Berlin, especially I experienced a dark period before that. I acknowledge him for all the supervision, supports and valuable discussion throughout my thesis, as well as the confidence he placed on my work. I also owe my gratitude to my second supervisor Dr. Dieter- Wolf Hergeth from Wacker Chemie AG for his unreserved pass of knowledge. Many part of the thesis would not have been possible without his support and guidance. I benefit a lot from their supervisions and experienced considerable progress on how to conduct scientific work. I also would like to thank DAAD (Deutscher Akademischer Austauschdienst) for financial assistance during my study. Personally, I deeply appreciate the support from David Hildebrand when he worked at DAAD. I like to take this opportunity to express my thanks to the following people at the chair: Jessica Grewe, Anja Städtke, David Dahnacke for their technical assistance; Agnieszka Kowalczyk from Kiwa for help on ICP; Annekathrin Aisch for all the administrative stuffs; Dr. -
Applications of Vinylidene Chloride
The Dow Chemical Company Vinylidene Chloride VCCEP Submission VINYLIDENE CHLORIDE (VDC) VCCEP SUBMISSION The Dow Chemical Company November 2002 1 The Dow Chemical Company Vinylidene Chloride VCCEP Submission Table of Contents 1. Executive Summary 4 2. Basis for VCCEP Pilot Program Listing 2.1 Overview 7 2.2 Biomonitoring Data 2.2.1 Review of Data 7 2.2.2 Analytical Issues 9 2.2.3 Relevance 9 2.3 Indoor Air Review 2.3.1 Indoor Air Monitoring Studies 10 2.3.2 VDC Concentration in Personal Air Samples 11 2.3.3 Discussion 11 2.3.4 Summary 12 2.4 National Contaminants Occurrence Database 13 3. Product Overview 3.1 Mfg. Process 14 3.2 Volume 14 3.3 Physical / Chemical Properties 15 3.4 Product Stewardship Program 15 3.5 Regulatory Approvals 16 4. Potential VDC Sources to Humans and Environment 17 4.1 VDC Manufacturing & Processing 17 4.1.1 U.S. Toxics Release Inventory 17 4.1.2 Occupational 18 4.2 VDC Applications 19 4.2.1 Polyvinylidene Chloride Applications 20 4.2.2 Intermediate Applications 22 4.3 Higher Chlorinated Products Degradation 22 4.3.1 Fate of VDC in Groundwater & Soil 23 4.3.2 Fate of VDC in Air 23 4.3.3 Summary 23 4.4. Summary of Potential VDC Sources 24 5. Exposure Assessment 5.1 Exposure Pathways 5.1.1 Plausible Exposure Pathways 24 5.1.2 Selected Exposure Pathways 25 5.2 Ambient Air Exposure Assessment 5.2.1 Distribution of Exposure 26 5.2.2 Summaries of Additional Relevant References 27 5.3 Water Exposure Assessment 5.3.1 Distribution of Exposure 32 2 The Dow Chemical Company Vinylidene Chloride VCCEP Submission 5.3.2 Summaries of Additional Relevant References 32 5.4 Application Assessments 5.4.1 Food Wrap 34 5.4.2 Carpet Latex 35 5.5 Estimated Aggregate Exposure 41 5.6 Aggregate Exposure Summary 42 6. -
Industry Acronyms
INDUSTRY ACRONYMS AAS — Methacrylate-acrylic-styrene JIT — Just-in-time (delivery) PTFE — Polytetrafluoroethylene ABS — Acrylonitrile-butadiene-styrene LCD — Liquid crystal display PTMT — Polytetramethylene terephthalate AN — Acrylonitrile LCP — Liquid crystal polymer PUR — Polyurethane AO — Antioxidant L/D — Length:diameter ratio PVAC — Polyvinyl acetate APP — Atactic polypropylene LDPE — Low-density polyethylene PVAL — Polyvinyl alcohol AS — Antistatic LIM — Liquid injection molding PVC — Polyvinyl chloride ASA — Acrylonitrile-styrene-acrylate LLDPE — Linear low-density polyethylene PVCA — Polyvinyl chloride acetate ASTM — American Society for Testing & Materials LSM — Liquid silicone molding PVCC — Chlorinated polyvinyl chloride BMC — Bulk molding compound MAP — Modified atmosphere packaging PVDC — Polyvinylidene chloride BOPP — Biaxially oriented polypropylene MPC — Microprocessor-controlled PVDF — Polyvinylidene fluoride CAD — Computer-aided design MSDS — Material Safety Data Sheet PVF — Polyvinyl fluoride CAM — Computer-assisted manufacturing MDPE — Medium-density polyethylene QC — Quality control CAMM — Canadian Association of Mouldmakers MI — Melt index RAPRA — Rubber and Plastics Association (U.K.) CAP — Controlled atmosphere packaging mLLDPE — Metallocene linear low-density R&D — Research and development CFC — Chlorofluorocarbon polyethylene RFI — Radio frequency interference CIM — Computer-integrated manufacturing MMW — Medium molecular weight RFID — Radio frequency identification CM — Compression molding MRP — Materials requirement -
ABS Acrylonitrile-Butadiene-Styrene ACM-V Vulcanized Acrylate Rubber
ABS Acrylonitrile-Butadiene-Styrene ACM-V Vulcanized acrylate rubber ACS Acrylonitrile Chlorinated polyethylene Styrene AES or AEPDS Acrylonitrile EPDM Styrene ASA Acrylonitrile Styrene Acrylate BMC Bulk Moulding Compound BOPP Bi-axially Oriented PolyPropylene CA Cellulose Acetate CAB Cellulose AcetoButyrate CBT Cyclic polyButadiene Terephthalate CE Cyanate Ester CF Carbon Fibre CFC ChloroFluoroCarbon CM or CPE Chlorinated PolyEthylene COPE or TPEE COPolyEster TPE CP Cellulose Propionate CPE or CM Chlorinated PolyEthylene CPVC or PVC-C Chlorinated PVC Cy PolyCyanate DAP DiAllyl Phthalate DCPD Poly(DiCycloPentaDiene) DMC Dough Moulding Compound EBA, EGMA Ethylene-acid and ethylene-ester copolymers e.g. Ethylene-ButylAcrylate ECTFE, EEA, EMAH, EAA Ethylene monoChloroTriFluoroEthylene EMA Ethylene-MethAcrylate ionomers EMI ElectroMagnetic Interference EP EPoxy EPDM rubber Terpolymer ethylene propylene diene EPS Expandable (or Expanded) PolyStyrene ETFE Ethylene-TetraFluoroEthylene EVA E/VAC Ethylene-VinylAcetate copolymers EVAC /VAE/ EVM /EVOH Ethylene-Vinyl alcohol copolymers F-PVC Flexible PVC FEP Fluorinated Ethylene Propylene GFRP Glass Fibre Reinforced Plastic HDPE or PE HD High Density PolyEthylene HPGF High-Performance short Glass Fibre reinforced polypropylene HTPC Hybrid ThermoPlastic Composite LDPE or PE LD Low Density PolyEthylene LFRT Long Fibre Reinforced Thermoplastic LFT Long Fibre reinforced Thermoplastic LGF Long Glass Fibre LIM Liquid Injection Moulding LLDPE Linear Low Density PolyEthylene LSR Liquid Silicone Rubber LWRT